Enter Ultra-High Molecular Weight (UHMW) plastic, a versatile engineering marvel with exceptional wear resistance, abrasion resistance, and more.
In this article, we delve into the molecular realm of UHMW plastic and its extraordinary potential in shaping a more sustainable and durable future.
What is UHMW Plastic?
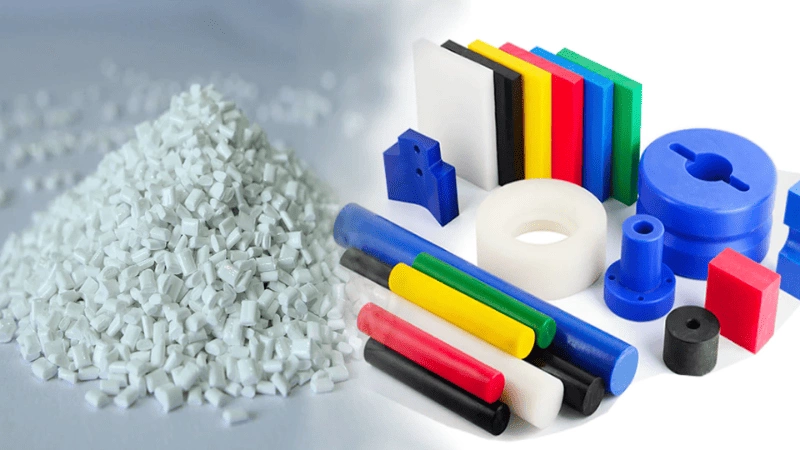
A standout member within the polymer family is Ultra-high molecular weight polyethylene, commonly known as UHMW plastic. It distinguishes itself with its extraordinary molecular weight, characterized by the presence of tiny molecules that create an ultra-high molecular weight crystalline phase.
UHMW plastic’s extraordinary set of properties is rooted in its unique molecular structure, making it a groundbreaking material in numerous industries.
Molecular Weight: The Key to UHMW’s Excellence
The hallmark of UHMW plastic is its exceptional molecular weight, which places it in a class of its own. Unlike many other polymers, UHMW boasts molecular chains that are exceptionally long.
This unique feature gives rise to several exceptional attributes, making it a preferred choice for a wide range of applications.
Low Coefficient of Friction
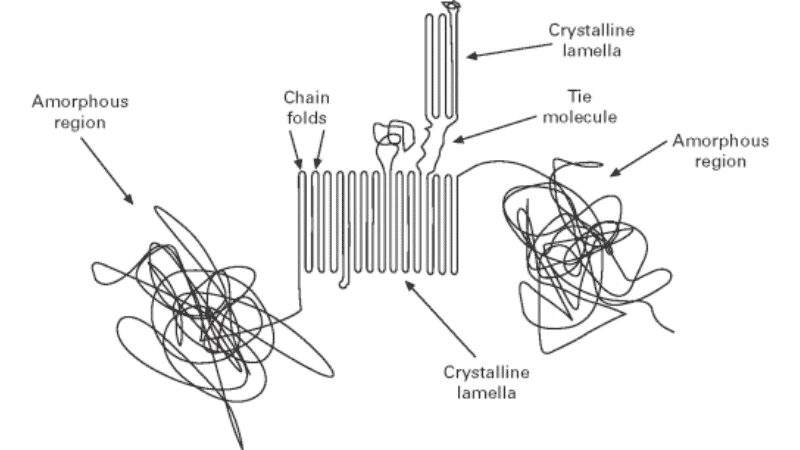
The incredible length of UHMW plastic’s molecular chains translates into a low coefficient of friction, a property that is highly coveted in numerous industries.
With its low friction coefficient, UHMW plastic showcases minimal resistance to movement, making it the perfect choice for applications where smooth, frictionless operation is essential.
Reduced Wear and Enhanced Durability
The combination of UHMW’s high molecular weight and low friction coefficient results in remarkable wear resistance. In practical terms, this means that UHMW plastic components can endure extensive usage without succumbing to wear and tear.
Whether it’s in conveyor systems, automotive components, or industrial machinery, UHMW’s durability is a game-changer.
Low Moisture Absorption and Chemical Resistance
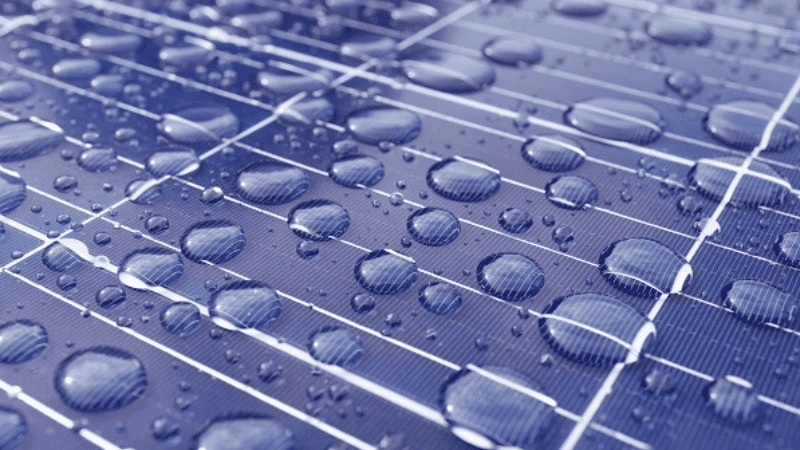
Another compelling feature of UHMW plastic is its low moisture absorption rate. This attribute is of significant importance, particularly in applications where exposure to moisture or humidity is a concern.
UHMW plastic’s low moisture absorption contributes to its overall dimensional stability and ensures that it maintains its outstanding properties even in damp environments.
Additionally, UHMW plastic exhibits exceptional chemical resistance. This quality makes it an excellent choice for environments where exposure to a wide range of chemicals is a daily occurrence.
Whether in chemical processing equipment or laboratory settings, UHMW’s resistance to chemical degradation ensures its longevity and reliability.
In summary, UHMW plastic, with its unique molecular structure and exceptional properties, is a material that continues to redefine possibilities across various industries.
Its high molecular weight, low friction coefficient, resistance to wear, low moisture absorption, and chemical resistance combine to make it an indispensable choice for applications where performance, durability, and reliability are paramount.
The Manufacturing and Processing of UHMW Plastic
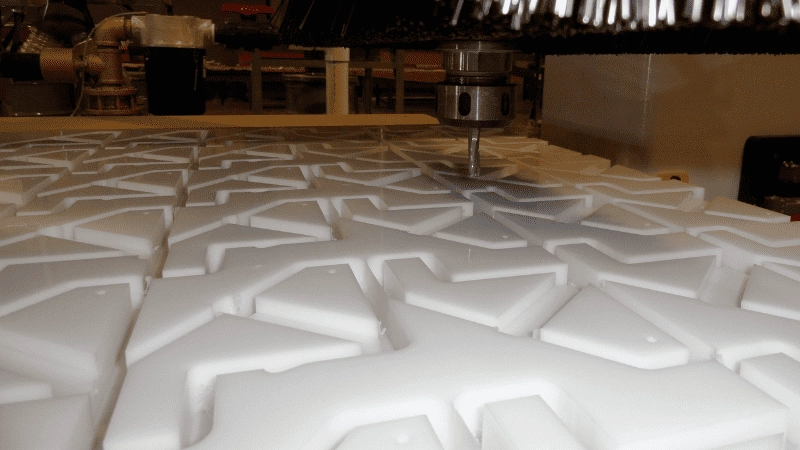
The production of Ultra-High Molecular Weight (UHMW) plastic is an intricate process that begins with the polymerization of ethylene.
This process is fundamental to creating the long molecular chains that define UHMW plastic’s exceptional properties. Let’s dive deeper into the manufacturing and processing journey of this remarkable material.
Ethylene Polymerization: Creating the Foundation
The journey of UHMW plastic starts with ethylene, a simple hydrocarbon gas. Through a process called polymerization, ethylene molecules are transformed into long and interconnected chains.
This is achieved by subjecting ethylene to specific catalysts and conditions, allowing the molecules to bond together, forming what is known as high molecular weight polyethylene.
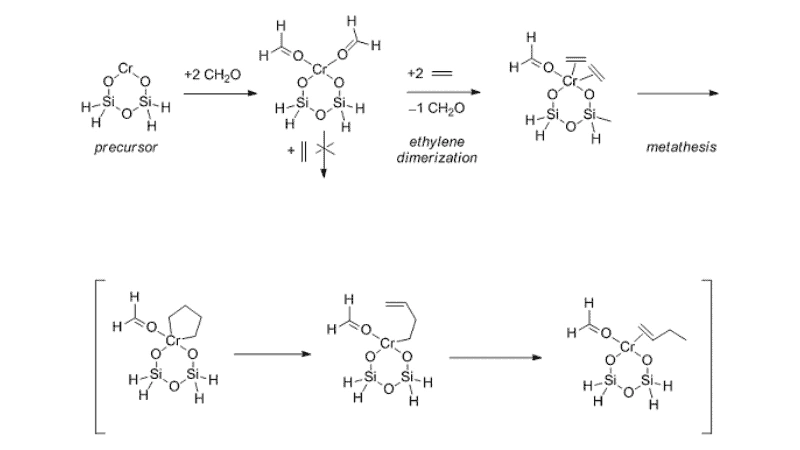
The key distinction of UHMW plastic lies in the length of these molecular chains. The polymerization process for UHMW plastic encourages the creation of molecular chains that are exceptionally long, often extending to millions of carbon atoms.
This gives rise to the ultra-high molecular weight that sets UHMW plastic apart from other polyethylene materials.
Molecular Weight: The Backbone of Excellence
The high molecular weight of UHMW plastic is the backbone of its exceptional properties. These long molecular chains are like the sturdy strands of a molecular rope, providing strength and durability.
Additionally, this extended molecular structure contributes to its low coefficient of friction and outstanding wear resistance.
The Role of Crystalline Lamellae
Within the molecular structure of UHMW plastic, crystalline lamellae are significant components that define its properties. Crystalline lamellae are regions within the material where the polymer chains are organized in a regular, repeating pattern. These regions contribute to the material’s overall strength and stiffness.
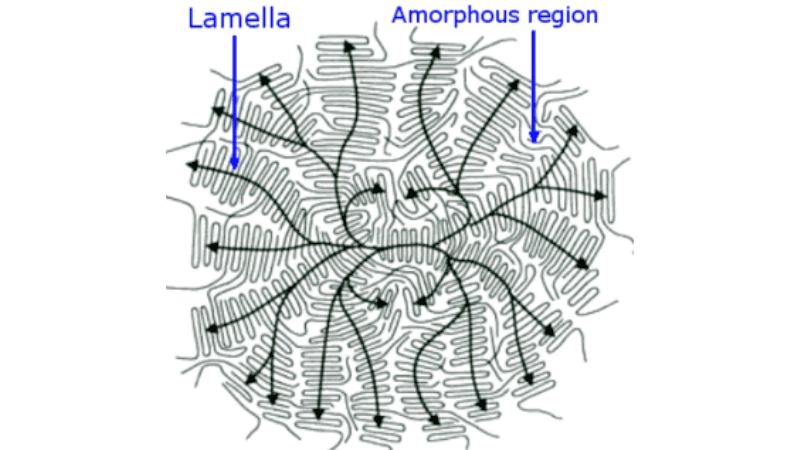
Crystalline lamellae play a crucial role in enhancing UHMW plastic’s durability. They act as reinforcing structures, effectively distributing mechanical stresses and preventing deformation. This unique arrangement of crystalline lamellae contributes to UHMW plastic’s ability to withstand high loads and maintain its structural integrity.
Cross-Linking for Enhanced Properties
To further enhance its properties, UHMW plastic can undergo a process known as cross-linking. Cross-linking involves creating additional chemical bonds between the polymer chains. This creates a three-dimensional network within the material, adding strength and stability.
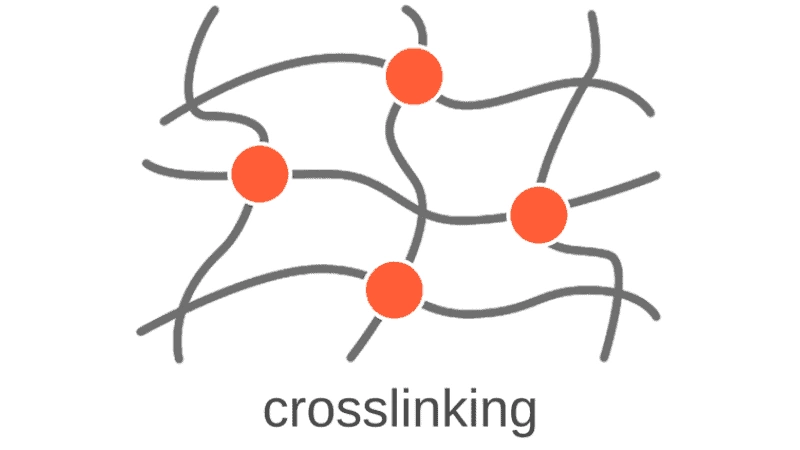
Cross-linked UHMW plastic exhibits improved resistance to wear and abrasion. It also exhibits enhanced dimensional stability, making it particularly suitable for demanding applications where precision and durability are paramount.
The cross-linking process transforms UHMW plastic into a material that excels in challenging environments, making it a top choice in industries such as automotive manufacturing and heavy machinery.
In summary, the manufacturing and processing of UHMW plastic are intricate and specialized procedures that result in a material with extraordinary properties. The polymerization of ethylene leads to the creation of high molecular weight polyethylene, setting the stage for UHMW plastic’s unique characteristics.
Crystalline lamellae within its molecular structure enhance its strength, while cross-linking further augments its properties, making UHMW plastic an indispensable material in numerous industrial and commercial applications.
Take the First Step:
Requst for an Inquire
Quality Meets Affordability. Inquire Now for High-Quality Products at Low Volumes.
Applications of UHMW in the Manufacturing Sector
UHMW plastic finds widespread use in various industries, thanks to its exceptional properties. Some key applications include:
- Conveyor Systems: UHMW is an excellent choice for conveyor components due to its low friction and wear properties, ensuring efficient material handling.
- Bearings and Bushings: Its abrasion resistance makes UHMW an ideal material for bearings and bushings, reducing friction and extending service life.
- Medical Devices: UHMWPE components are used in the production of artificial joints, harnessing their extremely strong and wear-resistant qualities.
- Automotive Industry: UHMW plastic contributes to the automotive industry by reducing friction, improving efficiency, and enhancing the overall performance of various components.
- Food Processing: UHMW’s low coefficient of friction and excellent chemical resistance make it a top choice in food processing equipment, ensuring hygiene and efficiency.
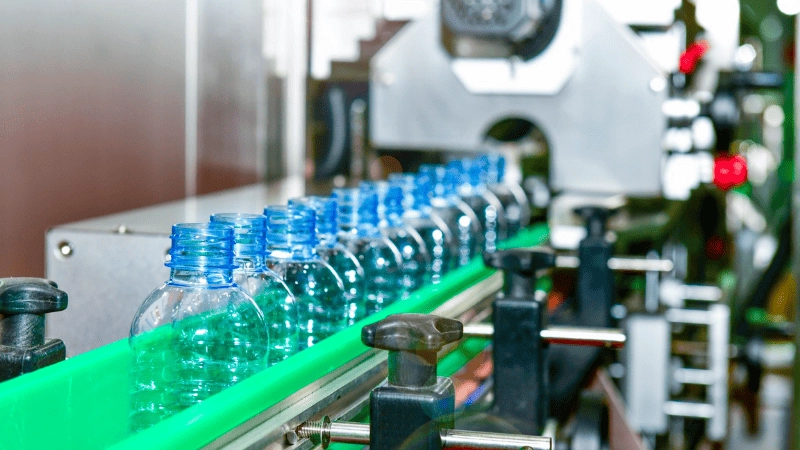
UHMW in Industrial Equipment
In industrial settings, UHMW plastic components have become indispensable. Its use extends to:
- Conveyor Belts: UHMW conveyor belts offer a perfect balance between durability and efficiency. They reduce friction, allowing products to glide smoothly along the production line. Moreover, they often feature RGB lights for easy tracking of product flow.
- Wear Plates: In heavy machinery, wear plates made from UHMW plastic ensure that components withstand high loads and maintain their structural integrity. This technology has revolutionized industries like mining and construction.
- Impact Strength: The impact strength of UHMW plastic is unparalleled. This makes it suitable for applications where materials must withstand high loads and shock absorbers.
Comparative Advantages of UHMW Plastic
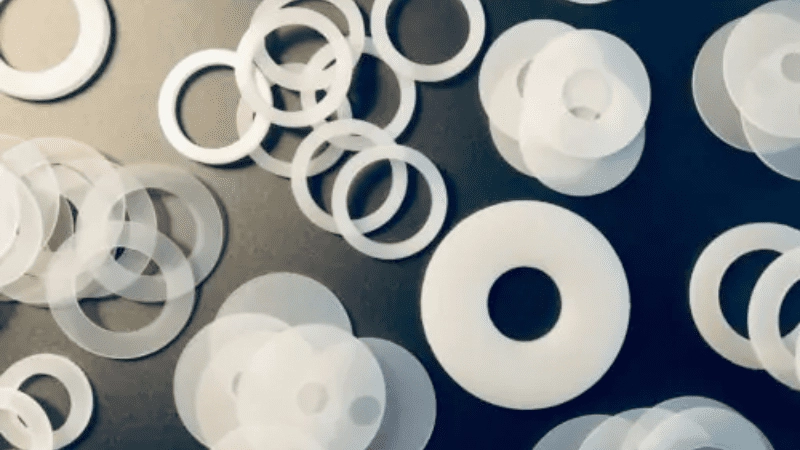
To truly grasp the significance of UHMW plastic, it’s essential to compare its properties with those of other materials commonly utilized in both industrial and commercial applications. This comparative analysis highlights the exceptional qualities that set UHMW plastic apart.
Below is a comparison table between UHMWPE (Ultra-High Molecular Weight Polyethylene) and some common types of plastic:
Property/Type | UHMWPE | LDPE (Low Density Polyethylene) | HDPE (High Density Polyethylene) | PP (Polypropylene) | PVC (Polyvinyl Chloride) | PET (Polyethylene Terephthalate) |
---|---|---|---|---|---|---|
Density (g/cm^3) | ~0.930-0.935 | 0.910-0.940 | 0.941-0.965 | 0.855-0.946 | 1.16-1.35 | 1.38-1.39 |
Tensile Strength (MPa) | 20-45 | 8~24 | 20-32 | 25-35 | 40-60 | 50-75 |
Impact Strength | Very High | Low | Moderate | High | Low to Moderate | Low |
Wear Resistance | Excellent | Poor | Moderate | Moderate | Moderate | Poor |
Chemical Resistance | Excellent | Good | Good | Good | Good (except solvents) | Good |
Processing Temperature (°C) | Difficult above 160 | 140-220 | 150-260 | 160-230 | 160-210 | 240-280 |
Applications | Wear parts, gears, liners | Films, bags | Bottles, pipes | Packaging, fibers | Pipes, cable insulation | Bottles, fibers |
Melting Point (°C) | 130-136 | 105-115 | 126-134 | 160-170 | 75-90 (for unplasticized) | 250-260 |
UV Resistance | Good | Poor | Good | Good | Poor | Good |
Cost | Higher | Low | Low | Low | Moderate | Moderate |
Analysis: From the comparison table, UHMWPE distinctly stands out in several key areas when juxtaposed against other common plastics:
- Impact Strength: UHMWPE has an exceptionally high impact strength, making it resistant to sudden impacts and stresses.
- Wear Resistance: UHMWPE showcases superior wear resistance, signifying that products made from it would have a longer lifespan under frictional applications.
- Chemical Resistance: With excellent chemical resistance, UHMWPE can be applied in environments where it might be exposed to various chemicals without degrading.
- UV Resistance: Good UV resistance ensures that UHMWPE-based products can maintain their properties even when exposed to sunlight for prolonged periods.
However, it’s also important to note that UHMWPE is on the pricier side and might pose challenges in processing at higher temperatures.
Highlighting UHMW’s Advantages: UHMWPE shines in its unparalleled wear and impact resistance, making it ideal for heavy-duty applications. Additionally, its excellent chemical and UV resistance ensures durability in diverse environments. Despite its processing challenges, its superior attributes make it an invaluable material in specialized sectors.
Take the First Step:
Requst for an Inquire
Quality Meets Affordability. Inquire Now for High-Quality Products at Low Volumes.
Challenges and Limitations of UHMW Plastic
While UHMW plastic offers a plethora of advantages, it’s not without its challenges and limitations. Understanding these is crucial for ensuring their effective use and addressing potential issues in various applications.
1. Processing Challenges Due to High Molecular Weight
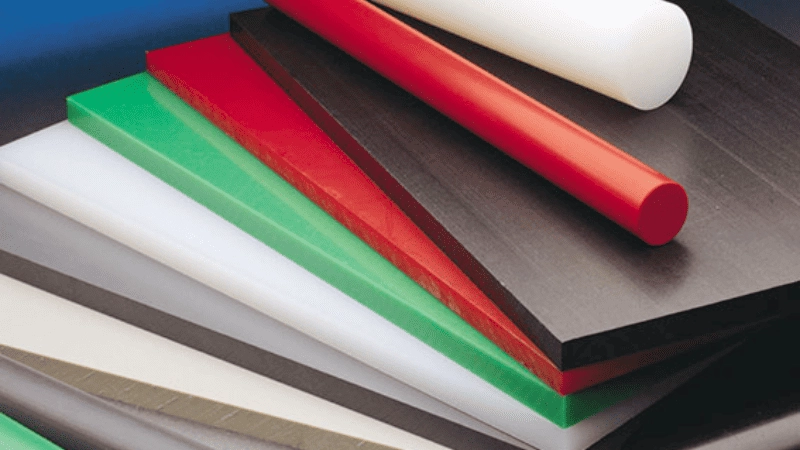
One of the most prominent challenges associated with UHMW plastic is its exceptionally high molecular weight. While this feature is responsible for many of its remarkable properties, it can also pose unique challenges during processing.
The molecular weight of UHMW plastic far exceeds that of conventional plastics, resulting in extraordinarily long polymer chains.
This characteristic necessitates specialized equipment and techniques for molding and shaping the material. Manufacturers often rely on advanced technologies like compression molding, ram extrusion, or sintering to achieve the desired product forms.
These specialized processing methods require precision and expertise, which can translate into higher production costs. However, the investment is often justified by the outstanding performance and longevity that UHMW plastic delivers.
2. Temperature Sensitivity and Potential Warping
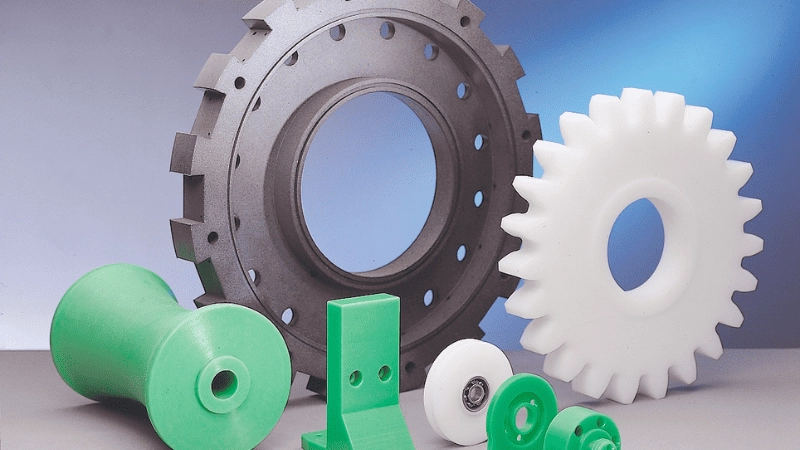
UHMW plastic can exhibit sensitivity to temperature variations, particularly extreme shifts in temperature. This sensitivity can potentially lead to warping or dimensional changes in certain applications.
To mitigate this challenge, engineers and designers must carefully consider the operating environment of UHMW plastic components.
Adequate insulation, temperature control, or thermal management solutions may be necessary in situations where temperature fluctuations are expected. By taking proactive measures, the risk of warping or deformation can be minimized, ensuring the material’s continued reliability.
3. Environmental Considerations: Recycling and Disposal
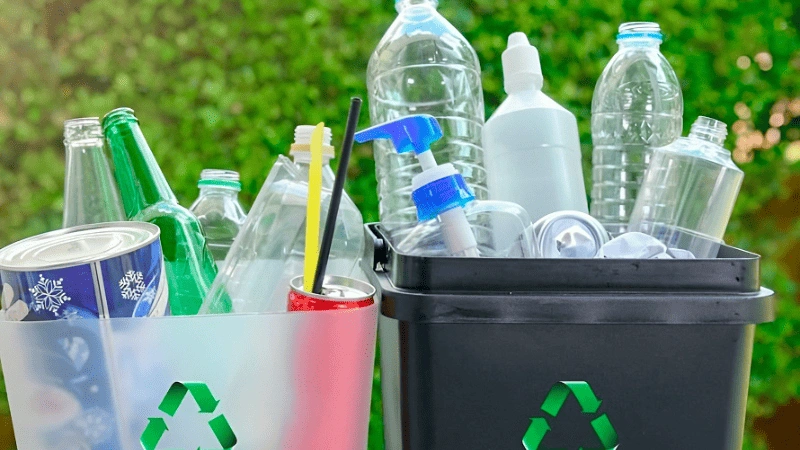
In an era where sustainability is paramount, addressing the environmental impact of materials like UHMW plastic is critical. While UHMW plastic is renowned for its durability, this very trait can pose challenges in terms of recycling and disposal.
Due to its long-lasting nature, UHMW plastic components remain in service for extended periods. However, when they eventually reach the end of their lifecycle, responsible disposal becomes a concern.
Unlike materials that degrade over time, UHMW plastic persists in its original form for an extended duration, which can lead to accumulation in landfills if not managed properly.
Efforts to address this concern include the development of recycling programs specific to UHMW plastic. By systematically collecting and recycling UHMW plastic components at the end of their life, companies can reduce their environmental impact and contribute to a more sustainable future.
Sustainability Efforts in UHMW Production
As the world increasingly turns its focus toward sustainability, the production of UHMW plastic has not remained immune to these concerns. Forward-thinking companies are actively implementing measures to minimize the environmental footprint associated with UHMW plastic production.
1. Recycled UHMW Plastic
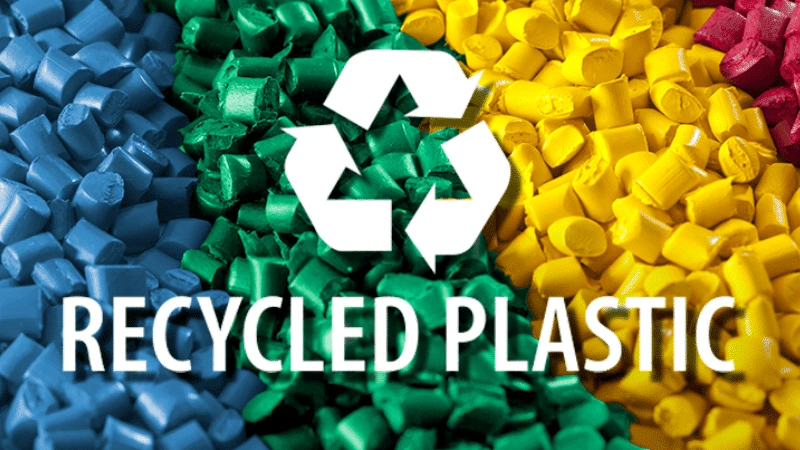
A notable stride toward sustainability in UHMW plastic production is the incorporation of recycled materials into the manufacturing process. This eco-conscious approach serves a dual purpose.
First, it reduces the demand for virgin raw materials, lessening the environmental impact of extraction and processing. Second, it helps alleviate the issue of plastic waste by repurposing materials that might otherwise end up in landfills.
By utilizing recycled UHMW plastic, companies not only contribute to a more sustainable future but also showcase their commitment to responsible resource management.
2. Efficient Manufacturing Technologies
Advancements in manufacturing technologies have revolutionized the landscape of UHMW plastic production. Modern processes prioritize efficiency, energy conservation, and reduced emissions. These developments are pivotal in making UHMW plastic production more environmentally friendly.
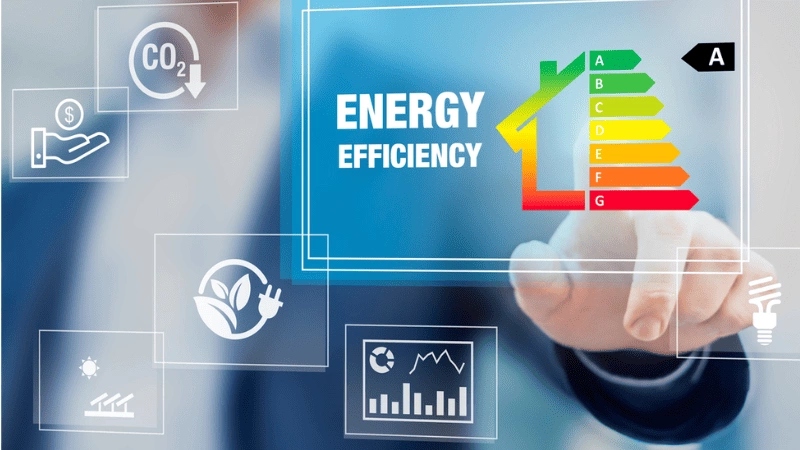
Energy-efficient technologies minimize energy consumption during production, reducing the carbon footprint associated with UHMW plastic manufacturing. Simultaneously, these technologies optimize resource utilization, leading to fewer material losses and less waste generation.
Reduced emissions from UHMW plastic production contribute to improved air quality and a healthier environment. Companies are actively investing in equipment and processes that adhere to stringent environmental standards.
These sustainable manufacturing practices not only benefit the planet but also position UHMW plastic as a responsible choice for businesses and industries committed to environmental stewardship.
Take the First Step:
Requst for an Inquire
Quality Meets Affordability. Inquire Now for High-Quality Products at Low Volumes.
Conclusion
In summary, UHMW plastic combines durability with sustainability, excelling in wear resistance and chemical resilience. While processing challenges exist, innovations using recycled materials enhance its eco-friendliness. As global sustainability needs grow, UHMW showcases that strength and eco-responsibility can align, pointing industries toward a greener future.
Discover the perfect solution for your business with Hongju!
Discover the perfect solution for your business with Hongju, a leading provider of UHMW plastic and other innovative technologies.
Whether you’re looking to enhance the durability of your products or explore more sustainable manufacturing options, Hongju has the resources and quality you need and improve your business. Join us now in embracing the future of durable goods with UHMW plastic.