Are you confused about which rubber to buy for your next project? There are two distinctions in the industry: EPDM rubber vs. Neoprene. EPDM is an ethylene propylene diene monomer; it is considered the most cost-effective option. While neoprene is an expensive option, it offers higher resistance and better insulation. But there is much more to it than just these qualities. Let’s break down the unique properties, benefits, and uses of two rubber materials and end the neoprene vs. rubber debate once and for all.
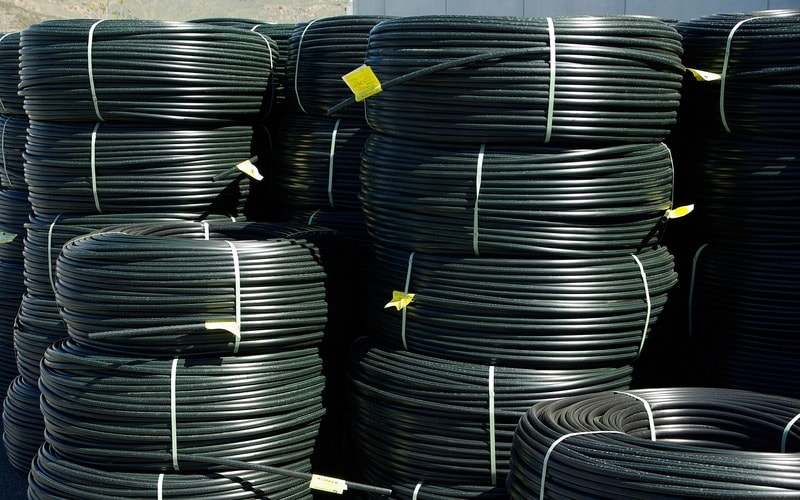
Characteristic Differences in EPDM and Neoprene
Understanding characteristic differences is important while evaluating the two great rubber material types. Both materials have other characteristics and are built for specific applications; hence, it is important that you go through these properties.
Properties of EPDM
EPDM rubber is known for its resilience towards specific challenging environments, including;
- Temperature: It performs well across a wide range of temperatures, tolerating both hot and cold environments.
- Ozone and UV radiation: It is ozone-resistant and protects against UV damage, making it ideal for outdoor applications.
- Water: Like all rubbers, it is waterproof. Thus, it is commonly used in roofing and other weather-stripping materials.
- Vibration: It exhibits excellent vibration resistance and is utilized in vibration mounts as well as noise-resistant rubber applications due to this property.
Properties of Neoprene
Neoprene rubber has its own list of properties where it shines, including;
- Corrosion and chemical resistance: It can withstand exposure to all sorts of chemicals, including oils, acids, and solvents, without damage.
- Insulation: It provides excellent insulation, thus making it a preferred choice for products like diving suits, rubber gloves, and high-pressure adhesives.
- Weather resistance: While not as strong as EPDM, Neoprene also offers sunlight and weather resistance to some extent.
Both of the materials offer very distinct advantages. EPDM’s popularity is due to its outdoor durability and extreme weather resistance. Neoprene is a standout insulation material, but it is also a preferred option for industrial use given its chemical and oil resistance. In the end, the choice between the two depends on the specific requirements of your project. Understanding these properties is a critical factor while making an executive decision for your business.
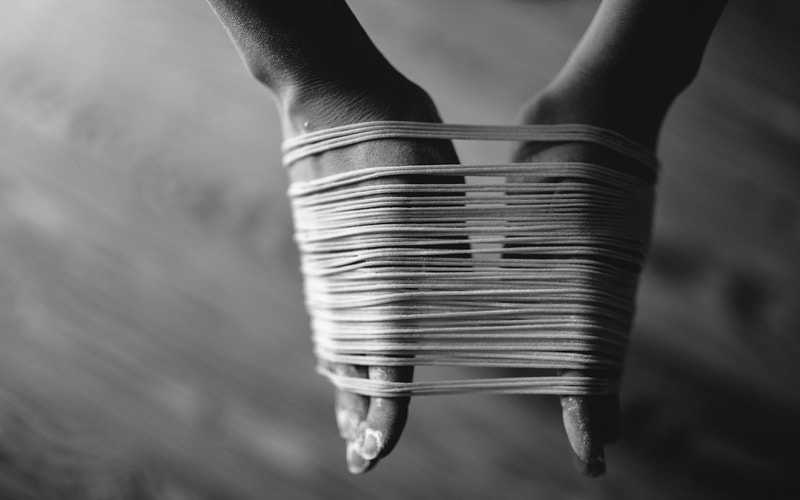
Durability and Stability Comparison
In the rubber world, durability and stability are the most important factors after elasticity. It is crucial to understand the conditions that challenge the durability and stability of both the rubbers while choosing material for your business. Both EPDM and Neoprene are highly durable and offer good resistance, but their strengths lie in different areas.
Let’s understand the difference between EPDM and neoprene to ensure you obtain the right material for your project.
Excellent Durability with EPDM
EPDM is regarded as the most durable man-made rubber. There are three qualities that make it a lasting material perfect rubber.
- Abrasion Resistance: The stable backbone structure of EPDM makes it highly abrasion resistant, allowing it to withstand wear and tear from rubbing with other surfaces.
- Compression set: EPDM offers extreme flexibility. It is known to retain its shape and flexibility even under high pressure.
- Ozone and sunlight resistance: The saturated structure of EPDM, made up of single bonds, makes it resistant to ozone damage.
Resilient and Versatile Neoprene Rubber
Neoprene rubber is considered the most reliable material due to its resistant properties to chemicals, including hydrocarbon solvents. It is renowned for its resilience and versatility for the following qualities:
- Adhesive Ability: It readily adheres to a variety of materials, from metals to fabrics, making it a suitable option for bonding applications.
- Abrasion resistance: It is able to maintain its integrity under rigorous use, making it a suitable option for products such as rubber gloves, diving suits, and vibration mounts.
- Elasticity and tear resistance: Neoprene has a good tensile strength, allowing it to stretch a great deal under high pressure without tearing or breaking. It is able to handle considerably high loads and manage dynamic movements effectively.
- Chemical and fuel resistance: Chemical resistance is one of the benefits of neoprene. Neoprene is made up of chlorine polymers that create a barrier against chemical substances, including aromatic and oxygenated solvents. Hence, it is resistant to corrosive substances, including oils, solvents, fuels, and other petroleum-based products.
Life-cycle
Depending upon the manufacturing, installation, and maintenance of the product, EPDM can last anywhere from 20 to 50 years. On the other hand, neoprene has a shorter life span of 5-10 years.
Stability Analysis
Both products exhibit excellent stability and are capable of withstanding high loads as well as maintaining performance under strenuous conditions. In the end, the choice between the two materials is application-dependent. In situations where outdoor durability is the priority, EPDM takes charge. When chemical resistance is the requirement, then Neoprene is the preferred material.
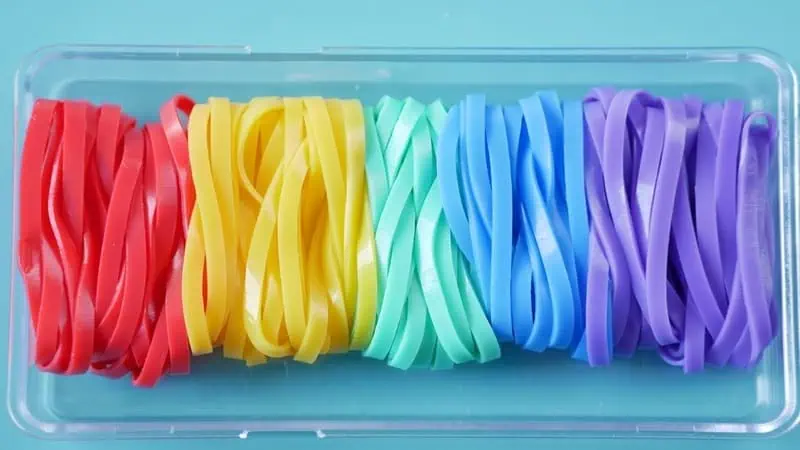
Cost and Selection Considerations
The cost has to be considered whether you need rubber for an engineering prototype or have a business. When comparing types of rubber, cost and selection criteria play a significant role in determining the right material for a project.
Cost Analysis: EPDM vs. Neoprene
EPDM rubber is known for its affordability. It is readily available in markets due to its low cost. Being cost-effective, it is used in a variety of applications, including roofing and seals. It is infamously used in outdoor installations because of its weather-resistant features. However, it has some performance limitations that should be evaluated to ensure you get a value-for-money deal.
On the other hand, Neoprene rubber comes with a significantly higher price tag. Its superior properties, including excellent resistance to chemicals, oils, and abrasion, drive its prices higher. These are the same qualities that make it more suitable for specialized uses such as diving suits, chemical-resistant gloves, and vibration mounts.
The cost of materials is highly dependent on the project requirements and durability needs. If project applications involve constant chemical disposition, then you need to opt for an anti-corrosive rubber. In other use cases, where coverage and weather resistance are key requirements, you can opt for a less chemically resistant rubber.
Choosing between EPDM and Neoprene rubber boils down to just three of these factors:
- Budget: EPDM is cheaper than Neoprene, but neoprene provides a high value for money deal in specialized projects
- Durability: EPDM shows high durability against weathering and lasts half a century. While neoprene only retains its perfect composition for a decade, it offers extreme chemical resistance.
- Performance Needs: It all boils down to your project’s needs. Assess environmental factors such as exposure to chemicals, UV radiation, or temperature fluctuations to ensure your material meets your project demand.
Choosing the Right Material for Your Needs
Choosing the right material between EPDM and Neoprene rubber is a decision that depends on your project’s specific requirements. While both materials are extremely adaptable, they thrive in different environments due to their unique features.
Consider the following factors while selecting between EPDM and Neoprene to ensure your project’s success.
- Temperature Range: EPDM can withstand a higher level of temperature on both extremes (-60°F to 350°F), making it suitable for situations with varying temperatures. While Neoprene is better heat resistant, its tolerable temperature range is lower (-50°F and 250°F), providing more constant performance in mild conditions.
- Chemical Resistance: The chemical structure of Neoprene protects it from any sort of chemical infringement, offering unparalleled resistance towards acids and petroleum solvents. However, EPDM also offers mild chemical resistance towards mild acids, oxygenated solvents, and alkalis.
- Durability Needs: EPDM is an affordable solution for outdoor applications that require resistance to UV radiation, ozone, and weathering. Neoprene is a higher-end material that is best suited for applications requiring chemical protection and water resistance.
You can select the material that delivers performance, reliability, and cost-effectiveness by evaluating your project’s needs on the above-mentioned points. If you are still unsure of what type of rubber to get for your project, here’s a closer look at when and why to use each material.
When to Use EPDM Rubber
EPDM should be the choice when you are looking for a cost-effective solution, but your project demands resilience against environmental conditions. Moreover, you have to choose EPDM when your project requires tolerating extreme temperature ranges. In short, if your project is related to outdoor coverage, EPDM should be your go-to choice.
When to Use Neoprene Rubber
You have to opt for Neoprene rubber if your project requires tolerating extreme chemical situations. For example, projects involving oils, solvents, acids, and petroleum substances have to use neoprene over EPDM. Moreover, if you want your product to be highly flexible under extreme stress, then Neoprene should be your preferred choice. Lastly, neoprene is the obvious choice in use cases where better thermal insulation is a key requirement.
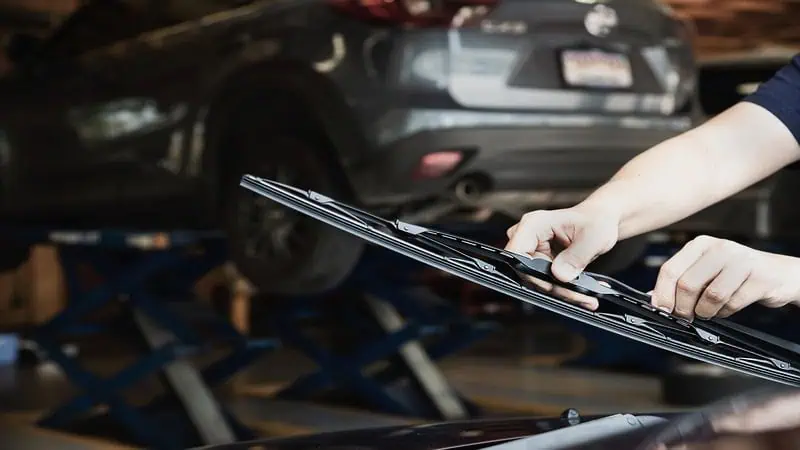
Applications and Uses
Both Neoprene and EPDM are versatile synthetic rubbers that have replaced natural rubber across various industries. They have become indispensable in modern engineering and manufacturing due to their unique properties. Let’s explore their unique applications and uses individually:
EPDM Applications
EPDM rubber is a practical and cost-effective solution for projects that demand resilience against environmental challenges. It boasts exceptional resistance to UV radiation and ozone. It also operates effectively in extreme temperature ranges, from -40°C to 150°C (-40°F to 302°F), thus managing harsh weather conditions. All these properties make it ideal for outdoor projects that endure prolonged exposure to sunlight and varying climates.
Vibration resistance EPDM is widely used in automotive, manufacturing, power sports, construction, roofing industries, and electrical engineering. It is used to make EPDM gaskets, EPDM seals, automotive weathering strips, electrical insulation, roofing materials, outdoor seals, HVAC systems, engine bays, etc.
Neoprene Applications
Neoprene rubber is the preferred material for applications that require chemical resistance, flexibility, and thermal insulation. As mentioned previously, it is resistant to oils, chemicals, and solvents and maintains its integrity when exposed to these harsh substances. It cannot be replaced with other rubbers in chemical plants, oil rigs, and other demanding industrial settings.
Neoprene also retains its flexible nature in a range of conditions. Hence, it is an excellent choice for applications that involve movement or vibration. Furthermore, its thermal insulation properties are unique to neoprene rubber only. Most commonly, it is used in diving suits, insulated hoses, gaskets, seals, rubber gloves, and personal protective equipment. Another unique property of Neoprene is its ability to form strong bonds, making it a great adhesive.
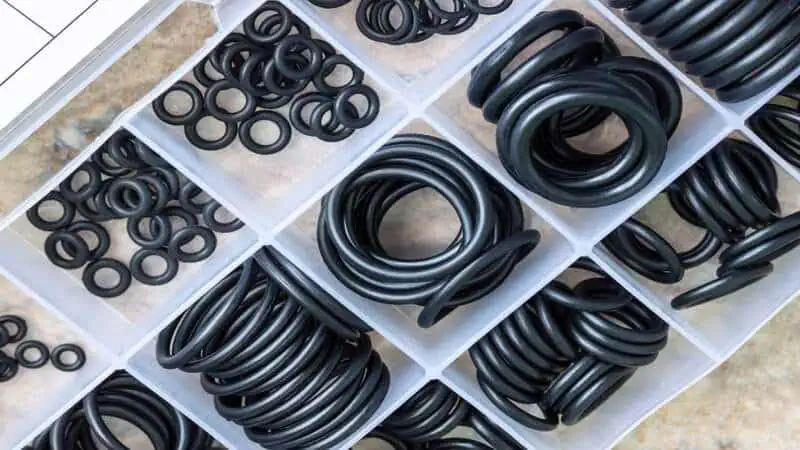
Environmental Impact and Sustainability
In an era of increased environmental awareness perpetrated by damage caused by synthetic materials, we have to be conscious of our choices. While synthetic rubbers offer excellent performance, their manufacturing and disposal procedures can leave a significant impact on the environment.
Eco-Friendliness of EPDM
EPDM is relatively more eco-friendly than other synthetic rubbers due to its long lifespan. While its manufacturing process relies on fossil fuels and utilizes petrochemicals, its resistance to degradation reduces the need for frequent replacements. Moreover, many of its applications are recyclable. Most end-of-life EPDM products can be repurposed into other products. For example, roofing membranes can be repurposed to make playground surfaces and other secondary synthetic rubber products.
Eco-Friendliness of Neoprene
Even though Neoprene is highly versatile and durable, it is less eco-friendly than EPDM. Its production process has a higher environmental impact as it is very energy-intensive and produces harmful by-products. Moreover, there aren’t many avenues to recycle Neoprene products. Given the shorter lifespan of neoprene, the products require frequent replacement, contributing to waste.
As we continue to strive for a greener tomorrow, we have to be conscious of the choices we make today. While the world is looking for alternatives and trying to develop recycling options, it is upon you to choose the material that leaves minimal environmental impact.
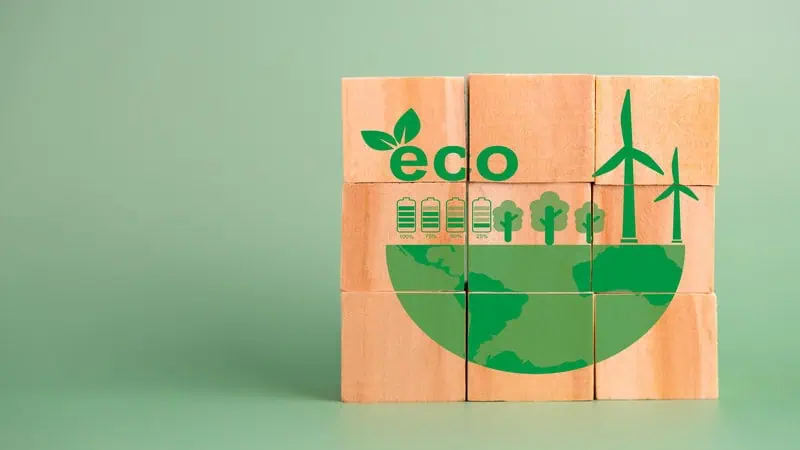
Pros and Cons Summary
If you are still unclear on the decision of EPDM vs. Neoprene, you can use this quick breakdown of the advantages and disadvantages of both materials to make an informed decision.
EPDM Rubber Pros and Cons
Advantages | Disadvantages |
---|---|
Durability: It is extremely resistant to UV radiation, ozone, weathering, and severe temperatures, making it perfect for outdoor applications such as roofs, seals, and gaskets. | Chemical Resistance: EPDM performs poorly in situations containing oils, fuels, and some chemicals, restricting its use in industrial and chemical applications. |
Cost-effective: EPDM is often less expensive than other synthetic rubbers, making it an excellent choice for larger projects. | Flexibility: While it is durable, it may not be as flexible as Neoprene in applications that require elasticity. |
Longevity: Its resistance to degradation ensures a long service life, which lowers maintenance and replacement expenses. | |
Noise and Vibration Resistance: It offers superior shock-absorbing characteristics, allowing it to be used in vibration mounts and noise-dampening applications. |
Neoprene Rubber Pros and Cons
Advantages | Disadvantages |
---|---|
Chemical and acid resistant: Neoprene thrives in conditions involving oils, solvents, and other chemicals, making it ideal for industrial, marine, and automotive applications. | Cost: Neoprene is more expensive than EPDM, which can be a drawback for tightly budgeted projects. |
Thermal Insulation: It provides excellent thermal insulation. | Weather Resistance: While it is resistant to sunshine and weathering, it does not perform as well in outdoor applications as EPDM. |
Flexibility and Elasticity: It is highly elastic, making it perfect for applications that require stretch and recovery. | Environmental Impact: Neoprene has a larger environmental impact and fewer recycling possibilities than EPDM. |
Versatility: It performs considerably well in water-related and industrial applications, for example in corrosion-resistant coatings and vibration mounts. |
Frequently Asked Questions
Q1: Which is better, Neoprene or EPDM?
A1: It totally depends on your project requirements. EPDM is ideal for outdoor applications, while Neoprene is useful in industrial settings.
Q2: Which material is better for outdoor applications?
A2: EPDM is better for outdoor applications because of its superior resistance to UV rays, ozone, and weathering.
Q3: Are rubbers recyclable?
Yes, to some extent, EPDM and Neoprene rubbers can be recycled. However, recycling programs are more developed for EPDM, while Neoprene’s recycling ability is quite limited.
Conclusion
Neoprene and EPDM rubber are both versatile and long-lasting synthetic rubber, with each having particular qualities adapted to certain uses. EPDM excels in outdoor, weather-resistant applications due to its UV and ozone resistance. Whereas Neoprene shines in chemical-intensive and thermal insulation conditions.
Despite their respective advantages and disadvantages, EPDM and Neoprene are still popular among both experts and do-it-yourselfers. However, understanding their distinctive qualities is critical for choosing the appropriate material for your project.
Choose The Best Quality Rubber From Us!
Hongju Silicone has over 23 years of experience manufacturing high-quality rubber products for a variety of industries. Our commitment to innovation and quality guarantees that your business receives the reliable solutions it needs.
Ready to find the perfect material for your project?
Request a free consultation today or explore our product catalog to see how we can meet your unique requirements!