Designing Silicone Rubber Keypad
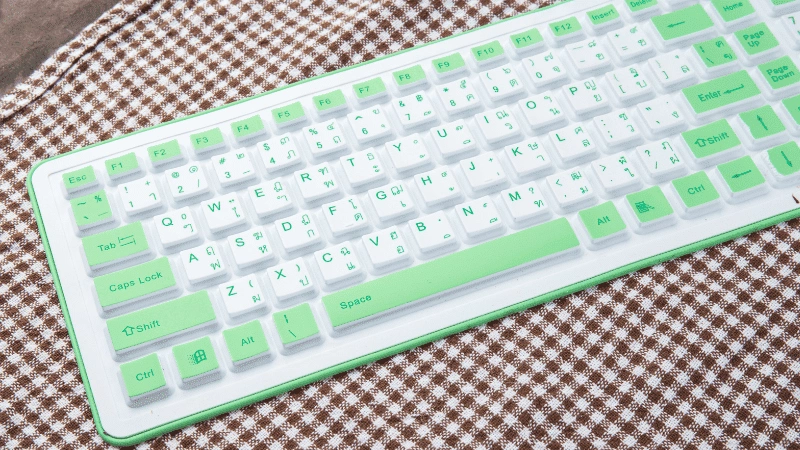
Silicone keypads can be customized in several ways to accommodate many applications. Despite the vast range of applications, the core steps involved in the design phase remain the same.
Here are the five key design elements of silicone rubber keypad that need to be considered. Let’s take a look together!
Dimensional Accuracy
The first and most crucial step for all designers is “Dimensional Accuracy.” Inaccurate or overly complex dimensions can halt the entire design process. Silicone rubber keypads and PCB (Printed Circuit Board) designs are co-dependent. If the silicone rubber keypad design fails, it will negatively impact the PCB design. In the worst-case scenario, you will re-design the circuit and the silicone rubber keypad.
Fortunately, with a few primary considerations, you can minimize errors and mistakes in your design. Following are a few general dimension guidelines.
- Unit Accuracy
Be consistent with your measurement units. Stick with either the imperial (inches) or metric (meters) units, and always label the units on the top of your drawings. If you decide to go with metric units, be consistent here as well, don’t use “cm” and “mm” in the same drawing. Write 100mm instead of 10cm.
Imperial units are more common in North American regions, but metric units are easier to define. Silicone or rubber keypad designs have very thin profiles, and inches are not ideal for measuring such small dimensions.
- Dimensional Tolerance
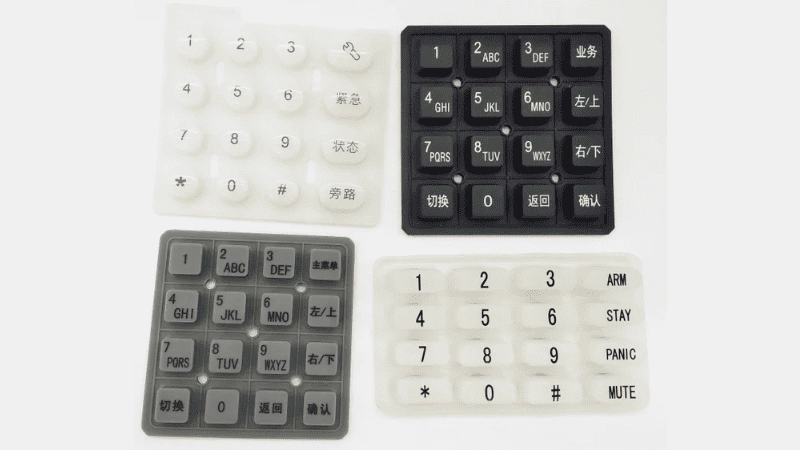
Tolerance is present in every industry. It is an unfortunate and unavoidable part of manufacturing. Rubber keypad designs will have a standard tolerance of 1%. For a 10mm wide design, the final product width can vary between 9.9mm to 10.1mm.
Luckily 1% dimensional tolerance is excellent for most applications. But if your particular application requires even better tolerances. Be mindful of the fact that manufacturers do offer tighter tolerances but at a cost premium.
- Layout
In rubber keypad design, layout refers to the distance between the keys/buttons and surrounding elements. Most keypad design molds have a physical limit on the inter-key distance, the distance between two adjacent keys/buttons. This limits the number of buttons per square mm of area.
Additionally, keypads require several locating holes after every few buttons. Buttons also cannot be placed too close to the edge or bezel of the keypad. A good design should consider all these elements to maximize the button layout.
- Standard Dimensions
Here are the standard dimensions for the keypad design. These are general guidelines to simplify the layout and dimension of keypads.
Inquire About Our Silicone and Plastic Products!
Button Design
Buttons have two distinct parts. The upper visible part has the lettering printed, and the lower hidden part has electrically conductive contacts interacting with the PCB. The lower part is called a dome and is responsible for the switching function of a keypad. While the upper part is just a keycap designed for better comfort and aesthetics.
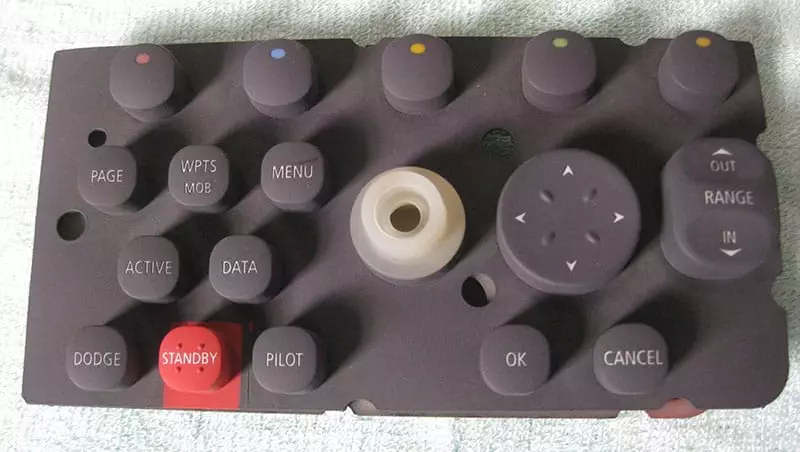
- Button Types
Buttons can be divided into two broad categories.
- Separate Designs – The Keycap is a separate element placed on top of a dome switch. This button type is most common in membrane keyboard manufacturing, where you can replace the plastic keycaps without damaging the silicone dome switch.
- Combined Designs – The keycap and the dome switch are fused into one unit. This type of button is most common in TV remotes.
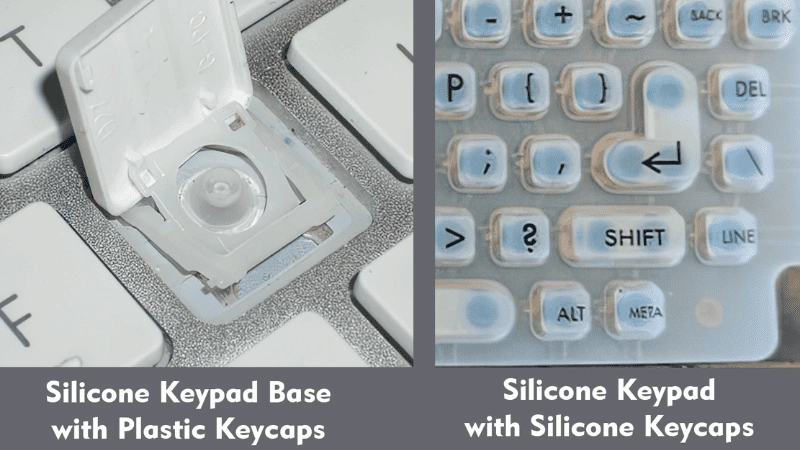
- Key Travel Distance
Key Travel distance is the verticle height a button must travel before a signal is detected on the circuit board. This distance is the gap between the circuit board and the inside of the dome switch.
A larger travel distance will require more force to press a button. Additionally, it will result in a slight but noticeable delay in the input signal. Input delay is a much more important factor for keyboard designs and less important for TV remotes.
- Switch Domes
The underside of a dome has an electrical contact, which is responsible for the switching function. This electrical contact is called a switch, and you can get two types of switches for your button domes.
- Metal Switch Domes
- Polyester Switch Domes
The metal switch has a plate attached to the base of the dome button. While the polyester switch uses a plastic plate with printed silver on the bottom surface. Metal switches have better reliability, better conduction, and higher costs. Polyester switches are low-cost alternatives to metal switches.
Inquire About Our Silicone and Plastic Products!
Tactile Response
Tactile response is the perceived feeling of touch when a button is pressed. Tactile feel is a metric for determining the accuracy of button presses.
A button press has 3 phases of the force application.
- Actuation force (Fa)
- Contact force (Fc)
- Return force (Fr)
To have good tactile feedback, button webbing is a key element because button webbing will affect actuation force. Silicone button actuation force not only is affected by the raw material hardness, but also affected by surface coating thickness, mold tool technology, and material placement in compression molding. Actuation force is the initial effort required to push the button down. This is the largest amount of force required to initiate a button press.
Contact force is the second phase of pressing. Once a button starts moving downwards, a smaller force is required to initiate a point of contact between the dome switch and the circuit board.
Return force is the resistance of the rubber keypad to return to its original position. It is the force with which the dome pushes the button back up.
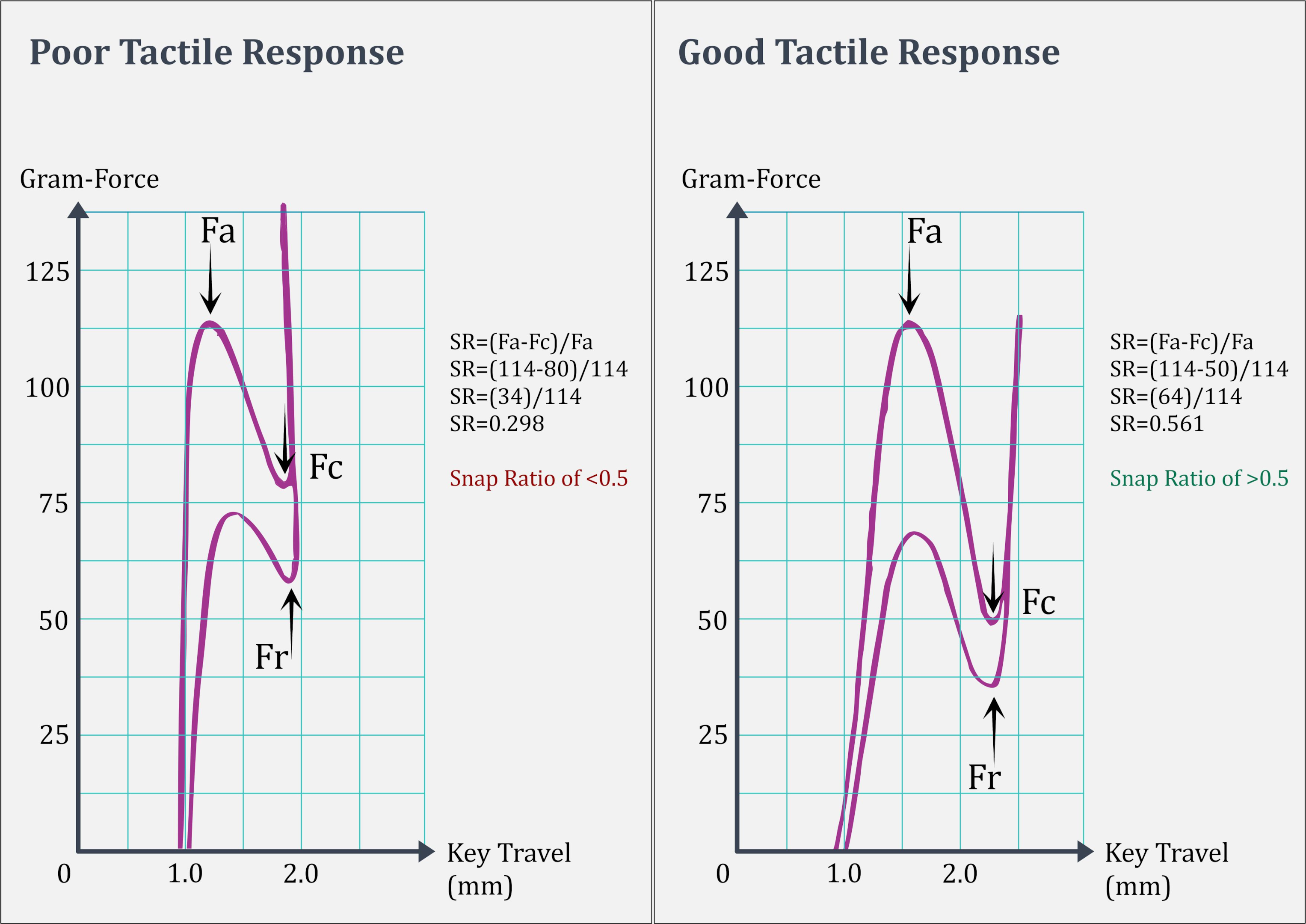
- Snap Ratio
Snap ratio measures the force differential between actuation and contact force to an actuation force. The following formula calculates it.
SR = (Fa -Fc)/Fa
A snap ratio of less than 0.5 is considered a weak tactile feel. Because there is very little difference between the actuation force and the contact force, for a good tactile feel, you should aim for a snap ratio of 0.5 or more.
Inquire About Our Silicone and Plastic Products!
Customization
Once you have determined all the practical factors of a silicone rubber keypad, you can focus on customization.
- Color Selection
Silicone rubber keypads can have colored buttons that are different from the base color. Colored buttons are made of separate colored silicone attached to the surface of the silicone rubber keypad.
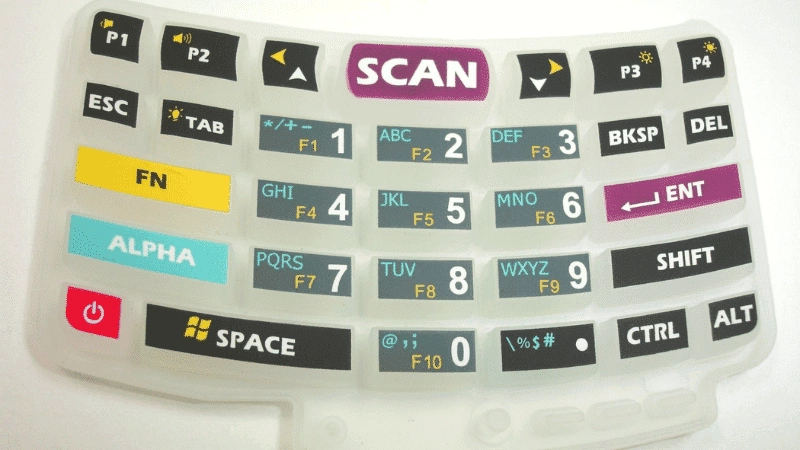
- Material Selection
Most silicone rubber keypad designs use soft-touch rubber keycaps. But you also can use hard rubber keycaps and plastic keycaps that are fused on top of the rubber keycaps.
- Printing
Finally, the simplest way of customizing a silicone rubber keypad is printing. You can select almost any color for the lettering on top of your buttons. Just be sure that the letter and button colors are compatible and easy to read.
Additionally, you can color in the buttons by printing color on them. This method is an uncommon alternative to using colored silicone buttons. The particular method of printing used in printing letters on buttons is called silk screening or legend printing.
If you don’t like the look of printed letters, you can also ask the manufacturer to use laser etching for the lettering.
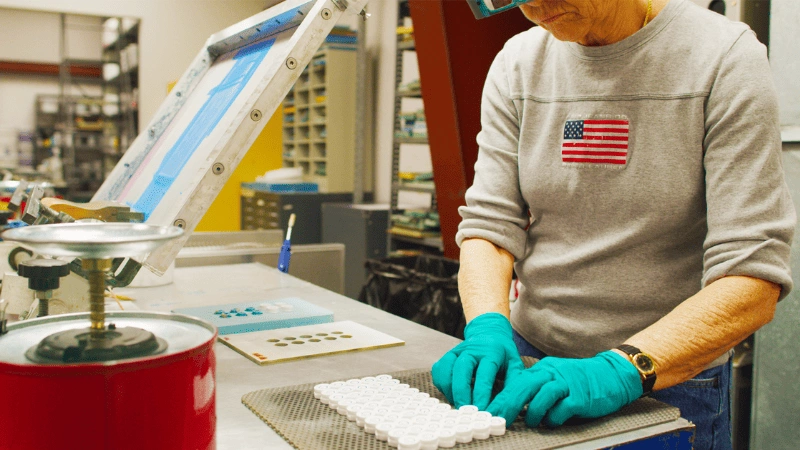
Lifespan
Lifespan is the last factor you must consider in your silicone rubber keypad design. Silicone is a soft but sturdy material; for most applications, a silicone rubber keypad will last a very long time.
However, there are a few criteria that can impact the lifespan of a keypad. Staying within the following criteria will result in longer life for your keypads.
- Temperature
Silicone rubber has a decent operating temperature range. It can withstand temperatures up to 150 ˚C and temperatures as low as -40 ˚C.
- Corrosion
Silicone rubber has excellent natural corrosion resistance. However, exposure to certain harsh chemicals can degrade the silicone over time.
- Actuation
Excess actuation force will decrease the lifespan of your keypad. Most keypads’ general operating actuation range is between 60-300 grams.
- Button Press
A standard silicone rubber keypad should have a hardness of “60 Shore A“, the same as a pencil eraser. At this hardness, keypads should withstand a minimum of 1 million button presses (strokes).
Inquire About Our Silicone and Plastic Products!
Conclusion
Silicone rubber keypads are incredibly versatile. They can be deployed in almost any environment and customized to specific applications. Be mindful of your dimensions and button spacing for the best results.
We hope you will use the information from this silicone rubber keypad design guide when designing your silicone rubber keypad. For high-quality silicone rubber manufacturing, we recommend you check out Hongju Silicone.
We make keypads, o-rings, gaskets, and other general-purpose silicone products. To get a free quote and inquire about free samples, Contact Us Now!