This blog post will look at how silicone rubber compares to other common elastomers. We’ll discuss what makes it special and why it could be the best pick for your business. Ready to learn more? Let’s get started.
What Is Silicone Rubber
Silicone rubber is a very special type of rubber. It’s made from silicone, a polymer containing silicon with carbon, hydrogen, and oxygen. Unlike regular rubber, silicone rubbers don’t come from trees. It’s man-made in labs using a process called vulcanization. This is when heat and pressure are used to make the rubber strong and elastic.
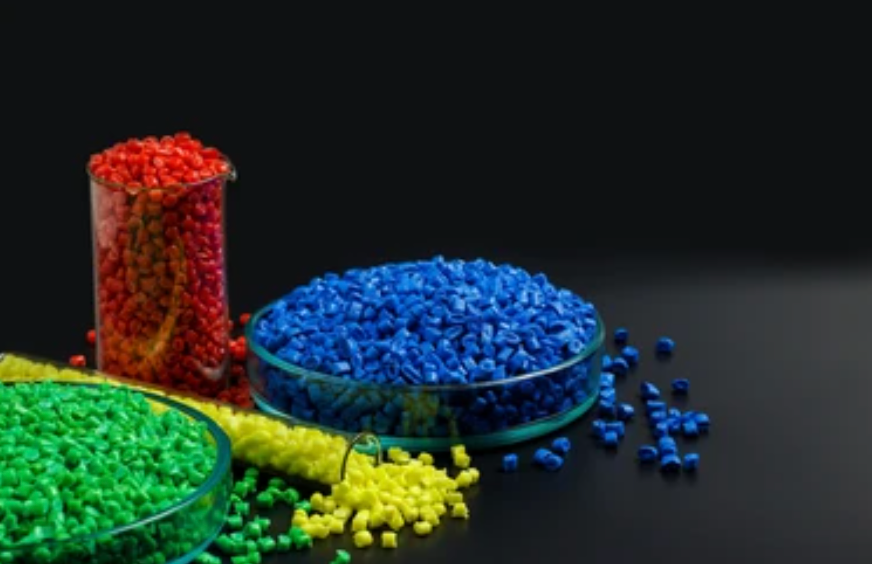
What Are The Properties of Silicone Rubber
Silicone rubber is known for its fantastic properties. Here are some of them:
- Highly resistant to temperature: It can withstand hot and cold temperatures.
- Long-lasting: It doesn’t wear out easily, making it durable.
- Flexible and stretchy: It can bend and stretch without breaking.
- Waterproof: It doesn’t let water pass through.
- Resistant to chemicals: Most chemicals don’t affect it.
Application Examples
Silicone rubber is used in many ways because of its great properties. Here are some examples:
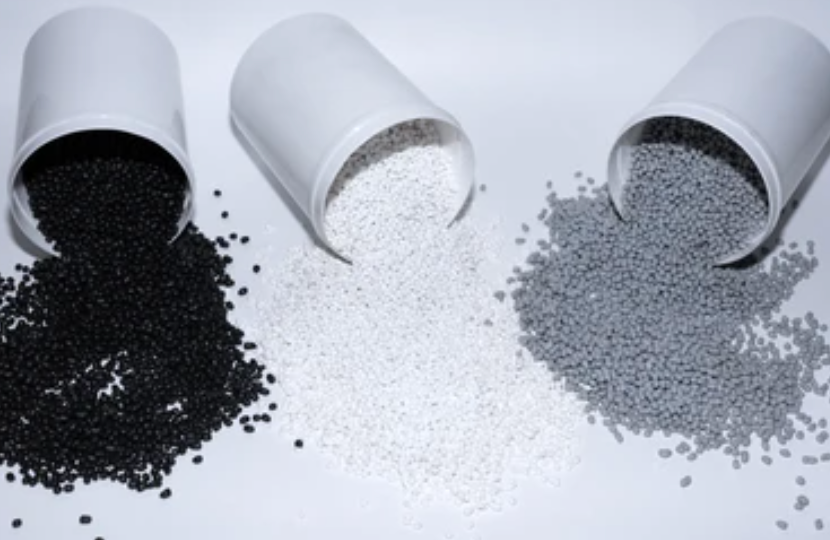
• Door and Window Seals: Silicone rubbers are an excellent material for door and window seals. Its flexibility allows it to maintain its shape despite regular compression and decompression when opening and closing doors and windows. In addition, it offers excellent thermal insulation, keeping indoor environments warm during colder months and vice versa.
• Kitchen Utensils: Silicone rubbers are used in various kitchen tools like spatulas, baking mats, and ice cube trays. It’s a food-safe material that can withstand various temperatures, from freezing cold to oven-hot, without degrading or releasing harmful substances. Its flexibility also makes it ideal for utensils that need to bend or flex during use.
• Electronics: Silicone elastomers are an excellent insulating and protective material in electronics. It coats wires, provides insulation in power supplies, and encapsulates electronic assemblies. It’s resistant to electricity, stable across a wide temperature range, and offers excellent protection against moisture, making it ideal for sensitive electronic components.
• Healthcare: Silicone elastomer is commonly used in various medical applications. Its biocompatibility makes it safe for implants and medical devices directly interacting with the body. It’s also easy to sterilize, a critical factor in medical environments to prevent contamination and infection.
• Automotive: In the automotive industry, silicone thermoplastic elastomer is utilized in components like gaskets, hoses, and spark plug boots. Its resistance to heat and aging makes it suitable for high-temperature, high-stress environments like car engines. It also provides excellent sealing properties, ensuring no unwanted leakage of fluids.
Silicone Rubber Vs. Other Elastomers
When comparing silicone rubber with other elastomers like natural rubber, nitrile rubber, and neoprene, it’s clear that each has its strengths. However, silicone rubber often stands out in several key areas. Let’s take a closer look:
Silicone Rubber | Natural Rubber | Nitrile Rubber | Neoprene | |
Elasticity and Flexibility | High | High | Medium | Medium |
Versatility | High | Medium | High | Medium |
High Resistance | High | Low | High | High |
- Elasticity and Flexibility: Silicone thermoplastic elastomer is highly elastic and flexible, allowing it to stretch and bend without damage. It can retain its original shape even after extensive stretching, far outperforming natural rubber, nitrile rubber, and neoprene.
- Versatility: Silicone rubber’s versatility makes it a top choice in various industries. For example, it’s used in the automotive, healthcare, electronics, and food and beverage sectors. Its versatility is higher compared to natural rubber and neoprene.
- High Resistance: Silicone rubber excels in resistance to extreme temperatures, UV light, and many chemicals. It can withstand temperatures from -60°C to 230°C, making it more resistant than natural rubber.
Different Elastomers
As we delve further into the world of elastomers, we must recognize that not all are created equal. Each type, from natural rubber to thermoplastic elastomers (TPEs) and liquid silicone rubber (LSR), brings unique properties and applications to the table.
Natural Rubber
Natural Rubber has:
- High elasticity and flexibility: Ideal for products that require stretch and rebound.
- Good resistance to abrasion and wear: Used in tires and shoe soles.
- Poor resistance to high temperatures and chemicals can degrade under these conditions.
Compared to Silicone thermoplastic elastomer, natural rubber doesn’t perform as well under extreme temperatures or when exposed to certain chemicals. Silicone rubber also tends to last longer due to its superior aging properties.
Thermoplastic Elastomers (TPEs)
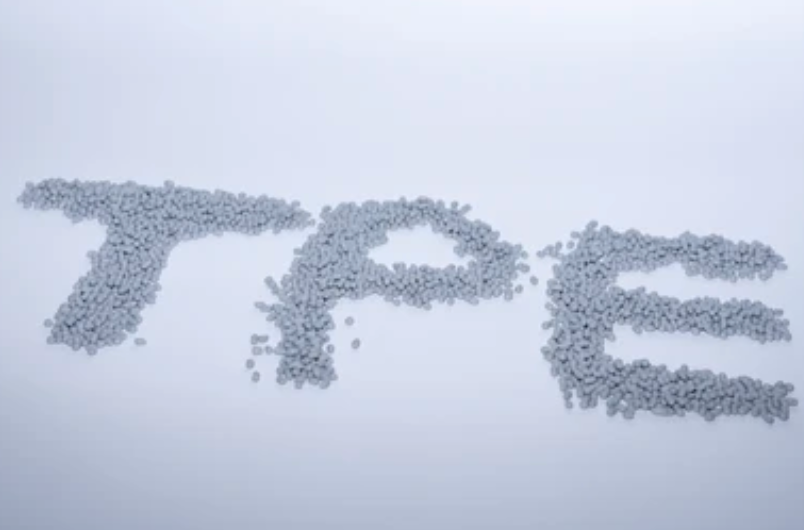
TPEs are rubber-like materials that can be melted and reshaped. They have:
- Flexibility at room temperature: They’re soft and stretchy but have relatively low abrasion resistance.
- Ability to be molded and colored: This makes them versatile for design.
- Recyclability: They can be reused, reducing waste.
Compared to Silicone Elastomers, Thermoplastic elastomers can’t withstand as high temperatures or resist as many types of chemicals. Their durability may also be lower, depending on the specific type of Thermoplastic elastomers and their formulation.
Liquid Silicone Rubber (LSR)
Liquid silicone rubber is a type of silicone rubber that’s liquid until it’s molded and heated. It has:
- High thermal stability: It can withstand high and low temperatures.
- Excellent flexibility and durability: It’s resilient and lasts a long time.
- Biocompatibility: It’s safe for use in medical applications.
Compared to other forms of silicone, Liquid silicone rubber can be easier to mold into complex shapes and fine details, making it ideal for precise applications like medical devices and intricate seals. Its liquid form also allows for faster and more efficient production.
Manufacturing Processes And Applications of Other Elastomers
Let’s take a closer look at the manufacturing processes and practical uses of other elastomers. We’ll explore materials like natural rubber, TPEs, and LSR, understanding how they are made and where they are applied in different industries. Get ready to discover the fascinating world of elastomer manufacturing and its wide-ranging applications.
Injection Molding Process for Elastomers
The injection silicone molding process is a cool way to make things from elastomers. Here’s how it works:
What is Injection Molding? Injection molding is when you melt the elastomer material and shoot it into a mold using an injection molding machine. It cools down and becomes solid in the shape of the mold. Then, you take the molded part out of the mold.
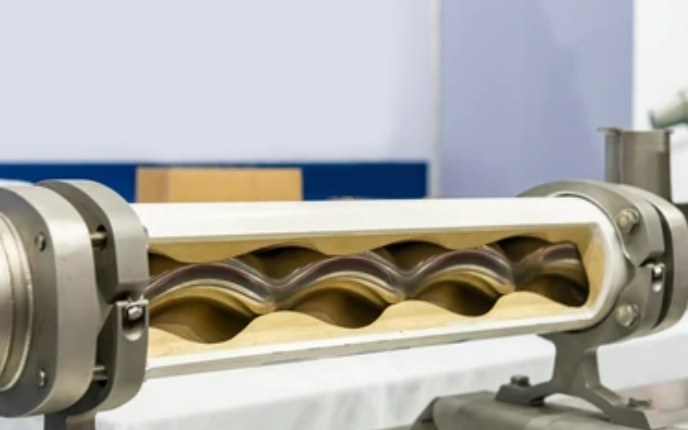
Special Considerations for Silicone and TPE Injection Molding: Silicone rubbers and thermoplastic elastomer material (TPEs) need some extra care during injection molding.
- Silicone Injection Molding: Silicone is thick, so it can be hard to fill the mold. They heat it up before injecting it to make it easier. The mold must also be designed differently because silicone polymer doesn’t shrink much.
- TPE Injection Molding: TPEs are easy to melt and mold again. This makes the process faster. But the molds for TPEs need to be made for lower temperatures and pressures.
Applications of Other Elastomers
- Natural Rubber: Natural rubber is used in lots of things! You can find it in car tires, hoses, belts, and even surgical gloves. It’s bouncy and strong, so it’s great for things that need to flex and last a long time.
- Thermoplastic Elastomers (TPEs): TPEs are flexible and can easily be molded into different shapes. They’re used in things like toys, tools with soft grips, and car parts. People like them because they’re fun to play with and can be made in cool colors.
- Liquid Silicone Rubber (LSR): LSR is special. It’s used in making medical things like seals and tubes because it’s safe and can be really precise. You can also find it in electronics and car parts. Even baby bottle nipples are made with LSR!
So, there are different ways to make elastomers, and they have many uses. Injection molding helps make elastomer products, and silicone, TPEs, and LSR each have their own cool applications in different industries.
Conclusion
In conclusion, understanding different elastomers’ properties, manufacturing processes, and applications is crucial for making informed decisions. Silicone thermoplastic elastomer offers unique advantages, but exploring natural rubber, TPEs, and LSR expands possibilities for various industries. We’re here to support your elastomer needs and help you make the right choices for your business. Thank you for joining us on this elastomer exploration, and we look forward to serving you.
Take the Next Step in Your Elastomer Journey – Learn More About Us!
Ready to explore the world of elastomers further? Visit our website to discover more about Hongju Silicone and our expertise in providing high-quality silicone rubber products. Whether you need custom solutions or have specific requirements, contact us; our team is here to assist you.