Have you ever experienced leaks or pressure loss in critical systems? They can be a nightmare, often leading to total breakdown. The most common cause of such problems is worn-out or unsuitable gaskets. Let’s find out how these seemingly small but vital components can make or break the efficiency of your operations. We will explain: what is a gasket, what gasket types are, and how they work.
What are Gaskets?
A gasket is a fixed seal or a filling between two closely adjacent sealing surfaces that prevents fluid or gas leaks. It ensures that the internal pressure in the system remains at an optimum level. Its shape and structure are designed to eliminate irregularities in mating surfaces and ensure proper sealing. Gaskets are also used for sound/vibration dampening or cushioning in machine parts.
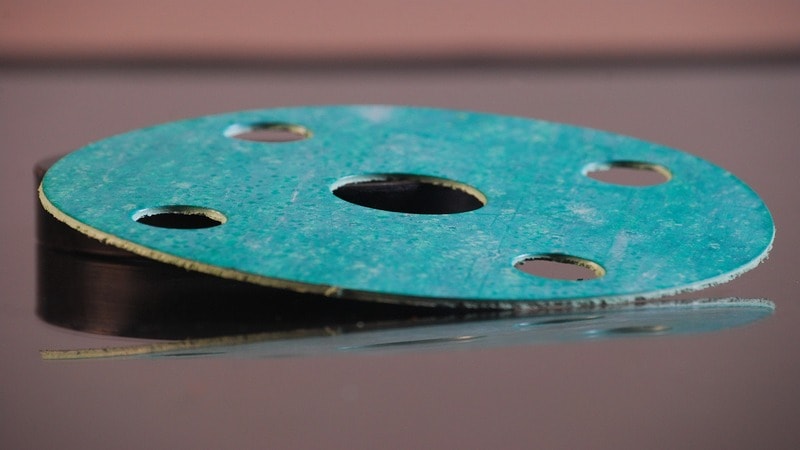
Gaskets are usually manufactured from deformable materials like cork or paper, rubber, metal, copper, or foam. The choice depends upon the application and its working conditions. For example, gaskets in automotive car engines are manufactured by using elastomeric material, such as rubber i.e., Nitrile, Silicone, or Viton.
Other considerations when choosing a gasket include cost and safety factors. Usually, ASTM and ISO standards govern the quality, performance, and safety requirements.
Common Applications:
Gaskets have extensive applications in various mechanical systems and machinery. It’s a formidable component critical for smooth operations.
Automotive Engines: These are equipped with gaskets in the main engine heads, oil pans, valve systems, fuel injectors, intake pipes, etc. Their function is to stop oil, coolant, or gas leaks from the engine block.
Plumbing Systems: In plumbing systems, there are several types of gaskets that are used for sealing pipe joints, faucets, and pumps. These ensure that water-tight connections are maintained without any fluid leakages.
Industrial Machinery: Gaskets in industrial machinery prevent leakage, maintain the system’s internal pressure, and protect sensitive components from exposure to the environment. They’re incorporated in industrial boilers, chemical processing equipment, and hydraulic systems.
What Does a Gasket Look Like?
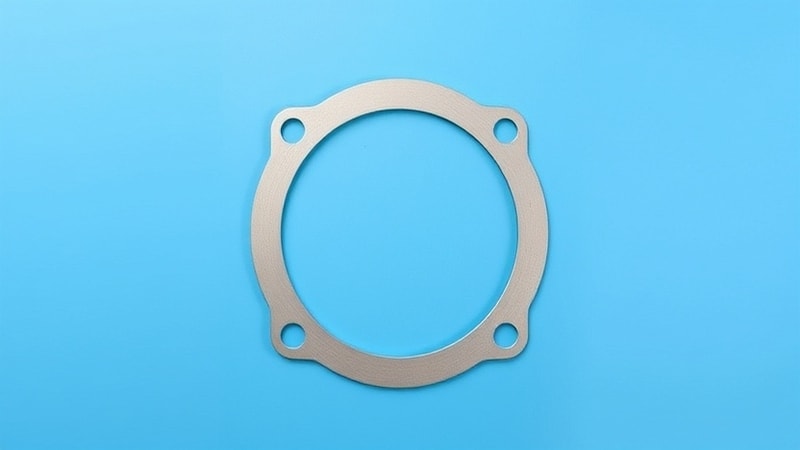
Gaskets do not have a standard appearance; their shape and size depend on the intended application. Common gasket types are circular or rectangular in design like spiral wound gaskets. For example, o-rings used in sealing valves are round, while gaskets used in engine heads are rectangular with carved-out openings.
Gasket materials like rubber, cork, and metal can also affect their appearance. Rubber gaskets are flexible and easy to mold. They’re usually shaped as flat rings, O-rings, or custom profiles. Similarly, cork gaskets have textured surfaces. They’re cut out to fit in different profiles as required. Metal gaskets are rigid and have application-specific designs.
The gasket size depends on the dimensions of the surface to be sealed. The gaskets used in automobile engines are larger than common faucet gaskets. The thickness is also determined by the gap between mating surfaces. Gaskets are also made thick for high-pressure, high-temperature applications.
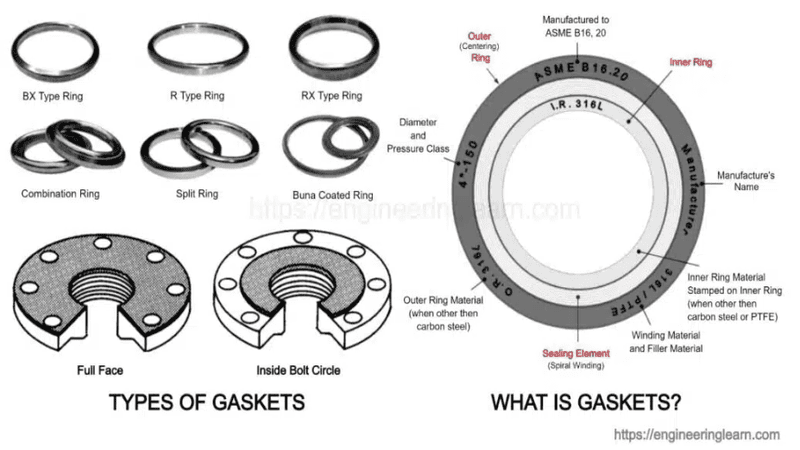
The illustration shows o-ring gaskets commonly used in engines, fuel lines, pumps, and valves. Like all gasket types, they come in various size variations. The ASME standards, material details, and size are embossed on the ring.
How Do Gaskets Work?
Gaskets have a very simple operation. You fit it between two surfaces and tighten them against each other. It gets compressed and creates a sealing effect. The seal acts as a pressure-tight barrier, preventing fluid and gas leakages. It also protects the sensitive components from frictional damage and environmental contaminants.
Adequate compression is critical to ensure the proper functioning of the gasket. Otherwise, the seal becomes loose and leads to the seeping of fluids. Check the appropriate fitment and tightening of the mating parts.
The size and dimensions should match the surfaces and must be aligned properly to achieve the perfect fit. Plus, the right material choice according to operating conditions (temperature range, pressure levels, chemical compatibility, etc) is indispensable.
Seal failure is common due to the overtightening of adjoining surfaces, which increases compression. It deforms the gasket, developing cracks and loosening with loss of elasticity. Aging is another prominent factor of gasket failure due to rough operating conditions, which cause it to wear quickly and perform poorly.
The use of incompatible material with the system’s temperature, pressure, or chemical environment can also cause swelling, corrosion, and failure.
Gasket Materials and Selection
Gaskets are made from various materials depending on the specific application. Operating conditions and environmental exposure are two crucial considerations in gasket material selection. Common materials include paper, rubber, silicone, metal, cork, and felt, with advanced options such as PTFE, flexible graphite, and composite materials. Silicone gaskets are becoming increasingly common.
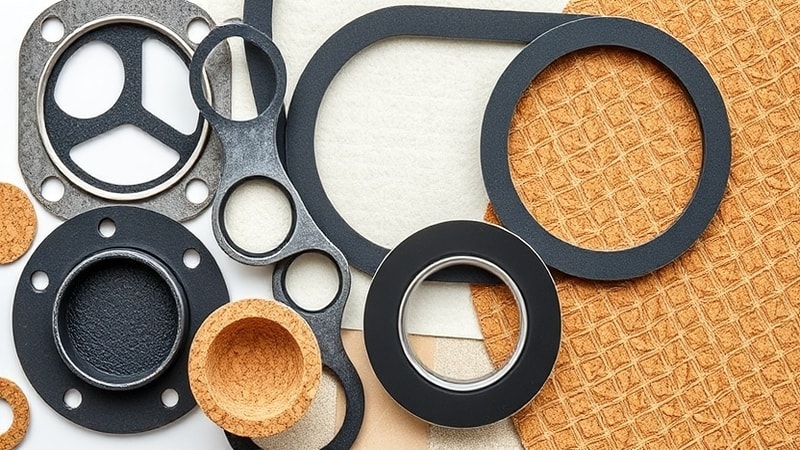
Selecting compatible gasket material for specific operating parameters, such as temperature range, system pressure, and exposure to chemicals, ensures proper functioning. Gaskets are used in key industries like food processing, petrochemicals, pharmaceuticals, water, and gas.
Every industry has specific material requirements, like the food processing industry, where hygienic and non-reactive materials are preferred. Here are some key considerations during the selection of gasket materials:
1. Temperature Range
The material must withstand the system’s operating temperatures without degrading. Any mismatch will affect the seal’s performance. Graphite and metal are suitable for high-temperature applications.
2. Max: Pressure Level
The material should withstand the maximum pressure level without excessive compression and loss of other properties. Metal and PTFE materials offer greater tolerance to extreme pressures.
3. Chemical Exposure
Gaskets may be exposed to corrosive chemicals, acids, and solvents. For efficient operations, the material selection must ensure excellent chemical resistance to such chemicals.
4. UV and Ozone Exposure
Sometimes, gaskets are used for outdoor applications, especially in the oil and gas sector. Weathering and UV degradation can affect gasket performance. Silicone and EPDM are commonly used for such applications.
5. Industry Standards
The industry you’re operating in will determine the gasket’s material specification. For instance, food processing industries require food-grade gasket material to ensure hygiene. Ensure compliance with recognized ISO and ASME standards.
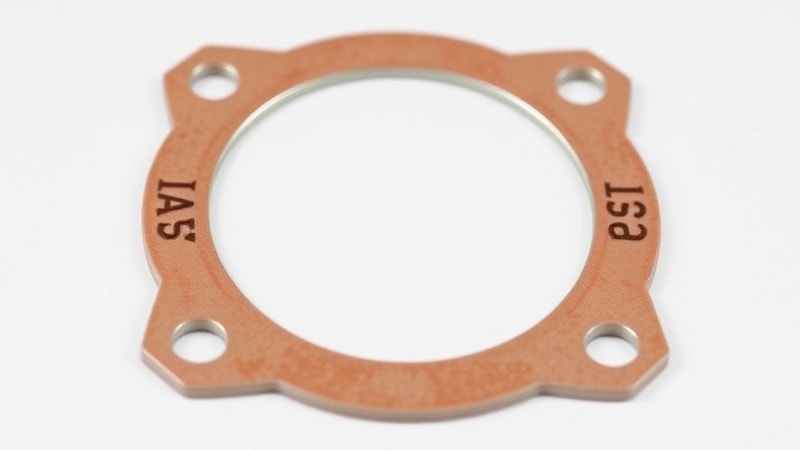
Types of Gaskets
Multiple gasket types are developed for a variety of applications in different sectors. Each of its types has different characteristics and applications. Let’s explore common gasket types:
Gasket Type | Characteristics | Application |
---|---|---|
Flat Gaskets | These are thin, flat, and are made up of materials such as rubber, cork, or PTFE. They provide wide surface sealing and maintain optimal pressure levels. | These gaskets are installed in low-pressure systems such as plumbing fixtures, HVAC systems, and general piping connections. |
O-Ring Gaskets | These are the most common gasket types with circular or oval shapes. Usually made from metal, rubber, or PTFE. They provide sealing in pipes and grooves. | Commonly used in moderate pressure applications in pressure vessels and oil and gas machinery. |
Spiral Wound Gaskets | These gaskets are multi-layered with a layer of metal (stainless steel or similar) and a soft filler (graphite, PTFE, or mica). They provide resistance to extreme pressure, temperature, and chemicals while maintaining seal quality. | Extensively used in high-pressure and high-temperature applications in oil rigs, power plants, and chemical plants. |
Double-jacketed Gaskets | Unique in design, these gaskets have a metallic outer layer (steel, copper, or aluminum) with a soft filler core (graphite or ceramic). They are ideal for uneven surfaces in high-pressure and temperature applications. | Used in critical machine parts such as heat exchangers, boiler systems, and industrial equipment. |
Gasket Design and Construction
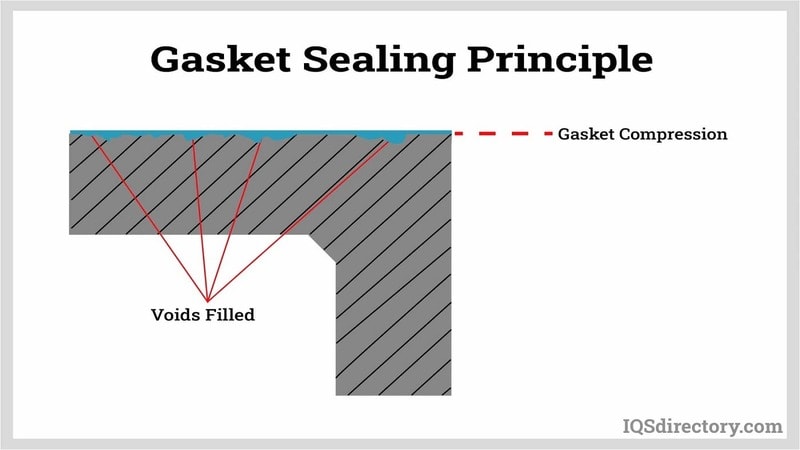
How do gaskets work? Their primary function is to fill gaps between two surfaces and create a sealing effect. There are three critical design considerations for gaskets: the properties of the mating surfaces, application requirements, and size/profile.
The pressure and temperature fluctuations it will withstand, the mechanical stresses it will undergo, and chemical exposure, all affect material choice. The geometry depends on the size and dimensions of mating surfaces.
From a construction point of view, strength, flexibility, and durability are emphasized in gaskets. Simple gaskets like o-rings are made from rubber, cork, or compressed fiber. They are covered with additional layers of non-stick, chemical-resistant coatings. The gasket types, like spiral wounds, are reinforced with metallic cores and filler material for usage in rough operating conditions.
Each of these design and construction aspects will determine what a gasket looks like. Proper design and construction are critical to ensure a tight seal and prevent leaks. Multiple standards govern gasket design and construction.
For instance, ASME B16.21 outlines the design, material, and dimensions of flat gaskets. Similarly, ASTM F104 specifies requirements for elastomeric gaskets used in chemical-resistant environments.
Gasket Testing and Inspection
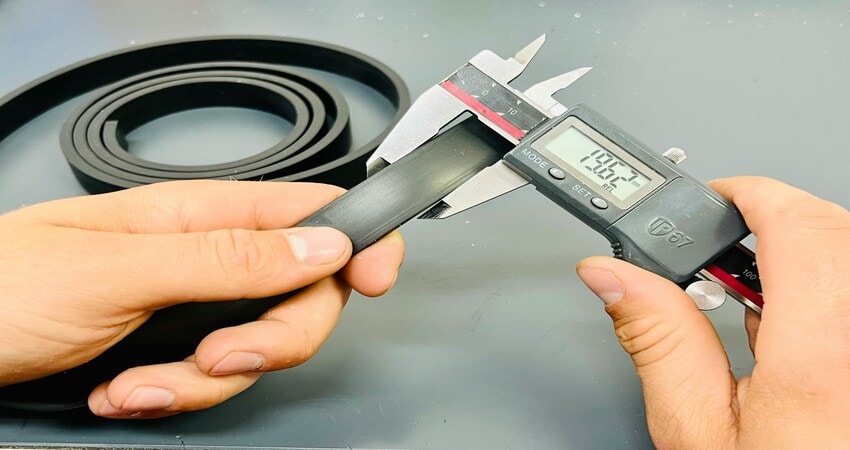
Gaskets are tested and inspected to check their physical properties and compatibility with different applications. The test procedures are set by standardization organizations like ASTM and DIN. Here are a few common tests:
- Hot Compression Test (ASTM D5950)
The hot compression test evaluates the gasket’s performance under extremely high temperatures. It tests the level of permanent deformity in a compressed gasket exposed to high temperatures and determines the amount of heat the material can withstand without failure.
- Fluid Resistance Test (ASTM F14)
This test checks the chemical resistance of gasket materials. The material is immersed in different fluids, such as oils, fuels, and chemicals. It measures the degradation caused by exposure to different chemicals. The test helps ensure that gaskets will maintain their sealing properties when exposed to potentially harmful chemicals.
- Non-metallic Gasket Tension Test (ASTM F152)
The test is done to check the tensile strength and elongation properties. It checks what a gasket looks like when experiencing mechanical stresses. The Universal Tester is employed to apply different levels of tensile forces. It determines how well the gasket materials can withstand tension without losing seal quality.
In addition, inspection is a process that includes checking for defects, including cracks, tears, or inconsistencies in material thickness. It helps determine the gasket’s viability for smooth operations.
Industries and Applications
Gaskets are being utilized in most industries ranging from aerospace to automobile industries as well as construction companies. In aerospace, gaskets find a place in parts of the engine, fuel system, and hydraulic lines. These pressure-tight and leak-proof mechanical seals resist extreme working conditions.
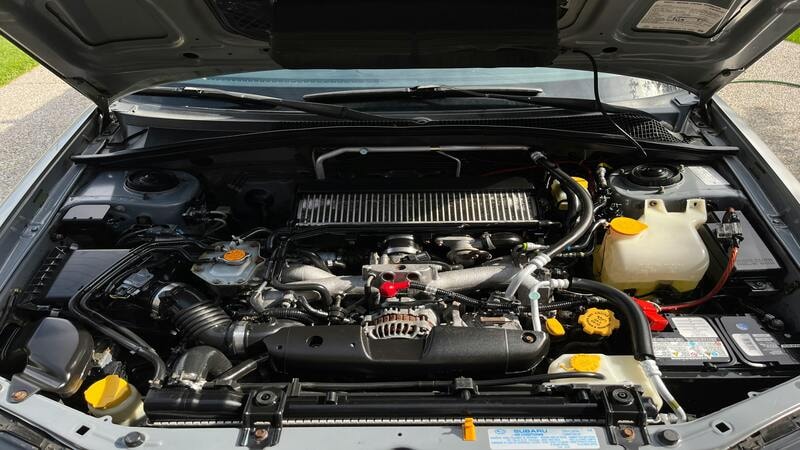
You will find at least 20 to 40 gaskets in your car used in engine assemblies, exhaust systems, and transmission units to prevent fluid leaks. The plumbing systems and HVAC units in buildings also have many gaskets to prevent water leaks and air loss.
Gaskets are also used in various machinery and equipment. Hydraulic and pneumatic systems in conveyor belts, excavators, elevators, etc., have a variety of gaskets that ensure efficient operations.
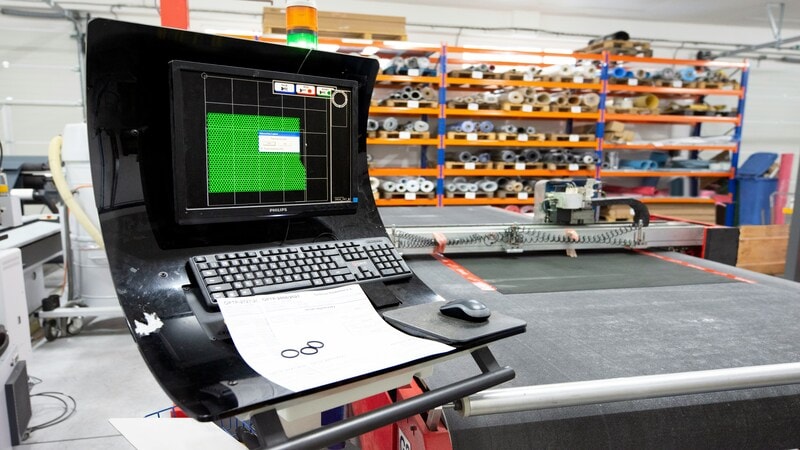
Gaskets are not only used as seals; they have multiple other applications. In automobiles and machinery, they act as dampening agents, reducing vibration and sound transfer. They are also used in food processing to prevent contaminants from entering the system, helping ensure hygiene and sterility.
Choosing the Right Gasket
Understanding what is a gasket is one thing, but the critical part is to choose the right type. An inappropriate selection can be disastrous, resulting in leakage problems, costly shutdowns, and downtime. By keeping the following considerations in mind, you can prevent such problems from arising in the first place:
Operating Conditions
What is your intended application? You must know the operating conditions, such as temperature range, pressure levels, and chemical and environmental exposure. The material type will be selected accordingly.
Gasket Materials
Once you know the operating conditions, it becomes easy to select a compatible material. For instance, if the gasket experiences high temperature and pressure, go for materials with high thermal stress resistance and high-pressure tolerance.
Size and Dimensions
Next, measure the size and dimensions of the mating surfaces accurately. Any difference in size will make the gaskets ineffective, leading to leaks and total failure. A slight variation in size also impacts the performance, as the compression becomes uneven.
Gasket Type
Now, you’re in a good position to select the right gasket type. Review your intended application and choose the right material. With this information and proper size measurements, you can explore different gasket types. Each type has unique characteristics; you can go for o-rings or spiral wound gaskets as per your requirements.
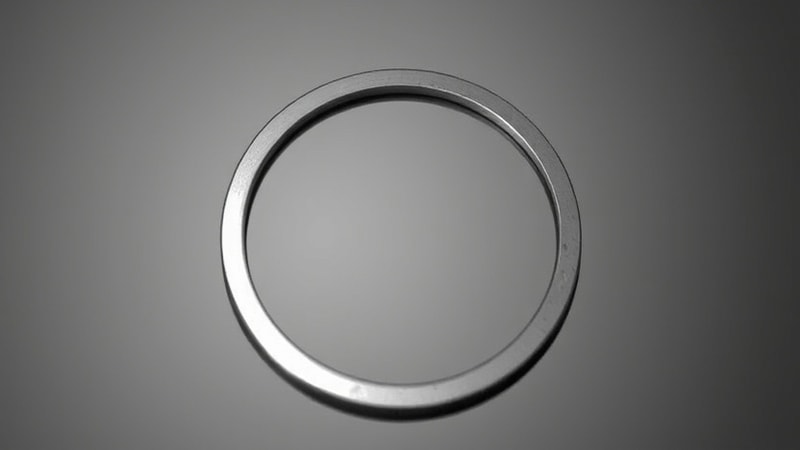
Proper Installation
After selecting a gasket, the proper installation is imperative for smooth operations. Any misfit can lead to over-compression or under-compression. It will not function properly and lose its performance.
Gasket Installation and Maintenance
Proper installation and maintenance are necessary to ensure efficient operations. Clean and smoothen the surface before fitting the seal. Dust or debris can affect the sealing and cause leaks. Dry with a cloth and inspect for cuts or nicks on the surface. Avoid installation if the surface is not smooth.
When installing a gasket, you need to be careful about fitment, alignment, and seating. The size and dimension of the seal should match the mating surface for proper fitment. You should align the gasket properly and avoid tilting for a perfect sealing effect. The seating of the gasket between two surfaces must be well-spread to ensure even compression.
Gasket maintenance increases its durability and longevity over time. Follow a proper maintenance schedule with regular inspections. Examine for any signs of wear and tear, damage, or decay such as fissures, hardening, or erosion. The gasket, primarily, suffers from exposure to environmental and extreme mechanical stresses. Signs of damage necessitate a gasket replacement.
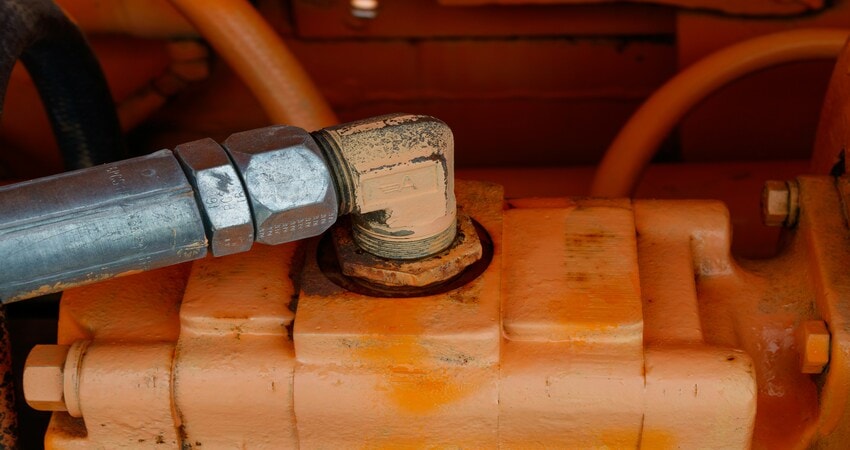
Troubleshooting Common Gasket Issue
Gaskets are simple in design and construction. You may encounter some common issues when working with gaskets that are very easy to troubleshoot. The problems occurring in gaskets are leakage, damage, and total failure. Whenever a gasket stops functioning, here’s how you can troubleshoot:
Step 1: Thoroughly inspect the gasket and machine parts to identify the main problem. Damages to the gasket, leakage, or failure to maintain the seal can all be a cause.
Step 2: After identifying the problem, the next step is to check the cause. These issues are mostly because of improper installation. The gasket could be tilted, over-compressed, or not fitted well.
Step 3: Check the operating conditions and gasket specifications. The damages may be due to high temperature and pressure levels. The material incompatibility is also a root cause.
Step 4: If the gasket is damaged, you must replace it. When installing the new gasket, be mindful of operating conditions, material specifications, and type.
Step 5: Ensure proper care and maintenance of the gasket. Follow a strict inspection schedule, check for wear and tear, and clean the gasket periodically.
Where to Buy Gaskets
Ready to go on a market hunt for gaskets? Be sure about the intended application, operating conditions, gasket type, and specifications. Explore multiple brands and check client reviews. Consider three factors when choosing a gasket supplier: brand value in terms of positive reviews, material quality, and warranty.
You can go for Hongju, a trusted name in the industry with two decades of manufacturing expertise. It will save you time and money. They offer the best quality head gaskets at market-competitive rates. You can order bulk quantities with customization. The products come with extensive warranties and quality assurance from international bodies. Get a quote now!
Frequently Asked Questions (FAQs)
- What is the purpose of a gasket?
A gasket prevents fluid and gas leakages by filling gaps between two machine parts. Common uses of gaskets include preventing leaks, containing pressure, and protecting machinery and systems from frictional damage.
- How can I identify a damaged gasket?
You can thoroughly inspect the gasket to identify damage. Any signs of cracks, leaks, or material thinning indicate that the gasket is damaged.
- What are gaskets made of?
The selection of gasket material depends on its applications in various industries. Commonly used materials for gaskets are natural rubber, metal, cork, flexible graphite, etc.
- Can I reuse a gasket?
Once a gasket is damaged, it can’t be reused anymore. A damaged or old gasket would lose its seal quality, which would lead to functional problems, often creating total failure.
Conclusion
Now, after you have gained all knowledge regarding gaskets, their types, and how gaskets can work, you can choose the most suitable type of gasket you need. A good choice of gasket will help you avoid the costly breakdowns and downtime caused by the failure of the gasket. You will be able to ensure efficient and safe operations enhancing the system’s reliability.
You must follow the proper maintenance and inspection schedule for solid material gaskets to avoid early damage to the gasket. Learn more about compression in gaskets to increase their durability and longevity.
Hongju: A Quality Manufacturer of Gaskets
Hongju is the largest manufacturer of gaskets in the world, supplying gaskets to clients in many industries such as automobile, food processing, chemicals, and construction. Hongju has invested in the most advanced R&D and manufacturing technologies and prides itself on providing customer-specific solutions so that clients get exactly what they are looking for.
Get in touch with our customer representative for one-on-one guidance about Hongju’s expertise in gaskets. You can also connect with our engineering team for a detailed discussion. Contact us now for a seamless ordering process.