So, if you’re looking for a reliable method that combines the best of both worlds, look no further than rubber to metal bonding. Its versatility and many benefits have made it an indispensable part of modern manufacturing processes.
What is Rubber to Metal Bonding
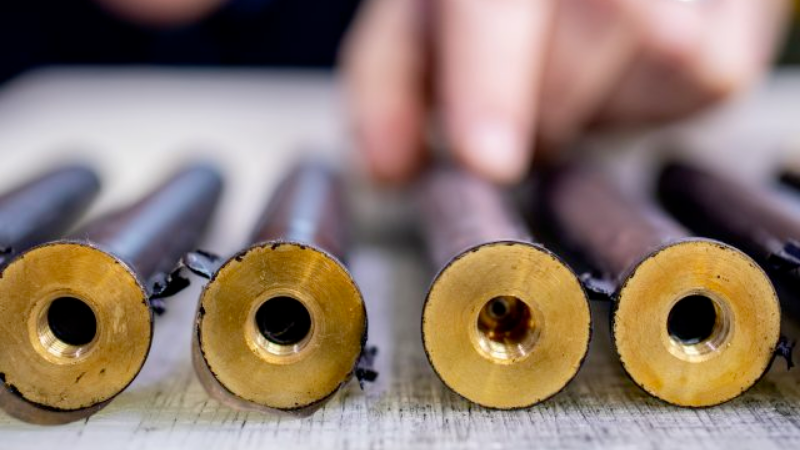
Rubber to metal bonding is a process that involves joining rubber and metal parts using adhesives or vulcanization. This technique ensures a secure bond between the two materials, resulting in enhanced performance and longevity of the final product.
The use of rubber to metal bonding techniques is widespread across various industries, including automotive, aerospace, and industrial applications. Let’s delve deeper into the significance and applications of this process.
Adhesive vs Vulcanization
There are two primary methods used in rubber to metal bonding: adhesive bonding and vulcanization.
Adhesive bonding involves applying a specialized adhesive between the rubber component of the heated mold and the metal substrate. The adhesive cures over time, creating a strong bond between the two materials.
Vulcanization involves chemically using natural rubber latex and cross-linking the rubber with the metal substrate. This process requires heat and pressure to cure the rubber, resulting in a permanent bond. Vulcanization is often preferred for applications that require high strength and resistance to extreme conditions.
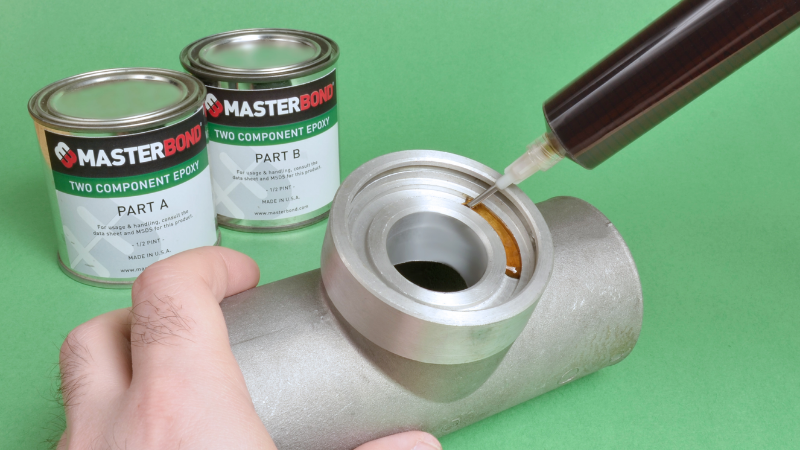
Benefits and Applications of Rubber to Metal Bonding
Rubber to metal bonding is a versatile technique that offers numerous benefits and finds applications in various industries. This process involves joining rubber and metal components together, creating a strong bond that combines the flexibility of rubber with the durability and strength of metals. Let’s explore some of the key advantages and applications of rubber to the metal bonding process.
Benefits of Rubber to Metal Bonding
Rubber to metal bonding offers several benefits, including:
Excellent Vibration Isolation
One of the primary benefits of rubber to metal bonding is its ability to provide excellent vibration isolation. By absorbing vibrations, this technique helps reduce noise levels, making it ideal for applications where noise reduction is crucial. Whether it’s in automotive engines or industrial machinery, rubber to metal bonded components effectively isolate vibrations, improving comfort for both operators and nearby individuals.
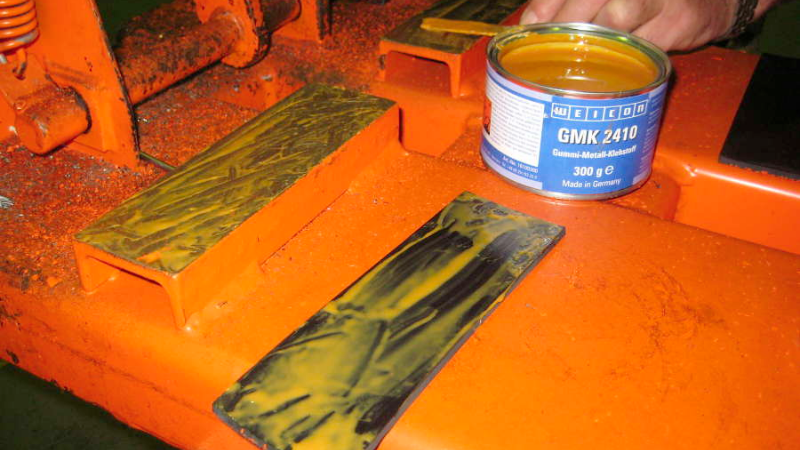
Flexibility Combined with Strength
Rubber to metal bonding is great because it combines the flexibility of rubber with the strength of metals. This makes it useful in many industries. The rubber absorbs shocks and keeps the bond between the rubber and metal strong. This means the bonded parts can handle heavy loads, high temperatures, and tough environments without breaking.
Wide Range of Applications
The versatility of rubber to metal bonding makes it suitable for a wide range of applications across various industries. Here are some common examples:
- Engine Mounts: Rubber bonded with metal is commonly used in engine mounts as they help absorb engine vibrations, reducing noise transmission into the vehicle cabin.
- Suspension Systems: In automobiles, suspension systems benefit from rubber to metal bonded parts as they dampen shocks caused by uneven road surfaces.
- Seals and Gaskets: Rubber bonded with metal is widely used in seals and gaskets due to its ability to create an effective barrier against fluid or gas leakage.
- Industrial Machinery: Rubber-metal bonded components find application in industrial machinery such as pumps, compressors, and motors to reduce vibrations and noise levels.
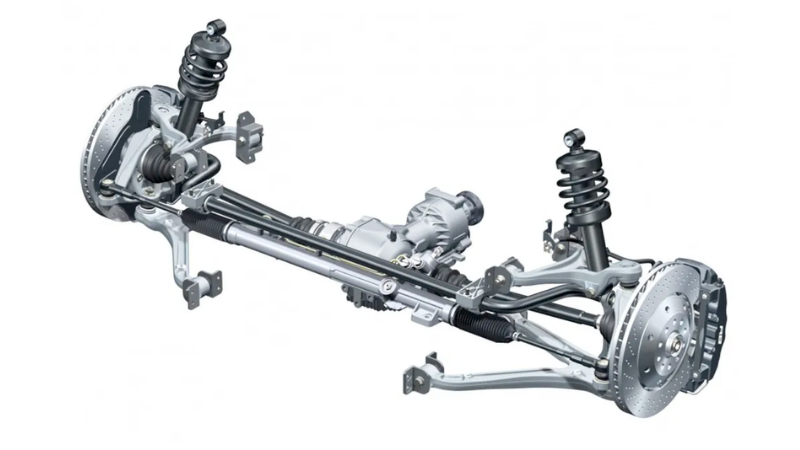
In addition to these examples, this bonding technique is also employed in the manufacturing of automotive bushings, anti-vibration mounts, conveyor systems, and many more applications where the combination of rubber’s flexibility and metal’s strength is advantageous.
Rubber to metal bonding offers a range of benefits that make it a preferred choice for various industries. With its excellent vibration isolation properties, ability to create complex designs and wide range of applications, this technique plays a crucial role in improving comfort, reducing noise levels, and enhancing the performance of numerous products.
Considerations for Designing Rubber-to-Metal Bonded Assemblies
Designing rubber-to-metal bonded assemblies requires careful consideration of various factors to ensure optimal performance and durability. Let’s delve into some considerations in more detail.
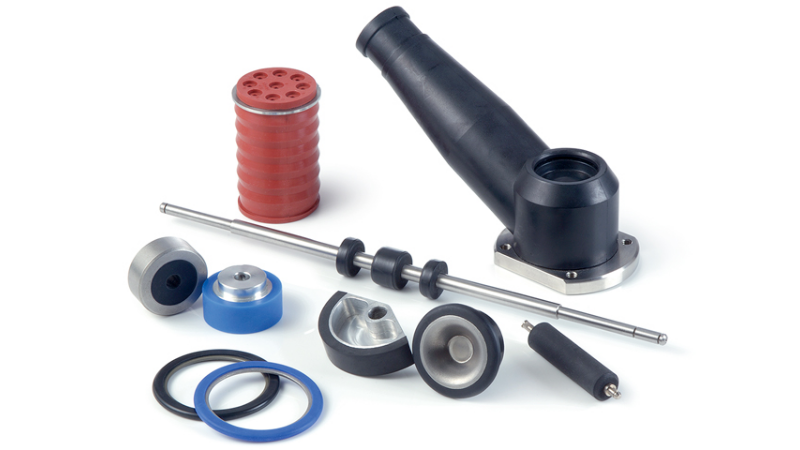
Selecting Suitable Materials
Choosing the right materials is crucial for achieving a successful rubber-to-metal bond. Both the rubber component and metal substrate should be carefully evaluated based on their mechanical characteristics and compatibility with each other. Molded parts can be used in such assemblies, which are created through processes like injection molding or the transfer molding process.
Load-Bearing Capacity
Rubber-to-metal bonded assemblies often encounter varying loads during operation. It is essential to consider load-bearing capacity when designing these assemblies to ensure they can withstand the expected forces without compromising structural integrity. Reinforcement techniques such as adding more metal inserts, or fabric layers can enhance load-bearing capabilities.
Temperature Resistance
Temperature resistance is another critical factor to consider in design. The selected rubber compound should have suitable heat resistance properties to withstand anticipated operating temperatures without degradation or loss of functionality. Understanding the application’s temperature requirements is vital for selecting an appropriate rubber material or compound.
Chemical Compatibility
When designing rubber-to-metal bonded assemblies that will be exposed to chemicals or fluids, engineers must assess chemical compatibility between the materials involved. Certain chemicals may cause degradation or swelling of rubber compounds if they are not chemically resistant.
Choosing the Right Elastomer for Bonding
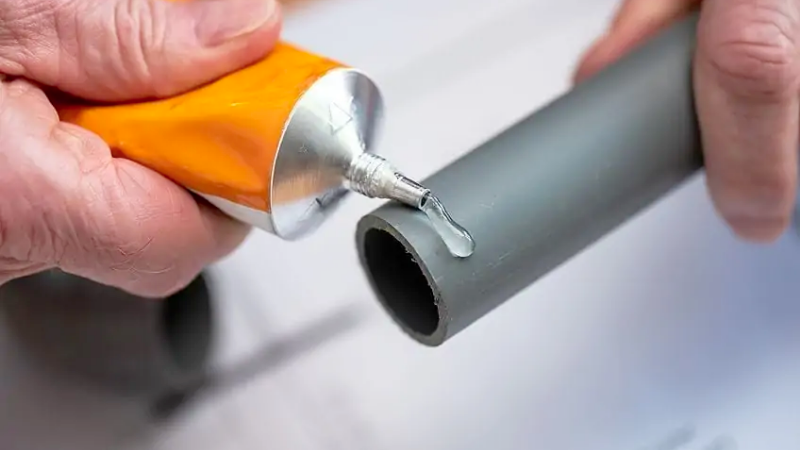
In rubber-to-metal bonding, several common elastomers find widespread use due to their specific characteristics and performance capabilities. Some examples include:
- Natural Rubber (NR): Known for its excellent tear strength and resilience, NR is often used in applications requiring high flexibility and vibration isolation.
- Styrene-Butadiene Rubber (SBR): SBR offers good abrasion resistance and is commonly employed in automotive components like engine mounts and suspension bushings.
- Neoprene (CR): With its superior resistance against weathering, ozone, and moderate oil exposure, CR is suitable for outdoor applications or those involving exposure to oils.
- Nitrile(NBR): NBR exhibits exceptional resistance to oils, fuels, and other petroleum-based fluids. It finds extensive use in sealing applications within the automotive industry.
By considering factors like temperature range, chemical exposure, hardness, compression set resistance, dynamic properties like tear resistance, and tear strength, one can make an informed decision when choosing the right elastomer for rubber-to-metal bonding. Each elastomer has its own unique characteristics that lend themselves well to different application requirements.
Low Viscosity and Fast Curing Silicone Compound
The choice of adhesive plays a crucial role in ensuring strong and durable bonds. One option that has gained popularity in recent years is the use of low viscosity and fast curing silicone compounds. These compounds offer several advantages that make them highly desirable for this application.
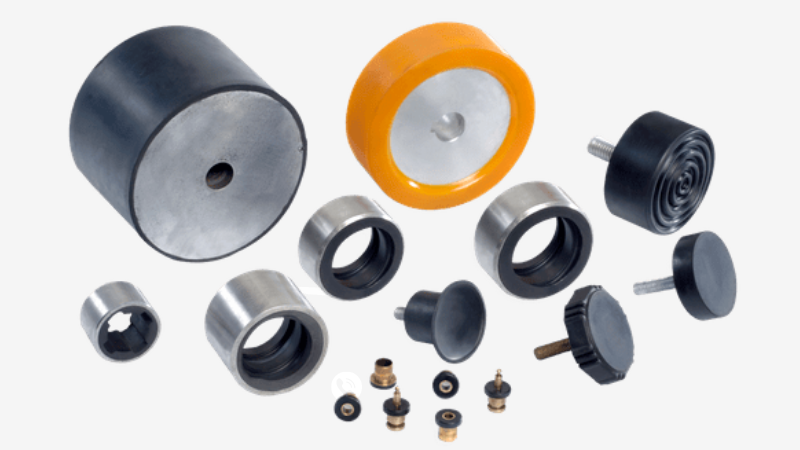
Easy Flow into Intricate Geometries
Using low viscosity silicone compounds facilitates easy flow into intricate geometries during the injection molding process. This means that even complex rubber parts with intricate designs can be effectively bonded to metal components without any compromise on bond strength. The low viscosity allows the silicone compound to fill every nook and cranny, ensuring complete coverage and a secure bond.
Reduced Production Time with Fast Curing
Fast curing silicone compounds are another key advantage. These compounds significantly reduce production time while maintaining bond strength requirements. The quick curing process ensures that manufacturers can move swiftly through each step of production, from applying the adhesive to final assembly. By minimizing cure times, manufacturers can increase their output capacity without compromising on quality or performance.
Excellent Adhesion Properties
In addition to their ease of use and fast curing capabilities, low viscosity silicone compounds offer excellent adhesion properties when used in rubber-to-metal bonding applications. The unique chemical composition of these compounds enables them to form strong bonds between rubber and metal surfaces. This high level of adhesion ensures reliable performance even under challenging conditions such as exposure to extreme temperatures or harsh chemicals.
Primer and Adhesive Application for Successful Bonding
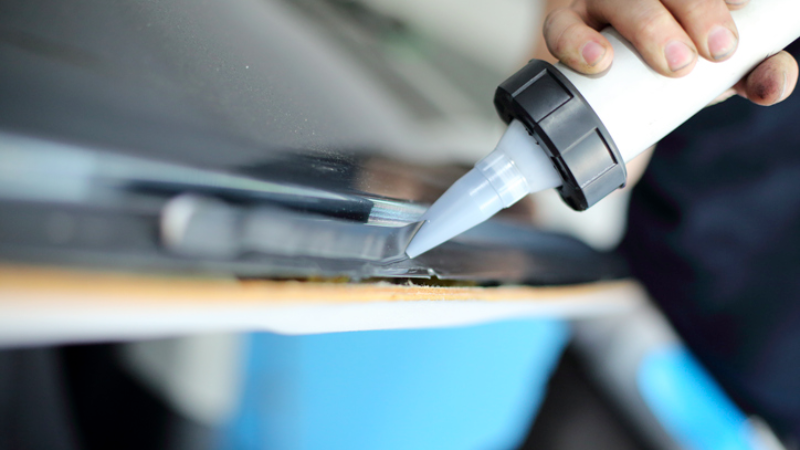
Rubber to metal bonding is a technique for joining two different materials, typically rubber and a metal surface, together. This can be used to create strong, durable bonds that can withstand a variety of conditions.
The process of rubber to metal bonding typically involves applying an adhesive to both the rubber and metal surfaces and then applying pressure to ensure a strong bond. The first step in this process is to properly prepare the surfaces to ensure that the adhesive and rubber can form a strong bond.
Applying a primer is an essential step in ensuring proper adhesion between rubber and metal surfaces. Without a primer, the bond may not be as strong or durable, leading to potential failure over time. The primer acts as a bonding agent, creating a secure bond between the rubber and metal.
One of the key factors to consider when preparing the surfaces for bonding is to clean and degrease them. Surfaces that are not properly cleaned can have contaminants that can prevent the adhesive and rubber from bonding properly. Another important step is to roughen the surface, which can be done using sandpaper or a wire brush. This can help the adhesive and rubber to form a stronger bond.
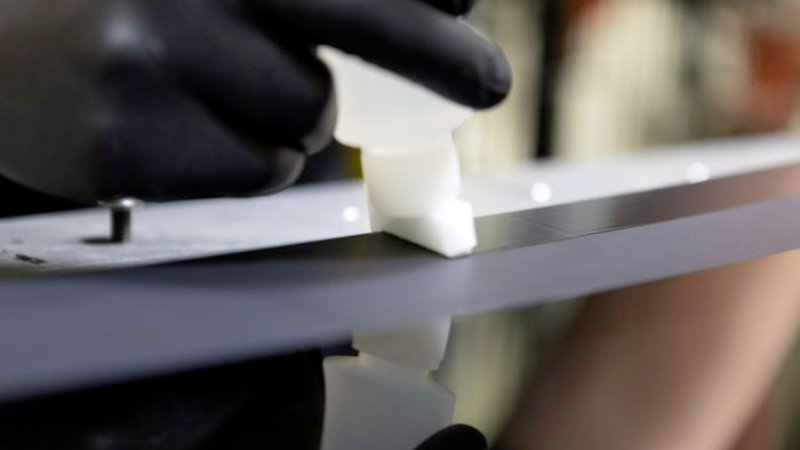
Once the surfaces are properly prepared, it is time to apply the adhesive and rubber. This can be done using a variety of techniques, including rolling, pressing, or spray-coating. It is important to ensure that the adhesive and rubber are applied evenly and fully cover the surface area.
Once the adhesive and rubber are applied, it is time to apply pressure to ensure a strong bond. This can be done using a fixture, such as a clamp or press, and will depend on the size and shape of the bonded parts. The amount of pressure necessary to form a strong bond will vary depending on the materials being bonded and the specific bonding process being used.
Conclusion
In conclusion, rubber to metal bonding offers significant advantages in terms of product performance and durability across various industries.
By considering design aspects, selecting suitable elastomers, and utilizing proper compounds and adhesives while ensuring adequate surface preparation techniques are employed; manufacturers can achieve robust bonds that meet their application requirements effectively.
Discover the Perfect Solution for Your Business with Hongju
At Hongju Silicone, we offer a wide range of rubber to metal bonding materials that can be tailored to your specific requirements.
We can work with you to identify the optimal solution for your product or application, whether it’s a simple hand application or a more complex automated process. At Hongju Silicone, we’re committed to helping you create the best possible product.
Take the First Step:
Requst for an Inquire
Quality Meets Affordability. Inquire Now for High-Quality Products at Low Volumes.