Two Styles of Molded Silicone Rubber Keypads
Silicone rubber keypads are keypad switches made from silicone rubber materials. They are used to provide tactile feedback to the user when a button is pressed and are commonly used in various consumer electronic devices such as remote controls, calculators, and keyboards.
Molded silicone rubber keypads have been used for over 30 years because customers like their 3-dimensional operating surface. The most noteworthy point about these keypads is that they come in various styles and offer multiple benefits.
Here we will compare the two basic styles with details about their available design range.
Conductive Rubber Keypad
The conductive rubber keypad comes with a puck on the backside or an in-built semi-conductive pill. The pill is made from conductive carbon particles and silicone rubber.
When the keypad is pressed, The semi-conductive pill comes into physical contact with the exposed inter-digitated conductors on the PCB. The conductive rubber keypad closes the switch, and the operation is carried out.
The pill imitates a mechanical actuator. In other words, it works by opening and closing a circuit. Keypads made of conductive rubber have easy construction, and their uniqueness makes them the most popular among keypad designers.
Non-Conductive Rubber Keypad
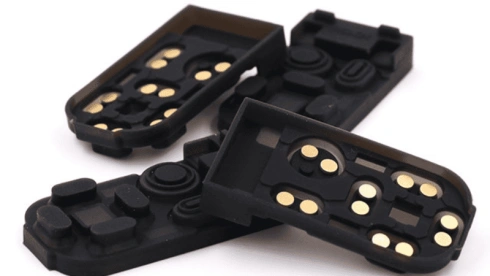
Non-conductive rubber keypad relies on a metal snap dome switch mechanism.
Metal snap dome switches, known as snap domes, are open momentary contacts. They are made of stainless steel. When used with a PCB, they provide a feeling of touch as soon as the user presses the button.
The dome gives an audible sound and a feeling of resistance when pressed. The perceived sense of touch is known as the tactile feel. As soon as the force is removed, the dome snaps back up.
Non-conductive keypads are constructed with a thicker material web between the keytops and the base. When the keytop moves, it is less prone to tearing. There is no restriction from the forcing cone, so the keytop’s movement is enhanced.
They use a metal snap dome that provides high control force and a feeling of touch. In addition, they don’t deteriorate faster as their switch cavity can be sealed.
Conductive Rubber Keypad | Non-conductive Rubber Keypad |
Contains a semi-conductive pill. | It consists of a metal dome switch. |
The pill is made of carbon particles and silicone rubber. | The dome is built out of stainless steel. |
The pill makes contact with the PCB’s conductors to close the circuit. | The metal dome switch closes the circuit. |
It uses a thin webbing material called the forcing cone between the keytop and base. | It uses a thicker webbing material. |
The thin material allows the forcing cone to flex so as not to crack. | The thicker webbing material doesn’t flex and is not prone to tearing. |
The forcing cone compresses to provide the snap feel. | The metal dome closes momentarily to give a snap feel. |
The force cone is made of soft rubber to give a perceived feeling of touch. | It uses hard rubber because the snap dome is enough to give a perceived sense of touch. |
Inquire About Our Silicone and Plastic Products!
How Molded Rubber Keypads Are Made?
Molded rubber keypads are manufactured by using high-grade molded silicone rubber. They include visible keytops into a base mat resting against the Printed Circuit Board (PCB) while a thin rubber web lies between the keytops and the base mat.
High-quality molded silicone keypads are manufactured by using two methods:
- Low-pressure compression molding process.
- High-pressure liquid silicone rubber injection molding process.
People refer to rubber keypads as molded silicone or the complete keypad assembly. The Printed Circuit Board (PCB) and sometimes the decorative bezel (keypad edges) are included in the assembly.
However, a molded rubber keypad is not a stand-alone component and should be treated as part of a large keypad assembly with interactive features.
A significant aspect of these rubber keypads is that they come in various solid and translucent colors, combining solid colors within isolated areas. Moreover, you’ll find different ways to achieve keytop legends, meaning etchings on the keycap.
- Use laser etching for translucent silicone rubber keypads that have been spray-painted with one or more coats of silicone paint.
- Use screened silicone ink for solid-color rubber keypads.
Silicone Coating Rating
The critical point is that most silicone rubber keypads are not rated for UL 94V0 flammability. To attain a flame retardant UL 94V0 rating, the material must retain its shape when exposed to high heat.
Silicone rubbers are flame resistant, which means they can withstand heat for a short duration. They can be flame retardants when added with heat blockers such as dimethylpolysiloxane gum and a platinum compound.
Only a few silicone rubber keypads require a UL 94V0 rating, saving the designer extra lead time. Besides, when the quantity is larger, the cost is lower.
Often a wear-resistant coating is used for the front surfaces of the rubber keytops, similar to polyurethane. These coating textures include matte, satin, and gloss.
Likewise, other aesthetic surface treatments are also available, including epoxy and dual-durometer keytops. Here, surface treatment is purely for aesthetics and does not affect the core design or operating parameters.
Inquire About Our Silicone and Plastic Products!
Comparison of Conductive and Non-Conductive Silicone Rubber Keypads
We can proceed further as you understand the two styles of molded silicone rubber keypads. Our next step is an in-depth comparison of non-conductive and conductive rubber keypads to decide which will work for you.
Here are the key differences between each feature:
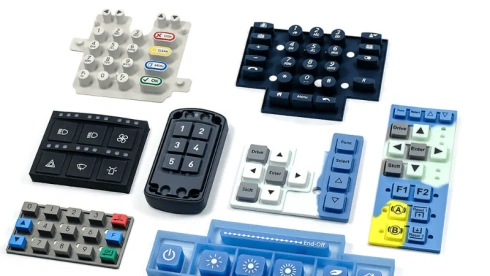
1. Switch Sealing
Switch sealing holds the utmost importance for all types of rubber keypads. It means sealing the place between two switch contacts and the air volume surrounding them.
The switch cavity of the conductive rubber keypads cannot be sealed by design because it requires the air to move freely when the keytop is pressed. These keypads could be designed to prevent the air from passing through or around the keypad.
New keypads have a less than 50 Ohms switch resistance which increases over time with use due to the contamination disintegrating the pill surface. The same pill is found on the back of conductive rubber keypads. Nevertheless, setting the switch resistance higher at 1,000 to 10,000 Ohms will slow down the disintegration process.
However, the same scenario doesn’t apply to non-conductive rubber keypads as their switch cavities can be sealed environmentally or by design.
In the case of non-conductive rubber, keypads are actuators against metal snap dome switches and do not affect the switch resistance. The PCB controls the switch resistance, the metal domes’ contact surface, and the switch cavity’s environmental seal.
2. Switch Bounce
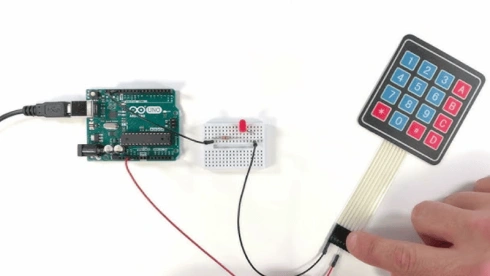
The switch bounce is the next feature to compare these two rubber keypads. It depends on the pressure applied and how the pill pushes against the PCB.
Conductive rubber keypads exhibit high switch bounce. If the force is applied on the center instead of the edge or the corner, it reduces the contact between the pill surface and the PCB. The pill is pushed against the PCB, increasing the closed contact resistance and causing a switch bounce.
In contrast, the metal snap dome switch’s design, contact surfaces, and PCB control the switch bounce in non-conductive rubber keypads. Metal domes have a far lower switch resistance than conductive rubber keypads, decreasing the switch bounce significantly.
3. Operating Force
To give tactile feedback, the conductive rubber keypads use a stressed force cone present around the edges of the keytop. However, there are practical inhibitions to the forcing cone that do not allow it to exhibit a high operating force inside the reasonable switch life cycle.
Operating force is the pressure required to press the key, and for conductive rubber keypads, it ranges between 60-200 grams.
On the other hand, a non-conductive rubber keypad’s operating force is passive, which adds very little to the switch’s driving force. The resulting operating force combines linear displacement and the metal snap dome switch’s operating pressure.
A non-conductive rubber keypad has an operating force that ranges between 240 grams to 2000 grams depending upon the design of its dome switch.
4. Intermittent Switch Operation
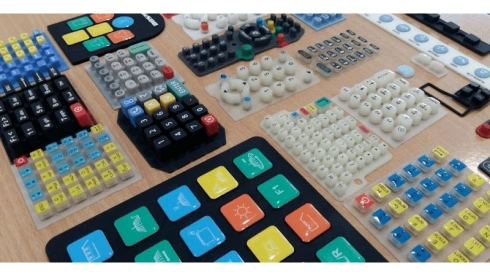
An intermittent switch operation is an irregularity that occurs only in conductive rubber keypads. This happens when the pill’s surface is coated with a non-conductive contaminator. The anomaly makes it impossible to seal the switch cavity where the pill interacts with the exposed inter-digitated conductors on the PCB.
Whenever the keytop is released, any dust or lint sucked into the switch cavity will settle over the exposed contact surfaces of the pill and PCB. This can cause deterioration of the switch over time.
In comparison, the switch cavity of the non-conductive rubber keypads can be sealed entirely. Metal snap dome switches can be designed to work in an environmentally sealed switch cavity to eliminate the contamination effect and intermittent switch operation.
Inquire About Our Silicone and Plastic Products!
5. Keytop Wobble
Keytop wobble is associated with the construction. One of the primary reasons that wobble occurs is the switch stem having a small clearance within the switch housing.
In conductive rubber keypads, if the force applied on the keytop is off-center, they tend to wobble due to the collapsing force cone surrounding the keytop. The forcing cone is the primary reason behind tactile feedback, so if it collapses, it can cause the keytop to wobble.
Some users may correlate the wobble with switch closure, even though the switch may not have been closed electrically.
On the other hand, non-conductive rubber keypads are made with higher durometer rubber that closes the switch even if the user presses the keytop off-center. Thus, there is slight imprecision in keytop movement and switch closure. Besides, non-conductive keypads don’t use force cones for a tactile snap.
6. Keytop travel
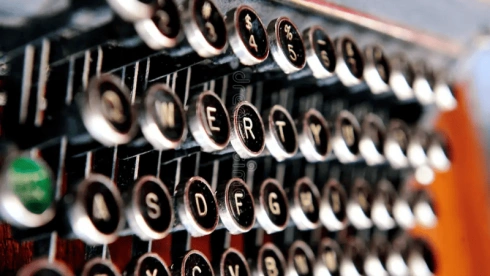
Keytop travel is the distance between its resting and pressed positions, meaning how far down the keytop can be pressed. It has a linear relationship with a tactile feel.
For conductive rubber keypads, more extended keytop travel is required so the forcing cone can collapse to give a tactile feel.
Both keytop travel and tactile feel give the impression of a closed switch. If the keytop travel is longer, it reduces the force cone’s life cycle, and if shorter, it can decrease the tactile feel while the keytop is pressed. For conductive rubber keypads, keytop travel ranges from 0.03 to 0.07 inches.
On the other hand, non-conductive rubber keypads have a higher tactile snap provided by the metal snap dome switch. They also have a higher control force. Keytop travel is limited to 0.022 or less, depending on the type of metal dome.
Assembly keytop travel could be as much as 0.4 inches depending on the dome’s diameter, operating force, and design of the rubber actuator. When pressed, the compression in the keytop adds up to the travel of the dome switch. So, the keytop travel is more significant than just the dome switch.
7. Switch operating points and over-travel
The switch operating point is the position where a key press is recognized. Over-travel is the keytop’s travel from the actuation point (operating switch point) to complete travel. You don’t need to press the keytop further when you are already exceeding its operating travel. The keytop will bottom out depending on its characteristics and operator.
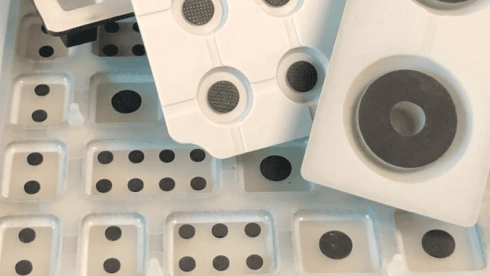
Until the pill contacts the exposed conductors on the PCB at the end of travel, conductive rubber keypads do not make electrical contact. As the keytop compresses while you press it, the switch will close, and you will feel a small amount of over-travel.
Usually, conductive rubber keypads have an operating switch point near 90% of all keytop travel, including over-travel. It is possible to ‘tease’ the keypad by slowly pressing the keytop to the point where you’ll get a tactile feel but not far enough that it will close the switch.
Non-conductive rubber keypads make electrical contact when the metal dome switch collapses. The collapsing point is near 70% of all keytop travel. When the keytop is pressed, the compression adds to the over-travel. Usually, the operating switch point is near 60% of all keytop travel.
If the non-conductive rubber keypads are adequately designed, it’s impossible to feel the snap without closing the switch when the dome collapses.
Features | Conductive | Non-conductive |
Switch Sealing | The switch cavity cannot be sealed. | The switch cavity can be sealed. |
Switch Bounce | Higher switch bounce. | Lower switch bounce. |
Operating Force | The forcing cone restricts the application of higher forces. (60-200 grams) | The operating force depends upon the metal dome’s design and is passive. (240-2000 grams) |
Intermittent Switch Operation | Often exhibits irregular switch operations because the switch cavity cannot be sealed. | No chance of irregularity because the switch cavity can be sealed. |
Keytop Wobble | If pressed off-center, the keytop will wobble because of the forcing cone. | It uses a metal dome so that even if pressed off-center, the keytop won’t wobble even if pushed off-center. |
Keytop Travel | Requires more extended keytop travel. Typical keytop travel is 0.03 to 0.07 inches. | Keytop travel is less and depends upon the dome switch. Limited to 0.022 inches. |
Switch Operating Point | The operating switch point is near 90% of the keytop travel. | The operating switch point is near 60% of the keytop travel. |
Inquire About Our Silicone and Plastic Products!
Final Verdict
While you are designing your rubber keypad project, you’ll get a choice between two basic types of silicone molded rubber keypads. Depending upon the requirements of your project, you can select conductive or non-conductive rubber keypads.
To put it simply, if your project is intended for a wet or dirty environment, non-conductive rubber keypads could be a great choice. Their switch cavities could be sealed easily to save them from contamination. If you like simple construction and unique design, then conductive rubber keypads are the most renowned among designers.
But, it’s imperative to understand the basics, structure, and differences between each type of rubber keypad. Knowing more about the limitations of each keypad style will help you make a better decision regarding which kind you require for your project.
Conclusion
Molded silicone rubber keypads have been the customers’ choice for over 30 years because of their various benefits. They come in two basic styles: conductive and non-conductive rubber keypads, which can be used to make your custom keypad. But be aware of choosing a design that will produce the desired results in a specific environment.
Looking for Rubber Keypads? Hongju Silicone Can Help You
Our rubber manufacturing includes keypads, o-rings, gaskets, seals, grommets, and silicone products. All our products are tested and certified. Hongju silicone is designed and manufactured according to customer requirements. Our experienced team can help you save time and cost if you need our assistance in keypad design.