There are several FDA-grade elastomers, and choosing a suitable one for your application may be challenging. Fortunately, this article discusses how to choose FDA-grade rubber materials and tips on making them last as long as possible.
What are FDA-Grade Rubber Materials?
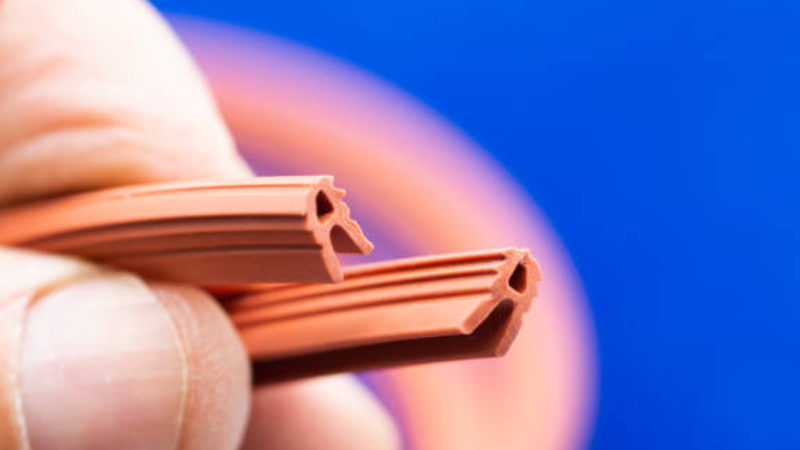
FDA-grade rubber materials are approved for use by the Federal Drug Administration (FDA). This approval means the rubber materials are safe for manufacturing food, pharmaceutical, and medical products. In addition, FDA-grade rubber materials are tested and have met the standard safety conditions.
Furthermore, FDA-grade rubber materials are safe and resilient. They possess properties like temperature and chemical resistance. They are also resistant to bacterial buildup, do not leach into food, and are non-allergenic.
What are FDA-Grade Rubber Materials Used for?
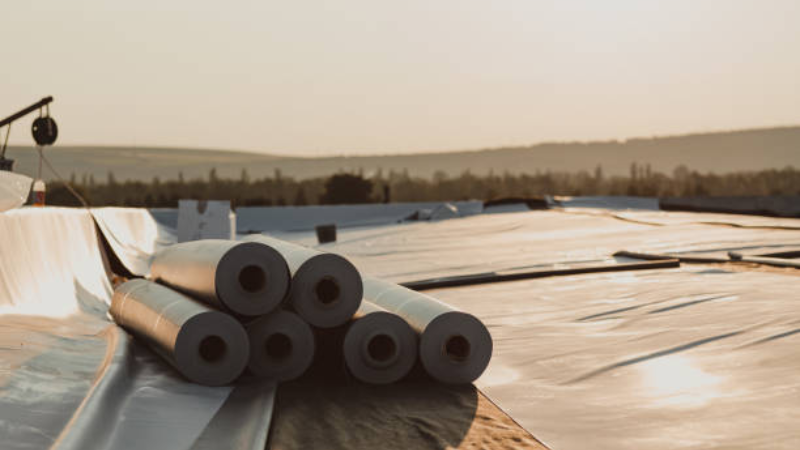
FDA-grade rubber materials are used for several food processing and packaging applications. Due to their properties, these materials are used in handling beverages, meat, dairy, and pharmaceuticals. These materials are also used to protect
Food-grade rubber is also used to manufacture FDA-grade seals, gaskets, suction cups, rubber couplings, and dust covers.
The Benefits of Using FDA-Grade Rubber Materials in Your Business
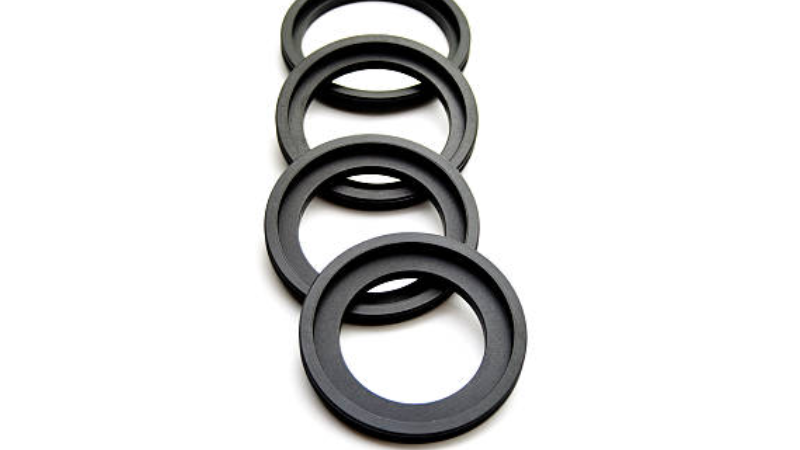
Using FDA-grade rubber materials in your business provides several benefits, including;
- Establishing your reputation in your industry
FDA-approved products establish your product as safe and quality. Products with this approval undergo rigorous tests and FDA regulations before they are certified. The certification distinguishes your product from your competitors, helping you to stand out.
- Ideas to improve your product
Because your product will undergo rigorous testing, it gives you and your team ideas on where to improve and make your product even more reputable. So, even though your FDA-grade rubber product is already utilized in the food and beverage industry, you can still upgrade and enhance it for better customer satisfaction.
- Access to international markets
Food-grade rubber products come with a certificate that allows you to do business outside your country. Because of the approval, you can market and export your products and ensure they are recognized in another country.
- Product Acceptance
Food and medical industries strictly accept only standard products. Your rubber product will be readily accepted into these industries with FDA approval. In addition, you can also work with these industries to get ideas on improving your product and creating more consumer-oriented products.
- Increased sales
Consumers are likely to purchase a product with a seal of approval. For example, it is common knowledge that FDA-grade rubber materials are tested, trusted, and pass stringent standards. Consequently, using FDA-approved rubber products in your business increases demand and sales.
How to Choose the Right FDA-Grade Rubber Material for Your Needs
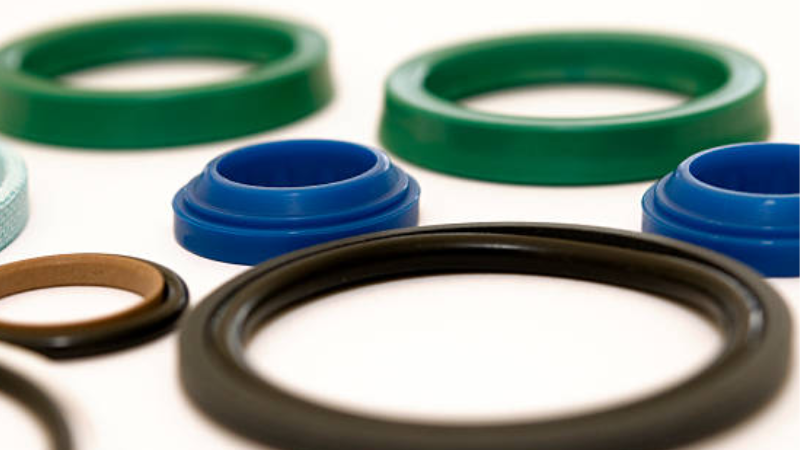
FDA-grade rubber materials are made from different rubber compounds. Therefore, because all rubber compounds have varying properties, it is essential to consider the operating conditions of your application before choosing one. Some Food-grade rubber materials are more suitable for high-heat applications, while some are better for chemical applications.
Some popular FDA-grade elastomers you can choose from include;
Food-grade Silicone
Food-grade silicone rubber is widely used in the food industry because of its thermal stability and low chemical reactivity. This elastomer is also heat resistant and has low toxicity. In addition, silicone has a long lifespan.
Of all food-grade rubber materials, silicone has the broadest operating temperature range between -50 to 200 degrees Celsius. Furthermore, food-grade silicone is widely used in producing gaskets, rubber seals, and kitchen utensils.
Neoprene
Food-grade neoprene has a fine finish, making it resistant to oil and grease. This elastomer is also resistant to mold buildup, water, and the weather. In addition, neoprene can withstand temperatures between -40 and 135 degrees Celsius. Although neoprene cannot withstand as much heat as silicone, this elastomer is ideal for producing refrigeration seals and medical devices.
EPDM
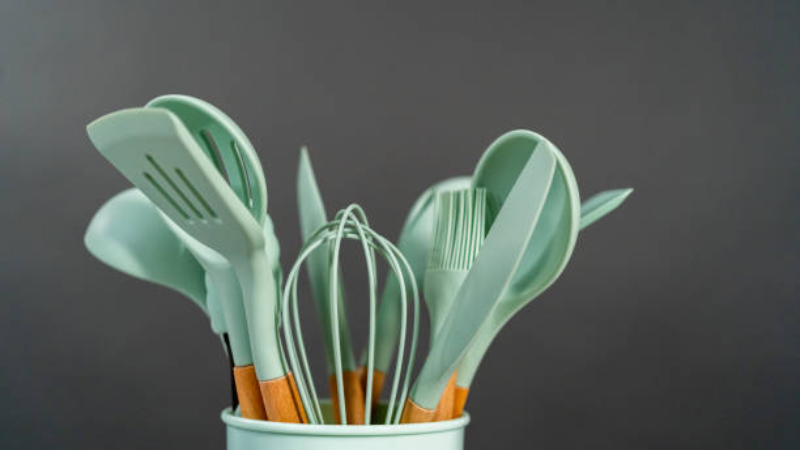
Food-grade ethylene propylene diene monomer (EPDM) is an odorless and tasteless synthetic elastomer. This elastomer has excellent thermal stability and can function properly in hot water and steam. In addition, EPDM has a temperature range between -50 and 150 degrees Celsius. It is also ideal for manufacturing gaskets and skirting for food processing.
FFKM
Perfluoroelastomer (FFKM) is a non-toxic elastomer with low chemical reactivity. This food-grade elastomer is used in applications that require sterilization. FFKM is used to produce O-rings and sealing solutions. Furthermore, food-grade FFKM rubber products are used in the dairy, food, and beverage industries. The temperature range of this elastomer is -15 to 300 degrees Celsius.
Nitrile
FDA-approved nitrile rubber is a non-toxic and non-allergenic rubber product. The elastomer has excellent resistance to petroleum-based oils and fuels. It is also resistant to grease and hydraulic fluids. The temperature range of food-grade nitrile rubber is between -40 and 125 degrees Celsius. Cosmetic, medical, and food applications use FDA-approved nitrile rubber products.
FKM
Fluorocarbons (FKMs) are water-resistant elastomers with high-temperature resistance. It can retain its properties even after prolonged exposure to high operating temperatures. This rubber material is suitable for food applications that use steam and hot liquids. FKMs are ideal for manufacturing mechanical devices, gaskets, and seals. Furthermore, due to their non-toxicity and low chemical reactivity, FKMs reduce the chances of food contamination.
The Importance of Quality Control in the Manufacturing Process
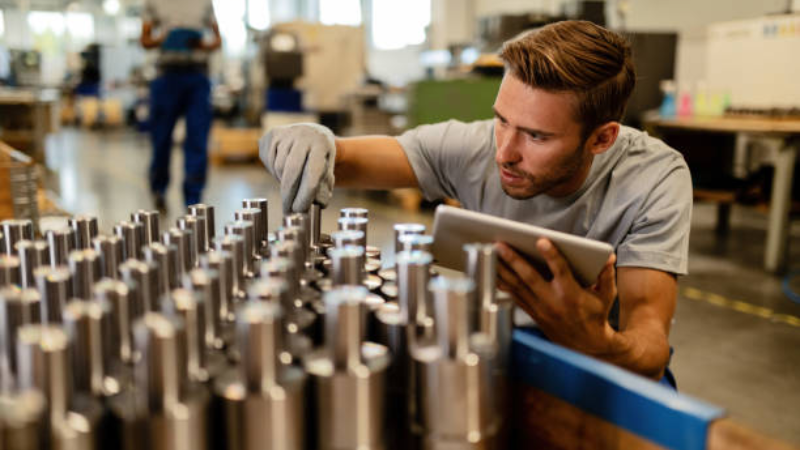
Quality control is essential in the manufacturing process because it ensures you only release products that satisfy consumers to the public. Quality control is more than just inspecting the final products before releasing them. It entails material, in-process, and final inspection. Each inspection stage helps you catch issues and fix them, ensuring the overall quality of the product.
Besides quality, other reasons why quality control is critical in the manufacturing process include the following;
- Consistency – quality control ensures that your products meet a standard. Therefore, every product from your production line has the same consistent quality. A compatible product builds customer trust and helps you gain customer loyalty.
- Compliance – before releasing a product to the public, it must meet the rules and regulations of certifying bodies. Otherwise, there may be delays in production and hefty fines. Consumers are more likely to purchase products that comply with safety standards.
- Minimizing risks – quality control identifies the root cause of a problem, reducing the potential for product defects and errors.
- Waste reduction – you can identify and fix issues with a product before producing them en masse. Consequently, quality control saves you money on materials and downtime.
Tips for Maintaining Your FDA-Grade Rubber Products Over Time
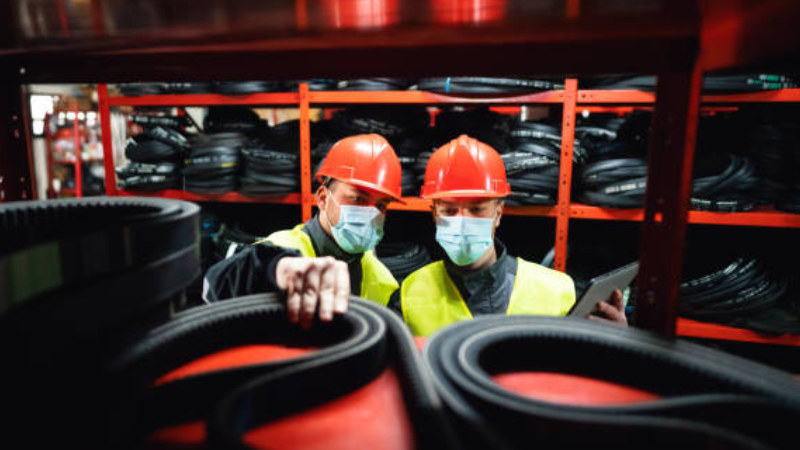
- Store in a cool and dry place. Food-grade rubber products have different shelf lives depending on the elastomer they are made from. For instance, silicone rubber is more durable than nitrile rubber. Nevertheless, storing your rubber product in a cool, dry, and dust-free space allows you to achieve maximum shelf-life.
- Monitor the strorage temoerature. Keep your rubber products at temperatures between 15 and 25 degrees Celsius. Ensuring the temperature does not drop below -10 degrees Celsius is best. Elastomer products stiffen at lower temperatures, shortening their lifespan.
- Store rubber products in relatively humid conditions. Humidity should not exceed 65%. It is also best to avoid arid conditions.
- Protect your elastomers from UV-light sources. Direct sunlight or intense artificial light can damage your rubber products.
- Avoid contact with metals and alloys to prevent damage. You should also keep your rubber products from fuels, greases, and plasticizer-containing materials.
- Avoid deformation. Exposing your rubber products to strains or compressions may damage or crack them, leading to a shorter lifespan. It is best to store your food-grade rubber materials in an adequate space without subjecting them to deformative forces.
Conclusion
FDA-grade rubber materials are essential in the manufacturing industry. They are instrumental in the food, medical, and pharmaceutical industries. These rubber materials comply with FDA standards, making them suitable for use in industries that require low toxicity and high purity.
Using FDA-grade rubber products in your business provides many benefits, including establishing your credibility and increasing demand for your product.
Get Your FDA-grade Rubber from Hongju!
Although FDA-grade rubber is excellent for your business, not all manufacturers are truthful with what they produce. But at Hongju, we can guarantee 100% food-grade elastomer products. With over two decades of experience producing rubber products, our work speaks for itself.
We provide top-of-the-line solutions if you are looking for a reliable rubber product supplier. We produce household appliances, medical equipment, and automotive rubber products to suit your specifications.
Kindly reach out today!