Are you working on a critical application and want to ensure o ring reliability? Allow us to become your guide to master o ring seal selection. In this article, you will uncover key insights into O-ring functionality and nuances of compression and squeeze. Ready to enhance your sealing solution and elevate your design? Let’s get started.
Understanding O-Ring Fundamentals
O-rings are extremely simple yet reliable tools. They have become increasingly popular in sealing applications due to their versatility. In this section, we will explore their design, popular applications, and material variations to help you fully understand the O-ring fundamentals.
What is an O-Ring?
O ring is a sealing system in the shape of a circle. It is a loop of elastomeric material, also referred to as packing. This doughnut-shaped closed circular seal is designed to fill gaps between two mating components. Their job is to prevent gas and fluid leakage from the compartments. They are also tasked with keeping contaminants out of the inner compartments of machinery.
An o ring can be used in both static (non-moving) joints and dynamic joints, providing efficient sealing in both situations. Their design is simple yet effective enough to have become a key component of sealing solutions in various applications.

Common O-Ring Applications
O rings have become indispensable in a variety of industries. They are used by engineers and manufacturers in automotive, aerospace, plumbing, and industrial systems to optimize specific application performance. Here are some industry scenarios where O rings play a critical role.
- Aerospace Sector: These little round seals are essential to maintaining the integrity of complex hydraulic systems. Even a thin cross-section O-ring creates a sealing vacuum able to maintain system pressure differential.
- Plumbing Systems: The circular design sits ideally in the inner diameter of fixtures, pipelines, and valves to prevent leaks.
- Automotive Industry: In car or bike engines and transmissions, these seals keep the oil, fuel, and coolant system in the compartments, allowing only the required amount to escape.
- Manufacturing Industry: It is the perfect option for maintaining seals in high-pressure oil and gas pumps.
Materials and Sizes
O rings can be made with various materials depending on the application requirements. The seal material’s hardness and other characteristics directly impact the machine’s functionality. The seal’s ability to handle compressive force, high temperature, chemical exposure, and volume swell changes depending on the material. Some common materials include:
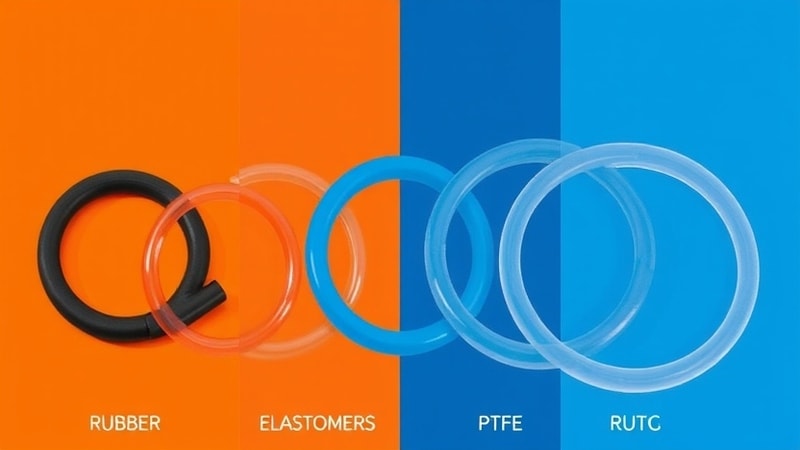
Common O-Ring Materials
- Nitrile Rubber (NBR): A highly resistant synthetic rubber that can resist chemicals, high pressure, and high temperatures. It is mostly used in automotive and industrial settings.
- Silicone: It is a flexible material capable of enduring extreme temperature variations, ozone, and UV radiation. It is non-reactive and biocompatible, making it ideal for food processing and medical equipment.
- Polyurethane: It is a plastic abrasion-resistant material used in situations where mineral oils and greases are involved. It adds tensile strength to the O-ring features.
- EPDM Rubber: This is another synthetic rubber designed to resist ozone, UV radiation, and weathering damage. It is ideal for HVAC systems and potable water applications.
- Coated Rubber: Simple rubber enhanced by coatings resists friction, weathering, chemical exposure, and abrasion under intensive conditions without any damage.
- Neoprene: Neoprene is a highly chemical-resistant material that can handle temperature variations as well. It is one of the low abrasion-resistant materials, hence suitable for environments like refrigeration or marine systems.
- Viton: Viton O-rings are created to cater to demanding environments where all sorts of resistance are required, such as aerospace, automotive, and chemical processing.
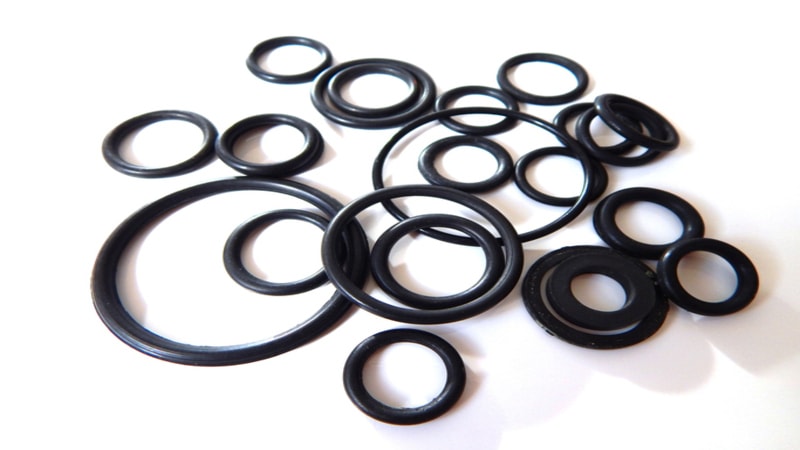
Size Considerations:
O ring sizes are determined by inner diameter (ID), outer diameter (OD), and cross-sectional area. There are standardized systems such as AS568 and ISO 3601 that have classified o rings into standard sizes.
However, you can use an O-ring calculator to determine the exact dimensions of the O-rings required for your application. You can also contact a custom manufacturer to create an o-ring groove design that will provide the perfect face seal for your project.
O-Ring Design Considerations
There are three vital components of the ring design all of which depend on the groove size. The design considerations should be taken seriously, as a minor difference can lead to seal failure.
O-Ring Cross Section
It is the diameter of the round cross-section of the O-ring cord. There are a couple of standards in place, such as AS568 and ISO 3601, that define the groove size and their compatible o rings. The cross-section sizes according to ISO 3601 range from 1.02 mm to 6.99 mm.
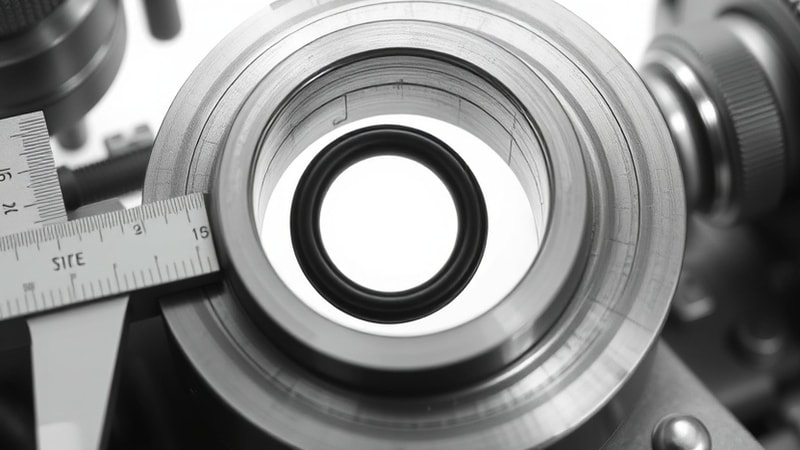
As a rule, the o ring cross section should be at least 15 percent smaller than the groove cross-section. The extra space is given so that the material can compress in the joint without getting damaged. The size obviously affects the o ring’s ability to seal and resist.
O-Ring Material Selection
The material of the O-ring impacts the functionality of the seal in a fundamental manner. If the seal material is not compatible with the application requirements, then it can lead to product failure. The two key factors in O-ring material selection are:
Hardness of Elastomer
The hardness of an elastomeric material is measured on a Shore A scale and directly impacts the seal’s performance and durability. A lower number on the Shore A scale indicates the softness of the material, while a higher number represents the harder material.
The softer O rings are highly flexible, allowing them to flow into microfine grooves to enhance the sealing efficiency. They work perfectly fine in static and low-pressure systems. You can also use softer O-rings for irregular mating surfaces if your budget does not allow for a custom modification.
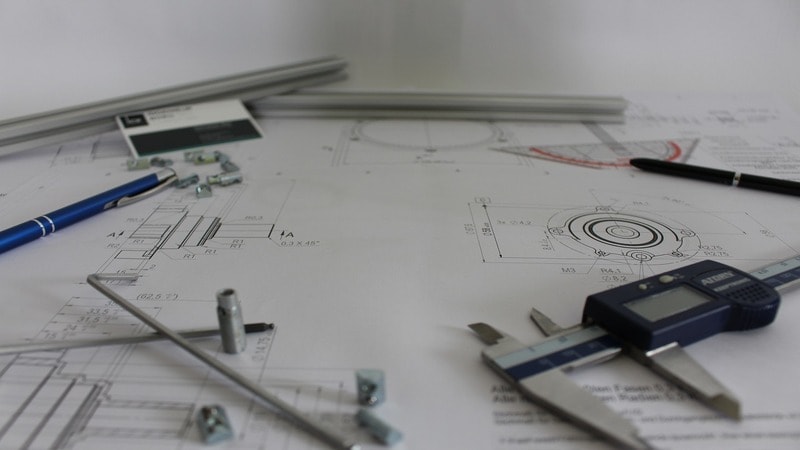
The harder o rings offer excellent resistance to extrusion, making them essential for high-pressure applications. If seal displacement due to gaps is a critical factor, then you cannot opt out of a harder material for your O-ring. They are ideal for high-pressure operations with wide extrusion gaps.
Understanding the balance between softness for better sealing and hardness for extrusion resistance helps in selecting the appropriate O-ring for specific operating conditions.
Chemical Resistance
Chemical resistance is a vital factor for O-ring material selection. It ensures long-term performance without the threat of failure in chemically intensive environments. Most O-rings are created from material compounds that are formulated by adding substances to polymer bases. The resultant compounds offer enhanced durability, temperature, and chemical resistance.
The polymer materials have been discussed above in the materials section. Generally, O-rings are made with nitrile, EPDM, Viton, or silicone. The key factor in material differentiation is chemical resistance.
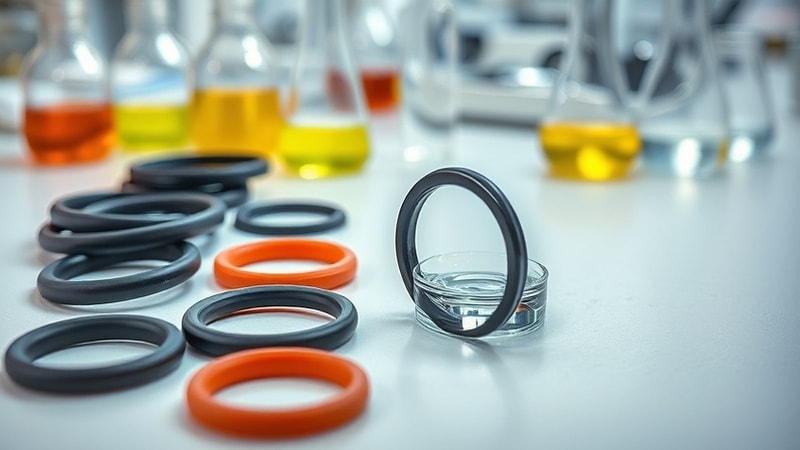
In the end, you should choose a material that offers a balance between resistance to chemical degradation and required mechanical properties.
O-Ring Installation and Mounting
Installing an O-ring correctly is crucial to ensuring its effectiveness and longevity in sealing applications. Proper assembly techniques not only prevent O-ring damage but also enhance its sealing performance.
You can use an assembly grease to reduce friction during installation. It allows the O-ring to slide smoothly in the groove. It is quite helpful, especially when working when tight grooves or hard materials.
Moreover, there are specialized o ring installation tools that have blunt edges to minimize the risk of damage during installation. Any sharp or metallic tool can compromise the O-ring integrity by causing a puncture or tear.
Additionally, care should be taken to avoid contact with sharp edges or burrs on mating components, as these can nick or cut the O-ring during installation. Only efficiently installed O-rings can provide optimal sealing performance.
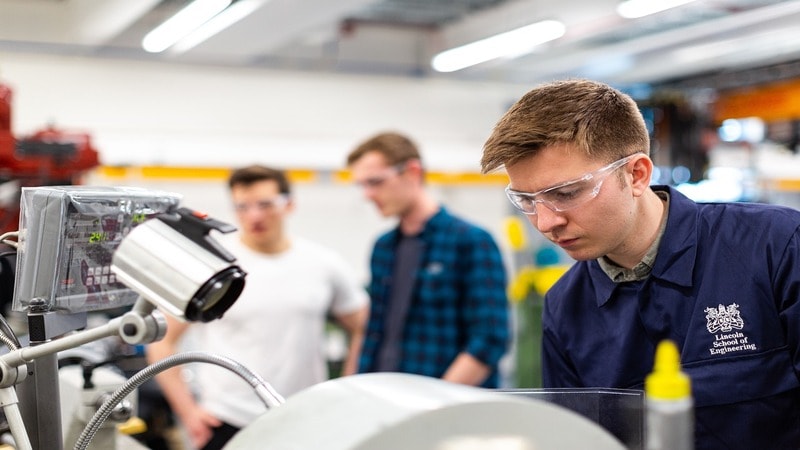
O-Ring Performance Factors
Several key factors, including compression stress, surface finish, and gland design, influence the performance and reliability of O-ring seals. Understanding these factors is essential for anyone working with O-rings in their project.
Compression Load
Compression load is the force required to compress the O-ring into its groove. It depends on the material properties of the O-ring, its cross-sectional thickness, and the percentage of compression applied. Softer materials require lower compression loads as compared to harder materials that demand higher forces.
You can refer to compression load tables. Such documents provide precise information to calculate the required O-ring compression force based on the application parameters and compressive strength. Proper compression load ensures that the O-ring is compressed enough to provide effective sealing without being damaged due to over-compression.
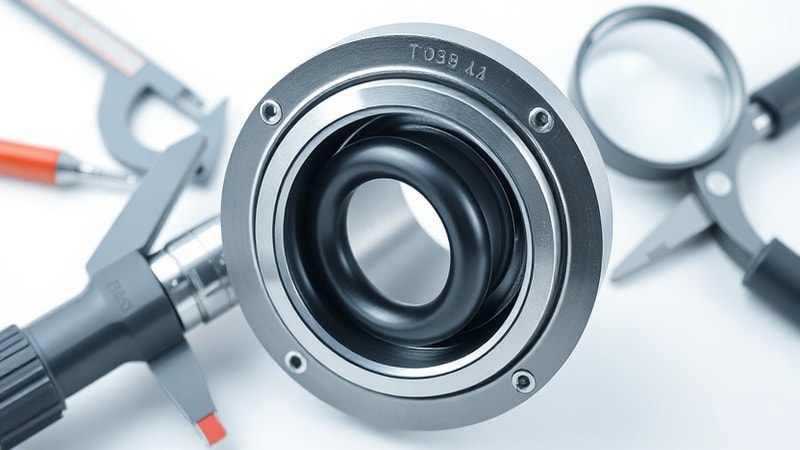
Surface Finish and Gland Design
The condition and design of the gland are equally important for optimal performance. The surface should be smooth so the O-ring can fill in any microscopic gaps, ensuring a tight seal. The surface texture is measured in micometers or micro inches, indicating roughness. A smooth surface is essential in high-pressure and vacuum environments.
The gland design should also align with the O-ring dimensions. Furthermore, the gland material tolerances should complement the O-ring properties to minimize the risk of failure. The gland design preparation and alignment with the O-ring are essential for ensuring a long-term and reliable seal.
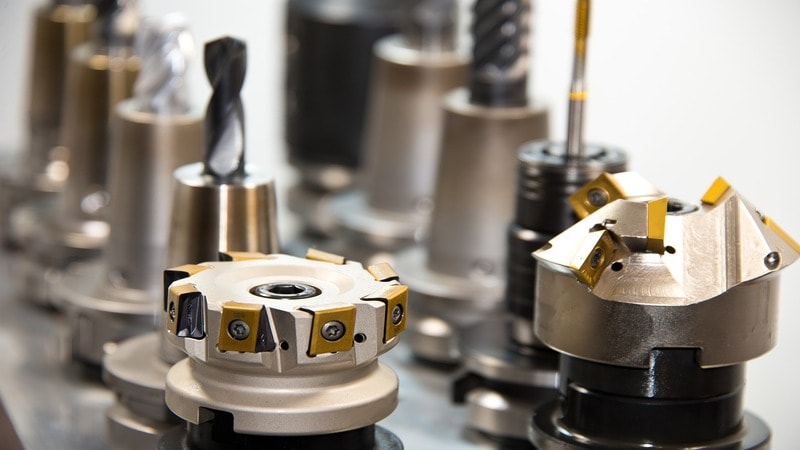
O-Ring Application Consideration
The right application conditions are essential to ensure optimal performance and long life of O-rings.
Pressure and Clearance
O-rings have the capacity to withstand varying pressure ranges depending on the material. Some O-rings are created for low-pressure static applications, while others work ideally in high-pressure hydraulic systems.
Moreover, the gland clearance gap also has a direct influence on the compression load and sealing performance of the O-ring. An optimal gap is critical to prevent extrusion and maintain a perfect seal under pressure.
Eccentricity and Side Loading
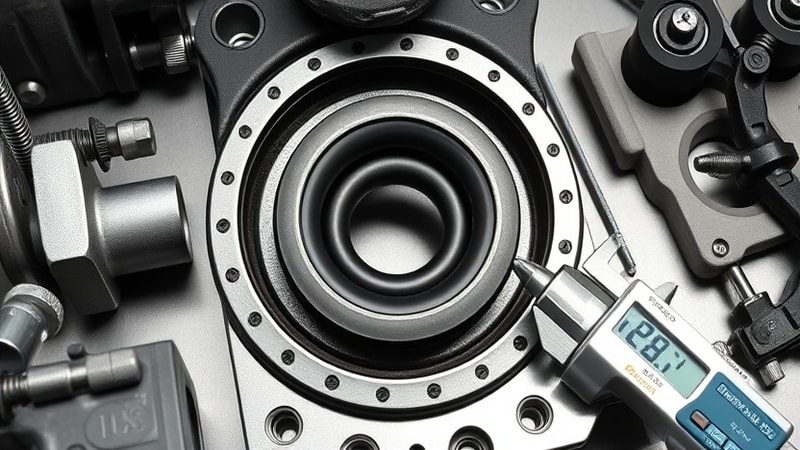
Eccentricity means misalignment and side-loading translates to uneven forces. Both factors can cause severe wear and tear and premature failure of the O-ring. These risks can be avoided by ensuring proper installation and use of backup rings for support. It is also important to align the design and material tolerances of both the O-rings and the gland to avoid eccentricity and side loading.
O-Ring Tolerances and Standards
O-ring tolerances are the acceptable dimensional deviations. These tolerances play a critical role in ensuring optimal performance and optimal fitting. The tolerance for O-rings and the gland should be perfected to avoid any issues.
The dimensional o ring tolerances include inner diameter (ID), outer diameter (OD), and cross-sectional thickness. These determine the fitting of the ring in the gland thus directly influencing seal efficiency.
The material tolerances ensure the O-ring’s properties align with the project demands. These include hardness, chemical resistance, and compression characteristics. Controlling these tolerances prevents material extrusion, degradation, or failure under stress.
The standard o rings are built in compliance with industry standards. The material is also selected based on ASTM D2000 standards. These standards dictate acceptable limits of sizes and material properties ensuring reliable performance across the world.
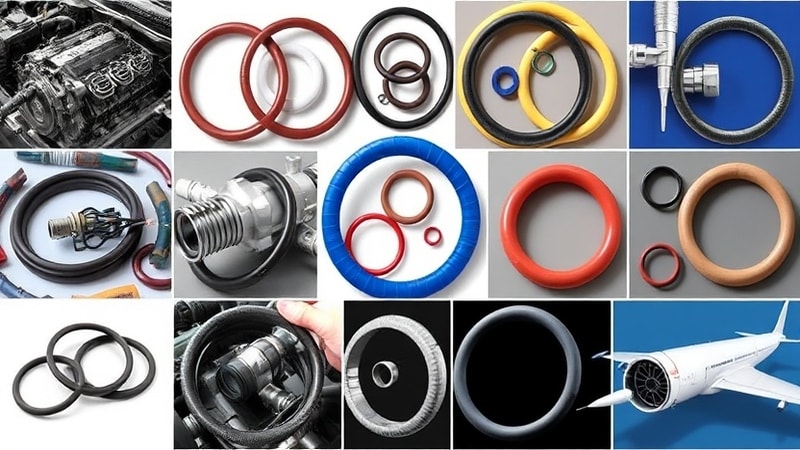
O-Ring Alternatives and Future Developments
Although O-rings dominate the manufacturing industry, some complex designs require the invention of other seal designs. Some O-ring alternatives include:
- X-rings
- Flat gaskets
- lip seals
- V-rings
Best Practices for O-Ring Selection and Design
Selecting the ideal O-ring design for your application requires attention to several key factors. These are the best practices to follow while selecting O-rings
- Material: Opt for polymers that can withstand your application conditions.
- Gland Design: align O-ring squeeze compression, gland depth, installed stretch, and surface finish with the gland design.
- Compression ratio calculation: evaluate the factors impacted by compression load, such as cross-section thickness.
Common Mistakes in O-Ring Selection and Installation
Mistakes during O-ring selection and installation can compromise performance, leading to leaks, material degradation, or seal failure.
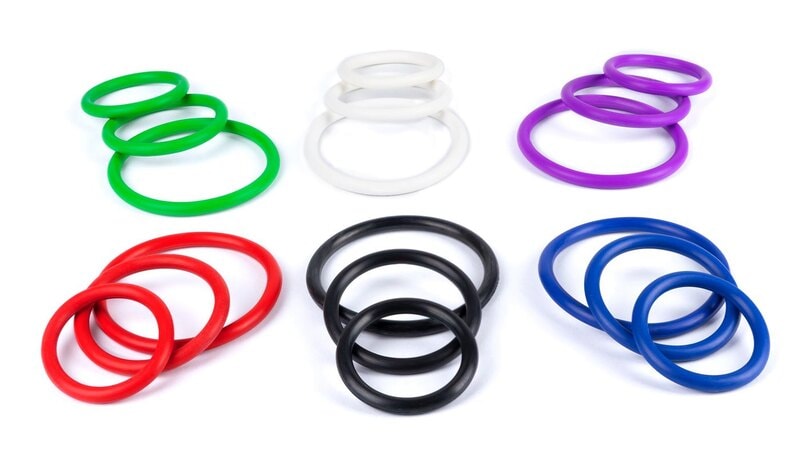
- Temperature and pressure have a profound impact on O-ring functionality. For example, nitrile rings can degrade in high temperatures, while EPDM and neoprene will function ideally
- Inaccurate compression calculations can lead to either extrusion or poor sealing. For example, a hydraulic system can fail if improper compression percentages are applied.
- Choosing the right material is essential for optimal functionality. For example, using EPDM in chemical environments will cause it to fail completely.
How to Choose the Right O-Ring for Your Application
Here is a step-by-step breakdown of an O-ring selection process.
- Define the application requirements, factoring in temperature, pressure, and chemical exposure.
- Account for exposure to UV light, ozone, or abrasion, and select a material resistant to these factors.
- Select material compatible with the project
- Calculate the optimal percentage for compression and squeeze based on the application’s gland dimensions.
- Measure the inner diameter and cross-section using tools like an O-ring calculator to ensure a precise fit.
There are a couple of tools available online that can assist in O-ring selection. These tools include O-ring calculators, material compatibility guides, and sizing tools such as O-ring cones.
Frequently Asked Questions
Q1. What lubrication should be used with an O-ring seal?
A1. Lubricant needs to be selected based on compatibility with the O-ring and groove material. silicone-based greases are used for general purposes while fluorinated lubricants are used where chemical resistance is necessary.
Q2. Can O-rings be reused after disassembly?
A2. It is generally not suggested to reuse O-rings since they may have undergone deformation or chemical deterioration which reduces their sealing efficiency.
Q3. How does temperature affect O-ring performance?
A3. Extreme temperatures can cause O-rings to harden or soften, leading to seal failure.
Conclusion
O-rings are extremely important components for machine building. Understanding their compression, squeeze, and seal performance is essential to obtaining optimum sealing performance.
By leveraging the knowledge in this guide, you can select just the right O-ring for your application needs.
Ready to find the perfect O-ring for your needs?
Ready to optimize your sealing performance? Explore our comprehensive product catalog or schedule a free consultation with our experts to discover the best O-ring solutions for your business.