Are you in the middle of a project and can’t figure out whether you need a seal or a gasket? Not to worry, because this guide has it all. We will break down their critical distinctions so that the gasket vs. seal debate ends once and for all. If you are an engineer or a manufacturer and you need to master the essentials of sealing solutions, then get reading.
The definition of Gaskets and Seals
Seals are the guards of machinery that prevent products from leaking and contamination from getting inside. The purpose of a seal is to create a leakproof connection between two objects. Seal is a broader term that encompasses many types of products, including gaskets, rotary seals, mechanical seals, O-ring seals, liquid sealants, shaft seals, and valve stem seals.
On the other hand, a gasket is a subtype of seal that is physically placed between two flanges to create a sealant joint. Gaskets are the static seals that are used to fill up space between stationary components of a machine. While all gaskets are seals, not all seals are gaskets.
A seal, however, is designed to cover all sorts of joints, whether static or rotatory. Many types of rotary seals are designed to accommodate moving parts while preventing leaks.
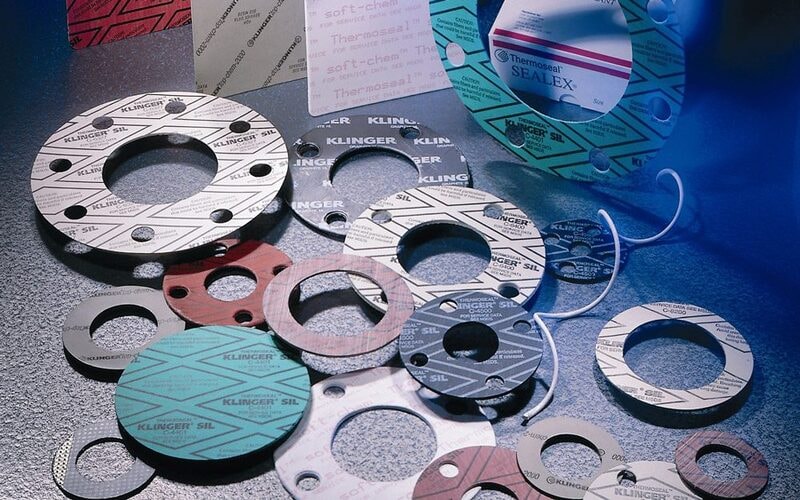
Types of Seals
Engineering is deployed in all industrial applications, from the manufacturing industry to aerospace and even medicine. Seals are essential engineering components that connect two surfaces without altering functionality.
You have to understand the basic types of sealing components and their roles to be able to choose the ideal solution for your needs. Here is a list of the most common seal materials used in the manufacturing process.
- Gaskets: A static seal made with elastomeric materials. Gaskets seal flat and non-moving parts together, such as flanges. They are critical parts of machine building and engineering.
- Rotary Seals: These form a secure connection between a rotating and a stationary component of a machine. Their job is to protect electrical motors and equipment from damage.
- Mechanical Seals: These seals have three components: a rotating part, a stationary part, and a spring. They are critical for sealing rotating shafts. The spring maintains pressure to ensure the seal remains intact during movement.
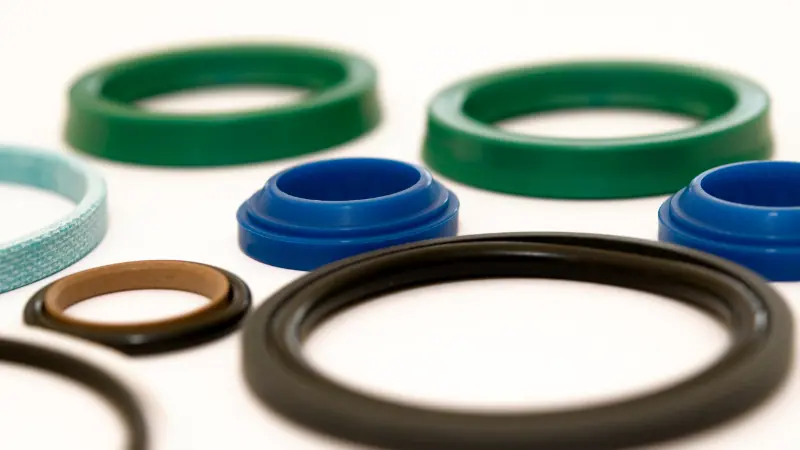
- Shaft Seals: These are also deployed in machines where one moving part is connected to a stationary part and a high level of sealing is required. It has three components, including a mechanical seal, an impression seal, and a shaft sleeve.
- O-Ring Seals: These are versatile seals mostly made from synthetic rubbers to bear fluid exposure. They perform excellently in high pressure and are mostly used in hoses.
- Valve Stem Seals: These are located in the valve systems and control the amount of oil that lubricates the valve stem. They are highly critical in engines.
Materials and Properties
While the characteristic property of gaskets and seals is to form joints and prevent leakage, their individual properties vary depending upon the material used in construction. Both materials can be made from a variety of materials, including natural rubber, synthetic rubber, metal, and plastic.
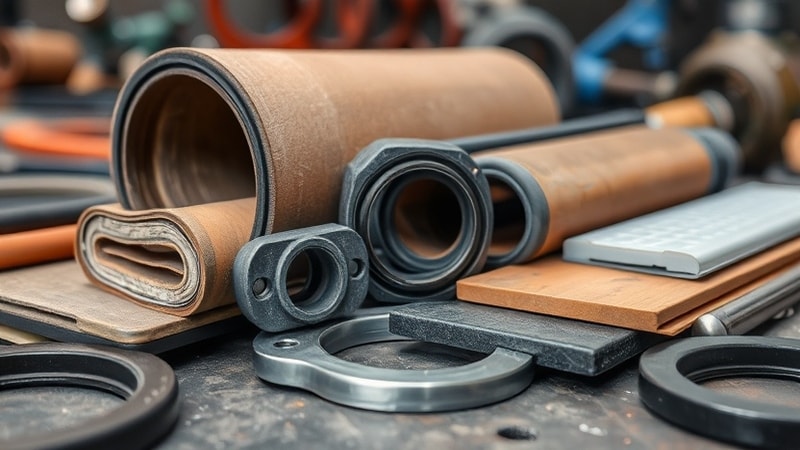
However, material selection for sealing gaskets depends on your application’s specific requirements, such as temperature resistance, chemical resistance, durability, etc.
Gasket Materials
Gaskets are made from materials that can endure static conditions. These conditions involve sustaining pressure, temperature, and chemical exposure as well. Here are some of the materials used in gasket manufacturing.
- Metal: The metal gaskets do not offer much flexibility, but they are ideal for high-pressure applications and are often deployed in industrial machinery and automotive settings.
- Plastics: Gaskets made with plastics such as PTFE are famous for their chemical inertness, making them particularly suitable for corrosive environments.
- Natural Rubber: gaskets made from natural rubber are created for general-purpose applications. They offer excellent flexibility and tensile strength.
- Synthetic Rubbers: EPDM, Neoprene, or NBR are synthetic rubbers used in gasket manufacturing. Such gaskets are highly resistant to oil, temperature, and weather damage.
The extent of functionality of a gasket depends on the type of material, so choose wisely.
Seal Materials
A seal material seals depending upon its construction material properties. Seals are often used in dynamic applications; hence, they require materials that can withstand all sorts of motion while maintaining equipment integrity.
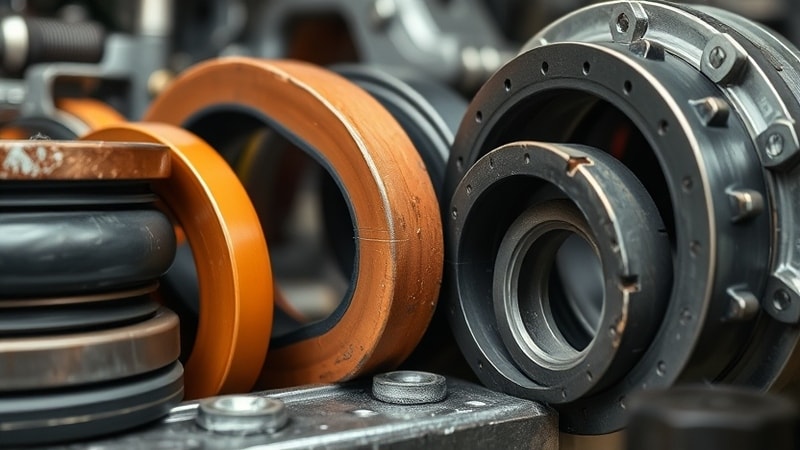
- O-Ring Materials: O-rings are tasked with fluid containment in high-pressure environments. The suitable material for this application is synthetic rubber or silicone.
- Plastic and Metal Seals: These are created for extreme environments to provide high tensile strength and resistance to all situations.
- Mechanical Seal Materials: These seals are integral to maintaining the functionality of highly technical equipment. They are often made with composite materials such as silicon carbide or tungsten carbide to combine durability with wear resistance.
Applications and Considerations
Gaskets and seals serve a critical role in forming connections between multiple systems. One key difference between a gasket and a seal is their application. While functionality is the same, to prevent leaking, their applications differ based on the type of joint and the extent of sealing required.
Gaskets are used in conditions where static seals are required. Static joints are connection points for two stationary parts of machinery. They are used to form flange connections in pipelines and industrial machinery. Moreover, gaskets are used in engine parts to connect one flat piece to another.
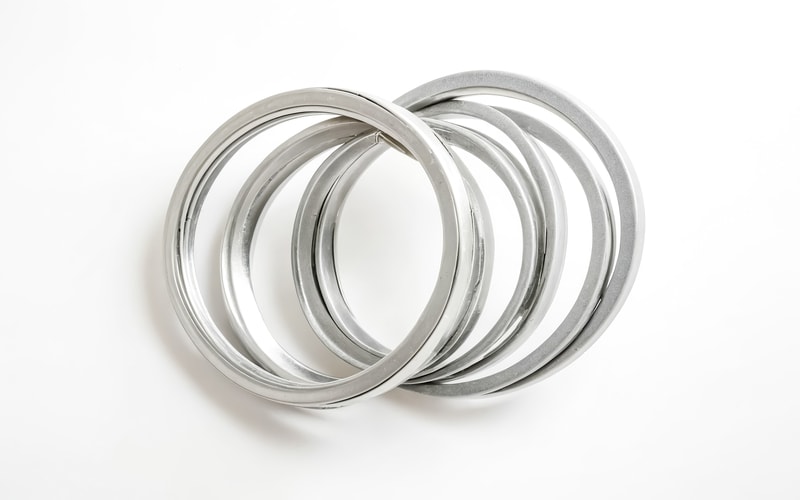
Seals are designed to join two moving parts or one moving part to a static joint. Their applications are versatile, as they are found in almost all machines in the world. A few common examples include rotary seals in pumps and motors to prevent leakage around rotating shafts.
O-ring seals are used in cylinder heads to control water or gas flow. Valve stem seals are deployed in engines to control oil flow into the combustion chamber.
Considerations for Gasket and Seal Selection
There are several factors that come into play when deciding between a gasket and a seal. The first consideration is the operating conditions. You need to monitor the extent of your application’s exposure to temperature, pressure, chemicals, and fluids.
The second step is to match the gasket and seal material specifications to your project intricacies. The material you choose should be resistant to your project conditions, such as exposure to corrosive substances.
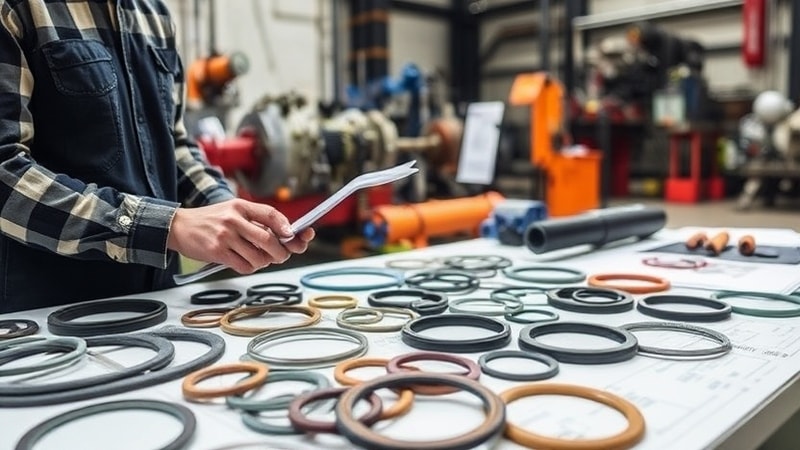
Lastly, considering the cost of the sealing solution is also important. Most gaskets and seals found online or in hardware stores are inexpensive and available in multiple sizes to cater to a variety of operations.
However, if an off-the-shelf solution does not meet your requirements, then you can opt for a customized gasket or seal. The custom designs are created for specialized applications to meet precise operational demands.
Customization and Sourcing Options
If you cannot find the right sealing solution for your project, then you have to opt for custom gaskets and seals. A custom design can be created to address your operation’s unique needs, such as unusual shapes, extreme operating conditions, and material compatibility.
Whether you need your sealant to handle high pressure, extreme temperature, or harsh chemical exposure, a custom design will handle everything to ensure optimal performance. Whether it’s handling high pressure, extreme temperatures, or exposure to harsh chemicals, custom solutions provide the adaptability required for demanding environments.

Sourcing Custom Solutions
Customized seals and gaskets can be created by a manufacturer. Choosing a custom design has its own benefits, such as increased quality and specific characteristics. By going down this path, you can also streamline the production of your project due to faster production time.
Custom gaskets and seals significantly enhance the efficiency and lifespan of industrial applications. Thus, making this investment is always a smart choice while working on demanding projects.
However, there are some things you should keep in mind while sourcing custom sealing solutions.
- Ensure that the manufacturer and supplier can meet your project deadlines.
- evaluate the cost of the material with that of the final product
- only partner with vendors who adhere to international standards such as ASTM D2000
- make sure your product is molded to your specific requirement
Testing and Validation
Gaskets and seals must be rigorously tested and validated to ensure optimum performance and durability. These stages are critical for ensuring that the sealant successfully joins two components and prevents leaks. They also validate that the material can resist the operational demands of your application.
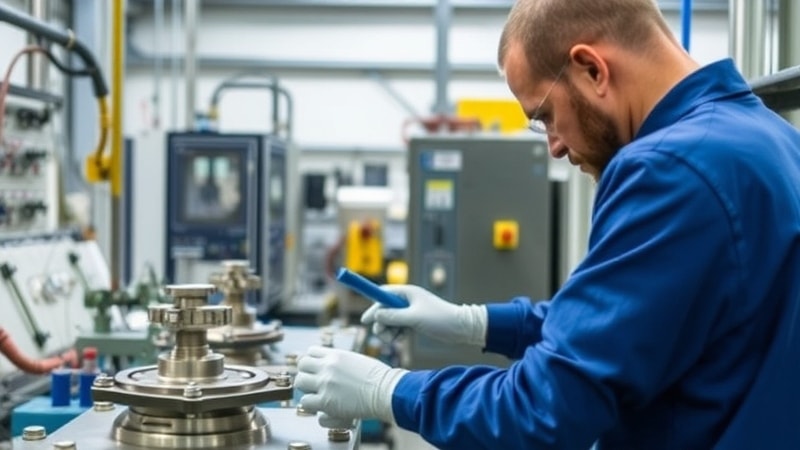
Testing methods
Compression Testing | Verifies a gasket’s ability to maintain a seal under pressure. |
---|---|
Tensile Testing | Measures the strength of materials to withstand pulling forces. |
Leakage Testing | Identifies potential points of failure by simulating real-world operating conditions. |
Validation Approaches
Inspection | Examines dimensions, materials, and surface finishes to ensure compliance with design specifications. |
---|---|
Performance Testing | Confirms that gaskets and seals function as intended under specified conditions. |
Certification | Provides documentation that materials and products meet industry standards, such as ASTM D2000. |
Proper installation and maintenance are key to ensuring the effective performance of a gasket or seal. common installation techniques ranging from hand installation for small-scale operations or machine-automated installation for complex assemblies requiring high accuracy.
The maintenance protocols are necessary to ensure optimum functionality till the end of the life of the product. It starts with an inspection, where you can check for signs of wear and tear or notice misalignment. Then comes cleaning to ensure all debris and residue is removed. And lastly, replacement of worn or damaged components to prevent failures.
Troubleshooting and Repair
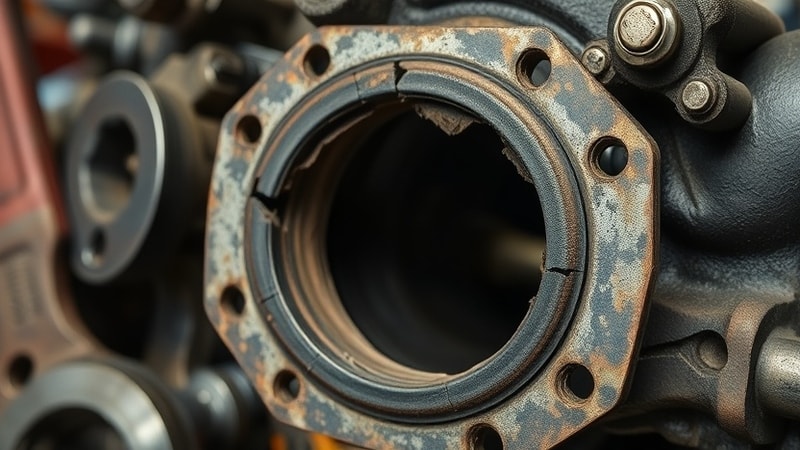
Like all other machine components, sometimes gaskets and seals also fail. The factors that cause them to fail include improper installation and maintenance. Even material stress like exposure to incompatible chemicals can degrade materials, causing failure.
In such situations, troubleshooting becomes compulsory. If your product fails to deliver, the first step is to inspect it thoroughly and check for any cracks, distortions, or leaks. Then perform tests to pinpoint failure points and analyze the contributing factors that might have led to failure.
The solution in such situations is the replacement of damaged material with new ones. To enhance security, you can apply a protective coating to extend the life span of the seal.
How to Choose the Right Gasket or Seal for Your Project
Choosing the right gasket or seal for your application is critical to maintaining operating efficiency and avoiding costly breakdowns. Here are the main aspects to consider when making your decision:
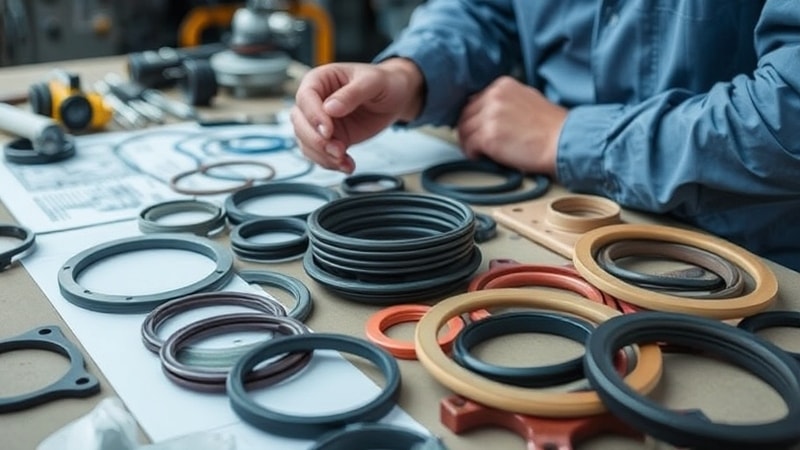
- Material Compatibility: Consider factors such as temperature ranges, pressure levels, and chemical exposure. For example, high-temperature environments might require materials like silicone or PTFE, while EPDM and neoprene offer the best chemical resistance.
- Application Type: Determine whether your application involves a static joint or a dynamic joint. Gaskets can be used for static joints, seals for dynamic joints, and custom seals for complex joints
- Durability and Expected Lifespan: Assess the expected wear and tear on the sealing component. You might have to apply coating if it is intended for a high-stress environment to ensure a long life span.
- Customization Needs: If your application is truly unique and traditional seals do not fit properly, then opt for customized designs.
Frequently Asked Questions
Q1: How do I know when to replace a gasket or seal?
A2: Replacement is necessary if your gasket breaks; however, if you notice extreme wear and tear, then it is better to replace it before it fails
Q2: What is the fundamental difference between gaskets and seals?
A2: Gaskets are designed for static applications where two surfaces are stationary, while seals are used for dynamic applications involving movement between components.
Q3: Is it worth it to invest in a Custom seal and gasket solution?
A3: When the project is too complex to be completed by regular materials then obtaining custom solutions is the only way to go. A set of custom gaskets and seals pay back the price by offering premium functionality and a longer lifespan.
Conclusion
Gaskets and seals are essential components in manufacturing processes, each providing specific functions. While gaskets are suitable for static joints, seals work well in dynamic settings. Choosing the proper component ensures maximum efficiency, longevity, and cost-effectiveness.
Discover the perfect sealing solution with Hongju
As a leading manufacturer with over 15 years of industry experience, we specialize in delivering high-quality sealing solutions tailored to meet your specific needs.
Contact us today to request a consultation or explore our comprehensive product catalog.