Silicone polymer can also be injection molded and offers unique benefits compared to other polymers. This guide will discuss some of the key factors you need to consider when designing a silicone injection mold.
What is Liquid Silicone Rubber (LSR) Injection Molding?
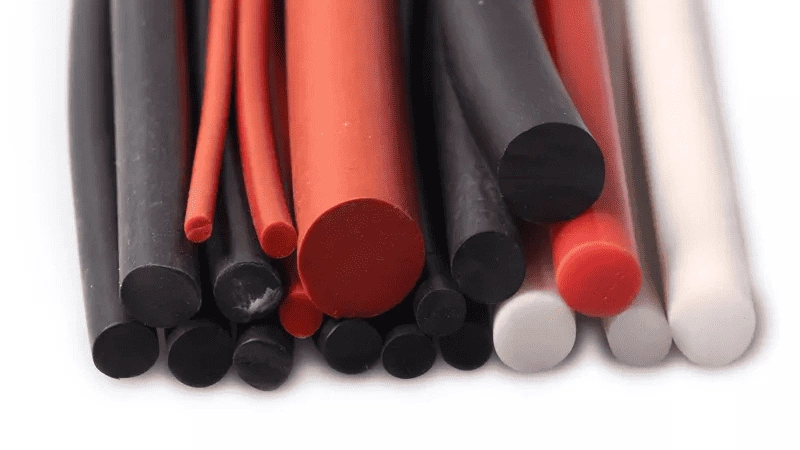
LSR injection molding is an elastic substance transformed into a core part of medical tools. Liquid silicone rubber (LSR) injections are also used in automotive, consumer, aerospace, and power applications.
The LSR as thermosetting elastic shows considerably high elasticity, perpetually high-temperature performance, and it’s less sensitive to ultraviolet (UV) rays. It generally has beneficial biocompatibility.
There’s a well-known technique used for LSR injection molding to create many products in the fields above, among many others. Apart from its technical and physical makeup, the process elements are also very exigent.
It is one of the newest advancements in NEWTOP’s molding activities. Thanks to its short mold life and inbuilt optimized performance features, the LSR products are the top choices for different mold designs.
This injection molding comes in different levels of hardness, known as a durometer. The LSR grades exhibit elasticity between lower than 200% and higher than 1200% on the commercial scale. The temperature range for LSR injections can be less than 400C to higher than 2000C according to the length of its exposure.
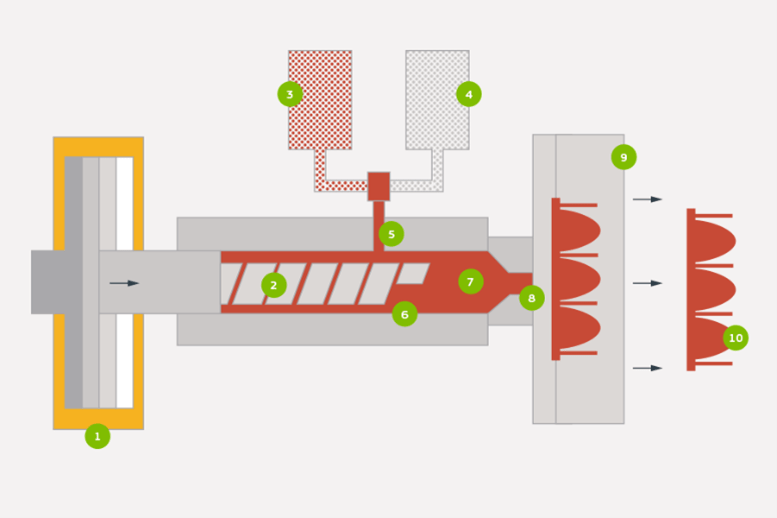
Thanks to chemical reactions on the outer parts of the LSR, UV radiation has fewer effects over an extended period. When created for medical use, they are less volatile and have low leachable properties. They have also proved to result in low external body reactions compared to some other flexible implantable polymers.
Liquid silicone injection molding has various properties that undergo a range of production methods. Durometers typically mark commercial LSR materials. Thanks to its friendly biocompatibility, LSR injection molds are suitable for skin contact, implantable, and hypoallergenic use like membranes, electronic medical tools, catheters, etc.
It is one of the newest advancements in NEWTOP’s molding activities. Thanks to its short mold life and inbuilt optimized performance features, the LSR injection is a top choice for different mold designs.
Take the First Step:
Requst for an Inquire
Quality Meets Affordability. Inquire Now for High-Quality Products at Low Volumes.
What are the Benefits of Using Liquid Silicone Rubber?
In some industries, manufacturers prefer plastics during their molding process. While plastics are a popular choice because they are strong, can be easily molded to any shape, and are lightweight, they are not so durable.
Plastics are not built to last under high temperatures. They either lose shape or they become disfigured. Liquid silicone rubber takes this burden off manufacturers’ minds, hence, its recent popularity. Here are some reasons why LSR mold design is taking over:
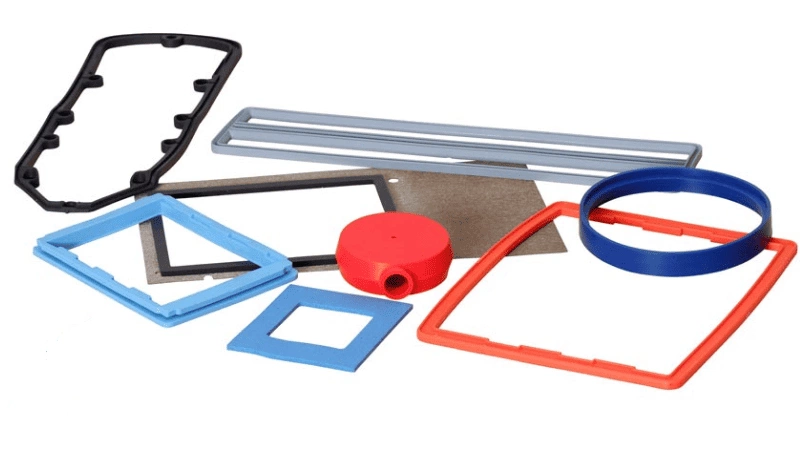
Versatility:
Liquid silicone rubber is a favorite for automotive tools, medical equipment, electrical materials, kitchen, and other household tools. LSR can be molded into a single or dual-sided injection. They can also be over-molded into other liquid silicone materials. LSR mold cavities can be used to create a wide range of materials, from regular parts like gaskets to complex instruments.
High temperatures resistance:
LSR has outstanding thermal stability. It doesn’t lose shape when subjected to high temperatures and can withstand extreme cold. It remains flexible even at low temperatures that go below -400C. This is why it is now embraced for various consumer products like ice trays, complex industrial tools, muffin trays, etc.
Hygiene:
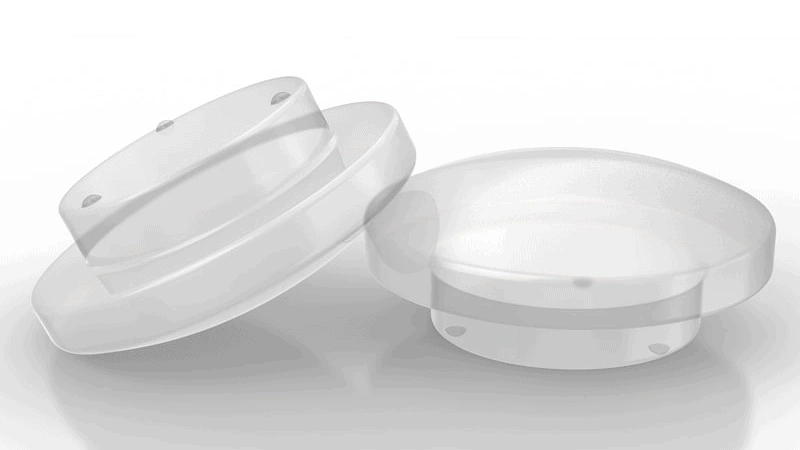
There’s little wonder why liquid silicone rubber is now used for many kitchen utensils. The non-porous nature of this rubber makes it a favorable choice. The use of LSR in the kitchen removes the burden of bacteria pile-ups, hence its usefulness in beverage and food preservation/preparation. Silicone is not toxic. It is water-resistant and can be recycled at designated plants.
Moisture resistance:
you can throw LSR molds into boiling or warm water without fearing negative impacts. It can also resist oils and other chemicals without dissolving or losing shape with time. These are some of the reasons LSR design features make it desirable for plumbing tools, medical applications, and other equipment that needs regular steaming or chemical sterilization.
Low compression set:
This means that it is opposed to complete deformation when subjected to consistent strain. The compression set of LSR molds ranges from 15% to 20%. They retain their shape and flexibility even when suppressed for a long time and subjected to temperatures.
Electrical insulators:
Liquid silicone rubber is also more desirable because it resists corona discharge, hence a perfect insulator. However, it isn’t out of place for LSR to have conductive properties, which makes it great for keyboards and other electronic components.
Flexibility:
LSR can be molded into any desired shape. Apart from its compression set, it easily takes in vibrations without altering its performance. LSR molds are an excellent choice for producing tools and other appliances that demand high endurance.
Take the First Step:
Requst for an Inquire
Quality Meets Affordability. Inquire Now for High-Quality Products at Low Volumes.
How Does Liquid Silicone Rubber Molding Work?
Liquid silicone molding is done with two silicone rubber content in the molding cavity. These properties, in turn, produce a chemical reaction that births the end product of the mold. Liquid silicone is almost the same as popular injection molding in terms of how the shapes are formed in the mold. They differ when it comes to the way it cures the shapes.
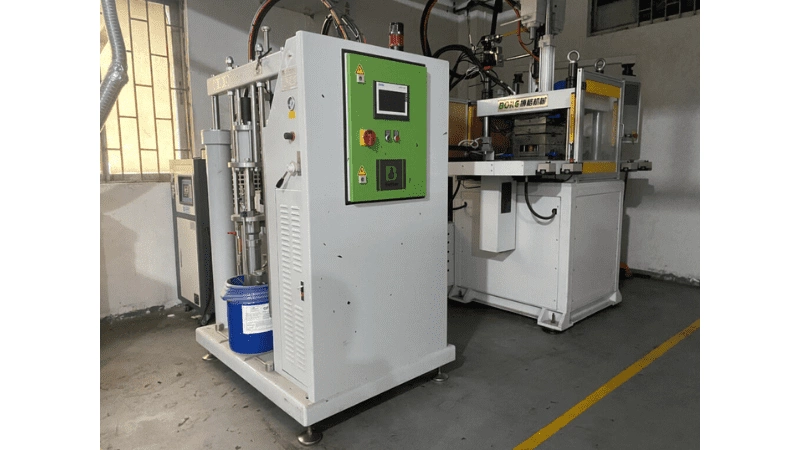
Molding an LSR injection requires thermosetting by mixing two different materials. Both materials are treated with heat using what is known as a mold conductor. After the treatment, a mold is used to deliver the finished fabric. Like what is obtainable in plastic shot molding, LSR parts are made with an injection molding process.
However, both processes are dissimilar in a lot of ways. The mechanical compound is stabilized in plastic injection molding instead of the pressure barrier compound in plastic shot molding. For LSR injection molding, the system is allowed to cool and take shape, after which it is heated gradually.
Once the LSR has taken shape, it becomes impossible to revert or improve it because it takes a lot of strength to break down the linked product.
An elastic substance transformed into a core part of medical tools, liquid silicone rubber (LSR) injections are also used in automotive, consumer, aerospace, and power applications. The LSR as thermosetting elastic shows considerably high elasticity, perpetually high-temperature performance, and it’s less sensitive to ultraviolet (UV) rays. It generally has beneficial biocompatibility.
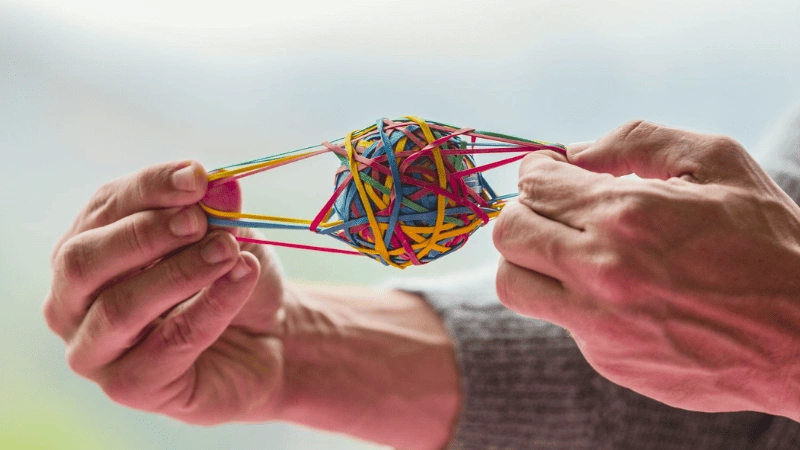
There’s a technique used in LSR injection molding that enables the creation of many products used in multiple industries, including healthcare, consumer goods, automotive, and aerospace. Not only does the process require technical and physical precision, but it also entails rigorous quality control processes to ensure its reliability and safety for end-users.
When used in the liquid injection molding process, they come in two forms: platinum-cured polymers which are the most stable. The Platinum-cured LSR is poured into two different drums labeled A and B. When the content of A and B are mixed inside the injection nozzle of the machine, the curing process, otherwise known as the vulcanization process, starts.
If you want colored parts, you must add another liquid with the desired color pigment to the barrel. The vulcanization process becomes more intense when it gets to the hot mold cavity. At this point, it becomes solid and takes shape.
Take the First Step:
Requst for an Inquire
Quality Meets Affordability. Inquire Now for High-Quality Products at Low Volumes.
LSR Molding Design Considerations
To design an LSR molding, some things must be considered as they will go a long way in determining the outcome of the process. Creating a suitable mold is one of the most important factors to consider if you must get the most accurate LSR product of high quality. To meet production standards, here are some of the things you must consider:
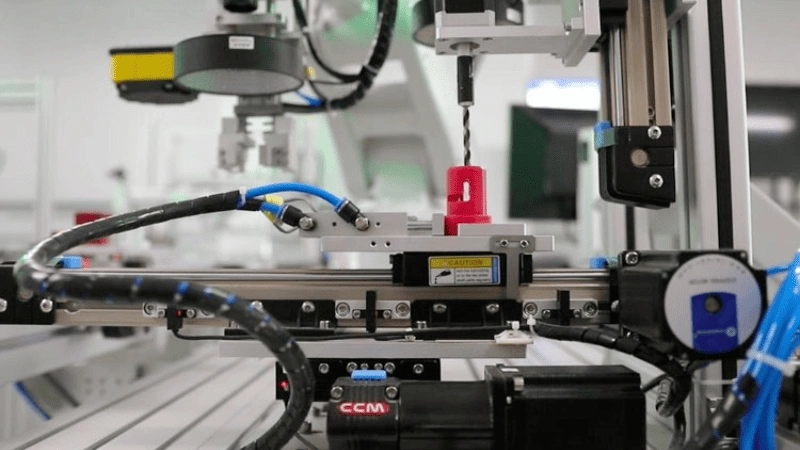
Function:
What will the mold or part be used for? This is the first consideration of the design process. Are you designing a medical device that’ll be inserted into the body for many years? Is it a button on a device, automobile, or knob part? Will it be used in a disposable material or a high-endurance tool?
The purpose of the design determines the level of exposure it will face, which affects its material selection, shape, and other aspects. This requires a thorough assessment of the requirements of the product and the production process at the very beginning of the development process. It’s crucial to have a clear picture of the design’s purpose and its intended use to ensure its optimum performance and quality.
Size:
The manufacturing process of liquid silicone rubber parts is also influenced by the size of the part and the production volume of the LSR molding process. Mass production needs more time to cure silicone instead of smaller productions. Mass production also means that you’ll spend more money on purchasing materials.
The size of the mold design also determines the ejection and manufacturing process. Fragile parts, for instance, may end up with dents and disfigured surfaces during the production process. You may then decide to use finishes to guard against this.
Will the part require sterilization, or will it be dispensable? You’ll have to incinerate disposable products to get more freedom with the choice of material. This isn’t the case with those subjected to constant sterilization. Liquid silicone rubber molds that will be sterilized with steam will require high resistance to hydrolysis and heat.
On the other hand, those that will be fixed with ethylene oxide (EtO) must be chemically resistant. On the other hand, Gamma, e-beam, and UV sterilization demand that you use other materials. Note that only a few materials for parts need sterilization with different methods during use.
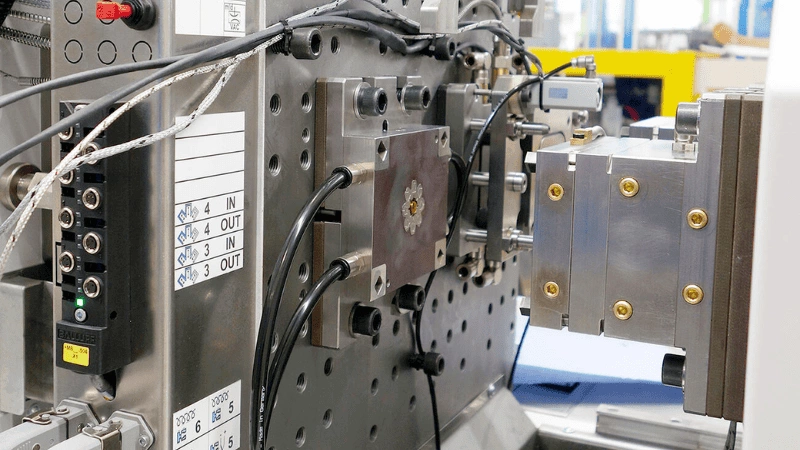
Shot size:
For LSR injection molding, size is an essential consideration in the manufacturing process. While anything below ten cubic cm. is not acceptable for some manufacturers, some mold construction permits either LSR Multi-Shot Injection or LSR 2-Shot.
There’s something called liquid silicone rubber over-molding, twin-shot molding, and multi-shot injection molding. This procedure has to do with molding the LSR into a substratum containing a thermoplastic. This happens shortly after forming the substratum. The process occurs in the same mold with the machine and the LSR.
When you use the liquid silicone rubber multi-shot technique, you’ll be able to add different materials or parts to a particular component that could be combined permanently. The two-part silicone rubber molding gives room for the best materials in the end product. This may remove the need for an assembly process to enhance the cosmetic appearance at the end of the production.
Take the First Step:
Requst for an Inquire
Quality Meets Affordability. Inquire Now for High-Quality Products at Low Volumes.
Conclusion
In conclusion, liquid silicone rubber injection molding has revolutionized manufacturing with exceptional thermal stability and versatility. LSR’s durability, chemical resistance, and long-lasting performance can prolong the lifespan of critical products, making it an excellent choice to enhance quality and safety.
As a result, LSR injection molding is a worthwhile investment to improve product quality without compromising cost efficiency. It’s essential to partner with a reliable supplier and follow a detailed design guide like ours to maximize results.
Buy High-Quality Silicone Rubber Products from Hongju
Discover more about Hongju Silicone and the silicone rubber products we’re proud to offer. We’re committed to providing high-quality custom solutions and are ready to assist you with your requirements. Visit our website and reach out to our team to take your product development to the next level.