This article covers the benefits of rubber prototypes and how to create them. Kindly read along.
What is a Rubber Prototype?
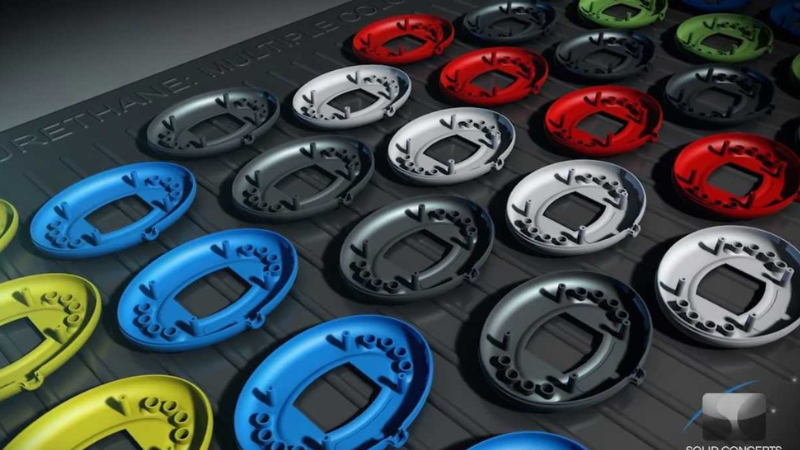
A rubber prototype is a sample or model that fits a project’s requirements before its design phase. You can use this model in similar environments to the project environment to ascertain its performance and identify potential problems before mass production.
Why is Rubber Prototype Important?
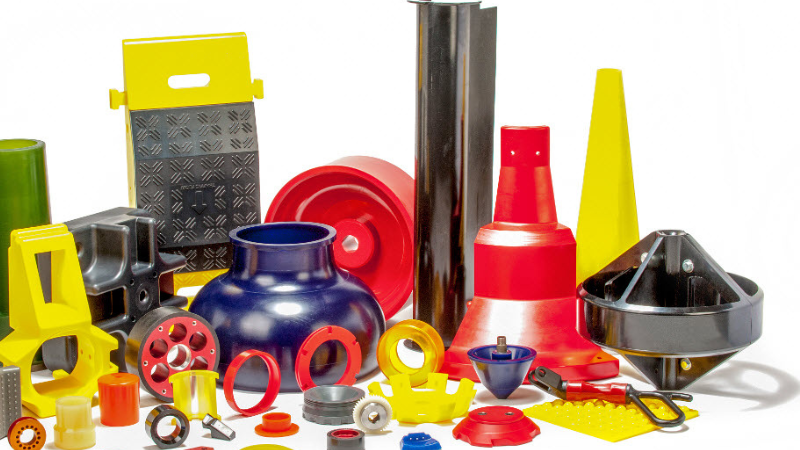
Because rubber prototypes are models of a final product, they are essential in the design and manufacturing process. These prototypes may come at an additional cost. However, they help save time and money on your manufacturing process.
In addition, rubber prototypes help you focus on the quality and function of a potential product without incurring a high financial cost.
The Benefits of Using Rubber Prototype
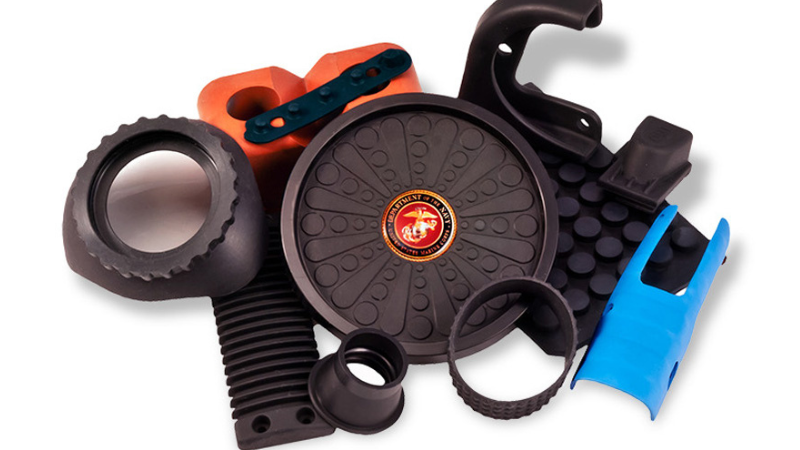
Rubber prototypes are important and offer numerous benefits, including cost-effectiveness, access to a physical copy, and time efficiency.
Cost-effectiveness
Although you must spend money to create a rubber prototype, this cost is more effective in the long run. With a rubber prototype, you see mistakes and correct them before running a large-scale production. Consequently, this saves money on faulty molds.
Time Efficiency
Rubber prototypes can save you production time. With a prototype, you can notice and rectify errors with potential components. Consequently, you can get everything in your production right once and for all. This helps you deliver projects at their estimated turnarounds instead of running around to look for a solution if there is something wrong with the new parts.
Access to a Physical Copy
You have access to a physical copy of your rubber component before mass production. So, with a rubber prototype, you can test and see what you are building before moving along in a project. In addition, a physical copy helps you check the fit and function of a piece to ascertain potential issues.
Furthermore, with a physical copy, you can carry out user tests to know the fit of the final product.
Increased Customizations
Creating a rubber prototype helps you assess and customize a product until you get an exact market fit. Then, with increased customizations, you get to focus and improve the quality of your product seamlessly.
How to Create a Rubber Prototype?
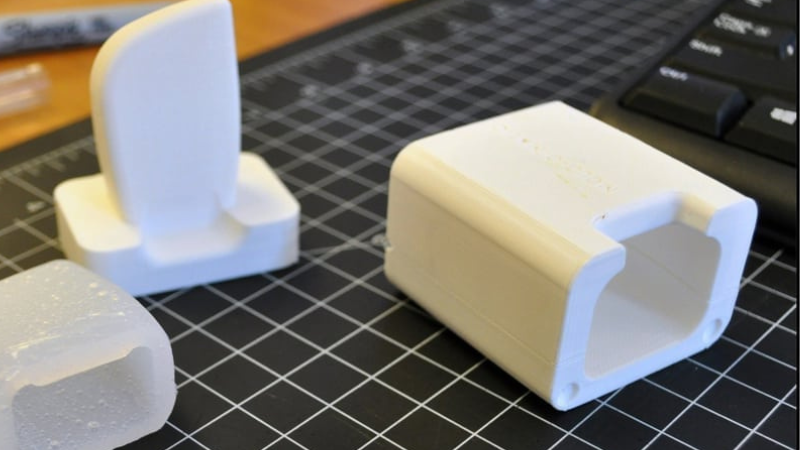
There are several ways to create a rubber prototype. Each method has its advantages and disadvantages. The following are rubber prototype-creating methods;
3D Printing
3D printing is a digital process of creating 3D solid objects. The process saves time compared to traditional prototyping methods. With 3D printing, you must create a model in a CAD file to be printed by the 3D printer.
The 3D printer uses additive manufacturing to create a rubber prototype layer by layer. This rubber prototyping method is also known as rapid prototyping because it creates prototypes in a few days or hours, depending on the complexity and speed of the printer.
The most significant advantage of 3D rubber prototyping over other methods is that it saves time. Nevertheless, there is a drawback to this method. 3D prototypes do not account for chemical resistance and compression sets. Therefore, this method is only suitable for producing lightweight rubber parts, including rubber feet, seals and gaskets.
Die-cutting is another rapid prototyping process that allows you to create complex rubber products. This prototyping method has high precision and can produce a machine’s intricate parts, including washers, seals, and gaskets. Furthermore, with die-cutting, you can create several consistent and flexible shapes.
Urethane Casting
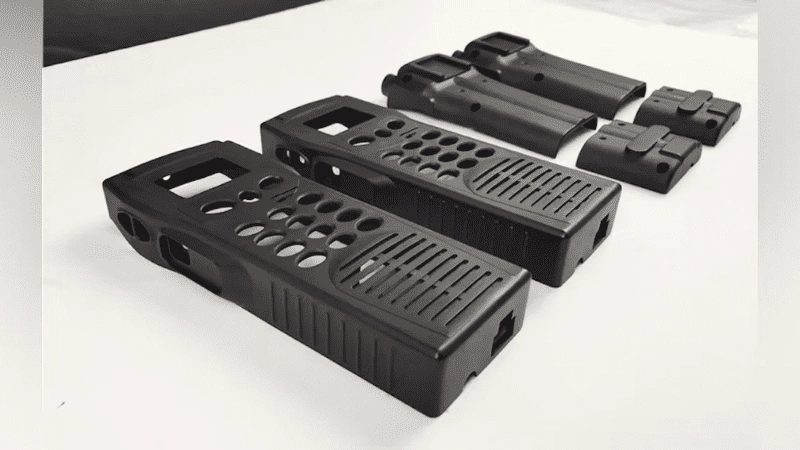
Urethane casting creates prototypes through a silicone mold around a master pattern. The master pattern has the dimensions and exact geometry of your desired prototype. This master pattern can be 3D-printed or CNC machined.
After the mold sets, you can cut it open to remove the prototype, a replica of the master pattern. Urethane casting allows you to create prototypes of varying hardness and colors. This prototyping method is also helpful for low-volume production.
Injection Molding
Injection molding involves using silicone rubber to create prototypes. Silicone rubber is versatile, chemical resistant, and flexible. Hence, the material is excellent for creating medical equipment and household appliance prototypes.
Compression Molding
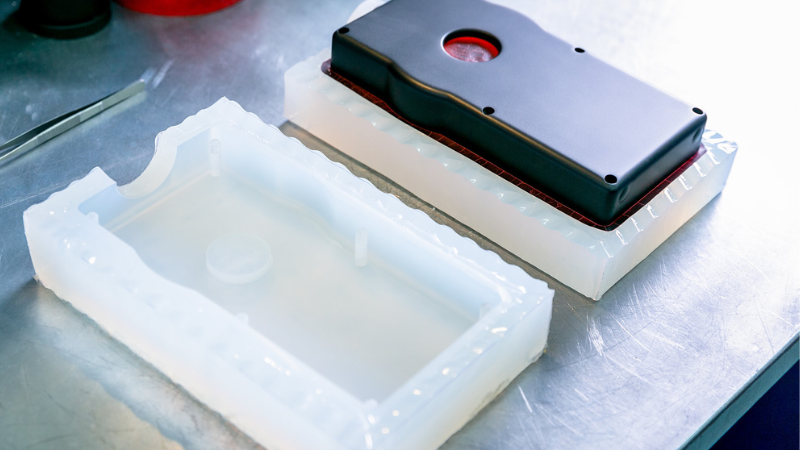
Compression molding is suitable for creating complex prototypes. This method can create large-sized products at high volumes. Furthermore, compression molding creates durable products with minimal waste material.
Compression molding is used for customized products, including o-ring seals, rubber grommets, and gaskets.
How does Prototype Rubber Molding Work?
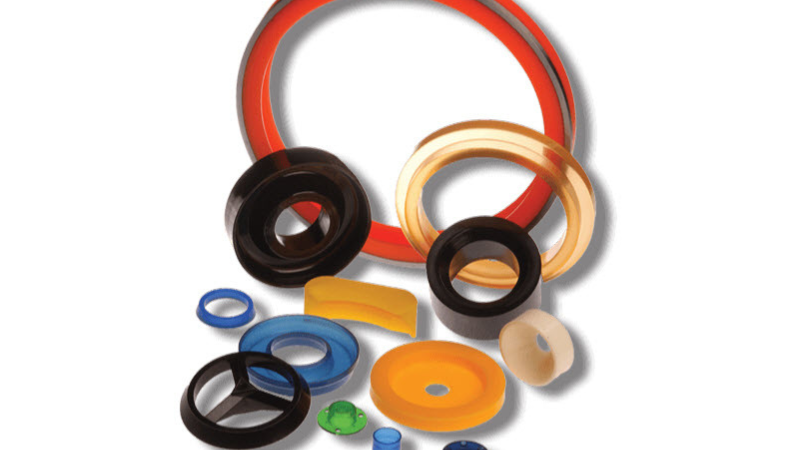
Before creating a product, a manufacturer carries out non-linear finite element analysis. This helps to assess the likely performance of a rubber component. Consequently, you see the component’s performance data, helping you make informed decisions before choosing a final design.
Afterward, your manufacturer should produce a small prototype batch using a low-volume tool. These prototypes come in the actual material you choose. On the other hand, if you choose 3D prototypes, you should be able to assess the fit and appearance. However, you may be unable to evaluate the product’s performance since it is made from resin material.
Conclusion
Rubber prototypes can save you money and time in your manufacturing process. Because there are several rubber prototyping methods, you can discuss them with your manufacturer to know the best method for your desired product.
Prototype Rubber Molding Products from Hongju’s Rubber
Hongju is a leading rubber manufacturer. We produce customized rubber products according to your material specifications. We can create prototypes with injection molding, compression molding, and die-cutting capabilities.
Furthermore, we provide top-notch products timely. Our customer service is also efficient and always ready to assist you. Contact us today!