Whether you’re in chemical processing dealing with corrosive fluids, aggressive chemicals, or navigating other extreme temperatures, FEP encapsulated O-rings provide a level of seal integrity that other O-ring types simply can’t match. This article aims to explore the unique properties, advantages, and applications of FEP-encapsulated O-rings, equipping you with comprehensive insights for your sealing needs.
What is FEP?
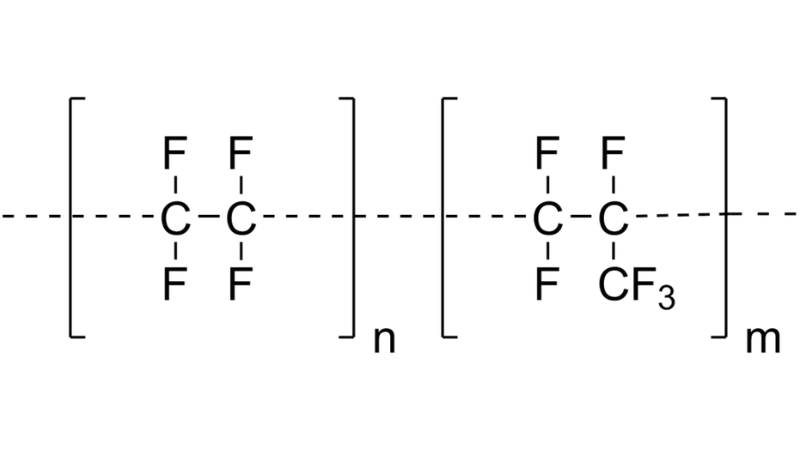
FEP(Fluorinated Ethylene Propylene) is a type of fluoropolymer that possesses unique properties and characteristics. It is known for its exceptional chemical and temperature resistance, which makes it a nearly universal choice in sealing applications where aggressive chemicals and extreme temperatures are involved. Unlike some traditional materials, FEP is virtually chemically inert and exhibits low reactivity, making it robust against chemical attacks and minimizing the risk of premature seal failure.
FEP also showcases other remarkable features like a low coefficient of friction and high electrical insulation, extending its utility beyond just sealing applications to electronic components and wiring as well.
Why Use FEP Encapsulation?
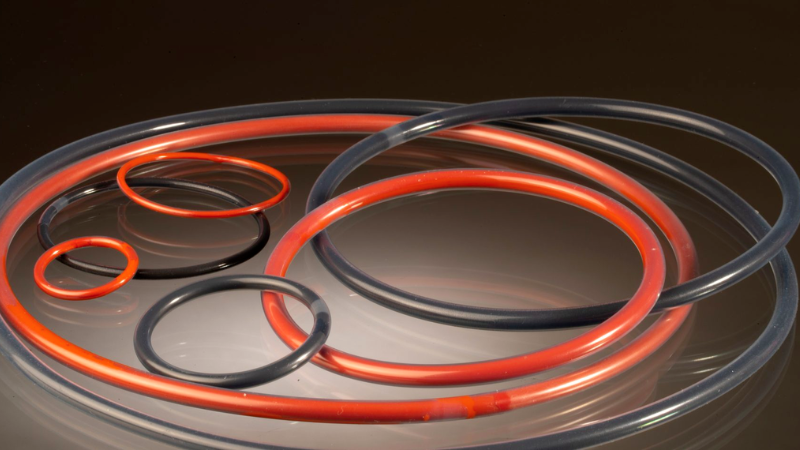
The utilization of FEP encapsulation, especially in O-rings, addresses many of the shortcomings associated with both traditional and exotic O-ring compounds. Here’s why:
- Chemical and Temperature Resistance: FEP encapsulated O-rings can withstand extreme temperatures and are impervious to most aggressive chemicals and corrosive fluids, making them ideal for high-risk applications in chemical treatment, pharmaceuticals, and more.
- Reliable Sealing: The combination of an elastomeric core with a robust FEP outer layer provides a seal that is both flexible and strong. This dual-layer design ensures long-lasting, reliable sealing even under fluctuating pressures and temperatures.
- Low Friction: FEP’s low coefficient of friction reduces wear and tear, further extending the life span of the seal and reducing maintenance needs.
- Core Material Options: FEP encapsulation can be done around different core materials, like silicone or Viton, offering customization based on specific needs.
- Minimized Risk of Seal Failure: Because FEP is virtually chemically inert, the risks of chemical attack and premature seal failure are significantly reduced.
Given these advantages, FEP encapsulated O-rings offer preeminent performance across various industries and applications, from dealing with aggressive chemicals to operating in extreme temperature environments.
Anatomy of an FEP-Encapsulated O-Ring
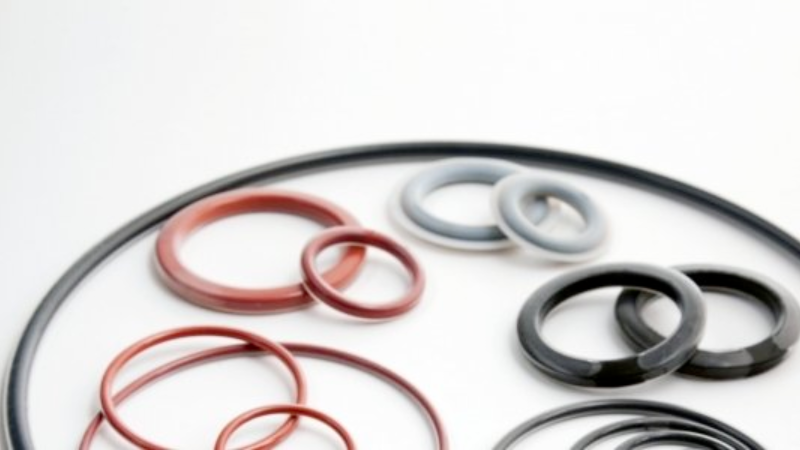
An FEP-encapsulated O-ring is a specialized sealing component that offers exceptional performance in various industries and applications. Let’s take a closer look at the structure and composition of this unique O-ring design, exploring the core material, the role played by encapsulation, and how it contributes to superior sealing performance.
Structure and Composition
FEP-encapsulated O-rings consist of multiple layers that work together to provide effective sealing capabilities. At the core lies a resilient elastomeric material such as silicone or Viton®. This core material acts as the primary sealant, offering excellent compression set resistance and chemical compatibility.
Surrounding the core material is a layer of FEP (fluorinated ethylene propylene), which serves as an encapsulating barrier. FEP is a high-performance thermoplastic known for its outstanding chemical resistance, low friction properties, and wide temperature range. This transparent layer provides protection to the core material while ensuring efficient sealing.
The Role of Encapsulation
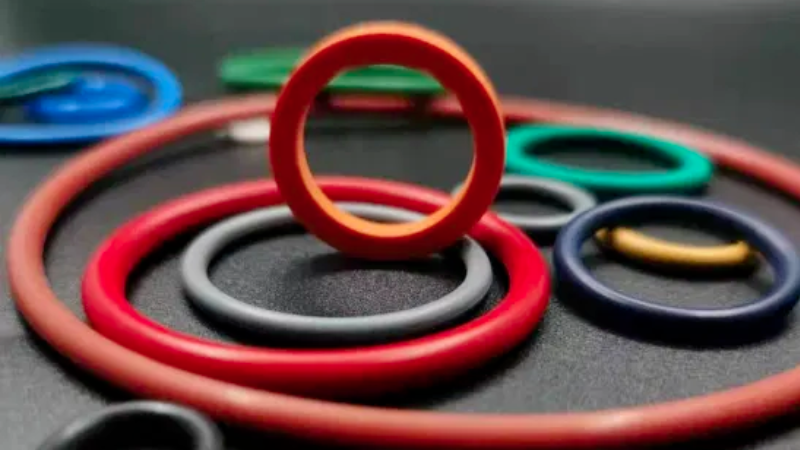
The encapsulation process involves molding the FEP layer onto the elastomeric core under carefully controlled conditions. This fusion creates a strong bond between the two materials, resulting in an integrated structure with enhanced durability and reliability.
One of the key advantages offered by encapsulation is improved resistance against aggressive chemicals, solvents, and high temperatures. The FEP layer acts as a barrier between the core material and external elements, preventing degradation or swelling that could compromise seal integrity. This makes FEP-encapsulated O-rings suitable for demanding environments where conventional seals may fail.
Encapsulation helps minimize friction during installation or operation due to its low coefficient of friction. This reduces wear on mating surfaces while facilitating smooth movement without compromising sealing efficiency.
Properties and Applications of FEP Encapsulated O-Rings
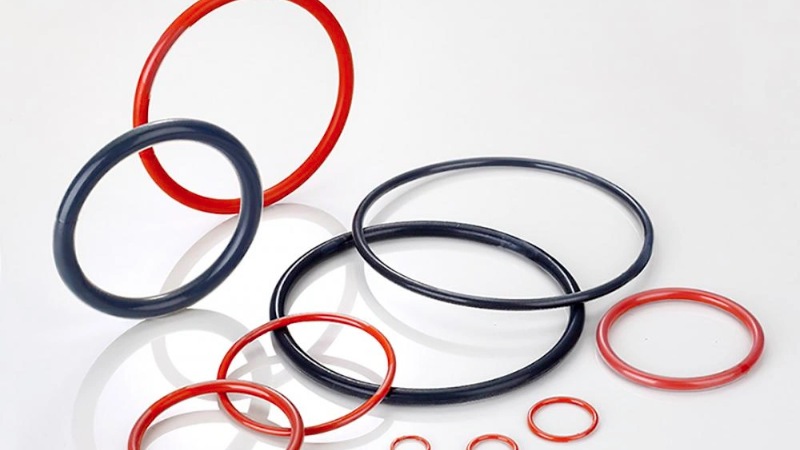
Properties of FEP Encapsulated O-Rings
- Temperature Resistance: FEP encapsulated O-rings can operate effectively within a broad temperature range, offering excellent performance under extreme temperatures.
- Chemical Resistance: These O-rings are highly resistant to chemical attack, making them ideal for applications that involve exposure to aggressive chemicals.
- Core Material Flexibility: The elastomeric core can be made of various materials like silicone or Viton, each offering unique properties.
- Low Coefficient of Friction: FEP’s low coefficient ensures minimal wear and tear on both the O-ring and the sealing surface, which translates to longer life and less maintenance.
- Highly Inert: FEP is virtually chemically inert, reducing the possibility of premature seal failure or degradation over time.
Applications of FEP Encapsulated O-Rings
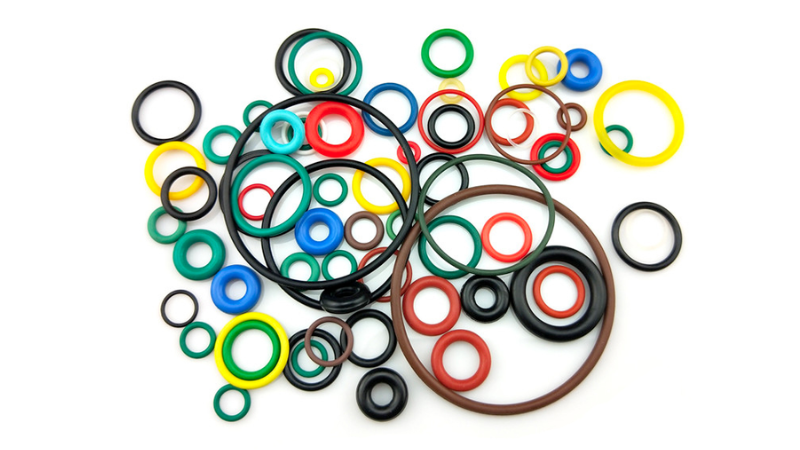
- Chemical Processing: Their high chemical and temperature resistance makes them invaluable in environments that handle corrosive or hazardous substances.
- Pharmaceuticals: Given their resistance to chemical exposure and a wide temperature range, they are used in pharmaceutical manufacturing and storage facilities.
- Food Industry: Their chemical inertness makes them suitable for applications where food and beverages are processed and stored.
- Oil and Gas: In oil and gas applications, they provide reliable sealing against corrosive fluids and extreme environmental conditions.
- Aerospace: The O-rings’ ability to withstand extreme temperatures and chemical processing makes them ideal for aerospace applications, where they often come into contact with high-performance engineering materials.
Comparison with Other Types of O-Rings
To fully understand the value of FEP-encapsulated O-rings, it’s essential to compare them to other common types such as solid PTFE O-rings and traditional elastomeric O-rings.
Features/Types | FEP Encapsulated O-Rings | Solid PTFE O-Rings | Traditional Elastomeric O-Rings |
---|---|---|---|
Chemical Resistance | High | High | Moderate to Low |
Temperature Resistance | Extreme Temperatures | High Temperature | Moderate Temperature |
Elasticity/Flexibility | Moderate (due to elastomeric core) | Low | High |
Friction Coefficient | Low | Moderate to High | Varies |
Cost | Moderate to High | High | Low to Moderate |
Resistance to Chemical Attack | High | High | Low |
Application Scope | Broad (from aerospace to food industry) | Specialized | General Purpose |
Failure Rate | Low (virtually chemically inert) | Moderate | High in aggressive chemicals |
Suitability for Corrosive Fluids | High | High | Low |
Key Takeaways:
- Chemical Resistance: While both FEP encapsulated and solid PTFE O-rings offer high resistance to chemical attack, the former often performs better in dynamic applications due to its elastomeric core.
- Temperature Range: FEP-encapsulated O-rings can withstand extreme temperatures, making them superior to traditional elastomeric O-rings in this aspect.
- Flexibility and Seal Integrity: The elastomeric core in FEP encapsulated O-rings offers better flexibility than solid PTFE O-rings, making them more versatile for a variety of sealing applications.
- Cost-Effectiveness: Although FEP-encapsulated O-rings may initially be more expensive than traditional O-rings, their long lifespan and low failure rate often make them more cost-effective in the long run, particularly in applications involving corrosive fluids and extreme temperatures.
Potential Drawbacks
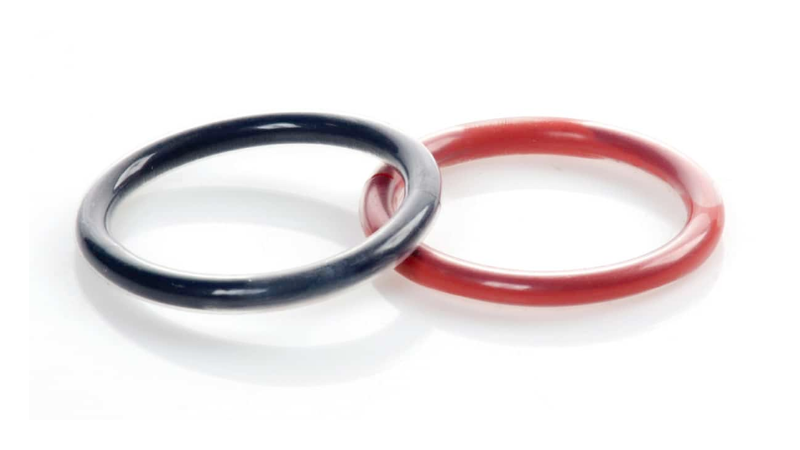
While FEP encapsulated O-rings offer numerous advantages, like any product, they come with a set of drawbacks that should be carefully considered. Here are some potential downsides:
- Limited Elastomeric Core Options: The range of elastomeric core materials that can be used in conjunction with FEP encapsulation is limited. Generally, it’s either silicone or Viton, restricting customization based on specific application needs.
- Compatibility Limitations: While FEP offers excellent chemical resistance, the core material may still be vulnerable to specific chemical attacks, possibly leading to premature seal failure.
- Not Ideal for Dynamic Sealing: Although they offer low friction, FEP-encapsulated O-rings might not be ideal for high-speed or highly dynamic applications due to their encapsulated nature.
- Compression Set: Despite having a relatively low compression set, some FEP-encapsulated O-rings may lose their sealing capability faster than exotic O-ring compounds when exposed to aggressive chemicals over extended periods.
Material Options for FEP Encapsulated O-Rings
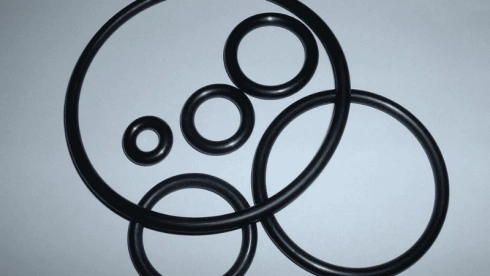
The core material for FEP-encapsulated O-rings is important. It makes the O-ring even better at resisting chemicals and handling high temperatures. Here’s a look at some of the most commonly used core materials for FEP-encapsulated O-rings:
- Temperature Versatility: Well-suited for a broad temperature range, making it ideal for fluctuating thermal conditions.
- Flexibility: Maintains excellent elasticity, ensuring a durable seal.
- Food-Safe: Commonly used in the food industry due to its non-reactive properties.
- Chemical Toughness: Exceptional resistance to an extensive array of chemicals, including acids and hydrocarbons.
- High-Temperature Endurance: Superior heat resistance, especially beneficial for industrial applications.
- Oil and Gas: Frequently employed in challenging oil and gas applications because of its resistance to hydrocarbons.
- Water Resilience: Highly effective against water and steam, making it suitable for hot water applications.
- Chemical Resistance: Good resistance to certain chemicals, although not as wide-ranging as Viton.
- Cold-Weather Performance: Exhibits good flexibility in low-temperature conditions.
Choosing the right core material for your FEP-encapsulated O-rings is crucial, as it significantly influences the O-ring’s performance.
Selecting the Right FEP Encapsulated O-Ring
Selecting the appropriate FEP-encapsulated O-ring involves a variety of factors, including the operating environment, material compatibility, and the specific needs of your application. Here are some guidelines to help you make the right choice:
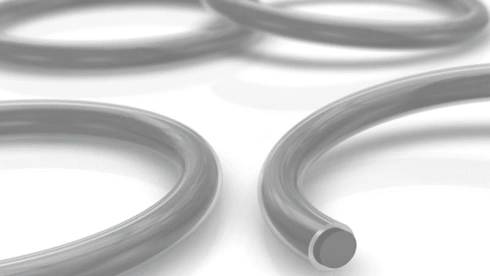
Assess Your Operating Environment
Take into account the extreme temperatures, aggressive chemicals, or corrosive fluids your O-rings might encounter. FEP-encapsulated O-rings have excellent chemical and temperature resistance, but the core material may also play a role in how well the O-rings perform under certain conditions.
Examine Material Compatibility
Different core materials like silicone or elastomeric cores offer distinct advantages. Consider the substances the O-ring will be exposed to, and make sure that both the core material and the FEP encapsulation are compatible with them to prevent a chemical attack or premature seal failure.
Consider the Size and Dimensions
Always refer to technical specifications for size options and tolerances. The right size is crucial for ensuring a reliable seal. Check for both standard and custom-size options that can meet your specific needs.
Evaluate the Supplier
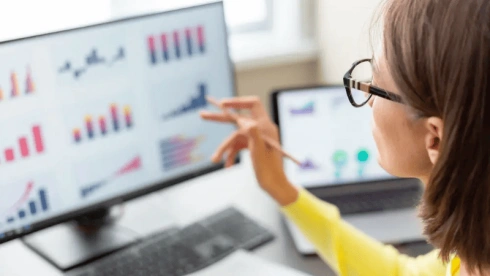
Opt for a supplier that offers first-class quality seals and has a reputation for reliability. They should be able to guide you through the selection process and offer products that comply with industry standards, especially if you’re in a regulated industry like food processing or medical applications.
Think About Cost vs. Longevity
Though FEP-encapsulated O-rings can be more expensive upfront compared to traditional O-rings, their durability and lower maintenance can result in cost savings over the long term.
Consult with Engineers and Experts
Before making a final decision, it may be beneficial to consult with in-house engineers or external experts who have experience with O-rings and their applications. This can offer valuable insights into which type of O-ring would be best suited for your operations.
Conclusion
In conclusion, FEP-encapsulated O-rings offer superior performance in demanding environments, providing excellent resistance to extreme temperatures and aggressive chemicals. By carefully assessing your operational needs and consulting with experts, you can select the right FEP-encapsulated O-ring that meets your specific requirements.
Get Reliable and Durable FEP-Encapsulated O-rings with Hongju
Unlock the Full Potential of Your Sealing Applications with Hongju’s FEP-Encapsulated O-rings. Don’t compromise on quality or durability; Choose Hongju for O-rings designed to withstand even the harshest conditions. Contact us today to find out how our FEP-encapsulated O-rings can elevate your project to the next level.
Take the First Step:
Requst for an Inquire
Quality Meets Affordability. Inquire Now for High-Quality Products at Low Volumes.