This article provides comprehensive insights into understanding what O-rings are, how static and dynamic situations affect the selection of O-rings, and how you can make an informed decision based on these factors.
Tailoring your O-ring choice to specific operating conditions can significantly enhance equipment efficiency and lifespan. Let’s delve deeper into the world of O-rings and uncover the secrets to their effective utilization.
A Primer on O-Rings: From Materials to Standards
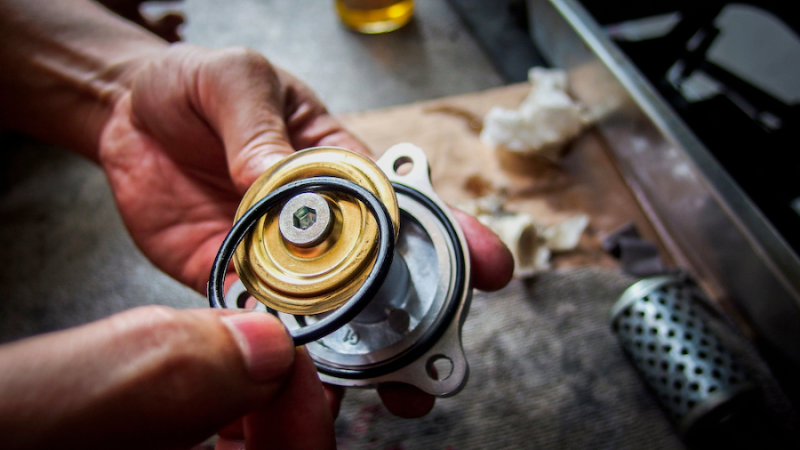
Understanding the essential nature of O-rings is the first step toward making an informed choice for your specific needs.
Let’s take a closer look at the various aspects of O-rings, ranging from the materials they’re made from to the sizes and standards used across different industries.
What are O-rings?
O-rings are donut-shaped mechanical gaskets designed to be seated in a groove and compressed during assembly between two or more parts.
They serve as a critical component in a wide range of applications, thanks to their cost-effectiveness, reliable sealing capabilities, and simplicity of design.
Exploring Different O-Ring Materials
O-rings are commonly made from a variety of materials, each with its own unique properties and advantages. These materials play a crucial role in determining the performance and durability of the o-ring in different conditions. Here, we will explore some of the most commonly used materials in o-ring manufacturing.
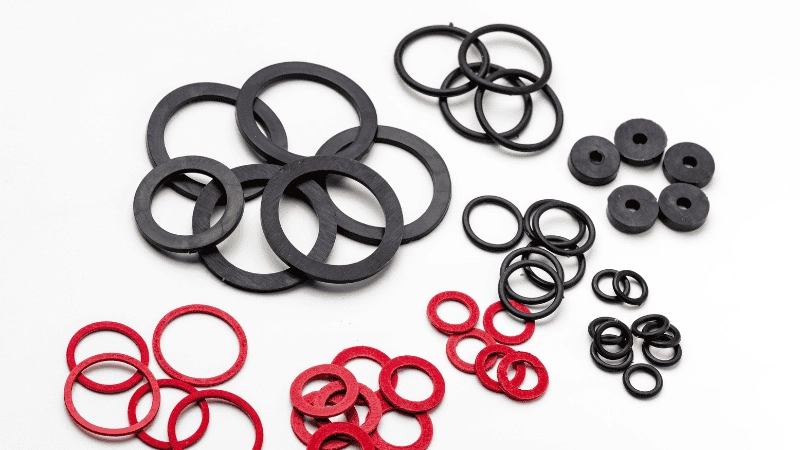
Understanding Material Properties and Advantages
- Rubber: Natural rubber is widely used due to its excellent tear resistance and resilience. It offers good resistance to abrasion, tearing, and compression set.
- Silicone: Silicone rubber o-rings are known for their high-temperature resistance, making them suitable for applications where extreme heat is involved. They also provide a reliable seal at a high-temperature range.
- Nitrile: Nitrile rubber provides excellent resistance to oils, fuels, and other petroleum-based fluids. It is commonly used in applications that require sealing against hydrocarbons.
- Viton: Viton o-rings offer superior chemical resistance against a wide range of aggressive fluids such as acids, solvents, and fuels. They are often chosen for demanding industrial environments.
Examples of Suitable Applications

- Silicone o-rings are ideal for use in automotive engines or aerospace applications where they can withstand high temperatures without losing their sealing properties.
- Nitrile O-rings find extensive use in hydraulic systems or machinery that comes into contact with oil or fuel.
- Viton o-rings are preferred for sealing applications involving aggressive chemicals found in industries like pharmaceuticals or chemical processing.
Sizes and Standards
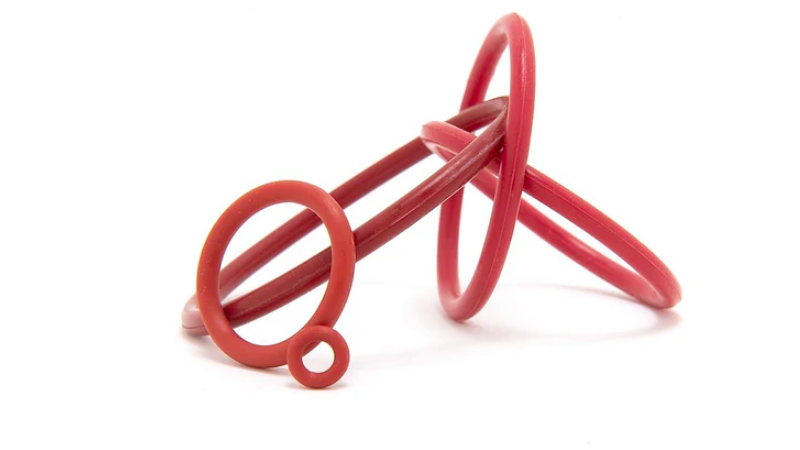
O-rings come in a plethora of sizes and are often standardized to allow for universal fitment across different applications. In the US, for example, the American standard AS568B is widely used.
This standard defines 379 sizes of O-rings in five different cross-sections and diameters. By choosing the correct O-ring size, manufacturers ensure compatibility and interchangeability.
Take the First Step:
Requst for an Inquire
Quality Meets Affordability. Inquire Now for High-Quality Products at Low Volumes.
Deciphering Static and Dynamic Conditions for O-ring Application
The next crucial step in selecting the right O-ring for your needs is understanding the difference between static and dynamic conditions in an application.
In this section, we will explore the distinction between these conditions, analyze their unique requirements, and ascertain how they influence the choice of an O-ring.
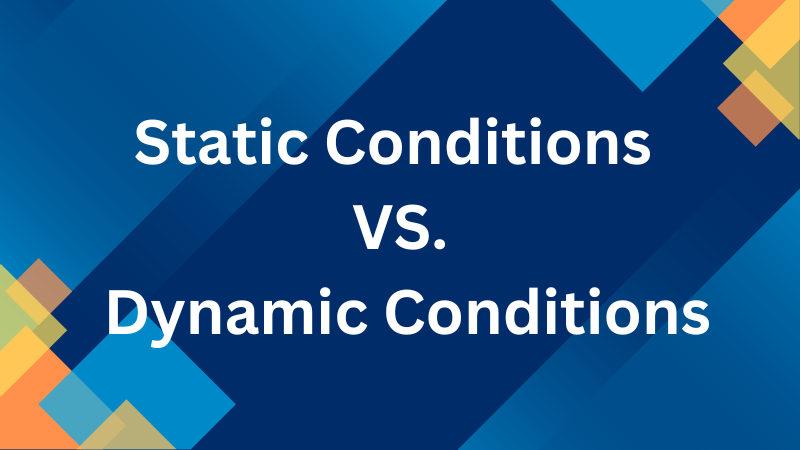
What Are Static and Dynamic Conditions?
Static conditions refer to situations where the O-ring is confined to a groove and is sealed against a stationary, non-moving part. In these instances, once the seal is engaged, there are minimal fluctuations in pressure, no movement across the sealing surfaces, and the seal compression and O-ring can remain in a constant state.
Dynamic conditions involve scenarios where either the O-ring or the mating part moves. This movement could be reciprocating (back and forth), rotational, or oscillating in nature. In dynamic applications, the O-ring is exposed to wear and tear due to friction, posing a significant impact on the selection of the O-ring materials.
Differences Between Static and Dynamic Conditions
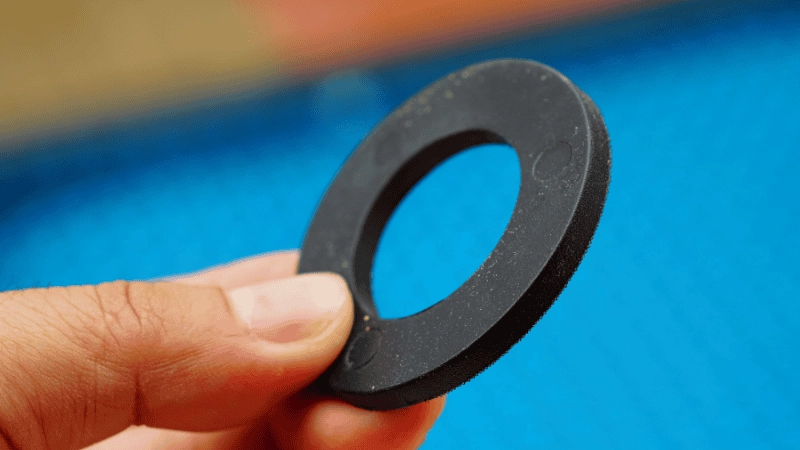
In static conditions, the seal is subjected to less stress since it’s not in constant motion, which makes it less prone to wear and tear. The focus in these conditions lies in the ability of the O-ring to maintain a proper seal under varying pressures.
With static seal applications, the system has little to no motion. High-quality seals used in static applications are made to be elastic to ensure the best performance.
Contrarily, in dynamic conditions, the O-ring seals will undergo repetitive movement, causing increased friction and wear.
Thus, the material and design of the O-ring must be chosen considering its resistance to wear, extrusion, and overall durability.
How does the O-ring Work in Static and Dynamic Conditions?
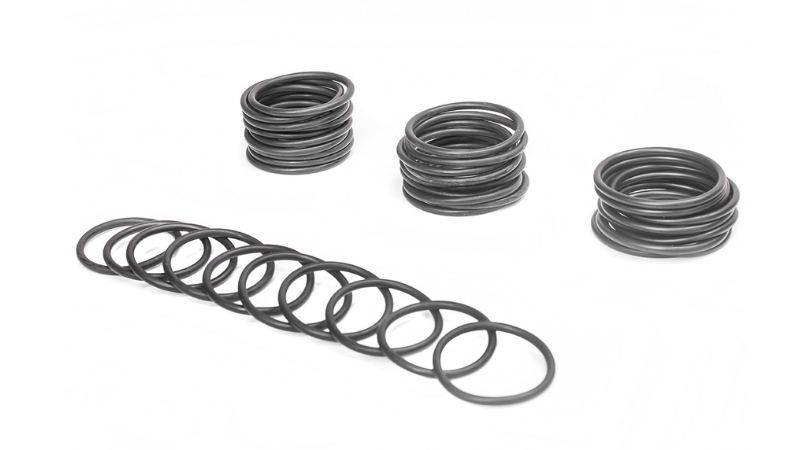
In static conditions, O-rings function as a constant seal between two non-moving parts, providing two surfaces with an airtight barrier to keep fluids or gases from leaking out.
This is achieved due to the elastomeric properties of the O-ring material, which enable it to deform under pressure, filling up the space between the two static surfaces to create a tight seal.
In contrast, in dynamic conditions, O-rings not only have to serve as a seal but also must endure the movement of the parts they are installed in. This could be either rotary (twisting) movement, as in rotating shafts, or reciprocating (back-and-forth) movement, as in hydraulic or pneumatic cylinders.
In such applications, the O-ring must not only maintain the seal but also resist wear and tear caused by the moving parts, and potentially also offer low friction to allow smooth movement of the components.
Choosing the correct O-ring for these applications requires careful consideration of the material properties, shape, and size of the O-ring, as well as the operational environment, including pressure, various temperature ranges, and the type of fluid or gas being sealed.
Take the First Step:
Requst for an Inquire
Quality Meets Affordability. Inquire Now for High-Quality Products at Low Volumes.
Choosing the Right O-Ring for the Conditions
When it comes to picking the appropriate O-ring for your application, understanding the differences between static and dynamic conditions, as outlined above, is only the first step. In the following section, we will delve into the specific factors you need to consider to make an informed choice.
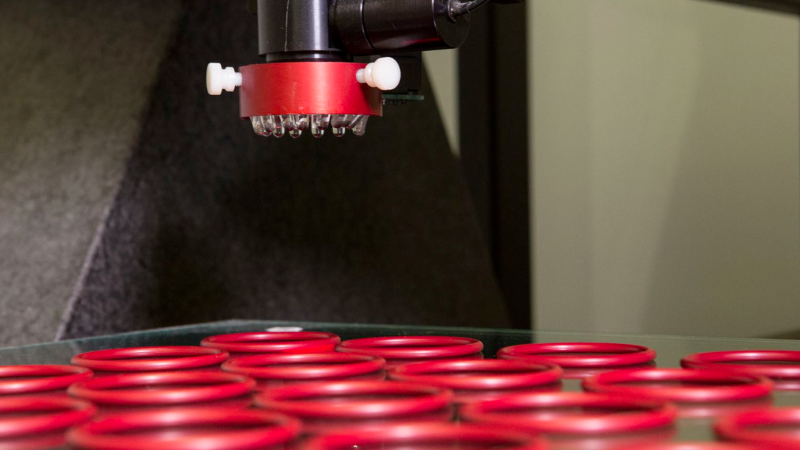
Selecting an O-ring for Static Seal Application
When it comes to selecting an O-ring for static conditions, the main criteria to consider are material compatibility, resistance to deformation under pressure, and ability to retain its shape over time.
1. Material Compatibility: The O-ring material should be compatible with the environment it will be operating in, including exposure to specific fluids, gases, or chemicals. For instance, Nitrile is a popular choice for static conditions due to its excellent resistance to petroleum-based oils and fuels.
2. Resistance to Deformation: In static conditions, the right material of the O-ring will be exposed to pressure for extended periods. The material should be resistant to deformation and exhibit low compression set characteristics.
3. Shape Retention: Even after being subjected to varying pressures, a good O-ring for static conditions should have excellent shape retention abilities to maintain an effective seal.
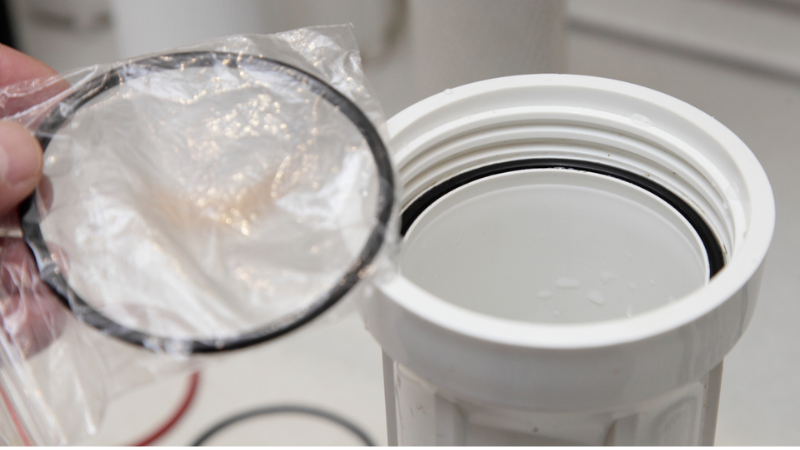
Transitioning from the relatively tranquil realm of static conditions, let’s explore the harsher and more demanding world of dynamic conditions.
Selecting O-Rings for Dynamic Seals
In dynamic conditions, the O-ring faces challenges far beyond those in static environments, making the selection process even more critical. Here are some primary factors to consider when selecting O-rings for dynamic applications.
1. Wear Resistance: O-rings in dynamic applications are subjected to continuous movement, leading to potential wear and tear. Therefore, materials with high wear resistance, like Polyurethane or Fluorocarbon, are usually a good choice for dynamic seals.
2. Low Friction: Materials that exhibit low friction characteristics can minimize wear and extend the seal’s life in dynamic conditions. Often, O-rings may need to be lubricated to reduce friction.
3. Extrusion Resistance: In high-pressure dynamic applications, the O-ring material needs to resist extrusion into the clearance gap. Harder materials are generally preferred for these applications.
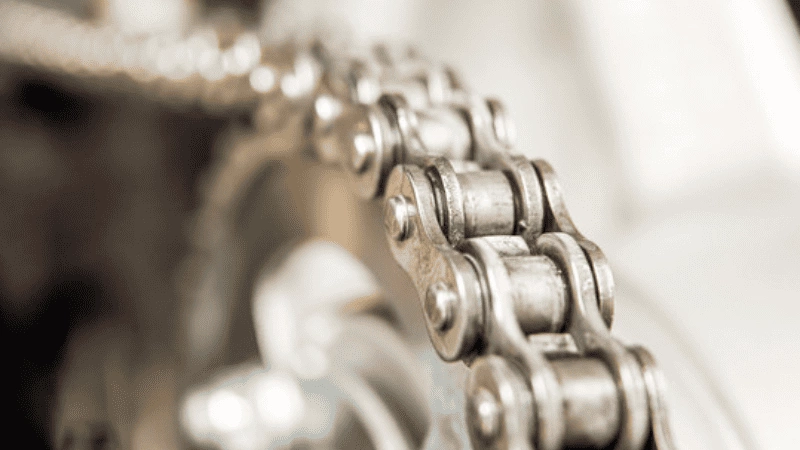
Selecting the right O-ring involves understanding the application’s nature and matching it with the O-ring’s attributes. As we’ve seen, the decision varies significantly depending on whether the application involves static or dynamic conditions.
Advantages of Using O-Rings in Static and Dynamic Conditions
While O-rings play a crucial role in a wide range of applications, their benefits are particularly pronounced when dealing with static and dynamic situations. Let’s take a closer look at these benefits and how they can enhance the performance and longevity of your machinery.
Benefits in Static Conditions
In static seal applications, O-rings provide an ideal sealing solution due to their simplicity, cost-effectiveness, and reliability. They can withstand high pressures, extreme temperatures, and corrosive environments.
The fact that they can create a near-perfect tight seal means they significantly minimize the risk of fluid or gas leakage.
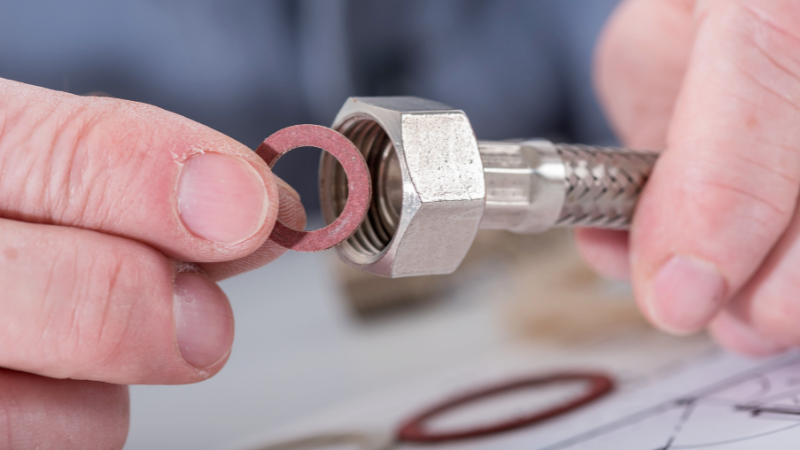
Advantages in Dynamic Conditions
In dynamic conditions, O-rings excel due to their durability, flexibility, and wear resistance. These seals can handle continuous motion and varying pressures without losing their sealing integrity.
They can also resist abrasion and tearing, key factors in maintaining high performance and extended service life in moving machinery.
Furthermore, O-rings for dynamic applications are designed to minimize friction, thereby reducing wear and tear and enhancing the overall efficiency of the equipment.
Take the First Step:
Requst for an Inquire
Quality Meets Affordability. Inquire Now for High-Quality Products at Low Volumes.
Conclusion
In conclusion, the choice between static and dynamic O-rings largely depends on the application.
Whether it’s for static use, where pressures are constant and movements are non-existent, or dynamic use, where parts are in continuous motion, the right O-ring types can make all the difference in the efficiency and longevity of your equipment.
Choose Top-Of-The-Line O-ring From Hongju
If you’re looking for top-tier O-ring design for both static and dynamic seal applications, look no further than Hongju Silicone. Our selection of custom O-rings caters to diverse needs, ensuring optimal performance for your equipment.
Choose Hongju Silicone for your O-ring manufacturer. Your satisfaction and the successful operation of your equipment are our utmost priority. Contact Hongju Silicone today for expert guidance and high-performance custom O-rings tailored to your needs.