While these materials share some similarities, their main differences lie in their production process and ability to withstand heat. So let’s dive in!
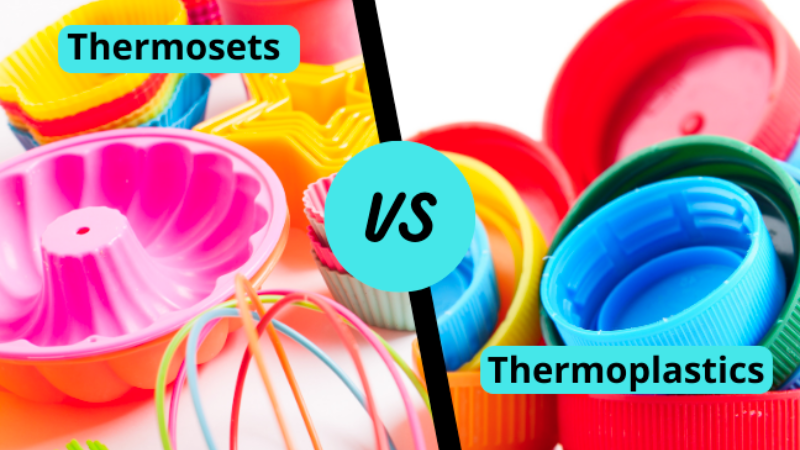
What is Thermoplastic?
Thermoplastics are a fascinating type of plastic that possesses the unique ability to be melted and re-molded numerous times without undergoing any chemical changes.
The molecular structure of thermoplastics can be either linear or branched, which contributes to their exceptional behavior. When subjected to heat, these plastics have the capacity to soften, allowing for easy reshaping and manipulation. Conversely, when cooled, they regain their original solid state, providing them with durability and stability.
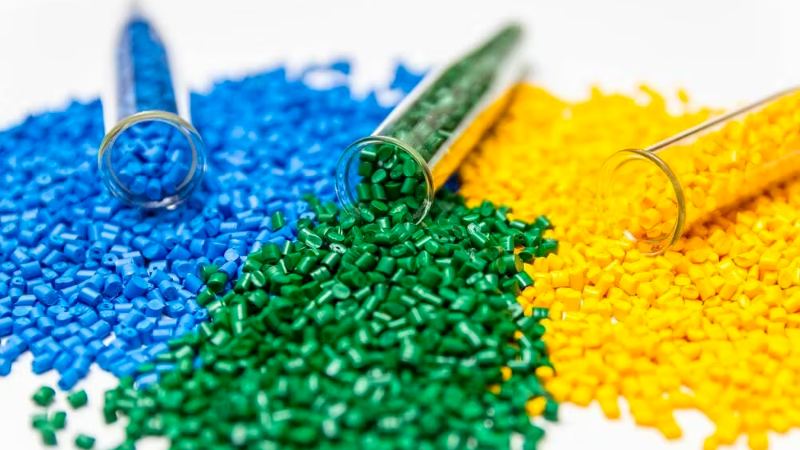
Some of our most common thermoplastic polymers include Polyethylene (PE), Polypropylene (PP), Polystyrene (PS), Polyvinyl Chloride (PVC), and Polyethylene Terephthalate (PET). These materials are widely used in various industries due to their versatility and ease of processing.
What is Thermoset?
Thermosets are a special kind of polymer that goes through a process called curing, where they experience irreversible chemical reactions. This transformation causes thermoset materials to become rigid and unable to be melted or reshaped, even when exposed to high temperatures. Additionally, the rigidity of thermoset materials ensures that they maintain their shape and structural integrity over time, making them suitable for long-term use in various industries.
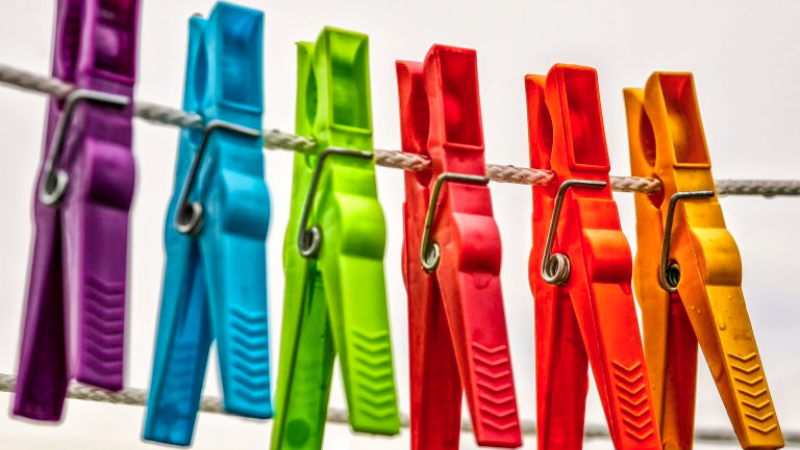
However, it is important to note that once a thermoset has been cured, it cannot be reprocessed or recycled like thermoplastics can. This limitation contributes to the environmental concerns surrounding the disposal and waste management of thermoset materials.
Nonetheless, with their exceptional properties and wide range of applications, thermosets continue to play a significant role in numerous industries that require durable and high-performance materials.
Properties and Applications of Thermoplastics
Thermoplastics possess a range of material properties that distinguish them from thermosets. These physical properties contribute to their widespread use in various industries and applications.
Properties of Thermoplastics
Let’s explore some of their material and physical properties:
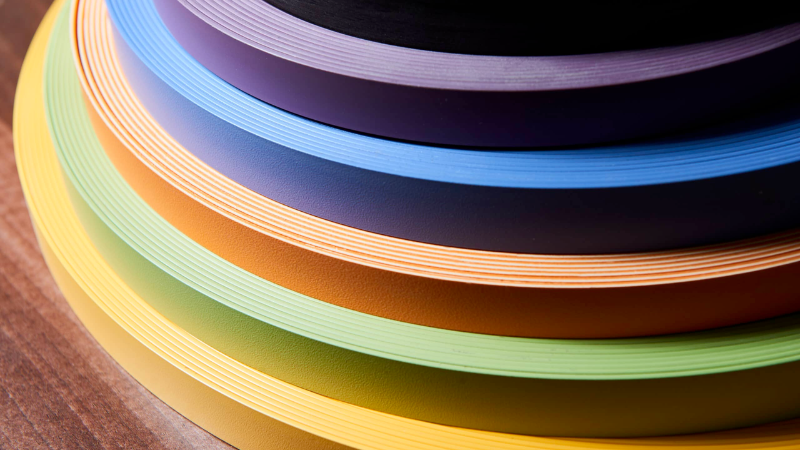
- Toughness and flexibility: One key characteristic of thermoplastics is their ability to undergo reversible changes in molecular structure. This property grants them high toughness and flexibility, allowing them to withstand impact and deformation without breaking easily.
- Lower melting points: In comparison to thermosets, thermoplastics have lower melting points. This attribute makes them highly suitable for processes such as injection molding or extrusion, where the material needs to be heated and shaped. The lower melting points facilitate easier processing, enabling manufacturers to efficiently produce complex shapes and intricate designs.
- Recyclability: Another advantage of many types of thermoplastics is their recyclability. This is possible due to the reversible nature of their curing process. Once thermoplastic pellets soften when heated, they become more fluid as additional heat is applied. The curing process is completely reversible as no chemical bonding takes place during this process, making it completely reversible.
This characteristic allows thermoplastics to be reworked and recycled without affecting their physical properties.
By understanding these different properties exhibited by thermoplastics, designers and engineers can make informed choices when selecting materials for specific applications. Whether it’s the need for toughness and flexibility or the requirement for ease of processing and recyclability, thermoplastics offer versatile solutions across various industries.
Applications of Thermoplastics
Thermosetting polymers offer a multitude of advantages in various industries, including automotive, packaging, and construction. Their versatility allows them to be used in a wide range of applications.
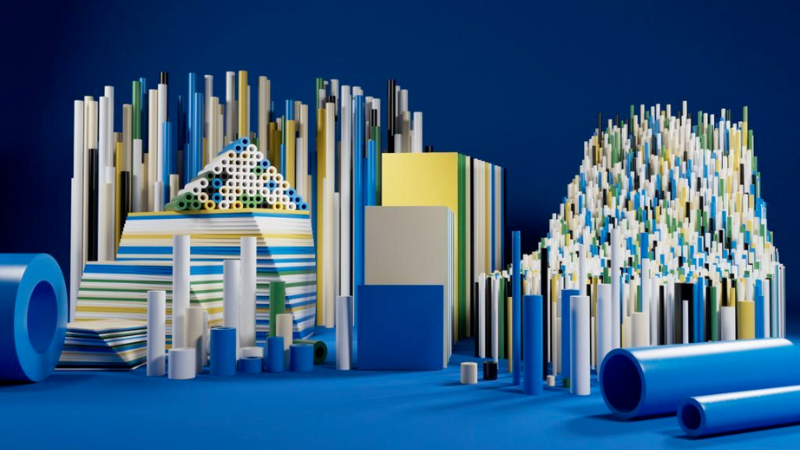
- Packaging: Thermoplastics are widely used in the packaging industry, thanks to their durability, resistance to moisture, and flexibility. They are used to make bottles, jars, bags, and other packaging materials that protect products during transportation and storage.
- Automotive: Thermoplastics are widely used in the automotive industry, thanks to their durability, low weight, and resistance to corrosion. They are used for various components, including dashboards, door panels, seat covers, and other interior trim.
- Construction: Thermoplastics are widely used in the construction industry, thanks to their weather resistance, ease of processing, and low cost. They are used for various applications, including pipe fittings, waterproofing membranes, and building siding.
- Electronics: Thermosetting polymers are widely used in the electronics industry, thanks to their non-conductivity, insulating properties, and low cost. They are used to make casing, brackets, and other components for electronic devices.
- Healthcare: Thermosetting polymers are widely used in the healthcare industry, thanks to their resistance to bacteria and ease of cleaning. They are used for various applications, including medical devices, laboratory equipment, and diagnostic tests.
Furthermore, the repairability and modifiability of thermoplastic components are noteworthy attributes. If damaged or requiring modification, these components can be easily repaired or modified without compromising their strength or functionality.
Properties and Applications of Thermosets
Thermosetting polymers, such as thermosets, possess unique properties that make them highly desirable for various applications. These materials exhibit excellent dimensional stability even at high temperatures due to their structure.
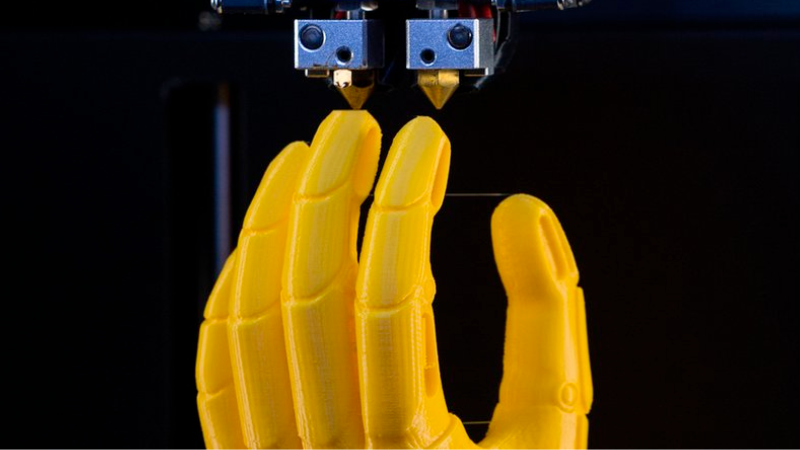
Properties of Thermosets
Here are some key characteristics of thermosets:
- Dimensional Stability: Thermosets maintain their shape and size even when exposed to extreme heat or pressure. This is because the crosslink density in these polymers prevents them from melting or deforming easily.
- Superior Chemical Resistance: Thermosets offer exceptional chemical resistance, making them suitable for applications where exposure to harsh substances is common. They can withstand corrosive environments without deteriorating or losing their structural integrity.
- Excellent Electrical Insulation: Due to their inherent properties, thermosetting polymers serve as excellent electrical insulators. They have a high glass transition temperature, which means they can withstand elevated temperatures without compromising their electrical performance.
- High Strength and Rigidity: Once cured, thermosets exhibit remarkable toughness, strength, and rigidity. This makes them ideal for structural applications where durability and load-bearing capabilities are crucial.
Applications of Thermosets
The unique thermoset properties and wide range of applications make them a versatile and valuable material for a wide range of industries, here are some of the most common applications of thermoset plastics:
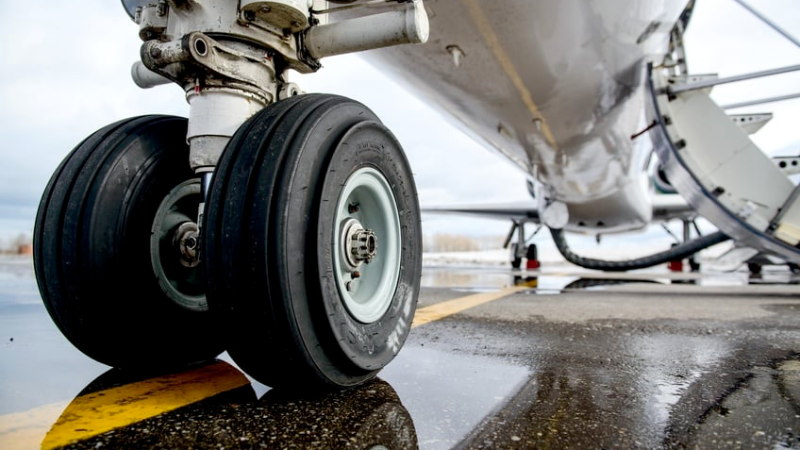
- Construction: Thermosetting Plastics are widely used in the construction industry for applications such as insulation boards, roofing materials, flooring systems, windows, pipe fittings, and other structural components. Thermoset plastics are also used for construction projects that require high levels of fire resistance, moisture resistance, and thermal insulation.
- Transportation: Thermosetting plastics are widely used in the transportation industry for applications such as brake pads, clutches, and engine components due to their resistance to heat and friction. They are also used for applications that require high levels of endurance, such as brake and timing belts, and gears.
- Electrical: Thermosetting Plastics are used for manufacturing electrical components such as insulated wires, transformers, motor windings, and other electrical applications. They are also used for applications that require high levels of insulation, electrical insulation, and resistance to high voltage and frequencies.
- Electronics: Thermoset plastics are used for manufacturing electronic components such as printed circuit boards, electronic packaging, and other high-performance electronic applications. They are also used for applications that require precision manufacturing, such as lead-free soldering systems, semiconductor packaging, and other microelectronics applications.
- Sports: Thermoset plastics are used for manufacturing sports equipment such as golf clubs, tennis rackets, and other sporting equipment that require high levels of durability, resilience, and elasticity. They are also used for applications that require low weight and high strength-to-weight ratios, making them ideal for applications that require high levels of performance and precision.
Comparison of Thermoplastics and Thermosets
Thermoplastics and thermosets are two types of plastics that differ in their properties and applications. Understanding the differences between these materials is crucial when considering their use in various industries.
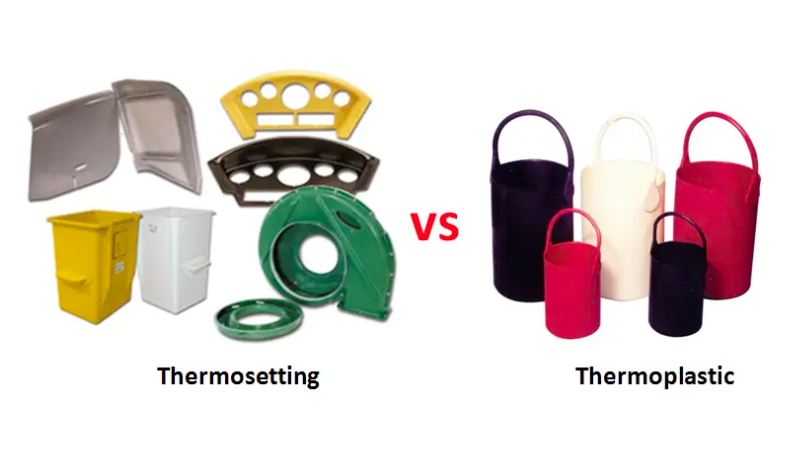
The Main Difference of Thermoplastics and Thermosets
Thermoplastics can be melted multiple times, making them highly versatile. This characteristic allows for easy reshaping and recycling, reducing waste and promoting sustainability.
Thermosets, on the other hand, undergo irreversible curing reactions during processing. Once cured, they cannot be melted or reshaped like thermoplastics. This property gives them exceptional strength and durability, making them suitable for applications where rigidity is required.
Factors Should Be Considered
When choosing between thermoplastics or thermosets, several factors need to be considered:
- Desired material properties: If flexibility and recyclability are essential requirements, thermoplastics are a better choice. However, if high strength and rigidity are necessary, thermoset plastics excel in these areas.
- Processing requirements: The manufacturing process differs significantly for each type of plastic. Thermoplastics can be easily molded using techniques such as injection molding or extrusion. In contrast, thermoset plastics typically require more complex processes like compression molding or reaction injection molding.
- End-use application: The specific application also plays a vital role in selecting the appropriate material. For example:
- Automotive parts often require the strength provided by thermoset plastics due to safety considerations.
- Packaging materials may benefit from the flexibility and recyclability of thermoplastics to reduce environmental impact.
Choosing the Right Material for Your Needs
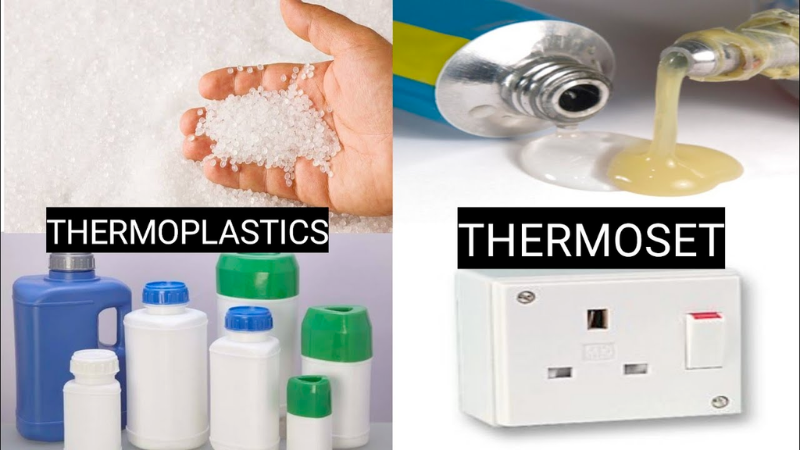
When choosing between thermoplastics and thermosets, think about what you need. Thermoplastics are better for easy processing and change in shape, while thermosets are better for strong and long-lasting applications.
To make an informed decision about which material is right for you, consider factors such as desired properties (e.g., flexibility vs. rigidity), processing requirements (e.g., injection molding vs. curing), intended application (e.g., packaging vs. aerospace), budget constraints, and environmental considerations.
Conclusion
In conclusion, the choice between thermoplastics and thermosets depends on the specific requirements of the application, and both materials have their own strengths and weaknesses. Therefore, it is essential to consider the specific requirements of the application and consult with industry experts before making a decision on which material to use.
Buy High-Quality Plastic Materials from Hongju
If you are looking for high-quality thermoplastics and thermosets, Hongju Silicone is an excellent place to start. We offer a wide range of plastic products that can be customized to meet your specific needs, and our commitment to quality and sustainability makes it a trustworthy partner for your plastics needs.
Take the First Step:
Requst for an Inquire
Quality Meets Affordability. Inquire Now for High-Quality Products at Low Volumes.