Because TPE materials are available in several types, choosing one that most suits your application is essential. Consequently, this article explores the TPE materials available and how to choose them.
What is TPE?
TPEs (Thermoplastic Elastomer) are rubber-like materials; they are soft, flexible, and easy to process. Furthermore, due to their molecular structure, TPEs are highly elastic.
Thermoplastic rubbers have several benefits, including their ability to return to their original shape after compression or stretching. Hence, they are more durable and have a better physical range than other materials.
How are TPEs Made?
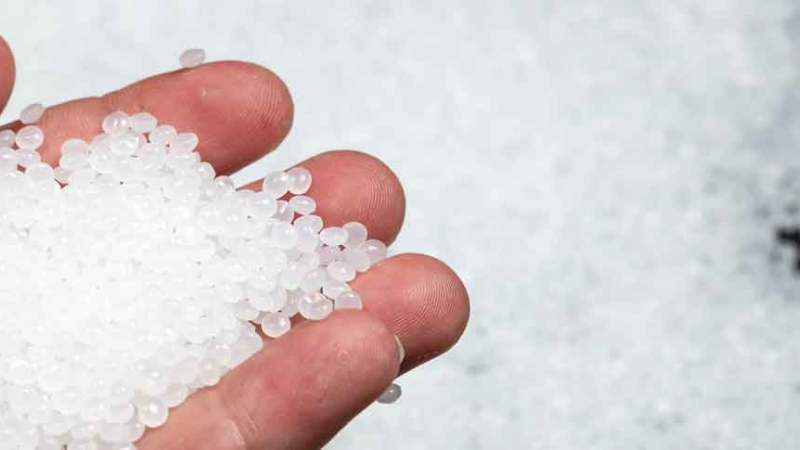
The production method for TPEs consists of mixing a stiff polymer with a flexible elastomer, either mechanically or through chemical means. In the context of mechanical methods, TPEs are created using high-shear compounding machinery that constantly blends the elastomer and the rigid polymer together.
The raw materials in the mechanical process should have to match viscosities at the process conditions. Therefore, it is always best to consider the materials’ parameters before blending.
Chemically, TPEs are made through dynamic vulcanization. For more details, you can see the article “What is Vulcanization and Vulcanized Rubber?” Dynamically vulcanized TPEs have two elastomeric phases – discontinuous and cross-linked. The two phases are because the soft elastomer phase of the raw materials is partially vulcanized at high temperatures and shear rates.
The temperature must be above the thermoplastic’s melting point to activate and complete the vulcanization process. Therefore, for optimum results, factors to consider before dynamic vulcanization include material compatibility, degree of cure, and particle size.
Where are TPEs Used?
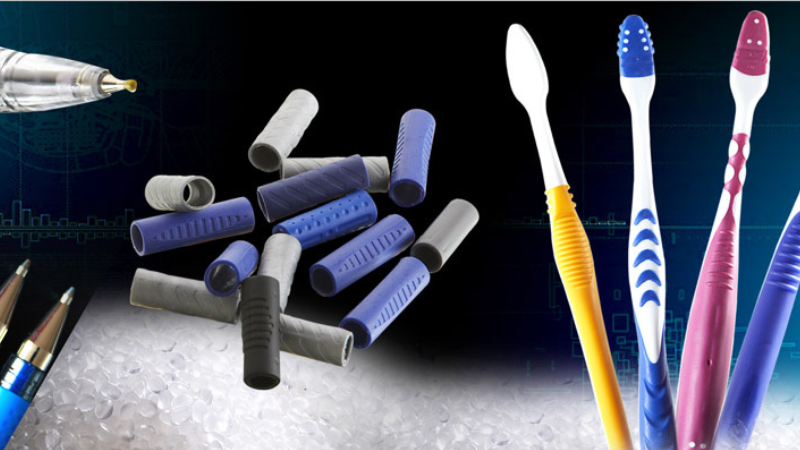
TPEs are used in applications requiring flexible materials. The material is cost-effective and safe, offering quality and low toxicity. Furthermore, TPEs are versatile and easy to process. Hence, the material is suitable for several applications.
Generally, TPEs manufacture sealants and coatings, electronics, and sporting goods. They are also helpful in the medical industry due to their safety and low toxicity levels.
Types of TPEs
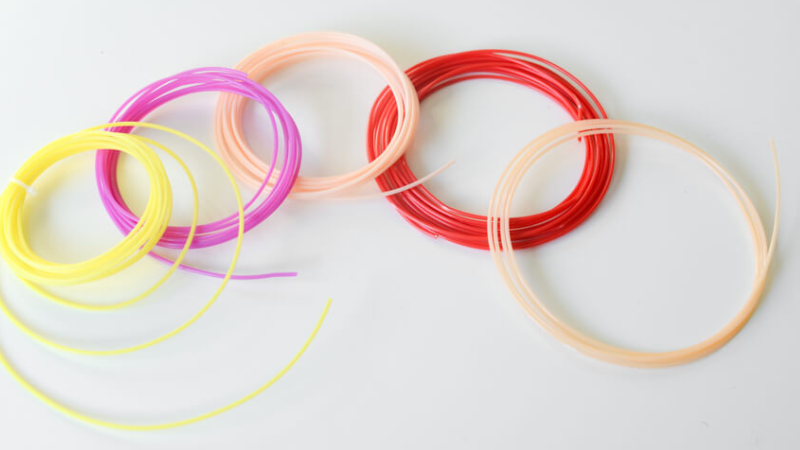
There are several types of TPEs, and they vary in structure and constituents. Common types of TPEs include;
- Styrenic TPEs
- Olefinic TPEs
- Urethane TPEs
- Polyester TPEs
- Polyamide TPEs
- Vulcanizate TPEs
- Soft-PVC
Thermoplastic Styrenic Elastomers (SBC / TPS / TPE-S)
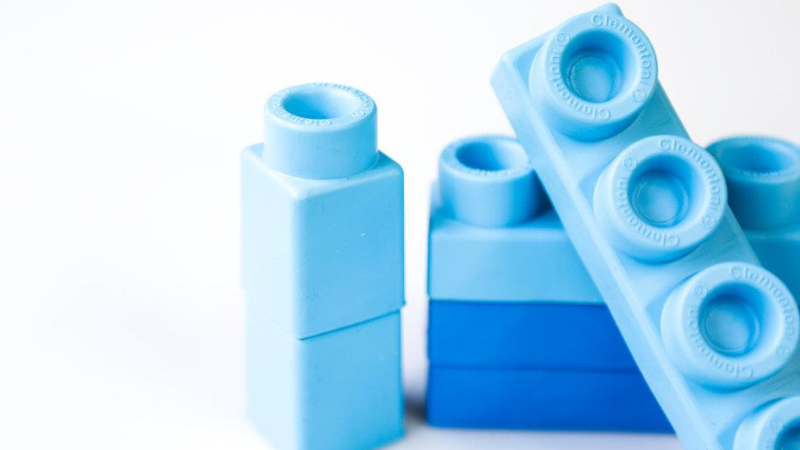
Styrene block copolymers (SBCs) are the most widely used TPE materials. The versatility of styrene block copolymers is due to their unique multiphase structure. This structure comprises soft raw material end blocks and hard styrene mid-blocks.
Block copolymerization results in SBC forms. SBC material properties include high abrasion resistance, tensile strength, and elasticity. In addition, styrene thermoplastic elastomers function over a wide temperature range, absorbing shock in varying degrees.
Some applications that use SBCs include the manufacture of resins, additives, and fillers.
Olefinic Thermoplastic Elastomer (TPE-O/TPO)
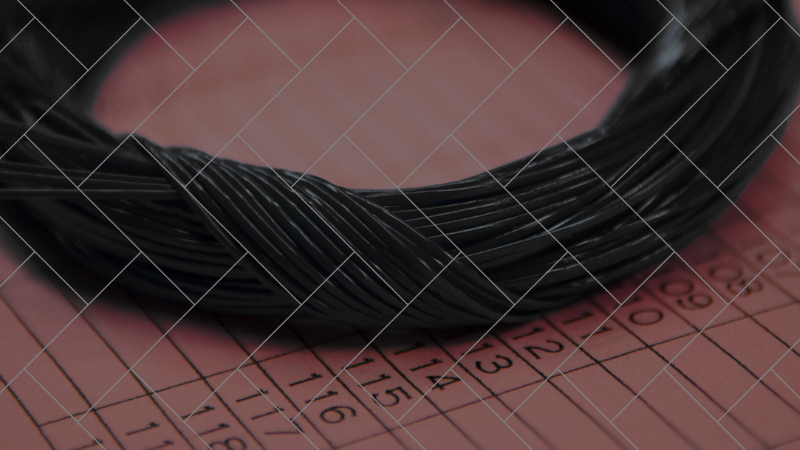
Thermoplastic polyolefins (TPOs) are TPE compounds formed from blending uncrosslinked EPDM rubber and polyolefins. TPO’s properties include high chemical resistance and strength and low densities.
In addition, thermoplastic polyolefins are suitable for applications that require high wear and tear resistance and high plastic durability.
Urethane Thermoplastic Elastomers (TPU / TPE-U)
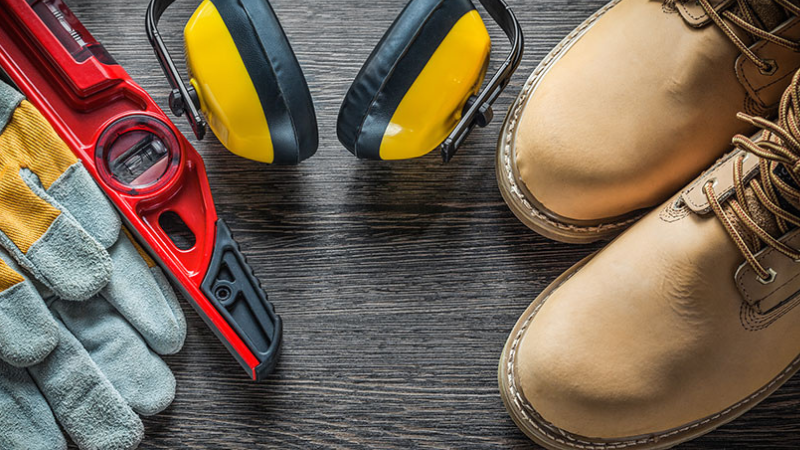
The polyaddition reaction of polyisocyanates and diols or polyols forms thermoplastic polyurethane (TPU). The urethane group is a characteristic feature of TPUs, giving the material varying properties over a broad range.
TPUs have varying concentrations of the cross-linking degree, the isocyanate, and the OH component. Therefore they are suitable for use as elastomeric alloys and rubber substitutes.
Thermoplastic polyurethane has material properties, including good oxygen and ozone resistance, excellent abrasion resistance, and thermal properties. The material is also extensible and possesses a high tensile strength.
Polyester Thermoplastic Elastomers (TPE-E/TPC)
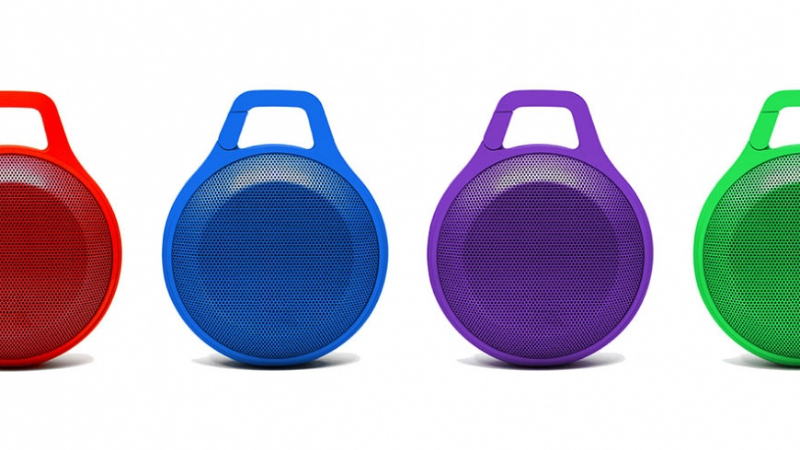
Thermoplastic polyesters (TPCs) are polymers with a linear block structure. However, they have both a crystalline and amorphous segment. Consequently, TPCs are elastic and easy to process.
Furthermore, the crystalline part of a thermoplastic copolyester makes the material resistant to temperature over a wide range. The material also has properties including good aging and chemical resistance.
Furthermore, TPCs have excellent electrical properties, making them suitable for manufacturing cables and hoses in the automotive industry.
Thermoplastic Polyamide Elastomers (COPA / TPA / TPE-A)
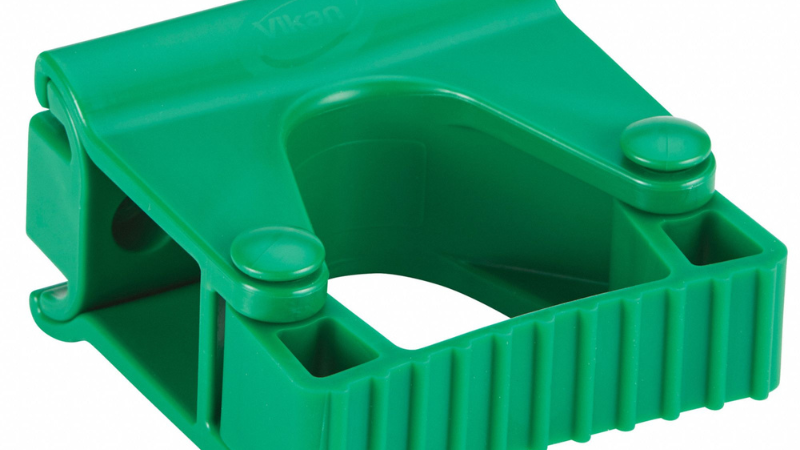
Polyamide block copolymers (TPAs) are elastic materials made from copolymers, including polyether-amide, polyester-amide, or polyether-ester-amides. TPA’s physical properties depend on its copolymer blocks’ number, length, and type.
Generally, thermoplastic polyamides are ideal for applications requiring high temperature and oil resistance. This type of TPE is also flexible at low temperatures. Other physical properties of TPA include its excellent chemical and weather resistance and abrasion and impact resistance.
Vulcanizate Thermoplastic Elastomers (TPV /TPE-V/ EA)
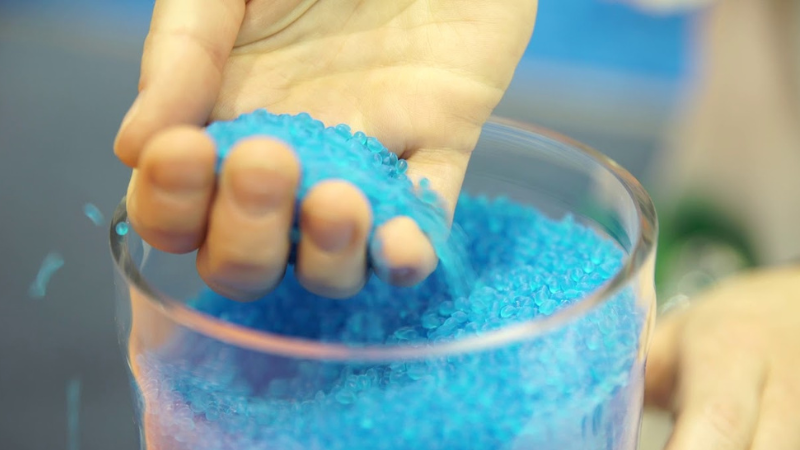
Thermoplastic vulcanizates (TPVs) are made through the dynamic vulcanization process. This TPE material is a mix of polypropylene compounds and EPDM rubber. TPVs have rubber-like properties and are cost-effective.
Furthermore, TPVs have excellent thermal properties. Hence, they are used in high-heat applications. They also have good oil and chemical-resistant properties.
Soft-PVC Thermoplastic Elastomers (TPVC)
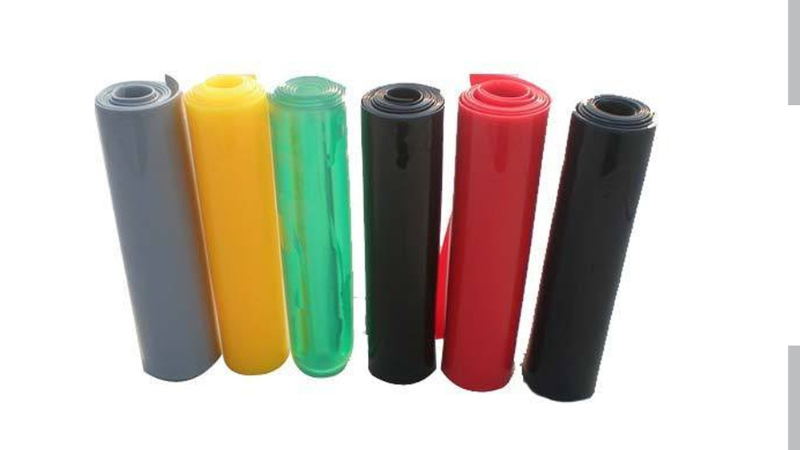
Polyvinyl chloride (PVC) is a commonly used polymer in plastic production. The chain polymerization of vinyl chloride produces PVC, which is amorphous, brittle, and complex. However, adding plasticizers increases the processing capabilities of PVC, making it suitable for several applications.
PVC is available in two categories – soft and rigid. Although plasticizers increase the flexibility of PVC, they have their downsides. For instance, products made from flexible PVC are less durable and have limited recyclability. In addition, plasticizers are hazardous to health and can leach into food and the environment.
The Benefits of TPEs
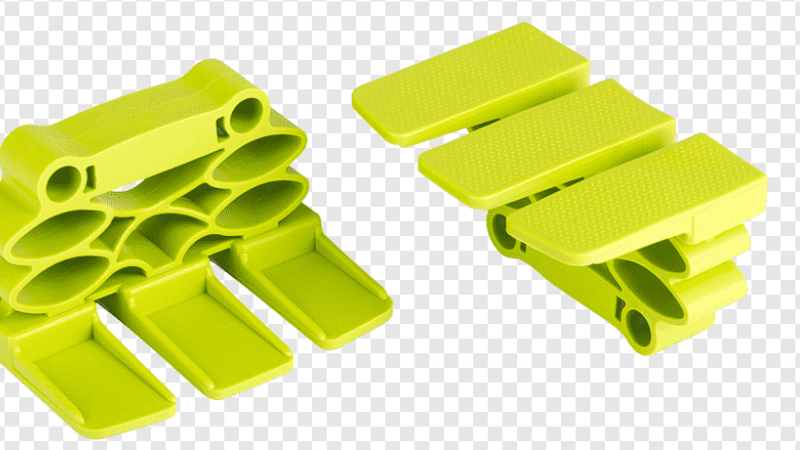
Lower energy consumption: TPEs have short molding cycles and are quickly processed. Thus, they consume less energy.
Low costs: TPEs have lower volume and quality control costs. The material’s low density compared to conventional rubber materials results in low volume costs. In addition, the consistency and reproducibility of TPE resins result in lower quality control costs.
Minimal compounding: TPEs have little to no compounding. Most of these materials are usually ready for fabrication due to their complete formulation.
Finished parts costs: TPEs have short fabrication times and molding cycles. Hence they need several seconds to process, resulting in lower finished parts costs.
Hardness range: TPEs have a wide hardness range. They possess Shore A, Shore C, and Shore D hardness ranges.
Permeability: TPEs have low permeability and possess good coloring properties
Resistance: thermoplastic rubber is resistant to heat and oil within specific temperatures.
Applications: TPEs are used in a broad range of applications. They are useful in several industries, including medical and automotive.
Electrical insulation: TPEs have excellent properties, making them useful in electronic applications.
Applications of TPEs
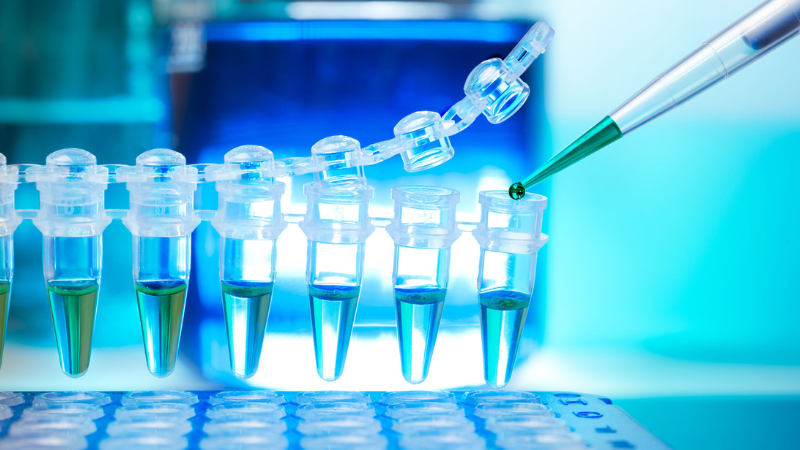
Because of their versatility, TPEs are helpful in several industries, including;
- Medical
Due to its biocompatibility, TPE is suitable for use in the medical industry. The material is free of plasticizers and latex protein. Furthermore, TPEs are hygienic, secure, and recyclable with minimal waste.
Therefore they are used for various applications, including medical tubes, masks, and syringe gaskets. TPEs also produce orthopedic gels, catheter bags, and medical tubing.
- Automotive
TPEs are used in the automotive sector due to their high temperature, weathering, and abrasion resistance. In addition, TPEs are used in several automotive applications. The material produces bumper stops, shock-absorbing seals, and vibration dampeners.
- Electronics
Thermoplastic elastomers have electrical properties, and they function correctly in varying temperatures. Furthermore, TPEs increase electronic products’ service life and quality because of their flame retardancy and resistance to microorganisms.
Generally, TPEs are used in producing self-driving cars, new communication technologies, and optical fibers.
Furthermore, because of their excellent skin compatibility and soft touch feeling, TPEs are used to manufacture personal electronics, including wristbands for sensors and smartwatches.
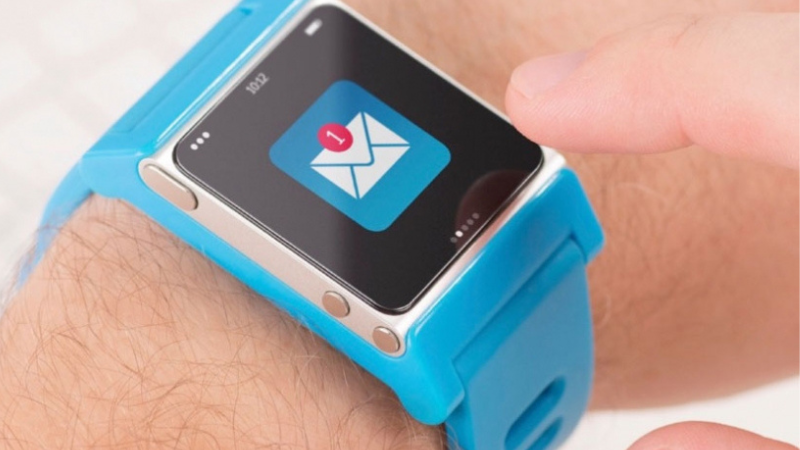
- Consumer goods
TPEs are used in manufacturing several consumer goods because the material is safe for use with the skin and in food. Consumer goods generally use thermoplastic rubber, including toys, diapers, shoe soles, sports equipment, and soft-touch components in personal care products.
- Construction
TPEs are flexible, durable, and recyclable. The construction industry uses TPEs as additive materials in road asphalts. They are also used to manufacture sealants, coatings, and adhesives.
Properties of TPEs
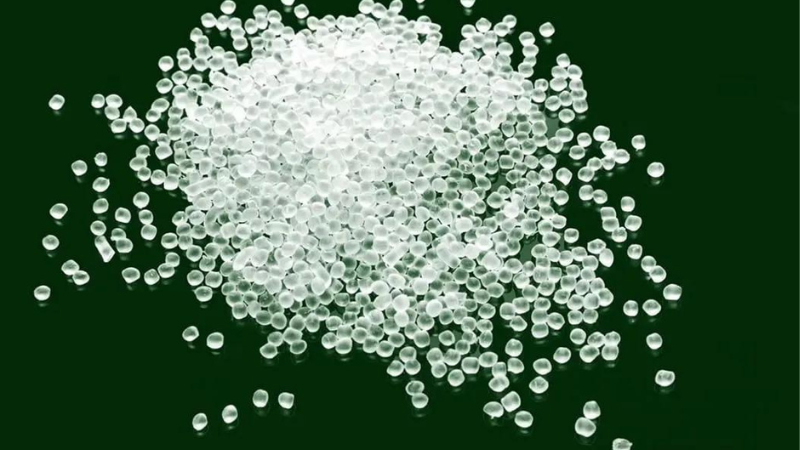
TPEs possess several properties, making them useful in several applications. Because there are several TPEs, you must consider these essential characteristics before choosing a suitable one for your application. The properties include:
Hardness
The shore value measures a thermoplastic elastomer’s hardness. Hardness is an essential criterion in choosing a TPE. The shore durometer, the instrument for measuring hardness, measures the depth of depression a given force creates in the material.
Thermoplastic elastomers have a wide range of hardness, including the Shore A, Shore C, and Shore D scales.
Temperature Resistance
Most TPE materials have thermal properties that make them suitable for high-heat applications. However, they must have different temperature resistances for each application. Factors affecting a TPE material’s temperature resistance include the shape of the material, type of stress, and duration of heat exposure.
Generally, TPEs are resistant to high and low temperatures. The material has a temperature range between -30 degrees and 150 degrees C.
Tensile Properties
Tensile at break and tensile modulus are standard tensile properties testing the strength of a TPE.
Tensile at break measures the breaking strength of a TPE. This tensile property measures the pressure a thermoplastic elastomer can withstand when stretched before it reaches the breaking point. It is important to note that a high tensile at break value means the TPE does not break easily when pulled compared to those with lower values.
Tensile modulus is the relationship between stress and strain on a solid body when it undergoes permanent deformation in a linear elastic manner. Generally, TPEs are resistant to tearing.
Compression Set
The compression set measures a TPE material’s behavior to constant contraction and immediate release for an extended period.
TPEs with low compression sets almost return to their original thickness after contraction and release. Usually, TPE materials with soft compression sets are ideal for sealing applications.
Shrinkage
Molded TPE material parts shrink when cool. Usually, the shrinkage is very micro. However, it affects the appearance and exact fit of the product. Therefore, consider its shrinkage before choosing a TPE material for your application. You can obtain shrinkage information from the TPE manufacturers.
UV Stability
UV stability is especially critical for using your product in outdoor applications. TPEs with high UV stability are suitable for outdoor use. Generally, thermoplastic elastomers are highly resistant to weathering, ozone exposure, and UV radiation.
Electrical Properties
TPE materials are good insulators depending on the polarity level of the material. Although most thermoplastic elastomers possess electric properties, non-polar TPE materials are better electrical insulators.
Chemical Resistance
A TPE material’s polarity also determines its chemical resistance. For instance, non-polar amorphous TPEs have limited chemical resistance to many solvents.
How are TPE Materials Processed?
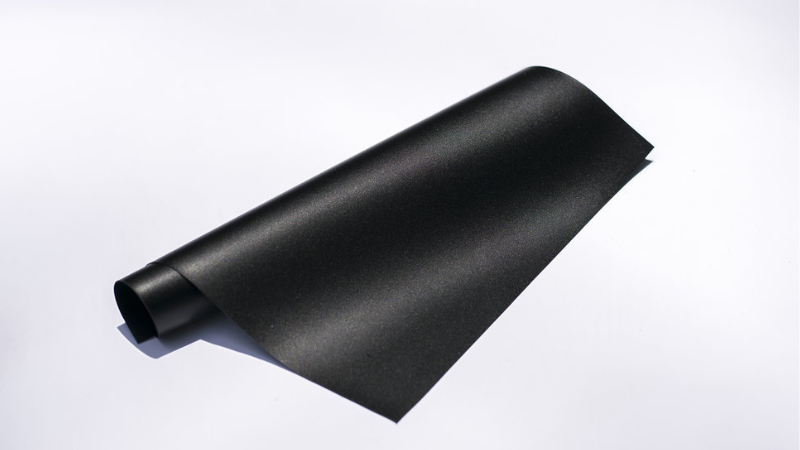
Thermoplastic elastomers are simple to process, and they have short recyclable times. Consequently, TPE processing helps to create several products all around us. Standard TPE processing methods include;
Injection Molding
The injection molding process is the most essential thermoplastic elastomer material processing technique. This method has high productivity and is residue-free.
The injection molding process uses a mold. During production, molten plastic is injected into a mold to create thermoplastic elastomer products taking the mold’s shape. TPEs behave like thermoplastics in this process. Furthermore, this process has great precision and can produce high volumes.
Consequently, it creates solid parts, including tools and components.
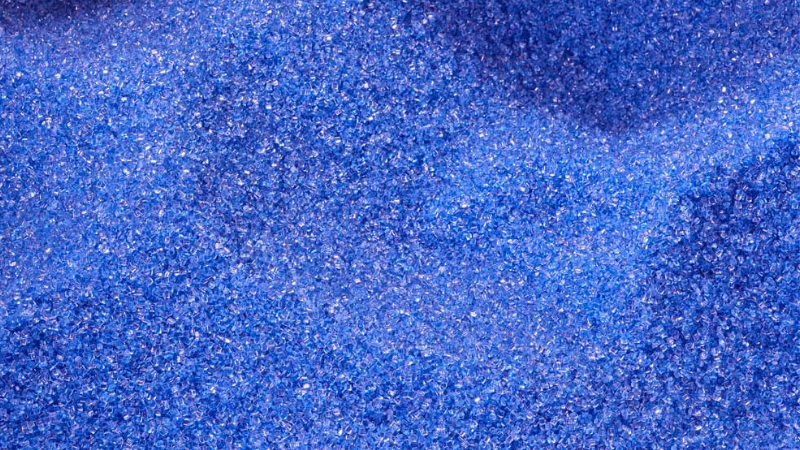
Extrusion
The extrusion process is continuous. The die-cutting process involves forcing TPE material through a die to shape it. The die has a cross-sectional profile, and the material eventually takes shape. An extrusion machine has a hopper, spiral screw, and barrel.
You have to feed TPE pellets into the hopper during the extrusion process. The spiral screw rotates, heats, and melts the pellets in the heated barrel.
Following that, the screw forces the molten plastic through a die. This results in continuous lengths of mold that are subsequently cooled. The extrusion process differs from injection molding because extrusion creates partially finished products that require further processing.
Therefore, the extrusion process is ideal for complex cross-section productions with good surface finish and a high degree of design freedom.
Extrusion Blow Molding
Extrusion blow molding is ideal for shaping TPE profiles. In this process, molten plastic is ejected into a die or mold. Blowing air into the mold helps create TPE products in the desired shape.
The commonly used types of extruders include single-screw and triple-screw extruders. The extrusion process is suitable for creating products with complex hollow profiles like bottles. They are also used to produce sheets and pipes.
Are TPEs Eco-friendly?
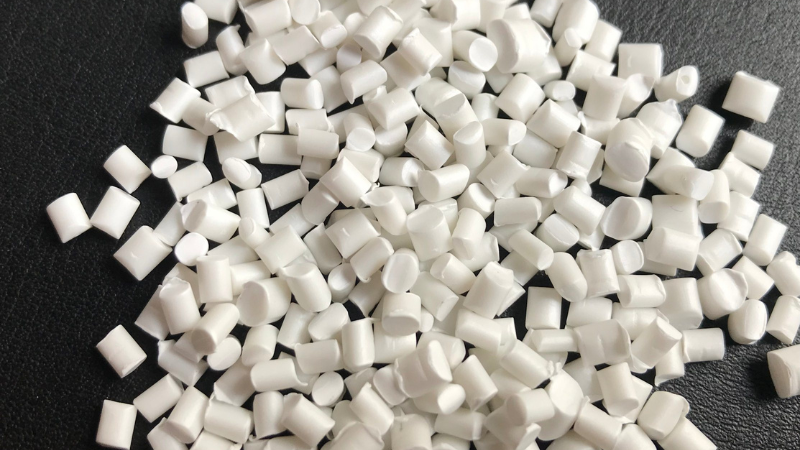
Yes. TPEs are environmentally friendly. This material is lightweight and recyclable. Furthermore, the manufacturing process has low energy demands. However, it is essential to note that the material is not biodegradable.
What are Medical-grade TPEs?
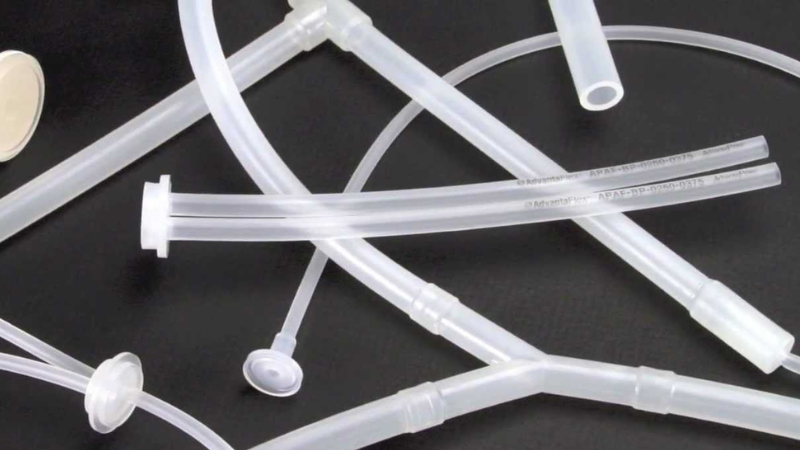
Medical grade TPEs are safe and environmentally friendly materials used to manufacture medical devices. In addition, medical-grade thermoplastic elastomers do not contain phthalate plasticizers, making them alternatives to PVC and silicone.
Furthermore, medical-grade TPEs do not release dioxins or chlorine during use. Hence they are non-carcinogenic and safe for human health. Medical-grade TPEs manufacture IV bags, tubes, and syringe stoppers. They are also used in self-sealing applications for medicine vials and vaccine containers.
What’s the Difference between Silicone and TPE Rubber?
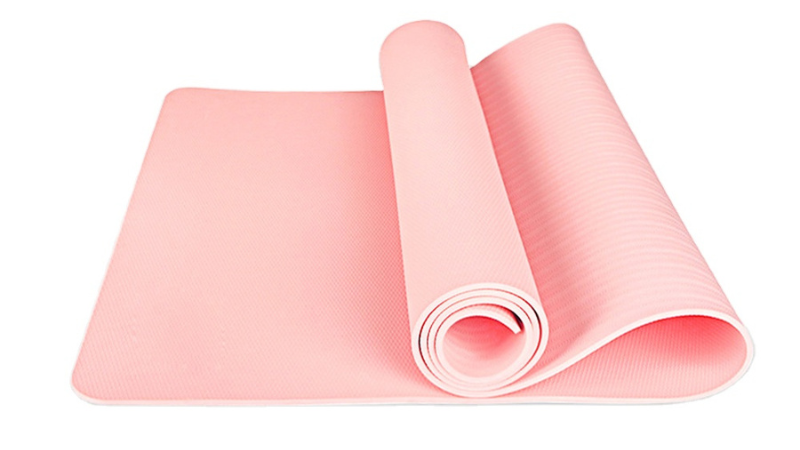
Both TPEs and silicone possess elastomeric properties and are suitable for several applications. Nevertheless, these materials have several differences. The table below summarizes the differences between silicone and TPE rubber.
Thermoplastic Elastomers (TPEs) | Silicone | |
Material | TPEs are a copolymer of rubber and plastic. Hence, they possess elastomeric and thermoplastic properties. | Silicone is an elastomer with plastic and rubber properties. Silicone is also generally referred to as rubber. |
Product performance | Products made from TPEs are incredibly versatile. They possess outstanding thermal properties and material stability | High-quality products possess fire resistance, flame retardancy, thermal conductivity, and extreme temperature resistance |
Melting point | 260 – 320 degrees | No melting point. Silicone remains solid till combustion occurs. |
High-temperature resistance | 130 – 150 degrees. The material age and cracks beyond the temperature range. | 200 – 300 degrees. The material loses its mechanical properties at higher temperatures and becomes brittle |
Reaction to heat | TPEs can be reprocessed after heat exposure | Silicone cannot be altered or reprocessed after heat exposure |
Chemical resistance | Natural chemical resistance | Good chemical resistance |
Safety | TPEs are flexible because they contain phthalates. Phthalates can be harmful to human health. Nevertheless, the low levels present in TPEs do not pose a risk. | Silicone is safe. Food-grade silicone does not react with or contaminate food. |
Usage | TPEs are widely applied in the automotive, medical, and construction industries. | Silicone is helpful in HVAC, medical, aerospace, and electrical applications. |
Conclusion
Thermoplastic elastomers are elastic and easy to process due to the combination of the thermoplastic and elastomer constituents. Therefore, they offer the best of both worlds. They are easy to process yet, flexible and soft.
Because of their properties, TPEs are applicable in several industries. Nevertheless, before choosing TPEs for your application, ensure its properties can withstand the parameters of such an application.
Buy Thermoplastic Elastomer (TPE) Products from Hongju!
Hongju Silicone manufactures rubber products, including gaskets, seals, and o-rings. Because customer satisfaction is our goal, we work with you to create the perfect product based on your specifications.
In addition, we provide several services, including injection molding, to create products in simple and complex designs.
Take the First Step:
Requst for an Inquire
Quality Meets Affordability. Inquire Now for High-Quality Products at Low Volumes.