From consumer electronics to high-end medical devices, the emphasis on creating a responsive and reliable keypad has never been more paramount. As we dive deeper into this article, we’ll unravel the intricate design elements that make silicone keypads a preferred choice, ensuring both functional excellence and optimal user experience.
What are Silicone Rubber Keypads?
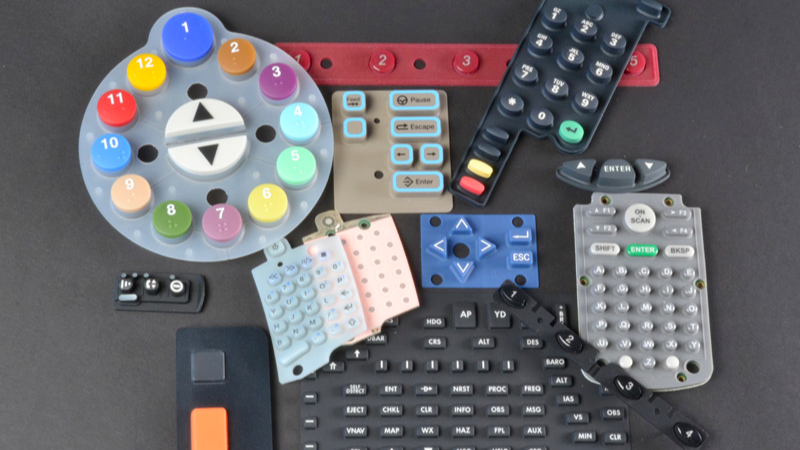
Silicone rubber keypads, also known as silicone keypads or rubber keypads, are a type of keypad made from silicone rubber material. These keypads are commonly used in various industries and applications due to their unique design elements and advantages.
Definition and Basic Structure of Silicone Rubber Keypads
Silicone rubber keypads consist of multiple buttons or keys that are molded from silicone rubber. The keypad is typically designed with a base layer made of silicone material which provides flexibility and durability. On top of the base layer, there is a conductive pill or dome made from carbon or gold material. This dome acts as a switch when pressed, allowing electrical contact to occur.
A distinctive trait of these keypads lies in their tactile feel, which is determined by a combination of design features. Four major features found in rubber keypads, including the contact force and Snap Ratio, play a critical role in determining the tactile response of the finished product.
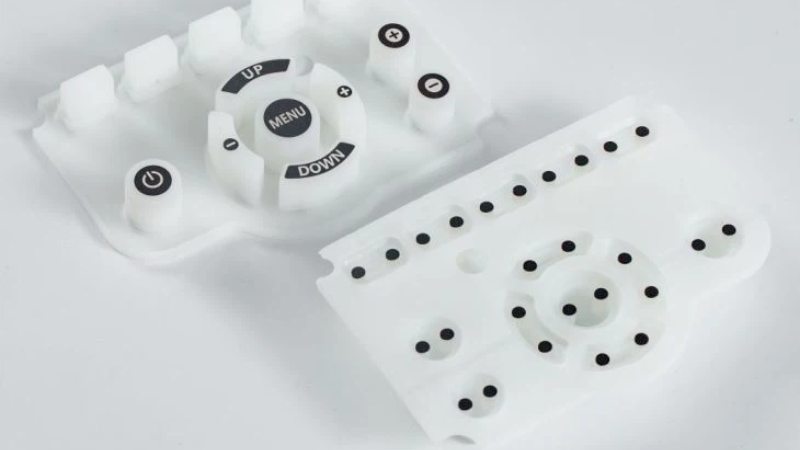
Specifically, the actuation force (the force needed to depress a key), key travel (the distance the key moves), contact force (the force at the point of contact), and return force (the force with which the key returns to its original position) all interact to produce a specific tactile response. The Snap Ratio, emerging as a key element from this combination, offers insights into the feel and feedback of the keypad, ensuring that users can confidently press keys even without looking.
Advantages of Using Silicone Rubber Material for Keypads
Silicone rubber material offers several advantages when used for keypads:
- Durability: Silicone rubber is highly resistant to wear and tear, making it suitable for long-lasting applications.
- Flexibility: The inherent flexibility of silicone allows the keypad to conform to different shapes and designs.
- Water resistance: Silicone has excellent water resistance properties, protecting the keypad from moisture damage.
- Temperature tolerance: Silicone can withstand extreme temperatures without losing its functionality.
- Chemical resistance: Silicone is resistant to chemicals such as oils, solvents, and cleaning agents commonly found in industrial environments.
These advantages make silicone rubber an ideal choice for applications where durability, flexibility, and reliability are crucial factors.
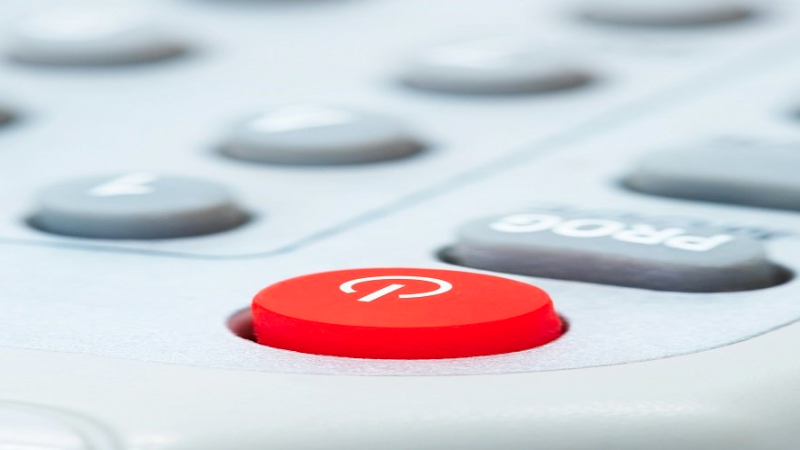
Common Applications and Industries that Utilize Silicone Keypads
Silicone keypads find application in various industries due to their versatility:
- Consumer electronics: Remote controls, calculators, gaming controllers
- Automotive industry: Car key fobs, dashboard controls
- Medical devices: Hospital equipment, diagnostic tools
- Industrial equipment: Control panels, machinery interfaces
The ability to customize the design and appearance of silicone keypads makes them suitable for a wide range of applications.
Key Design Elements for Silicone Keypads
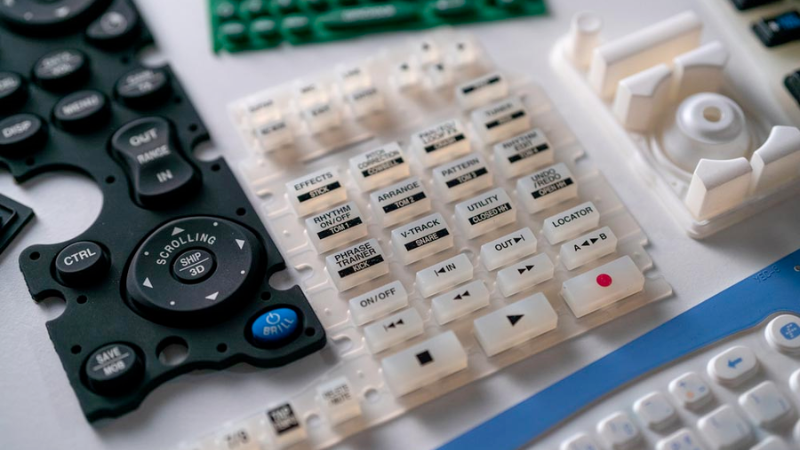
Designing a silicone rubber keypad requires a delicate balance of functionality, user experience, and aesthetic appeal. Here are some crucial elements to consider when mapping out your keypad design:
Importance of Tactile Feedback in Keypad Design
Tactile feedback is a crucial aspect of silicone keypad design as it enhances the user experience and ensures accurate input. When users press a key, they expect to feel a certain level of resistance and responsiveness. This feedback not only confirms that the button has been pressed but also provides a satisfying tactile feel.
To achieve optimal tactile feedback, designers must consider factors such as key travel and actuation force. Key travel refers to the distance a key travels when pressed, while actuation force is the pressure required to activate the switch. By carefully selecting these parameters, designers can create buttons that offer just the right amount of resistance and clickiness.
Considerations for Button Shape, Size, and Layout
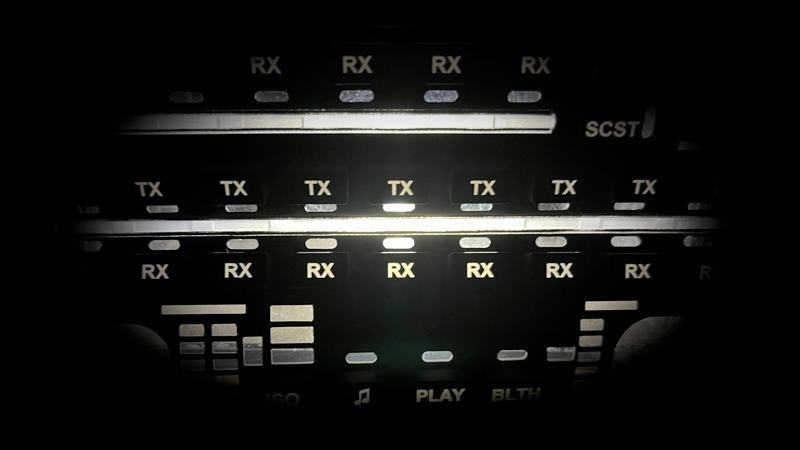
The shape, size, and layout of the buttons play a significant role in silicone keypad design. Buttons should be ergonomically designed to ensure comfortable usage over extended periods. They should be easy to locate by touch alone and allow for precise finger placement.
Designers must also consider the overall layout of the keys on the keypad. The arrangement should be intuitive and logical, minimizing errors caused by accidental presses or difficulty in locating specific buttons quickly.
Here are some examples:
- Rounded or contoured button shapes provide better tactile feedback.
- Concave or domed tops help fingers rest comfortably on keys.
- Different sizes or textures can differentiate frequently used buttons from others.
- Raised edges around each button prevent accidental presses.
Integration of Backlighting Options in Keypad Design
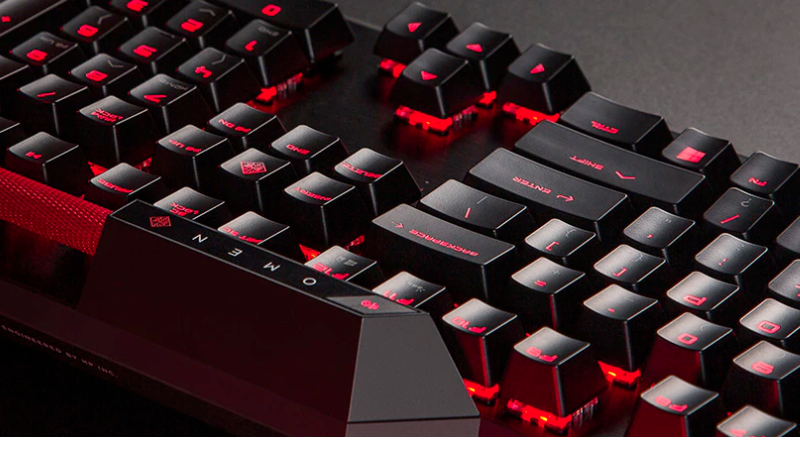
Backlighting options add visual appeal and improve usability in low-light conditions. Incorporating backlighting into silicone keypads allows users to easily identify buttons even when there is limited ambient lighting.
There are various backlighting techniques available:
- LED backlighting: Light-emitting diodes (LEDs) placed beneath each button provide uniform illumination.
- Fiber optic backlighting: Light is transmitted through fiber optic cables to illuminate the buttons.
- Electroluminescent(EL) backlighting: A thin, flexible layer of EL material is placed behind the keys to emit light.
By selecting the appropriate backlighting option, designers can enhance the aesthetics and functionality of silicone keypads.
Selection of Appropriate Contact Mechanisms for Reliable Performance
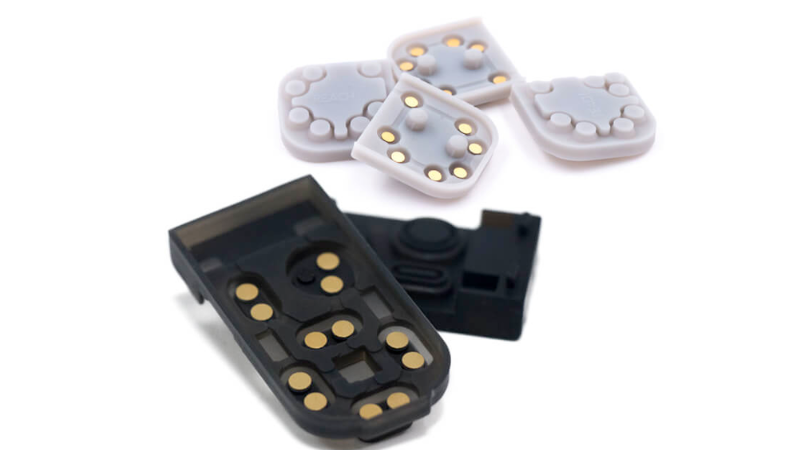
The contact mechanism between the button and underlying circuitry greatly influences the reliability and longevity of a silicone keypad. There are several options available, each with its own advantages:
- Carbon pills: Small carbon-filled rubber pills act as conductive elements when pressed, completing an electrical circuit.
- Conductive rubber: Buttons made from conductive rubber provide consistent electrical contact when pressed.
- Metal domes: Dome-shaped metal discs beneath each button offer tactile feedback and ensure reliable electrical connections.
Designers must carefully evaluate the requirements of their application to choose the most suitable contact mechanism for optimal performance and durability.
Silicone Rubber Keypad Design Guide
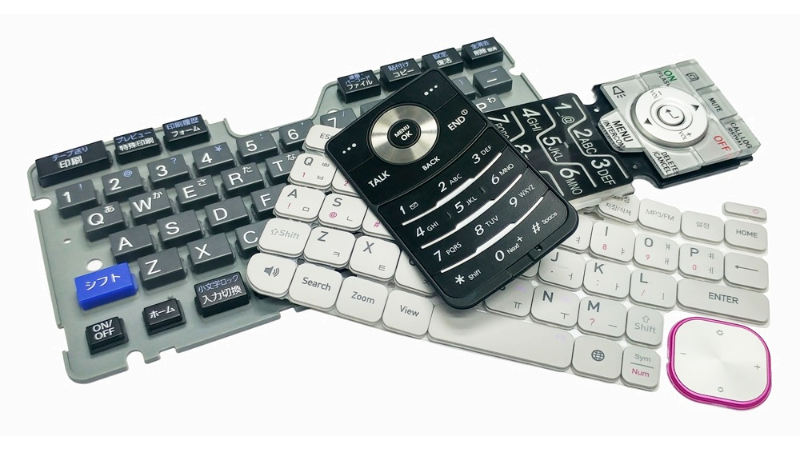
In silicone rubber keypad design, button webbing, button travel, and clearance between the silicone keys with plastic covers all these elements should be taken into account. This step-by-step guide will walk you through the key design elements to ensure a successful outcome.
Factors to Consider During the Design Process
When designing a silicone rubber keypad, it is crucial to take into account the specific environmental conditions in which it will be used. Factors such as temperature extremes, moisture exposure, and chemical resistance can significantly impact the performance and durability of the keypad. Understanding the user requirements is essential for creating an ergonomic and intuitive design.
To address these considerations effectively, follow these steps:
- Environmental Conditions: Determine the temperature range and potential exposure to moisture or chemicals that your silicone keypad may encounter. This information will help you select appropriate materials with suitable properties.
- User Requirements: Understand how users will interact with the keypad. Consider factors like button size, shape, and layout for ease of use and comfort during operation.
Selecting Materials and Manufacturing Techniques
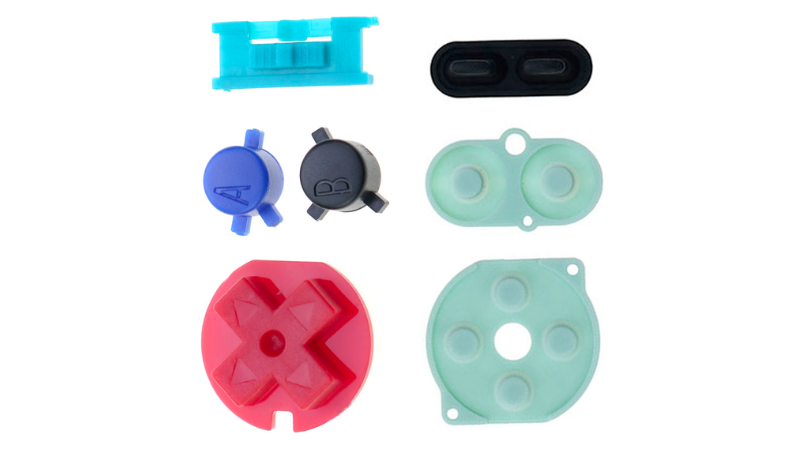
Choosing the right materials is critical for achieving desired outcomes in terms of functionality, durability, and aesthetics. Silicone rubber keypads offer excellent tactile feedback and long-lasting performance. When selecting materials, keep in mind their compatibility with your chosen manufacturing techniques.
Consider these tips when choosing materials:
- Use medical-grade silicone for applications requiring biocompatibility.
- Opt for conductive silicone if your design requires electrical conductivity.
- Choose translucent or pigmented silicone based on aesthetic preferences.
- Consider using laser etching or pad printing techniques for custom labeling options.
Testing and Validation Methods
To ensure the quality and durability of your silicone rubber keypad design, testing and validation are crucial steps in the process. These methods help identify any potential issues early on before production begins.
Here are some commonly used testing methods:
- Tactile Feedback Testing: Evaluate the responsiveness of buttons by conducting force-displacement tests to ensure the desired tactile feel.
- Environmental Testing: Subject the keypad to extreme temperatures, humidity, and chemical exposure to assess its resistance and performance under different conditions.
- Life Cycle Testing: Simulate real-world usage by repeatedly pressing buttons to evaluate their durability over time.
- Electrical Performance Testing: Verify electrical conductivity and contact resistance of conductive silicone keypads using appropriate testing equipment.
By incorporating these testing methods into your design process, you can identify any potential issues early on and make necessary adjustments before moving forward with production.
Optimizing Dimensions and Layout for Silicone Keypads
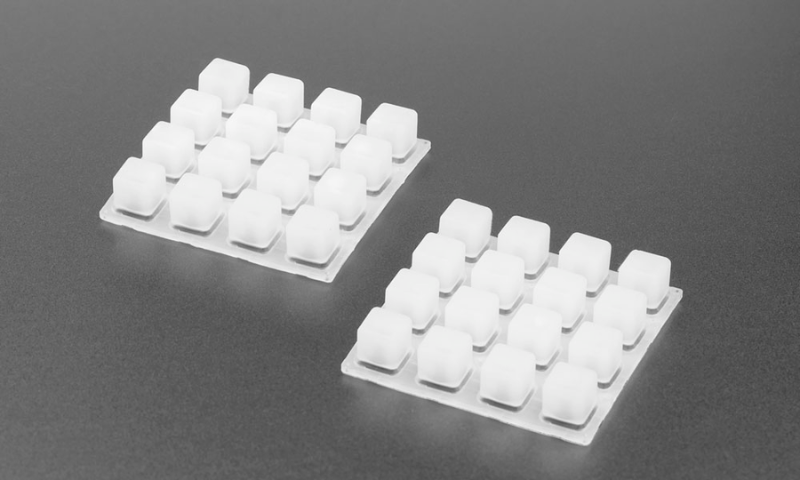
Determining the optimal dimensions and layout for silicone keypads is crucial in ensuring a user-friendly experience. By following ergonomic guidelines, arranging buttons intuitively, and balancing space constraints with functionality requirements, manufacturers can create silicone keypads that are both comfortable to use and efficient.
Guidelines on determining optimal button dimensions based on ergonomic considerations
Considering ergonomic factors is paramount. The dimensions of the buttons play a significant role in ensuring user comfort and ease of operation. Here are some guidelines to follow:
- Button size: Buttons that are too small may lead to accidental presses, while oversized buttons can cause discomfort during extended use. Striking the right balance between these extremes is essential.
- Button height: The height of the buttons should be carefully considered to provide adequate tactile feedback without requiring excessive force from the user.
- Button shape: Besides size and height, the shape of the buttons also affects usability. Rounded edges or slightly concave surfaces can enhance precision while minimizing accidental presses.
By adhering to these guidelines, manufacturers can optimize button dimensions to meet ergonomic requirements effectively.
Arranging buttons in an intuitive layout to enhance user experience
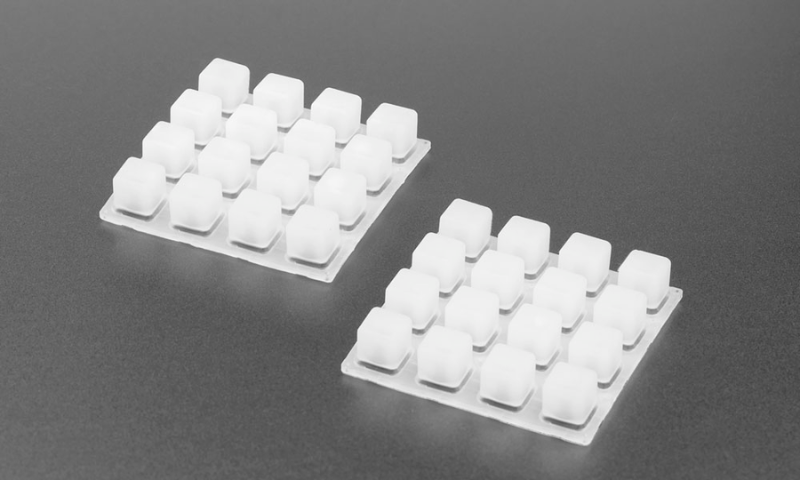
In addition to optimizing button dimensions, arranging them in an intuitive layout significantly improves the overall user experience. Considerations include:
- Grouping related functions: Placing buttons with similar functions together allows users to locate them easily and reduces confusion.
- Logical flow: Organizing buttons in a way that follows a logical sequence enhances usability. For example, placing navigation controls close together or positioning frequently used functions within easy reach.
- Visual cues: Incorporating visual cues such as color coding or icons help users quickly identify different button functionalities.
A well-designed layout of the keyboard ensures that users can operate silicone keypads effortlessly and intuitively.
Balancing space constraints with functionality requirements
While optimizing dimensions and layout, it is crucial to balance space constraints with functionality requirements. Here’s how:
- Prioritizing essential functions: Identify the core functionalities that need to be easily accessible and ensure sufficient space allocation for these buttons.
- Streamlining design: Minimize unnecessary buttons or combine functions where possible to reduce the overall footprint without compromising usability.
- Consideration for external components: Take into account the printed circuit board (PCB) or other electronic components that will interface with the silicone keypad, ensuring proper alignment and integration.
By striking a balance between available space and required functionalities, manufacturers can create compact yet functional silicone keypads.
Installation Tips – How to Install A Silicone Keypad Correctly
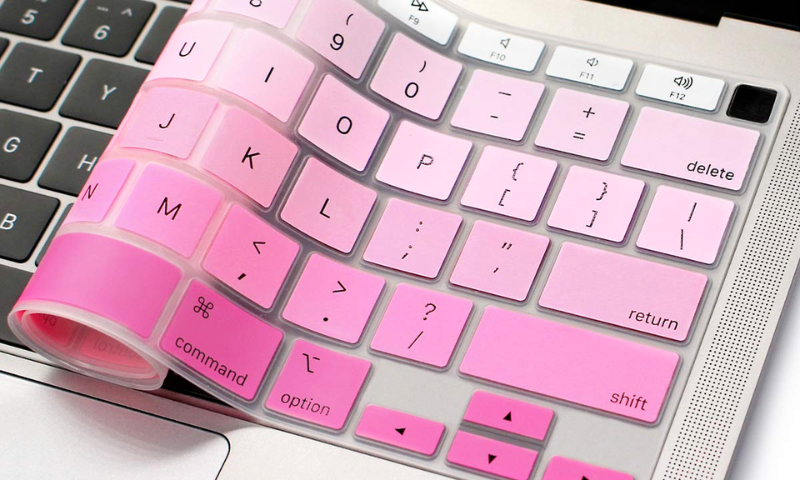
Installing a silicone keypad onto a device or control panel requires careful attention to detail and proper techniques. By following these step-by-step instructions, you can ensure a successful installation that maximizes the performance of your keypad.
Adhesive Selection and Application Techniques
Choosing the right adhesive is crucial for securely attaching the silicone keypad to your device. Look for adhesives that are specifically designed for bonding silicone materials. These adhesives provide excellent adhesion while maintaining flexibility.
When applying the adhesive, make sure to clean both the keypad and the surface it will be attached to. Remove any dust, dirt, or grease using a mild detergent solution or rubbing alcohol. This ensures optimal bonding between the surfaces.
Apply a thin layer of adhesive evenly on both the backside of the keypad and the designated area on your device. Avoid using excessive amounts of adhesive as it may cause unwanted bulges or unevenness in the final installation.
Proper Alignment and Positioning
Proper alignment and positioning of the silicone keypad are essential for its functionality. Before attaching the keypad, carefully align it with any existing buttons or openings on your device. This ensures that all functions can be easily accessed without any obstruction.
To achieve accurate alignment, consider using alignment guides or markers during installation. These can be temporary markings made with a non-permanent pen or tape placed strategically on both the keypad and the device. They serve as visual references to ensure precise placement.
Precautions During Installation
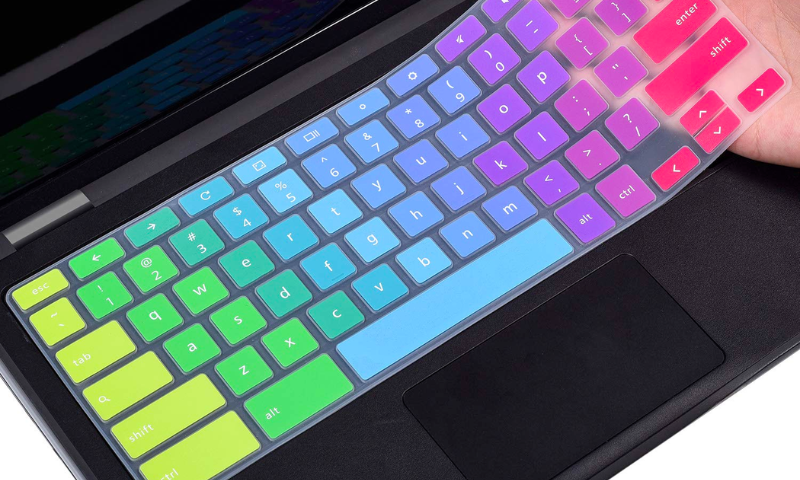
While installing a silicone keypad, it’s important to take precautions to avoid damaging it:
- Handle with care: Silicone keypads are sensitive to sharp objects and excessive force. Handle them gently throughout the installation process.
- Avoid stretching: Do not stretch or pull on the silicone material excessively as it may lead to deformation or tearing.
- Temperature considerations: Ensure that both the keypad and device are at room temperature during installation. Extreme temperatures can affect the adhesive’s performance.
- Gradual pressure application: Apply even pressure across the entire keypad to ensure proper bonding without causing any damage.
By following these precautions, you can minimize the risk of damaging your silicone keypad and prolong its lifespan.
Conclusion
The design intricacies of a silicone rubber keypad are paramount to its efficacy and user satisfaction. Beyond mere functionality, these keypads represent the interface between the user and the device, dictating the quality of interaction and overall impression. By prioritizing tactile feedback, aesthetics, accessibility, and durability, manufacturers can ensure their keypads stand the test of time and use.
Explore Excellent Silicone Rubber Keypad Design with Hongju
Unlock the full potential of your electronic devices with HongJu‘s meticulously crafted silicone rubber keypad. With our attention to detail and focus on user experience, we ensure each design stands out. Embark on a journey of innovation and precision with us.
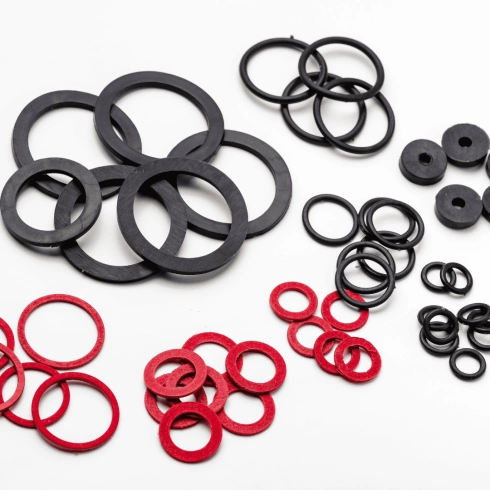
Send Your Inquiry Now!
Quality Meets Affordability. Inquire Now for High-Quality Products at Low Volumes.