Hence, this article will detail everything you must know about custom-molded rubber parts for construction, including the benefits, types, uses, and applications. Happy Reading!
Rubber Materials Used In The Construction Industry
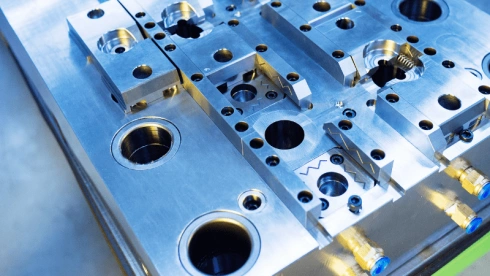
Let’s start with the different types of rubber materials used by the construction industry. These include a variety of synthetic rubber materials apart from natural rubber:
Nitrile Butadiene Rubber: famously known as NBR or nitrile rubber, this material has tons of benefits for the construction industry. For starters, the material handles fuels and oils pretty well. On top of it, it is the perfect material for gaskets and seals used in construction equipment.
Silicone Rubber: this rubber material performs exceptionally well in low-temperature conditions. Especially when it comes to flexibility in cold environments. Hence, the construction industry readily uses it as seals for applications that require high elasticity in low-temp conditions.
Ethylene Propylene Diene Monomer: the industry term for this rubber is EPDM. It offers high durability, especially in outdoor conditions. Hence, the construction industry uses this rubber material for applications where exposure to UV and high temperatures readily occurs.
Chloroprene Rubber: known as CR, this synthetic rubber resists a variety of oil and chemicals. On top of it, the material performs well in varying weather conditions, making it a suitable choice for equipment and machinery.
Styrene Butadiene Rubber: This synthetic rubber, popularly known as SBR, offers high tensile strength. To add to it, the material also resists regular abrasions pretty well. Hence, the construction industry regularly uses it for vibration dampening.
Rubber Molding Techniques Used for Construction Parts
You must know that manufacturers mold rubbers using different methods to transform uncured rubber. However, despite the numerous ways out there, the following three are the most widely used to produce custom-molded rubber parts for the construction industry:
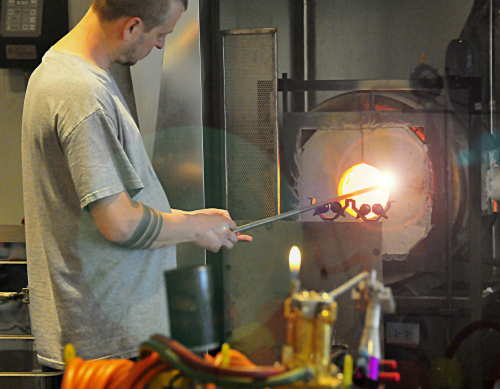
Injection Molding
Injection molding requires molten rubber and a mold. The manufacturer takes the molten rubber and injects it into the mold cavity. Once the correct amount goes in, they wait for it to cool down and form the desired shape.
Compression Molding
As the name suggests, the compression molding technique uses pressure and heat to form different rubber-molded parts. Hence, manufacturers use a pre-formed rubber compound in a pre-formed mold. The combination of heat and pressure produces the final rubber products.
Transfer Molding
There is not much difference between transfer molding and compression molding, just that manufacturers transfer the molded rubber part into a relaxed environment to have a precise shape.
The Benefit of Using Molded Rubber Parts for Construction
Expectedly, custom-molded rubber products serve great benefits to the construction industry. The most prominent ones include the following:
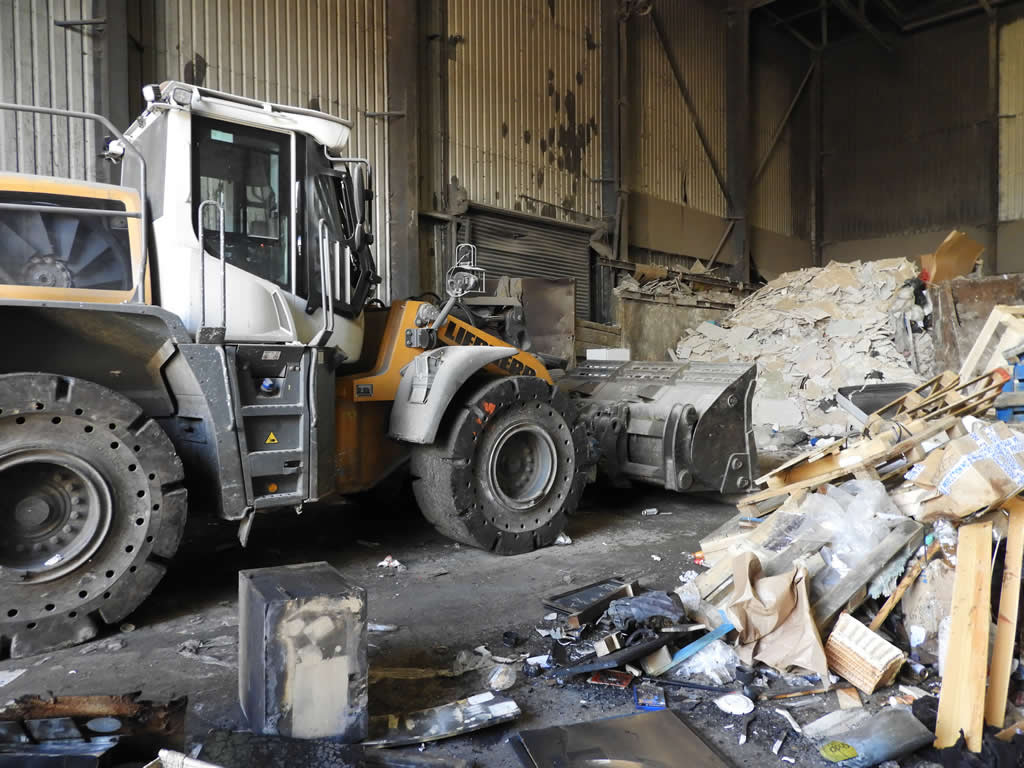
- Customizability: molded rubber components are easily customizable. Mainly if manufacturers use different molding methods for production, they can customize the parts’ size, shape, and color to fulfill customers’ needs.
- Weather Resistance: the construction process often comes in contact with harsh weather, water, and temperature changes. Hence, custom-molded rubber parts come in handy to tackle such conditions, whether used in construction or for equipment.
- Chemical Resistance: custom rubber molded parts, especially those made from NBR, offer excellent resistance to chemicals. These include oils and fuels. Hence, the construction industry readily uses them in machinery and equipment.
- Sealing: custom rubber is an excellent sealant, and construction requires it more often than we know. All the sealing around your house uses some form of rubber compound.
- Durability and Flexibility: unlike many other materials, such as plastic, rubber offers high flexibility and durability. This allows it for long-term use even in outdoor conditions with harsh weathering, ozone, and UV exposure.
Common Molded Rubber Products for Construction
Which custom rubber molded products the construction industry uses? Here is a list for you:
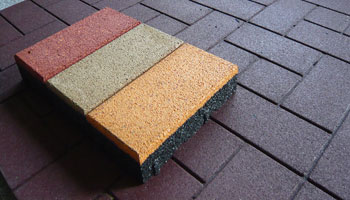
- Cable Cover & Hoses: custom molded rubber products such as cable covers and hoses are protective covering for cables and other components.
- Bearings: bridges often have to handle a lot of loads. Hence, bridge bearings absorb the movements when the load falls on bridges.
- Joints: similar to bearings, joints help accommodate expansion in construction structures when the weather gets hot.
- Mounts: molded rubber mounts are used in equipment and construction to reduce noise and vibration.
- Seals: construction structures such as houses and buildings require custom rubber sealing to keep external elements out.
- Membranes: construction companies use rubber membranes on the roof to add waterproofing and weatherproofing.
- Paddings: rubber paddings help absorb shocks between walls and make them soundproof.
- Tiles: custom rubber tiles are often used in the gym to handle the gym load weight with absorption.
How to Choose The Right Molded Rubber Part for Your Need?
Keep the following factors in mind:
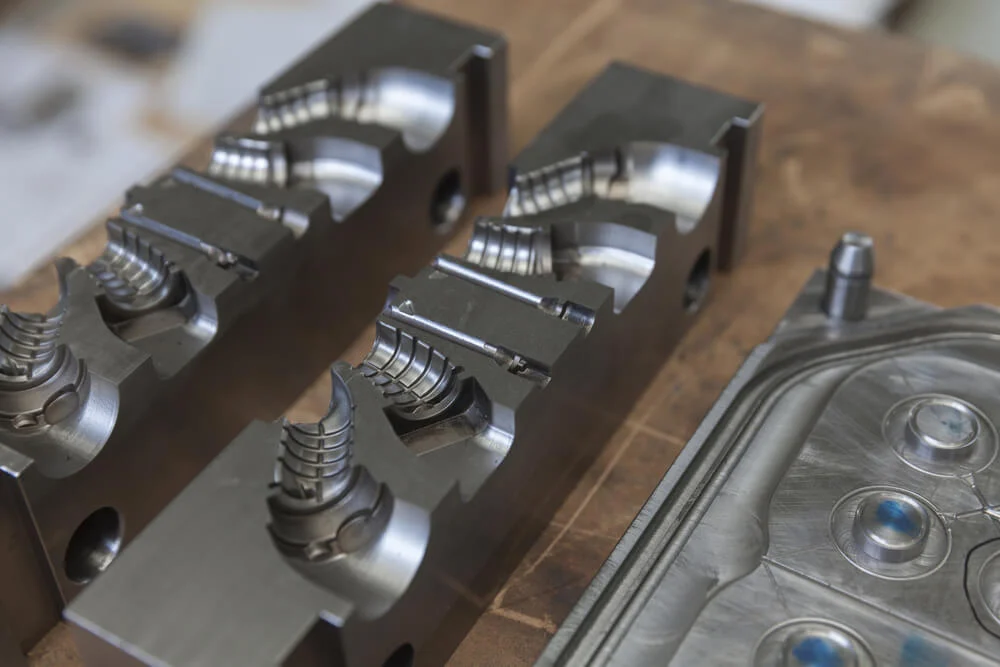
Application
This has more to do with choosing the suitable rubber material than the rubber part. Hence, you must know precisely the conditions of the applications and the requirements.
Based on these, you can request the manufacturer to produce rubber molded parts using a material that will withstand the conditions.
Budget
You must have a budget when going out shopping for inventory. We never recommend compromising on quality due to budget constraints. Hence, always look for a manufacturer that offers deals and has a reputation for reliability with low rates.
Size and Shape
Given the versatility of rubber molded parts, you can get them in any shape and size.
However, you have to define the shape and size to the manufacturer so that they create relevant molds for production. Thus, this requires close collaboration with the manufacturer’s design team.
Applications of Molded Rubber Parts In Construction
As discussed earlier, the rubber industry uses tons of rubber-molded parts for various applications. These include:
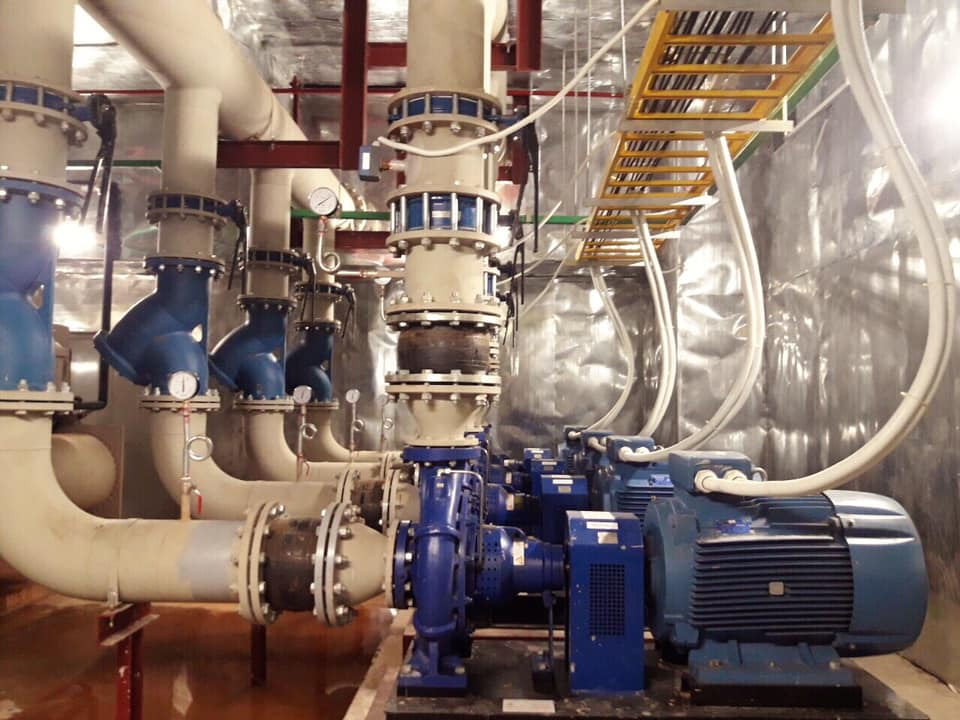
- Piping: the plumbing in buildings uses rubber piping, gaskets, and couplings. This is because rubber successfully prevents leaks, given its sealing abilities.
- Wall Claddings: construction companies use wall claddings and paddings for insulation, protection, and decoration.
- Machines: custom molded rubber components not only serve the buildings but also offer functional benefits to the machinery and equipment used for construction. Hence, you will come across various machines that use rubber hoses, seals, gaskets, grommets, etc.
- Roofing: rubber mats and pads help insulate and protect the roof from external elements such as harsh weather and extreme temperatures.
- Sewerage: rubber molded parts are also used in the sewerage systems of buildings. They help carry the toxic waste while preventing leakages and contamination to other areas.
- Electrical Systems: molded rubber components, such as hoses and cable covers, as well as connector covers, help keep electrical equipment safe. Hence, construction companies use them to provide safe electrical setups in buildings keeping moisture and other environmental factors at bay.
Faqs About Construction Molded Rubber Parts
How are custom rubber parts molded?
Rubber components are molded using specific molding techniques. The most common include injection molding, compression molding, transfer molding, and die cutting. Most reliable manufacturers have the equipment and expertise to mold rubber components using all techniques.
What is rubber molding used for?
Rubber molding helps create rubber parts for specific use. For instance, you can create a particular size of rubber O-rings using compression molding. Similarly, rubber molding helps create a wide range of rubber parts we use daily.
How do I mold my rubber parts?
You can mold your rubber parts at home. However, you cannot match professional manufacturers’ quality and precision. Hence, it is not recommended to set your rubber components. Instead, work with a skilled manufacturer with costly industrial equipment to mold them for you.
How long does a rubber mold last?
Typically, a rubber mold lasts for about 10-20 years. However, this depends on many factors, including material, quality, manufacturing technique, etc. Moreover, it also depends on how you use and maintain the molded rubber component.
Conclusion
To conclude, the construction industry is a big market for rubber-molded parts. On top of it, rubber is a restorative material that helps in many ways by making functionality more manageable and economical. If you run a rubber-molded parts business, you must have a solid inventory for the construction industry.
Your Construction Molded Rubber Parts are Our Responsibility
At Hongju, we have been operating rubber molding facilities for decades. With experience, skill, and passion, we offer customers the highest quality rubber products at the best prices. On top of it, our customer support stays with you till the end, so you have nothing to worry about. Get in touch today!