Thus, the vulcanization process came into being. The majority of the rubber that we use today comes about through the vulcanization curing process. Vulcanized rubber has a wide range of applications, including automotive tires, industrial seals, and shoe soles, among others. Let’s learn how the vulcanization process was introduced and what it does!
What is Vulcanization?
Vulcanization is a process that requires a combination of raw rubber and sulfur in a bath. The next step requires heating the combination. This enhances the strength and elasticity of the rubber compared to the original state. The most common vulcanized rubbers include styrene-butadiene rubber (SBR) and polyisoprene (natural rubber).
There is More to the Process!
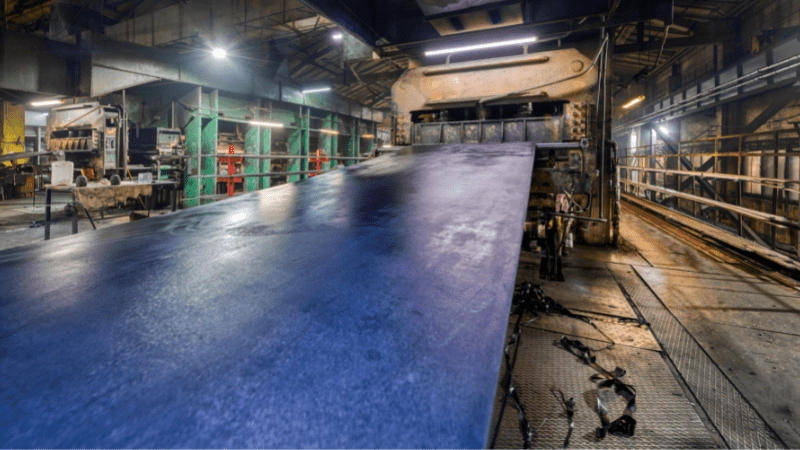
As for the vulcanization curing process itself, you will find various techniques. For instance, sulfur alone does not offer a speedy process. Hence, adding additives in the form of accelerators, activators, and retarders is vital to supplement the process. This makes the vulcanization curing process more efficient even at lower temperatures.
Moreover, additives also help reduce the amount of sulfur required in the process. This, in turn, allows for longer-lasting vulcanized rubber output with better aging and mechanical properties.
But why does the above process take place? To understand, we must learn the fundamentals of natural and synthetic raw rubber:
Natural Rubber
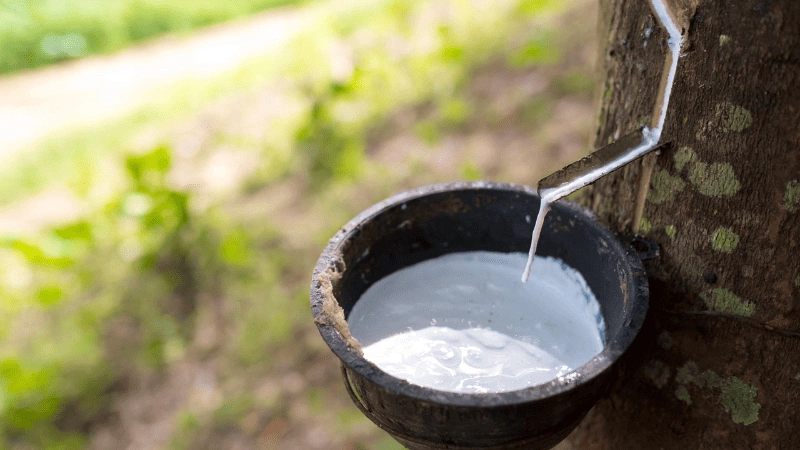
Typically, natural rubber has less odor and greater strength than synthetic rubbers. However, natural rubber cannot withstand extreme temperatures in its raw form. Moreover, natural rubber comes from the latex of rubber tree that produces rubber. While there are hundreds of rubber-producing plants, the natural rubber we use mainly comes from the rubber tree Hevea Brasiliensis.
Synthetic Rubber
Contrary to natural rubber, synthetic rubbers perform better in extreme weather conditions. Moreover, it also has a longer life comparatively. On top of that, synthetic rubbers are an excellent alternative for people who have allergies to natural rubber proteins.
Hence, around 70% of the rubber used in the USA today is synthetic. As for its origin, synthetic rubber comes from artificial polymers. These polymers are the by-products of petroleum.
So, why do we need Vulcanization? Well, both natural and synthetic rubber don’t prove to be valuable enough in their raw states. Hence, Vulcanization was introduced to turn them into more robust and resistant products.
Take the First Step:
Requst for an Inquire
Quality Meets Affordability. Inquire Now for High-Quality Products at Low Volumes.
Who Invented Vulcanization?
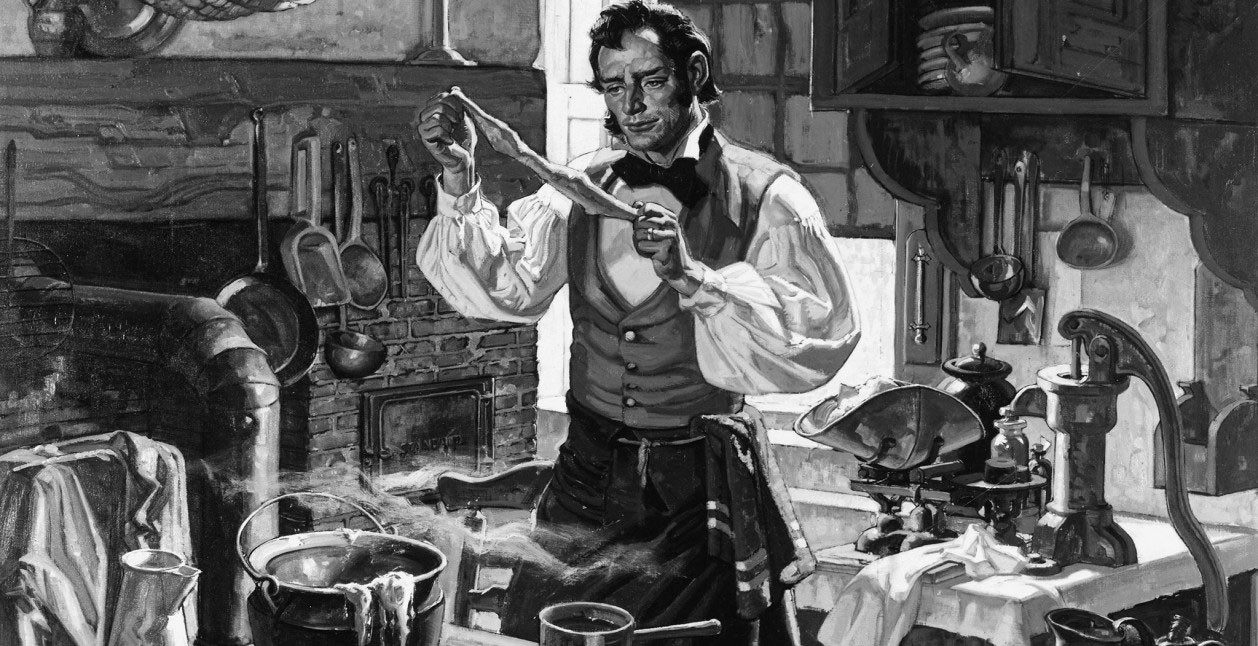
Central and South American natives have been using rubber products for centuries. However, they faced issues when the rubber product couldn’t stand extreme weather conditions. Come the 1830s. Efforts began to develop more robust and firmer rubber products.
Fast-forward to 1839, Charles Goodyear, an American, discovered the vulcanization curing process, where he added sulfur to rubber and heated it. This resulted in a more decisive rubber that also retained elasticity. Hence, the world found a solution to soft rubber in the form of vulcanized rubber, which was then used in extreme weather conditions.
Over the years, more and more experts added their contributions to the process following Charles Goodyear. Thus, we have complex, elastic, strong, and abrasion-resistant rubber products that perform far better than rubber in its raw form.
The Vulcanization Process
Now, let’s shift our focus to the vulcanization curing process, which consists of multiple steps.
Step One:
Firstly, rubber or synthetic rubber in its raw form is added to a sulfur bath. This bath also contains additives that help speed up the process. Moreover, manufacturers also add color pigments at this stage if they want the final rubber product to be a particular color.
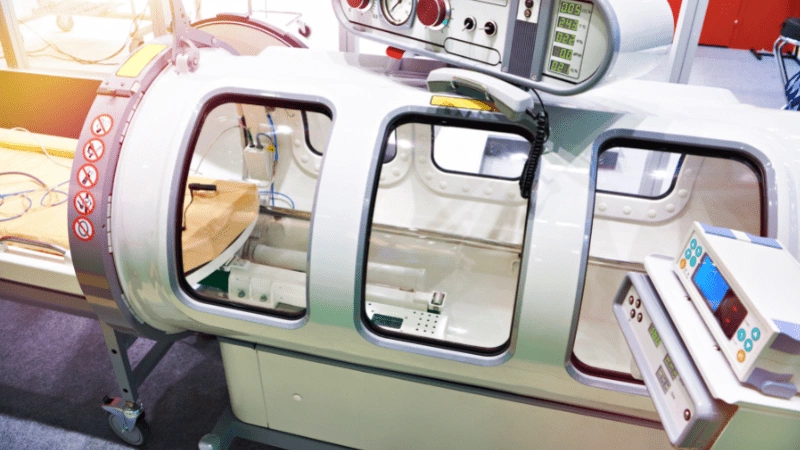
Step Two:
Once everything is in order, it is time to mold the rubber in the desired shape. However, since adding sulfur and other additives makes it stronger and more elastic, molding the vulcanized rubber isn’t easy.
Step Three:
As a result, heat comes in contact with the mixture, speeding up the process and making it easier to mold the rubber. For this, the temperature goes as high as 300 to 400 degrees Fahrenheit. After reaching this temperature level, the molded vulcanized rubber must be removed from the chamber and left to cool.
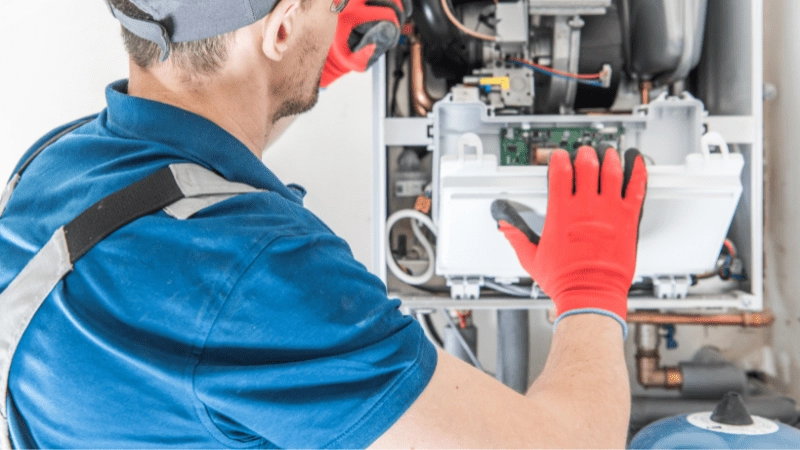
Vulcanization Additives
As discussed, the vulcanization curing process requires a curing agent. Since traditional times, sulfur has been used as a joint curing agent. Every part of sulfur requires approximately 100 parts of rubber. However, since sulfur does not speed up the process, manufacturers often use additives such as fatty acids and metal oxides. The most common metal oxide is zinc oxide.
Take the First Step:
Requst for an Inquire
Quality Meets Affordability. Inquire Now for High-Quality Products at Low Volumes.
What is Vulcanized Rubber?
Vulcanized rubber is classified by the category of elastomers. This type of rubber goes through the bio-chemical process, vulcanization, to make it more durable. For this, sulfur and other additives are added to the milky latex from the rubber tree and then heated. The result produces a much stronger rubber with multiple applications in our daily lives.
As for the uses and benefits of vulcanized rubbers, they are countless. We will discuss both sections separately to give you a better idea of how vulcanized rubber has changed how we implement and use rubber products.
Uses of Vulcanized Rubber
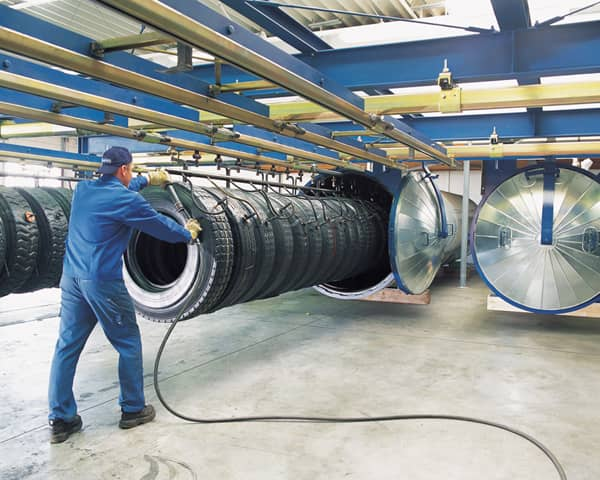
Vulcanized rubber is typically better protected against abrasion than traditional rubber. Vulcanized rubber can be used in a myriad of industries. You can find them in almost every other product that you use. Even the laptops we use have rubber feet to prevent slips. Perhaps, the most popular use for vulcanized rubber is in the tire industry. All the vehicle tires you see on the road use vulcanized rubber with the addition of carbon black to add greater strength.
However, the tire industry isn’t the only one that uses vulcanized rubber. Many other industries prominently use rubber products. These include rubber hoses, shoe soles, erasers, shock absorbers, O-rings, seals, rubber feet, insulation pads, rubber gaskets, grommets, conveyor belts, etc.
Benefits of Vulcanized Rubber
Even though Vulcanization shrinks the solid rubber, it still does more good than harm. For instance, it makes the rubber more complex and less prone to deformations. On top of it, the rubber also gains more tensile strength allowing it to retain its original shape even under high pressure. Here are some further standout benefits that rubber curing vulcanization offers:
- Excellent Abrasion Resistance and Oxidation Resistance: adding additives makes natural or synthetic rubber more resistant to oxidation and abrasion. Hence, it becomes more useful in outdoor conditions.
- Enhanced Electrical Insulation: another benefit of rubber vulcanization includes electrical insulation. Since the rubber becomes more challenging and firmer, it prevents electrical flow, making it an excellent insulator.
- Low Water Absorption: the less stickiness and more firmness also help keep any liquids out. Thus vulcanized rubber also leads to low water absorption, making it great for sealing products.
- High Tensile Strength: this allows the rubber to retain its original shape even after being stretched. Therefore, it makes it more durable and longer lasting. As a result, it minimizes replacement costs since the rubber lasts quite a long time.
- Resilience to Extreme Weather Conditions: this was the main reason why Vulcanization was sought after. Thus, today vulcanization turns rubber into a highly resilient material that can withstand extreme cold and scorching weather conditions.
- Organic Solvents Resistant: Vulcanization also enables rubber to be used in applications with organic solvents. Previously this was an issue since raw rubber was too fragile to withstand any solvent.
What about the Eco-Friendliness of Vulcanized Rubber?
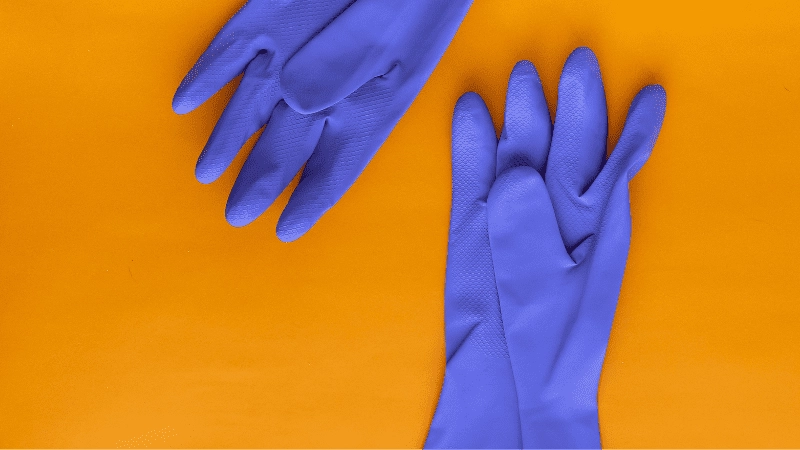
Vulcanized rubber offers more resistance to decomposition as compared to natural raw rubber. However, studies have shown the possibility of biodegradation of vulcanized rubber. For this, a hot composting bin must be used.
Additionally, despite being resistant to decomposition, vulcanized rubber brings more good to the environment. How? Well, refurbishing and repurposing of vulcanized rubber products happen worldwide. As a result, they hardly ever go to waste. A good example involves using old rubber tires as livestock matt or asphalt.
Take the First Step:
Requst for an Inquire
Quality Meets Affordability. Inquire Now for High-Quality Products at Low Volumes.
Conclusion
To conclude, the vulcanization curing process has changed how we use rubber products today. It has revolutionized the rubber industry, allowing rubber products to play critical roles in almost every other industry. Hence, you will come across various business opportunities, especially given the product’s uses, benefits, and environmental friendliness.
Get Top-Of-The-Line Products From Hongju
Listen up if you run a rubber products business and need to proliferate. At Hongju, we cater to a broad customer base with an even greater demand for synthetic rubber or natural rubber products. Our motto is premium, whether it’s our products or service. Learn more today by getting in touch with our sales team. Time to take your business to new heights!