If you’re sourcing sealing solutions for equipment, electronics, or industrial machinery, silicone gaskets are a high-performance option you shouldn’t overlook.
In this guide, we’ll walk you through what silicone gaskets are, the different types available, key benefits, and how to choose the right material for your application.
Whether you’re an importer, OEM, or product developer, this article will help you make smarter buying decisions and avoid costly mistakes.
What are Silicone Rubber Gaskets?
Silicone gaskets are often misunderstood by individuals who lack knowledge about their purpose. Let’s delve into the fundamental information about silicone gaskets together.
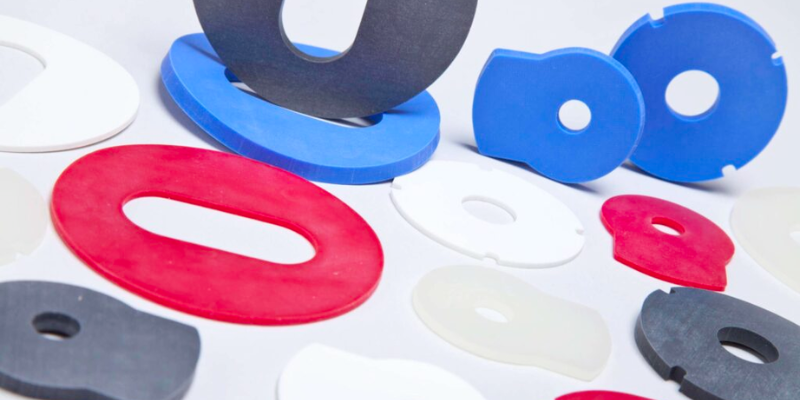
Definition of silicone rubber gaskets
Silicone rubber gaskets are rubber gaskets made of silicone rubber. They are specifically designed to provide reliable sealing solutions in applications where there is a need for resistance against extreme temperatures, moisture, chemicals, and UV radiation.
They exhibit exceptional flexibility and elasticity, allowing them to conform to irregular surfaces and maintain a tight seal.
Basic Characteristics of Silicone Rubber Gaskets
The key characteristics of silicone rubber gaskets include:
- Temperature resistance: Silicone gasket materials can withstand both high and low temperatures without losing their physical properties. They can endure temperatures ranging from -60°C to 230°C (-76°F to 446°F), making them suitable for diverse environments.
- Electrical insulation: Silicone rubber is an excellent insulator, making it ideal for applications requiring electrical isolation or protection against electromagnetic interference (EMI).
- Chemical compatibility: Silicone gaskets have good resistance to various chemicals such as acids, alkalis, solvents, oils, and fuels. This chemical stability ensures the longevity of the seal even when exposed to harsh substances.
- Weatherability: The inherent UV resistance of silicone rubber allows these gaskets to maintain their integrity when exposed to sunlight or outdoor elements over extended periods.
- Compression set resistance: Silicone rubber exhibits low compression set properties, meaning it can retain its original shape after being compressed or deformed. This characteristic ensures consistent sealing performance over time.
Types of Silicone Gasket Material
Silicone gasket materials are available in various types, each offering unique properties and characteristics that make them suitable for specific applications.
These types differ based on hardness, temperature resistance, and chemical compatibility. Let’s explore the different options:
1. Solid Silicone
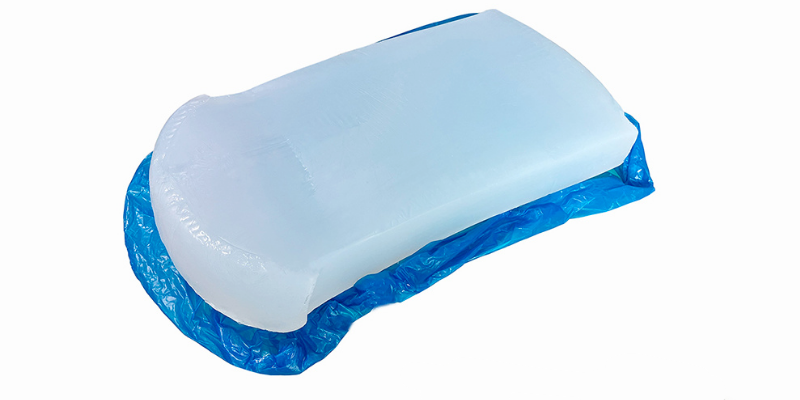
Solid silicone gaskets are made from a solid sheet or strip of silicone rubber. They are known for their excellent thermal stability and resistance to extreme temperatures ranging from -60°C to 230°C.
This type of silicone rubber gasket material is commonly used in high-temperature environments where sealing integrity is crucial. Solid silicone gaskets also exhibit good chemical resistance, making them ideal for applications involving exposure to oils, fuels, and solvents.
Advantages:
- High sealing integrity
- Good chemical compatibility
- Excellent temperature resistance
Disadvantages:
- Limited compressibility
- Less flexibility compared to sponge or foam silicone
2. Sponge Silicone
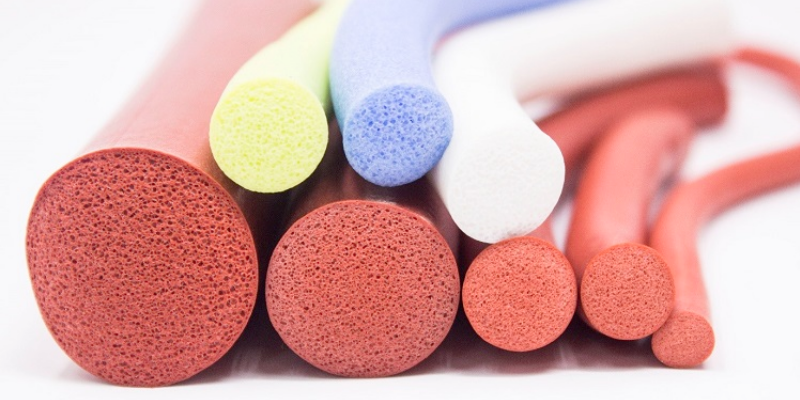
Sponge silicone gaskets are manufactured by blending liquid silicone with a foaming agent before curing it into a solid form with air pockets. This results in silicone sponge material, a soft and compressible material that can conform to irregular surfaces effectively.
Sponge silicone offers superior compression set resistance, meaning it can maintain its original shape after being compressed repeatedly over time. It also provides extreme temperature resistance and excellent vibration-damping properties.
Advantages:
- High compressibility and flexibility
- Superior vibration dampening
- Good sealing performance on uneven surfaces
Disadvantages:
- Lower temperature resistance compared to solid silicone
- Reduced chemical compatibility
3. Foam Silicone
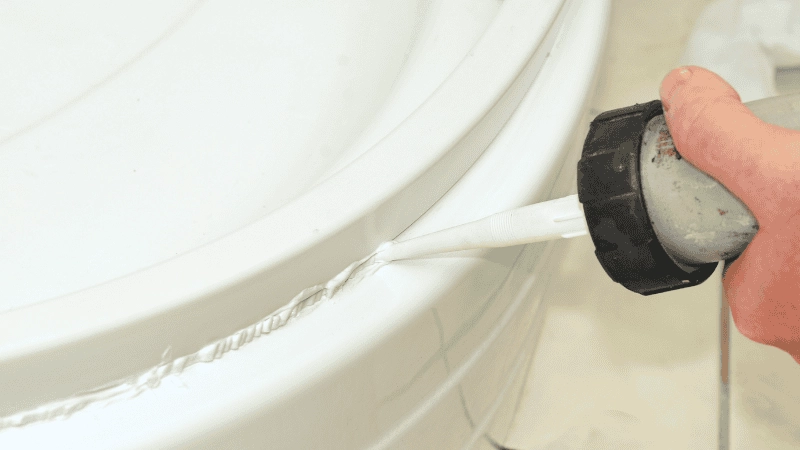
Similar to sponge silicone, foam silicone gaskets have air pockets within the material structure but possess higher density and lower porosity. This makes them more resistant to compression while still maintaining some level of flexibility.
Foam silicone is often used in industrial applications requiring a balance between cushioning and sealing capabilities.
Advantages:
- Enhanced durability due to higher density
- Improved compression resistance compared to sponge silicones
Disadvantages:
- Limited flexibility compared to sponge silicone
- Reduced chemical compatibility
4. Specialty Variations
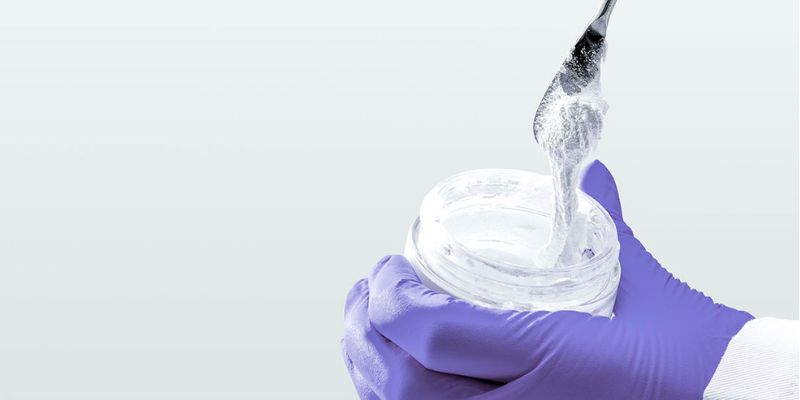
In addition to the basic types of silicone rubber gasket materials mentioned above, there are specialty variations available for specific requirements. These include:
- Conductive Silicones: Designed to provide electrical conductivity, these gaskets are commonly used in applications where electromagnetic interference (EMI) shielding is necessary.
- Flame-Retardant Silicones: These gaskets are formulated with additives that make them self-extinguishing and resistant to flame propagation. They find extensive use in industries where fire safety is a priority.
Each specialty variation offers unique properties tailored for specific applications.
5. Commercial-Grade vs High-Performance Grades
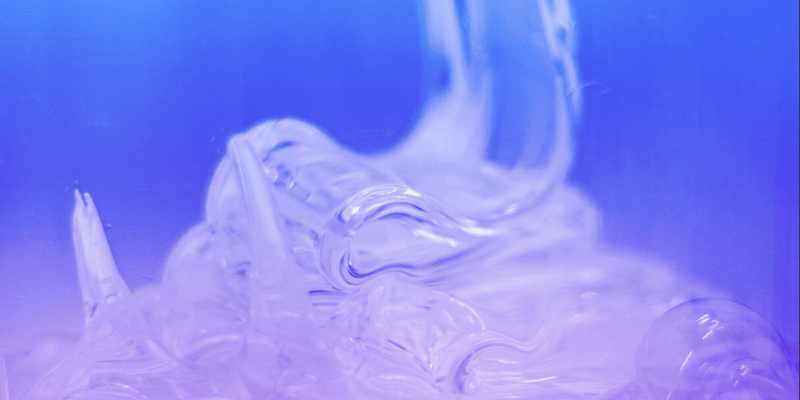
Different grades of silicone gasket materials exist in the market, ranging from commercial-grade to high-performance variants. Understanding the differences between them is vital when choosing silicone material of the appropriate grade for your application.
- Commercial-Grade: These silicone gaskets offer good performance at an affordable price point. They often meet basic industry requirements but may not possess exceptional properties demanded by more demanding applications.
- High-Performance Grades: Designed for specialized applications, high-performance silicone gaskets excel in areas where extreme temperatures, chemical resistance, or stringent sealing requirements are necessary. These grades exhibit superior tear strength and durability compared to commercial-grade options.
Importance of Selecting the Appropriate Grade
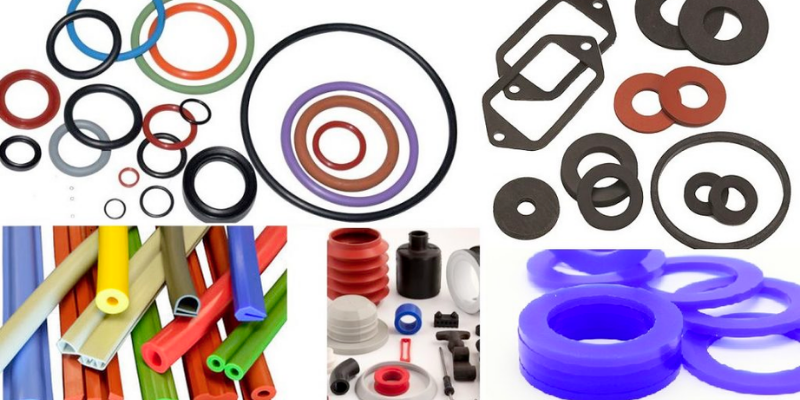
Selecting the right grade of silicone gasket material is crucial for ensuring optimal performance and longevity in specific applications. Using an unsuitable grade can lead to premature failure, compromising the integrity of seals and causing costly downtime or safety hazards.
Considerations when choosing a grade include:
- Environmental Factors: Evaluate temperature extremes, exposure to chemicals, UV radiation, or other challenging conditions the gasket will encounter.
- Application Requirements: Determine if food-grade compliance is necessary for applications involving contact with consumable products.
- Performance Expectations: Assess the required tear strength, compression set resistance, flexibility, and durability needed for reliable sealing.
Applications of Silicone Gaskets
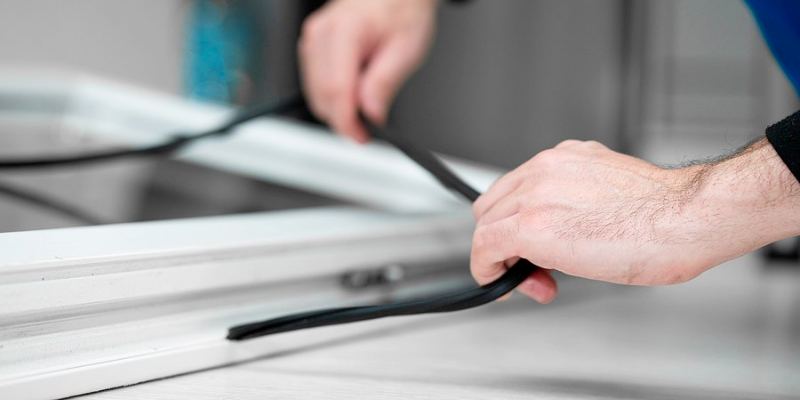
Silicone gasket material is widely recognized for its versatility in sealing applications across various industries. From automotive and aerospace to electronics, silicone gaskets have become an indispensable component in many products.
Let’s explore some specific examples of how silicone gasket material is used across different industries:
- Automotive
Silicone gaskets play a vital role in automotive engines by sealing various components such as cylinder heads, oil pans, valve covers, and intake manifolds. They provide a reliable barrier against oil leaks and ensure optimal engine performance.
- Aerospace
In the aerospace industry, where extreme temperatures and pressure differentials are common, silicone gaskets find extensive use in aircraft engines and fuel systems. They help maintain airtight seals under challenging conditions.
- Electronics
Silicone gaskets are widely employed in electronic devices to protect sensitive components from dust, moisture, and other contaminants. They create a secure seal between enclosures or circuit boards while providing electrical insulation.
- Oven door gaskets
Silicone gaskets are commonly used in oven doors to create a heat-resistant seal. They withstand high temperatures without deforming or losing their sealing properties, ensuring efficient cooking and energy conservation.
- Medical devices
Silicone gaskets are an integral part of many medical devices, such as infusion pumps and respiratory equipment. They provide a sterile and leak-proof interface between different components, ensuring patient safety.
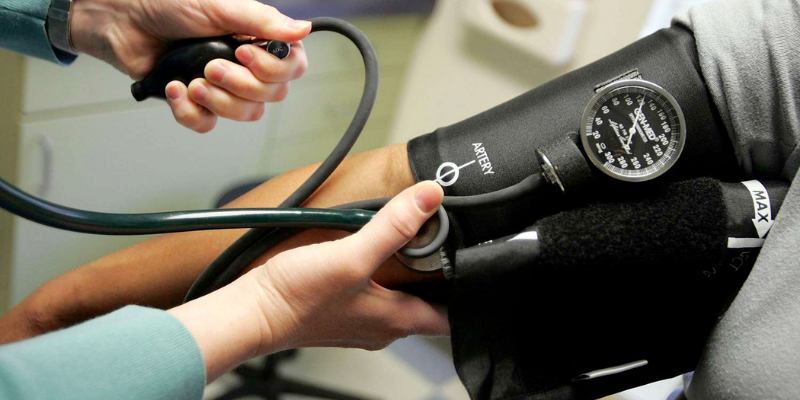
It’s worth mentioning that silicone gasket material is also favored by DIY enthusiasts who need custom gaskets for various projects.
With its adhesive backing, silicone sheets can be easily cut into desired shapes and sizes for gasket applications in crafts, pads, or even food-related projects.
How to Select a Silicone Gasket Material?
Selecting the right silicone gasket material depends on the specific application and the requirements of the customer. Here are some guidelines to help you select the right silicone gasket material:
- Determine the Operating Temperature Range: The operating temperature range of the application should be considered when selecting a silicone gasket material. Some materials have a wide operating temperature range, while others have a more limited range. Choose a material that can withstand the temperatures in your application.
- Consider the Chemical Environment: If the application is corrosive or has high levels of chemicals, you should choose a silicone gasket material that can withstand those conditions. Choose a material that is resistant to the specific chemicals that will be present in your application.
- Take into account the Pressure Differentials: If there are significant pressure differences in your application, choose a silicone gasket material that can handle the pressures involved. Some materials have a higher pressure differential tolerance than others.
- Consider the Operating Environment: If your application is outdoors, you may need a silicone gasket material that is durable and can withstand the elements, such as rain, wind, and UV exposure.
- Evaluate the Available Shapes and Sizes: Choose a silicone gasket material that comes in the shape and size that you need. Some materials are available in a variety of shapes and sizes, while others are more limited.
By considering the application requirements, operating temperature range, chemical environment, pressure differentials, operating environment, and available shapes and sizes of silicone rubber gasket materials, you can select the right fluorinated silicone rubber gasket material that will perform well in your specific application.
How do Silicone Gaskets Compare to Rubber Gaskets?
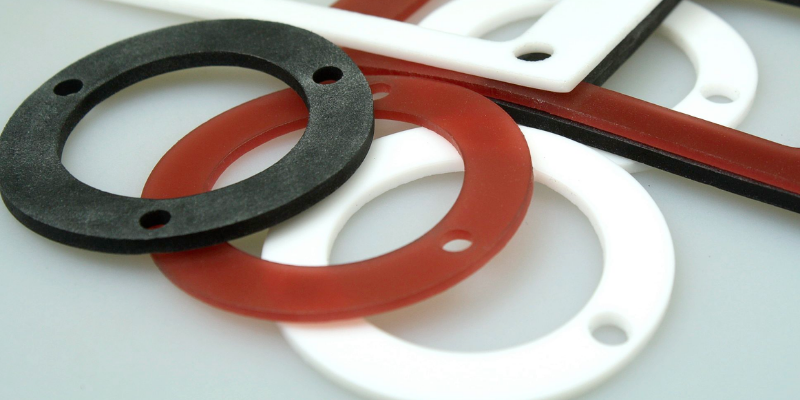
Silicone gasket material offers several advantages over traditional rubber gaskets.
From superior resistance to extreme temperatures and chemicals to enhanced durability and longer lifespan, silicone gaskets have become the preferred choice for manufacturing gaskets in many industries.
Let’s delve into the key differences in material properties and performance that make silicone gaskets stand out.
Property | Silicone Gasket | Rubber Gasket |
---|---|---|
Material | Synthetic polymer made with silicon, carbon, hydrogen, and oxygen | Typically natural or synthetic polymers like neoprene, nitrile, or EPDM |
Temperature Resistance | Very high (up to 600 degrees F for some grades) | Moderate (around 300 degrees F for most types of rubber) |
Chemical Resistance | Excellent against weathering, ozone, moisture, UV rays, and high temperatures. Limited resistance to oils, fuels, and hydrocarbons. | Good general resistance, but the specifics vary widely by the type of rubber. Some rubbers, like nitrile, are excellent for oils and fuels. |
Flexibility | High flexibility and compressibility even at extreme temperatures | Good flexibility at room temperature, but can harden or become brittle in cold or very hot conditions |
Durability | Long-lasting durability, does not become brittle or hard over time | Long-lasting durability does not become brittle or hard over time |
Cost | More expensive than most rubber materials | Generally cheaper, but the cost can vary based on the specific type of rubber |
Remember, the specific properties can vary within each category (silicone or rubber) based on the exact formulation or grade of the material. So, the best choice will depend on the specific requirements of your application.
Conclusion
In conclusion, silicone gasket material plays a crucial role in environmental sealing used in various industries and applications. Its unique properties make it an ideal choice for sealing purposes.
With this understanding of silicone gasket material’s importance and advantages, you can confidently choose the most suitable option for your sealing needs.
Contact Hongju for Your Silicone Gasket Materials
At Hongju, we take pride in crafting premium silicone gaskets and seals tailored to your specific needs. Our silicone gaskets come in a variety of colors, hardness levels, and thicknesses, offering versatility for any application.
With our wealth of experience in the industry, you can trust that the products you receive are of the utmost quality.
We’ve been helping global B2B customers with custom gasket solutions for over 20 years. Contact us today to request a quote or sample—we’re here to help make your next project a success.