Thermoforming is the adaptable shapeshifter, while injection molding unlocks the precise sculptor. Before you decide what the proper process is, you need to learn what injection molding and thermoforming are, what their pros and cons and what materials you can use with both.
To make the selection process simple, you must compare injection molding and thermoforming. Now, are you ready to get an understanding of both methods to the point where you can compare and pick the proper process? So, let’s get started.
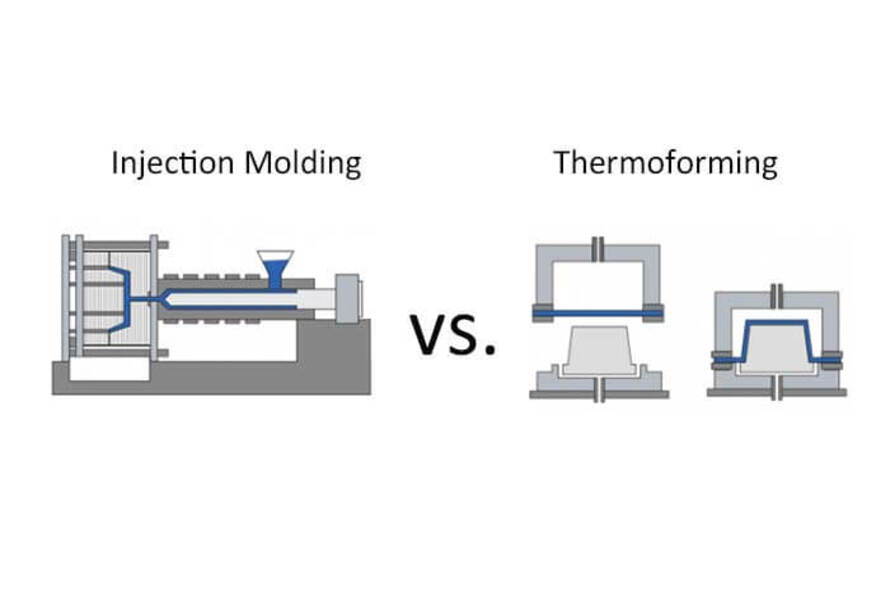
What is Injection Molding?
It is the most famous manufacturing process for creating parts in high-volume production. This process works by injecting molten material into a mold and forming parts. Whether you want to create a high volume of small parts or parts with complex geometries, this method is quite suitable.
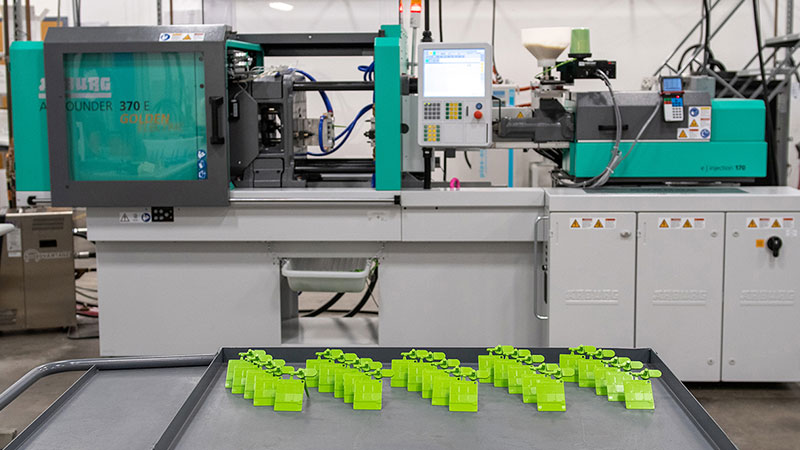
Material used for Injection Molding
Here are some most choice of materials for injection molding.
- Thermoplastic
It is the most commonly used material for this manufacturing process. The best thing about them is that they can be melted and solidified without significant degradation or deformation. The most popular thermoplastics are Polyethylene (PE), Polyvinyl Chloride (PVC), Polystyrene (PS), Acrylonitrile Butadiene Styrene (ABS), Polypropylene (PP), and Polycarbonate (PC).
- Thermosetting Plastics
These materials can’t be melted and reshaped multiple times after molding like thermoplastic. However, they are an excellent choice for applications where high-temperature resistance is a must in heated plastic sheets. These materials are commonly used to produce automotive and electrical components. Two common examples of thermosetting plastics are epoxy resins and phenolic resins.
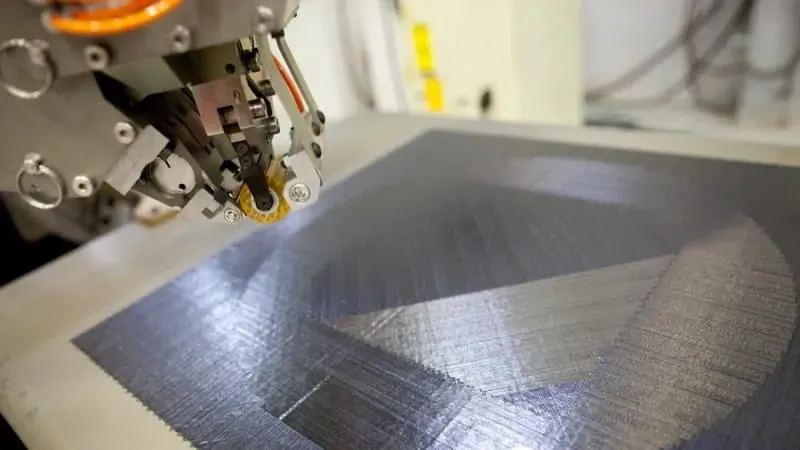
- Elastomers
They are rubber-like materials such as silicone and thermoplastic elastomers that are commonly used for applications that require flexibility and resilience.

- Bioplastics
These materials are sourced from renewable sources and commonly used in packaging and disposable cutlery.
- Metal and Ceramic Powders
When your production requires the creation of high-precision and complex parts, then metal and ceramic powders are used.
Advantages and Disadvantages of Injection Molding
Let’s start exploring the shortcomings and benefits of this plastic injection molding:
Advantages
- The plastic injection molding process is quite suitable for high-volume production. It is possible because mold can have several cavities.
- Whenever you need to complete an order of intricate parts or mass production of small parts, you should always go with injection molding.
- This method is super adaptable to a high level of automation, which is a requisite in the mass production of parts.
Disadvantages
- Many companies think about going with injection molding, but they can’t because the biggest issue is the tooling cost. You need to spend heavily on the creation of molds. Injection molding machines and equipment are expensive.
- When you need to produce complex shapes and designs, the lead time for mold building and repair is high.
Inquire Now for Fast Quotations!
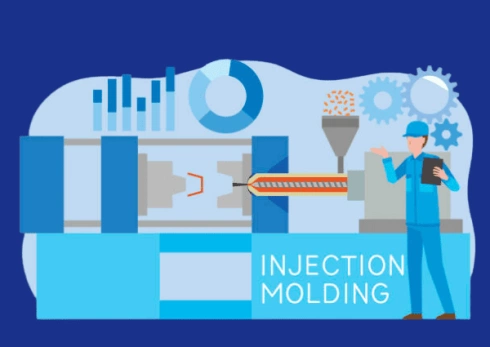
What is Thermoforming?
In this manufacturing technique, heated plastic sheets are pressed into a single mold to create parts. Thermoformed parts are produced by either putting pressure on a sheet or by forcing all the air out of the mold, as in the case of vacuum forming.
Once parts are formed, they are trimmed and finished based on the customer’s requirements. This plastic manufacturing method is an ideal choice for parts with large tolerances and simple geometries.
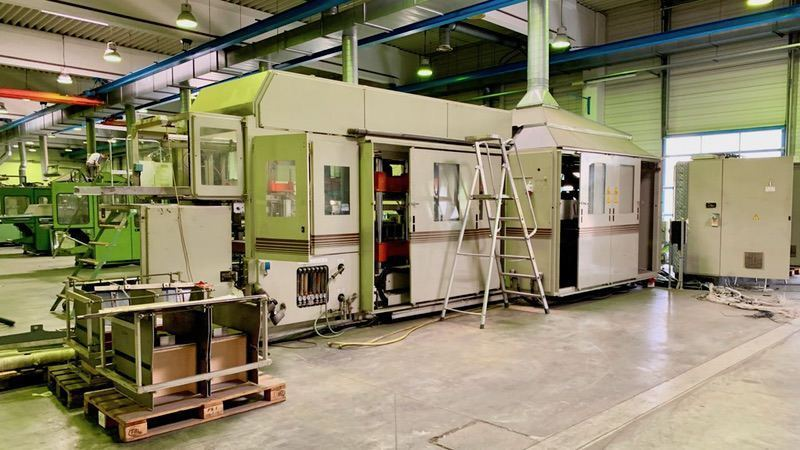
Material used for Thermoforming
Here are some common choices of materials for plastic thermoforming
- Polyethylene (PE): Both high-density and low-density polyethylenes are used in this process. Packaging films and plastic bags are created with Low-Density Polyethylene because it is flexible. Big containers and bottles are formed with High-Density Polyethylene because this material has high chemical resistance and toughness.
- Polypropylene (PP): This material is mainly used to produce food containers, medical packaging, and automotive components because it has a diverse temperature range and excellent chemical resistance properties.
- Polystyrene (PS): Whenever you see medical trays and disposable cups, they might be produced with PS. This material has exceptional clarity and is also lightweight.
- Acrylonitrile Butadiene Styrene: This manufacturing method is suitable for producing luggage and consumer electronic cases, as ABS is a strong material with excellent resistance.
- Polyethylene Terephthalate: This material has the properties of clarity and barrier. Therefore, it is used to produce food packaging containers and beverage bottles.
- Acrylic (PMMA): These materials are commonly employed for the production of display cases, lighting fixtures, and signage because of their weather resistance and optical clarity properties. Acrylic offers excellent optical clarity and weather resistance. It’s used for products like signage, display cases, and lighting fixtures.
- Thermoplastic Elastomers: This material is a hybrid as it combines the properties of rubber and plastic. Therefore, it produces footwear, consumer goods, and automotive parts.
Advantages and Disadvantages of Thermoforming
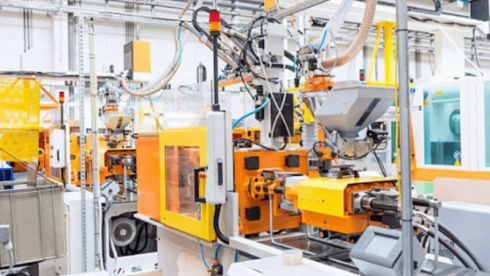
Let’s uncover the benefits and shortcomings of plastic thermoforming in comparison with injection molding.
Advantages
- It is the most suitable process for smaller production quantities. You can produce one part at a time with this method.
- Businesses with low investment can opt for this process because it has low startup and tooling costs.
- The tools of thermoforming have simple designs. If you need any changes in the tools, it will be easy and cost-effective.
- You can use plastic thermoforming for prototyping and quick product development. You can easily make tools for thermoforming rather than injection molding.
Disadvantages
- It is not suitable for large-volume production.
- This process produces high waste because you need to try multiple times before you get the desired shape of thermoformed parts.
Inquire Now for Fast Quotations!
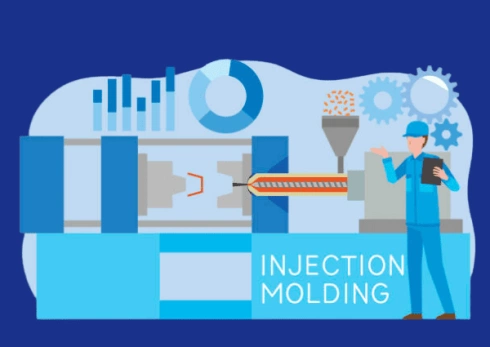
Comparison of Injection Molding and Thermoforming
Let’s begin the comparison between injection molding and thermoforming:
Factor | Injection Molding | Thermoforming |
---|---|---|
Process Description | Melted plastic is injected into a closed mold under high pressure. | A plastic sheet is heated to a pliable forming temperature, then shaped over a mold by using a vacuum, pressure, or mechanical force. |
Materials | Thermoplastics, thermosetting polymers, and metals (in metal injection molding). | Mainly thermoplastics. |
Tooling Cost | High, due to the complexity and precision of molds. | Lower compared to injection molding, as molds can be made from less expensive materials. |
Part Complexity | Can produce highly complex parts with intricate geometries and details. | Generally limited to simpler shapes, though complex features can be added in secondary operations. |
Surface Finish | Excellent; parts have a smooth finish directly from the mold. | Thermoplastics, thermosetting polymers, and metals (in metal injection molding). |
Production Speed | It can generate more waste due to the trimming of excess material; however, the scrap can usually be recycled. | Faster cycle times as the plastic sheets can be heated and formed quickly. |
Production Volume | Suitable for high-volume production runs due to the durability of the molds. | Cost-effective for small to medium runs; however, it can also be used for high-volume production with multiple molds. |
Waste | Typically generates less scrap as excess plastic can often be recycled back into the process. | Good, dependent on the quality of the plastic sheet and the mold. |
Material Distribution | Uniform material distribution is achievable, allowing for precise control over wall thickness. | Material distribution can be less uniform, with thinning occurring in some areas due to stretching of the material. |
Typical Applications | Slower cycle times are needed due to the need to cool the material inside the mold. | Packaging, disposable cups, appliance linings, vehicle doors, and dash panels. |
1. Production Volume Comparison
When you need to deliver high-volume production or a project involves producing small, intricate parts, injection molding is better than thermoforming. However, if your project needs large parts at low production volume, thermoforming is a better choice.
2. Lead Time and Initial Cost Comparison
Manufacturers need to incur higher tooling costs for injection molding than thermoforming. Aluminum is used to form tools for thermoforming, so it’s an inexpensive investment. However, expensive tool steels such as H13 or P20 are used to form tools for injection molding.
Another thing to look into is the lead time. The time required to create tools for injection molding is high because most tools have intricate and complex designs. So, lead time is higher in injection molding than in thermoforming.
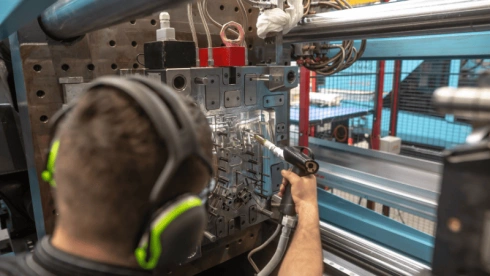
3. Speed Comparison
How fast you get your production output matters the most. In the case of injection molding, it’s easy to fill multiple cavities with molten material, so that you can have a much higher output rapidly with injection molding.
In the case of thermoforming, you can easily modify the tools so that product design and molding will be faster than injection molding.
4. Materials Comparison
You can use the same plastic parts with injection molding and thermoforming. However, you use plastic pellets with injection molding, while plastic sheets are employed in thermoforming. The difference between the two processes is that thermoforming materials are usually more ductile and malleable.
Inquire Now for Fast Quotations!
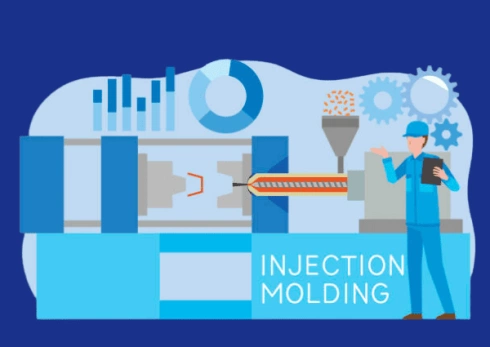
Factors to Consider in Choosing the Right Process
Do you want to choose the right process between injection molding and thermoforming? If yes, then here are some factors to consider first.
1. Part Complexity
You need to select a manufacturing method based on part design. If a design is relatively straightforward with a few undercuts and features, thermoforming is a good choice. Conversely, when you need to produce highly detailed parts with complex geometries and tight tolerances, injection molding is the right choice.
2. Production Volume
What is the production volume you want to achieve? With high-volume production, you can achieve low per-unit costs with plastic injection molding. However, when you plan to run small or medium-scale production, go with thermoforming.
4. Tooling Cost
Thermoforming is an excellent choice to meet the demand for quick prototyping and small production runs. This is because of the initial tooling’s minimal cost. However, when you have to meet the demand of large production quantities, you need to go with injection molding, even though it brings high tooling costs.
5. Lead Time
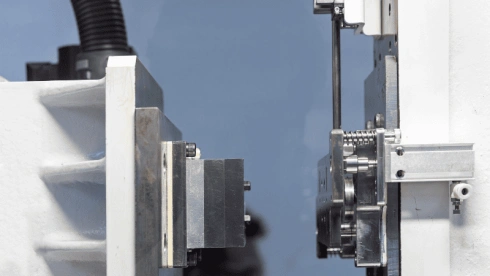
Do you need a short lead time? You can achieve it through thermoforming because the tooling cost is low, and the production setup is simple.
If you are okay with long lead times due to complex tooling and setup, injection molding is the right process.
6. Material Selection
Every application requires specific materials. You can choose a process based on your material as well. For example, when you need to work with thermosetting plastic or elastomers, injection molding is the right choice.
Contrary to this, when you need to work with biodegradable materials, the right process is plastic thermoforming.
7. Part Size and Weight
Thermoforming is a suitable method for oversized and lightweight parts, whereas injection molding is suitable for small to medium-sized part production.
8. Surface Finish and Appearance
Another factor to consider is surface finish and appearance. You can’t achieve intricate texture or high gloss with thermoforming because only plastic injection molding allows you to control the design and get precise texture and finish with an injection molded product.
Inquire Now for Fast Quotations!
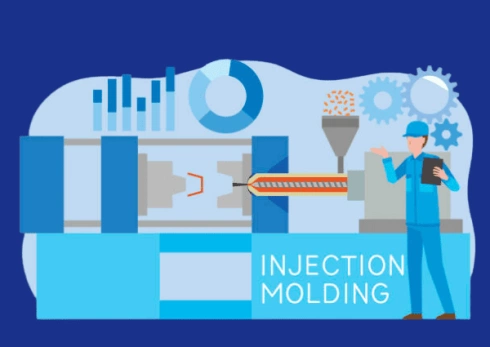
Conclusion
Choosing between injection molding and thermoforming is like picking the right tool for a job. This article comprehends popular manufacturing processes and lets you compare injection molding and thermoforming, so it becomes super simple for you to choose the right process per your project’s unique requirements, budget, and timeline.
So, whether you are crafting large-volume production with a plastic injection molding process or designing large prototypes with plastic thermoforming, this guide unlocks the right knowledge to bring your brilliant product idea to life.
Let’s Transform Your Product Idea into Life with Hongju
When choosing between plastic injection molding and thermoforming, you must analyze multiple factors, such as your budget, production volumes, lead time, and design.
At Hongju, we help every business to make the right choice based on their project requirements. Once you decide, please don’t hesitate to collaborate with our experts, who can guide you.