So, in this guide, we’ll clarify everything you need to know about chemical-resistant O rings. By the end, you can effortlessly choose the perfect static seal for your specific applications.
Understanding Chemical Resistance
Chemical resistance is a material’s ability to withstand exposure to specific chemicals or substances without significant degradation, damage, or changes in chemical properties.
This means the material will retain its structural integrity, mechanical properties, and functionality even after contact with a substance like acid, petroleum base, solvent, fuel, mineral oil, or any other corrosive fluid or gas.
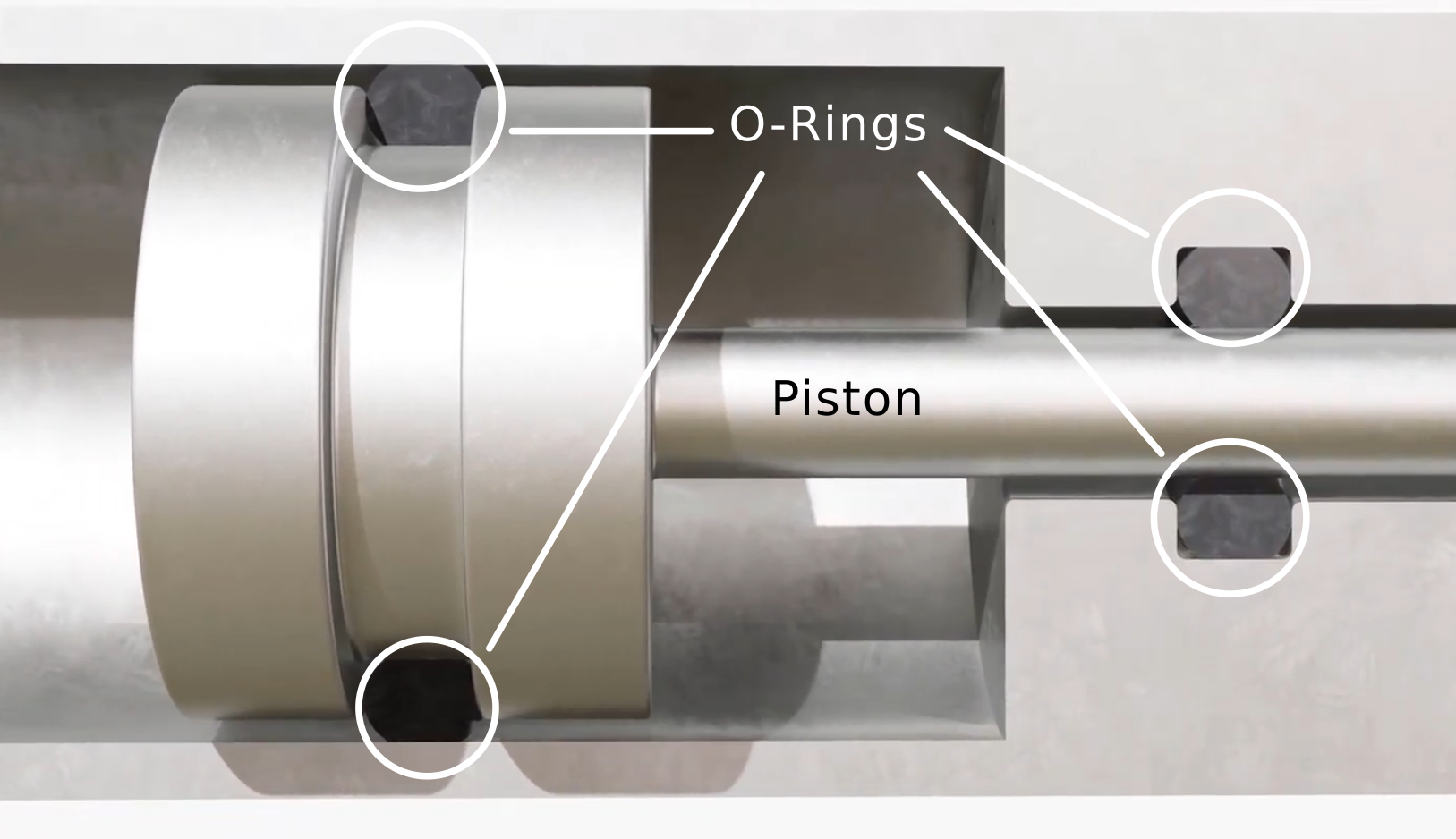
A compound with suitable chemical resistance can essentially prevent equipment failure, safety hazards, and costly downtime. For example, you’re often exposed to aggressive chemicals in a sector like pharmaceuticals, oil and gas, and manufacturing.
So, you must find reliable and specific parts resistant to particular materials. The molecular structure, surrounding temperature, chemical concentration, and exposure rating influence chemical resistance.
Chemical-resistant rubber rings, made from specialized compounds like Viton, EPDM, and PTFE, offer unique resistance properties that can be utilized in different situations. In the following sections, we will learn about the usage and effectiveness of different rings exposed to different chemical conditions.
Why is Chemical Resistance Important for O-rings
1. Maintains Seal Integrity:
O-rings are designed to create a tight seal between two surfaces to prevent the leakage of liquids or gases. Oxygen cylinders, LPG gas bottles, If the O-ring material is not chemically resistant, exposure to aggressive chemicals can cause the O-ring to swell, crack, or degrade.
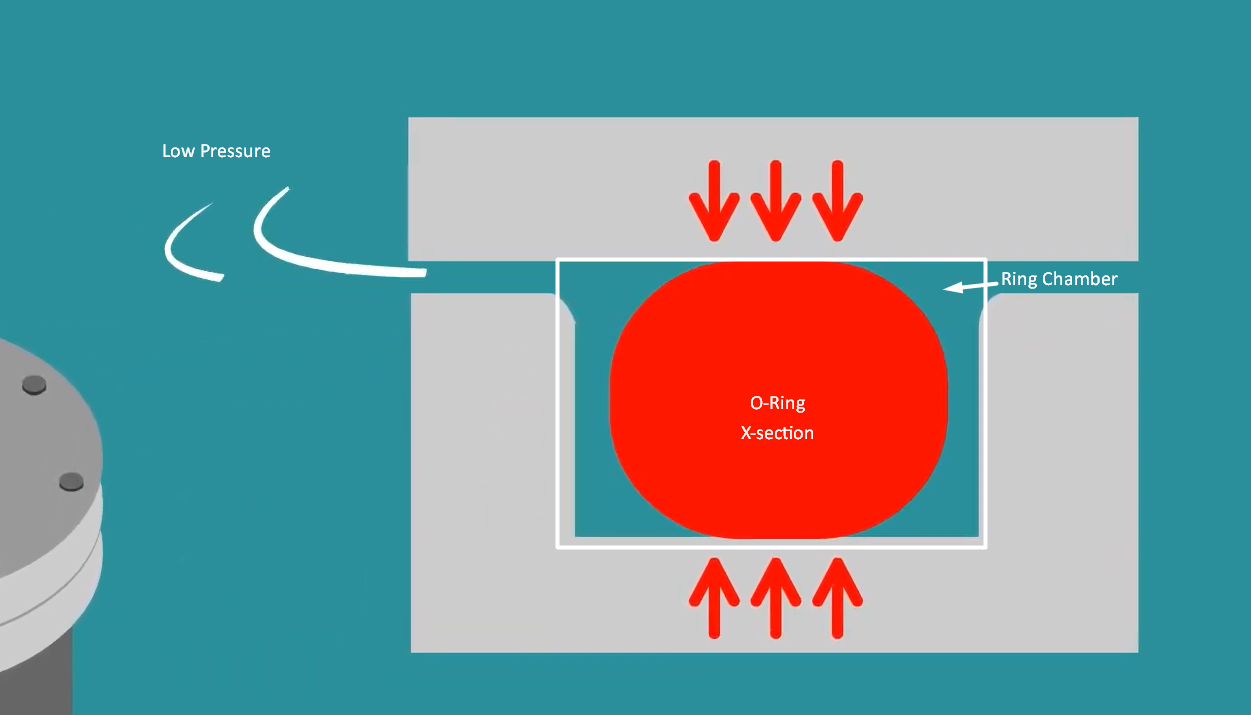
This compromise in the material integrity can lead to seal failure, resulting in leaks that can cause system malfunction, contamination, or safety hazards.
2. Ensures Longevity and Durability:
Chemically resistant O-rings can withstand prolonged exposure to harsh substances without significant wear and tear. Such durability reduces the frequency of maintenance and replacement.
On the other hand, non-resistant materials may degrade quickly and need frequent replacements that increase downtime.
3. Prevents Contamination:
Chemically resistant O-rings prevent product contamination in applications where purity is critical (e.g., food processing, pharmaceuticals, and medical devices).
Degraded O-ring materials can leach into the liquid substances they are meant to contain. These degradations often lead to contamination and compromise product safety and quality.
4. Enhances Safety:
O-rings used in cases involving hazardous chemicals (such as acids, solvents, and fuels) must resist chemical attacks to maintain a safe operating environment. Failure of an O-ring in such settings can release toxic or flammable substances that pose significant safety risks to personnel and the environment.
5. Ensures Compatibility with Operating Conditions:
Different scenarios require O-rings to operate under various conditions, including varying temperatures, pressures, and chemical exposures.
Chemical resistance ensures that the O-ring material remains stable and effective across the specific conditions of a given application. For example, Viton (FKM) is chosen for its excellent resistance to oil substances and solvents, making it suitable for automotive and aerospace environments.
6. Supports Regulatory Compliance:
Industries are often subject to regulations regarding material compatibility and chemical resistance. Chemically resistant rubber rings help companies comply with these regulations.
7. Minimizes Maintenance and Downtime:
Chemically resistant O-rings require less frequent inspection, maintenance, and replacement. This reliability minimizes system downtime.
Top Factors Affecting Chemical Resistance
Type of Material
Different materials have varying chemical structures that influence their resistance to different chemicals. For example:
PTFE (Teflon)
Known for its outstanding chemical resistance across various chemicals, including strong acids, solvents, and bases. Produced by the polymerization of TFE monomer, its non-reactive nature makes it suitable for harsh chemical environments. These rings are believed to be one of the best rings out there.
Nitrile (Buna-N)
It offers good resistance to oil compounds, fuels, and certain hydraulic fluids but has poor resistance to aromatic hydrocarbons, ketones, and chlorinated solvents. It is not recommended with MEK (Methyl ethyl ketone). Lubricating them with silicone-based grease is a good practice that protects the rings from abrasion within the section.
Concentration of Chemical
The concentration of the chemical can significantly impact the material’s resistance. Higher concentrations may lead to faster or more severe degradation.
Ethanol at a low concentration may be less aggressive towards certain elastomers than at higher concentrations. EPDM, for instance, can handle ethanol up to certain limits but may degrade faster at higher ethanol concentrations.
Duration of Exposure
Prolonged exposure to chemicals can lead to cumulative damage, even if the ring initially resists the chemical.
Short-term exposure to sulfuric acid may have little immediate effect on Viton (FKM) seals. However, long-term exposure can lead to gradual deterioration.
Environmental Conditions
Temperature, pressure, and other environmental factors (e.g., UV light, humidity) can influence a substance’s chemical resistance.
Temperature
Elevated temperatures can accelerate chemical reactions and degradation processes. For instance, EPDM may show reduced resistance to certain chemicals at higher temperatures.
Pressure
High pressures can increase the rate at which chemicals penetrate materials, potentially leading to faster degradation. Materials like Neoprene may handle moderate pressures well but may degrade under high-pressure conditions combined with certain chemicals.
UV Light and Humidity
UV light can cause certain materials to become brittle, and humidity can lead to hydrolysis in susceptible materials. Silicone, for example, may degrade faster when exposed to UV light despite its excellent heat resistance.
Chemical Compatibility of O-Ring Materials
Here’s a detailed table showing the compatibility of various O-ring materials with different chemicals. This table includes common materials such as Nitrile (Buna-N), EPDM, Viton (FKM), Silicone, Neoprene, and PTFE (Teflon).
Chemical | Nitrile (Buna-N) | EPDM | Viton (FKM) | Silicone | Neoprene | PTFE (Teflon) |
---|
Notes on Material Compatibility:
- Nitrile (Buna-N): Good for oil substances and fuels. Poor for most solvents, acids, and bases.
- EPDM: Excellent for water, steam, and brake fluid. Poor for oil, gas, and most hydrocarbons.
- Viton (FKM): Excellent chemical resistance, especially to toluene, fuels, and solvents. Not suitable for hot water and steam. It can be used to contain chlorine water.
- Silicone: Excellent heat range but poor resistance to fuels, oil compounds, and acids.
- Neoprene: Good for moderate chemicals, oil molecules, and weather resistance. Poor for aromatic and oxygenated solvents.
- PTFE (Teflon): Excellent chemical resistance across various chemicals. Suitable for extreme temperatures.
How to Select the Right O-Ring Materials?
Selecting the right O-ring materials involves considering various factors that ensure the O-ring will perform effectively and last in its intended application. Here are the key steps and considerations for selecting the right O-ring material:
1. Identify the Operating Environment:
- Temperature Range: Determine the minimum and maximum operating temperatures. Different materials have varying temperature tolerances. Silicone O-rings are excellent for high and low-temperature use cases (approximately -70°C to +230°C or -94°F to +446°F), while Nitrile (Buna-N) is suitable for moderate temperature ranges (approximately -40°C to +120°C or -40°F to +248°F).
- Chemical Exposure: Identify the chemicals the O-ring will be exposed to, including any potential contaminants.
- Pressure: Consider the pressure the O-ring will need to withstand.
- Environmental Factors: Assess exposure to UV light, ozone, humidity, and other environmental factors.
2. Evaluate Physical Properties:
- Hardness: Measured in Shore A, an O-ring’s hardness affects its sealing ability and compression set resistance. You can calculate the strength of a ring to apply the perfect ring for your tool. Softer O-rings provide better sealing but may wear out faster. Grease can help reduce the rings’ overall abrasion, pinching, and wearing.
- Tensile Strength and Elongation: These properties determine the material’s ability to stretch and return to its original shape.
- Compression Set: The material’s ability to maintain its shape and sealing force after compression. Low-compression set materials are preferred for maintaining long-term seals.
3. Compatibility with Media:
Use compatibility charts to match the O-ring substance with the chemicals it will encounter. Use sources like the Cole-Parmer Chemical Resistance Guide and the Parker O-Ring Handbook for detailed compatibility information.
4. Application-Specific Requirements:
- Dynamic vs. Static Seals: Dynamic seals (moving parts) require materials with low friction and high wear resistance, while static seals (stationary parts) focus on compression sets and chemical resistance.
- Industry Standards and Certifications: Certain industries may have specific requirements, such as FDA compliance for food and pharmaceutical or NSF standards for drinking water systems.
5. Cost Considerations:
- Balance the performance requirements with cost. High-performance materials like FFKM (Perfluoro elastomer) offer superior chemical resistance and heat range but are more expensive than standard materials like Nitrile.
6. Testing and Validation:
- To validate the element choice, tests should be conducted under actual operating conditions. These may include accelerated aging tests, chemical immersion tests, and mechanical stress tests.
Common O-Ring Materials and Their Applications:
- Nitrile (Buna-N): Excellent for petroleum-based oils and fuels, moderate temperature range. Common in automotive and industrial uses.
- EPDM: Excellent for water, steam, and outdoor purposes due to its resistance to weathering, UV, and ozone. Used in potable water and brake systems.
- Viton (FKM): High-temperature resistance and excellent chemical resistance, especially to oils, gas, and solvents. Used in automotive, aerospace, and chemical processing industries.
- Silicone: Wide temperature limits and excellent flexibility. Used in medical devices, food processing, and high-temperature environments.
- Neoprene: Good weather, ozone, and abrasion resistance. Suitable for refrigerants and moderate solvents.
- PTFE (Teflon): Excellent chemical resistance and high-temperature tolerance. Used in aggressive chemical environments and cases requiring low friction.
Conclusion
The ring’s chemical compatibility will significantly affect the results and actual performance. To make more informed decisions, utilize online tools and resources to evaluate specific parts before choosing the ring compound.
Whether you need high-temperature resistance, superior flexibility, or compatibility with specific fluids, materials like Viton, EPDM, Nitrile, and PTFE offer tailored solutions. By understanding the unique properties of each material, you can make an informed choice that enhances efficiency and reduces maintenance costs.
Get High-Performance O-Ring Solutions Now!
Choosing the right O-ring is crucial for ensuring reliable operation in harsh environments and reducing maintenance costs. We offer high-performance materials like Viton, EPDM, and PTFE, with OEM customization to meet your specific needs.
Contact us today to find the best sealing solution or request a free quote to enhance efficiency and durability in your applications!