This article will discuss encapsulated O-rings, their advantages, disadvantages, and the manufacturing process. It will also help you understand the heating method used in the manufacturing of these O-rings and their different types. Stick with us till the end if you are interested in mechanics and the Encapsulated O-rings.
What is an Encapsulated O-ring?
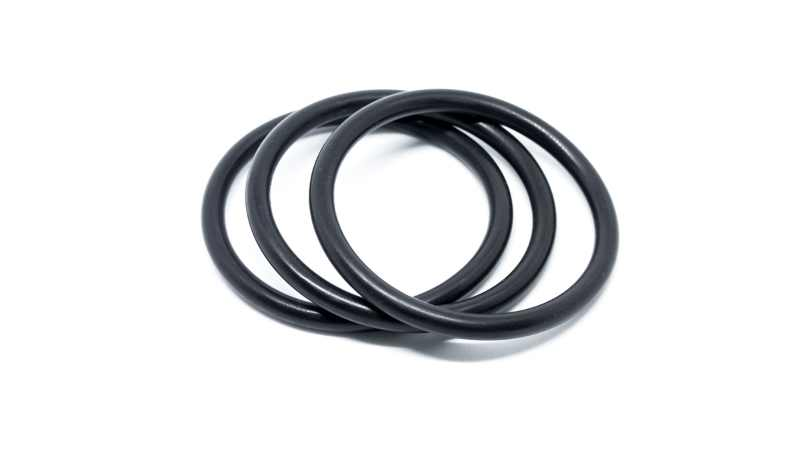
An encapsulated O-ring is a specialized seal made from a combination of two materials, consisting of two major parts, i.e., outer coat and inner core. Such seals are often used at both industrial and domestic levels to stop leakage of air, gas, or liquids through the joints.
These seals provide additional flexibility, endurance, stability, and chemical and temperature resistance. Though you can use any rubber O-ring or seal to do the job, using an encapsulated O-ring has its additional perks.
The double-layered o-ring is made of an outer coat, which is usually a material named Teflon, and an inner core, which is either silicone or Viton. The outer Teflon material encapsulates the inner core, hence giving the name Teflon encapsulated O-rings.
How Were Encapsulated O-rings Made?
The history of O-rings dates back to the 20th century, when a Denmark-born machinist, Niel Christensen, was working as a brake system mechanic for street cars in the US. Niel Christensen was born in 1865 in Denmark and later moved to the US in 1891.
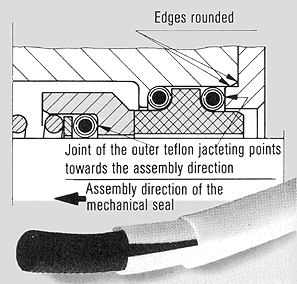
During his job as a brake system mechanic, he tried different materials to seal the pipes and other joints for an effective braking mechanism. It was in 1936 that he found a way to install rubber seals in pistons, and just three years later, in 1939, he successfully finished the patent application.
Take the First Step:
Requst for an Inquire
Quality Meets Affordability. Inquire Now for High-Quality Products at Low Volumes.
Types of Encapsulated O-Rings
Though the purpose of all the encapsulated O-rings is almost the same, there are minor differences in their manufacturing and design, which make their task a bit more specific.
Hollow core O-rings and Solid core O-rings are the two types of Encapsulated O-rings based on their core design. There are several other types of O-rings depending on the material used in the outer jacket and inner core, each with its unique features.
Solid Core
Solid core O-rings are specifically made to deal with lower temperatures. It is because their inner core is filled with a material named Silicone or Viton, like the tires of a tubeless bike.
Solid core O-rings provide excellent contraction and flexibility, making them the best choice for use in Frigid temperatures. The core material also plays a major role in determining the premium features of the encapsulated O-ring.
The Viton inner core O-ring is well known for its flexibility and shrinking abilities, while the Silicone inner core O-ring is famous for its heat-resistant ability. Solid core encapsulated O-ring is renowned for its retention of elasticity.

Hollow Core
Hollow core o-rings, as the name suggests, are hollow from the inside, like any inflatable bike tire. Hollow core O-rings are similar to solid core O-rings as both have an outer jacket made of Teflon that encapsulates the inner core, except that the former is hollow from the inside.
The outer jacket is either made of PFA or FEP, depending on the requirements and the conditions it has to survive in. On the other hand, the inner core is either FKM (made of Viton) or silicone, giving it the unique ability to squeeze into tight spaces. However, such O-rings struggle with recovery after contraction.
FEP
FEP, expanded as Fluorinated Ethylene Propylene, is not a type of encapsulated O-ring but a specific material that makes a unique type of encapsulated O-ring. Most people confuse it with Teflon, which is another material used in the outer coating of the encapsulated O-rings.
FEP also has several other names in the industry, such as Neoflon FEP, Teflon FEP, and Dyneon FEP. The numerous features of FEP-coated O-rings include low friction and resistance to temperatures ranging from -60°C to +205°C.
It can also remain flexible at cryogenic temperatures, showing effective cryogenic seal performance. Moreover, it is also highly resistant to corrosive chemicals, besides being non-flammable.
FEP has a very low compression set, which shows that it can come back to its original shape after deformation. This material can help manufacture different types of O-rings, such as FEP encapsulated solid silicone, FEP encapsulated steel spring, and FEP encapsulated hollow silicone.
PFA
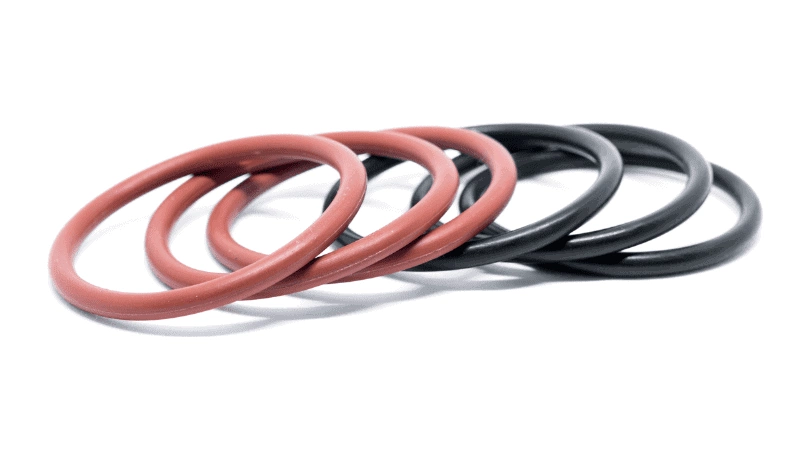
Perfluoroalkoxy-copolymer, abbreviated as PFA, is another material used in encapsulated O-rings. It is almost similar to FEP in all of its features, except that it is a bit more advanced and offers more resistance to temperatures (-60 °C to +260 °C).
Besides, it is resistant to a wider range of chemicals than FEP, such as petroleum, acids, naphtha, aromatic solvents, and alcohol.
PFA has higher mechanical strength, which means it can withstand high pressures and stretches. It is also resistant to cracks and high-stress conditions and is often used at an industrial level where high durability and thermal stability are required. On the contrary, it is also more expensive than FEP.
Nitrile Elastomer
If you are looking for an encapsulated O-ring for common use, such as sealing joints that deal with water, oils, or hydraulic fluids, then Nitrile Elastomer is your go-to choice. Also known as Buna-N or NBR, Nitrile Elastomer is a general-purpose rubber often used for temperature ranges of -50°C to 120°C.
Though it has good resistance to temperatures and abrasive processes, there is a high risk of damage if the limit is exceeded.
For example, substances like ketones, nitrohydrocarbons, Phosphorus esters, etc., can cause damage to the rings. Due to this, nitrile elastomers are only suitable for limited applications in automobiles, railways, sanitary, and agricultural.
Viton O-rings
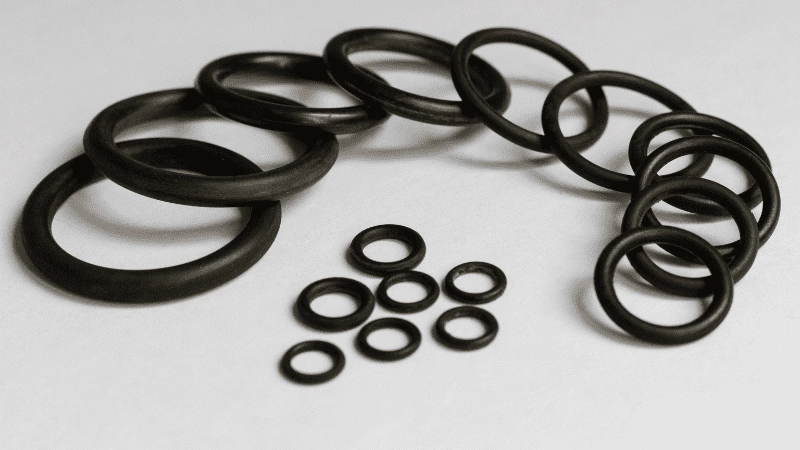
Viton O-rings are a type of encapsulated O-ring with an FKM or Viton inner core. The outer jacket might be of PFA or FEP, depending on whether you need an FEP-encapsulated Viton core or a PFA-encapsulated Viton core. These also have excellent thermal stability within a temperature range of -40 °C to 250°C.
In a nutshell, Viton O-rings have high mechanical strength, low compression set resistance, and low gas permeability. These features make it a perfect choice for automobiles, aerospace industries, and chemical engineering industries.
Though they work fine with petroleum, acids, halogenated hydrocarbons, and silicone fluids, one should avoid contact with heated hydrofluoric acids, esters, low molecular weight amines, and Skydrol.
Silicone O-rings
Like other encapsulated O-rings, silicone O-rings have excellent thermal stability for temperatures ranging between -100°C and 300 300°C.
Moreover, Silicone O-rings’ specially designed inner core provides exceptional tolerance up to -115°C to 315°C for some time. This makes it an ideal choice for areas where extreme temperature fluctuations are expected.
Like other encapsulated O-rings, Silicone O-rings also work better with static applications.
Moreover, these O-rings are acclaimed for their flexibility and abrasion resistance. However, they only work better with water, oil, and steam. There are two types of Silicone O-rings: Hollow Silicone core and solid silicone core.
Take the First Step:
Requst for an Inquire
Quality Meets Affordability. Inquire Now for High-Quality Products at Low Volumes.
Benefits and Limitations of Encapsulated O-rings
So far, we have discussed different types of encapsulated O-rings and their applications in different industries and conditions. Here are some benefits of encapsulated O-rings that make them a better choice than an ordinary plastic or elastomeric seal.
- Exceptional thermal stability for temperatures up to 500 degrees Fahrenheit.
- Available in different shapes and sizes as per your demand.
- Resistant to corrosive chemicals
- Made from FDA-approved non-toxic materials
- Highly flexible and durable for stress conditions
These were some of the positive aspects of using encapsulated O-rings instead of regular rubber seals. However, here are some limitations that you must know before dealing with encapsulated O-rings.
- Most of these O-rings work with static applications.
- You must check the compatibility of the material with various chemicals
- All types have temperature limitations, though the limits are quite high.
Encapsulated O-Rings Heating Method
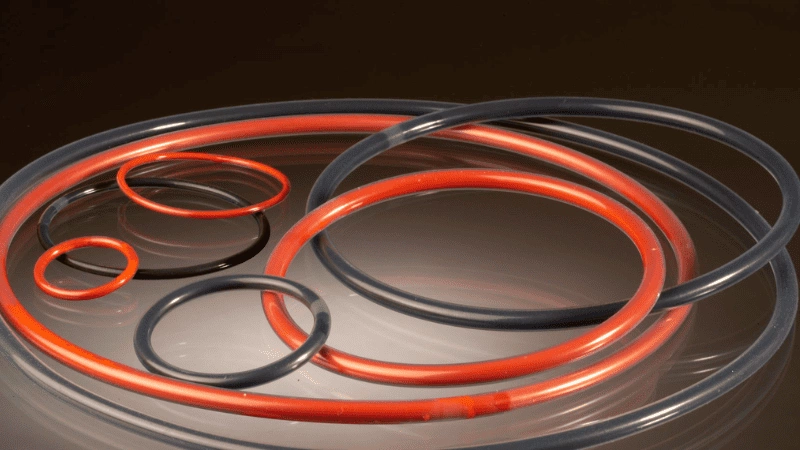
Encapsulated O-rings are made from durable materials that might not provide much stretch when cold. For installation, it is recommended to heat the O-rings for a seamless procedure.
The perfect procedure is heating the O-rings in hot water at 100°C for up to 3 minutes. You can then install the O-rings where you want to, while the O-rings are still hot.
On the other hand, you can also use oven heating for the procedure. However, this might require extra time as you have to heat the O-rings in the oven at 100°C for up to 15 minutes. After that, you can follow the installation procedure while ensuring the O-rings are still hot.
Take the First Step:
Requst for an Inquire
Quality Meets Affordability. Inquire Now for High-Quality Products at Low Volumes.
Conclusion
Encapsulated O-rings are notable for their premium features in various industries. Their exceptional endurance and compatibility with a variety of chemicals and gases make them a perfect choice. Though they are available in a variety of sizes and shapes, the circular or cylindrical shape is the standard, which is readily available.
Contact Hongju for Encapsulated O-rings
To suit the requirements of your machinery and equipment, Hongju Rubber Products produces many variations in various sizes, materials, and styles. If you’re looking for an o-ring that works well in your application, get in touch with us immediately.
We can get you started on your upcoming project and assist you in locating the ideal o-ring for your requirements.