However, selecting the ideal sealing material can be challenging due to various factors such as strict requirements such as extraction, production, heat, and performance requirements. That’s where we come in! Join us as we explore different sealing solutions and materials suitable for food-grade o-rings. Let’s dive into this important topic without compromising on quality or safety!
What is an O-ring?
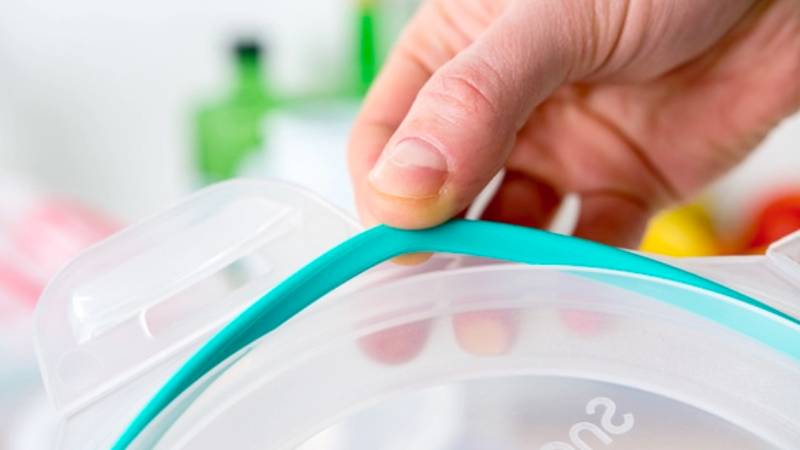
An O-ring is a type of gasket or sealing ring that is commonly used in various industries, including the food-grade sector. It is designed to create a tight seal between two or more parts, preventing leakage and ensuring the integrity of the system.
Definition and Basic Characteristics of An O-ring
An O-ring is typically made from elastomer materials such as rubber or silicone. These materials possess unique properties that make them ideal for sealing applications. The O-ring has a circular cross-section and is shaped like a doughnut, with a hole in the center.
O-rings are known for their flexibility and resilience. They are highly flexible and can be compressed to fit into grooves or gaps between mating surfaces, creating a secure seal. Due to their elasticity, they can return to their original shape after being compressed or stretched, maintaining the sealing effectiveness over time.
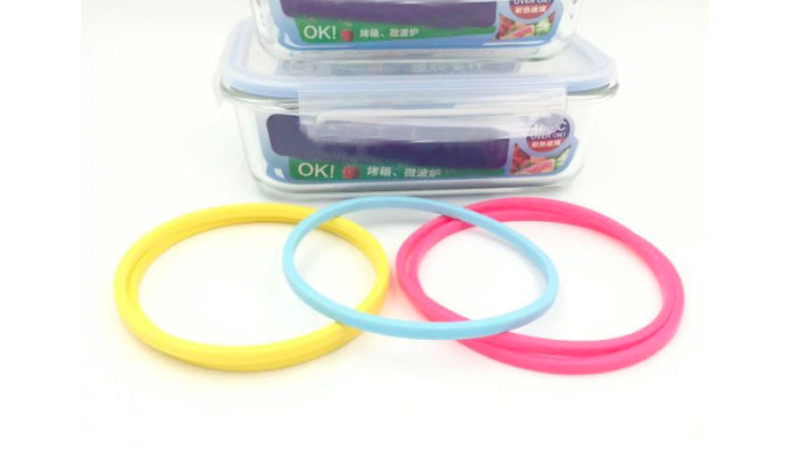
Explanation of How O-rings Function as Seals
The primary function of an O-ring is to prevent fluid mineral oil or gas from escaping between two surfaces. When placed in a groove or gap, it forms a barrier that blocks any potential leakage paths. The compression force applied during assembly causes the food-grade seals O-ring to deform and conform tightly against the mating surfaces, effectively sealing off any gaps.
The key to its effectiveness lies in its ability to maintain contact pressure even under varying conditions such as high temperature changes, pressure differentials, and mechanical movements. This ensures that the seal remains intact regardless of external factors.
Key Features of O-rings
O-rings offer several advantages that make them well-suited for diverse applications:
- Versatility: O-rings can be used in static (non-moving) as well as dynamic (moving) applications.
- Wide temperature range: They can withstand extreme temperatures ranging from -50°C (-58°F) up to 250°C (482°F), depending on the material used.
- Chemical resistance: O-rings are resistant to a wide range of chemicals, including oils, fuels, solvents, and ozone.
- Pressure tolerance: They can handle high-pressure environments, making them suitable for sealing applications in hydraulic and pneumatic systems.
- Cost-effective: O-rings are relatively inexpensive compared to other sealing options.
Criteria for Food-Grade O-Rings
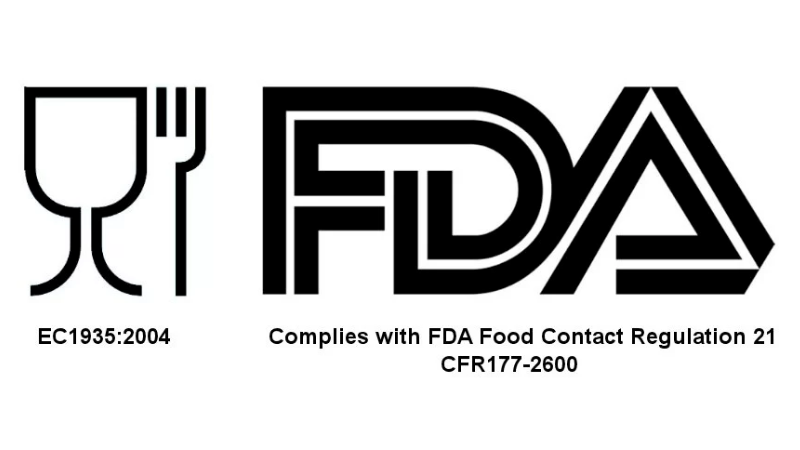
Food safety is of utmost importance. These o-rings are extensively utilized in the food and beverage industry to maintain the integrity of equipment and prevent contamination. To ensure that these sealing materials meet the required standards, various criteria must be met, including compliance with regulatory bodies such as the FDA or the European Framework Regulation EC 1935/2004.
Importance of Using Compliant Materials
Using compliant materials for food-grade o-rings is essential for maintaining food safety throughout the production process. These o-rings are in direct contact with food products, making it imperative that they do not introduce any harmful substances or contaminants. Compliance with food-grade standards ensures that only safe and suitable materials are employed, minimizing potential risks.
Consequences and Risks of Non-Compliant Materials
Using non-compliant materials for food-grade O-rings can have severe consequences. These materials may introduce toxic substances, leach chemicals, or harbor bacteria, leading to contamination of food products. Such contamination can result in health hazards for consumers, product recalls, damage to brand reputation, and legal repercussions.
Different Food-Grade elastomers for making O-rings.
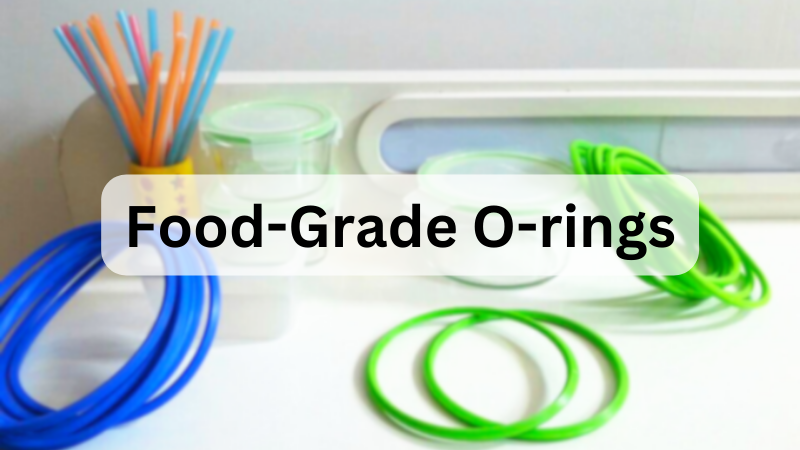
Creating food-grade O-rings requires a careful selection of elastomers to ensure safety, performance, and compliance with health regulations such as the U.S. Food and Drug Administration (FDA) guidelines or the European Framework Regulation EC 1935/2004.
Food-Grade Elastomers for Making O-rings
FDA-grade materials are selected for their durability, chemical compatibility, and resistance properties. Here’s a closer look at the best FDA-approved o-rings.
- Silicone (VMQ): FDA-approved silicone is widely used due to its excellent temperature resistance, non-toxicity, and compression set resistance. It’s ideal for applications requiring a seal over extended periods.
- Ethylene Propylene Diene Monomer (EPDM): EPDM offers high temperature resistance reaching +350°F. Known for its excellent resistance to hot water, steam, and various food and beverages, EPDM O-rings are popular choices for food and beverage applications.
- Nitrile Rubber (NBR): White food-grade nitrile rubber is commonly used due to its excellent oil and grease resistance. It’s FDA-approved and suitable for various food and beverage applications.
- Fluorocarbon (FKM, Viton): Some FKM variants are FDA-approved and offer high heat and chemical resistance. This makes them suitable for food processing equipment, especially under harsh conditions.
- Perfluoroelastomer (FFKM): Offering exceptional heat and chemical resistance, FFKM is used for O-rings in demanding food processing environments. While expensive, its performance can justify the cost in certain applications.
- Teflon (PTFE): Although not an elastomer, PTFE is used in O-rings due to its excellent chemical resistance and wide temperature range. It’s also FDA-approved, making it suitable for food and beverage applications.
With the use of such FDA-approved materials, food-grade O-rings not only withstand the speed and abrasive demands of continuous operation but also meet a rigorous standard of quality and cleanliness.
Pros and Cons of Different Food-Grade Sealing Materials
Here’s a table that compares the advantages and disadvantages of different food-grade sealing materials for O-rings:
Material | Advantages | Disadvantages |
Silicone (VMQ) | High-temperature resistance, non-toxic, odorless, tasteless, good compression set resistance | Lower tensile strength, less wear resistance |
EPDM | Excellent resistance to hot water, steam, and various food and beverages, good weatherability | Poor resistance to oils, greases, and solvents |
Nitrile Rubber (NBR) | Excellent oil and grease resistance | Lower temperature and chemical resistance |
Fluorocarbon (FKM, Viton) | High heat and chemical resistance | Not all grades are FDA-approved higher cost |
Perfluoroelastomer (FFKM) | Superior heat and chemical resistance | Higher cost limits used to demand applications |
Teflon (PTFE) | Excellent chemical resistance and wide operating temperature range | Lower flexibility due to not being an elastomer, harder to install |
The right choice will depend on the specific requirements of your application, including the types of food or beverages involved, cleaning processes, operating temperatures, and budget. Always ensure that the chosen material is food-grade and complies with relevant safety regulations.
Factors Influencing Material Selection for Specific Applications
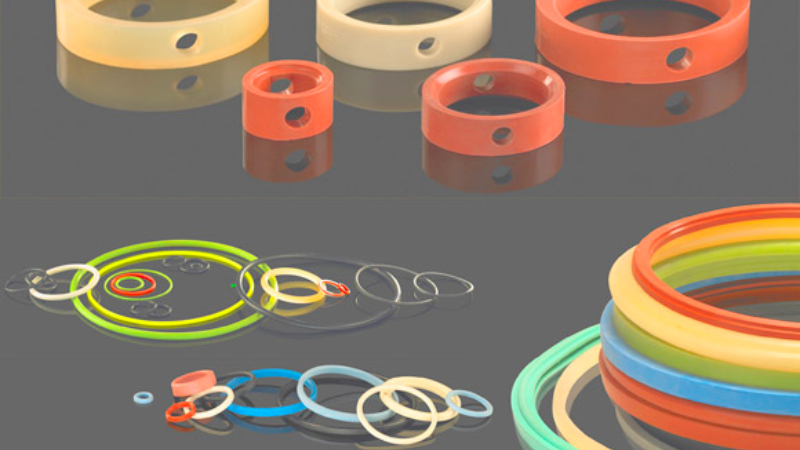
When determining the best sealing material for food-grade o-rings, various factors come into play. These include:
- Non-Toxicity: Food-grade o-rings should be made from non-toxic materials that do not leach harmful substances into the food.
- Low Extractables: These sealing materials should have low levels of extractable compounds to avoid contamination.
- Chemical Resistance: O-rings need to resist chemicals commonly found in food processing environments without degradation or leaching.
- Temperature Resistance: They should withstand a range of temperatures prevalent in different stages of food production.
- Hygiene Maintenance: The material should facilitate easy cleaning and sterilization procedures.
By carefully considering these factors and understanding the unique properties of different elastomers, manufacturers can choose the most suitable material for their specific food-grade o-ring applications.
Preventing Contamination in Food-Grade O-Rings
Food-grade o-rings play a critical role in maintaining the integrity and safety of food processing equipment. However, these essential components can be susceptible to contamination if not handled and maintained properly.
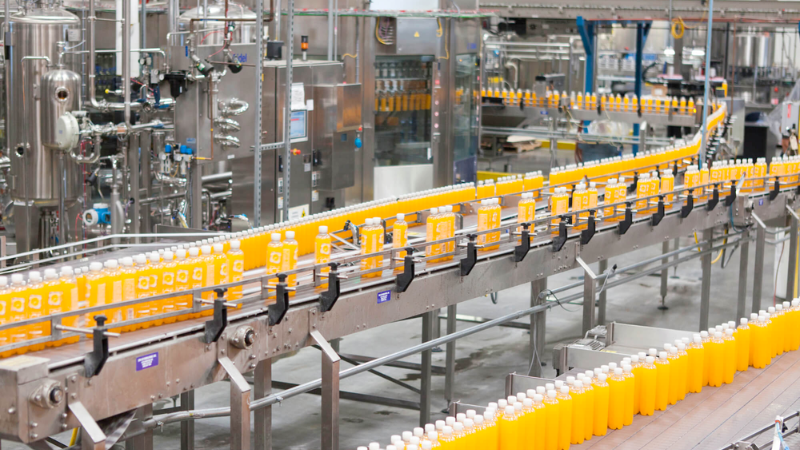
Potential Sources of Contamination
In food processing, factors such as high temperatures, steam, and chemical contaminants are common. Contamination in food-grade o-rings can originate from various sources throughout the manufacturing, storage, and usage processes. It is crucial to identify these potential sources to implement effective preventive measures. Some common sources include:
- Raw Materials: The materials used for manufacturing food-grade o-rings must comply with strict regulatory standards for food contact. Any impurities or contaminants present in the raw materials can pose a risk to food security.
- Cross-Contamination: During the production process, there is a possibility of cross-contamination if equipment or tools used for non-food applications come into contact with food-grade o-rings.
- Storage Conditions: Improper storage conditions, such as exposure to chemicals or extreme temperatures, can compromise the quality and safety of o-rings intended for use in food processing.
Best Practices to Prevent Contamination

To ensure the highest level of hygiene and prevent contamination in food-grade o-rings, several best practices should be followed throughout their lifecycle:
- Material Selection: Choose o-ring materials that are specifically designed for food contact applications. Look for certifications like FDA (Food and Drug Administration) compliance or NSF (National Sanitation Foundation) certification.
- Manufacturing Processes: Employ stringent manufacturing processes that minimize the risk of contamination. This includes maintaining clean production environments, using dedicated equipment for food-grade applications, and implementing proper cleaning procedures between production runs.
- Sensitive Environments: In sensitive environments like cleanrooms, take additional precautions to prevent contamination. Implement strict gowning procedures, including the use of gloves and hairnets, to minimize the introduction of foreign particles.
Conclusion
In conclusion, It is crucial for the dairy industry to prioritize safety and compliance with industry standards.
The FDA-approved sealing materials, such as nitrile rubber, offer excellent resistance to oils and chemicals commonly found in food processing environments. These materials ensure that the O-rings maintain their integrity and prevent contamination of the food products.
Discover the Perfect O-rings for Your Business with Hongju
Hongju Silicone is pleased to offer a wide variety of O-rings for your business needs. From food-grade gaskets to food-grade O-rings, we offer a range of O-rings to suit your specific needs.
Our inventory includes numerous sizes, shapes, materials, and colors to meet your needs, whether you are looking for a quick fix or a long-term solution.
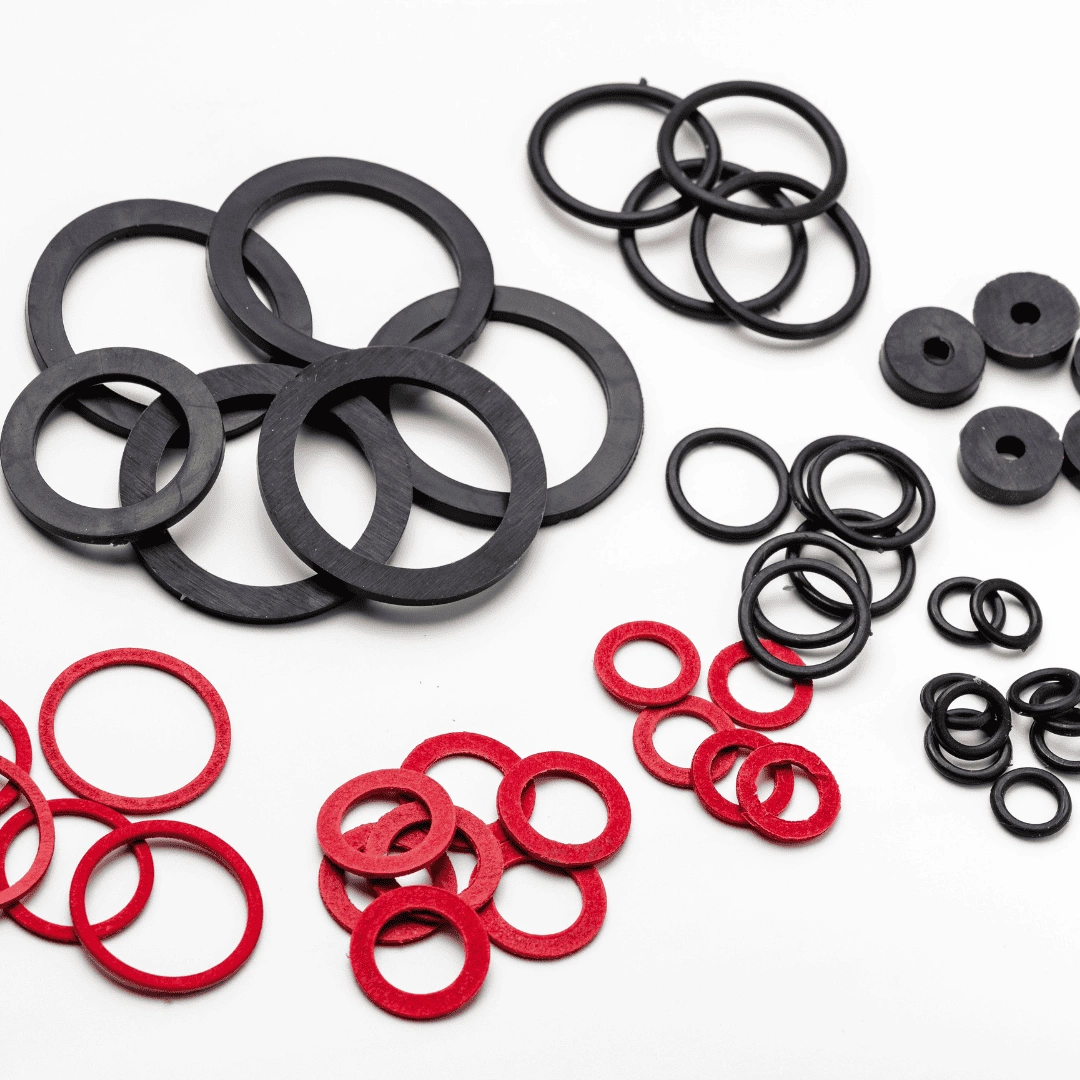
Send Your Inquiry Now!
Quality Meets Affordability. Inquire Now for High-Quality Products at Low Volumes.