What Is Silicone Rubber (VMQ)?
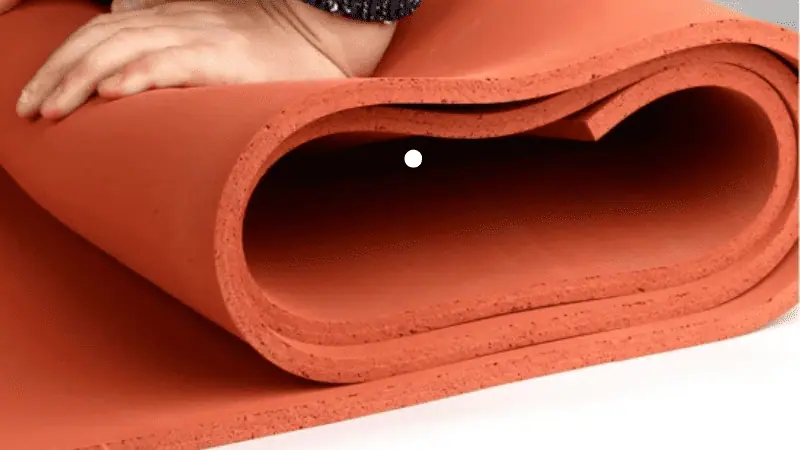
Silicone rubber is a synthetic rubber made from processed quartz and methyl chloride. Chemically it is made up of silicone metal, carbon, hydrogen, and oxygen, all tied up in polymer form. The proper scientific name for silicone rubber is polydimethylsiloxane.
Silicone rubber is an all-purpose polymer that is used for a wide variety of applications. It has excellent temperature resistance and can withstand most environmental damage.
How Is Silicone Rubber Made?
Silicone metal, the basis for silicone rubbers, commonly exists as quartz ( SiO₄) crystals which are widely present in beach sand. This natural mineral is processed with several chemicals to produce a pure elastic silicone rubber.
Following are the basic steps involved in the production of silicone rubber.
- Quartz crystals are heated to an extreme temperature in the presence of a carbon catalyst. The oxygen atoms in quartz bond to the carbon atoms, leaving behind pure silicone metal.
- Silicone metal is now heated alongside methyl chloride to form the base of a silicone rubber called dimethyldichlorosilane.
- The silicone base is then distilled into polydimethylsiloxane, the base component in silicone oils.
- Polydimethylsiloxane can be polymerized using various proprietary techniques to make silicone rubber.
What Is Fluorosilicone Rubber (FVMQ)?
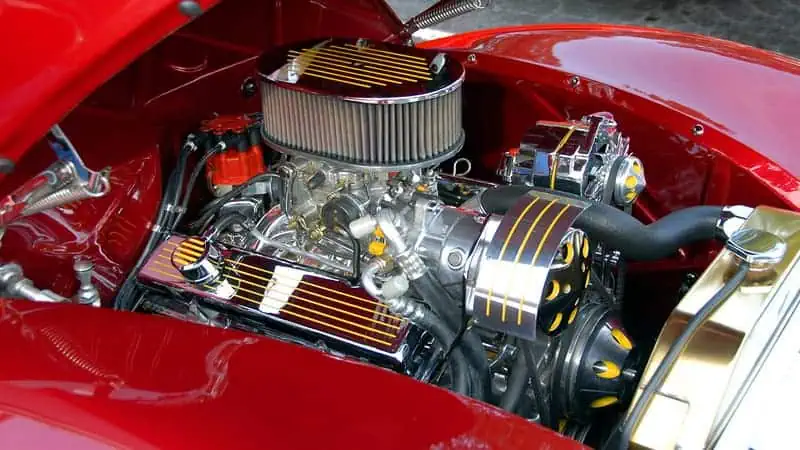
Fluorosilicone rubber is a derivative of silicone rubber. Here fluorine atoms are introduced into the silicone base to increase its chemical compatibility properties. The added fluorine groups decrease the base mechanical properties of fluorosilicone but give it extra resistance to chemicals. The scientific name for fluorosilicone is Fluorovinyl Methyl Siloxane or FVMQ.
Silicone rubber can endure mechanical and elemental damage, but it will degrade quickly when exposed to chemical compounds like acids, gasoline, solvents, etc. Silicone is used for everyday applications, while fluorosilicone is specially designed for industrial use.
How is Fluorosilicone Rubber Made?
Fluorosilicone rubber is made using special patterned techniques that are not widely available. But the basic steps involved in the process are as follows.
- Fluorine is added to a Vinyl (Carbon-Hydrogen) base.
- This Fluorovinly compound is then introduced to the silicone base, dimethyldichlorosilane, to produce FVMQ.
- The FVMQ is then polymerized using standard industrial techniques into a rubber.
Properties of Fluorosilicone vs. Silicone Rubber
As a silicone derivative, fluorosilicone shares many of the same material properties; both materials have excellent high-temperature stability and are resistant to environmental damage. But at a closer look, you can see that the properties of the two rubber have minor differences.
Mechanical Properties
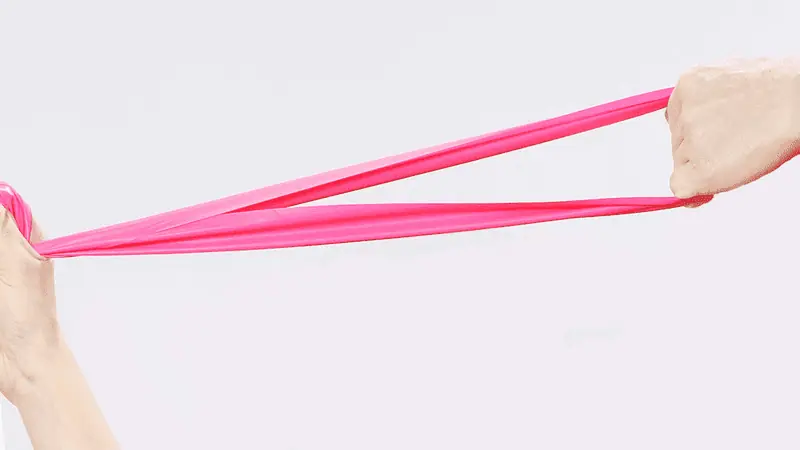
Mechanical properties refer to the ability of a material to withstand impact forces, tearing, and elongation. A simple table compares the mechanical (physical) properties of silicone and fluorosilicone rubber.
Mechanical Properties | Silicone | Fluorosilicone |
Hardness | 20-90 Shore A | 35-80 Shore A |
Tensile Strength | 200-1500 Psi | 200-1500 Psi |
Elongation | 100-900% | 100-500% |
Abrasion Resistance | Poor | Poor |
Compression Set | Excellent | Good |
Impact Resistance | Good | Good |
Resilience | Good | Fair |
Tear Resistance | Fair | Fair |
Vibration Dampening | Fair | Good |
From the above table, we can easily conclude that silicone is a much more rigid and resilient rubber material. But It should be noted that the properties of fluorosilicone are only slightly behind silicone. For most applications, fluorosilicone rubber will be more than a good option.
Due to their poor abrasion resistance, neither material is suited for rough environments with high friction characteristics.
Environmental & Thermal Resistance
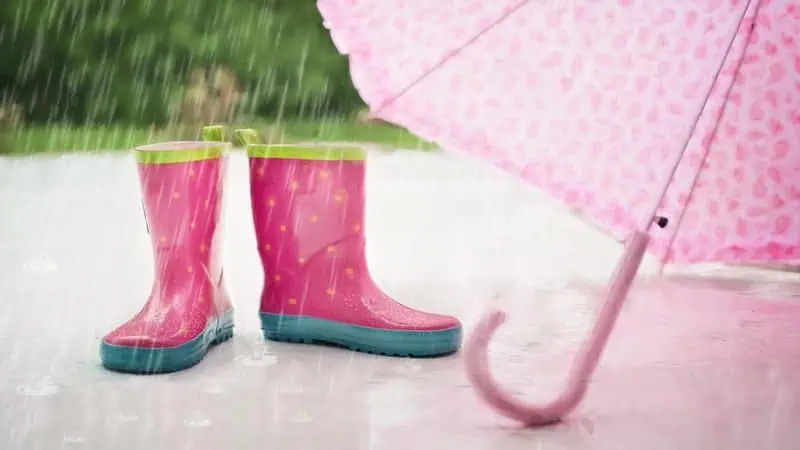
Environmental damage is caused by naturally occurring compounds like water, ozone, and sunlight (UV). Following is a table comparing the environmental resistance and thermal properties of silicone and fluorosilicone.
Silicone | Fluorosilicone | |
Colorability | Excellent | Great |
Flame | Great | Excellent |
Gas Permeability | Poor | Fair |
Ozone | Excellent | Excellent |
Sunlight | Excellent | Excellent |
Water | Excellent | Excellent |
Temperature Properties | Silicone | Fluorosilicone |
Cold Resistance | -178º to -90º F | 400º to 550º F |
Heat Resistance | -85º to -70º F | 400º to 450º F |
Again, the two materials have similar properties, but silicone has slightly better temperature resistance. Silicone products can withstand a broad temperature range, environments with high humidity, and locations where flame damage is expected.
Gas permeability is the ability of a material to allow the flow of gas through it. Poor permeability is good, as silicone rubber will be air-tight, allowing any chemical gasses to bypass it.
Though fluorosilicone is very close in properties, the slight difference disqualifies it as a potential option for medical applications.
Chemical Resistance
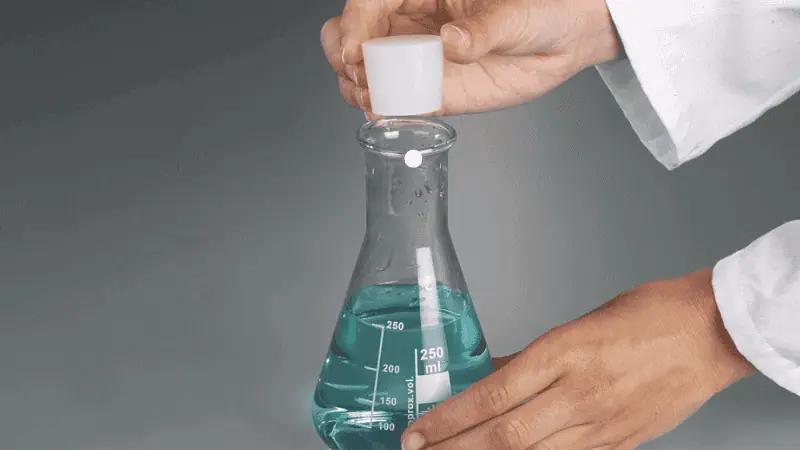
Rubber materials are fragile to chemical degradation. Acids, alkaline chemicals, vegetable oils, and other chemicals will either dissolve the rubber or erode it over time. Here is a table comparing silicone and fluorosilicone and their resistance to various industrial chemicals.
Chemical Resistance | Silicone | Fluorosilicone |
Acids | Good | Excellent |
Alkalies | Good | Excellent |
Amines | Good | Poor |
Vegetable Oils | Great | Excellent |
Fuels | Poor | Excellent |
Ketones | Poor | Poor |
Petroleum | Fair | Good |
Refrigerant | Poor | Good |
Silicone Oil | Poor | Excellent |
Solvents | Poor | Excellent |
Here we can finally see some fundamental differences between the two rubber materials. So far, silicone has been the superior option, but when dealing with harsh chemicals, fluorosilicone is the clear winner.
Silicone can deal with the occasional dilute chemicals, but it will melt and dissolve under anything else. Silicone rubber is not meant for automotive applications as it would be constantly exposed to brake fluids and petroleum oils.
In contrast, fluorosilicone rubber distinguishes itself based on its unique properties. It will withstand almost every chemical out there with the expectation of a select few. Fluorosilicone’s resistance to refrigerant damage makes it a good material for refrigerator seals and gaskets.
List of Applications
If we go by material properties, silicone, and fluorosilicone are great options for commercial and residential applications. They have excellent resistance to mechanical stress and can operate in extreme environments. Fluorosilicone also has excellent resistance to concentrated acids and can resist solvents and other aromatic hydrocarbons.
But the cost of fluorosilicone restricts its applications to specialized cases.
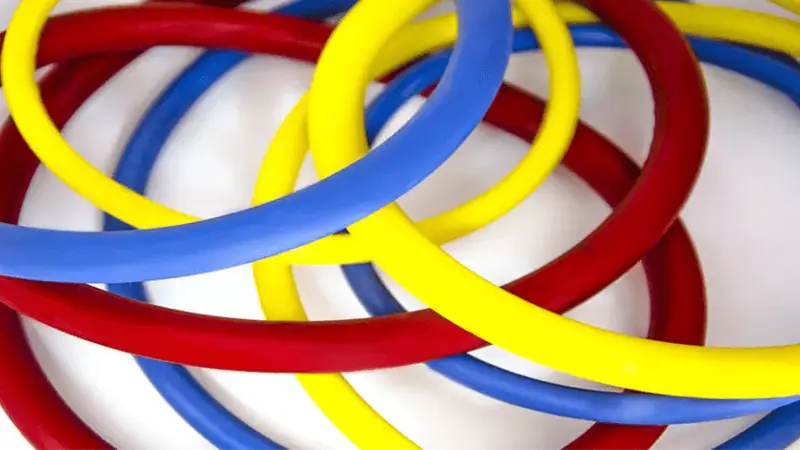
What Is Fluorosilicone Rubber Used For?
Fluorosilicone makes several sealing solutions, including gaskets, seals, adhesives, tubings, and o-rings. It is the industrial application of these sealing solutions that matters more.
The following applications of fluorosilicone are categorized by industries. It should be noted that all of these industries use the same seals, gaskets, o-rings, and more but for different applications.
- Automotive Industry
Due to their excellent heat resistance, the automotive industry uses fluorosilicone gaskets, o-rings, and seals for engine blocks. Another benefit of fluorosilicone is its high resistance to gasoline, brake fluids, and other automotive chemicals.
- Petroleum Oils Industry
Fluorosilicone is highly resistant to petroleum-based compounds. So it only makes sense to use fluorosilicone for seals on oil tanks and hoses for oil transfer.
- Commercial Appliances
Large commercial equipment requires high-quality seals, gaskets, and adhesives that can withstand damage. Since most commercial equipment is quite expensive, the added cost of fluorosilicone is negligible compared to its benefits.
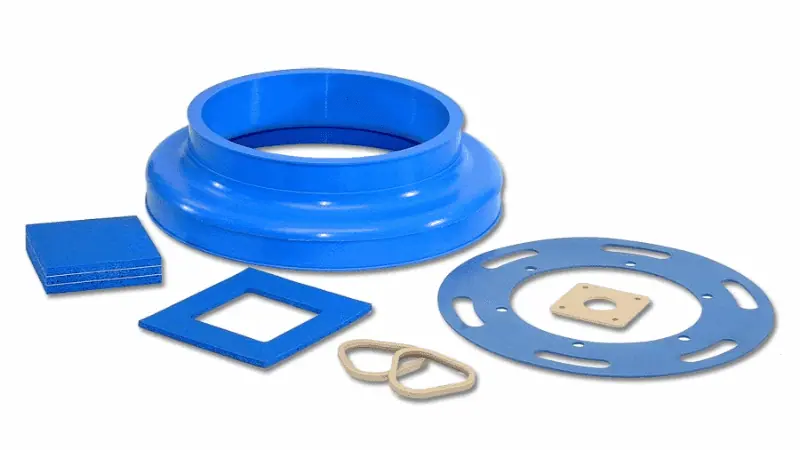
- Chemical Processing Plants
Chemical plants constantly transport large volumes of dangerous and harmful chemicals nationwide. They need high-quality rubber tubing with good heat resistance and can withstand most chemicals like oils, fuels, and aromatic hydrocarbons.
What Is Silicone Rubber Used For?
The most significant advantage of silicone rubber is its low cost and wide range of properties. Even though some alternative materials might offer better properties, silicone will still be a top choice based on its lower cost. As such, too many silicone applications are to be listed in this article. So here is a list of the most popular applications of silicone rubber.
- Aerospace Industry
Due to its excellent thermal-resistant properties, silicone rubber is used for small gaskets and o-rings for space-bound equipment.
- Construction Industry
Silicone seals and coatings are typical applications used on a construction site. The lower cost makes it easier to use large amounts of silicone to cover window borders, ceilings, etc.
- Electronics Industry
Silicone is a low-cost and versatile material that is also an electrical insulator. As such, you will see silicone used for electronic housing and adhesion.
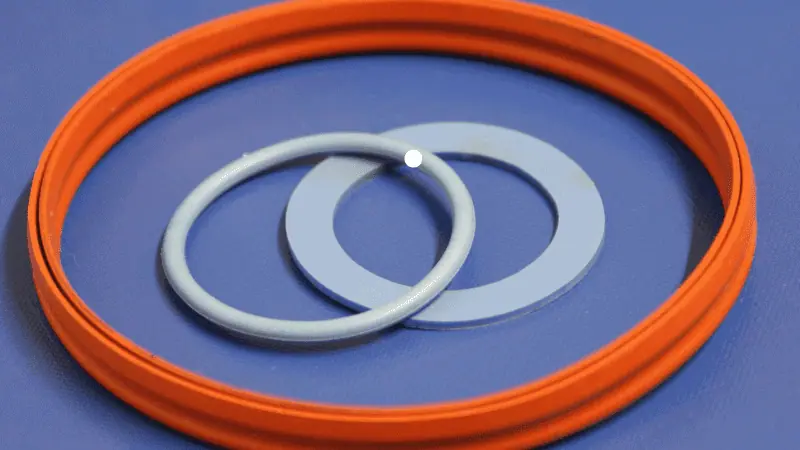
- Toy Industry
A toy material needs to accomplish two things, be cheap and non-toxic. Health and safety regulations worldwide prohibit selling toys with harsh chemicals (materials). Luckily silicone is a non-toxic material used to make wheels and rubber dolls and coat sharp edges.
- Medical Industry
Silicone is also one of the few materials out there that are medical grade, meaning it can be sterilized without affecting its overall properties. Silicone tubing, seals, and grommets are commonly used in medical and hospital equipment.
- Food & Beverage Industry
Medical-grade silicone is also food-grade. It is commonly used for bottle seals, air-tight food containers, and packaging.
Conclusion
When it comes to selecting the right rubber material for specific applications, careful consideration is needed to assess the benefits and drawbacks of each option. Flouroicone, for example, offers excellent resistance to high temperatures and chemicals, while silicone is known for its superior electrical properties. Both rubber materials have proven strengths and weaknesses.
Ultimately, the best material choice depends on the specific application and requirements. It is essential to work with a knowledgeable manufacturer that can guide you through the process and help you select the ideal rubber material.
Choose Hongju for All Your Fluorosilicone & Silicone Needs
Hongju is an industry leader when it comes to manufacturing high-quality rubber products. All our products and OEM & ODM services are CE and FDA-approved, so you don’t have to worry about safety.
We also offer a diverse range of rubber material choices and low MOQs. Become one of the several businesses that have succeeded in using Hongju products.