From the construction industry to consumer goods, premium finishes can significantly improve the aesthetic appeal, structural integrity, and even the cost-effectiveness of plastic products. This article aims to delve deep into the world of premium finishes for plastics and explore how they are transforming products across sectors.
The Basics of Plastic Finishing
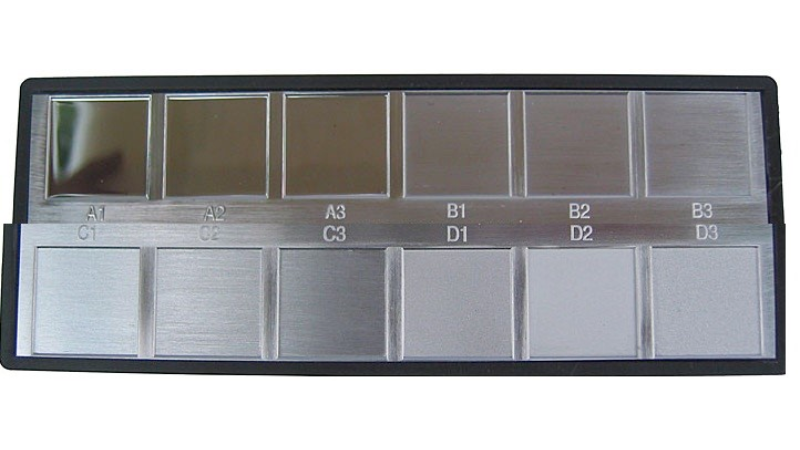
Plastic finishing refers to the post-production processes that improve the material properties and functional characteristics of plastic products. This is not merely an aesthetic enhancement; it’s an imperative step that affects the product’s structural integrity, corrosion resistance, and even heat resistance. For example, finishes can be applied to augment the high melting point of high-density polyethylene (HDPE) or to improve the dimensional stability of an injection-molded part.
Aesthetically speaking, a well-executed surface finish can give plastic products a high-end look akin to premium materials like metal or wood. This visual appeal plays a significant role in attracting consumers and creating a positive impression of the product’s quality. Moreover, an attractive finish can help differentiate a product from competitors in crowded markets.
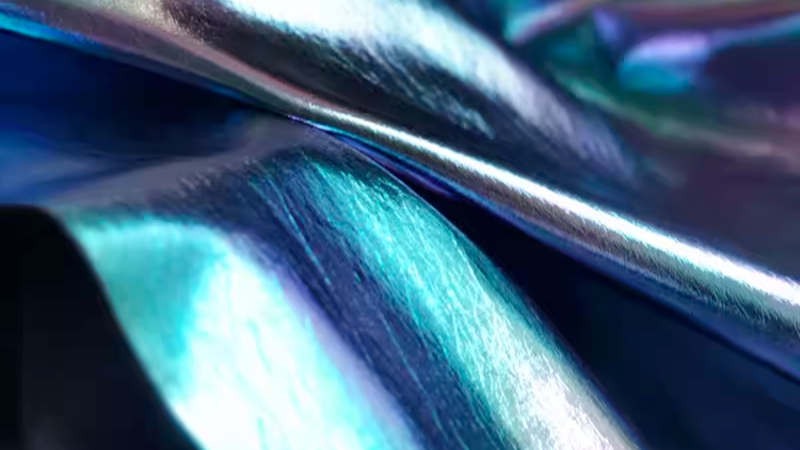
Functionally speaking, plastic finishes provide protection against external elements such as moisture, chemicals, UV radiation, and abrasion. They serve as a barrier between the underlying material and potential sources of damage or degradation. For instance, plumbing fixtures with appropriate surface finishes are more resistant to corrosion caused by water exposure over time.
Types of Premium Plastic Finishes
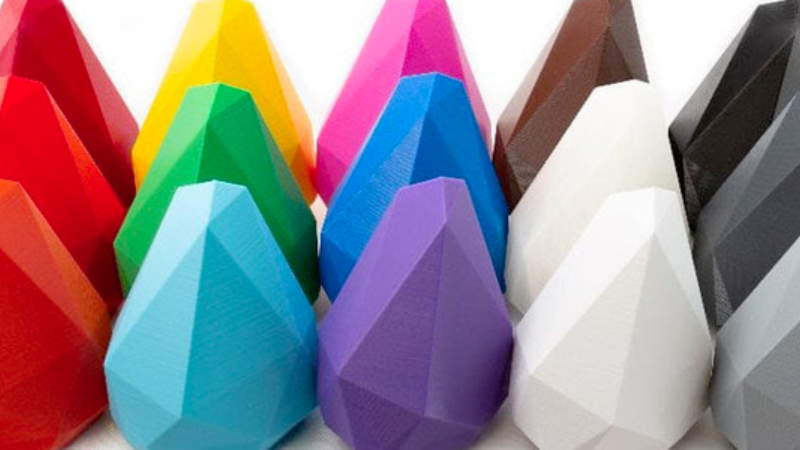
When it comes to elevating the quality of plastic products, the market offers an array of premium finishes that vary in their material properties, aesthetic appeal, and functional advantages. Below are some of the most sought-after types of finishes:
Electroplating
Electroplating offers exceptional strength and corrosion resistance to plastics, making it ideal for automotive parts and high-end consumer goods. Given its complex geometries, electroplating ensures both structural integrity and an attractive appearance.
Powder Coating
Known for its excellent resistance to environmental wear and tear, powder coating is widely used in the construction industry. It enhances both the mechanical strength and the aesthetic quality of plastic materials.
UV-Resistant Finishing
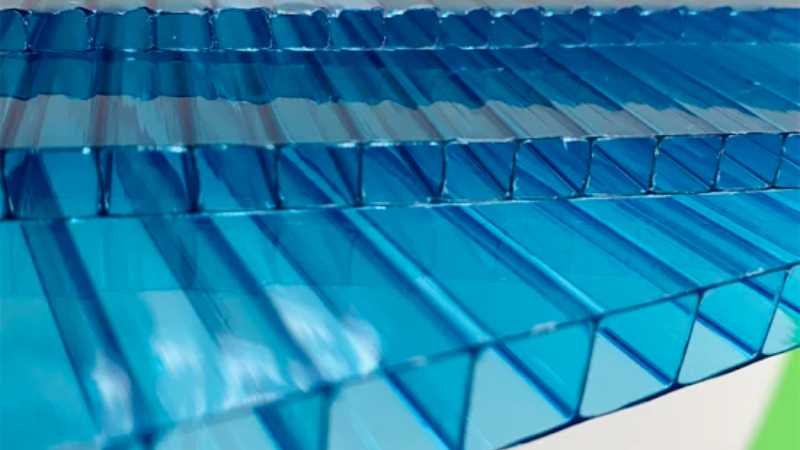
This finishing technique enhances the material’s resistance to prolonged exposure to sunlight, making it perfect for outdoor furniture and construction materials. UV-resistant finishes preserve color fidelity and maintain the high-density polyethylene’s structural integrity.
Textured Finishes
These finishes are designed to improve grip and tactile qualities, often used in handheld devices and safety goggles. Textured finishes add both functional and aesthetic appeal to a range of plastic products.
Anti-microbial Finishes
In healthcare and food packaging, anti-microbial finishes offer superior performance by inhibiting the growth of bacteria on plastic surfaces. This is especially crucial in maintaining hygiene standards and ensuring consumer safety.
High-Gloss Finishes

Utilized mainly for its aesthetic appeal, high-gloss finishes provide a sleek, polished look to consumer goods. However, they also offer some level of protection against minor scratches and impact forces.
Each of these premium finishes has unique characteristics that meet specific industry needs, from corrosion resistance and heat resistance to aesthetic upgrades and cost-effectiveness. Selecting the appropriate finish can therefore significantly affect a product’s marketability, lifespan, and even cost savings.
Benefits of Premium Finishes
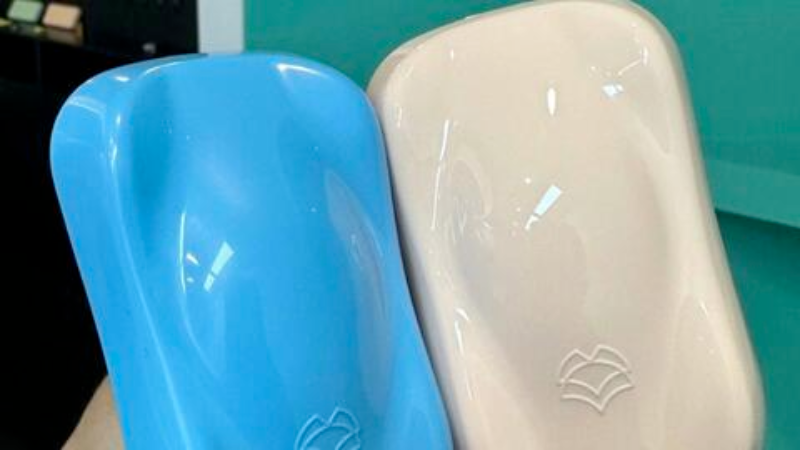
Incorporating premium finishes in plastic products is not just a design enhancement, but it also provides a myriad of tangible advantages. Here are the significant benefits of opting for premium finishes:
- Aesthetic Appeal: Premium finishes can transform the look of a plastic product, giving it a luxurious touch and feel. This lasting impression can significantly elevate the brand value, especially in consumer goods where design aesthetics play a crucial role in consumer purchasing decisions.
- Enhanced Durability: With finishes that offer corrosion resistance, heat resistance, and UV protection, the lifespan of the plastic product can be substantially extended, reducing the need for replacements or repairs.
- Improved Mechanical Properties: Some finishes enhance the mechanical strength of plastics, offering exceptional strength and tensile strength. This ensures that products retain their shape and function even under stressful operating conditions.
- Versatility in Design: Premium finishes enable intricate designs, varied textures, and various colors, allowing brands to customize their products according to market demands or specific target audience preferences.
- Enhanced User Experience: The feel of a soft-touch coating or the shine of an electroplated surface significantly enhances the user experience. Such finishes can also provide a comfortable and firm grip on products like phone cases or kitchen appliances.
- Differential Market Positioning: In a competitive market, having a unique selling proposition is crucial. Premium finishes offer brands that distinguishing factor, making their products stand out on the shelves.
In the realm of materials science, premium finishes represent the fusion of aesthetics and functionality. They showcase how advances in technology can blend with design philosophies to produce plastic products that are not only visually appealing but also robust and functional.
How to Choose the Right Finish for Your Product
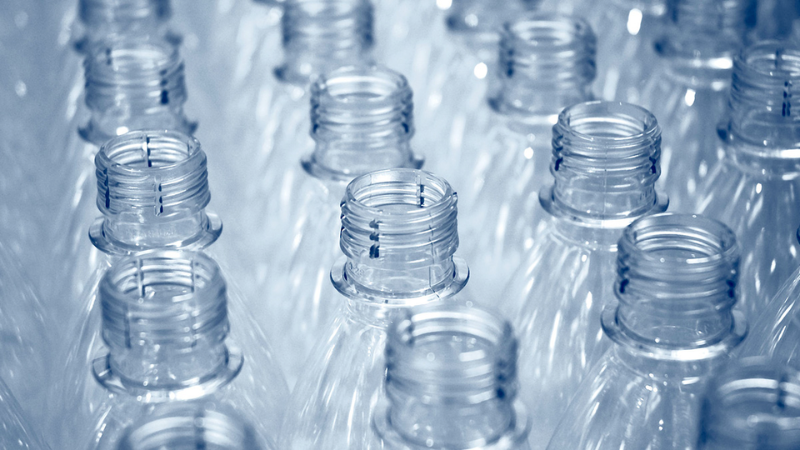
Selecting the right finish is crucial. The finish you choose can greatly impact the final product and its overall appeal. To ensure you make the best decision, there are several factors you should consider.
Understanding the Target Market and Consumer Preferences
Before deciding on a finish for your plastic product, it’s important to understand your target market and their preferences. Different finishes evoke different emotions and perceptions in consumers. For example, a glossy finish may give off a sense of luxury and sophistication, while a matte finish may convey a more understated elegance. By understanding your target market’s preferences, you can select a finish that aligns with their expectations and desires.
Assessing Compatibility Between Plastics and Finishing Techniques
Not all plastics are compatible with every finishing technique. It’s essential to assess the compatibility between different types of plastics and specific finishing techniques before making a decision. Some finishes may not adhere well to certain types of plastics or could cause damage or discoloration. Consulting with experts or consultants who specialize in plastic finishes can help you determine which combinations will work best for your product.
Collaborating with Experts or Consultants
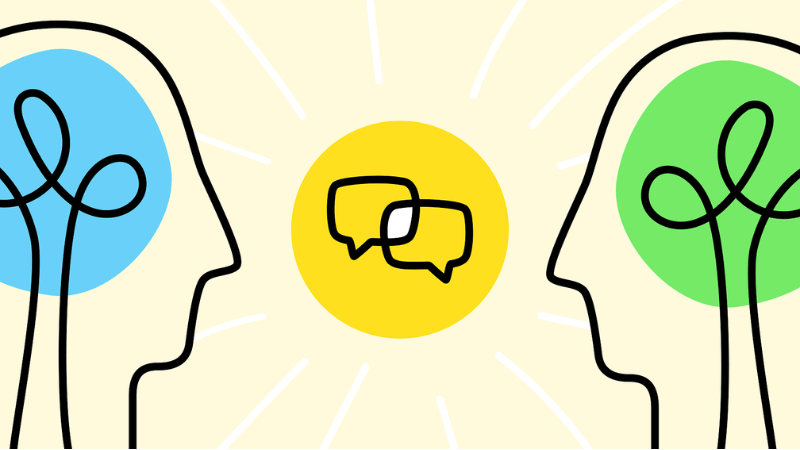
Collaborating with experts or consultants in the field of plastic finishes can be invaluable when choosing the right finish for your product. These professionals have extensive knowledge and experience in working with various materials and techniques. They can provide insights into which finishes will achieve the desired effect for your product while ensuring its durability and longevity.
Factors to Consider When Selecting a Suitable Premium Finish
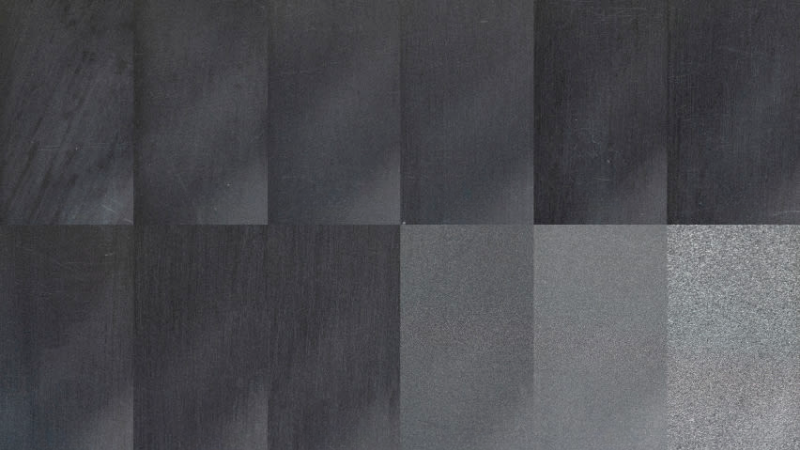
Due to their lightweight nature, plastic products offer ease of transport and cost savings. Advanced finishes also withstand intense heat, broadening their application scope. To ensure that you choose an appropriate premium finish for your plastic product, consider the following factors:
- Product Functionality & Durability: How a product will be used often dictates the best finish. For example, products that will be exposed to harsh operating conditions might need finishes that offer exceptional strength and chemical resistance.
- Material Properties: Different plastic materials, like high-density polyethylene and low-density polyethylene, interact differently with finishes. It’s vital to select a finish that complements the material properties, ensuring dimensional stability and a lasting impression.
- Aesthetic Requirements: While functionality is paramount, aesthetic appeal is also critical. Depending on the consumer goods in question, you might want a finish that offers various colors or unique characteristics.
- Regulatory and Safety Standards: In consumer goods and the construction industry, it’s crucial to choose finishes compliant with safety standards, especially when the finished products interact directly with the user or environment.
- Production Cost Implications: Every finish has its cost, affecting the overall production costs. Some finishes, while delivering superior performance, might elevate costs.
- Consumer Preferences: Sometimes, a finish might be chosen based on market trends, ensuring the finished product aligns with consumer expectations and offers cost-effectively.
Achieving the Desired Surface Finish in Injection Molding
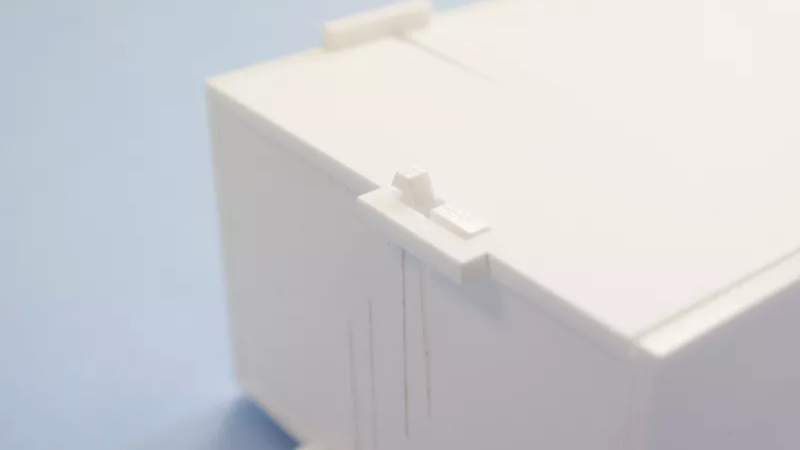
In the realm of plastic manufacturing, injection molding stands out as one of the most versatile methods, widely used for producing everything from automotive parts to consumer goods. However, achieving the perfect surface finish in injection molding is often a complex task that requires a deep understanding of material science, production processes, and design intricacies. This section aims to discuss how to obtain the desired surface finish using injection molding, and the factors that influence it.
Material Selection
One of the first considerations is the choice of plastic material. Different materials have different melting points, tensile strength, and mechanical strength, all of which affect the final surface finish. Materials like high-density polyethylene (HDPE) and low-density polyethylene (LDPE) have their unique characteristics and melting behaviors that influence the surface finish.
Mold Design

The mold’s design plays a significant role in the quality of the surface finish. Factors such as the complex geometries of the mold, gate placement, and type of ejector pins can greatly impact the outcome. Mold designs should be aligned with the material properties to achieve optimal dimensional stability and surface finish.
Injection Parameters
The injection speed, pressure, and temperature can affect the plastic’s behavior as it fills the mold, thus influencing the final surface finish. Properly adjusted parameters can help achieve a higher mechanical strength and exceptional strength in the final product.
Post-Processing Options for Enhanced Surface Finish Quality
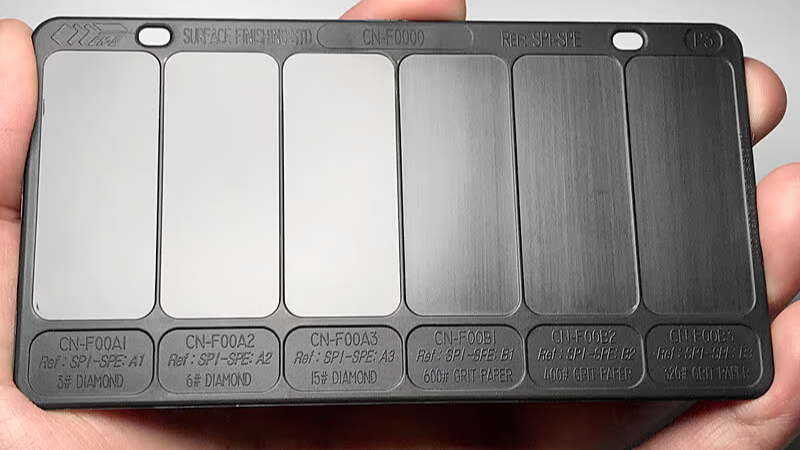
While injection molding produces satisfactory results for many applications right out of the mold, there are post-processing options available to further enhance surface finish quality. These additional steps allow manufacturers to meet specific requirements or achieve premium finishes on plastic products.
- Polishing: Polishing is a technique often employed post-injection molding to remove any surface imperfections or burrs. It involves using abrasives in a buffing or sanding process until the desired level of smoothness is reached. Polishing enhances the product’s dimensional stability and imparts a high-quality look, making it suitable for consumer goods like safety goggles and automotive components.
- Texturing: Texturing serves to impart patterns or textures on the surface of plastic products, serving both functional and aesthetic purposes. Techniques like chemical etching or mechanical engraving are used to create these textures. Textured surfaces offer improved grip, corrosion resistance, and exceptional strength, making them ideal for applications in the construction industry and other areas where structural integrity is crucial.
- Painting: Painting introduces a wealth of color options and can also serve as a protective coating. Painting can enhance the product’s resistance to impact forces, UV rays, and chemicals, as it often involves multiple layers of primer, paint, and sealant. It is widely used in packaging materials and consumer goods to create a lasting impression and differentiate products in the market.
- Coating: Coatings can serve multiple purposes, ranging from enhancing heat resistance to providing excellent resistance to chemicals and environmental elements. Materials like high-density polyethylene can be coated with special substances to improve their already substantial durability. These coatings often offer benefits like fuel efficiency and low density but with superior performance.
Exploring In-Mold Decoration Techniques for Plastic Products
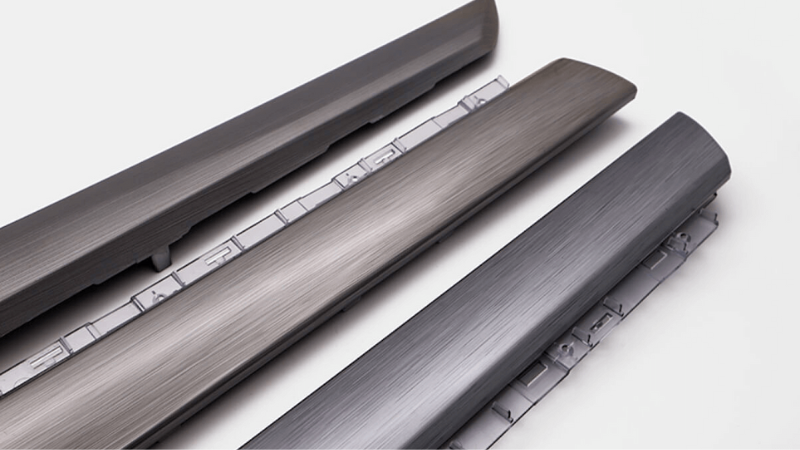
In the world of plastic manufacturing, finding innovative ways to incorporate designs directly into products has become increasingly important. One technique that has gained significant popularity is in-mold decoration(IMD). This process allows for the seamless integration of premium finishes onto plastic products during the molding process itself.
Improved Durability and Resistance to Wear
One of the key advantages of utilizing IMD is the enhanced durability and resistance to wear that it offers compared to surface-applied decorations. With traditional methods, such as painting or printing, there is a risk of the design peeling off or fading over time. However, with IMD, the design becomes an integral part of the product, ensuring long-lasting visual appeal.
Types of IMD Techniques and Their Applications
There are various types of IMD techniques available today, each with its own unique applications across different industries. Let’s take a closer look at some popular options:
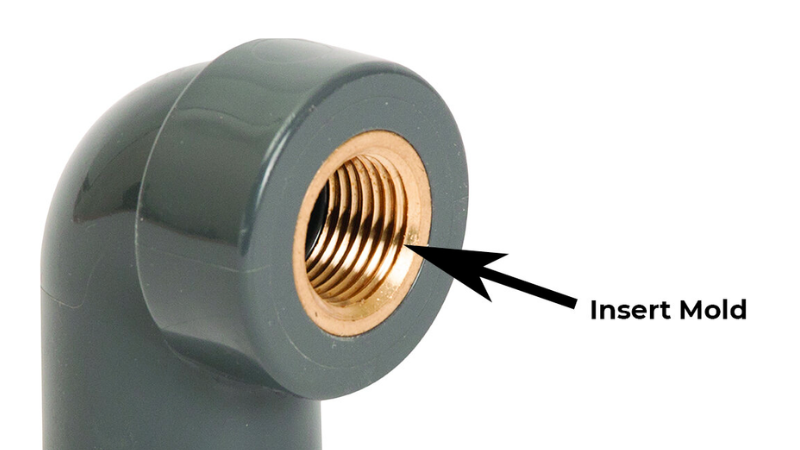
- Insert Molding: This technique involves placing pre-formed inserts into a mold before injecting molten plastic around them. The result is a product with embedded designs that seamlessly blend with the surrounding material.
- Overmolding: Overmolding takes IMD a step further by allowing multiple layers of materials to be combined in a single molding process. This technique enables intricate designs and textures to be incorporated into plastic products effortlessly.
- Mold Textures: Mold textures offer endless possibilities for creating visually appealing finishes on plastic products. By using specialized molds with unique patterns or textures, manufacturers can achieve stunning effects like wood grain or leather-like surfaces.
The versatility offered by these techniques makes IMD suitable for a wide range of industries, including automotive, consumer electronics, and household appliances.
Case Studies of Premium Plastic Finishes: A Focus on Hongju’s Expertise
The transformative power of premium plastic finishes is best exemplified through real-world case studies. Below, we delve into instances where Hongju’s advanced surface treatment technologies have significantly elevated the quality, durability, and market value of various plastic products for undisclosed client companies.
Case Study 1: Automotive Industry
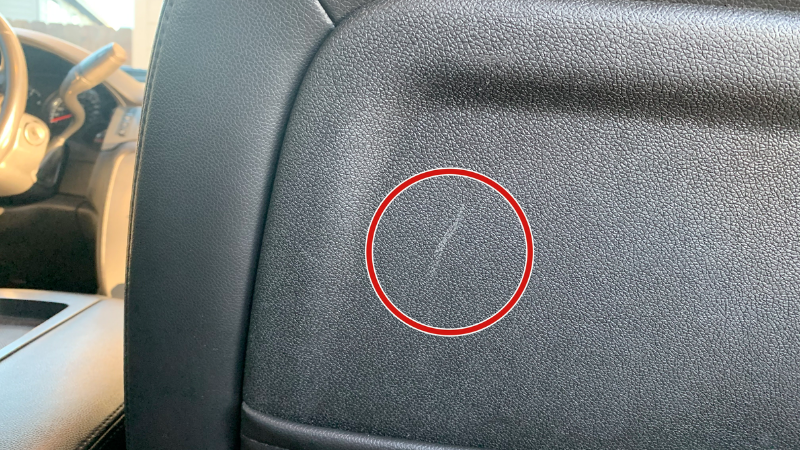
In one remarkable case, an automotive company was struggling with wear and tear on interior components, impacting both the vehicle’s resale value and customer satisfaction. Hongju’s specialized texturing techniques were employed, resulting in components with exceptional strength, reduced glare, and improved grip. The finished product not only elevated the car’s aesthetic but also significantly increased its market value.
Case Study 2: Electronics Sector
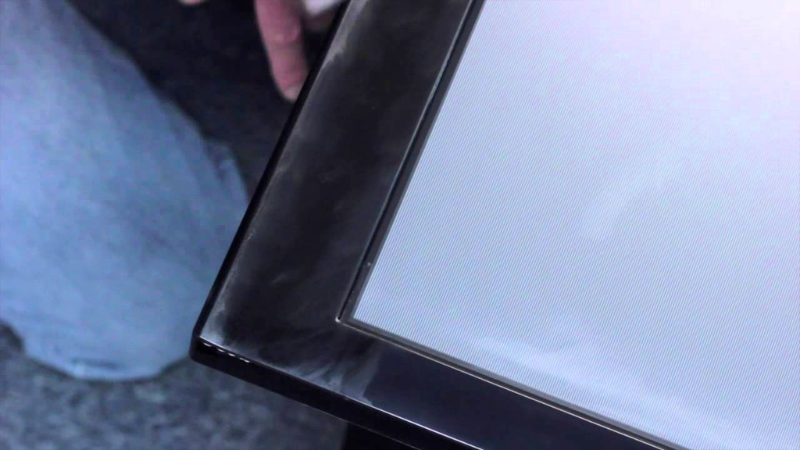
For a consumer electronics company facing the challenge of products losing their sheen and attractiveness over time, Hongju’s advanced polishing technology proved to be a game-changer. The polished surfaces remained free from grime and were easy to clean, resulting in consistently high customer reviews and an increase in sales.
Case Study 3: Household Appliances
A manufacturer of premium household appliances sought to differentiate its products in a crowded market. Hongju applied a combination of advanced coatings and texturing methods to enhance the products’ visual appeal and functional utility. This led to increased market share for the client, as the textured and coated surfaces added an unparalleled degree of sophistication and durability to the appliances.
Case Study 4: Sporting Goods
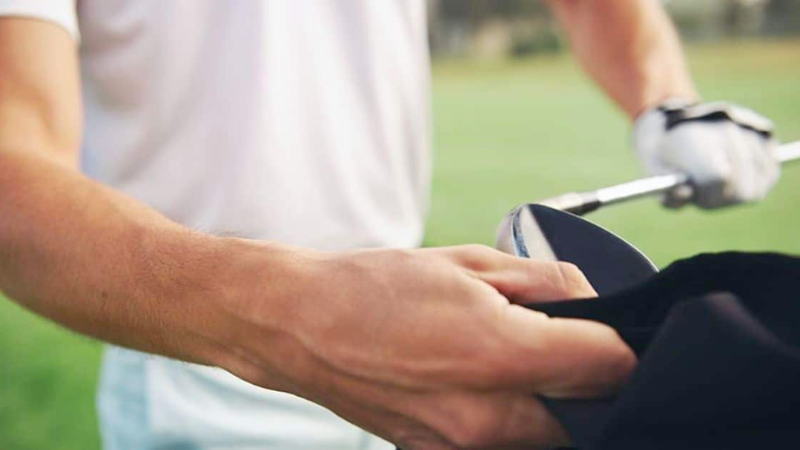
For a sporting goods manufacturer, Hongju’s versatile texturing technologies added enhanced grip and aesthetic variety to various products, from bicycle handles to gym equipment. The textured surfaces not only provided superior performance but also concealed wear and tear, maintaining the products’ aesthetic appeal for a longer period.
These case studies showcase how Hongju’s expertise in premium plastic finishes, ranging from polishing to texturing and advanced coatings, can provide tangible benefits across industries.
Conclusion
In summary, premium plastic finishes can significantly elevate a product’s aesthetic and functional quality. Hongju’s advanced surface treatment technologies offer a range of options, from polishing to advanced coatings, proven to enhance durability and market value. Investing in such finishes is not just an aesthetic choice but a strategic move for any business aiming for excellence.
Choose Hongju for Cutting-Edge Surface Treatments
Looking to elevate the finish of your plastic products? As a leading materials science company, Hongju specializes in cutting-edge surface treatments that enhance both aesthetic and functional qualities. Don’t settle for less—choose Hongju for a finish that lasts and impresses.
Take the First Step:
Requst for an Inquire
Quality Meets Affordability. Inquire Now for High-Quality Products at Low Volumes.