A rubber compound is a raw rubber mixed with some additives in a process called rubber compounding. Rubber compounding is done to increase the performance and potential of the rubber. Industrial manufacturers perform rubber compounding to produce rubber with the desired properties.
In over a decade of real-world compounding for automotive, medical, and construction clients, we’ve seen how tuning a formula can double a component’s service life and reduce downtime-related costs by up to 30%.
Understanding Rubber Compounding: The Basics
Rubber compounding is the process of blending natural or synthetic rubber with carefully selected chemicals to achieve targeted performance properties.
In its raw form, rubber is soft and prone to wear. Compounding transforms it into a material that can withstand demanding environments—from high-temperature engine bays to ozone-rich outdoor settings.
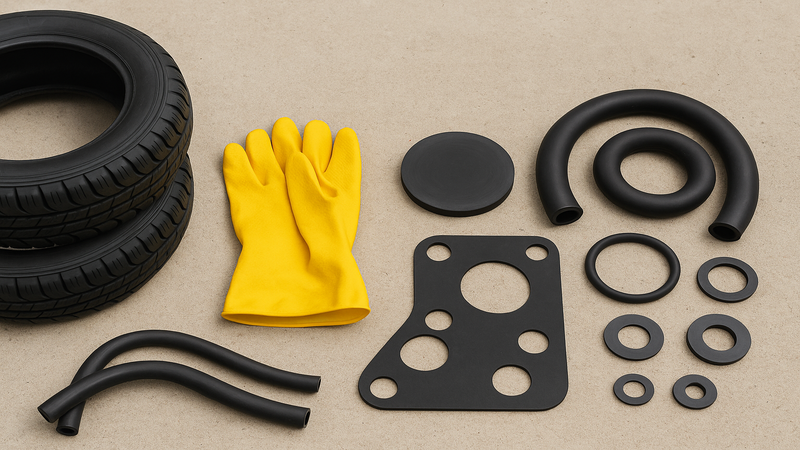
The central part of compounding is vulcanization. When rubber is mixed with additives, the compounds undergo a process called vulcanization. This chemical reaction uses sulfur or peroxide to form cross-links between rubber molecules.
Different additives are used to adjust the properties of rubber. Some additives make rubber flexible, while others add to its heat resistance properties. By selecting the type and quantity of these additives, manufacturers can produce rubber that suits their specific needs.
Depending on additive selection, the same base rubber can be tuned for high-temperature engine seals, food-grade gaskets, or offshore oilfield hoses.
Components of a Rubber Compound: Materials & Additives
Successful compounding starts with the right base polymer and additive system. It involves determining the type and ratio of additive to mix with rubber, thereby giving the desired properties to the rubber. Some of the components of rubber compounds and their purpose are given below:
1. Base Polymers: Natural vs Synthetic Rubber
The base polymer provides a compound rubber with its primary characteristics, including elasticity, resilience, and compatibility with other materials. Common base polymers include NR, EPDM, NBR, SBR, Neoprene, and Silicone—each selected based on performance needs, regulatory compliance, and cost targets.
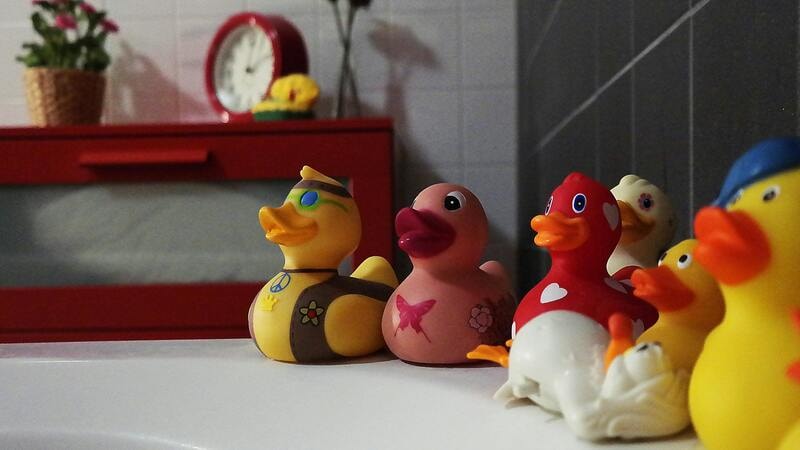
- Natural Rubber
Natural Rubber (NR), tapped from Hevea brasiliensis, delivers unmatched tensile strength (~25 MPa), elasticity, and fatigue resistance, making it the default choice for dynamic load applications like heavy-duty tires, suspension bushes, and vibration dampers.
In tropical climates, NR retains resilience where synthetics may stiffen prematurely.
- Ethylene Propylene Diene Monomer
EPDM (Ethylene Propylene Diene Monomer) is a synthetic rubber with high resistance to ozone, UV, and aging. EPDM excels in outdoor exposure, making it a top choice for roofing membranes, automotive weather seals, and HVAC gaskets—lasting over 15 years in field conditions.
- Nitrile Rubber
NBR (Nitrile Rubber) is ideally suited for use in the automotive industry, specifically in gaskets and hoses. Its outstanding oil, fuel, and chemical resistance make it the industry standard for fuel system seals, hydraulic hoses, and O-rings.
Nitrile Rubber (NBR) offers superior resistance to petroleum oils and fuels, remaining flexible at −30 °C to +100 °C, which is why it dominates in hydraulic seals and fuel hoses.
- Styrene-Butadiene Rubber
SBR balances abrasion resistance and cost efficiency, making it a workhorse for economy-grade tires and industrial mats. While SBR lacks the oil resistance of NBR, it outperforms in abrasion endurance, especially in indoor flooring.
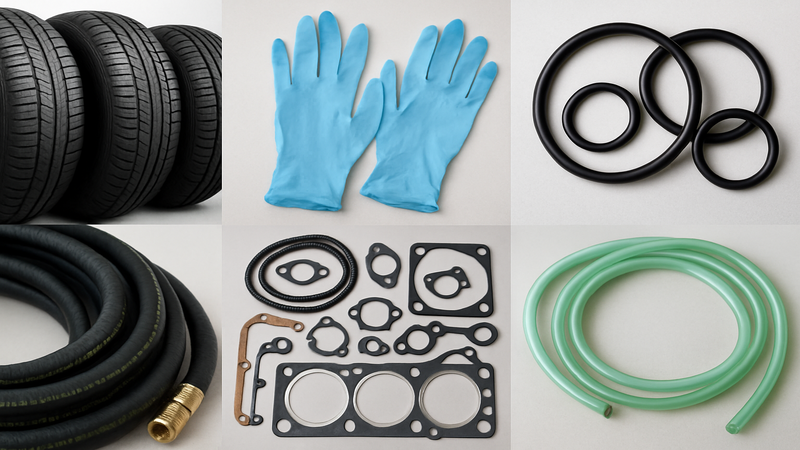
- Neoprene rubber
The other base type is Neoprene rubber, which delivers a balance of chemical resistance, moderate oil resistance, and durability. It’s widely used in marine environments, HVAC insulation, and industrial belts, thanks to its weathering and moderate oil resistance.
Neoprene’s moderate oil resistance and flame-retardant potential make it popular for HVAC duct insulation and marine hatch seals.
- Silicone rubber
Silicone rubber is another base type known for its high-temperature resistance properties. It is commonly used in medical and food-grade applications. A table comparing different rubber types is provided below:
Silicone withstands −55 °C to +300 °C, ideal for autoclave sterilization cycles in medical device production.
Type | Source | Temp Range (°C) | Flexibility | Common Use |
---|---|---|---|---|
NR | Natural | -60 to +80 | Excellent | Tires, footwear, suspension parts |
EPDM | Synthetic | -50 to +150 | Good | Weather seals, roofing, and tubing |
NBR | Synthetic | -30 to +120 | Moderate | Oil hoses, automotive gaskets |
SBR | Synthetic | -50 to +90 | Good | Conveyor belts, shoe soles |
Neoprene | Synthetic | -40 to +120 | Moderate | Gaskets, protective clothing |
Silicone | Synthetic | -100 to +230 | Excellent | Food & pharma seals, electronics |
2. Fillers
Fillers are used in rubber compounding to increase the tensile strength of the rubber. It is also added to reduce the cost of the rubber. Different types of fillers include carbon black, silica, or white clay.
Carbon black is a reinforcing filler that enhances the tensile strength, UV resistance, and abrasion resistance of the rubber. Silica, on the other hand, improves the wet grip of the rubber and is commonly used in tires and some food-grade applications.
White clay filler is used to reduce the cost and enhance the colors of rubber. The ratio of filler added determines the flexibility and stability of the rubber. Also, it affects the color and tear strength of the rubber.
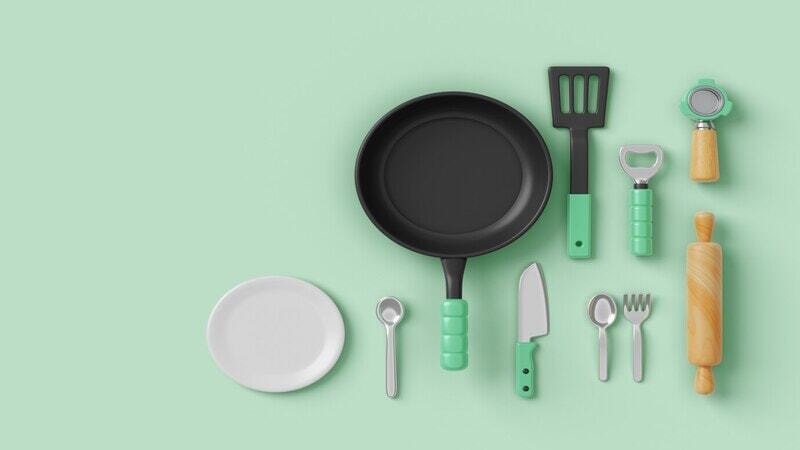
3. Plasticizers (Extender Oils)
Plasticizers are used to increase the softness, add flexibility, and reduce the viscosity of the rubber. They’re critical in applications requiring low hardness and high elongation—such as medical catheters or flexible hoses. Today, bio-based plasticizers are replacing traditional petroleum-based oils to meet sustainability goals.
4. Processing Aids
Processing aids help with mixing and molding, as well as preventing sticking. They enhance throughput in mixing lines, reduce scrap rates, and improve mold release—directly lowering production costs.
Internal mixing and open mill mixing are two standard methods used in the rubber compounding process to mix base rubbers with additives. Both these methods work differently, but processing aids are essential in both mixing methods.
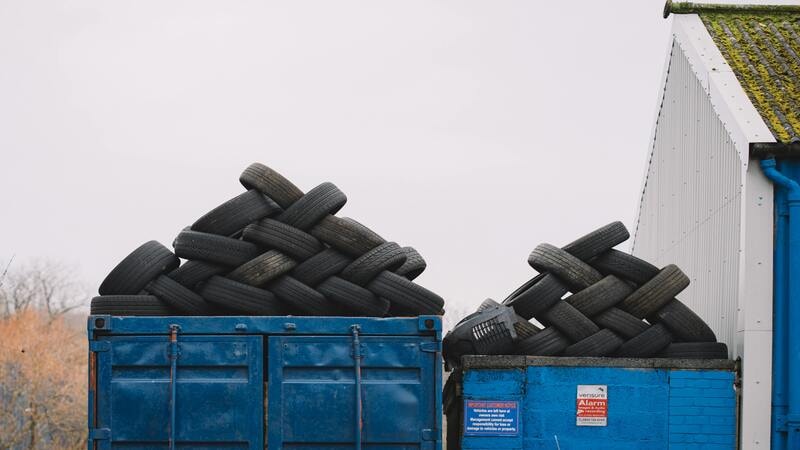
5. Antiozonants & Antioxidants
These additives increase the durability of the rubber product, making it ideal for use in outdoor or automotive applications.
Antioxidants prevent the cracking of rubber material, thus making them great for tires, gaskets, and hoses. Whereas antioxidants help prevent products from heat and oxygen degradation.
6. Scents & Specialty Additives
Scents and specialty additives don’t enhance the performance of the rubber but are widely used. The scent reduces the natural odor of the rubber and adds a pleasant fragrance to rubber products.
Special additives, such as pigments, flame retardants, anti-static agents, and electrically conductive materials, are widely used in consumer goods, including rubber toys and fitness products.
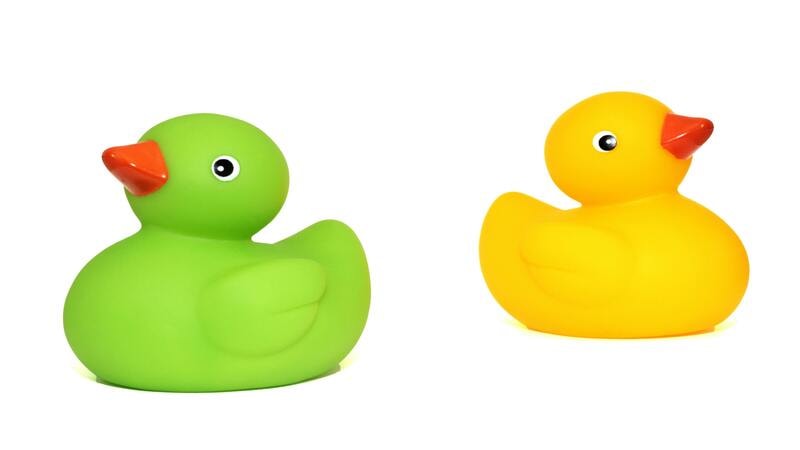
7. Curing Agents
Curing agents transform the soft rubber into a durable one by forming cross-links with the rubber. The curing agents play a crucial role in the vulcanization process.
Sulfur and peroxide are commonly used curing agents; the table below compares these agents to help industrial buyers choose the one that best suits their applications.
Curing Agent | Pros | Cons | Best For |
---|---|---|---|
Sulfur | Cost-effective, flexible | Slower cure, odor potential | NR, SBR, general applications |
Peroxide | High-temperature stability | More expensive, sensitive to mix | EPDM, Silicone, NBR, pharmaceutical use |
The Rubber Compounding Process Step-by-Step
Rubber compounding is the process of converting raw rubber into durable products. This process comprises multiple steps, and each step is discussed in detail below:
Material selection
The first and most crucial step of the compounding process is to choose the materials. Always select the material that meets your requirements.
The materials include base polymer, filters, plasticizers, processing aids, antioxidants, curing agents, scents, and special additives. Carefully analyze your flexibility, tensile strength, and resistance needs to choose the materials that best suit your needs.
Weighing and Mixing
Accurately weighing the ingredients is crucial. Only the ratio of ingredients needed should be added, as even a slight indifference can impact the performance and potential of the rubber products.
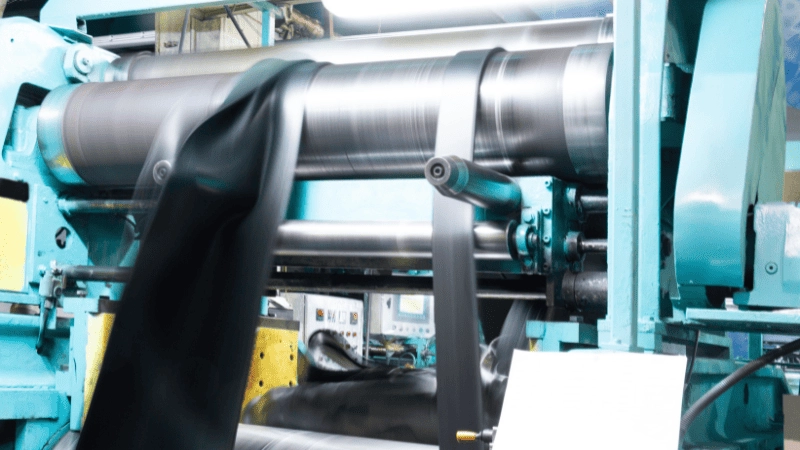
Ensure you know the ratio of ingredients required and measure the chemicals accurately to achieve the desired results. Some mixing techniques in rubber compounding are:
- Internal Mixing: This process utilizes enclosed machines, such as Banbury mixers, for high-speed, uniform blending. This type of mixing is ideal for large batches and heat-sensitive compounds.
- Open Mill Mixing: This process uses twin rollers and is slower than other methods. Still, it allows for manual control, making it often used for custom or small-batch rubber compounds.
- Tandem mixing: It combines both methods—first dispersing in an internal mixer and then refining in open mills—for precise, high-performance formulations.
Ensure you select the correct mixing technique to achieve a homogeneous blend.
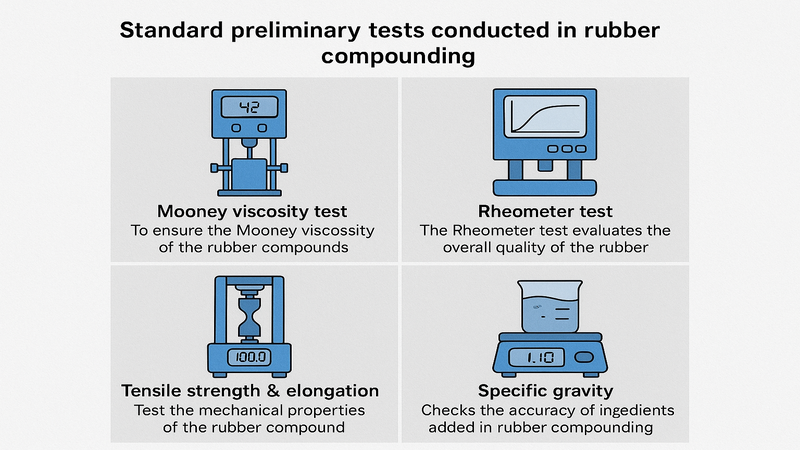
Preliminary testing
The third step in rubber compounding is preliminary testing. After mixing, the compound is tested to ensure quality and consistency.
The initial tests enable manufacturers to adjust formulations to suit their specific applications before proceeding with final production.
Some standard preliminary tests conducted in rubber compounding include:
- Mooney viscosity test: To ensure the Mooney viscosity of the rubber compounds.
- Rheometer test: The Rheometer test evaluates the overall quality of the rubber.
- Tensile strength & elongation: Test the mechanical properties of the rubber compound.
- Specific gravity: Checks the accuracy of ingredients added in rubber compounding.
Vulcanization
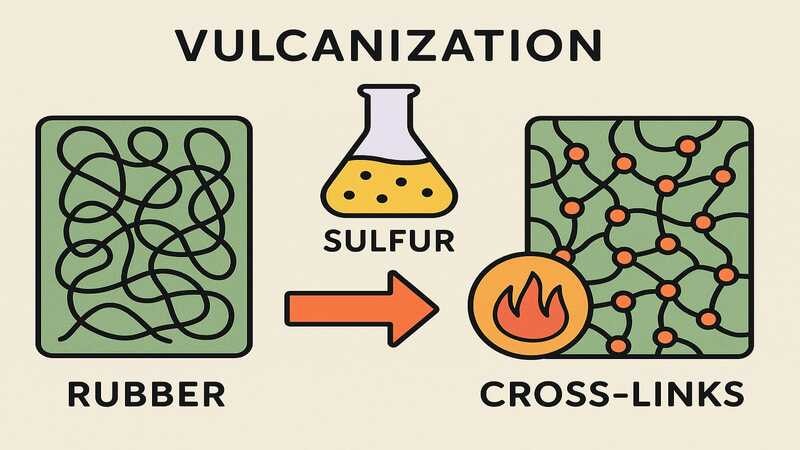
Vulcanization is the final and most crucial step in rubber compounding. In this step, the rubber gains its final properties, i.e., durability, resistance, and elasticity. The curing agents, sulfur or peroxide, form a cross-link with the rubber molecule to give rubber its final properties.
Vulcanization works under heat and pressure. The curing ingredients, temperature, and time must be selected according to the specific requirements of the material.
Quality Control and Final Testing
In the final step, the product is tested to ensure it is flexible enough to meet your needs. The final testing also tests the tensile strength, durability, heat resistance, and other features of the rubber.
Products must meet specific industry standards, including those established by ASTM, ISO, or client-specific requirements. If the quality test fails, the formulation must be modified to accommodate your specific needs.
What are Rubber Mixing Methods?
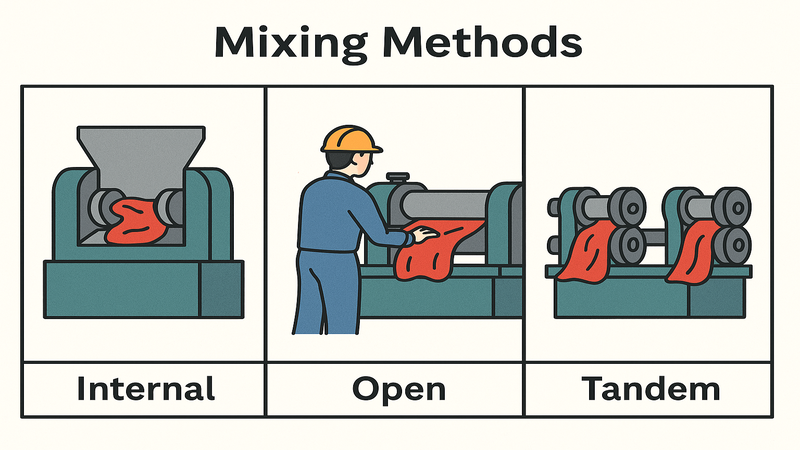
As discussed earlier, mixing is a critical step in rubber compounding formulation. This step determines the uniformity, consistency, and quality of the final rubber product. The three standard mixing methods are discussed below in detail:
Internal Mixing
This involves using enclosed and high-shear machines, such as the Banbury or Intermix mixers. This method is ideal for large-scale production and in cases where consistent quality is essential. This method is primarily used in the automotive industry to produce high-quality rubber.
The internal mixers allow easy blending of chemicals, fillers, and curing agents with a rubber base. The closed chambers contribute to making this mixing method ideal while working with heat-sensitive and highly resistant rubbers.
Open Mill Mixing
This mixing method is manual and uses two horizontal rollers that rotate in opposite directions. This process is slow, but it allows manufacturers to inspect the process visually.
Open mill mixing is ideally used for mastication, i.e., where natural rubber or synthetic rubber is softened before compounding. The open mills lack dispersion quality but are excellent for small-scale production.
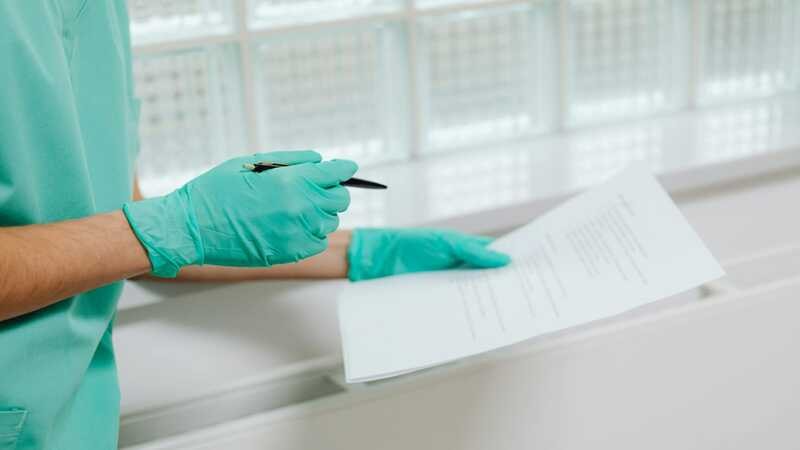
Tandem Mixing
This method combines the pros of both internal and open-mill mixing. In this mixing method, the rubber is first dispersed in an internal mixer and then transferred to open mills for distribution and refining.
This hybrid approach guarantees high consistency. Tandem mixing is suitable in cases where precision, performance, and batch customization are essential.
Industrial Applications of Rubber Compounds
Rubber compounding plays a vital role across various industries. The following are examples of how it is used in different sectors:
Automotive:
In the automotive sector, rubber compounding is used to make rubber efficient enough to use in tires, engine mounts, hoses, gaskets, and seals. In the automotive industry, rubber is compounded to be heat-resistant, oil-resistant, and abrasion-resistant.
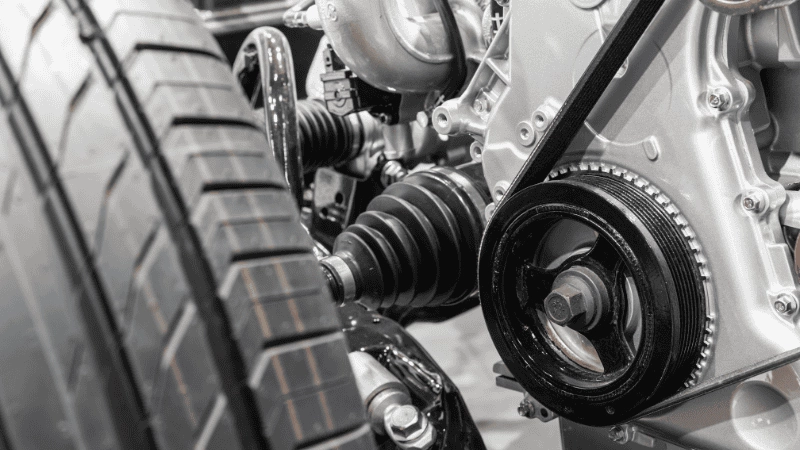
Medical:
In the medical field, rubber compounds must meet purity and biocompatibility standards. Silicone rubber or natural rubber is used in the medical industry for applications such as surgical tubing, gloves, and stoppers.
In the medical sector, rubbers are tailored to resist chemicals, maintain elasticity, and be safe for skin and body contact.
Food Industry:
The rubber products used in the food industry must be non-toxic, odorless, and compliant with FDA or international food safety standards.
Silicone rubber is particularly common in the food industry, and through the use of rubber compounding, the rubber is made resistant to temperature, grease, and cleaning chemicals.
Construction:
In the construction industry, rubber products that resist weathering, UV exposure, and mechanical wear are used. Neoprene and butyl rubber offer excellent sealing and longevity, making them commonly used in the construction industry.
Choosing the Right Rubber Compound

Choosing the right rubber compound is essential. Manufacturers must ensure that the selected compound possesses environmental resistance properties. The rubber must be durable enough to resist UV rays, ozone, and other chemicals.
The second thing to consider when choosing a compound rubber is its operating temperature range. Silicone performs well in high temperatures, whereas natural rubber is best suited for moderate temperatures.
Determine the temperature range of rubber products and select the rubber compound that best suits your specific temperature requirements.
Mechanical stress is another crucial factor to consider when choosing a rubber compound. Go for a rubber that can resist compression without breaking or losing its shape.
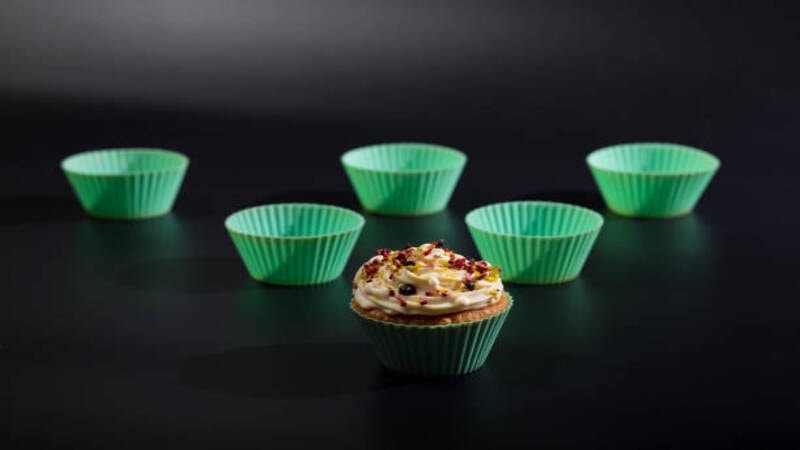
Lastly, choose a rubber that complies with industry standards, including those of the FDA, RoHS, and WRAS, to ensure safety and compliance with relevant regulations. To make an informed decision, it is advisable to consult a rubber technologist.
Material Grades: Food, Medical, Pharmaceutical & WRAS
Rubber material grades refer to the suitability of rubber for specific applications, especially those involving contact with food, medical devices, or pharmaceuticals. Each grade meets regulatory standards that ensure safety and purity.
Food-Grade Rubber
Food-grade rubber must comply with FDA 21 CFR 177.2600, which ensures that rubber won’t release harmful substances into food or beverages. These rubbers are widely used in seals, belts, tubings, and other food production equipment.
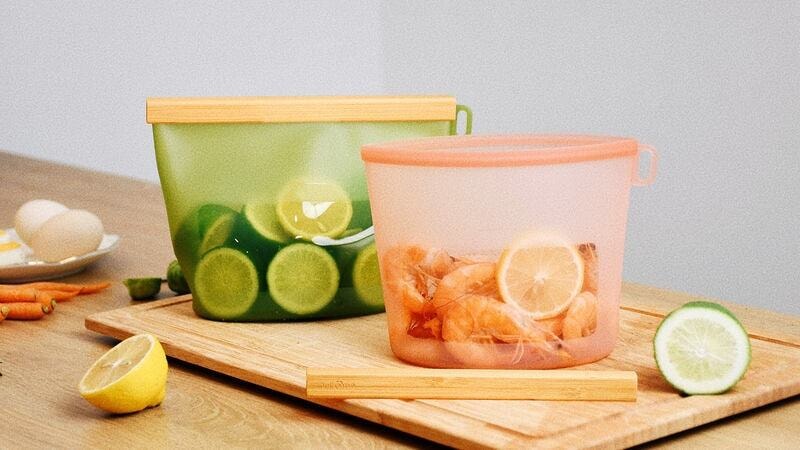
Medical-Grade Rubber
Rubber used in medical products must meet USP Class VI and ISO 10993 biocompatibility standards. These standards ensure that the products are safe even when used in direct contact with the human body.
The medical-grade rubber is often used in syringes, implants, and diagnostic devices.
Pharmaceutical-Grade Rubber
Pharmaceutical-grade rubber refers to rubber products that meet the highest standards of purity and chemical stability to prevent drug interaction. Pharmaceutical materials must comply with FDA, EP, and USP <381>/<87>/<88> standards to ensure safety.
How Rubber Compounding Tailors Performance?
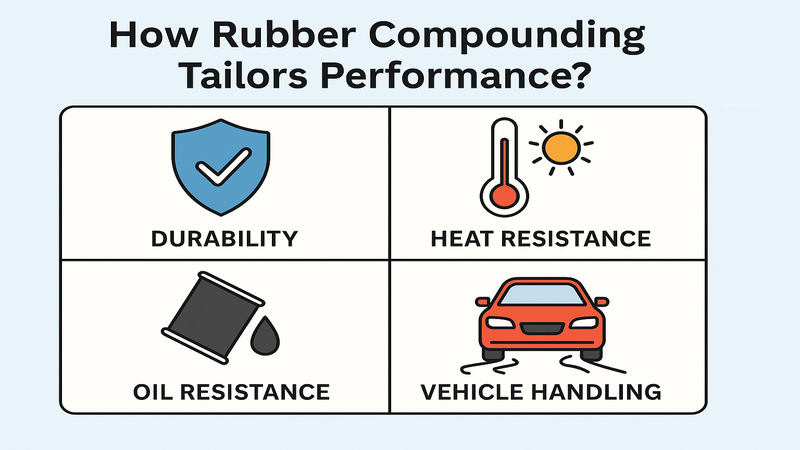
Rubber compounding is the art and science of mixing rubber with additives to improve the performance of rubber. The rubber compounding alters the performance of the rubber by enhancing its resistance to oil, abrasion, heat, and compression.
Current Challenges in Rubber Compounding (2025 Update)
Rubber compounding is currently facing some challenges; fortunately, these challenges can be easily addressed. The challenges being faced in rubber compounding include:
- Following the COVID-19 pandemic, global supply chain disruptions and geopolitical tensions have created challenges in sourcing additives, including sulfur, carbon black, and accelerators.
- Lead times have doubled in some regions.
- Prices of key materials remain elevated.
- The rising demand for sustainable formulations is prompting manufacturers to explore bio-based and non-toxic alternatives. Balancing sustainable options with performance is a challenging task.
Conclusion
Rubber in its original form is too delicate to be used in industrial applications. Rubber compounding enhances the durability of the rubber and improves its performance.
When done correctly, rubber compounding helps meet the specific requirements of various applications. It is advised that you collaborate with experienced compounders to ensure formulations are tailored to your particular needs.
Partner with Hongju Silicone for High-Quality Silicone Rubber Products
With over a decade of experience in manufacturing silicone rubber products, Hongju Silicone is here to help you with your silicone-related needs.
Our low MOQ requirement and fast delivery differentiate us from our competitors. Contact us to get customized rubber solutions tailored to your business needs now.
FAQs
Q1. What compound is rubber?
Rubber is a type of polymer compound made from natural rubber (polyisoprene) or synthetic rubbers. Rubber is mixed with additives during the rubber compounding formulation to enhance its performance.
Q2. Is Rubber chemically hazardous?
Certain rubber chemicals, such as specific accelerators, sulfur, or solvents, can be hazardous, particularly during the manufacturing process. However, once compounded, rubber products are generally safe for use.
Q3. What is the chemical for rubber compounding?
Rubber compounding utilizes various types of chemicals, including sulfur for vulcanization (cross-linking), Carbon black for strength and durability, accelerators to expedite curing, antioxidants to prevent aging, plasticizers to enhance flexibility, and fillers to control cost and properties.
You need to choose the chemical that suits the required properties of the final rubber product.