This comprehensive guide aims to enlighten you about dynamic seals – their functions, types, applications, and the essential factors to consider when selecting one.
Furthermore, we’ll guide you on how to maintain these seals for optimal performance and troubleshoot common issues that might arise.
So, whether you are a veteran engineer or a curious newbie in the field, this article will provide valuable insights into the world of dynamic seals.
What are Dynamic Seals?
Dynamic seals, also known as shaft seals or rod seals, play a crucial role in various industries by preventing leakage and maintaining the integrity of mechanical systems.
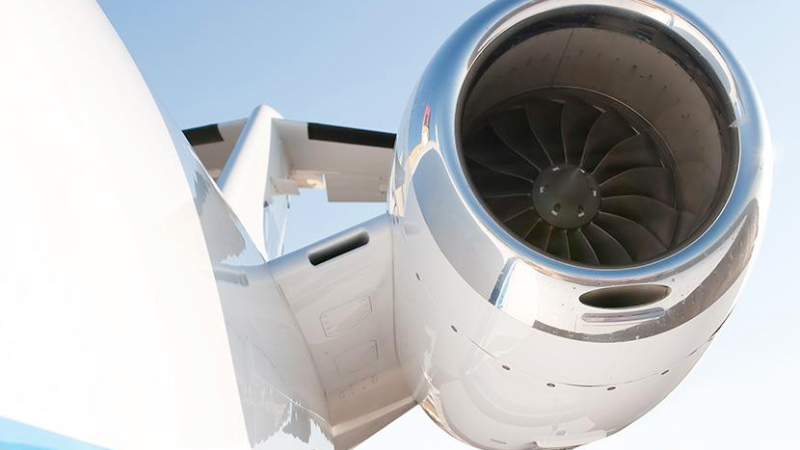
A dynamic seal is the generic term that refers to any seal that is fitted between two mating surfaces that move. Unlike static seals that remain stationary, dynamic seals are designed to accommodate movement between components.
Differentiating from static seals, which primarily serve to contain fluids under pressure when there is no relative motion between parts, dynamic seals are specifically engineered to withstand the continuous motion and friction generated by rotating or reciprocating shafts or rods.
Key characteristics of dynamic sealing include:
- Low friction: To minimize wear and energy loss, dynamic seals need to have low friction properties.
- Easy installation: The design of dynamic seals should facilitate easy installation and maintenance.
- High durability: Dynamic seals should be able to withstand constant movement without compromising their sealing capability.
- Effective containment: Dynamic seals must effectively contain fluids while allowing the required motion.
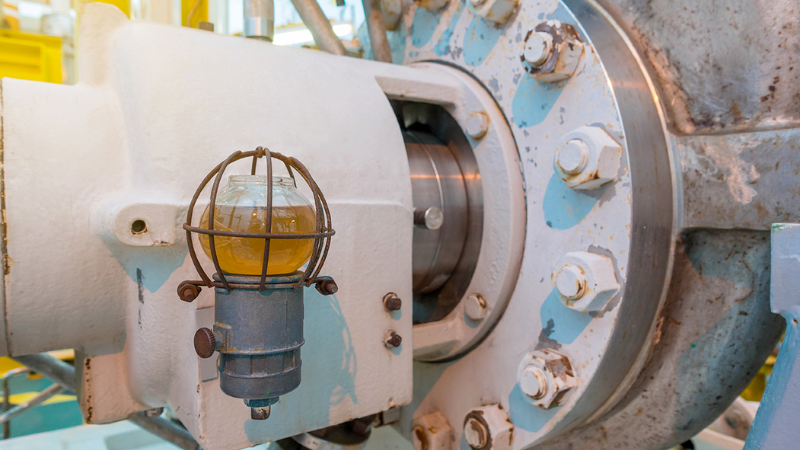
- Chemical compatibility: They must be resistant to the specific fluids they will come into contact with during operation.
- Temperature resistance: Dynamic seal materials should be able to handle a wide range of temperatures without degradation.
Materials for Dynamic Seals
Material selection is one of the most critical aspects of choosing dynamic seals. The material must withstand the conditions it will be exposed to without degrading or failing. Here are some common materials used for dynamic seals and their properties:
- Nitrile Rubber (NBR): NBR is a versatile material used in many dynamic seals due to its excellent resistance to oils, fuels, and other petroleum products. It also has good mechanical properties and can operate at temperatures between -40°C and 120°C.
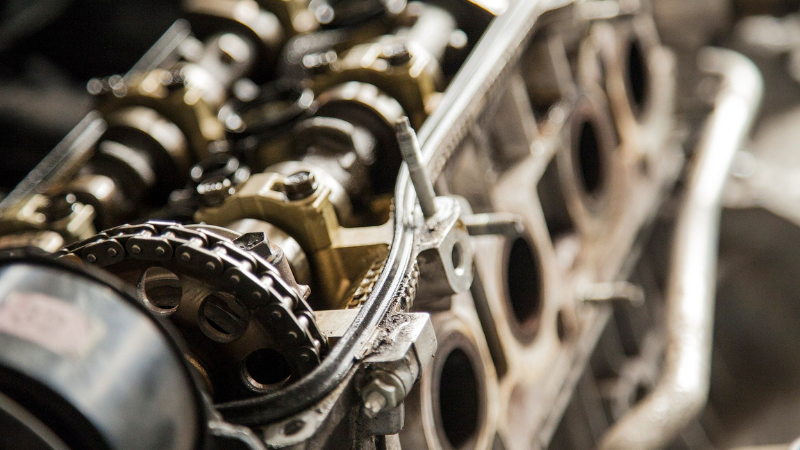
- Fluorocarbon (Viton or FKM): FKM is known for its superior heat resistance, up to 200°C, and its excellent chemical resistance, especially against hydrocarbons, oils, and acids. This makes it ideal for use in engines, transmission systems, and chemical processing equipment.
- Polytetrafluoroethylene (PTFE or Teflon): PTFE is a chemically inert material with a wide temperature range (-200°C to 260°C), making it suitable for extreme environments. It also offers low friction, which is beneficial in dynamic applications to reduce wear and heat generation.
- Ethylene Propylene Diene Monomer(EPDM): EPDM is used in dynamic seals for its excellent resistance to weather, ozone, and UV rays, as well as a wide range of chemicals. It has a temperature range of -50°C to 150°C.
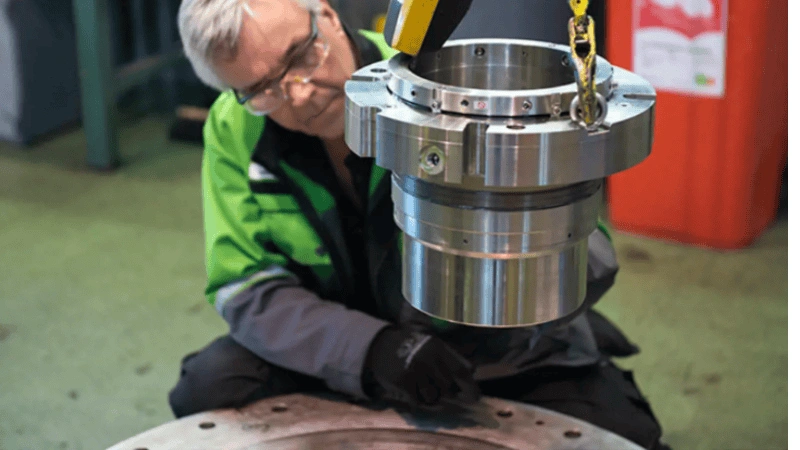
- Silicone: Silicone is a soft material that offers excellent flexibility and good temperature resistance (-60°C to 200°C). It’s commonly used in food and medical applications due to its excellent biocompatibility.
Each material has its strengths and limitations, and the choice should be based on the specific application’s requirements. When in doubt, consult with experts like the team at Hongju, who can provide guidance based on their extensive experience in the field.
Exploring Different Types of Dynamic Seals
Dynamic seals play a crucial role in ensuring the proper functioning and longevity of various types of machinery. Depending on the application, different dynamic seals are employed to tackle specific challenges. Here’s a detailed breakdown of the different types of dynamic seals:
- Pneumatic Seals: Designed specifically for air or gas applications, these seals prevent external contaminants from entering the system while maintaining internal pressure. Pneumatic seals are used in gaseous or air mediums. This may include rod seals, piston seals, flanges, and U-cups.
- Labyrinth Seals: also known as clearance seals, these seals function by maintaining a small clearance gap between the sealing surface and the mating surface. The tiny clearance inhibits the passage of fluid or gas, making them ideal for applications that need minimal friction.
- Piston Seals: Installed in cylinders, piston seals segregate the two pressure chambers on both sides of the piston. They are used to seal cylinders and ensure that fluid or gas does not pass the piston, enabling it to function effectively and ensuring optimal pressure balance.
- Grease Seals: These seals are crafted to retain lubrication within a bearing while stopping contaminants like dirt and dust from entering. They are common in automotive and industrial applications.
- Radial Seals: Radial seals function by sealing radially or perpendicular to the axis of the shaft. These seals are mainly used for rod or rotating shaft applications.
- Contact Seals: Directly contacting the surface they are sealing against, contact seals are designed to provide a barrier against fluid or gas leakage. They offer a higher sealing efficiency but may cause more friction compared to non-contact seals.
- Rotary Seals: Crafted for sealing rotating components, such as a shaft or rotating bore, rotary seals offer high resistance against wear and are vital for applications like motors and gearboxes.
- Exclusion Seals: The primary function of exclusion seals is to keep contaminants out. Whether it’s dirt, moisture, or other environmental elements, these seals ensure that contaminants are excluded from sensitive parts of the machinery.
Choosing the right dynamic seal involves understanding the specific requirements of the machinery and the challenges posed by the operational environment.
When selected and installed correctly, dynamic seals can dramatically improve the efficiency, safety, and lifespan of machinery across a wide range of industries.
Criteria for Selecting the Right Dynamic Seals
Choosing the right dynamic seal type involves several important considerations. Here are some factors to keep in mind when making your selection:
- Compatibility with operating conditions: It is crucial to ensure that the dynamic seal can withstand the temperature and pressure conditions it will be exposed to. This compatibility ensures optimal performance and prevents any potential damage or leakage.
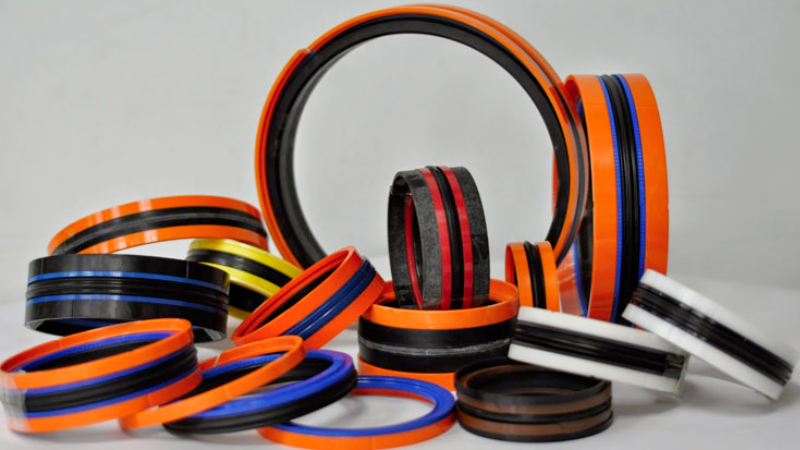
- Fluid compatibility and chemical resistance: Different seals are designed to work with specific fluids and chemicals. Consider the compatibility of the seal material with the fluid it will be in contact with, as well as its resistance to any chemicals present in the system.
- Cost-effectiveness versus performance requirements: Balancing cost-effectiveness with performance requirements is essential. While it may be tempting to opt for a cheaper option, it’s important to consider if it meets all the necessary specifications. A higher-performing seal may save costs in the long run by minimizing maintenance and downtime.
By carefully considering these criteria, you can select a dynamic seal that best suits your specific application needs.
Remember, finding a seal that is compatible with operating conditions, fluids, and chemicals while also meeting performance requirements will help ensure efficient operation and minimize potential issues down the line.
Enhancing Machinery Reliability with Dynamic Seals
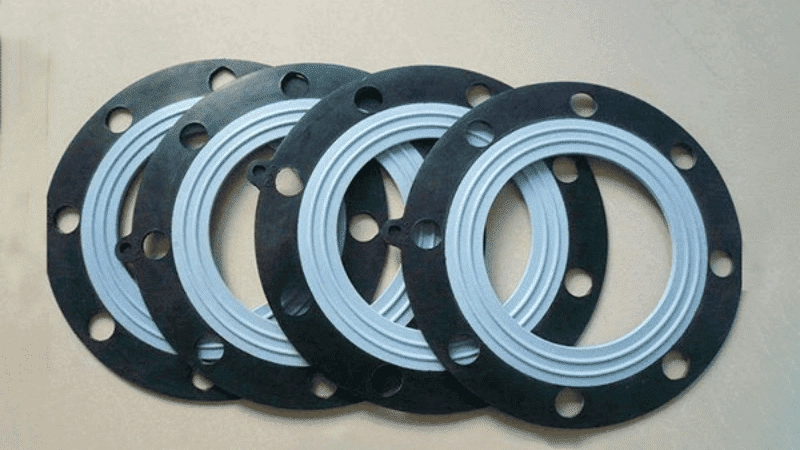
Proper maintenance is crucial for extending the lifespan of dynamic seals. Regular inspections play a significant role in detecting potential issues early on, preventing costly breakdowns and downtime.
By utilizing advanced technologies like condition monitoring systems, proactive maintenance strategies can be implemented to ensure optimal performance.
Here are some key points to consider:
- Maintenance: Implementing regular maintenance practices can significantly extend the lifespan of mechanical seals. Proper lubrication, inspection, and cleaning are essential for maximizing their efficiency.
- Inspections: Regular inspections allow for the timely detection of wear and tear, leaks, or other potential issues affecting dynamic seals. This enables prompt repairs or replacements before they escalate into major problems.
- Technological Advancements: Condition monitoring systems provide real-time data on the health of dynamic seals. By continuously monitoring factors such as temperature, pressure, and vibration levels, these systems enable early identification of abnormalities and facilitate predictive maintenance.
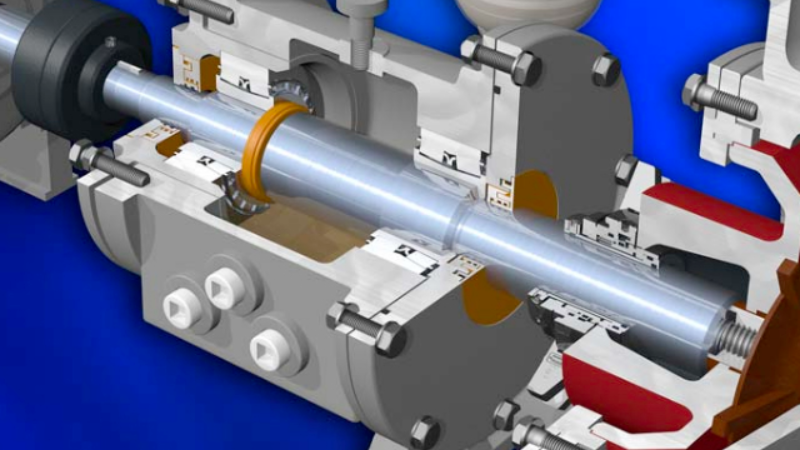
Case Studies
Several case studies demonstrate how the optimized use of dynamic seals has improved machinery reliability. For instance:
1. Automotive Production Line Efficiency Boost
A leading car manufacturer faced recurring downtime due to the leakage of hydraulic fluid from their robotic assembly arms. After a thorough investigation, it was discovered that the original dynamic seals used were degrading faster due to heat and continuous movement.
By switching to a custom-designed dynamic seal from Hongju, tailored for their specific operating conditions, the manufacturer noticed a 75% reduction in downtime over a year and improved overall production efficiency.
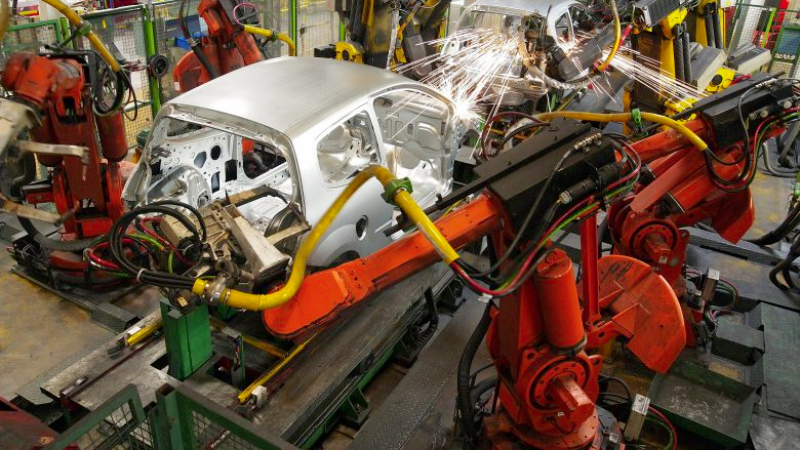
2. Pharmaceutical Liquid Filling System Upgrade
A renowned pharmaceutical company was dealing with contamination issues in its liquid filling machines. The problem originated from worn-out dynamic seals that allowed air to infiltrate the system.
After replacing the older seals with advanced dynamic seals with better material compatibility and design, the company reported zero contamination issues for the subsequent two years, ensuring consistent medication quality.
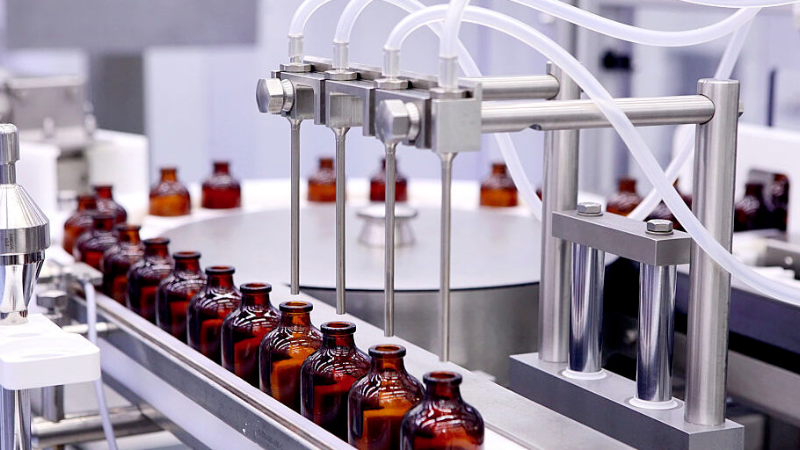
3. Water Treatment Plant Efficiency
A municipal water treatment facility was experiencing issues with its centrifugal pumps, leading to reduced water flow rates.
The culprit was identified as worn dynamic seals that were not tailored for continuous use in a challenging environment. After retrofitting their pumps with specialized dynamic seals from Hongju, the plant witnessed a 20% increase in water flow rates and extended pump service life.
Enhancing machinery reliability relies heavily on maintaining dynamic seals effectively.
Through proper maintenance practices, regular inspections, utilization of advanced technologies like condition monitoring systems, and learning from successful case studies within different industries, businesses can optimize their use of dynamic seals and achieve reliable machinery performance.
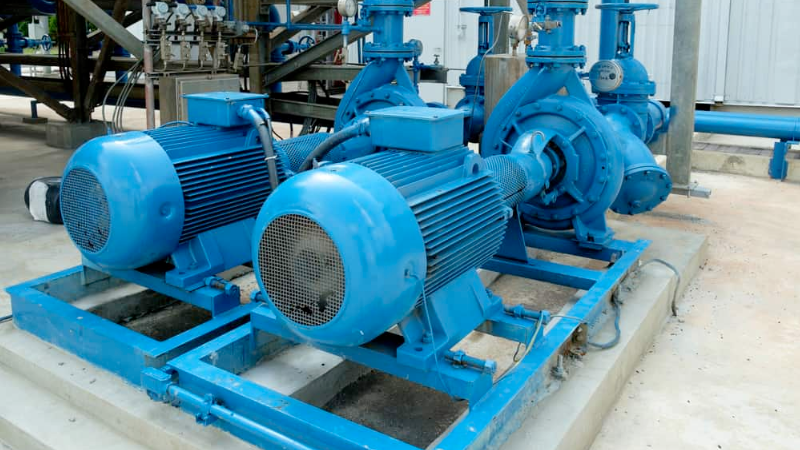
How to Improve the Lifespan of Dynamic Seals?
Dynamic seals play a critical role in various applications, so it’s paramount to ensure their longevity. Here are some tips to improve the lifespan of dynamic seals:
- Correct Installation: Proper installation is key to the seal’s performance and lifespan. If not installed correctly, a seal can fail prematurely. It’s important to follow the manufacturer‘s guidelines during installation and ensure that the seal is not twisted, stretched excessively, or damaged.
- Right Material Selection: Choosing the appropriate material for the application can drastically increase the seal’s lifespan. The material should be able to withstand the operating temperature, pressure, and any chemicals it may come in contact with.
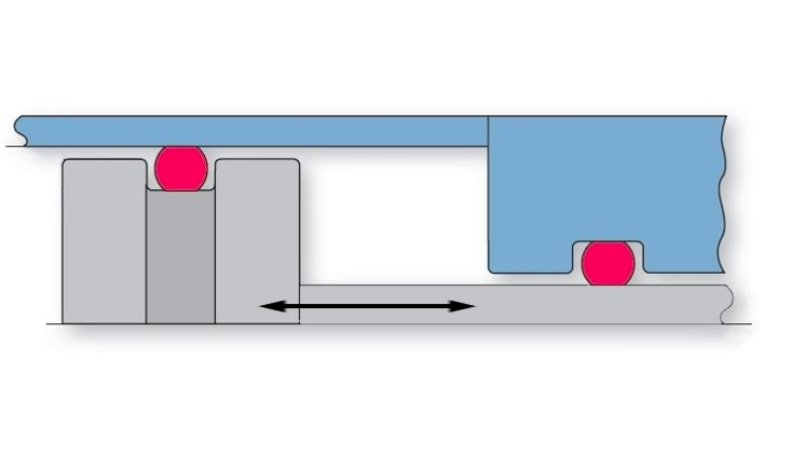
- Regular Inspection and Maintenance: Regular inspections can identify potential issues before they lead to seal failure. Look for signs of wear, deformation, or damage. Routine maintenance can also extend the seal’s life. This may involve cleaning, lubrication, and occasionally, replacement of worn-out parts.
- Proper Lubrication: In dynamic applications, lubrication can reduce friction, prevent wear and tear, and therefore extend the seal’s life. Use a lubricant compatible with the seal material and the operating environment.
- Environmental Control: External factors such as dust, dirt, and harsh weather conditions can accelerate seal wear. Where possible, use shields or covers to protect the seals from these elements.
- Optimal Design: The design of the seal and its housing can have a significant impact on the seal’s lifespan. It should allow for uniform pressure distribution, minimize friction, and have appropriate surface finishes.
By following these guidelines, the life expectancy of dynamic seals can be greatly extended, resulting in less downtime, lower maintenance costs, and improved reliability of your machinery.
As always, consulting with a sealing specialist like Hongju can provide further insights tailored to your specific application needs.
Final Words
Understanding dynamic seals is an essential part of maintaining and enhancing the efficiency of your machinery. From their diverse types and applications to the materials used and tips on extending their lifespan, these small but critical components play a pivotal role in the smooth operation of a wide variety of industrial equipment.
Partnering with Hongju for Dynamic Seals
At Hongju Silicone, we recognize the importance of reliable dynamic seals and are committed to providing high-quality sealing solutions tailored to meet the unique demands of your applications.
We combine state-of-the-art technology, innovative design, and top-notch materials to create dynamic seals that deliver optimal performance, durability, and longevity. Contact us today to find the right seal for your application. We would love to learn more about you and your project and make a new friend at the same time.
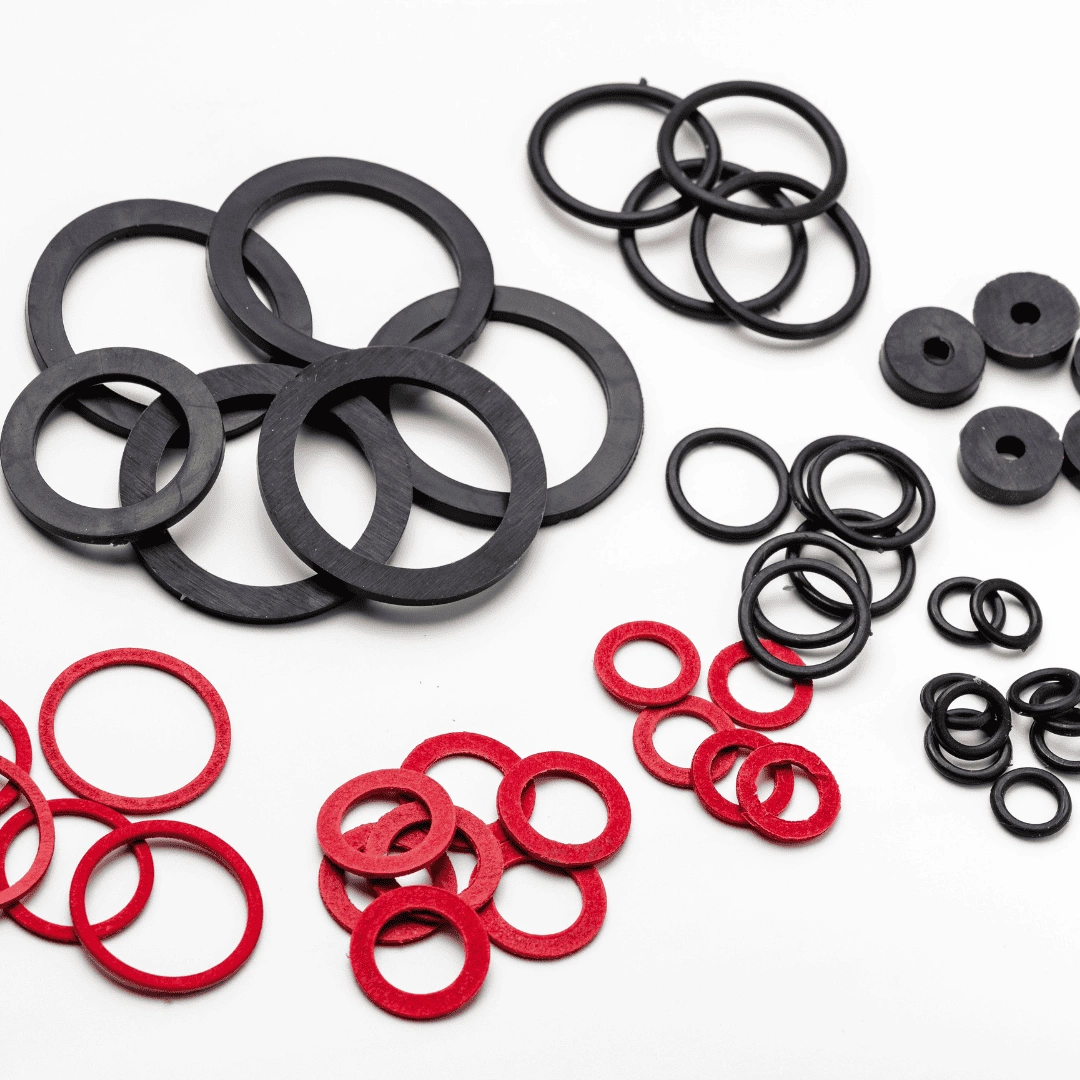
Send Your Inquiry Now!
Quality Meets Affordability. Inquire Now for High-Quality Products at Low Volumes.