Today, I’m going to explain why it is so necessary to reduce cycle time in injection molding. I have crafted a comprehensive guide on cycle time; it lets you unlock some critical strategies for optimizing cycle time.
Besides, you would get to know all factors impacting this cycle time and how you can control these factors to achieve shorter production cycles and enhance overall productivity. Let’s get started!
Importance of Reducing Cycle Time in Injection Molding
Injection molding is a commonly used manufacturing method for crafting various products. Often, a product is created in parts, and the cycle time in injection molding refers to the complete time required to produce a part, from injecting molten material into the mold to removing the final product.
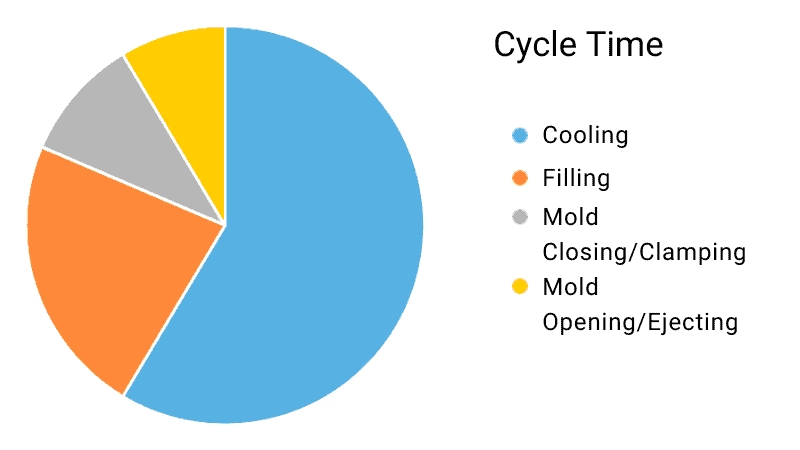
When making production efficient, it’s vital to reduce the cycle time in injection molding. It’s crucial to cut this time. Let’s find out why it is so essential to reduce injection molding’s cycle time.
Cost Efficiency
Every manufacturer wants to produce more products at a low cost. The goal of cost efficiency is achievable with a short cycle time. If the cycle time is high, the cost of energy, labor, and machine usage increases. As a result, high cycle time will contribute to the overall cost.
On the flip side, when a part gets ready quickly, it will consume less labor, energy, and cost. As a result, short cycle time will lead to significant cost savings.
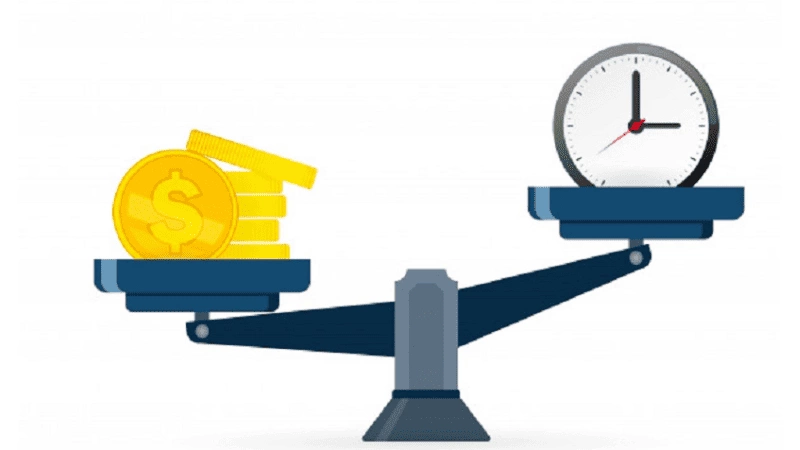
Keep in mind that when less time is spent on the production of a part, it will decrease overhead costs while increasing profit margins for the manufacturer.
Increased Production Output
It is vital to have a short cycle time because it increases production output. When you belong to an industry that has high demand and tight deadlines for production, you certainly need to drop the cycle time. This action will help you get a large share of the market while meeting your customer demand effectively.
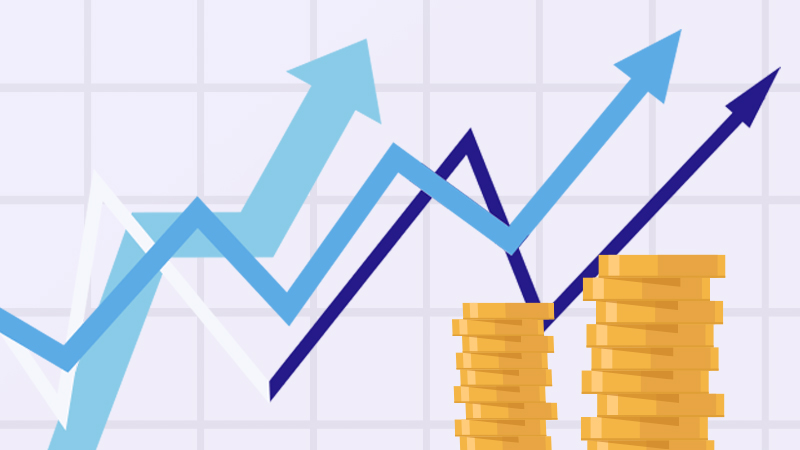
Improved Product Quality
To run a successful manufacturing business, you need to improve product quality while cutting off the cycle time. This short cycle time helps you achieve good quality products.
Are you wondering how?
Well, during the injection molding process, molten material is exposed to heat and pressure, and when the cycle time is too long, it may cause some material issues, such as injection molding defects. You can minimize these issues by reducing the cycle time.
Energy Efficiency
When the cycle time is short, the injection molding machine runs for a short time, and it consumes less energy to heat the material or to run the molds. The machine consumes less energy per part production, and it’s how you can hit the energy efficiency goal in no time.

Competitive Advantage
Do you want to stand out in the crowd? You can have a competitive edge in the manufacturing industry through a short cycle time. Try to offer a quick turnaround time for high-quality products. As a result, it will become easier for you to grow your business while winning more contracts.
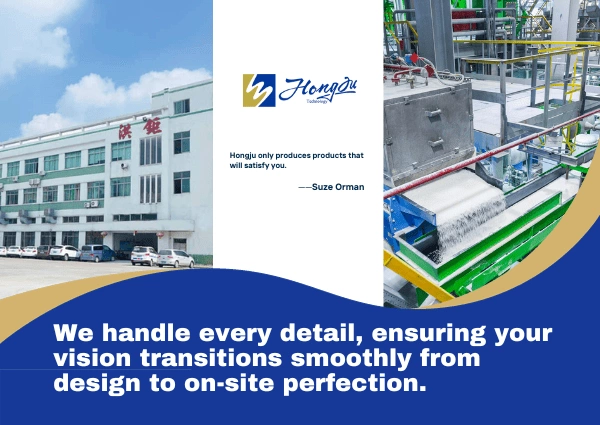
Hongju Awaits Your Quote Request!
Factors Affecting Cycle Time in Injection Molding
Now you know some reasons that emphasize reducing cycle time in injection molding. The next thing you should understand is all the factors that can affect this timing. Let’s unlock the details of all these factors below:
Injection Time
It refers to all the time it takes to inject molten material into a mold cavity. You can reduce the cycle time with a short injection time. However, you can’t decrease injection time because the material must be packed into the mold properly. Otherwise, the finished product will have some defects.
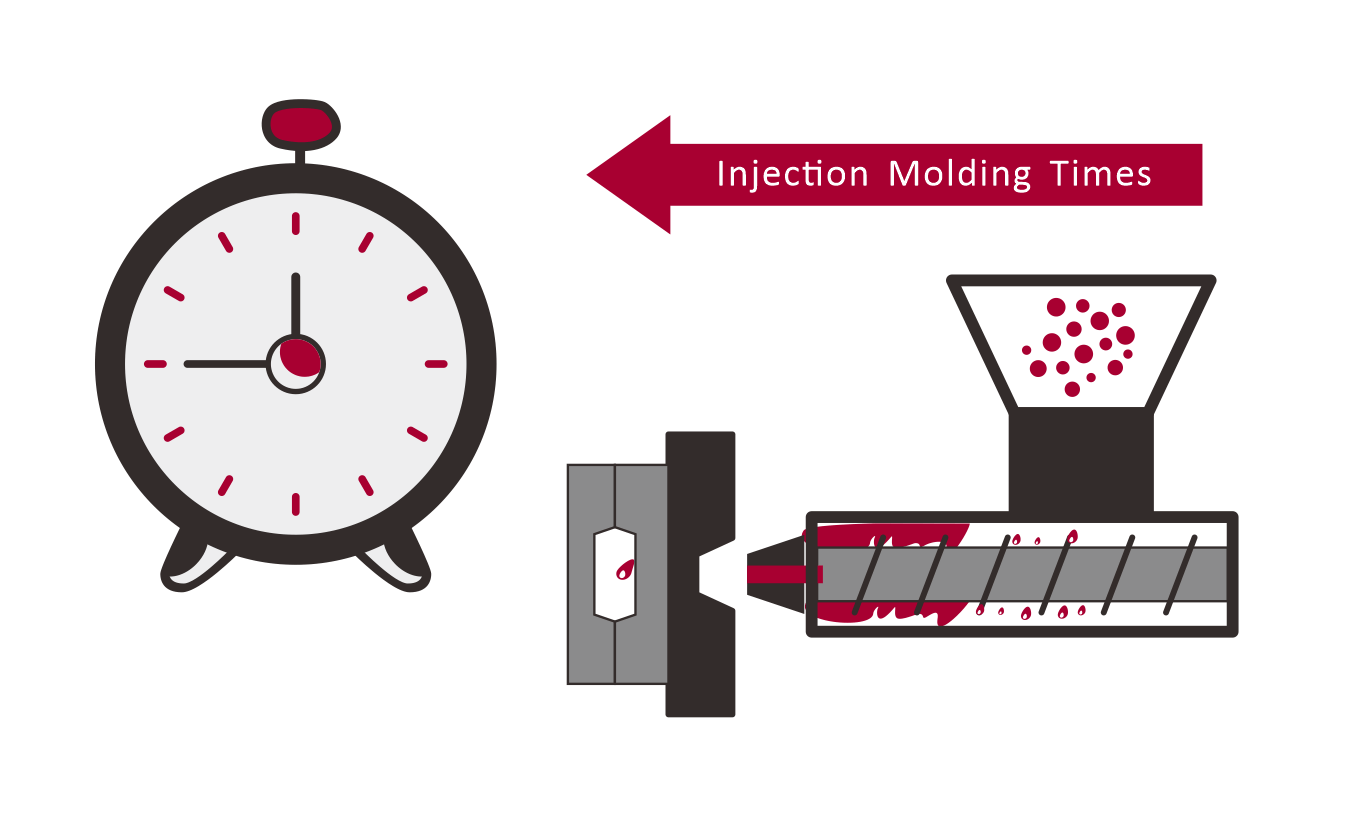
Cooling Time
It refers to the duration the part spends inside the mold until it solidifies and cools down before part ejection. This time is usually affected by the thickness and geometry of a part. Cooling time also depends on the cooling system and cooling channels.
When you have an efficient cooling design with optimal cooling channels, it helps in decreasing cooling time.
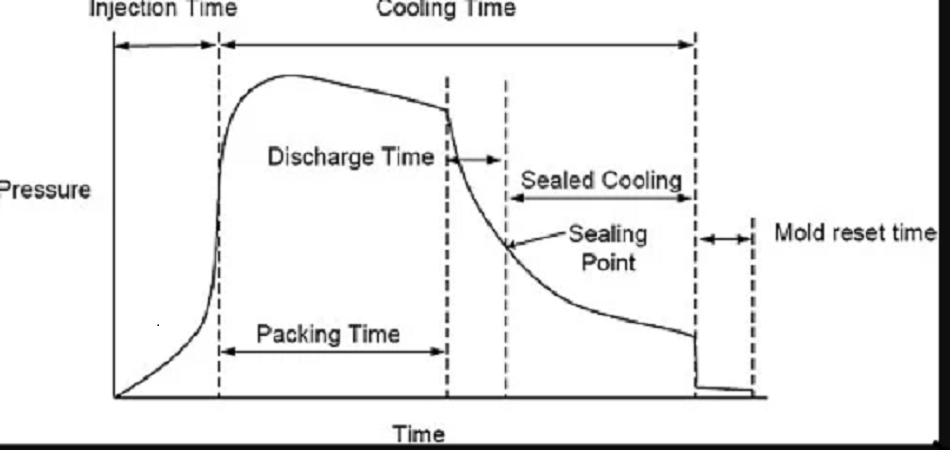
Material Temperature
It refers to the temperature of molten material as it enters the mold. The material must be heated at the right temperature to ensure proper flow and to reduce the cooling time. Expert engineers can adjust the temperature control system in the molding machine in a way that material temperature remains consistent throughout the process.
Besides, when the material temperature is high, it will also increase mold temperature, and as a result, the cooling time will be longer than usual.
Material Selection
A major factor that significantly impacts injection molding cycle time is material selection. You need to choose a suitable material for the application. Some materials have excellent cooling properties, so their production cycle is short.
Material flow characteristics such as shear rate, pressure, and viscosity also have a significant effect on this time. When you choose material with suitable flow properties, the injection time will decrease while the production cycle time is optimized.
Ejection Time

It refers to the time it takes to eject the finished part from the mold. To reduce the injection molding cycle time, you need to rely on an efficient ejection mechanism.
Part and Mold Design
Another thing that can leave a significant impact on injection molding cycle time is mold and part design. If a part has complex geometries, it leads to a high cooling time and an extended ejection mechanism.
You can reduce the part cycle time by optimizing part and mold design. A well-designed mold can make a big difference in decreasing cooling times.
Environment Conditions
During the injection molding, you can reduce time by controlling operation conditions, which refers to environmental conditions such as humidity, air quality, and temperature. It would be best to keep operating conditions suitable for this manufacturing process so you won’t have to deal with long cycle times or production defects.
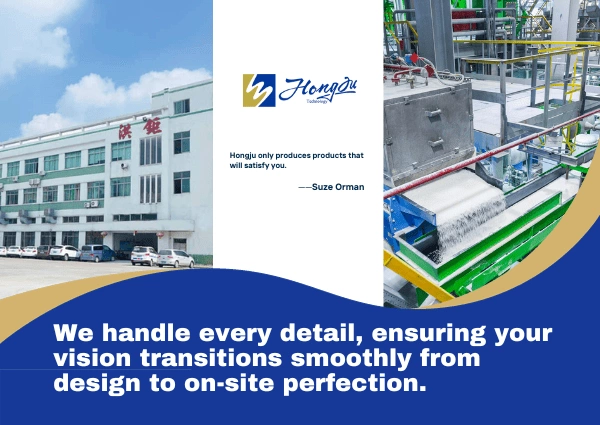
Hongju Awaits Your Quote Request!
5 Strategies for Reducing Cycle Time
Reduction of cycle time in injection molding is crucial to improve efficiency and cost-effectiveness in manufacturing. Here are five strategies for achieving shorter cycle times:
1. Optimize Machine Performance
If you want to minimize your injection molding cycle time, you should control your machine performance or optimize it.
When you have an old machine, it may have some performance issues. In most cases, old machines have inconsistent injection pressure or speed.
As a result, machines take more time to inject the same amount of material. When the mold cavity is not filled correctly, it will lead to defective parts, which, in turn, get rejected during the quality control process. Thereby, your overall cycle time increases.
Modern injection molding machines have advanced features and controls that can be optimized to reduce cycle time. Here are some aspects to control for short cycle time.
Aspect | Description |
---|---|
Boost Injection Speed | Adjusting the injection speed to the specific material and part design can help fill the mold faster without causing defects. |
Accurate Clamping Force | Properly setting the clamping force ensures that the mold is securely closed and reduces the risk of part defects. |
Invest in Parallel Actions | Utilize machines with parallel actions. For example, get machines with simultaneous ejection and injection to save time during each cycle. |
Precise Temperature Control | Precise temperature control for both the material and mold can improve material flow and cooling, reducing overall cycle time. |
You can invest money in a modern machine that offers consistent fill time and ensures that cavities are filled correctly, and there are fewer rejected finished products.
2. Human Expertise
Another thing you can do to minimize injection molding cycle time is to invest money in human resources. You can train your machine operators and process engineers.
They must know how to identify the issues in the machine parameters and how to set the variables such as holding time, cushion, and injection speed to optimize the process.
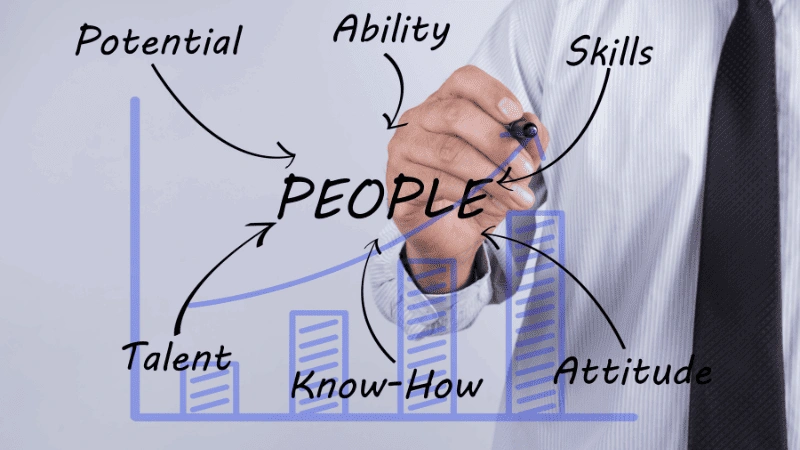
Having experts on your side will help you reap benefits in the long term. If there is any issue during the process, experts can adjust machine parameters in real time and resolve the problems.
At Hongju, we take pride in our expert injection molding engineers, who are well-versed in advanced techniques and technologies. They can make adjustments as and when necessary to improve part quality while reducing the cycle time.
3. Material Selection
The choice of material is often overlooked, but certainly, it has a significant impact on the cycle time. Certain materials have higher fill pressure ratings or higher flow rates. Now, it means that they will fill the mold cavities faster, thereby they can decrease the cycle time.
When you research different resin properties, you can easily find some materials with the most suitable flow characteristics and faster cooling properties.
To influence cycle time positively, research the material to pick the most suitable one for your application, or consult a material scientist.
4. Wall Thickness Optimization
During part design, it’s vital to optimize the wall thickness of your part so it can function correctly. Too thick walls of a part may lead to warped surfaces or sink marks. When walls are thick, they will take more time to cool down.
When walls are too thin, they will not allow proper material flow in the mold. Besides, thin walls will compromise the strength of the product as well. When wall thickness is optimized, the part cools down quickly, and it will also reduce cooling time.
You need to follow the best design practices for minimum wall thickness so that your parts get through the injection stage quickly while their cooling time is minimized.
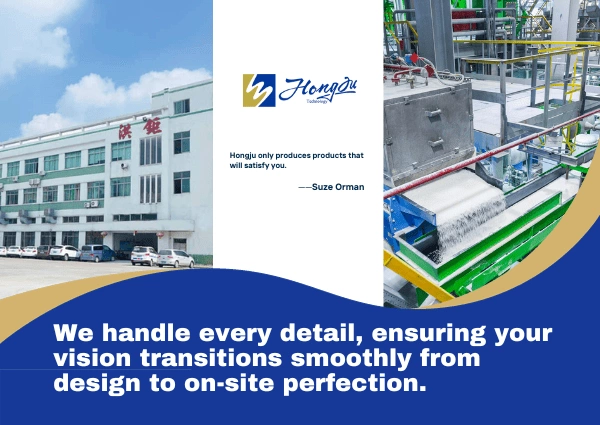
Hongju Awaits Your Quote Request!
5. Streamlining the Injection Molding Process
Another way to reduce cycle time in injection molding is to streamline the injection molding process. When you simplify this process, you can ensure the production of high-quality parts consistently while lowering costs and enhancing efficiency.
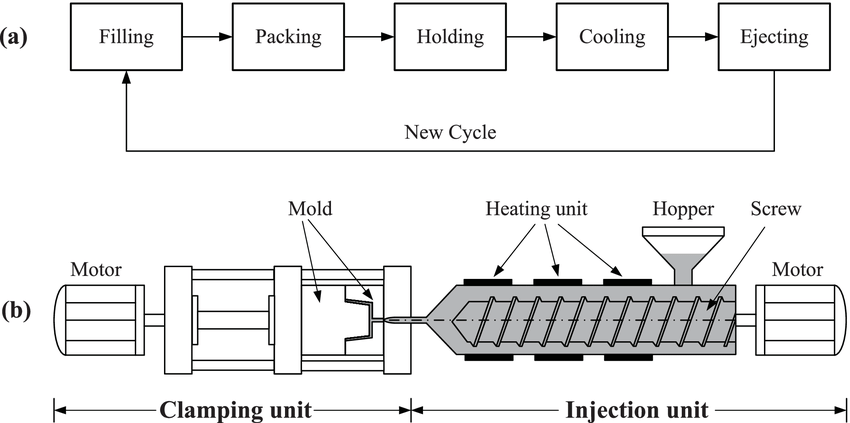
Here are six steps that help you streamline the complex injection molding process parameters.
Step 1. Develop a Consistent Process
Start working on the process and make it as consistent as possible. It means you need to:
- Cool the mold and part properly
- Melt plastic at the right temperature
- Apply the correct pressure during packing
- Inject molten plastic into a mold at the right speed
- And eject the finished part from the mold at the right time.
If you design a consistent process and repeat it for every cycle, you will reduce cycle time, save time, and make your production highly efficient.
Step 2. Maximize the Processing Window
You need to instill flexibility into your plastic injection molding process parameters. Mainly, manufacturers focus solely on the dimensions, while they should also consider injection speed and material flow direction. When you maximize your process window, you can ensure consistent part quality. Besides, it will also reduce the risk of production issues and failures.
Step 3. Use Scientific Molding
Many different factors impact the plastic injection molding process. To manage them well, you should implement scientific molding principles.
According to these principles, you must tweak the molding process based on pressure curves while monitoring material viscosity. If you do that, it’s not that hard to reduce cycle time while getting consistent production results.
Step 4. Set Up the Production Process First
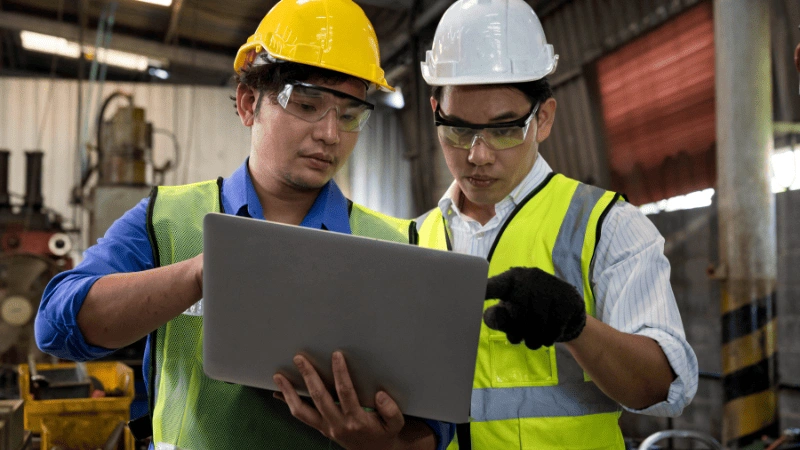
Manufacturers need to create parts in multiple stages, and they should set up the production process first and then make changes to the tool. It is essential because many things can have a significant impact on part size and quality.
Step 5. Pay Attention to Tool Temperature and Venting
Cooling rate and timing depend on the tool. Therefore, you need to ensure that cooling channels, vents, and transducers are adequately located in the tool. When a tool has a proper vent, it will control the overall flow of the plastic. Cooling channels should be well-maintained and clean; otherwise, they will impact the cooling rate.
Step 6. Consider Tool Functionality During Sampling
During sampling, you need to check how the tool functions. The finished part must get out of the tool quickly. However, if parts get stuck or come out deformed, you need to adjust the tools. Also, it’s vital to analyze the cooling and flow. If there is any issue, you need to fix it before finalizing the plastic molding process.
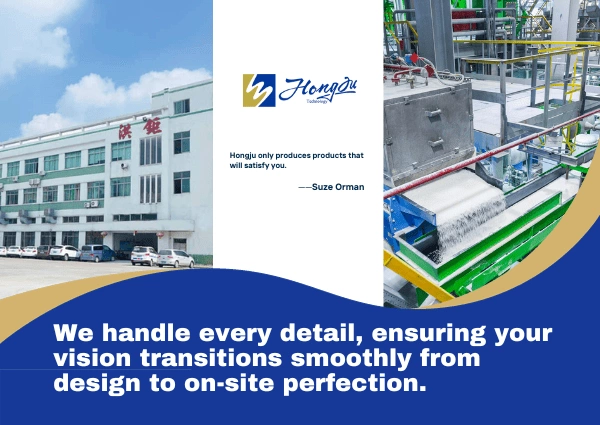
Hongju Awaits Your Quote Request!
Conclusion
Manufacturers always want to unlock substantial benefits through the injection molding method, which is widely used to produce plastic parts and products. The best way to achieve these benefits is to reduce the cycle time. Finally, you know five strategies to optimize cycle time while improving product quality and saving costs.
A boost in production output enables you to meet tight deadlines and gain a competitive advantage. All you need to do is streamline the injection molding process while embracing the culture of continuous improvement.
Don’t forget to invest in human resources and advanced injection molding machines because they let you deliver high-quality products faster and cost-effectively.
Let’s Streamline the Injection Molding Process with Hongju
Do you want to optimize your injection molding process by reducing its cycle time? If yes, it’s time to join hands with Hongju and consult with our expert engineers and material scientists.
We know how to implement effective strategies to thrive in your manufacturing process and keep your business competitive in this dynamic world. Start optimizing your products today and take your manufacturing efficiency to the next level!