Are you looking for a solution that can modify your product design while reducing production costs? Silicone or LSR overmolding is the transformative solution for your problems. This process provides design flexibility with durability even in the most demanding situations. Ready to discover how this technology can elevate your manufacturing processes? Let’s dive in.
What is Silicone Overmolding?
Silicone overmolding is an advanced manufacturing process that mixes liquid silicone rubber (LSR) with a substrate material to create a durable and flexible product. It includes injecting liquid silicone rubber (LSR) onto a substrate material to combine the properties of the two materials and obtain a superior product.
The manufacturing process involves using advanced techniques and machinery, such as liquid injection molding machines, to achieve precision and accuracy.
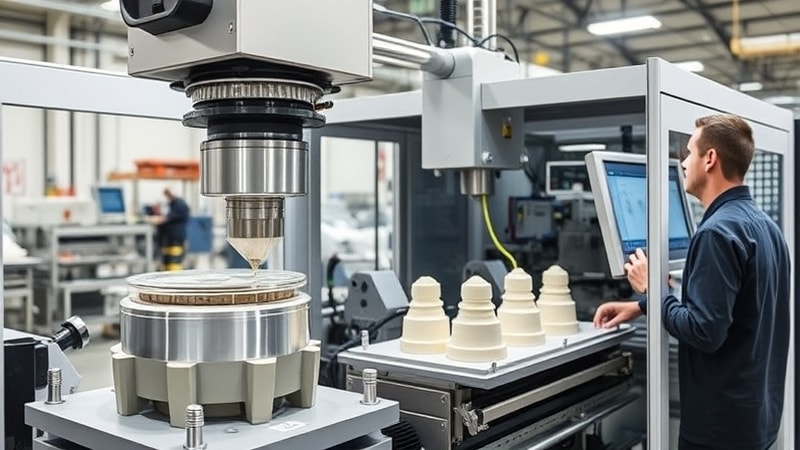
It is widely adopted across all industries to create a variety of innovative products, such as
- The medical industry uses it to create surgical instruments and implants
- Automotive components like steering wheels and custom seals are created through this method
- Protective covers and custom grips for consumer electronics are also made with silicone overmolding
It ensures the seamless integration of materials, enhancing both the performance and design possibilities of the end product.
The Silicone Overmolding Process
Silicone over-molding is a meticulous manufacturing process designed to create a durable and high-performing product by combining substrate material with liquid silicone rubber (LSR). The preparation of the substrate material, which is often plastic or metal, is the first step of the process.
Before beginning, you have to ensure material compatibility with the LSR. It is crucial to prepare the material properly so a strong mechanical or chemical bond can form during the molding process.
Then the LSR material is mixed with the catalyst to initiate the curing process. This step ensures that the silicone maintains its desired flexibility, durability, and sealing properties. This mixture is poured into the liquid silicone injection.
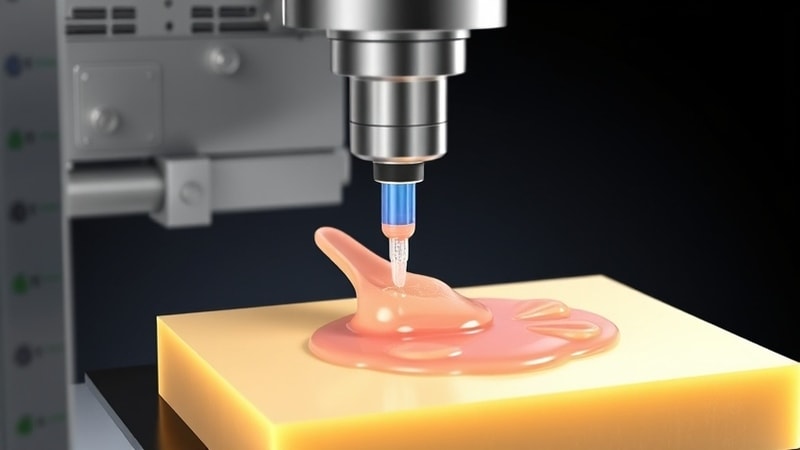
The substrate, plastic or metal, is placed within the mold cavity. The LSR is injected into the substrate material in the mold. The two materials create a bonded layer. The LSR encapsulates the substrate to offer supreme sealability. It is important to maintain control and precision during the injection molding process to ensure seamless bond formation.
One of the most significant advantages of the silicone over-molding process is its customizability. It allows manufacturers to cater to specific design considerations by creating tailored mold designs and molding techniques, altering injection parameters, and managing material properties to achieve the desired results.
The silicone over-molding process’s ability to achieve dimensional accuracy of complex shapes while integrating different materials has made it indispensable for modern manufacturing. This highly precise process is used in various industries, including the medical industry, automotive manufacturing, and consumer electronics.
Design Considerations for Silicone Overmolding
Silicone overmolding requires careful planning to achieve optimal results. Here are some of the critical design considerations to follow while creating unique parts with silicone over-molding.
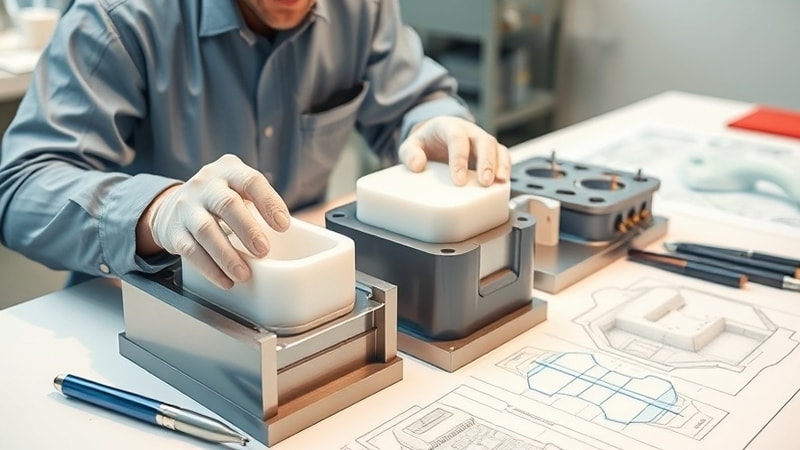
Substrate Material Selection
The design process begins with selecting the appropriate substrate material, which must be compatible with liquid silicone rubber (LSR) to guarantee a strong mechanical or chemical bonding. Metals and polymers are common substrates that can endure the molding process while remaining intact in harsh environments.
The substrate choice also has an impact on production efficiency and prices, making it an important option for industrial applications.
Creating the Mold Design
The success of the rubber over-molding process relies significantly on mold design. A well-designed mold ensures that components are precisely aligned, resulting in the required shape and finish. It is necessary to carefully analyze factors such as part ejection mechanisms, wall thickness, and draft angles.
A precise mold is very useful when producing over-molded components with complex geometries, such as those used in electronic devices, electrical components, and the automobile industry.
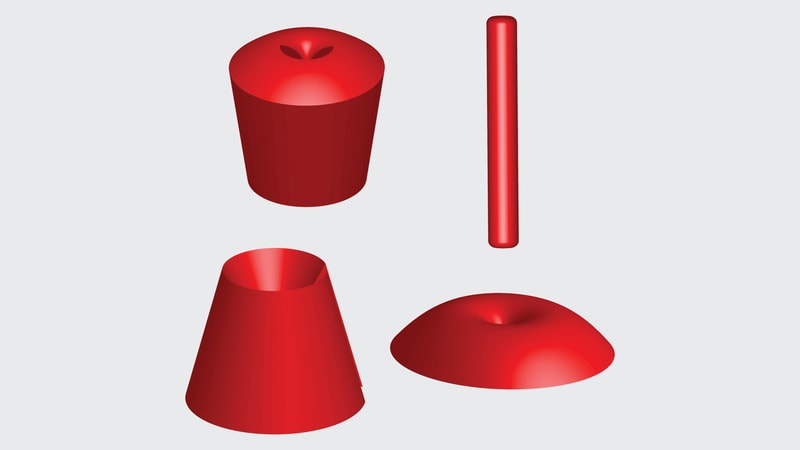
Aligning Material Properties
The qualities of the LSR material must be compatible with the product’s intended purpose. For example, chemical resistance and durability are required for industrial applications, whereas biocompatibility is required for medical equipment. By adjusting these qualities, you can guarantee that the end product has the required functionality while lowering production costs and improving overall product quality.
Properties of Silicone Rubber for Overmolding
Silicone rubber is known for its remarkable qualities, making it an ideal material for overmolding. Here are some of the qualities that have made silicone the ideal material for injection molding.
Extremely Flexible
Its extreme flexibility allows it to cope with complicated patterns and intricate shapes, making it perfect for applications requiring a high level of personalization.
High-Temperature Tolerance
Silicone rubber is extremely durable and can tolerate temperatures ranging from -55°C to over 200°C, as well as UV radiation. These properties make it an ideal choice for products that will be used in adverse conditions or outdoor settings.
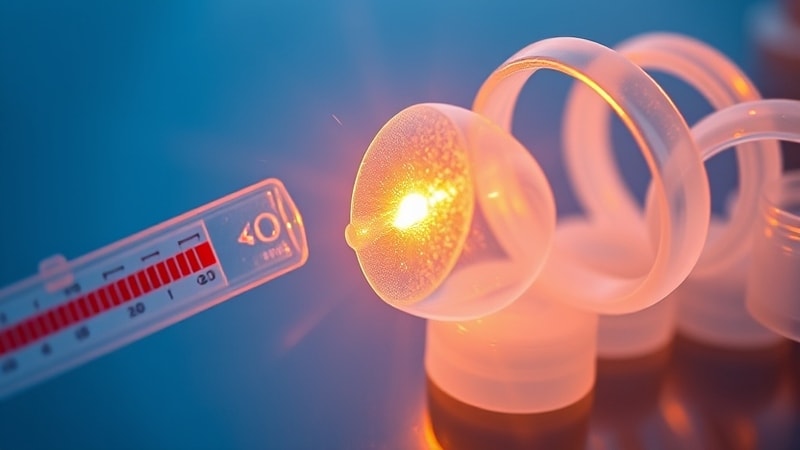
Biocompatible
One of the most prominent characteristics of liquid silicone rubber (LSR) is its biocompatibility and hypoallergenicity. This quality is especially important for medical devices and healthcare applications. LSR has been approved for direct skin contact and is resistant to microbial growth, ensuring adherence to strict medical requirements.
Chemical Resistance
Its inherent chemical resistance protects it against degradation caused by oils, solvents, and other harsh substances, making it more reliable in industrial applications.
Modifiable Characteristics
Other characteristics of silicone rubber can be modified to match certain design criteria. To obtain the desired performance, manufacturers can modify the hardness, tear strength, or flexibility. Such flexible qualities enable silicone rubber to be used efficiently in a wide range of industries, from consumer electronics to the automotive industry.
Applications of Silicone Overmolding
Silicone overmolding is a highly adaptable manufacturing method with multiple applications in a wide range of industries.
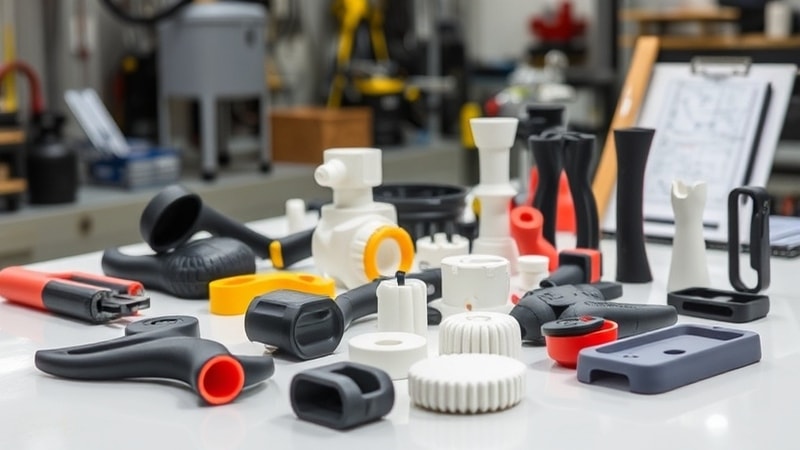
Medicine
The material’s biocompatibility, chemical resistance, and ability to form a protective layer make it excellent for applications that require both safety and durability, aka medicine. It is being used to make surgical equipment, catheters, and prosthetics.
Automotive Industry
Its resistance to severe temperatures, chemical exposure, and mechanical stress enables consistent performance in tough settings, aka the automotive industry. Hence, it is used to make automotive components such as steering wheels, gaskets, and seals. The method is also used to make personalized grips and handles, which improve the ergonomics and aesthetics of automotive parts.
Consumer Electronics
Silicone overmolding is essential for consumer electronics because it protects delicate equipment from environmental variables like dust, moisture, and UV exposure. Its versatility and durability make it ideal for products such as protective coverings, keypads, and sealing components.
Industrial Equipment
Silicone overmolding is also utilized in industrial equipment to make seals, gaskets, and shock-absorbing components that improve machinery longevity and reliability.
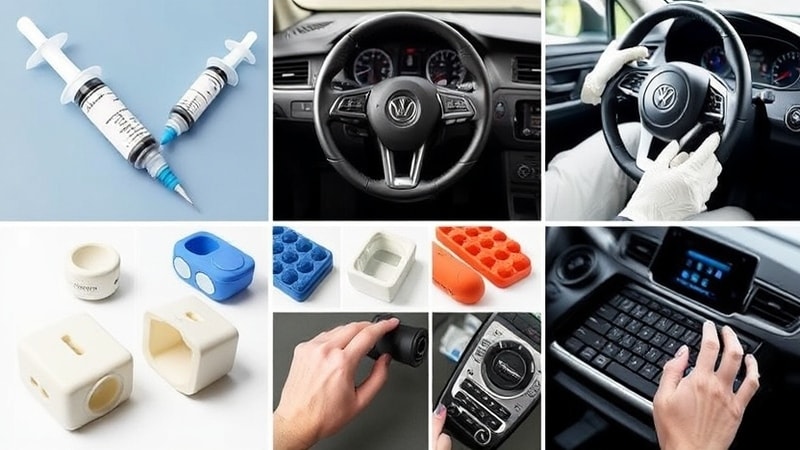
Special Parts
This technology is also effective in producing overmolded parts that combine different materials to generate complicated designs with improved functionality. Silicone overmolding achieves high-quality by creating chemical and mechanical bonding between two components. Thus effectively decreasing the need for further assembly and enhancing total manufacturing efficiency.
Benefits of the Silicone Overmolding Process
Silicone overmolding provides numerous benefits to industries that require long-lasting and high-performance components. This procedure is widely recognized as a game changer in industrial production, with benefits ranging from lower manufacturing costs to more innovative designs. Here is a breakdown of all the benefits of lsr overmolding.
Cost Reduction and Production Efficiency
One of the most significant advantages of silicone overmolding is its ability to lower total production costs. By integrating substrate materials and liquid silicone rubber (LSR) in a single molding process, producers can avoid the need for further assembly, adhesives, or fasteners.
This streamlined technique reduces material waste while increasing production efficiency, making it perfect for high-volume manufacturing.
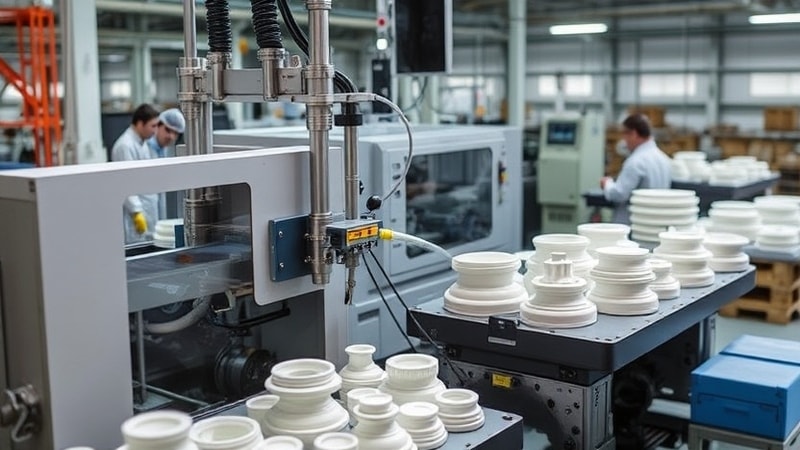
Enhanced Product Durability
The strong chemical and mechanical bonding achieved during the silicone overmolding process results in products with enhanced durability. Moreover, silicone’s intrinsic qualities, such as chemical resistance, UV resistance, as well as temperature resistance, contribute to the longevity and reliability of parts used in demanding applications.
Design Flexibility and Complex Shapes
Silicone overmolding enables manufacturers to easily create complicated shapes and customized designs. This is especially useful for industries where complex parts are often needed. The ability to incorporate various materials into a single item creates chances for unique design solutions that combine usefulness with aesthetics.
Quality Control Measures for Silicone Overmolding
Quality control is an essential part of the silicone overmolding process, ensuring that each product satisfies the required performance and safety criteria. By implementing extensive quality inspections throughout the production cycle, you can reduce the chances of defects and increase customer satisfaction.
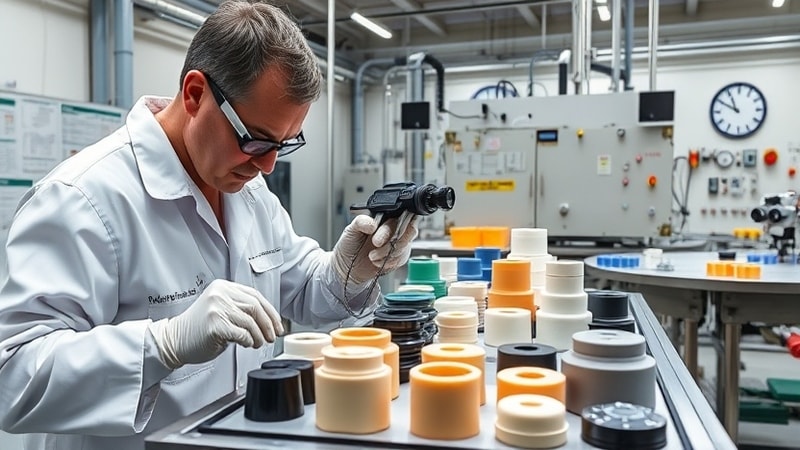
Material Inspection
The process starts with an inspection of the substrate material and liquid silicone rubber to assure compatibility and quality. The substrate must be devoid of impurities, and the LSR material must meet hardness, elasticity, and other application-specific requirements.
Testing for durability and performance.
Quality control techniques include extensive testing of the finished product to ensure its durability, flexibility, and resilience to severe temperatures and UV radiation. Chemical resistance is also tested in products where exposure to harsh substances is common, such as in the automotive and medical industries.
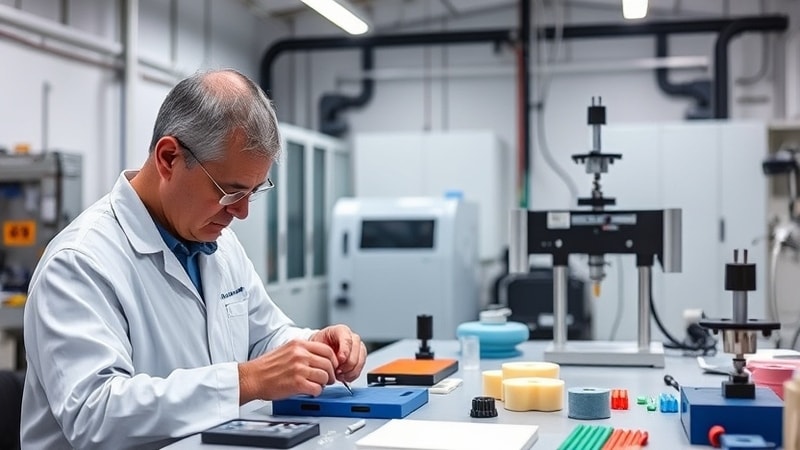
Dimensional and Visual Inspections
Dimensional inspections guarantee that the product’s dimensions meet design specifications. Whereas visual checks detect surface faults, color mismatches, and inconsistencies. These techniques are essential for applications that require a perfect surface finish.
Ensure Production Consistency
Automated systems and sensors are commonly used to monitor the overmolding process in real-time, ensuring consistent outcomes. Every step of the process, from combining the LSR material to injection molding, is examined to ensure high-quality standards are met.
Advantages of Silicone Overmolding in the Manufacturing Process
The use of silicone overmolding in manufacturing processes has created new opportunities for product development and innovation. Here are some of the benefits that have made it essential for a variety of industries.
Enhanced product Life
Products created with silicone overmolding are known for their increased durability due to the strong bond formed between the LSR and the substrate. This characteristic assures long-term performance, especially in difficult situations with severe temperatures, UV exposure, and chemical exposure.
Integration of Multiple Materials
Silicone overmolding enables the smooth integration of several elements, including metals and polymers, into a single component. This feature eliminates the need for additional assembly operations, saving time and money while increasing the structural integrity of the final product.
Enhanced design possibilities
The method offers unparalleled design flexibility, allowing for the production of complicated shapes and customized components. It supports the creation of inventive designs while maintaining functioning, whether it is for ergonomic grips, protective covers, or intricate seals.
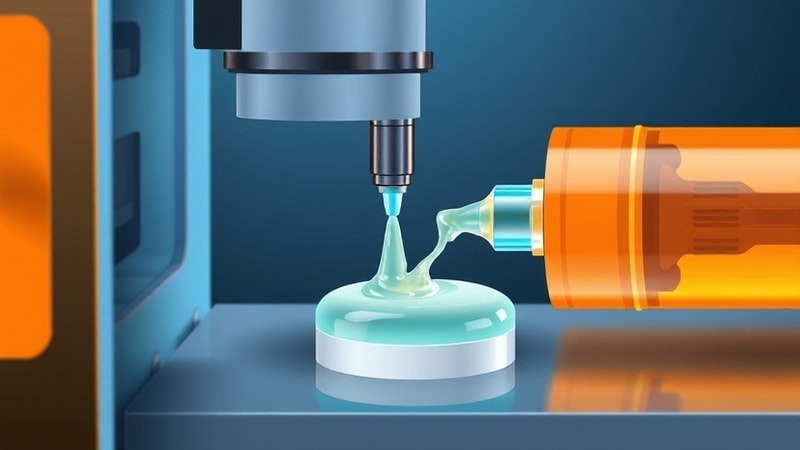
Cost and Time Efficiency
Silicone overmolding reduces manufacturing costs and accelerates production cycles by combining several production phases into a single process. This efficiency makes it especially useful for businesses that require high-volume production while maintaining quality and performance criteria.
Frequently Asked Questions
Q1. What materials can be used as substrates in silicone overmolding?
A. Metals, polymers, and various elastomers can be used as substrate materials. The key is ensuring material compatibility to achieve a strong mechanical or chemical bond between the substrate and the overmolded silicone.
Q2. How does silicone overmolding improve product durability?
A2. A protective coating is added via silicone overmolding which increases the product’s resistance to severe conditions, UV rays, and extremely high temperatures, therefore prolonging its shelf life.
Q3. What are the common challenges in silicone overmolding?
A3. A few of the difficulties of silicone overmolding revolve around making sure the silicone and substrate adhere properly, controlling the curing procedures, and dealing with intricate design elements like preserving uniform wall thickness and preventing flaws like flashing.
Conclusion
Does your business rely on silicone overmolding too? Silicone overmolding provides unparalleled advantages that have positioned it as the cornerstone for modern manufacturing, driving cost-effective and innovative solutions across a variety of industries. Now that you understand the numerous benefits, applications, and essential considerations of silicone overmolding, it’s time to explore how this innovative process can enhance your business.
Whether you’re looking to improve product durability, optimize manufacturing efficiency, or create customized designs, silicone overmolding offers versatile solutions to meet your needs.
Discover How Silicone Molding Can Work For You!
Hongju Silicone has extensive experience in custom silicone products. Contact us for a free consultation or browse through our product catalog.