How do rubber properties impact its applicability? Let’s explore essential rubber properties like tensile strength, heat resistance, elasticity, and compression. Understanding these rubber characteristics enables its efficient usage.
Every product, ranging from a gasket to surgical gloves, has different specifications. Manufacturers select specific rubber types based on their characteristics to produce a variety of products. Whether you’re planning to use rubber as a raw material or just want to understand its characteristics, we’ve got you covered!
What is Rubber?
Rubber is an elastomer (polymer with elastic characteristics) categorized as natural rubber and synthetic rubber. The major difference is in their composition.
Natural rubber is extracted from latex trees that usually grow in tropical environments. Hevea brasiliensis (Rubber Tree) and Parthenium argentatum (Guayule) are common trees that produce natural rubber composed of a natural polymer called polyisoprene.
Synthetic rubber is produced from petroleum products through chemical synthesis. It is composed of artificial polymers like butadiene, styrene, etc. The composition changes for different rubber types.
Synthetic rubber has more enhanced properties than natural rubber. It is produced to meet certain specification criteria for different applications. Both natural and synthetic rubber are used extensively in a variety of industries.
From an application point of view, rubber is an indigenous material that has been used since 1600 BC or before. It was used in the waterproofing of textiles, medicines, and toys. Later, with modernization in the 18th century, rubber was synthesized. It became a versatile material seen everywhere.
In the automotive sector alone, tires, seals, gaskets, hoses, and belts are made from rubber. It also has critical use in the medical sector; surgical gloves, catheters, etc, are rubber-made. Other applications involve sports equipment, electrical insulation, adhesives, and sealants.
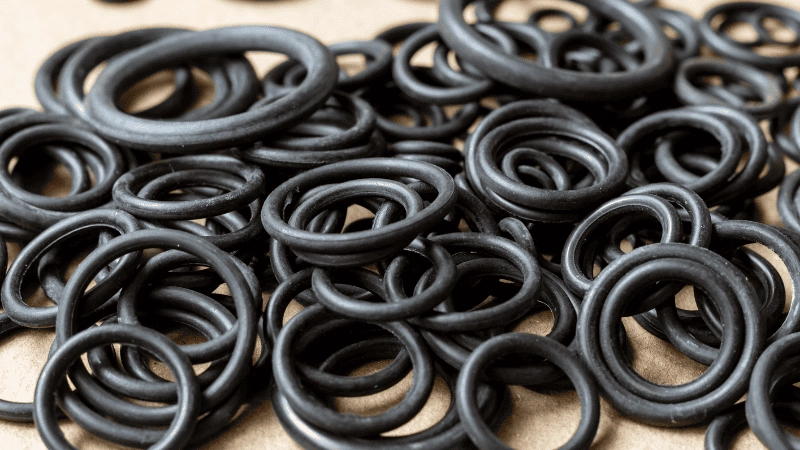
Physical Properties of Rubber
Physical properties of rubber are critical to determine its suitability for different applications. These rubber characteristics describe its interaction with the environment.
Let’s discover the physical properties of rubber and how you can measure them.
Hardness
Hardness is the resistance to deformation upon exertion of a force. It is an inherent property in rubbers due to their chemical structure. Every rubber type has a different level of hardness, which is set according to the intended application.
The hardness level can be modified through chemical compounding. Commercially available rubbers have different hardness levels. Hardness determines the load-bearing capacity of a rubber. It is a crucial performance parameter when selecting rubber for different applications.
Hardness is measured using a durometer on a shore scale. It determines the level of hardness on a scale of 100. The ASTM D2240 standard acknowledges 12 shore scales for a variety of rubber types. The categorization is based on rigidity levels. Commonly used shore scales include Shore A and Shore D. You can use Shore A for soft to medium-hard rubber and Shore D for highly rigid rubbers.
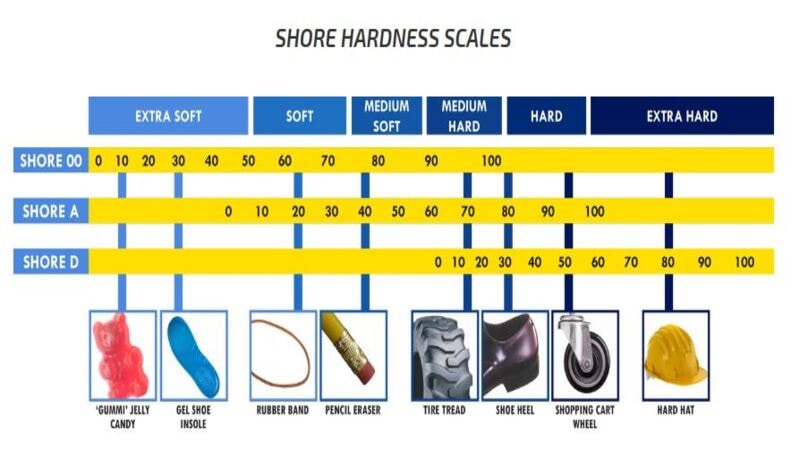
Tensile Strength
Tensile strength is the material’s ability to withstand a force to the point it breaks when being stretched. Simply put, tensile strength in rubbers is resistance to breaking when pulled apart. It is the breaking point that can’t be exceeded under any circumstances.
Tensile strength is a crucial consideration when choosing a rubber for any application. It impacts key performance parameters like durability, stress resistance, deformation, etc. Rubber products like tyres, conveyor belts, seals, and others need to have high tensile strength due to exposure to high pressure.
When compared to natural rubbers, synthetic rubber like styrene butadiene rubber (SBR) has a high tensile strength.
Tensile strength in rubbers is also referred to as Ultimate Tensile Strength (UTS), which signifies the material’s breaking point. The measurement unit for tensile strength is megapascals or pounds per square inch (psi) according to ASTM D412 standards. You can conduct a Tensile Strength Test (TST) employing a Universal Testing Machine (UTM) to measure the material’s tensile strength under a controlled environment.
Thermal Resistance
Thermal resistance is a material’s ability to withstand heat without any impact on chemical or physical properties. Rubbers offer good heat resistance, preventing heat flow due to their inherent composition. Many synthetic rubber types are modified to have high-temperature resistance for usage in electrical insulation and hot pipes.
Thermal resistance is measured based on the thermal conductivity of the material. It determines the amount of heat rubber can conduct. The lower the thermal conductivity, the higher the temperature resistance will be. Both parameters have an indirect relationship. According to ASTM C177 standards, a guarded hot plate test is suitable for measuring thermal resistance. The unit of thermal resistance is (K·m²/W).
Thermal resistance is one of the crucial properties of rubber. It affects the performance in high-temperature applications, especially in industrial settings. Rubber products like seals and gaskets need to have high-temperature resistance due to long exposure to high heat and pressure.
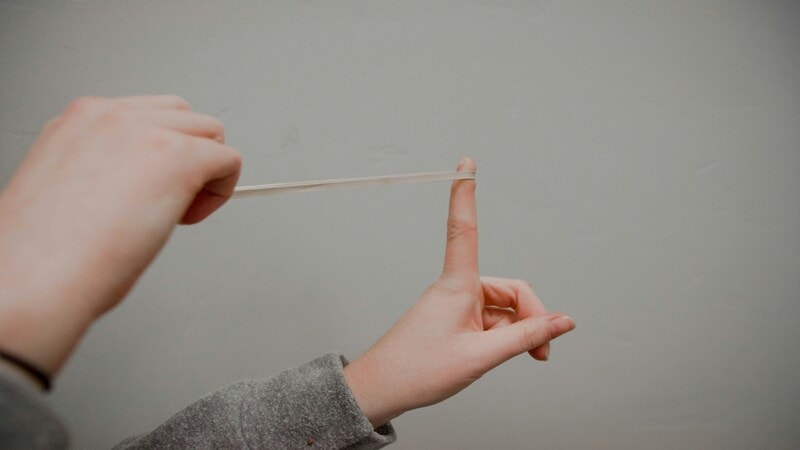
Mechanical Properties of Rubber
The mechanical properties of rubber dictate its behavior in different operating conditions. Understanding these rubber characteristics is necessary to see how rubber reacts when exposed to a variety of forces and stresses.
Elongation
Elongation is the stretching of a material due to tensile stress increasing its original length. Rubbers are highly elastic materials and tend to elongate three to four times their original length. This property enables the application of rubber in different settings.
Elongation is measured as a percentage increase in length. For instance, if a rubber elongates double its length, the elongation level will be 100 percent. Silicone rubber has the highest elongation rate, and it stretches 300% to 700% of the original length.
Why is elongation necessary? Rubber is used in different products that undergo extreme stress, like car tyres, gaskets, seals, etc. A certain level of flexibility is needed to prevent breaking. For example, the gasket stretches threefold under pressure. Similarly, other simple products like rubber gloves need to have good flexibility for proper fitment.
Resilience
Resilience is the material’s ability to absorb energy when stretched and release it to retain its original shape without deforming. Resilience in rubbers is a property that enables them to regain their original size and shape after undergoing deformity due to compressive, tensile, or bending forces.
Rubbers have good resilience due to their inherent molecular structure and bonding. It is measured as rebound resilience, which is the percentage of energy released compared to the percentage of energy absorbed. A greater than 50% rebound signifies a good resilience. The ASTM D7121 standard suggests a Rebound Resilience Test (RRT) to measure resilience in rubbers.
Rubber is best suited for applications where deformity is recurring. It is extensively used in dynamic seals due to its good resilience. Other applications include weatherstripping and use in sports equipment. Therefore, understanding resilience in rubbers allows you to select the appropriate rubber material properties for specific applications.
Durability Properties of Rubber

Durability increases the usability of rubber for a variety of applications. When selecting a rubber type, you must understand its specifications to ensure efficient operations. The following properties are critical to maintaining rubber’s structural integrity and performance levels for better durability.
Tear Resistance
Tear resistance is a property of material that prevents rupture when experiencing high tension. Rubber projects a good tear resistance due to its elastic nature. It prevents any tear or cut caused by rough metal edges or sharp objects. The propagation of cuts and nicks is also prevented to maintain operability.
Tear resistance is measured in kilonewtons per meter (kN/m) or pound-force per inch (lbf/in). The ASTM D624 is a standard test conducted to check tear resistance in vulcanized rubber material. It simply measures the amount of force required to propagate a tear. You should avoid exerting force over the resistance limit.
Tear resistance is a critical characteristic of rubber when used in high-tension applications in automotive, industrial, and other sectors. For example, conveyor belts in mining are exposed to sharp objects. You would need rubber material with high tear resistance for efficient operations.
Abrasion Resistance and Compression Set
Abrasion resistance is a material’s ability to resist abrasion (damage due to scraping or rubbing against itself and other objects) without deforming. Compression set refers to the material’s inability to decompress to its original shape and size after experiencing compression load. Both are critical rubber characteristics that impact durability.
Abrasion resistance is not measured in specific terms; however, the Abrasion Loss Test is employed to check the resistivity according to ASTM D394 standards. Similarly, the compression set is measured and tested based on the ASTM D395 criterion. It quantifies the permanent deformity due to compression.
Ideally, rubbers should have high abrasion resistance and low compression set for optimal performance. Rubber used in shock absorbers, conveyor belts, and dynamic seals experience continuous friction and compression. When selecting a rubber for a similar application, you must consider these rubber material properties.
Types of Rubber Materials
Let’s explore different types of rubber materials and their key characteristics. Usually, rubbers are in two categories, i.e., natural and synthetic rubbers, with the addition of specialty rubbers.
Natural Rubber (NR)
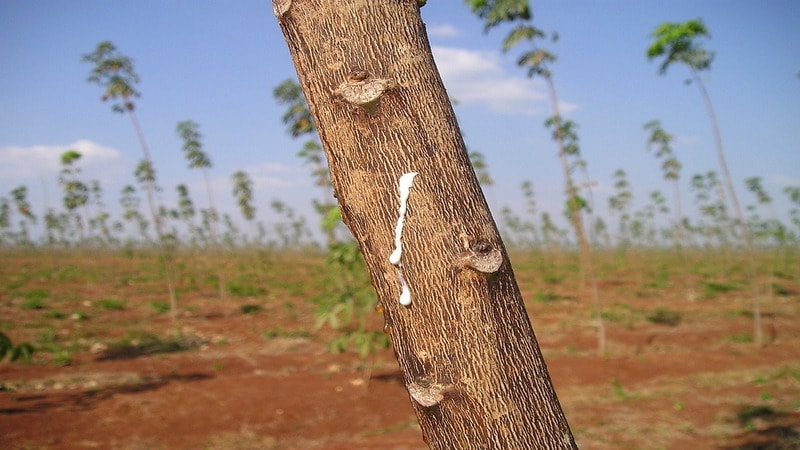
Natural rubber comes from tropical and subtropical trees found in countries like Brazil, India, Indonesia, Malaysia, and Sri Lanka. The trees have latex (a white liquid stored in plant tissues) that includes rubber particles. The rubber is formed naturally through polymerization (combining of monomers) of isoprene.
Natural rubber properties are better than synthetic rubber. It offers excellent mechanical properties, including tensile strength, elongation, tear resistance, and resilience. It is also renewable and sustainable. However, natural rubber properties project lower resistance to high temperatures and chemical interferences.
Natural rubber has specialized applications in the medical, aerospace, and footwear industry. Latex gloves are extensively used for their biocompatibility. Similarly, seals and gaskets incorporated in spacecraft are made from natural rubber. Most army shoes have natural rubber soles due to their comfort and durability.
Synthetic Rubber
Synthetic rubber is artificially produced through chemical synthesis of petroleum or natural gas byproducts. Usually, the copolymerization of butadiene with a monomer results in synthetic rubber. It mimics natural rubber properties with improved chemical and heat resistance.
The popular synthetic rubber types include styrene-butadiene rubber (SBR), butyl rubber, neoprene, nitrile rubber, and EPDM. All of these rubber types have high durability and boosted rubber properties. They’re used in high-performance applications like automotive tires, hoses, pipes, seals, gaskets, conveyor belts, etc.
Synthetic Rubber | Natural Rubber |
---|---|
Chemically produced from petroleum-based monomers through polymerization | Extracted from latex in rubber trees through tapping |
Composed of artificial polymers like styrene-butadiene, butyl, and neoprene | Composed of natural polyisoprene polymer formed through the polymerization of isoprene |
Strength characteristics depend on the chemical composition | Excellent physical and mechanical properties like elasticity, tensile strength, and tear resistance |
Enhanced resistance to chemical substances and high-temperature | Low chemical and heat resistance. |
Non-renewable and hazardous to the environment | Renewable and natural product |
Specialty Rubber Materials
Specialty rubbers are modified synthetic or natural rubbers to have application-specific properties. The natural rubbers are modified by vulcanization, a process through which cross-links are embedded in the rubber structure to increase its strength, elasticity, resistance, etc. Similarly, the chemical composition of synthetic rubber is changed to modify its characteristics.
Some common types of specialty rubbers include silicone rubber, fluorocarbon rubber, and nitrile rubber. The silicone rubber has a high-temperature resistance of -55°C to 300°C. It also shows the longest elongation, about 500%-700% of the original length. The material is resistant to ozone, UV radiation, and weathering. It is used in aerospace applications, specifically for seals, gaskets, and o-rings.
Similarly, fluorocarbon rubber and nitrile rubber offer exceptional chemical resistance to petroleum oils and fuels, solvents, acids, etc. Fluorocarbon rubber is an essential material extensively used in oil and gas sectors to develop compatible seals and gaskets. Nitrile rubber is popular in industrial applications and the medical sector. The medical gloves and protective wear are usually made from nitrile rubber.
Applications of Rubber Materials
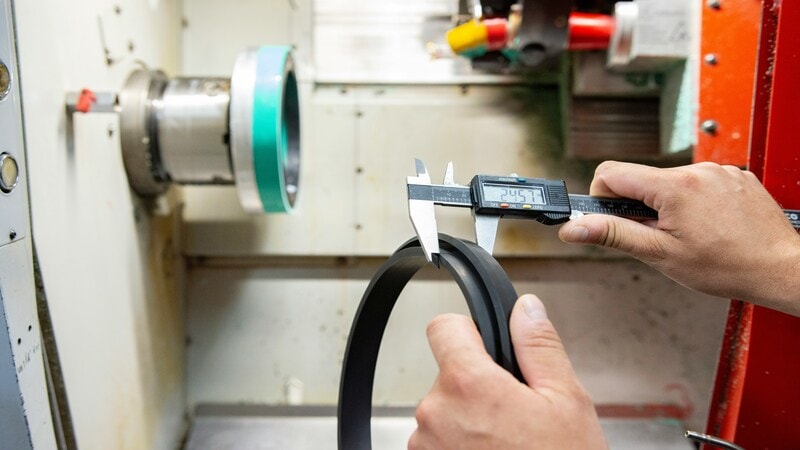
Rubber is used to manufacture a variety of products. From car tires to toys, you will find rubber almost everywhere. Let’s explore rubber material properties and applications:
Industrial and Automotive Applications
Rubber material is extensively used for industrial and automotive applications due to its mechanical and physical properties. For instance, the elasticity, flexibility, and good heat resistance of rubber make it an ideal material for critical components in car engines like gaskets, seals, and hose pipes. The high wear resistance and anti-weathering make it the best option for car tires.
Similarly, high abrasion resistance and low compression set enable rubber application in industrial settings. The vibration dampers, engine mounts, belts, and rollers in conveyor systems are made of rubber.
Consumer Applications
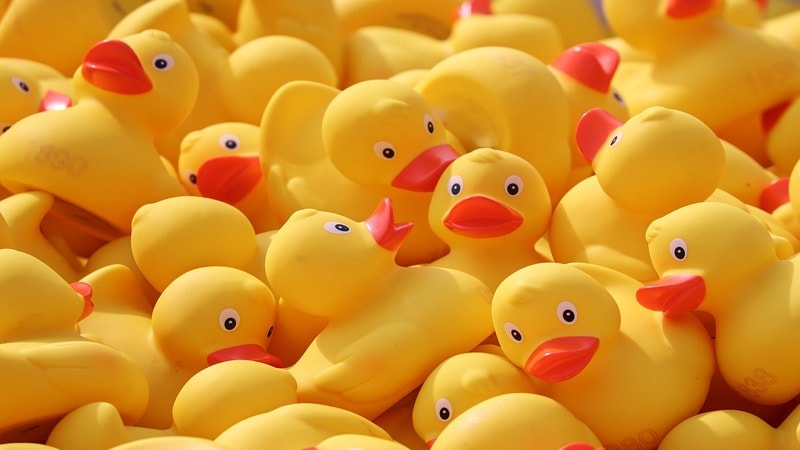
Rubber is a versatile material that is not limited to industries only. Many consumer products have rubber in them. You can find rubber in yoga mats, wearable fitness trackers, and shock-absorbing shoe soles.
The resistance to chemicals and water makes rubber best for toys, sporting goods, and household items. Rubber material is ideal for any product that requires flexibility, durability, and resistance to wear and tear.
FAQs
What are the benefits of rubber?
Rubber is a versatile material with unique properties like tensile strength, heat resistance, elasticity, and compression. It is used in the manufacturing of a variety of materials, including tires, seals, toys, shoe soles, etc.
What is the difference between natural and synthetic rubber?
Natural rubber is extracted from trees through indigenous techniques while synthetic rubber is produced from the chemical synthesis of petroleum byproducts. Both rubber types have comparable properties but different chemical compositions.
What are the properties of synthetic rubber?
Synthetic rubber has similar properties to natural rubber; it’s highly elastic, durable, resistant to heat and chemicals, and offers excellent impermeability to water.
Conclusion
Rubber is an essential material used across various industries. Its unique blend of properties like tensile strength, elasticity, heat resistance, etc, make it an indispensable material. There are a multitude of applications of rubber in medical, automotive, industrial, aerospace, fashion, and other sectors.
Understanding rubber material types and characteristics helps you make its efficient use. We have provided you with an in-depth analysis of critical rubber characteristics. You are in a good position to select the right material type with the required specifications as per your needs.
Get Tailored Solutions for Your Rubber Material Needs
Hongju is synonymous with high-quality and innovative products. We have a wide range of products for household appliances, consumer electronics, medical equipment, automotive, and electromechanical sectors. We have been leading the innovation by offering tailored solutions to our customers. You can come up with any performance specification, and we will engineer it from scratch!
What are you waiting for? Get in touch with one of our representatives for queries, ordering mechanisms, or anything you want.