Yet, with its rising popularity, there’s a swirl of information, both accurate and misconceived, surrounding this technique. In this article, we embark on a journey to dissect the truths from the myths, ensuring that stakeholders and enthusiasts alike gain a clear understanding of the marvel that is LSIM.
What is Liquid Silicone Injection Molding?
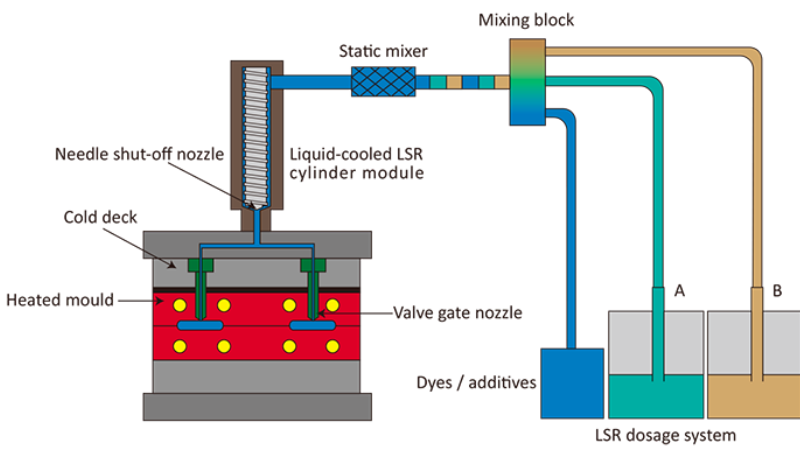
Liquid Silicone Injection Molding(LSIM) is a specialized molding technique used to produce precision parts from liquid silicone rubber. Unlike traditional molding methods that involve solid, granular forms of material, LSIM utilizes a two-component, platinum-cured liquid silicone rubber which is pumped into a heated mold cavity. As the silicone fills the mold, it undergoes vulcanization, a process where it transforms from a liquid to a solid state due to the application of heat, yielding durable and resilient parts.
Materials Used
Liquid silicone rubber, the primary material used in LSIM, stands out due to its unique properties:
- Temperature Resistance: LSR can withstand extreme temperatures, making it ideal for applications that experience fluctuating thermal conditions.
- Flexibility: The intrinsic flexibility of silicone rubber means products can be designed with intricate details and can endure bending or stretching without damage.
- Biocompatibility: Certain grades of LSR are biocompatible, making them perfect for medical applications where they might be in contact with the human body.
- Chemical resistance: Liquid silicone rubber resists water, oxidation, and some chemical solutions such as acids and alkalis.
Understanding the LSIM process and the capabilities of liquid silicone rubber paves the way for grasping the myriad applications and potential innovations achievable with this method.
How Does Liquid Silicone Injection (LSI) Molding Work?
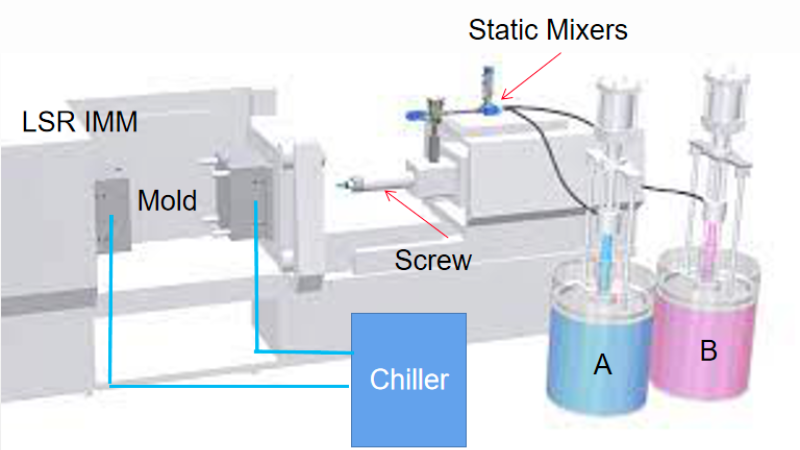
Liquid silicone injection molding, also known as LSR injection molding, is a widely used manufacturing process for creating precise and high-quality silicone parts. This method involves the use of liquid silicone material that is injected into a closed mold under high pressure, resulting in the formation of the final product within minutes. Let’s take a closer look at how molding processes work.
Mixing the Liquid Silicone Material
The first step in LSI molding is preparing the liquid silicone material by mixing two components: the base polymer and the crosslinker. These components are carefully measured and combined to achieve the desired properties of the final product. The base polymer provides elasticity and stability, while the crosslinker promotes the curing or solidification of the material.
Injection into Closed Mold
Once the liquid silicone material is mixed thoroughly, it is ready for injection into a closed mold. An injection machine is used to inject the material into the mold under high pressure. The mold is designed according to specific requirements and can be customized to produce various shapes and sizes of LSR parts.
Rapid Curing Process
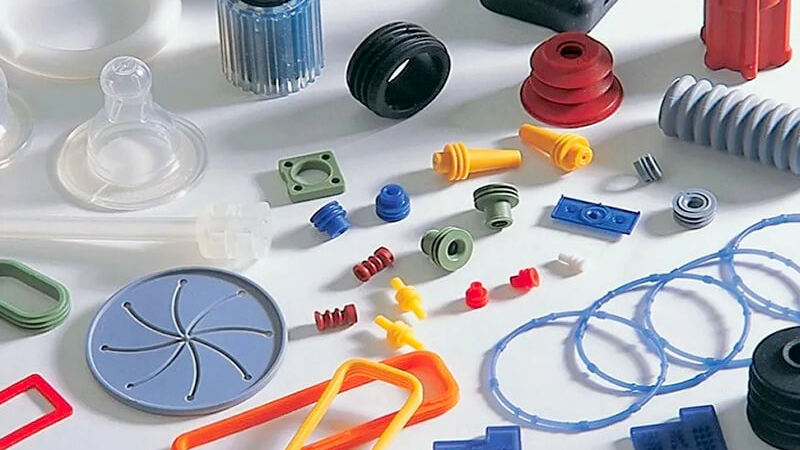
As soon as the liquid silicone material enters the closed mold, heat from within causes rapid curing or solidification of the material. This curing process takes place within minutes, allowing for quick production turnaround times. The heat applied can vary depending on factors such as part complexity and desired properties.
Precise Control over Parameters
One significant advantage of LSI molding is its ability to offer precise control over various parameters throughout the manufacturing process. Temperature, pressure, and curing time can be carefully adjusted to meet specific requirements for each part being produced. This level of control ensures consistent quality and reduces variations in finished products.
LSI molding allows manufacturers to create intricate designs with fine details that would otherwise be challenging or impossible with other manufacturing methods. It enables efficient production by minimizing waste since excess materials are not typically generated during the process.
Advantages and Benefits of Liquid Silicone Rubber Molding
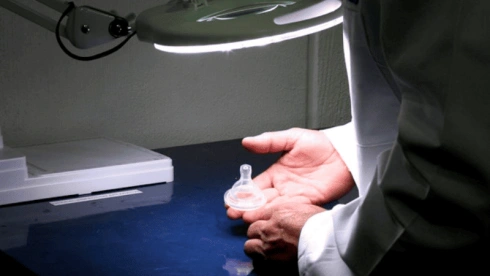
Liquid Silicone Rubber (LSR) Molding, a form of Liquid Silicone Injection Molding, has gained immense popularity in various industries, from medical to automotive, and for good reasons. Here are some of the standout advantages and benefits of this molding process:
- Exceptional Thermal Stability: Liquid silicone rubber can withstand extreme temperatures, both high and low. This makes LSR products suitable for applications that experience varying temperature conditions.
- Flexibility and Durability: LSR products maintain their flexibility over a wide temperature range and exhibit excellent tear strength, making them durable in challenging environments.
- High Precision and Complexity: The LSR molding process allows for the creation of intricate designs and shapes with tight tolerances. It is especially suitable for producing complex components with intricate geometries.
- Fast Curing Times: Due to the nature of LSR and the molding process, curing times are rapid. This quick turnaround time translates to higher production rates.
- Waste Reduction and Cost Efficiency: When delving into the LSIM process, its efficiency in reducing material waste is notably commendable. The nature of the procedure ensures minimal wastage and any excess silicone can often be recycled. This not only leads to a more sustainable manufacturing approach but also significantly lowers the material cost associated with the process.
Liquid Silicone Rubber Molding offers manufacturers versatility, efficiency, and high performance in product design and functionality, making it a sought-after choice in various industries.
Facts about Liquid Silicone Injection Molding
Liquid Silicone Injection Molding (LSIM) is a specialized technology with its own set of facts that often set it apart from traditional injection molding. Here are some factual insights about this advanced molding process:
Fact: Liquid Silicone Rubber is Ideal for Medical and Food Applications
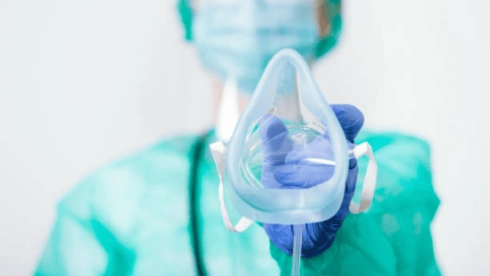
Liquid Silicone Rubber stands out because of its biocompatibility and hypoallergenic properties. This ensures it doesn’t react adversely with medications, body fluids, or even food. This intrinsic quality makes it a go-to material for medical devices, baby products, and culinary tools, ensuring safety and reliability.
Fact: Liquid Silicone Rubber Boasts Natural Transparency
The inherent transparency of liquid silicone rubber offers a plethora of design opportunities. It doesn’t just stop at transparency, though; this property also permits a broad spectrum of color variations, including crystal-clear components. This feature finds its significance in applications such as LED lighting systems or optical lenses where clarity and precision are paramount.
Fact: LSR Parts Offer Sterilization Versatility
Cleanliness and sterilization are paramount, especially in sectors like healthcare. Liquid Silicone Rubber components rise to the occasion, as they can undergo various sterilization methods. Whether you’re considering steam autoclaving, ethylene oxide treatments, or even gamma radiation, LSR parts come out unscathed, ensuring they maintain their structure and function.
Myths surrounding Liquid Silicone Injection Molding
Debunking myths is crucial for understanding and appreciating technology. Here are some myths about Liquid Silicone Injection Molding, followed by the real facts:
Myth: Liquid Silicone Rubber Molding is Expensive
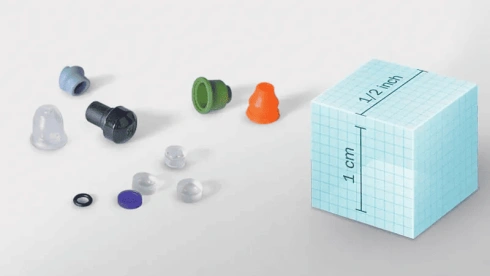
Many believe that due to its advanced nature, liquid silicone injection molding must be costly.
Fact: While the initial setup might have higher costs due to the precision tooling required, the long-term benefits, such as reduced waste, faster cycle times, and lower material costs, make it a cost-effective solution, especially for high-volume production.
Myth: Injection Molded Parts Can Only be Customized Post-Production
The prevalent perception is that parts produced via Liquid Silicone Injection Molding can only undergo customization after they’re made, restricting design flexibility.
Fact: This couldn’t be further from the truth. Liquid Silicone Injection Molding allows for extensive customization during the design phase itself. Modern CAD tools and prototyping methods enable manufacturers to adapt designs to specific needs before production commences, eliminating the necessity for later modifications. Thus, rather than being a limitation, LSIM offers comprehensive design freedom from the get-go.
Myth: Liquid Silicone Injection Molding is Similar to Plastic Injection Molding
A common misconception is that liquid silicone injection molding is just another variant of plastic injection molding, given that both processes involve injecting material into molds.
Fact: While there are similarities in the basic concept, the two processes are distinctly different. Liquid silicone rubber has unique properties that differentiate it from traditional plastics. For instance, LSR can withstand higher temperatures and is more flexible than most plastics. Additionally, the curing process for LSR involves heat-induced vulcanization, which is different from the cooling process used in plastic molding. These variations in materials and procedures lead to diverse outcomes in the finished products.
Myth: LSR Components are Not Environmentally Friendly
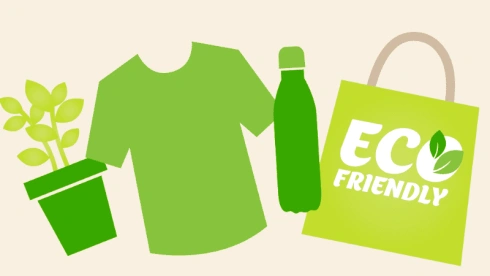
With increasing emphasis on sustainable solutions, any technology that seems to produce waste is eyed with suspicion.
Fact: LSR components are recyclable, and the LSI molding process is highly efficient, producing minimal waste. The ability to produce parts with less material wastage and the longevity of LSR components contribute to its environmentally friendly profile.
Conclusion
In conclusion, liquid silicone injection molding is a widely used manufacturing process for producing high-performance silicone parts with excellent mechanical properties, thermal stability, and a wide range of surface finishes.
By working with the right silicone providers and injection molding experts, manufacturers can ensure that they are getting the best materials and processes for their application, allowing them to produce high-quality, cost-effective silicone parts.
Why go to Hongju for your LSIM Manufacturing needs?
Hongju is a leader in the liquid silicone injection molding industry. Our commitment to quality is built on the principle of zero defects, and we use only the highest quality materials and processes to ensure that every part meets our customer’s specifications.
We also offer in-house R&D facilities to develop the latest silicone materials and processes for our customers, ensuring that our customers always have the best options available.
Take the First Step:
Requst for an Inquire
Quality Meets Affordability. Inquire Now for High-Quality Products at Low Volumes.