Are you unsure of the sealing solution for your project and want a reliable alternative? You should consider silicone rubber gaskets and seals for ideal sealing. All the information you need to choose the right seal for your project is included in this guide. Whether you’re in automotive, construction, or manufacturing, by the end you will have discovered the perfect sealing solution for your needs.
Introduction to Gasket Materials
Gasket material is the basic substance used to create the gasket or seal. The ability of a gasket to create a reliable seal between two mating surfaces, prevent leaks, and maintain system integrity depends on the type and quality of the material.
Rubber is the most sought-after gasket material due to its high flexibility, durability, and adaptability. A rubber gasket compresses under pressure and fills any irregularities between the surfaces, ensuring the formation of a tight seal.
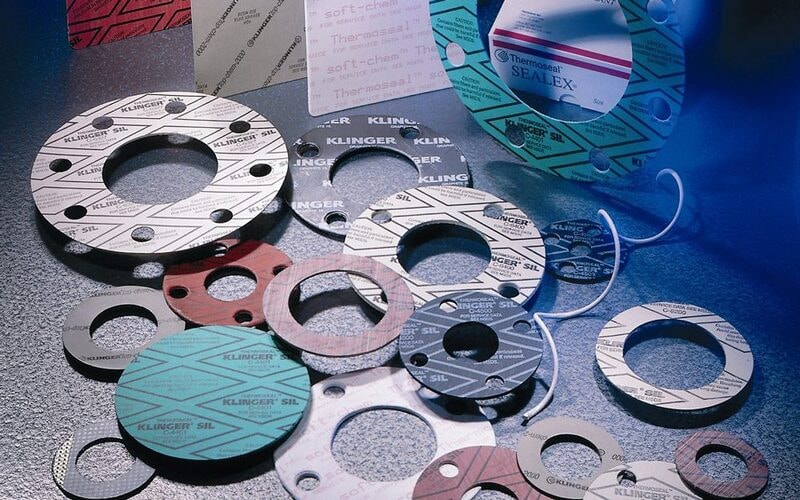
Gaskets and seals are indispensable across all industries, including automotive, oil and gas, food and beverage, and construction, for maintaining the functionality and efficiency of equipment. However, there is a specific gasket material that fulfills the needs of each industry. Let’s discover the variety of materials and the reason behind their use.
Gasket Materials and Applications
Gaskets and seals are used in almost all industries. There are many types of gaskets, and many different types of materials are used to make them. Depending upon the conditions of functionality of your project the material and type of gasket changes. Let’s explore the types of gasket materials and their best-suited applications.
Rubber Gaskets
The most famous kind of gaskets are made from synthetic rubber. There are many kinds of rubber gasket materials including silicone, EPDM rubber, NBR, and FKM. The rubber is highly flexible and chemically resistant. Moreover, they are ideal for dynamic conditions (seals between two moving parts).
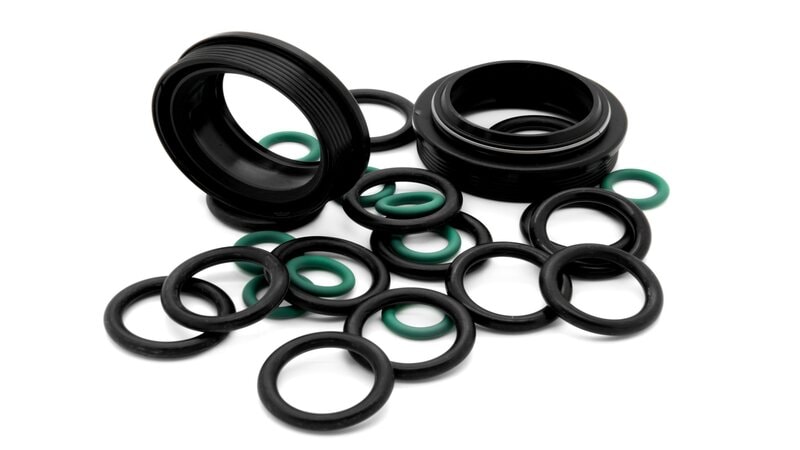
However, some types of rubber offer limited durability in extreme temperatures. They are a popular choice for industrial and commercial sealing. Some examples include the use of pipe flange gaskets to prevent leaks in piping systems under high pressure.
Moreover, they are often used to seal moving parts in machinery to prevent fluid escape as they create a pressure-sensitive adhesive. Since rubber gaskets are chemically resistant, they resist corrosion when exposed to harsh chemicals, making them a good option for the chemical processing industry and HVAC systems.
Metal Gaskets
Metal gaskets are known for their strength and durability. The most common materials to make metal gaskets include stainless steel, aluminum, and copper. Metal gaskets are exceptionally resistant to high pressure and temperature. Thus, they are often used as reliable sealing solutions in engine seals, turbines, and high-pressure pipelines.
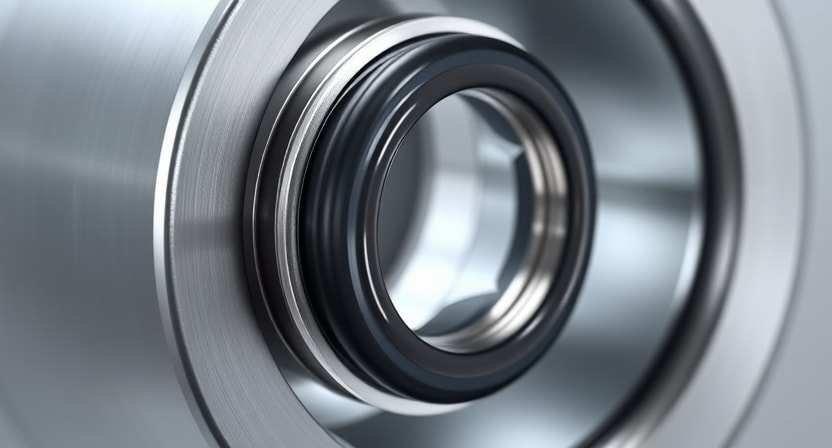
Despite their advantages, metal gaskets have several drawbacks. They are less flexible than other materials, which may limit their usefulness in dynamic sealing applications. Furthermore, their production costs might turn out higher because of the usage of premium materials. However, their extensive resilience to harsh circumstances makes them essential for key industrial systems.
Non-Metal Gaskets
Non-metal gaskets are often made of graphite, fiber, and ceramic, making them ideal for static sealing applications. These gaskets are extremely heat-resistant and work well in high-temperature situations like boilers and furnaces. Their ability to maintain an effective seal under extreme heat settings makes them the ideal choice for specialized industrial applications.
However, they are delicate and therefore unsuitable for dynamic applications involving movement or heavy loads. Despite this limitation, their low cost and unique heat-resistant qualities make them ideal for applications needing chemical resistance.
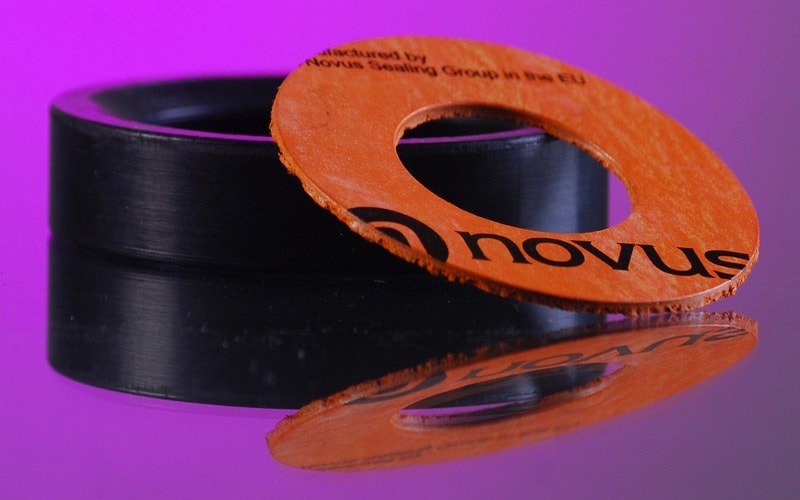
Composite Gaskets
Composite gaskets combine materials like PTFE coatings and laminated layers and harness the best qualities from multiple materials. These gaskets perform well in a variety of applications, including medical devices, food processing equipment, and corrosive environments.
Their features like oil resistance and abrasion abrasion resistance ensure long-term durability in harsh environments. On the flip side, composite gaskets are more expensive due to their sophisticated production procedures. They also necessitate specialist knowledge for production and installation.
Selecting the Right Gasket Material
There are many factors that need to be considered while selecting the right gasket material. Only the right gasket can achieve a reliable seal, providing integrity to your system. You have to consider factors like operating temperature, pressure, ozone resistance, and chemical compatibility.
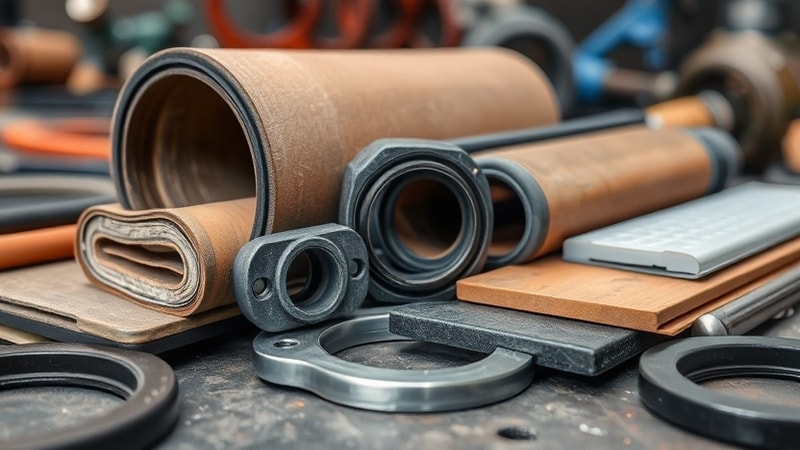
If one thing matters more than the gasket material, it is partnering with a trustworthy manufacturer. Partnering with an experienced gasket manufacturer can ensure access to expert guidance, high-quality materials, and custom solutions tailored to your specific requirements.
Rubber Seal and Gasket Materials
Rubber gaskets and seals are essential in industries requiring reliable sealing solutions. There are a variety of rubber materials available on the market, each one tailored for specific applications. The rubber material is differentiated based on factors like temperature resistance, chemical exposure, and environmental conditions.
Silicone rubber is known for its excellent high-temperature tolerance and chemical resistance. Silicone gaskets and seals are widely used in food processing and medical industries. The EPDM (Ethylene Propylene Diene Monomer) excels in outdoor applications due to its exceptional weather, ozone, and UV resistance.
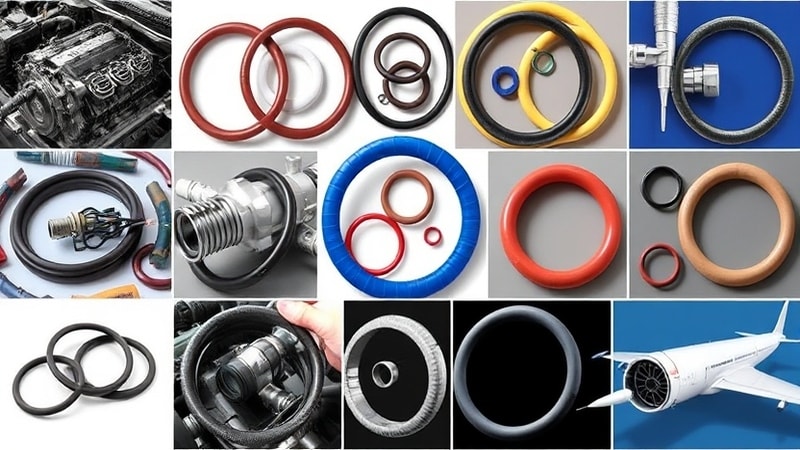
The Nitrile Rubber (Buna-N) is highly resistant to oils and fuels; thus it is employed in most automotive and industrial applications. Neoprene is another versatile material offering moderate oil resistance, along with heat and weathering resistance, making it suitable for HVAC and marine applications.
Viton rubber offers superior chemical and heat resistance and is usually reserved for harsh environments such as chemical processing plants. Lastly, natural rubber is also used in gaskets for its high flexibility and tear resistance. It is also scuff-proof, thus utilized in flooring, mats, and conveyor belts.
Here is a comparison table for all materials
Material | Temperature Range | Chemical Resistance | Durability | Common Uses |
---|---|---|---|---|
Silicone Rubber | -60°C to +300°C | Excellent resistance to a wide range of chemicals, including acids and bases. | High | Food processing, medical equipment, and applications requiring high-temperature stability. |
EPDM | -40°C to +120°C | Excellent resistance to weathering, ozone, and UV exposure; good resistance to steam and polar substances. | Moderate to High | Outdoor seals, weatherstripping, and applications exposed to environmental elements. |
Nitrile Rubber | -20°C to +108°C | Good resistance to oils and fuels; not suitable for applications involving ozone or weathering exposure. | High | Automotive gaskets, fuel systems, and oil-resistant applications. |
Neoprene | -30°C to +120°C | Moderate resistance to oils and weathering; suitable for applications requiring a balance of properties. | Moderate | HVAC systems, marine applications, and general-purpose gaskets. |
Viton (FKM) | -20°C to +204°C | Superior resistance to a wide range of chemicals, including fuels, oils, and solvents; excellent high-temperature stability. | Very High | Chemical processing, aerospace, and applications involving exposure to harsh chemicals. |
Natural Rubber | -60°C to +220°C | Limited chemical resistance; not recommended for use with oils, fuels, or solvents. | Moderate | Vibration dampening, conveyor belts, and applications requiring high elasticity. |
Gasket Types and Their Applications
There are many different types of gasket shapes depending upon their applications.
Sheet Gaskets
Sheet gaskets are created by punching specific shapes out of flat, thin material sheets. They are cost-effective and easy to install, making them ideal for applications with low to moderate pressures and temperatures.
Solid Material Gaskets
Solid material gaskets are made from and cannot be punched out of sheets. These gaskets are designed to endure high temperatures and pressures, making them suitable for demanding industrial environments.
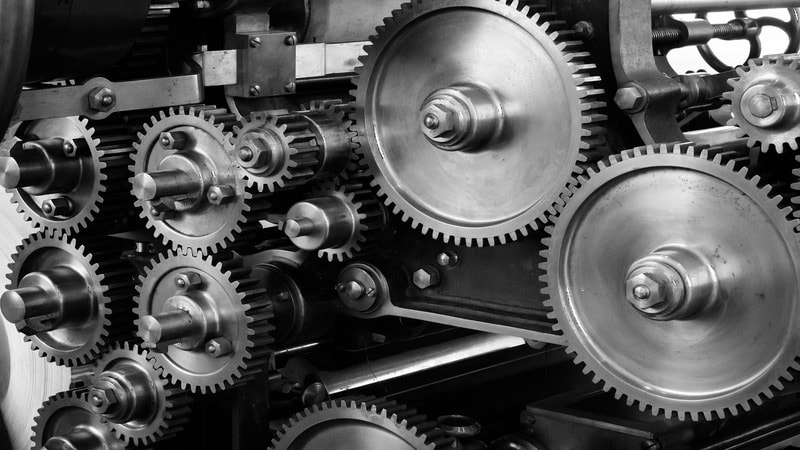
Spiral-Wound Gaskets
Spiral-wound gaskets combine metallic and filler materials. The filler material provides effective sealing, while the metal offers structural integrity.
Metal Reinforced Gaskets
Metal-reinforced gaskets have a strong metal core that prevents pressure seals and a soft core that ensures exceptional sealing. These gaskets are known for their durability and chemical resistance and are widely used in high-temperature and high-pressure applications, such as the chemical and petrochemical industries.
Gasket Standards and Certifications
There are certain international and industry specific standards that verify the quality of a gasket. ISO standards ensure uniformity and quality across gasket materials. ISO 3601 focuses on O-ring material specifications, while ISO 2230 provides guidelines for the proper storage of rubber products to maintain performance.
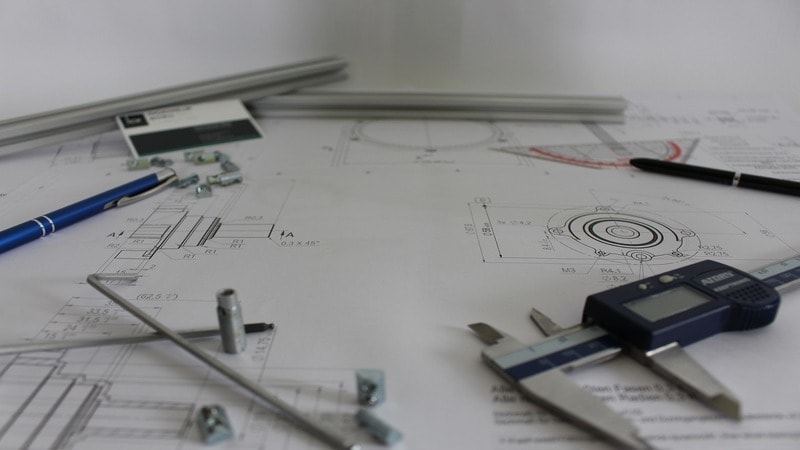
ASTM standards provide classification and testing protocols for gasket materials. ASTM D2000 specifies rubber material properties, and ASTM F104 classifies gasket materials based on performance and composition.
Certain industries require particular certifications for gaskets. FDA rules ensure that food-grade gaskets are safe for use in food and pharmaceutical applications, whereas API standards are crucial for gaskets used in oil and gas processing.
Frequently Asked Questions
Q. What are some challenges in gasket application?
Seal failure is one of the most common challenges in gasket applications. It often results from improper installation, material incompatibility, or extreme conditions. Ensuring proper alignment, regular maintenance, and selecting durable materials can prevent leaks.
Q. What are the latest innovations in gasket materials?
The industry is advancing with eco-friendly gaskets made from biodegradable or recycled materials, smart sealing technologies for real-time leak detection, and renewable elastomers, combining sustainability with superior performance.
Conclusion
Gaskets play a crucial role in ensuring operational efficiency and safety across various industries. They are the sealing hands that keep your machine running smoothly and efficiently.
Informed decisions always lead to better outcomes, so go through the guide before you select gasket material for your project.
Ready to enhance your sealing solutions?
Hongju Technology is an expert in producing high-quality gaskets for diverse industries. We also specialize in delivering customized solutions tailored to your business needs.
Request a free consultation today and let us help you find the right fit for your specific application.