Do you get confused while purchasing materials for your industrial project because of the confusing classification terms? Not to worry, for we will demystify ASTM D2000 in this guide so you can confidently make a purchase for your project. ASTM D2000 is a common term for rubber and elastomer specifications. It categorizes rubber materials based on their classifications, like BC, EPDM, and GE.
What is ASTM D2000?
The American Society for Testing and Materials (ASTM) developed a classification system for rubber products and termed it ASTM D2000. It is a standardized classification system that specifies the properties of vulcanized rubber materials. It was originally designed for automotive applications, but now it has been adopted by many other industries, including aerospace, medical, and manufacturing.
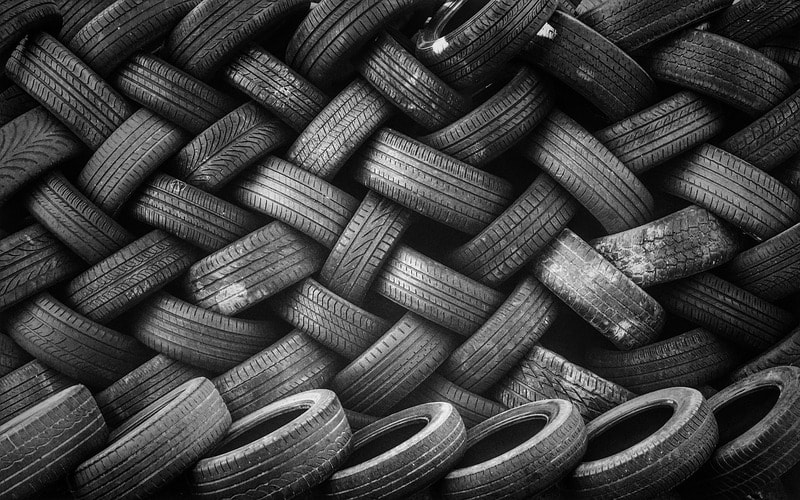
The system was created to streamline the material selection process and aid communication between customers and suppliers. A line callout designation is used to describe the properties of rubber.
The properties include type (based on temperature resistance), class (based on oil resistance), hardness (durometer), and tensile strength. Using the system expedites the material selection process to fulfill specific application needs.
In most industries, it is critical to use ASTM D2000, as it ensures materials perform reliably under specific conditions. By using this standard, you can ensure that the material you select caters to your project and has the necessary resistance to factors such as temperature variations, oil exposure, and mechanical stress.
Components of ASTM D2000 Line Callout
Understanding the main components of ASTM D2000 line callout is necessary if you are an engineer or manufacturer. Even the slightest bit of change in the callout can leave you with the wrong material that can alter your product’s performance. Here is a breakdown of the line callout of astm d2000:
Types
The type indicates rubbers’ ability to resist heat or cold. Rubbers are classified into three classes from A to C based on their performance at high to low temperatures. Type A rubbers offer high-temperature resistance, type B has medium, while type C features low resistance to temperature.
Class
It defines the rubber’s resistance to oils, fuels, and other chemicals. You can use this classification to select rubber for specific oil-based environments. A class 1 rubber works fine with petroleum oils, but a class 2 rubber is best for exposure to non-petroleum oils.
Hardness
The hardness of a rubber is measured by a durometer and indicated by the Shore A scale. It indicates the flexibility or stiffness of the rubber or elastomer. The higher the number, the harder the material it depicts. For example, 70A means a hardness of 70 on the Shore A scale.
Tensile Strenght
It is the ability of any material to resist breaking under tension. It is usually measured in pounds per square inch (PSI) and determines a rubber’s durability under stress.
Elongation
The flexibility of a material or percentage of stretch before breaking is elongation.
Compression Set
Compression is the rubber’s ability to return to its original shape after being compressed under heat or pressure. It is important to note in applications where rubber will experience constant deformation.
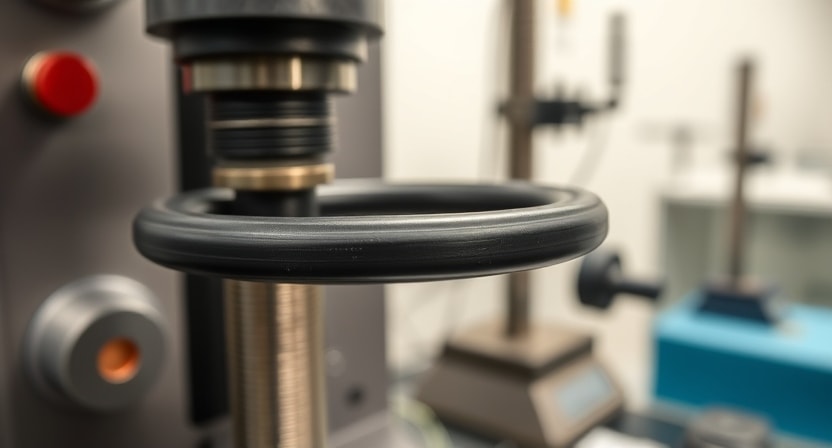
Ozone Resistance
This indicates the rubber materials resistance to degradation after being exposed to ozone. It is crucial in automotive and other outdoor applications.
Additional Modifiers
At times other modifiers are also included in the line call-out to specify characteristics such as low-temperature flexibility or resistance to acids, etc.
Understanding the ASTM D2000 Classification System
It is vital for engineers and manufacturers working with elastomers in the automotive, aerospace, and medicine industries to understand the astm d2000 classification system. It is not only used to differentiate materials but also ensures seamless communication between supplier and customer.
It allows you to save time and money by acquiring just the material with the desired properties for your project.
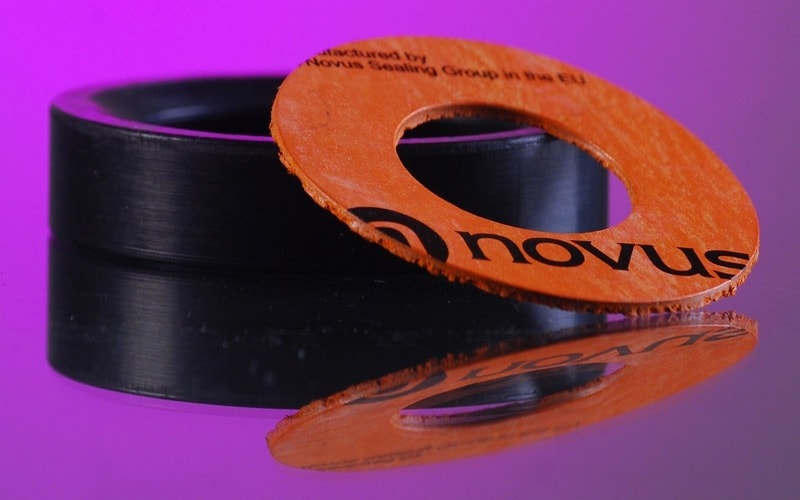
Standards and Units of Measure
The standards of ASTM International are built after applying rigorous test methods to ensure all information is authentic and reliable. The ASTM D2000 works as a universal framework to describe elastomer properties.
The line callout system, as explained, provides detailed material specifications in a concise format. It helps differentiate materials based on physical properties such as tear resistance and tensile strength.
The units of measure play a critical role in interpreting the system. The first thing to notice is the presence or absence of the letter M. This letter indicates that the measurements are in metric units or SI units. The absence of the letter M implies that English units are being used.
For example, the English unit for testing temperature is Fahrenheit, while the SI or metric unit is Kelvin. This information becomes critical in applications where rubber’s temperature resistance is a requirement.
Knowing the units of measure is essential for interpreting line callouts correctly. It ensures the materials meet the necessary basic requirements, such as oil and lubricant resistance or maximum temperature stability, based on the intended application.
Material Properties and Characteristics
The ASTM D2000 system defines material properties and characteristics of elastomers with numbers and syllables. A reliable test method is used to create this characteristic system. Here is a concise explanation of some characteristics defined by numbers in ASTM.
Durometer Hardness and Tensile Strength
The two most critical parameters for measuring a rubber’s durability are its hardness and tensile strength. Hardness is measured by a durometer, and depending upon the units of measurement, it is either expressed in megapascals or pounds per square inch. It measures the material’s resistance to permanent indentation or deformation when subjected to pressure.
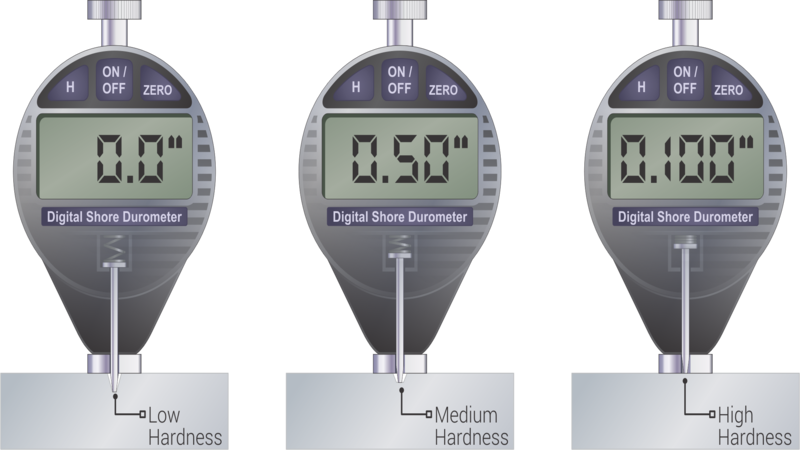
Tensile means pulling; thus, tensile strength refers to the maximum amount of pulling a material can endure without breaking. A higher tensile strength means the material is durable and resistant to wear and tear. It is also correlated with improved impact resistance and flex resistance.
Both of the values are indicated by a three-digit number. For example, 714 corresponds to a material with a 70 shore hardness level and 14 tensile strength.
Abrasion Resistance and Heat Resistance
Abrasion resistance reflects a material’s ability to resist wear and tear due to friction. It is an important classification for rubbers that will get exposed to repetitive motion or rough surfaces. A common example of a high wear and tear environment is automotive gaskets and seals.
As the name suggests, heat resistance is a measure of temperature resistance. It determines a material’s ability to endure high heat without degrading. ASTM uses test temperature with 70 hours of heat aging to ensure maximum temperature stability. Each rubber is categorized based on its specified temperature limits.
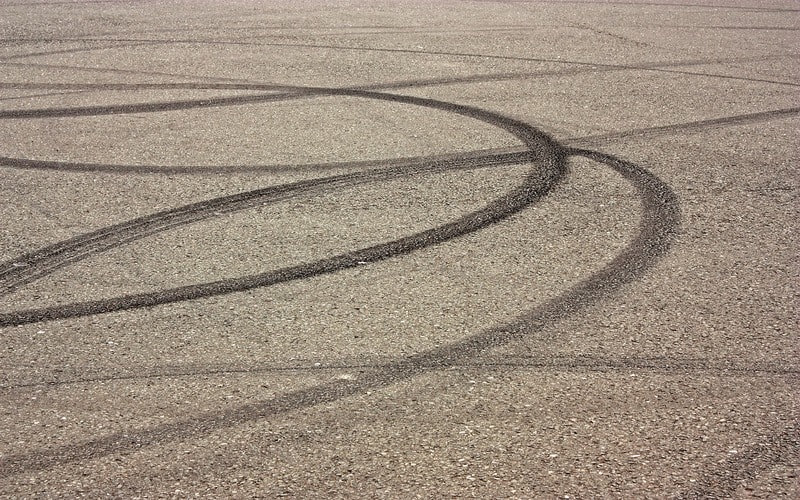
Special Requirements and Suffixes
Some elastomeric materials require additional properties to be used in specific applications. These special requirements are denoted by suffixes, combinations of letters, and numbers for each additional characteristic. Each letter-number pair corresponds to specific requirements.
For example, H flex resistance or J abrasion resistance are letters that denote their characteristic property in elastomers. Additional requirements can vary depending on project specifications and technicality. It can include fuel resistance, lubricant resistance, flammability resistance, and even fluid resistance.
Whether you are an engineer working on a project or a manufacturer creating products, it is important to know the suffix that denotes your desired material property.
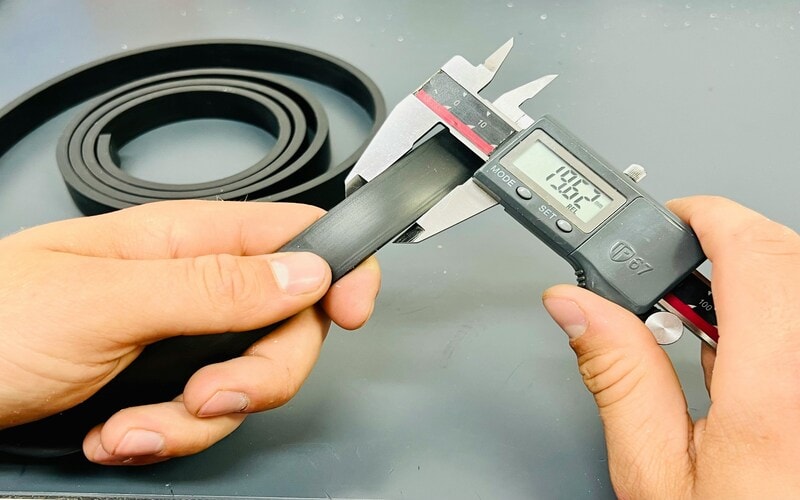
Real-World Applications and Use Cases of ASTM D2000
ASTM D2000 plays a vital role in all industries that require rubber materials. It is most prominently used in the automotive industry as rubber materials are used in seals, gaskets, insulation, etc. These products have to withstand high pressures and temperature fluctuations and also come in contact with fuels.
By using ASTM D2000, you can ensure the rubber material you obtain performs reliably throughout the lifespan of a vehicle.
The aerospace, industrial manufacturing, and medicine industries also rely on ASTM D2000 to ensure the optimum performance of elastomeric material. Aerospace components such as seals in hydraulic systems and engines must be built with materials that ensure ozone or weather resistance.
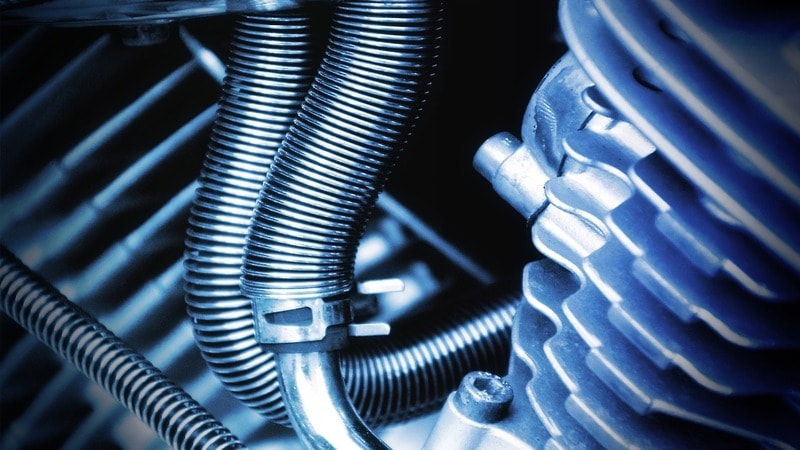
By utilizing the common language of elastomeric material classification, you can reduce the risk of product failure while enhancing performance. It is also an easy way to communicate your material needs across special industries without any hassle.
Best Practices and Tips
The best practice is to get familiar with the ASTM D2000 as soon as you enter the industry. You can use this guide or create one for yourself to stay up-to-date on ASTM D2000 specifications. You can start with understanding the basic components of a line callout and then advance toward understanding the suffixes for additional properties.
Not only will this knowledge guarantee you get the right product but also make you look like an industry expert in front of your superiors.
Expert Advice for Working with ASTM D2000
Follow these pointers to become an expert on ASTM D2000
- Learn all the segments of line callout and their meanings
- Know how to differentiate between units of measure
- Learn the units of measure of common properties
- Study which number specifies the qualities you want
- Understand how to denote specification revision, units of measure, grade number, type and class, hardness, and tensile strength
- Create a guide of materials with their ASTM D2000 used in your field frequently.
- Consult with an industry expert if you cannot decipher the code.
Common Materials Under ASTM D2000
After enduring rigorous testing, these elastomeric materials are classified by ASTM D2000 to be used by professionals. Some common materials under ASTM D2000 include:
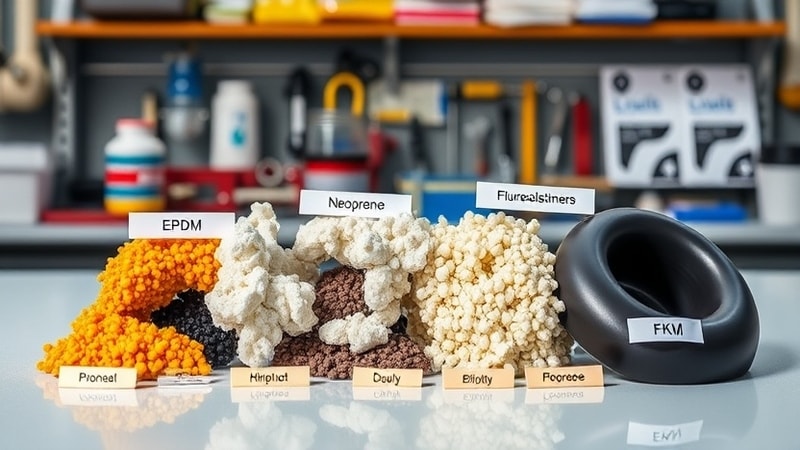
- EPDM: It is an ethylene propylene diene monomer. This elastomeric material offers extreme ozone or weather resistance, making it the perfect option for outdoor applications such as roofing and HVAC.
- Neoprene: It is made of chloroprene polymers, thus often referred to as chloroprene rubber. It offers extreme thermal insulation and the highest chemical resistance, including acids and petroleum fluids. It is ideal for automotive applications and medical products. It is most commonly used for electrical cable insulation and building wet suits.
- NBR or Nitrile Rubber: is renowned for its resistance to oils, fuels, and lubricants, making it a popular option for gaskets and seals in automotive as well as aerospace industries.
- Fluoroelastomers or FKM: are high-performing elastomers offering maximum allowable volume swell and compression deflection resistance. It is used to make o-rings and seals for hydraulic systems and engine components.
How to Choose the Right ASTM D2000 Material for Your Application
You have to understand the advanced requirements of your project before you choose the material. Here are four basic things to consider while choosing ASTM D2000.
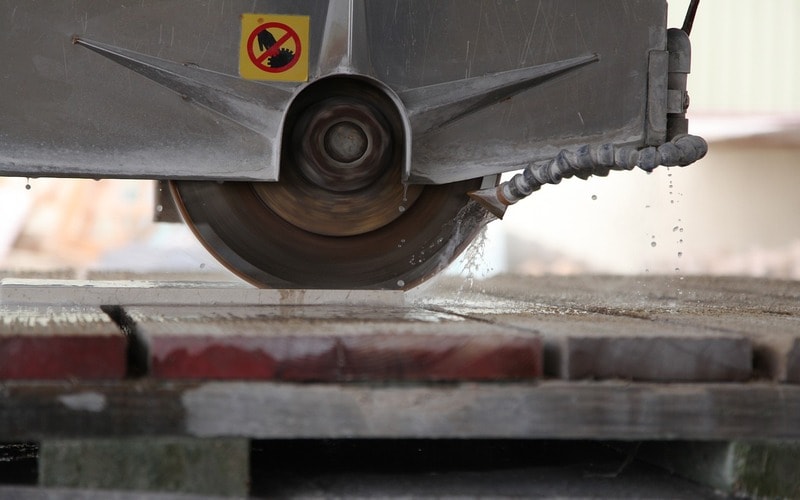
- Consider the temperature range of your application
- Evaluate the type and extent of chemical exposure on the rubber
- Must evaluate the mechanical requirements, including compression set and tensile strength.
- Environmental factors such as UV exposure and moisture should also be taken into account.
Where to Find ASTM D2000 Compliant Materials
There are many vendors that sell rubber products, but only a limited number provide ASTM D2000-compliant materials. Here is a list of ASTM D2000 material suppliers and manufacturers of gaskets and seals.
- Hongju Technology
- Elasto Proxy
- Mercer Gasket and Shim
- Seal and Design
You can read the certification handbook of ASTM D2000 on the official website of the American Society of Testing and Materials International before you decide on a manufacturer to buy gaskets. There is more critical information available on the SAE international website, an association of engineers and experts from technical fields.
Conclusion
Understanding ASTM D2000 is crucial for selecting the right rubber materials for industrial applications, ensuring performance, durability, and compliance with specific requirements. By navigating the ASTM D2000 classification system, you can choose the ideal elastomer for temperature resistance, chemical exposure, mechanical strength, and environmental resilience. With proper material selection, your business can enhance the efficiency, longevity, and safety of your products.
Providing high-quality elastomer materials that meet ASTM D2000 standards
Ready to enhance your operations with premium materials? Hongjui offers high-quality elastomeric materials that meet ASTM D2000 standards.
Request a free consultation today or explore our comprehensive catalog.