Protective surface coatings are ideal for reducing corrosion, improving adhesion, and protecting a substrate from exposure to harsh environmental conditions. Although there are different types of protective coatings, silicone rubber stands out due to its exceptional properties. Silicone rubber finishes are ideal for several industrial applications at a low cost.
This blog explores silicone rubber finishes, the types available, and the techniques for applying this protective coating. You will also learn why this material is ideal for your applications.
What Are Silicone Rubber Finishes?
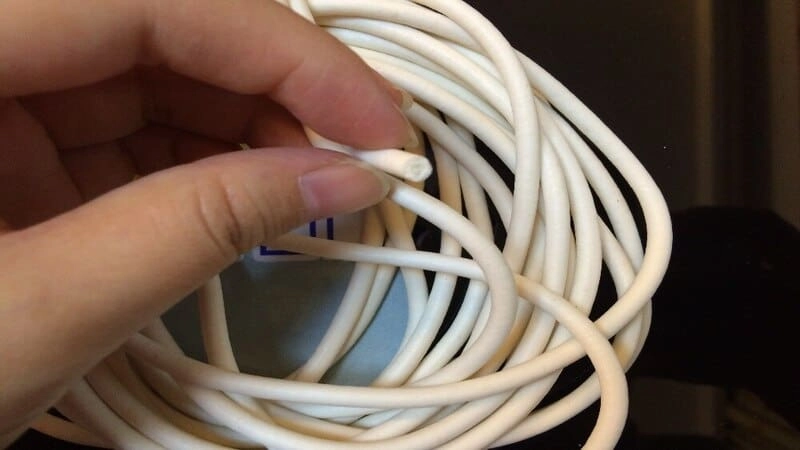
Silicone rubber finishes are protective coatings for various surfaces. This material protects a surface from environmental and chemical factors to improve performance and durability. The base materials of silicone rubber finishes are silicone compounds. Other additives include resins and pigments.
These additives are often cross-linked with the silicone elastomer to improve the chemical and mechanical properties of the elastomer. As a result, the chemical structure of a silicone rubber finish varies depending on its additives. Nevertheless, all finishes share similar chemical structures because of the silicone rubber base constituent.
What Are the Properties of Silicone Rubber Finishes?
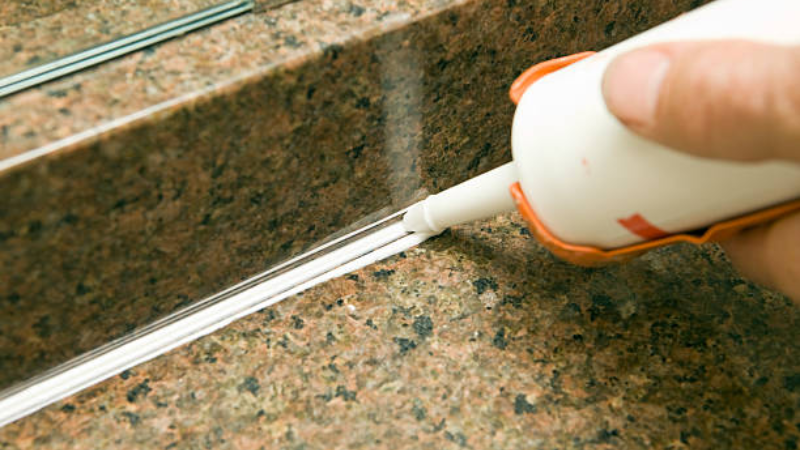
Chemical Resistance
Silicone rubber finishes resist several chemicals, including acids, solvents, and oil. Consequently, this finish is suitable for applications requiring exposure to corrosive substances. However, the chemical resistance of silicone finishes varies depending on their formulation.
Therefore, it is essential to discuss with the coating manufacturer to manufacture finishes that can withstand the conditions of your specific application.
Abrasion Resistance
Excellent abrasion resistance is another property of silicone rubber finishes. This property ensures a surface coated with a silicone rubber finish can withstand mechanical wear and tear.
Consequently, silicone rubber finishes are used for several applications, including automotive, manufacturing, and industrial equipment. Furthermore, the abrasion resistance of a silicone finish depends on its additives and the curing process.
UV Resistance
Silicone rubber has excellent UV resistance. Consequently, silicone rubber finishes are suitable for outdoor applications involving sunlight exposure. Furthermore, silicone rubber finishes can withstand degradation on exposure to UV radiation while retaining their physical properties, including flexibility and hardness.
Thermal Stability
Silicone rubber finishes can withstand extremely low and high temperatures. Silicone rubber finishes can withstand temperatures as low as -60 degrees Fahrenheit and as high as 450 degrees Fahrenheit.
The excellent thermal stability of this material ensures that it retains its physical and chemical properties even upon prolonged exposure to extreme temperatures. Consequently, it is suitable for industry-wide applications, including aerospace components and automotive engines.
Water Repellency
Silicone rubber finishes are water-repellent. They protect coated surfaces from water penetration, preventing corrosion and mildew growth. Consequently, silicone rubber finishes are used for coating architectural and marine components.
Electrical Insulation
Silicone rubber finishes are electrical insulators. This coating prevents the flow of electrical current. Consequently, it is used in several applications, including the manufacture of circuit boards and electronic devices.
Good Softness
Silicone rubber finishes have good softness, making them pliable. Consequently, these finishes are ideal for applications requiring flexibility. The softness of silicone rubber finishes is widely employed in manufacturing medical devices, gaskets, and seals.
What Are the Types of Silicone Rubber Finishes?
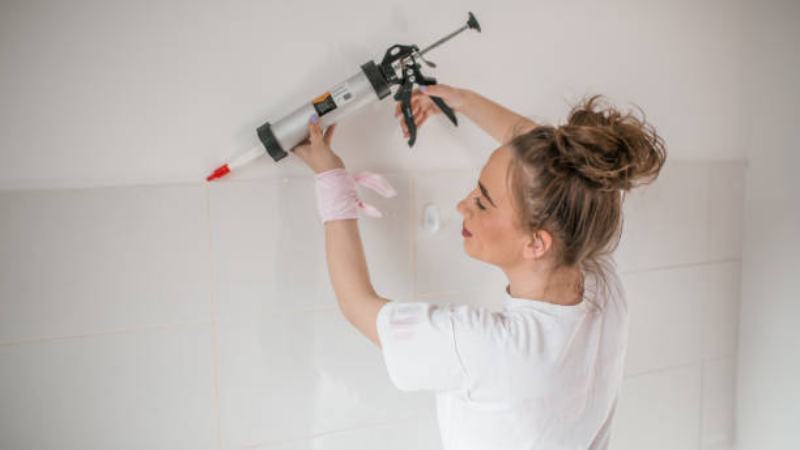
Liquid Silicone Rubber
Liquid silicone rubber finishes are made from a mixture of LSR and a curing agent. This type of finish is applied as a liquid on a surface. They are then cured till solid. LSR finishes have properties including excellent adhesion, biocompatibility, and low compression set. Hence, they are suitable for coating electronic components and medical devices.
Silicone Resins
Silicone resin additives are coatings made from silicone resin. This type of silicone-based finish has versatile properties, including electrical insulation, UV resistance, and chemical resistance.
Silicone resin finishes are often applied as a thin film coating on surfaces. In addition, this finish is often used as a protective coating for metals, plastic, and electrical insulators.
Silicone Elastomers
Silicone elastomer finishes are made from silicone elastomer. Hence, they are flexible and rubber-like. Silicone-elastomer finishes are often applied as a thick film coating, protecting medical devices, prosthetics, and industrial equipment surfaces.
Furthermore, silicone elastomer finish is used in aerospace and automotive applications because of its flexibility, thermal stability, and low compression set.
Silicone Additives
Silicone additive finishes are specialized finishes for specific applications. A silicone additive finish’s performance depends on the additive type used. For instance, flame retardant additives reduce the flammability of a coating and are suitable for applications that require fire safety.
Also, anti-static additives are useful for applications requiring electrostatic discharge protection.
Silica Nanoparticles
Silica nanoparticles finishes have silica nanoparticles in the coating material. The nanoparticles are tiny and interlock to improve the finish’s mechanical strength and abrasion resistance, making them suitable for several applications. The applications of silica nanoparticle finishes include medical devices, automotive parts, and electronic devices.
Advantages of Silicone Rubber Finishes
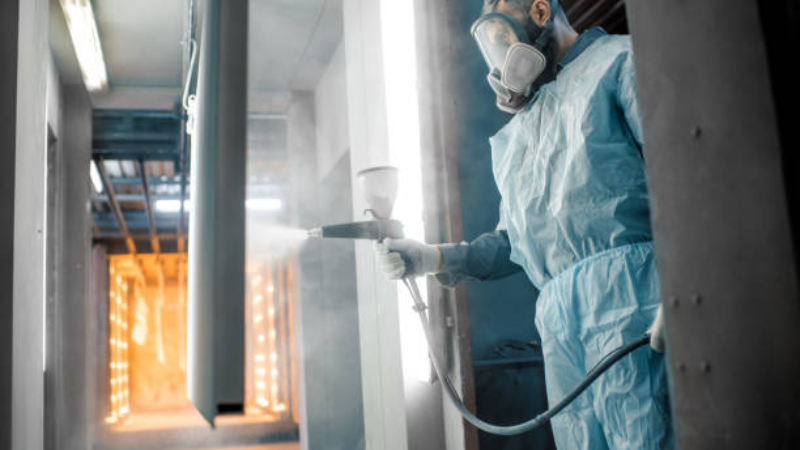
Exceptional Resistance to Various Substances
Silicone rubber finishes are used for several applications due to the material’s exceptional resistance to various substances. This protective coating can resist water vapor and chemicals, including acid, bases, and oils. Consequently, it is suitable for several applications involving chemical exposure across several industries.
Corrosion Protection
Silicone rubber finishes coat a substrate’s surface, creating a barrier between that surface and the environment. Furthermore, because of its water-repelling ability, the silicone finish prevents oxidation on the material’s surface, preventing corrosion.
Surface Modification and Promoting Adhesion
Silicone rubber finishes bond strongly with several substrates, conforming with the surfaces to provide surface modification and adhesion. Furthermore, the excellent properties of silicone rubber, such as high thermal stability and water resistance, promote adhesion, protecting the surface.
Low-cost and Practical Applications
The initial cost of silicone rubber finishes is relatively high. Furthermore, the cost of the silicone rubber finish varies depending on the specific application requirements. However, because this material is useful for several practical applications, it saves costs in the long run.
Non-toxic and Safe for the Human Body
Silicone rubber is an inert material that does not react with many chemicals. In addition, it does not leach even at extreme temperatures. Consequently, the material is safe for the human body and does not cause any adverse effects.
Durability and Long-lasting Coating Systems
Silicone rubber finishes provide a durable, long-lasting coating over a substrate’s surface. Because the material is resistant to environmental impact and abrasion, it protects the substrate’s surface for as long as possible. However, the coating system’s durability depends on the silicone rubber finish type and the application method.
Suitable for Different Substrates and Surfaces
Silicone rubber is versatile and popular for its adhesion to several substrates and surfaces. This protective coating can adhere to metals, plastics, ceramics, and individual fibers. It is also ideal for various construction materials, medical, and electronics.
Practical Applications of Silicone Rubber Finishes
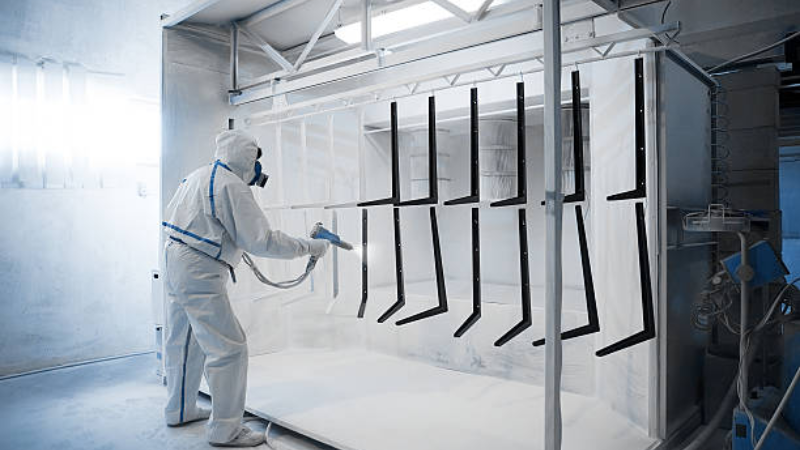
Architectural Coatings
Due to their exceptional UV, water, and abrasion resistance, silicone rubber finishes are used in architectural coatings. These finishes are widely employed in manufacturing roof coatings and exterior coatings. Furthermore, silicone rubber finishes are used as coatings for concrete surfaces like walls and foundations.
Other applications of silicone rubber finish in the architectural industry include coatings for metal surfaces like doors and window frames. The material also creates a waterproof barrier on walls and ceilings, preventing mildew growth and stains, especially in high-traffic areas.
Medical Devices and Drug Delivery Devices
Due to its biocompatibility and high thermal stability, silicone rubber finishes are used in medical and drug delivery devices. These finishes are often used to coat catheters, tubing, syringes, and inhalers. Other applications of silicone rubber finishes include prosthetics and medical gaskets and seals.
Coating Application in the Gas Industry
Silicone rubber finishes have excellent chemical and high-temperature resistance, making them ideal for use in the gas industry. Coating applications in the gas industry include gas storage tanks and regulators. The finish is also used to coat gas pipelines because it is water-repellent.
Industrial Applications
Silicone rubber finishes are used across several industries, from construction to electrical. For example, the coating is used in industries to prevent corrosion on machinery and equipment. In addition, the material is used for electrical components like wiring and cables, providing insulation.
Other industries that use silicone rubber finishes are the automotive and aerospace industries. The coating is used to coat components frequently exposed to high temperatures and harsh conditions.
Personal Care and Cosmetic Products
Silicone rubber finishes are used in the skincare and haircare industries. Due to its water resistance, silicone finishes are used in sunscreens, lotions, and moisturizers, to give the skin a silky and smooth feel. The coating also enhances water resistance, ensuring the skin care products last as long as possible on the skin.
In addition, hair care products like shampoo, conditioner, and styling products contain silicone rubber finishes. These products protect the hair, providing smoothness and shine and reducing tangles.
New Techniques in Silicone Rubber Finishes
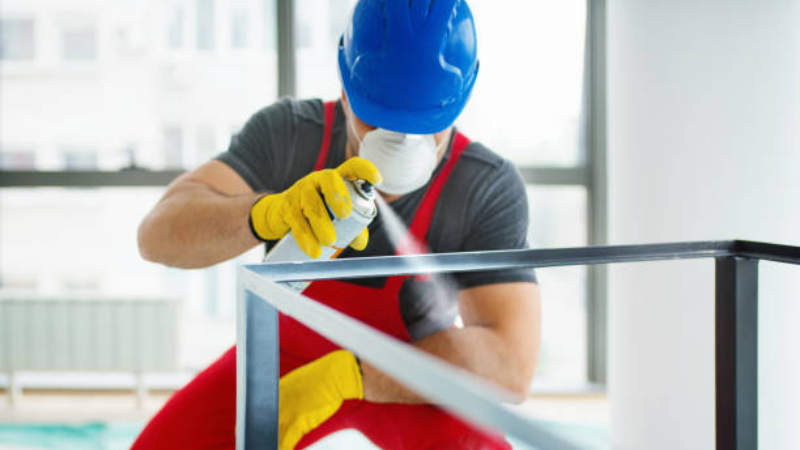
Chemical Vapor Deposition (CVD)
CVD is a process of depositing thin films of materials like silicone on a heated substrate surface to create a silicone rubber finish. The CVD process is versatile, involving the reaction of a vaporized precursor gas and a heated substrate to create a solid film. Because this process is suitable for depositing silicone rubber finishes on complex surfaces and geometries, it is useful for several applications.
CVD applications include industrial coatings, optical devices, and biomedical devices.
Thin Layer Coatings
Thin layer coating is a technique of spraying a very thin layer of silicone rubber finish on a surface for protection, functionality, and improved aesthetics. The coating layer is always very thin and can range between a few microns to a few hundred microns.
The thin-layer coating technique is helpful in applications that require uniformity, control over the coating layer’s thickness, and good adhesion to the substrate surface. Furthermore, this technique for silicone rubber finish is often used in biomedical devices and electronic components.
Intermediate Layer Coatings
The intermediate layer coating is a technique that applies a layer of material between the silicone rubber finish and the substrate. This technique is often used to improve adhesion and flexibility and to strengthen the bond between the substrate and the silicone rubber finish.
Intermediate layer coating is widely used in applications with complex substrate material posing challenges to adhesion to the silicone rubber finish. Industries that need this technique include automotive and aerospace. In addition, the technique is employed on printed circuit boards, sensors, and medical devices.
Example of a New Technique in the Market
Plasma-enhanced chemical vapor deposition (PECVD) is a new technique on the market for depositing silicone rubber on a substrate surface. This technique involves the use of plasma to break down the precursor gases. The formed reactive species then react to form a solid film over the substrate surface.
PECVD can be carried out at low temperatures, creating films with unique properties. This technique is used for depositing silicone rubber finishes on metal components, medical devices, and flexible electronics.
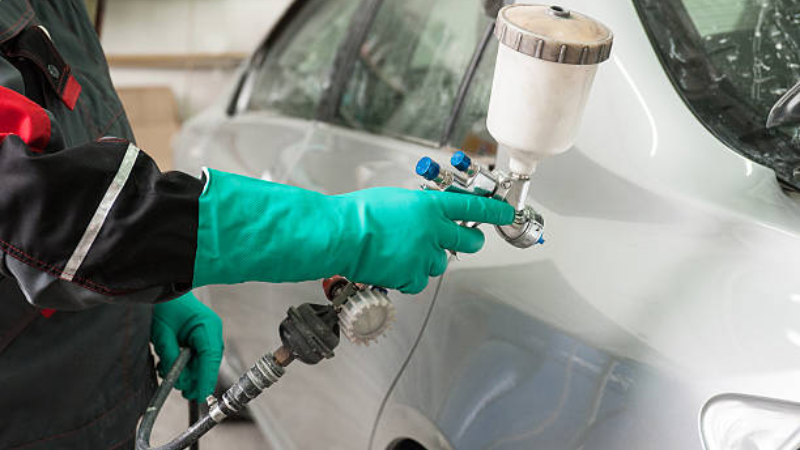
Conclusion
Silicone rubber finishes are ideal for protecting a substrate surface and promoting adhesion. The properties of the finish include water resistance, UV resistance, thermal stability, and chemical resistance. Consequently, a coated surface will last as long as possible while retaining its properties.
It would be best to incorporate silicone rubber finishes in your application because they are non-toxic, versatile, low-cost, and suitable for several practical applications.
Discover the Perfect Solution for Your Business with Hongju
Due to their excellent properties and low cost, silicone rubber finishes are the future of protective coatings global market. Fortunately, you can manufacture these finishes through a reliable rubber products supplier like Hongju. Hongju has over two decades of experience manufacturing silicone rubber products and finishes. The team can discuss this with you and create products that meet your specifications.
Kindly reach out today!