The Shore hardness scale, though seemingly simple, is diverse and can often lead to confusion, especially when differentiating between Shore A and Shore D.
This article provides an in-depth look into the distinct characteristics of these scales and their significance in material selection and application. Keep reading to gain a clearer picture of these seemingly similar yet different hardness scales.
Who Invented the Shore Scale?
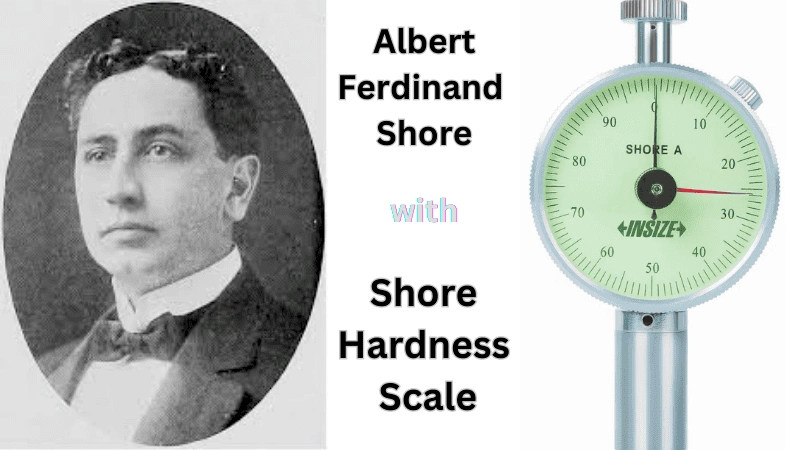
The Shore hardness scale is named after Albert Ferdinand Shore, who introduced it in the 1920s. Shore was an American who excelled in the field of material testing and inspection. He was driven by the need for a practical tool that could assess and categorize the hardness of different materials accurately.
His work was primarily focused on developing a device to measure the hardness of newly developed synthetic rubber.
This necessity paved the way for the creation of the Shore durometer and the associated Shore hardness scale that we use today. In his honor, these hardness measuring scales are collectively called “Shore hardness scales.”
Understanding Shore Hardness
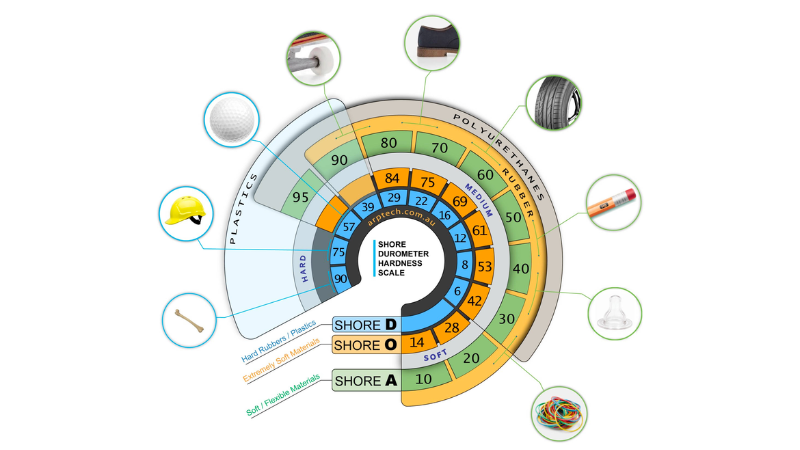
Shore hardness, also known as durometer hardness, is a crucial measure of how resistant a material is to permanent indentation or penetration by an indenter point under specified conditions.
It provides valuable information about the mechanical properties and durability of materials, making it an essential factor for engineers and manufacturers to consider when selecting appropriate materials for specific applications.
The shore hardness value quantifies the material’s resistance to deformation, with higher values indicating greater hardness. The measurement is determined using a device called a durometer, which applies pressure on the material’s surface and measures the depth of indentation.
The different Shore Hardness scales measure the resistance of a material to indentation. This standardized test allows for consistent and accurate comparisons between different materials.
What is the Shore A and Shore D?
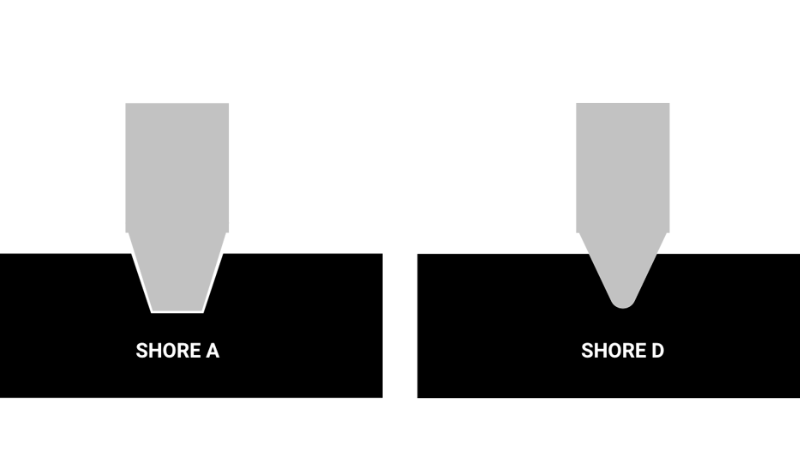
To understand materials and their properties in depth, one must grasp the difference between Shore A and Shore D scales. Both of these scales are subsets of the Shore hardness measurement system and are used to quantify the hardness of different types of materials.
Shore A Hardness Scale
Shore A measures flexible mold rubber materials. This range includes most rubbers from extremely soft and flexible to hard rubbers with minimal flexibility. It also evaluates non-rubber plastics that are semi-rigid and somewhat flexible.
The durometer used for this scale has a spring force of 822g (8.05N) and a blunt 35° conical indenter. Typical readings on the Shore A scale range from 10 to 90. Items such as rubber bands, car tires, and silicone seals often fall into the Shore A category.
Shore D Hardness Scale
On the other hand, Shore D is used for testing harder materials such as hard plastics and rigid polymers. The Shore D durometer applies a spring force of 4536g (44.5N) and uses a sharp 30° conical indenter.
The readings on this scale also typically range from 10 to 90. Items like hard hats, plastic cutting boards, and shopping cart wheels often have a Shore D hardness.
Take the First Step:
Requst for an Inquire
Quality Meets Affordability. Inquire Now for High-Quality Products at Low Volumes.
Understanding the Differences Between Shore A and Shore D
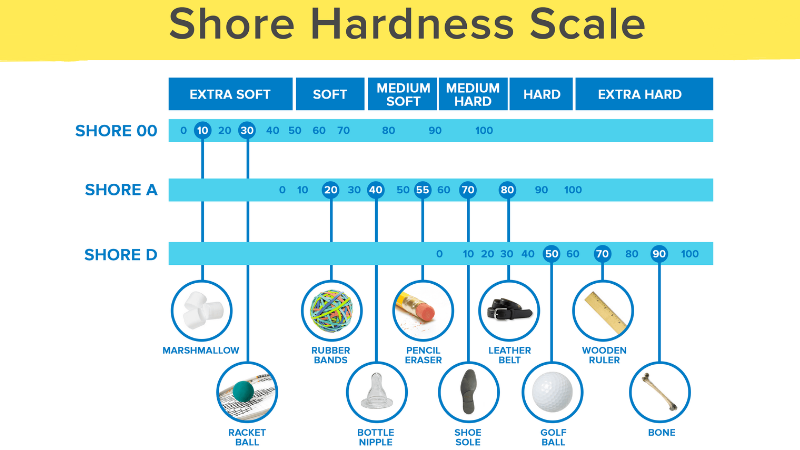
Shore A and Shore D are two different scales used to measure the hardness of materials.
While both scales provide valuable information about the hardness of a material’s properties, they have distinct differences that make them suitable for specific applications.
Shore A | Shore D | |
---|---|---|
Material Type | Softer materials (rubber, elastomers, softer polymers) | Harder materials (hard plastics, rigid polymers) |
Indenter Shape | Blunt 35° conical indenter | Sharp 30° conical indenter |
Spring Force | Lower (822g or 8.05N) | Higher (4536g or 44.5N) |
Common Applications | Industries dealing with softer materials (e.g., automotive, medical) | Industries dealing with harder materials (e.g., construction, safety equipment) |
Understanding these differences is critical to ensure the appropriate hardness scale is used when testing a material’s hardness, ultimately affecting the product’s quality, safety, and performance.
Measuring Softness vs. Hardness

Shore hardness scales were developed with a specific intention to gauge the hardness or softness of a material, and by extension, its flexibility or rigidity.
The Shore A scale measures the hardness of flexible, softer materials such as rubber or soft polymers. The measurement is achieved using a spring-driven blunt indenter which exerts a specific force on the material.
The depth to which the indenter penetrates the material gives the Shore A hardness value. A higher Shore A number represents a harder and less flexible material.
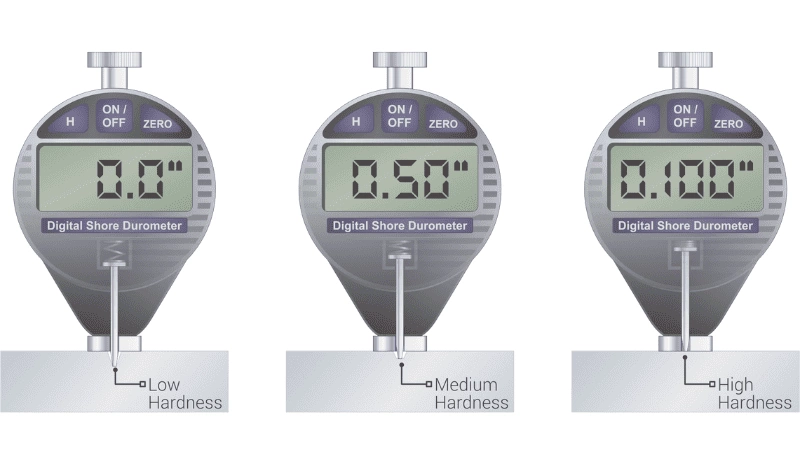
The Shore D scale is designed to evaluate the hardness of rigid or semi-rigid hard plastics. The Shore D scale uses a sharper indenter and higher spring force, making it better suited for materials that have a higher resistance to indentation.
As with Shore A, a higher Shore D number indicates a harder, more rigid material.
Both scales offer valuable insights into the material properties, allowing for the appropriate selection of materials based on their intended application.
Take the First Step:
Requst for an Inquire
Quality Meets Affordability. Inquire Now for High-Quality Products at Low Volumes.
Significance of Shore A and Shore D Hardness Testing
Measuring material hardness can be beneficial to performing maintenance on your system’s materials. Shore hardness testing plays a crucial role in determining the suitability of materials for specific applications.
By subjecting materials to this type of testing, valuable information about their durability, flexibility, and resistance to indentation can be obtained.
Determining Material Suitability
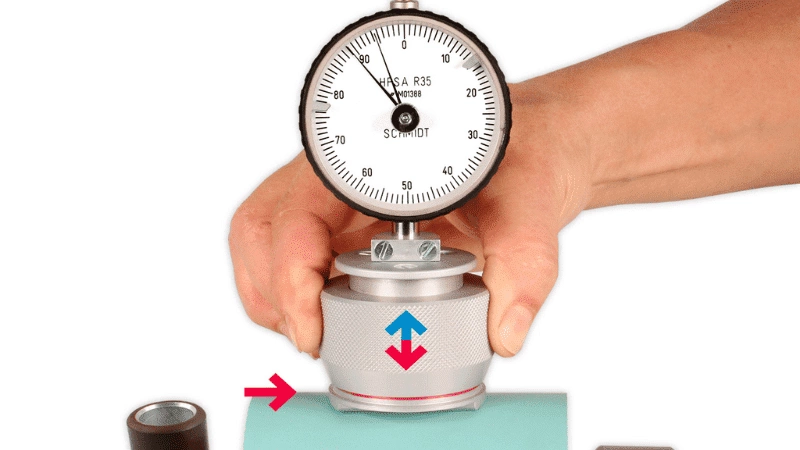
One of the primary reasons why shore hardness testing is significant is its ability to determine material suitability for specific applications.
Different materials have varying levels of hardness, which directly affect their performance in different environments or under different conditions.
For instance, a material with high Shore A hardness may be suitable for applications that require elasticity and flexibility, such as rubber seals or gaskets. On the other hand, Measuring a material hardness can also be beneficial to performing maintenance on your system’s materials.
A material with high Shore D hardness may be more appropriate for applications that demand rigidity and resistance to wear, like industrial flooring or automotive parts.
Evaluating Durability and Flexibility
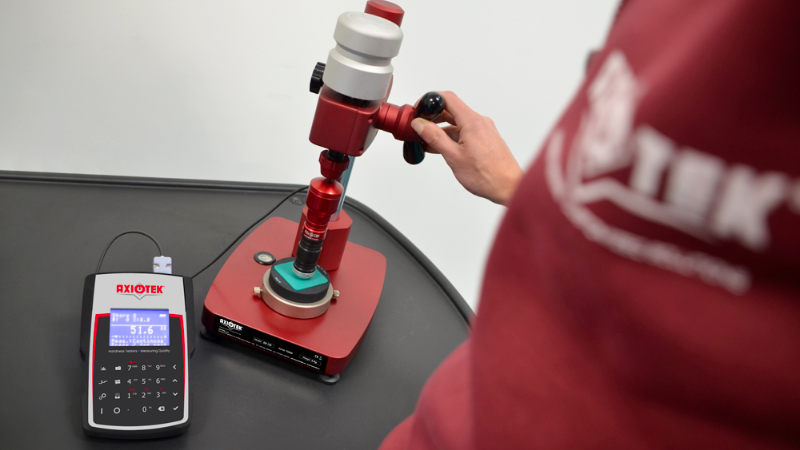
Shore hardness testing provides valuable insights into the durability and flexibility of materials. The test measures the resistance of a material’s surface to indentation using either a Shore A or Shore D durometer.
With this information at hand, manufacturers can assess how well a material will withstand external forces over time.
For example, if a product needs to endure constant impact or compression, it is essential to select a material with appropriate shore hardness that can withstand such stresses without deformation or damage.
Ensuring Consistent Quality
Manufacturers across various industries rely on shore hardness testing as an integral part of their quality control processes.
By consistently conducting these tests on raw materials and finished products, they can ensure that each item meets the required standards before reaching consumers’ hands. This helps prevent any defects or inconsistencies from arising due to unsuitable material choices.
Applications of Shore A and Shore D Hardness Testing
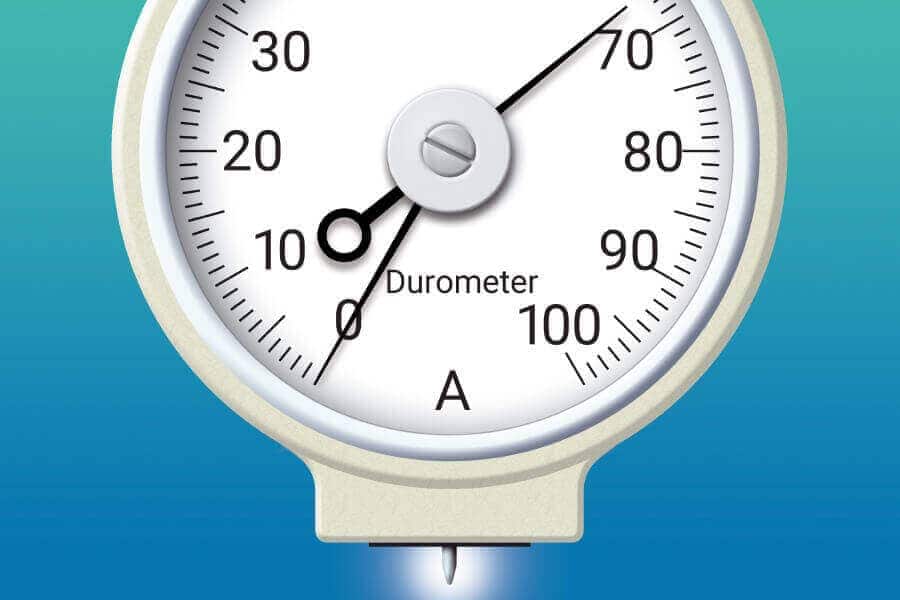
The Shore hardness scales, including Shore A and Shore D, have wide-ranging applications across numerous industries due to their effectiveness and ease of use in assessing the hardness of various materials.
Shore A Applications
Shore A hardness testing is generally used for softer materials such as rubber, elastomers, and other polymers. The most common applications include:
- Automotive: In the manufacturing of tires, seals, gaskets, and other rubber components.
- Consumer Goods: In testing the hardness of products like rubber shoes, erasers, mouse pads, and more.
- Medical Industry: In evaluating the hardness of soft medical components like catheters, elastomeric seals, and flexible tubes.
Shore D Applications
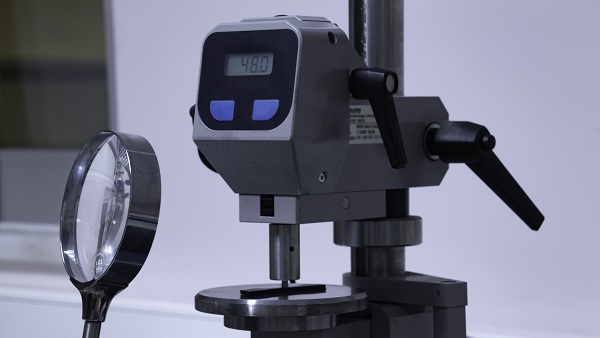
Shore D hardness testing is commonly applied for harder materials, such as rigid plastics, epoxies, plexiglass, and hard polymers. The typical applications are:
- Manufacturing: In checking the hardness of machine parts, gears, and other rigid components.
- Construction: In evaluating the hardness of hard plastic pipes, helmets, and safety gear.
- Electronics: In assessing the hardness of hard plastic enclosures, cases, and other components.
By understanding the hardness of a material through Shore hardness testing, manufacturers can ensure rigid materials in their products meet the required specifications and standards, thereby guaranteeing product reliability and customer satisfaction.
Take the First Step:
Requst for an Inquire
Quality Meets Affordability. Inquire Now for High-Quality Products at Low Volumes.
Exploring the Secrets of Shore Durometer Measurements
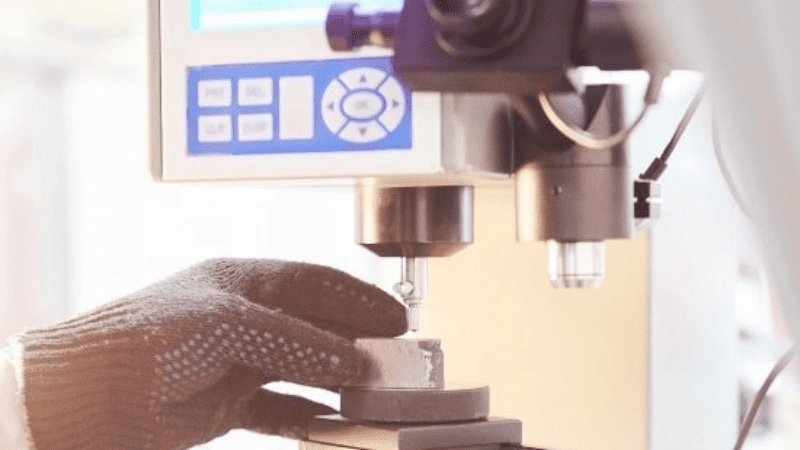
To get a fuller understanding of Shore A and Shore D hardness testers, here are some open secrets:
- Standardized Results Across Industries
Shore durometer measurements are widely used in various industries to determine the hardness of materials, particularly elastomers like rubber molds. This standardized testing method allows for consistent and comparable results across different applications.
Whether you’re working with automotive parts, footwear, or even toys, the shore durometer provides a reliable gauge for evaluating material hardness.
- Indenter’s Penetration Depth Determines Hardness Value
The key factor in inshore durometer measurements is the depth of penetration made by the indenter on the material’s surface.
The test involves pressing a specific indenter into the sample and measuring how far it sinks into the material. This indentation depth is then assigned a numerical value on either the Shore A or Shore D scale.
- Higher Reading Indicates Greater Resistance
A higher value indicates greater resistance to indentation or penetration. In other words, materials with higher shore durometer ratings are generally harder and less prone to deformation under pressure.
On the other hand, lower values suggest softer materials that may be more flexible but also more susceptible to indentations.
Ensuring Accurate Shore Durometer Readings
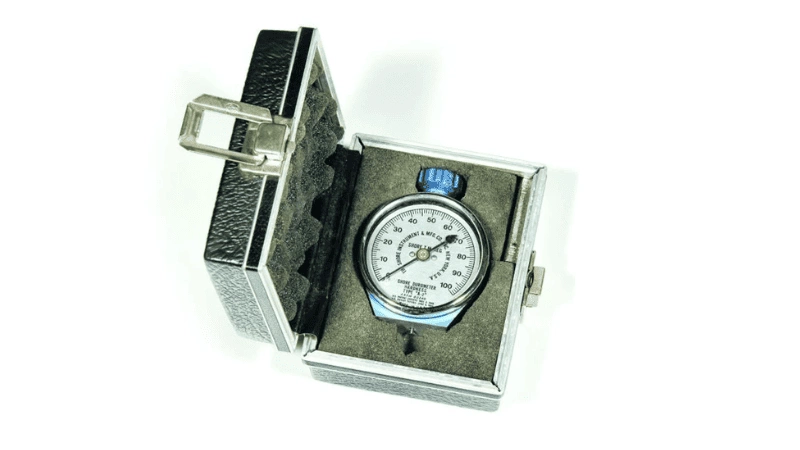
To ensure accurate shore durometer measurements, proper calibration and technique are crucial. Calibrating the instrument regularly helps maintain its accuracy over time.
Following specific guidelines when conducting tests ensures consistency and reliability in obtaining meaningful data.
When using a shore durometer gauge:
- Ensure that both the sample surface and indenter tip are clean.
- Apply uniform pressure perpendicular to the material surface.
- Allow sufficient time for stabilization before taking a reading.
- Take multiple readings at different locations on the sample for an average result.
By adhering to these guidelines, you can minimize potential errors caused by external factors such as temperature variations or operator inconsistencies.
Take the First Step:
Requst for an Inquire
Quality Meets Affordability. Inquire Now for High-Quality Products at Low Volumes.
Conclusion
In sum, the Shore Hardness Scale, encompassing Shore A and Shore D scales, is a crucial tool for understanding the properties of various materials.
Whether you are seeking flexibility as in the Shore A scale, or rigidity as represented in the Shore D scale, this measurement system provides invaluable data to guide your material selection process.
Unlock the Potential of Materials with Hongju’s Expertise
The experts at Hongju Silicone are here to help! We have extensive experience in material testing, including Shore Hardness measurements. Whether you need assistance with material selection or want to understand more about the difference between Shore A and Shore D hardness testing, contact us now!