Medical devices and equipment are critical in the healthcare industry. They not only help save lives, but they also protect healthcare professionals from hazards.
However, these devices must be safe and meet regulatory standards since they come in contact with the body. Fortunately, with surface finishes, medical equipment is safer and non-hazardous.
However, not all surface finishes are the same. Although there are different surface finishes for medical devices, silicone rubber finish stands out. This article explores silicone rubber finish for medical devices, its properties, and why it is ideal.
What Is Silicone Rubber Finish?
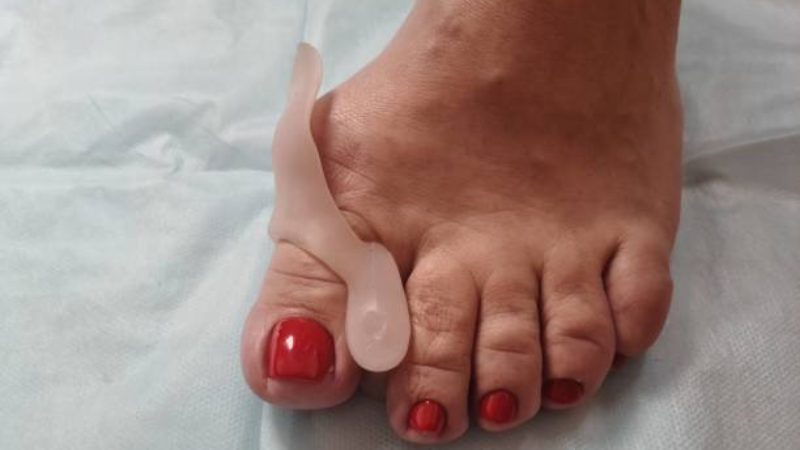
The silicone rubber finish is a protective coating or surface treatment made from silicone rubber. The finish is often applied to the surface of a material to give it extra protection, improve its durability, and enhance its performance. Materials that can be coated with silicone rubber finish include glass, textiles, metals, and plastics.
Because silicone elastomer finishes include additives, there are different types. Each type has its function since it is customized to meet the requirements of a specific application. Silicone finishes are useful in the aerospace, automotive, medical, and electronic industries.
What Are the Properties of Silicone Rubber?
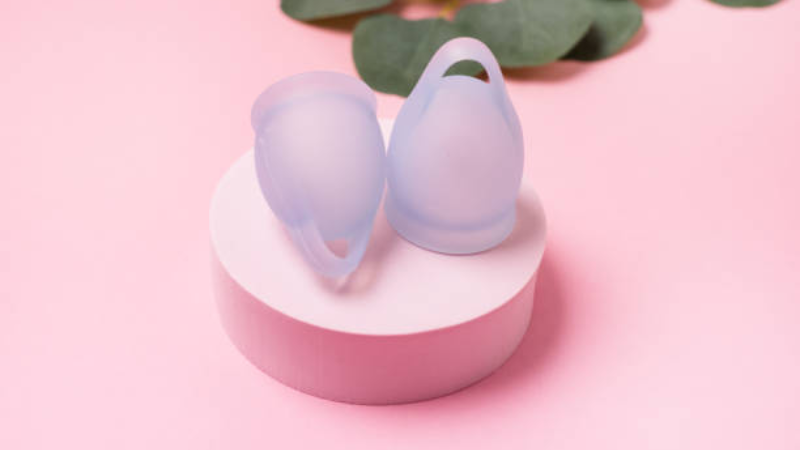
Silicone elastomers are used across several industries for their exceptional chemical and physical properties. This elastomer’s properties that make it stand out in the medical industry include the following.
Heat Resistance
Silicone rubber can withstand temperatures as high as 450 degrees Fahrenheit. Therefore, even at high temperatures, silicone rubber retains its properties and does not degrade. Due to its heat resistance, silicone rubber is widely applicable in the medical industry, especially when high-temperature sterilizations need to be used.
Biocompatibility and Low Toxicity
The medical industry needs devices that do not cause allergic reactions when they come in contact with the human body. Silicone rubber is inert and has low toxicity. In addition, the material is biocompatible and does not leach when exposed to high temperatures or sterilized. Hence, it is used for producing medical devices and equipment.
Flexibility
Silicone rubber is flexible and easily molded into different shapes and sizes. Consequently, the material manufactures medical devices with intricate designs and patterns.
Injection molding and compression molding are common processes for molding silicone components. The best method for manufacturing medical devices will depend on the size, design complexity, and parts’ properties.
Durability
Silicone rubber is durable. And this is due to its excellent abrasion resistance and tear strength – the material can undergo deformation without losing its properties. The material can also withstand harsh conditions, making it useful for extended periods.
Chemical Resistance
Silicone rubber can resist chemicals, including oils, acids, and bases. It can also withstand the chemicals used for cleaning and sterilizing medical equipment without losing its color or properties.
Tear Strength
Silicone rubber has excellent tear strength. The material can withstand repeated use with minimal wear and tear. Consequently, silicone rubber is an excellent choice for coating medical devices. The material protects the device, allowing it to be used for as long as possible.
UV and Weather Resistance
Silicone rubber can withstand weather and UV radiation. In addition, the elastomer retains its properties in harsh conditions. Therefore, it is suitable for use in outdoor applications. You can learn more about UV-resistant rubber from our website.
What Types of Silicone Rubber Are Suitable for Medical Devices?
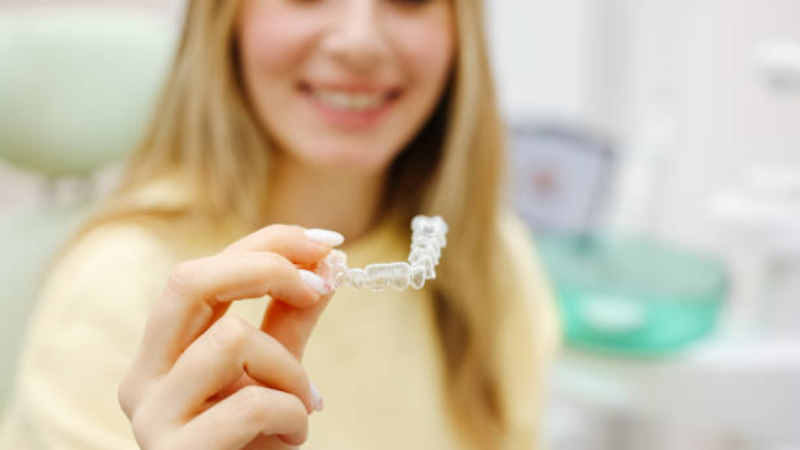
There are different types of silicone rubber, and they have varying physical forms, curing methods, and properties. The choice of a type of silicone rubber depends on the medical device, its design, and its intended properties.
High Consistency Rubber (HCR)
HCR is used in the medical industry because it can be molded into complex shapes and sizes using transfer, compression, or injection molding.
Furthermore, this type of silicone rubber is reinforced with additives that improve its tear strength, flexibility, and heat resistance. As a result, HCR rubber is used to manufacture flexible and durable medical devices.
Liquid Silicone Rubber (LSR)
Liquid silicone rubber is a viscous, two-part liquid elastomer with excellent properties that make it suitable for the medical industry. This elastomer is non-toxic and biocompatible. Furthermore, liquid silicone rubbers can be molded into complex medical devices that require precision through liquid injection molding. All in all, liquid silicone rubber has many advantages.
Room Temperature Vulcanizing (RTV)
RTV silicone rubber cures at room temperature. This type of silicone rubber is suitable for manufacturing medical devices that require electrical insulation and high thermal stability.
Fluorosilicone
Fluorosilicone rubber is silicone rubber with fluorine as an additive. This additive improves the properties of silicone rubber, including compression, stability, and chemical resistance. Consequently, medical devices made from this type of silicone rubber are ideal for applications that require frequent chemical exposure. We have written a blog to discuss whether fluorosilicone or silicone is better.
Medical Grade Silicone
Medical-grade silicone is silicone rubber that is certified safe for manufacturing medical devices and equipment. This type of silicone rubber undergoes stringent rules before it is certified safe for medical applications. The properties of medical-grade silicone include sterility, bio-compatibility, and non-toxicity.
What Are the Key Benefits of Using Silicone Rubber Finishes on Medical Devices?
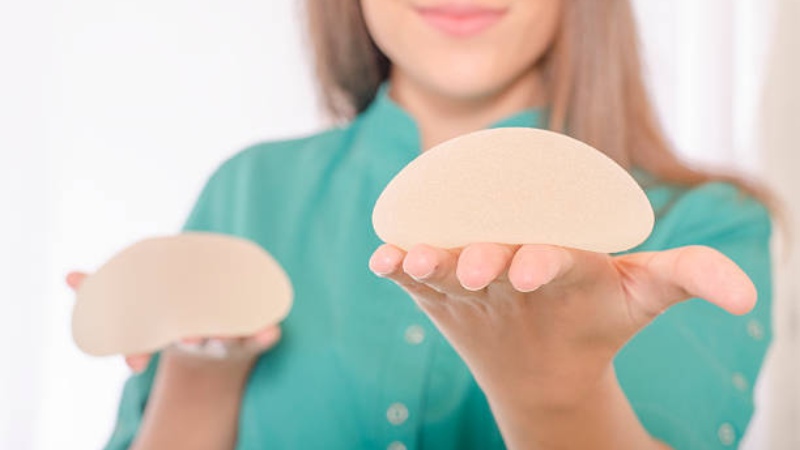
Coating medical devices with silicone rubber finishes have several benefits. The coating improves the flame resistance, antimicrobial properties, abrasion resistance, and durability of medical devices. Other key benefits of using silicone rubber on medical devices include the following.
1. Chemical stability: the medical industry often deals with exposure to different types of chemicals. Silicone rubber finishes protecting medical devices’ surfaces, making them prone to abrasion, scratching, and chipping.
2. Marking and decoration: silicone rubber finishes can be reinforced with additives for a more colorful coating. Besides decorating medical devices, colored silicone rubber finishes can be used to mark the devices. Thus, if there are any defective devices, they can be identified easily and traced back to the source.
3. Reinforcing hospital furniture: Bedside seating, treatment tables, and chemotherapy chairs are used and cleaned frequently. Frequent cleaning and sanitization can cause wear and tear. However, despite frequent sanitizations, the furniture can retain its shape and appearance with silicone rubber coating.
4. Protecting medical personnel: medical personnel uses wearables like aprons, surgical gowns, gloves, and shoe covers for protection. Furthermore, using protective clothing protects medical personnel from infection and cross-contamination. It is also required for regulatory performance. Medical protective clothing is usually coated with a silicone rubber finish to prevent exposure to hazardous substances.
The Types of Protective Coatings Available for Medical Devices
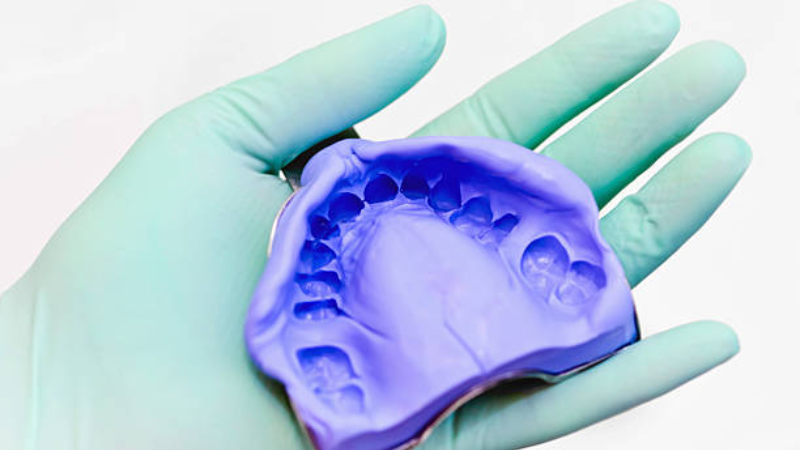
There are different types of protective coatings for medical devices. The choice of a suitable protective coating depends on the specific requirements of the device. The types of protective coatings for medical devices include;
1. Silicone rubber coatings: These types of coatings are made from silicone rubber and other additives. Silicone rubber coatings are employed in the medical industry due to their excellent chemical and mechanical properties, like biocompatibility, chemical resistance, and temperature resistance.
Furthermore, silicone coatings protect the surface of medical equipment, extending its lifespan and improving its look.
2. Polyurethane coatings: Polyurethane coatings have a thin and uniform texture that protects the surface of a medical device. This type of coating keeps out moisture and chemicals. It is also biocompatible and can withstand environmental factors. However, polyurethane coatings have poor heat resistance. Their chemical resistance is also poor, and the coating can become brittle when exposed to repeated impact.
3. Chloroprene rubber coatings: chloroprene or neoprene is also used in the medical industry due to its excellent properties like water resistance, chemical resistance, and abrasion resistance. However, compared to silicone coating, chloroprene coating cannot tolerate extreme temperatures; in some cases, it may cause allergic reactions.
4. Polyvinyl chloride (PVC): PVC coatings are also used in medical devices because of their moisture resistance and grip. They also provide a decent level of protection. However, the downside of PVC coatings is that the material is non-biocompatible and may contain materials that pose a health risk.
5. Acrylic: Acrylic coatings are also used to protect medical devices from moisture and dirt and to improve durability. In addition, this type of finish is biocompatible.
Therefore, it is more suitable for medical devices like prosthetics and implants that come in direct contact with the body.
Besides biocompatibility, acrylic coatings improve the chemical resistance of coated medical devices and equipment. The downside of acrylic coating is its low impact resistance and poor chemical and temperature resistance.
Why Does Silicone Rubber Provide the Ideal Finish for Medical Devices?
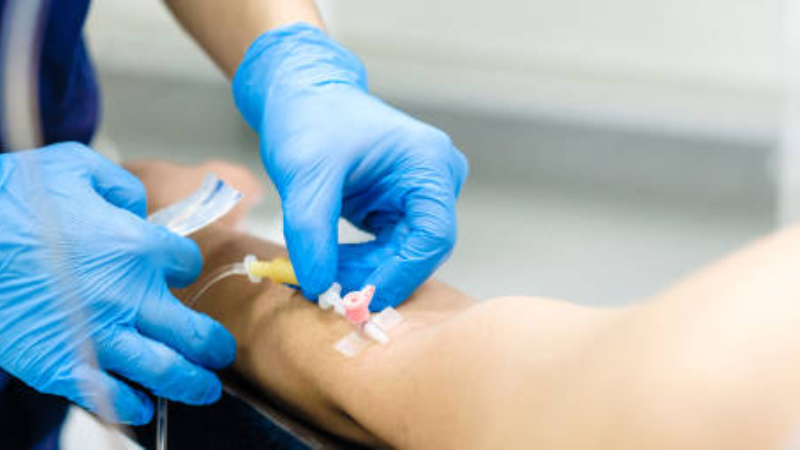
Silicone rubber is not the only biocompatible and chemically resistant finish. Nevertheless, this finish is suitable for medical devices compared to others. The advantages of silicone rubber finish over other finishes include its temperature resistance, flexibility, and non-stick properties.
Silicone rubber finish can withstand extreme temperatures without degrading. The material can withstand temperatures up to 450 degrees Fahrenheit.
In addition, the material is flexible and moldable into different medical devices over a durometer range, depending on the application. The non-stick properties of silicone rubber finish ensure they are easy to use and prevent blockages in devices like catheters.
The Importance of Durability and Safety for Medical Devices Components
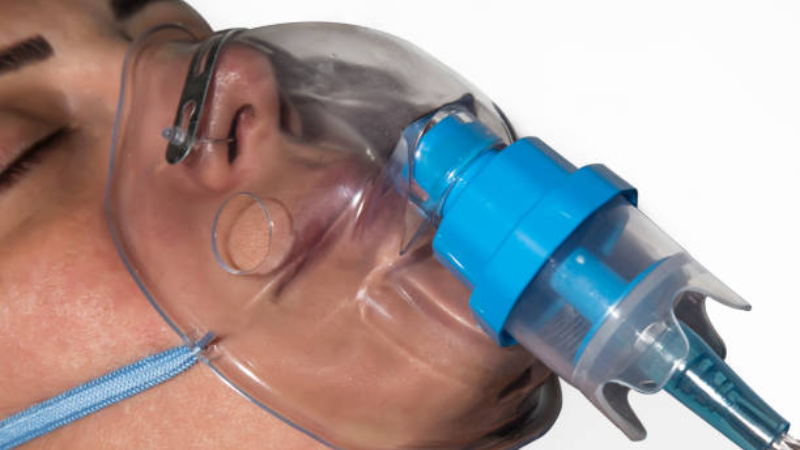
Durability and safety are essential considerations in medical device components because of patient safety and regulatory compliance. Many medical devices are often used in direct skin contact.
Therefore, silicone rubber components must be safe to limit the risk of allergic reactions and malfunction. Also, regulatory standards ensure medical device components are safe and meet strict regulations.
Another reason durability is essential in medical device components is that they reduce the cost of repairs and replacements. As a result, durable medical devices may have higher upfront costs. Still, they remain functional over extended periods, becoming cost-effective in the long run.
How to Properly Apply Silicone Rubber Finishes for Maximum Efficiency?
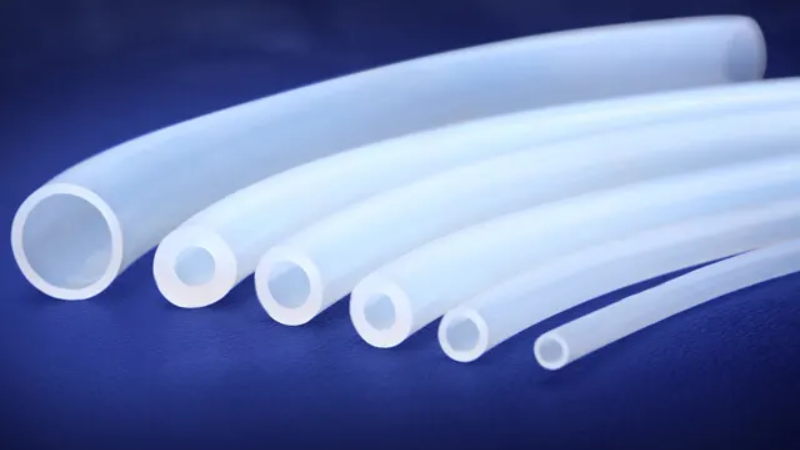
Applying silicone rubber finishes appropriately on medical devices is essential to ensure maximum efficiency. The steps for applying silicone rubber finishes appropriately include;
Surface Preparation
Cleaning the surface of the medical device before applying the silicone rubber finish is essential. Otherwise, the contaminants on the device’s surface will interfere with the adhesion of the finish and limit its effectiveness.
Application
The silicone rubber finish can be applied through several methods, including brushing and spraying. Because there are different types of silicone rubber finish, the thickness and coverage will vary. In addition, when applying the finish, the coating thickness will depend on the medical device.
Curing
After applying the silicone rubber finish, the next step is to allow it to cure. The appropriate curing method depends on the type of silicone rubber finish. Popular curing methods include exposure to temperature or humidity.
Inspection
After applying and curing the finish, it is ideal for inspecting it. The inspection ensures that the medical device satisfies quality control measures. In addition, it is easier to detect inconsistencies and defects and address them accordingly.
Conclusion
Silicone rubber finishes are used across several industries, including the medical industry. Although several types of protective coating exist, silicone rubber finishes stand out. This protective coating is biocompatible, flexible, and durable. It also offers excellent chemical resistance, ensuring protection even in applications with chemical exposure.
Because of the safety and durability of silicone rubber, medical devices coated with this finish can meet regulatory safety standards. Furthermore, by following the best practices for applying and curing silicone rubber finishes, you can ensure the maximum efficiency of medical devices.
Discover the Perfect Solution for Your Business with Hongju
Silicone rubber finishes in the medical device industry are a must for safety and durability. However, it is ideal to go for the best and use only reputable manufacturers. Fortunately, Hongju is a leading expert rubber products manufacturer with over two decades of experience.
We are experts at creating tailor-made solutions that exceed your expectations. For your silicone rubber finishes, our team will work with you to customize products according to your specifications.
Reach out today!