Choosing the correct gasket material is essential for the mechanical system to work well and be safe. You have to think about what the system needs, its environment, and what the gasket is for. Selecting the right characteristics prevents gasket failure. That’s why picking the correct gasket material is a big deal.
In this article, you’ll learn more about the different types of gasket materials to see which one will perfectly fit your specific application.
Factors for Choosing the Right Gasket Material
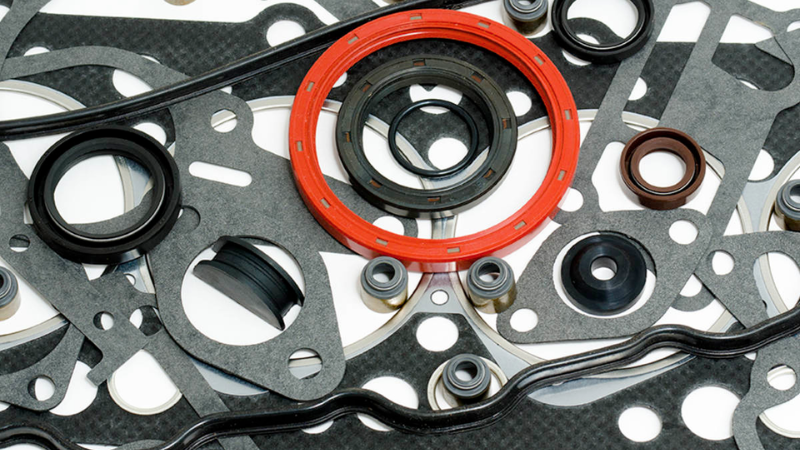
Right gasket material selection is crucial for ensuring optimal performance and longevity in various applications. Several factors need to be considered when selecting materials, including compatibility with operating conditions and fluids, temperature and pressure requirements, flange type and surface finish, and environmental factors.
Compatibility with Operating Conditions and Fluids
When choosing a gasket, it’s important to think about what it will be exposed to. Different fluids can have different effects on different materials. Acidic fluids need gaskets that can resist acid, like Viton or PTFE. If you’re dealing with oil, it’s better to use nitrile rubber or neoprene gaskets.
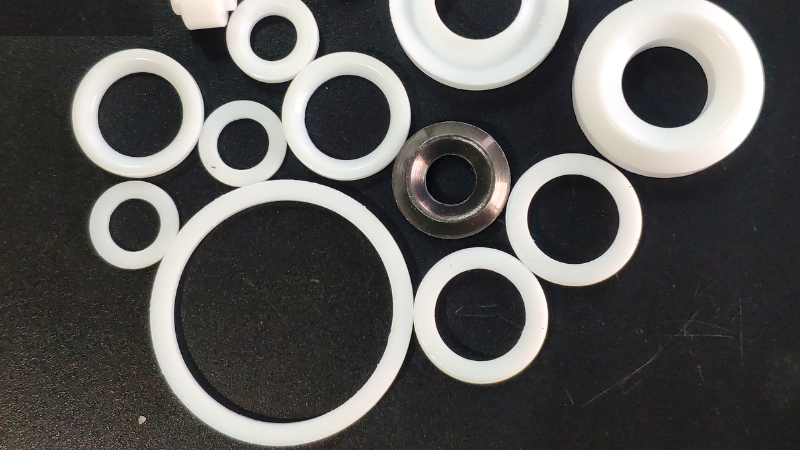
Temperature and Pressure Requirements for Gaskets
Temperature and pressure are important for choosing the correct gasket material. Extreme temperatures can make some materials degrade or lose their ability to seal. High-pressure places need gaskets that can handle compression fluid temperature without losing their sealing power.
Graphite or metal-reinforced elastomers are good for hot conditions because they resist heat well. It’s also important to think about how compressible the gasket is when operating temperature or pressure changes.
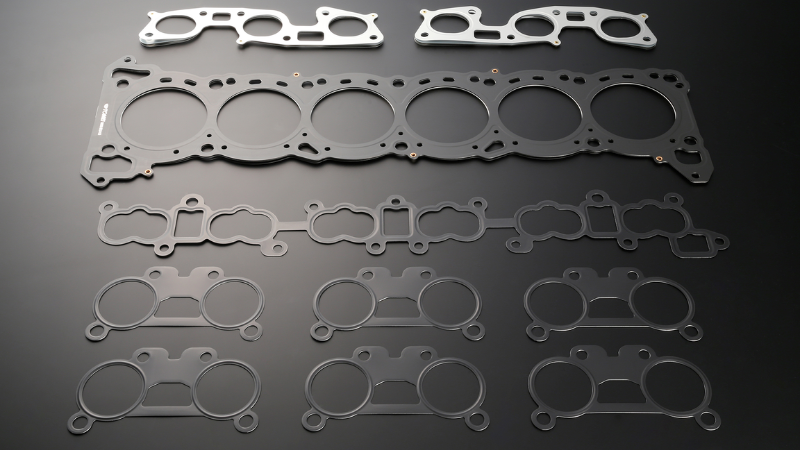
Consideration of Flange Type and Surface Finish
The type and thickness of the flange affect which gasket to use. Flat-faced flanges need softer materials like non-asbestos fiber or rubber. Raised face flanges need thicker gaskets made from compressed fiber sheets or spiral wound designs for higher pressures.
Surface finish matters too. Rough flanges need more compressible gaskets, while smooth flanges can use less compressible materials.
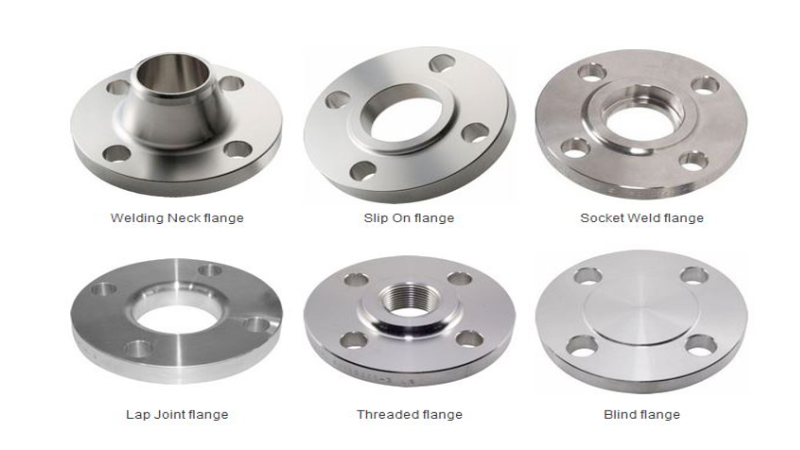
Environmental Factors Impacting Gasket Performance
Environmental factors such as exposure to UV radiation ambient temperature, moisture, or chemicals can significantly impact gasket performance. Outdoor applications might require gaskets made from weather-resistant materials like EPDM (ethylene propylene diene monomer) rubber or silicone.
Chemical resistance is crucial when dealing with aggressive substances, making materials like PTFE or chemically resistant elastomers suitable choices.
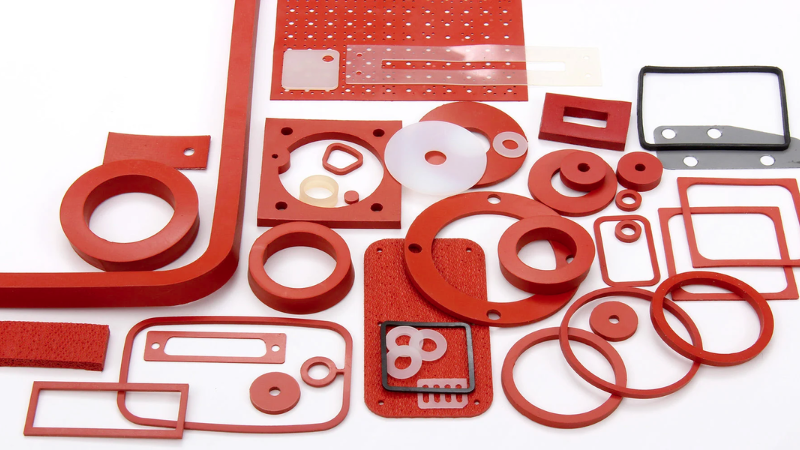
Key Types of Gasket Materials and Their Uses
Gasket materials play a crucial role in ensuring effective sealing in various applications. Different material properties make them suitable for specific applications. Let’s explore some common types of gasket materials and their respective uses.
Rubber Gaskets for General-Purpose Applications
Rubber gaskets, including natural rubber and synthetic rubber variants, are widely used in general-purpose applications due to their flexibility and durability.
They provide excellent resistance against water, air, and most chemicals, making them ideal for sealing joints with moderate pressure requirements. Rubber gaskets can be found in industries such as automotive, plumbing, and manufacturing.
Some Examples of Rubber Gaskets
Rubber gaskets are versatile and used in a broad range of industries due to their sealing properties. Here are some common examples:
Neoprene
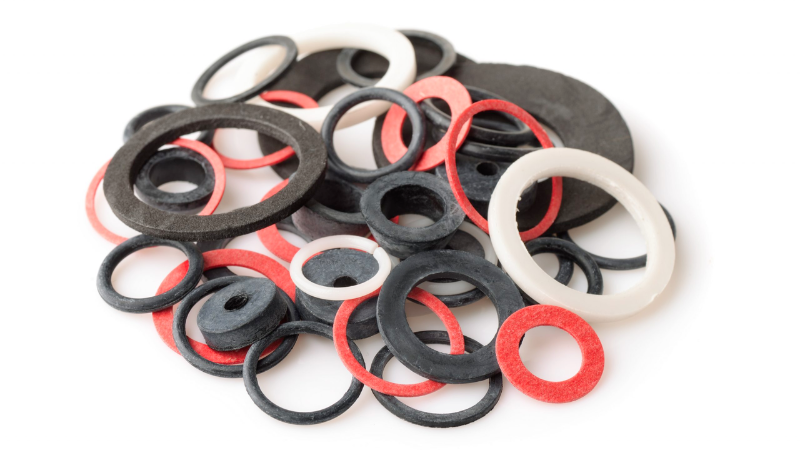
Neoprene rubber gaskets have outstanding weather resistance, making them ideal for outdoor applications. They can withstand extreme conditions and they can be used with PSA (pressure sensitive adhesive) to form a secure seal, protecting against heat, moisture and chemicals.
These incredible gaskets protect your equipment from the elements and ensure smooth operation under any circumstances. Commonly used to seal windows and doors in homes and protect electrical connectors from moisture, these gaskets are made from specially formulated rubber called neoprene.
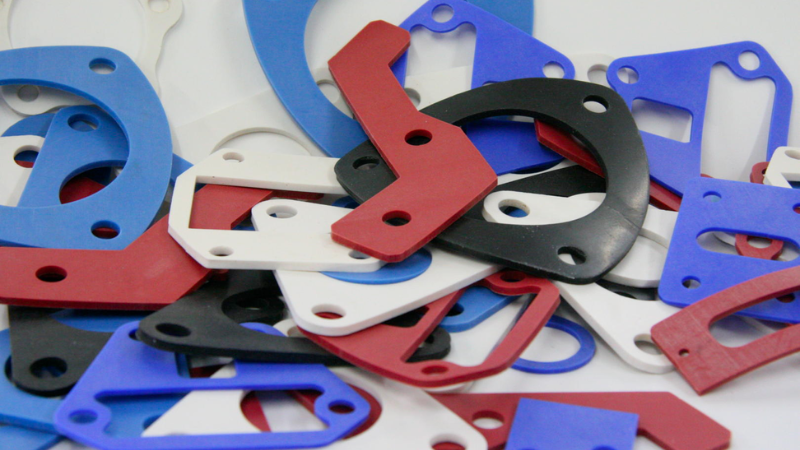
Known for their exceptional strength and durability, neoprene rubber gaskets are like a soft, protective forcefield for your equipment. Their exceptional flexibility makes them suitable for a range of applications, and they are perfect for fitting into tight spaces or irregular shapes.
Nitrile
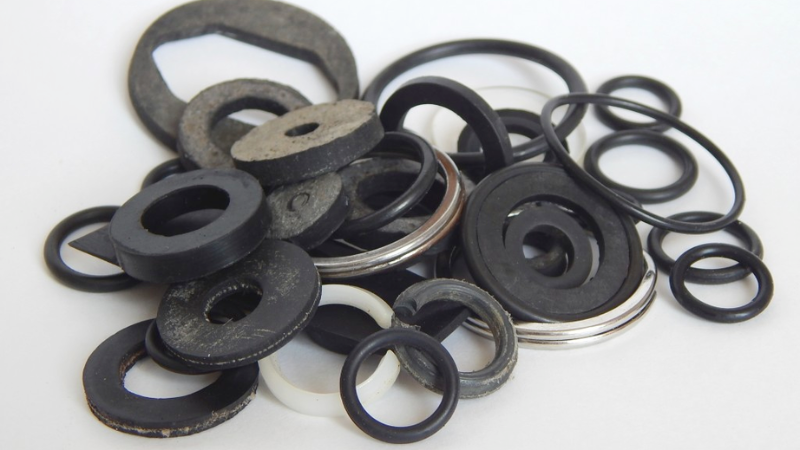
Nitrile rubber gaskets have a unique ability to resist oil, making them an ideal choice in industrial applications where the possibility of coming into contact with oils or fuels is high. These gaskets serve as protectors for machines and equipment, ensuring that no oil or fuel leaks occur and cause damage or complications.
In industries involving the use of oils and fuels, the possibility of a leak occurring is high, which can lead to disastrous consequences for the equipment and facilities involved. To prevent this from happening, nitrile rubber gaskets are specially designed to form a secure seal and prevent any leakage.
Silicone
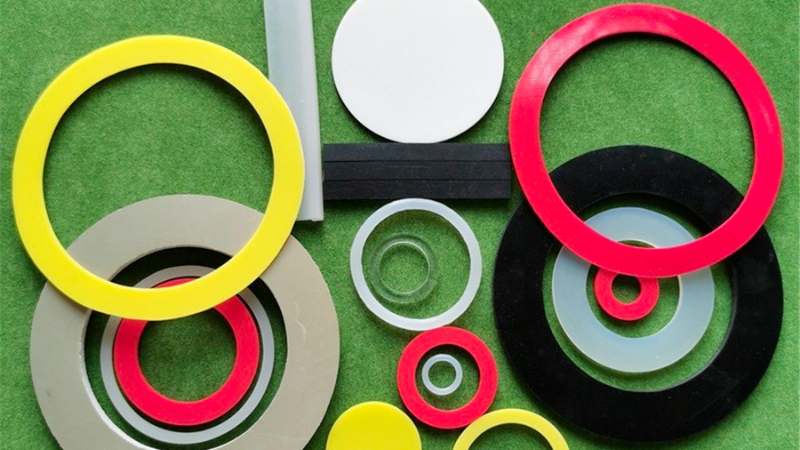
Silicone rubber gaskets have an exceptional ability to withstand extreme temperatures without melting, making them suitable for use in temperature range, high-heat applications.
Due to this property, they are commonly used in appliances and engines where they are seals that can effectively prevent leaks caused by high temperatures. Additionally, their tight seal can protect machinery and equipment from damage caused by heat.
Cork Gaskets for Low-Pressure Sealing Need
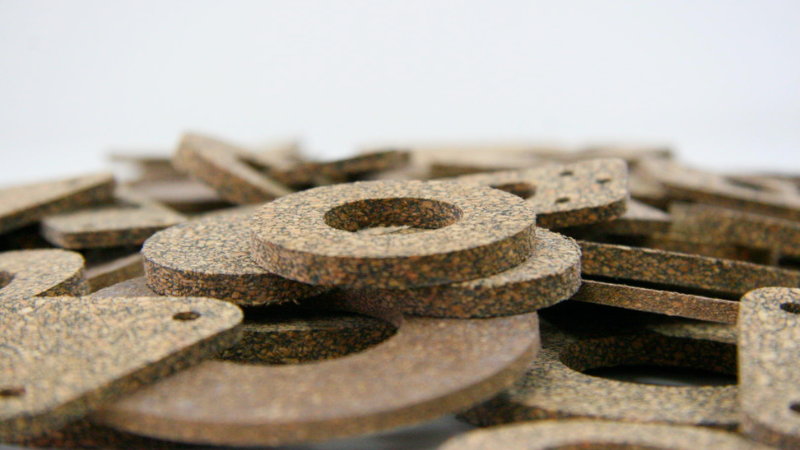
Cork gaskets are an economical choice when low-pressure sealing is required. Derived from the bark of cork oak trees, these gaskets possess good compressibility and resilience in low temperature applications. They find application in areas where a tight seal is needed but not under high pressure conditions.
Common uses of cork gaskets include sealing flanges on pipes carrying non-corrosive fluids or as insulation material between electrical components.
Metal and PTFE Gaskets for High-Temperature or Corrosive Environments
In extreme conditions involving high temperatures or corrosive environments, metal and PTFE gaskets offer reliable sealing solutions.
Metal gaskets:
- Composed of materials like stainless steel or copper, metal gaskets are highly resilient and can withstand substantial pressure.
- Their ability to resist extreme temperatures and corrosive substances makes them suitable for applications in the oil and gas industry, chemical processing plants, and power generation facilities.
PTFE (Polytetrafluoroethylene) gaskets:
- Known for their excellent chemical resistance, PTFE gaskets are widely used in industries dealing with aggressive chemicals.
- They exhibit low friction properties, making them suitable for applications involving moving parts.
- PTFE gaskets find use in pharmaceutical manufacturing, food processing, and semiconductor industries.
By carefully selecting the appropriate gasket material for a specific application, one can ensure efficient sealing that meets the demands of various industrial requirements. Whether it’s rubber gaskets for general-purpose needs, cork gaskets for low-pressure sealing, or metal/PTFE gaskets for high temperature applications or corrosive environments – each type serves its purpose effectively.
Understanding the Benefits of Custom Gasket
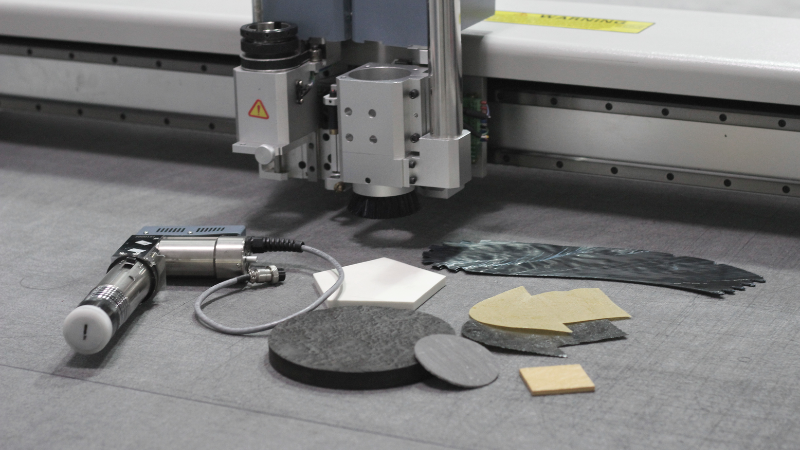
Custom gaskets are made to fit special needs. They are different from regular gaskets because they are designed just for one project or industry. This makes them work better and seal things tighter.
Custom gaskets are really great because they seal things up really well. They are made to fit perfectly in a specific situation, so they stop leaks, handle different pressures, and can even handle extreme temperatures or chemicals. They are made to be really precise and reliable.
Customized gaskets are a better choice because they save money in the long run. Off-the-shelf gaskets may seem cheaper at first, but they need to be replaced or fixed more often. A custom gasket is made to use materials efficiently, so there is less waste. This saves money on materials and reduces the time spent on maintenance or replacements.
They can help save money and make things run better. Customized gaskets are made to fit perfectly, so there are fewer leaks and equipment problems. This means less time wasted and more work getting done.
By selecting the right custom gasket material, you can ensure optimal performance and longevity for your application.
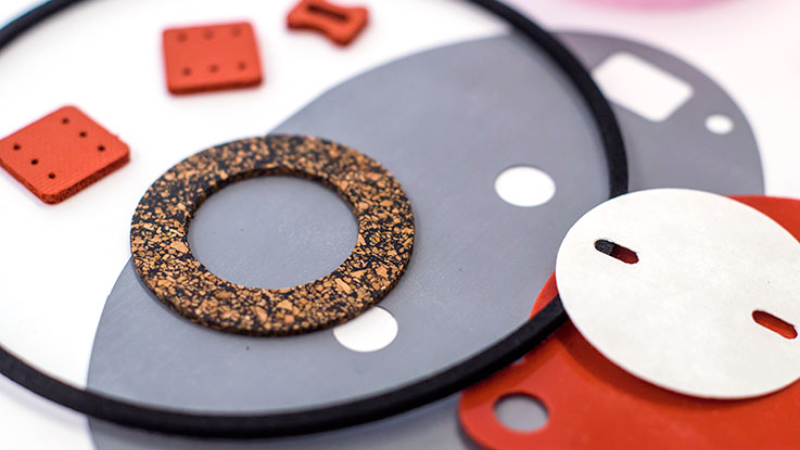
Conclusion
To sum up, this guide assists engineering beginners in making safe, effective sealing choices. Through comprehensive examples and explanations, readers can understand different gasket materials’ properties, enabling them to select the best material for their projects.
Buy High-Quality Gaskets Materials from Hongju
Choosing the right gasket material can be overwhelming. However, with patience and a clear understanding of your application, you can select the ideal material to suit your specific requirements.
Hongju Silicone is here to help with our expertise in creating gaskets. Our knowledge and experience in gasket design and materials selection can guide you in finding the ideal material for your project needs.