At Hongju Silicone, we understand the importance of this shift and are committed to providing our customers with the necessary resources and knowledge to navigate this change successfully. In this detailed guide, we will explore the reasons behind the transition from PC to PP in furniture making, highlighting the benefits and practical applications of PP material in the industry.
Understanding PP and PC Materials
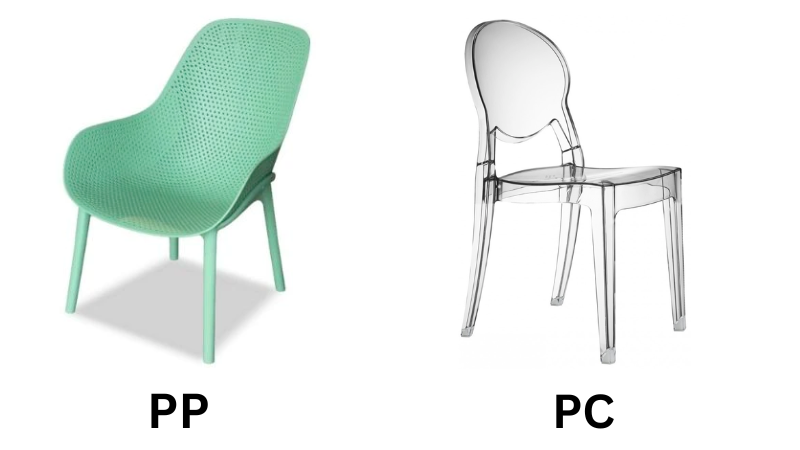
Polycarbonate (PC) and polypropylene (PP) are two common plastics used in various industries, including furniture making. Each material has its unique properties and applications, making them suitable for different purposes.
Polycarbonate (PC) is a type of thermoset material known for its high-temperature resistance and excellent impact resistance. PC is often used in the production of robust and durable plastic parts that need to withstand higher temperatures and external pressures. However, the use of chlorinated solvents in the processing of PC can have adverse environmental impacts.
On the other hand, polypropylene (PP) is an additional polymer that has gained popularity in the furniture industry due to its good chemical resistance, low melt viscosity, and lower melting point compared to PC. The low melt viscosity of PP makes it ideal for injection molding, a common manufacturing process used in furniture making. Additionally, PP is resistant to most chemicals and has a good balance of toughness and flexibility, making it a versatile material for various applications in the furniture industry.
The Rise of Polypropylene in Furniture Making
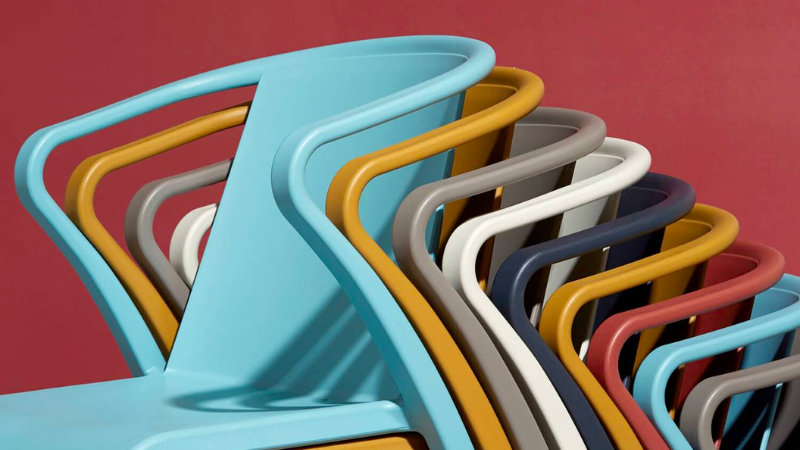
The furniture industry has seen a significant shift towards using polypropylene (PP) as a preferred material over polycarbonate (PC). This trend can be attributed to various factors that position PP as a superior option for furniture manufacturing.
- Cost-Effective Alternative: Polypropylene offers a more cost-effective solution for manufacturers. Being one of the most common plastics, PP is widely available and less expensive than PC, making it an attractive alternative for those aiming to reduce production costs while maintaining quality.
- Enhanced Flexibility and Lightweight Design: Moving from cost to design flexibility, PP is renowned for its malleability and lightweight nature. This quality enables manufacturers to experiment with innovative and creative designs, offering furniture that is not only visually appealing but also practical and comfortable. These design possibilities open up new avenues for the industry to explore, ultimately benefiting the end user.
- Environmental Benefits: In addition to its cost and design advantages, PP is an environmentally friendly option compared to PC. As a thermoset material, PP can be recycled and repurposed, effectively reducing the amount of plastic waste generated during the manufacturing process. This aligns with the industry’s growing emphasis on sustainable and eco-friendly practices.
- High Performance in Furniture Applications: From an application standpoint, polypropylene shines due to its excellent chemical resistance and high impact resistance, making it a prime candidate for durable furniture parts. Its low melt viscosity makes it suitable for injection molding, a preferred method for producing intricate plastic parts efficiently and cost-effectively. Moreover, PP’s resistance to high temperatures ensures that the final furniture product can withstand diverse environmental conditions, thus extending its lifespan.
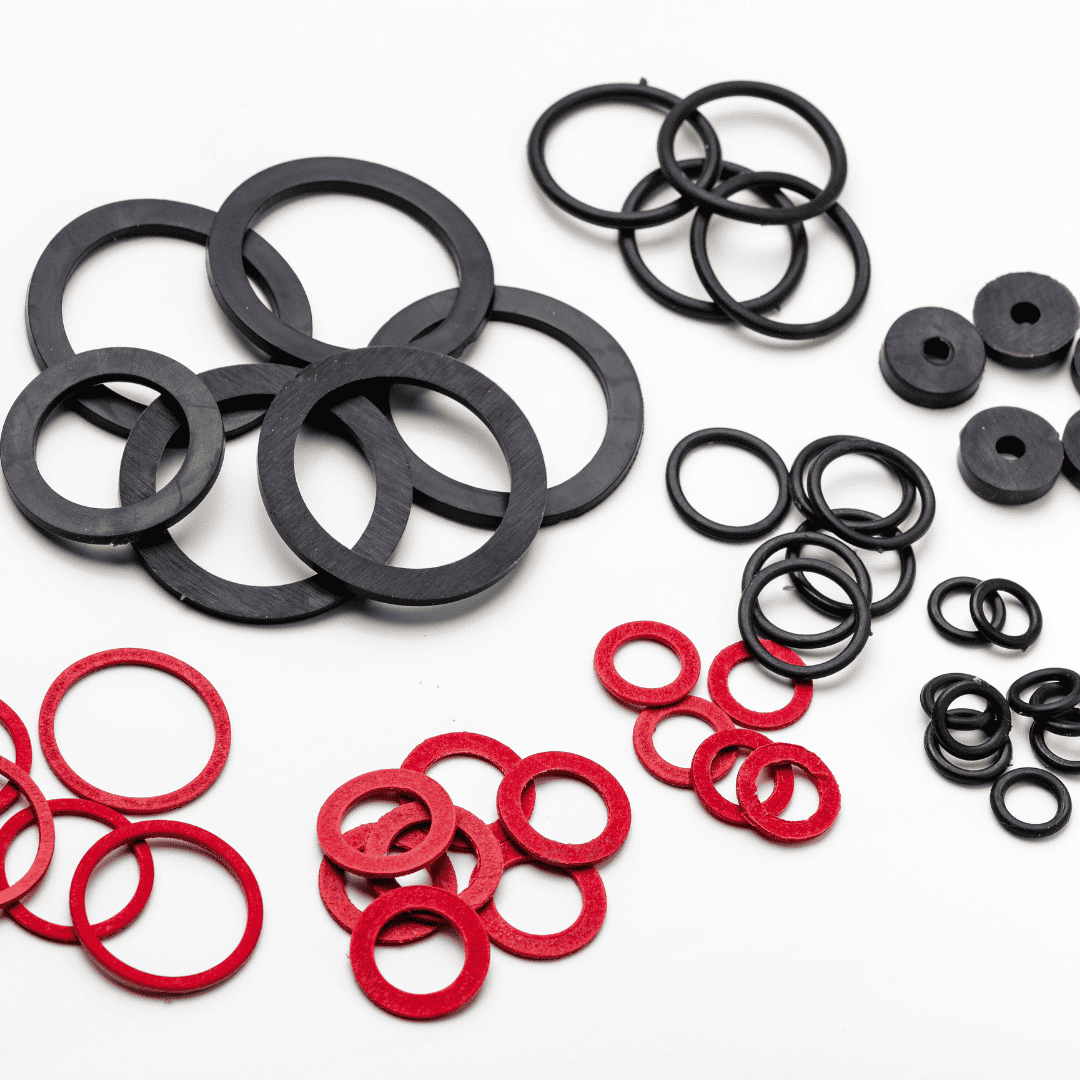
Send Your Inquiry Now!
Quality Meets Affordability. Inquire Now for High-Quality Products at Low Volumes.
Comparative Analysis of PC and PP in Furniture Manufacturing
In order to provide a clear comparison between polycarbonate (PC) and polypropylene (PP) in furniture manufacturing, let’s take a look at the following table:
Criteria | Polycarbonate (PC) | Polypropylene (PP) |
---|---|---|
Chemical Resistance | Moderate | Good |
Melt Viscosity | High | Low |
Melting Point | High (155-165°C) | Lower (160-166°C) |
Impact Resistance | High | High |
Cost | Higher | Lower |
Design Flexibility | Moderate | High |
Weight | Heavier | Lighter |
Environmental Impact | Requires chlorinated solvents for processing | Does not require chlorinated solvents; recyclable |
From the table, it’s evident that PP offers several advantages over PC in the context of furniture manufacturing. PP’s good chemical resistance, low melt viscosity, and lower melting point make it a versatile material that is easier to process and mold. Furthermore, PP is more cost-effective and environmentally friendly than PC. The lightweight nature of PP also makes it a preferred choice for furniture that is easy to transport and handle.
In conclusion, while both PC and PP have their respective benefits, polypropylene stands out as a more suitable material for furniture manufacturing, given its unique properties and advantages in terms of cost-effectiveness, design flexibility, and environmental impact.
Best Practices for Transitioning to PP
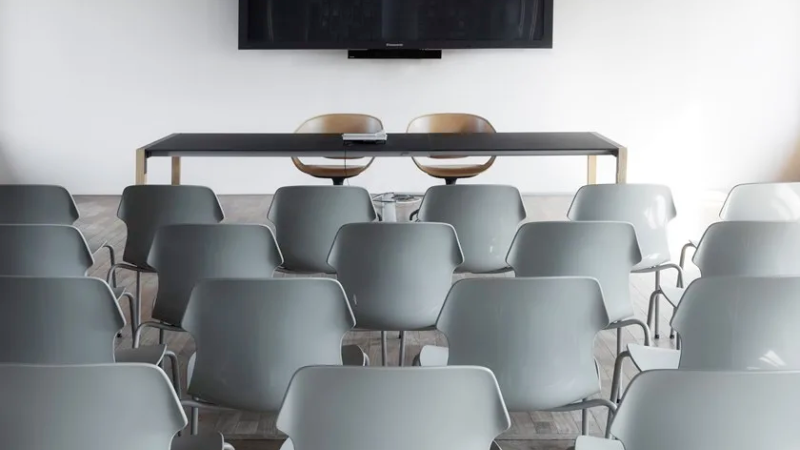
The shift from polycarbonate (PC) to polypropylene (PP) in furniture manufacturing can be a significant change. Here are some best practices to ensure a smooth and successful transition:
- Conduct Thorough Research and Testing: Before making the switch, conduct extensive research and testing to understand how PP will affect your specific products. This will help you identify any potential challenges and find the best ways to mitigate them.
- Leverage the Right Technologies: Take advantage of the latest technologies, such as machine learning and augmented reality, to optimize the processing and molding of PP. These technologies can also assist in creating intricate designs and patterns that might not be possible with traditional methods.
- Consult with Material Experts: Work with material experts and suppliers, like Hongju Silicone, to gain insights into the best practices for using PP in furniture manufacturing. They can provide valuable advice on how to maximize the benefits of PP while minimizing any potential drawbacks.
- Invest in Training: Invest in training for your team to ensure they have the necessary skills and knowledge to work with PP. This is crucial as the properties and processing methods of PP can differ significantly from PC.
- Focus on Quality Control: Implement stringent quality control measures to ensure that the PP furniture meets the required standards. This is vital as any issues with quality can have a significant impact on your brand reputation.
- Adapt Your Marketing Strategies: Update your marketing strategies to highlight the benefits of PP furniture, such as its environmental friendliness, cost-effectiveness, and versatility. This will help to attract new customers and retain existing ones.
- Monitor Market Trends: Stay updated on the latest market trends and consumer preferences to ensure that your PP furniture remains relevant and appealing to your target audience.
By following these best practices, furniture manufacturers can successfully transition from PC to PP and reap the numerous benefits that this versatile and cost-effective material has to offer.
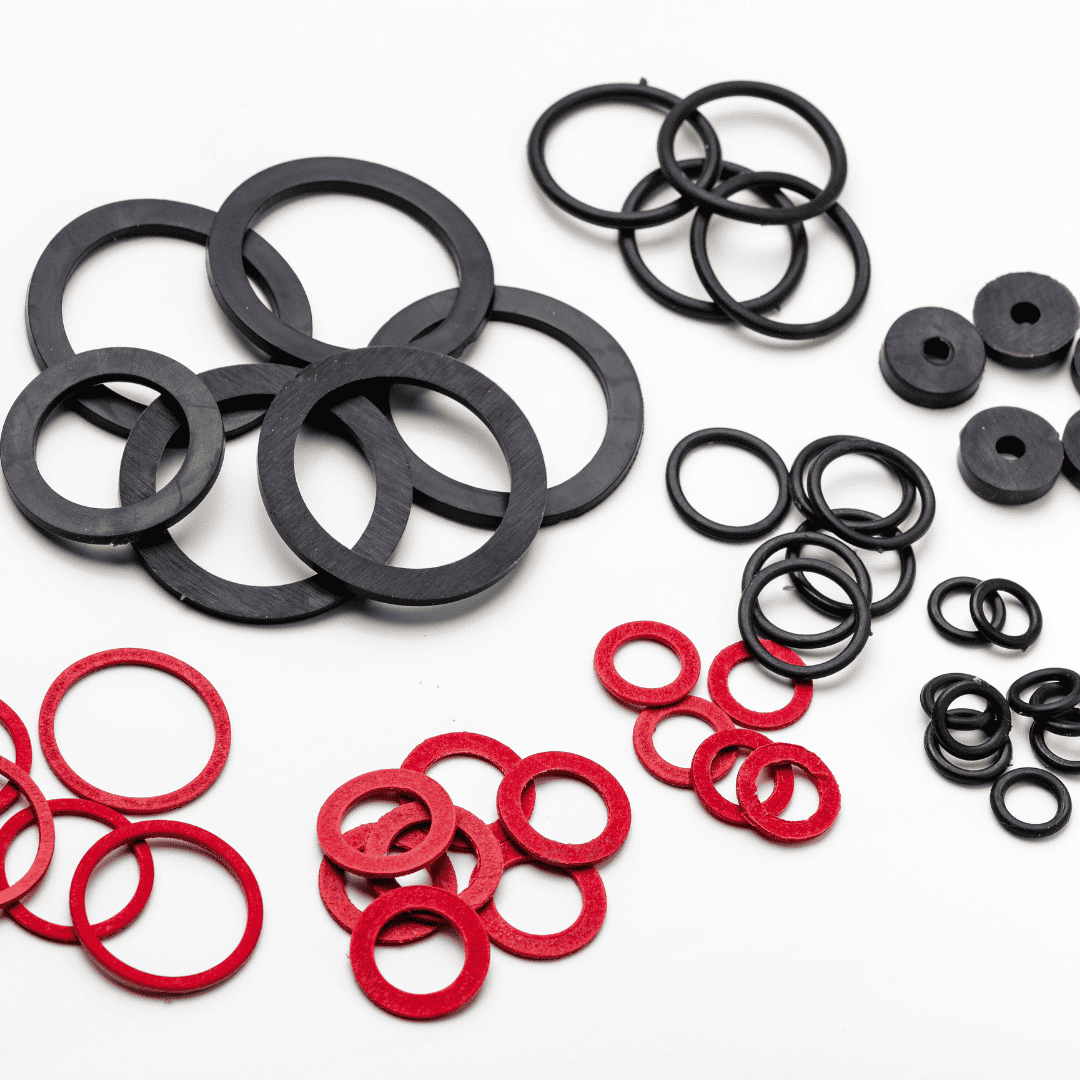
Send Your Inquiry Now!
Quality Meets Affordability. Inquire Now for High-Quality Products at Low Volumes.
Case Studies: Successful Transitions from PC to PP
At Hongju Silicone, we have been privileged to support numerous furniture manufacturers in their successful transition from polycarbonate (PC) to polypropylene (PP). Here are some notable case studies that demonstrate the tangible benefits of making this switch.
Company A: Outdoor Furniture Line
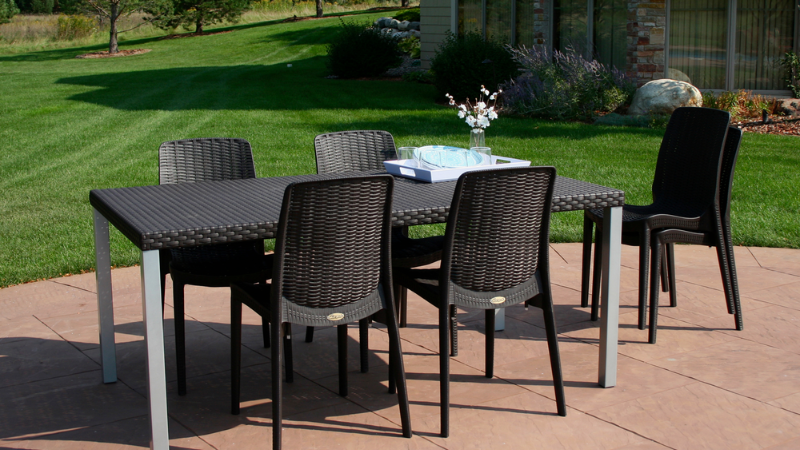
Company A approached us when they were exploring ways to reduce production costs for their line of garden chairs. Our team at Hongju Silicone provided them with custom silicone solutions that perfectly complemented the PP material they switched to. The result was a 30% reduction in production costs, enhanced chemical resistance, and a product that was lighter and easier to transport. The PP garden chairs, now backed by Hongju’s silicone enhancements, gained significant market traction, leading to increased sales and higher customer satisfaction.
Company B: Office Furniture Collection
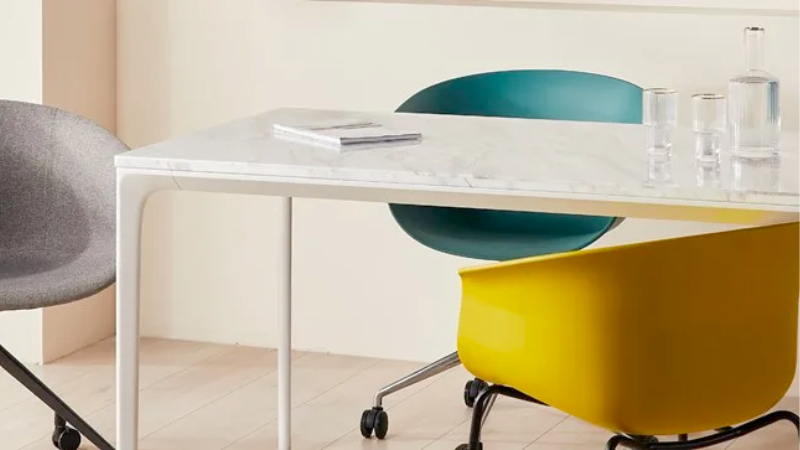
When Company B decided to revamp its office furniture line, they chose PP over PC to achieve more flexibility in design. Hongju Silicone stepped in to offer specialized silicone components that added to the modern aesthetic and ergonomic functionality of their new range of office chairs and desks. The synergy between PP and our silicone solutions not only elevated the product quality but also allowed Company B to price its products more competitively. This strategic move has since helped them carve out a larger market share and grow their customer base.
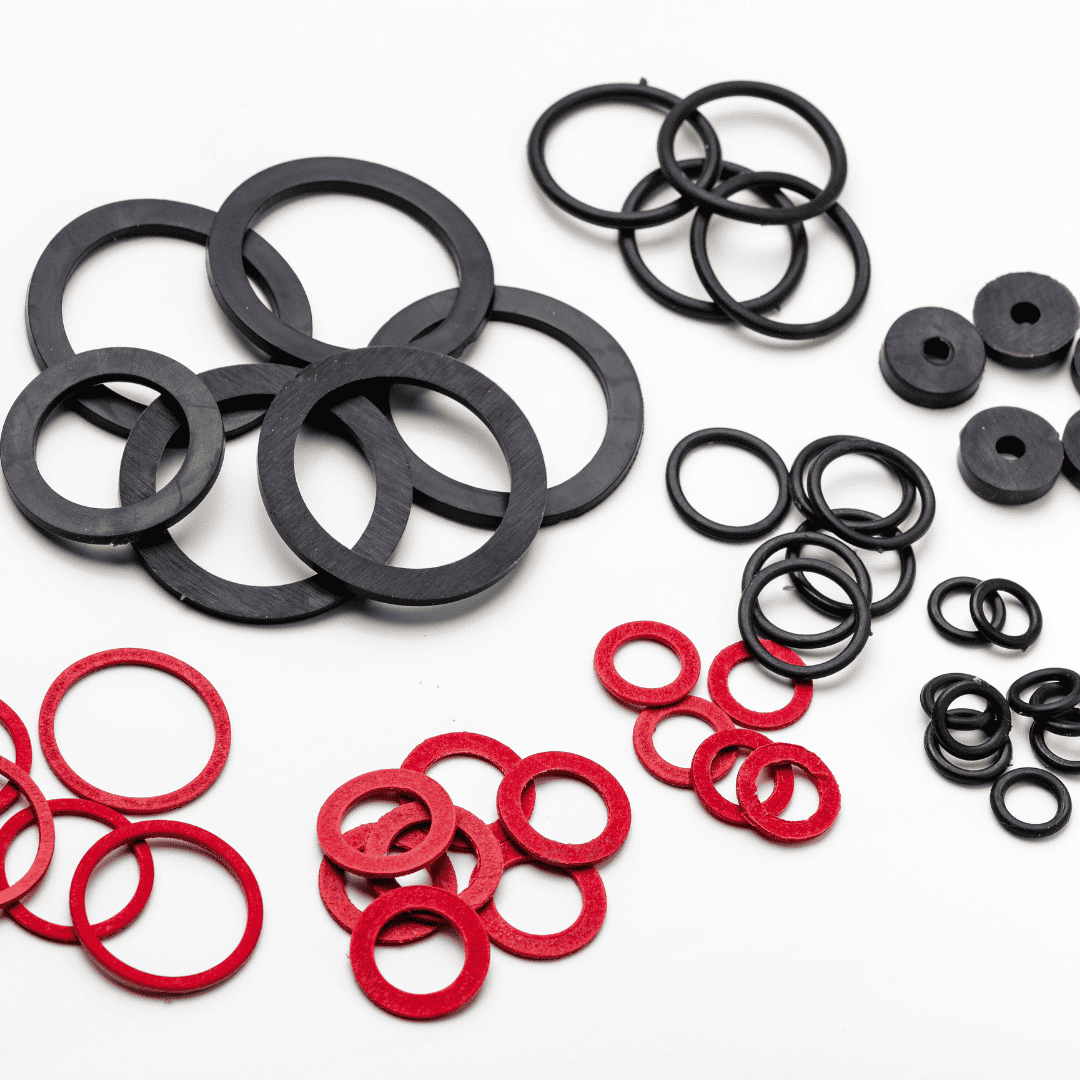
Send Your Inquiry Now!
Quality Meets Affordability. Inquire Now for High-Quality Products at Low Volumes.
Conclusion
In conclusion, the transition from polycarbonate (PC) to polypropylene (PP) in the furniture industry signifies a positive shift towards more sustainable, cost-effective, and versatile manufacturing processes. With PP’s advantageous properties such as low melt viscosity, good chemical resistance, and high impact resistance, it stands out as a superior choice for furniture manufacturing.
Buy High-Quality PP Plastic from Hongju
Hongju Silicone is committed to supporting this transition by providing tailored silicone rubber solutions that complement PP’s properties, ultimately enhancing the final product’s quality and performance. By embracing PP and leveraging the right technologies and expert guidance, furniture manufacturers can thrive in today’s competitive market.