A rubber grommet has various applications, from sports equipment to the automobile industry, medical sector, etc. There are also multiple types of rubber grommets, for example, oval rubber grommets, shaped rubber grommets, etc.
What is a Rubber Grommet?
A rubber grommet is a kind of attachment that seals the sharp edges of various mechanical, electrical, or manufacturing components. They serve multiple functions, such as protecting wires from cuts, sealing, reducing vibration to protect sensitive components, etc.
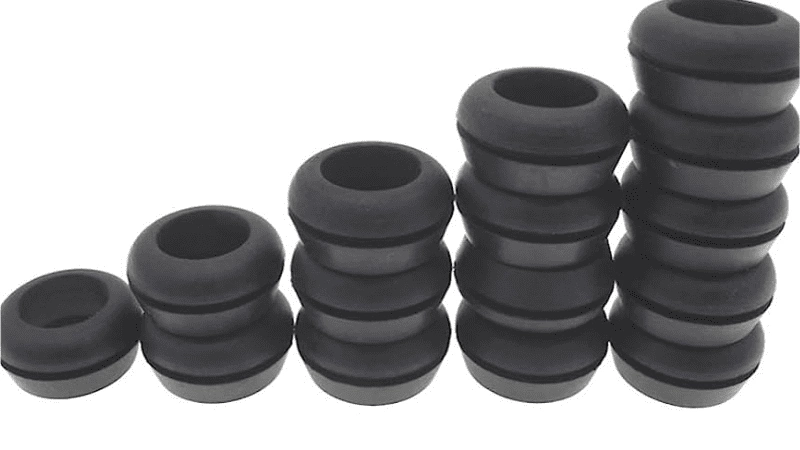
Rubber grommets are essential in protecting cables, wires, and pipes from wear and tear due to friction. They also function as barriers that keep water and dust from damaging equipment. Additionally, rubber grommets are particularly useful because they have flared collars that lock them in place and facilitate installation.
However, rubber grommets have various alternative names, such as eyelets, edging, bushing, insulating, etc. It is called insulating bushing, mainly used in electrical equipment. Such grommets have sizes usually up to 51 mm.
Materials Options of Rubber Grommets
The usage of a rubber grommet depends on the type of material it is made of. We have discussed some commonly used materials for rubber grommets below.
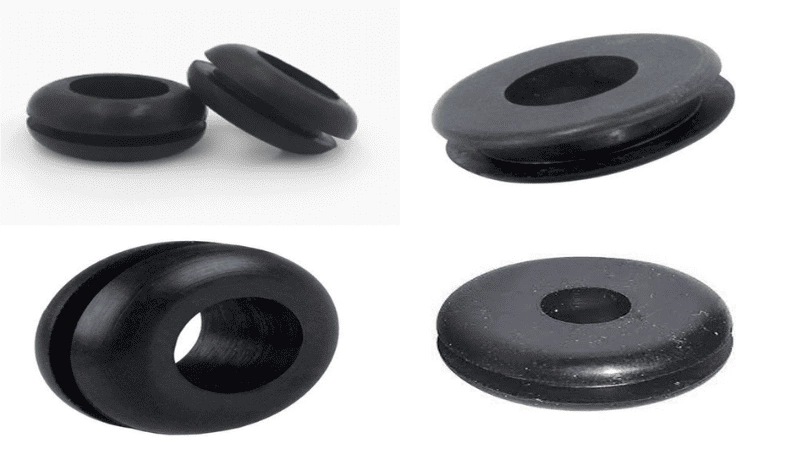
Thermoplastic Elastomer (TPE)
The thermoplastic elastomer is a cost-effective solution for rubber grommet manufacturing. This material has characteristics similar to natural rubber. The electrical properties of TPE are pretty promising.
At the same time, it is flexural fatigue resistant and can keep its properties constant in different weather. It is also chemical resistant. TPE works at a range of -22°F – 284°F temperature and its impact strength are excellent.
Ethylene Propylene Diene Monomer (EPDM)
Regarding excellent electrical insulation, the ethylene propylene diene monomer, aka EPDM, is at the top of the list. Manufacturers love the ethylene-propylene rubber of the next generation because it resists weathering quite well.
Its properties make it perfect for sealing applications. For this reason, it is considered an excellent grommet material. Its operating temperature range is -60°F – 300°F.
Styrene-Butadiene Rubber (SBR)
The styrene-butadiene rubber has similarities with nitrile rubber. But nitrile rubber is softer than SBR. It is suitable for hoses, belts, gaskets, seals, and various fields that must be waterproof. It operates within -60°F – 250°F temperature.
Thermoplastic Vulcanizate (TPV)
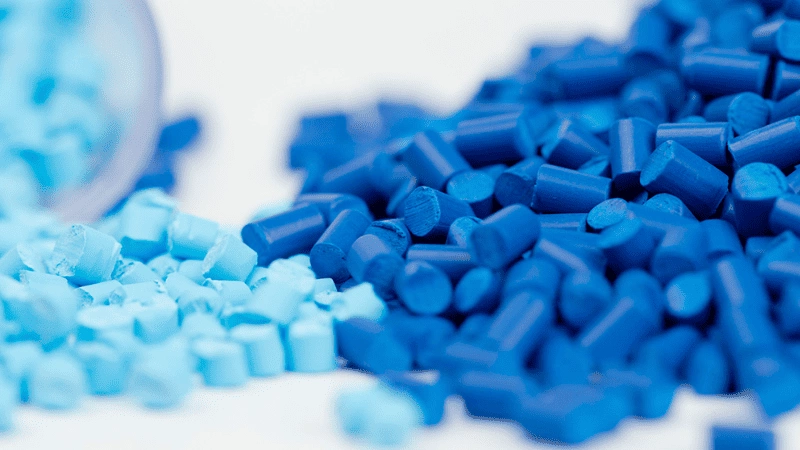
Thermoplastic vulcanizate is one kind of TPE. This is also called TPE-V. The TPV is suitable for various sealing applications because it has similar characteristics to EPDM. It is used vastly under the hood in the automotive industry, especially radiators.
It is mainly used for its heat-resistant properties and performs pretty well in oily environments. It operates under a range of -76°F – 275°F temperature.
Buna-N Grommets
Buna-N rubber grommets are also known as NBR. It is the best material compared to most other rubber materials when it comes to being oil-resistant. But its volume resistance is lower than most other rubber products. NBR is a semiconductor rubber material that has antistatic properties.
FKM Grommets
The chemical stability of FKM is excellent. For this reason, FKM grommets are one of the best elastomers. Manufacturers use FKM in environments with strong alkali and acid materials or components. Moreover, its operating temperature range can reach up to 300℃, and it will work perfectly well at that temperature for a long time.
Neoprene Grommets
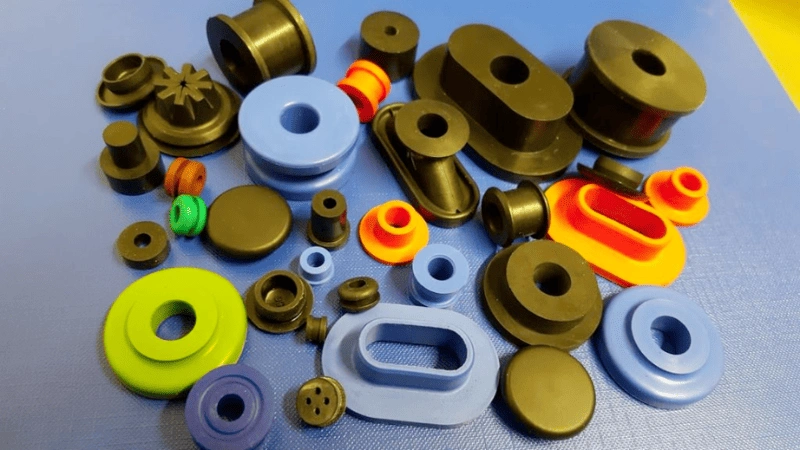
If manufacturers need good ozone aging resistance, heat resistance, and weather resistance, they use neoprene to make grommets. They are perfect for use anywhere, regardless of the weather condition.
The performance of retarding flame is excellent for neoprene grommets. For this reason, manufacturers also use it on products that need high flame retardancy.
Silicone Grommets
If manufacturers need to make grommets with bright colors, they use silicone. Silicone grommets are environment-friendly and safe to use. It is not a problem if silicone rubber grommets contact with skin or foods.
The anticoagulant effect of silicone rubber grommets resists them from adhering to the tissue of humans. This is why it is perfect for medical products and applications.
How Are Rubber Grommets Made?
There are different methods for making rubber grommets, such as compression, injection, transfer, etc. These manufacturing processes are discussed below:
Compression Molding
The main components of the compression molding process are two molds (one of which is movable while the other one is fixed), charge or raw material (could be natural rubber or other rubber material), and an ejector pin.
Below is a step-by-step process of how compression molding works:
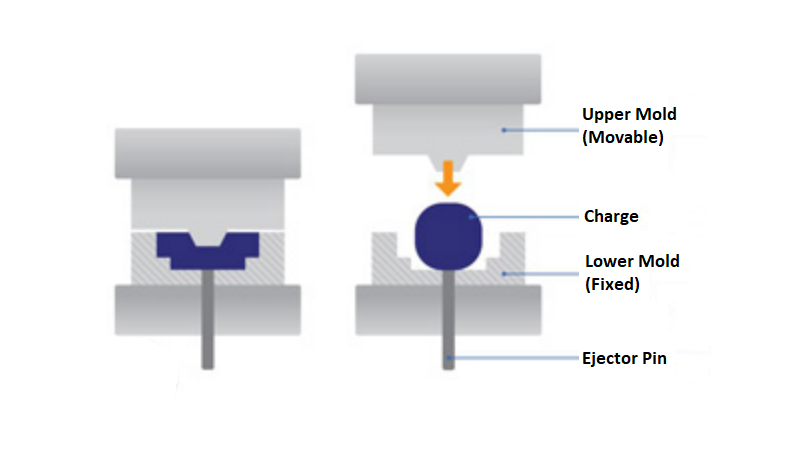
- First, the charge or raw rubber material is placed on the fixed mold, which is the lower mold.
- Then the upper movable mold pushes the charge down, and the charge achieves the shape of the mold.
- An ejector pin is used to take out the final part, and the part is ready to be used.
So, this is how compression molding works to make rubber grommets.
Injection Molding
Various parts that build up the injection molding process are the hopper, screw, barrel, nozzle, molds, ejector pins, etc. Its step-by-step working principle is given here:
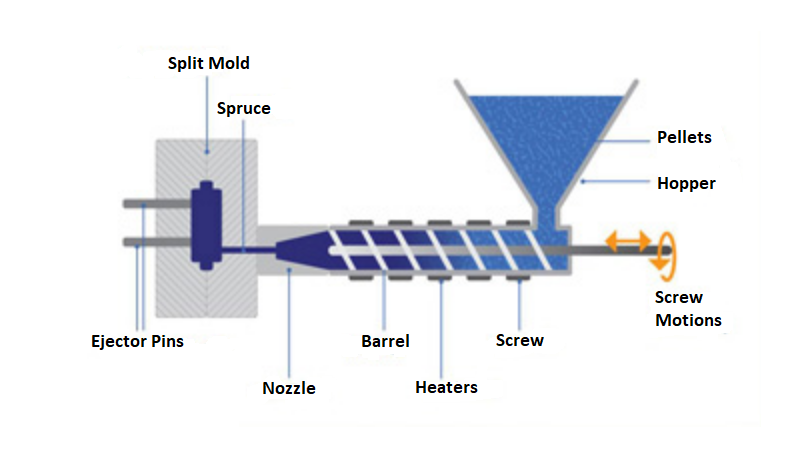
- At first, pellets or melted rubber are taken into the hopper.
- Then the pellets drop into the barrel, and the screw rotates to keep the mixture homogeneous.
- A heater is used to keep the charge at the required temperature.
- As the screw rotates, the mixture is injected or inserted into the molds through a nozzle.
- When the charge forms the desired mold shape, the split mold opens.
- Finally, ejector pins help to take out the finished part.
This injection molding method makes rubber grommets of different sizes, shapes, and colors.
Transfer Molding
The main components of transfer molding are a plunger, transfer pot, molds, spruce, heaters, ejector pins, etc. Below is the step-by-step working principle of transfer molding:
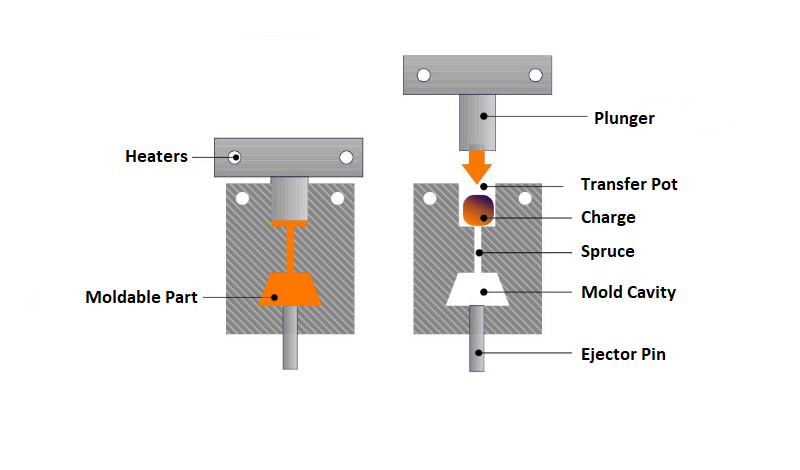
- Firstly the charge is placed inside the transfer pot.
- Then the plunger pushes the charge down to the mold cavity.
- There are heaters connected to the plunger that keep the charge hot.
- The charge is inserted into the cavity through spruce and forms into the required part.
- Finally, the mold is opened, and the ejector pins are part out.
So, this is how the transfer molding process is used for many rubber grommets with proper hardness and abrasion resistance.
Usual Shapes of Rubber Grommets
Rubber grommets have different applications, such as furniture and military applications. Also, these are used in holes of various electrical appliances, machinery, wiring, panel, cord, etc.
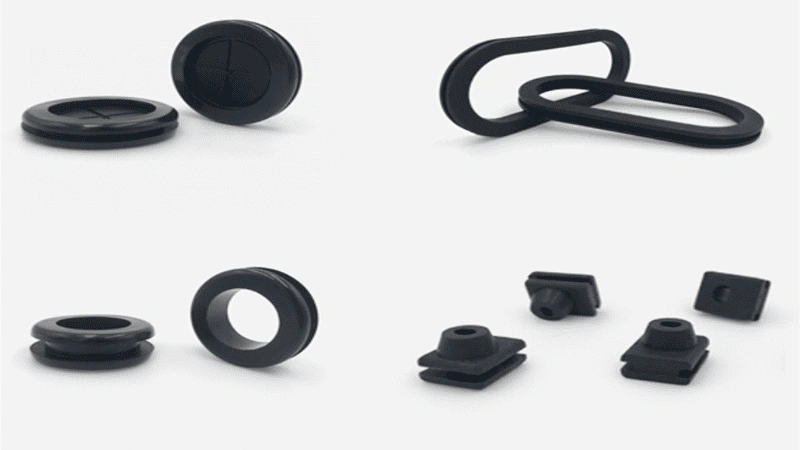
Based on these different usages, there are some common shapes of rubber grommets. These shapes are listed below:
- Oval Rubber Grommets
- Round Rubber Grommets
- Oblong Rubber Grommets
- Blind Rubber Grommets
- Square Grommets
- D Shaped Rubber Grommets
- Special Shape Grommets
Types of Rubber Grommets
There are various types of rubber grommets based on usage. These are:
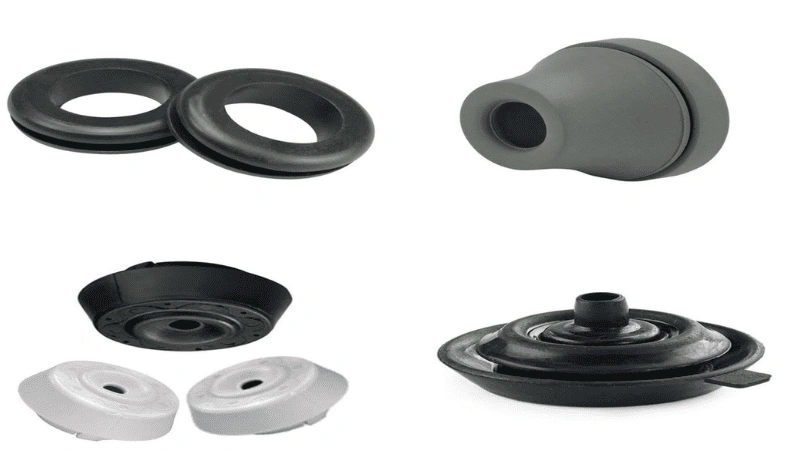
Push-in Flexible Grommets
This rubber grommet is often seen in blind holes of electronic devices. They can protect wires in holes of metal panels or serve as anti-skid feet for equipment. This type of rubber grommet is mainly made of polypropylene and TPE.
Standard Grommets
Standard grommets are round rubber grommets. These round grommets are mostly made of SBR and TPV. Round grommets are applicable for junction boxes of automobiles, chassis, and socket boxes.
Diaphram Grommets
Diaphram grommets are mainly rubber cable grommets. There is a thin film in the center of rubber cable grommets. This is present to make different sizes of holes so that other cables can pass through it to a panel.
This type of rubber grommet is mainly used in different control systems. TPE is the primary material for making diaphragm grommets.
Stepped Grommets
Cables with different diameters can fit through stepped grommets. The tapered feature allows thick cables to pass through it. Its size can be adjusted for thick cable diameters. Stepped rubber grommets are suitable for HVACs, panels, and panel holes. The main material for making this kind of grommet is EPDM.
Sealing Grommets
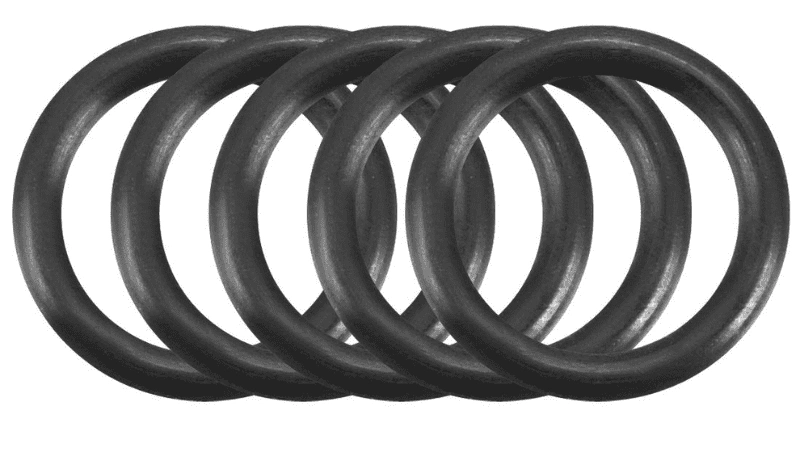
If there is any need for rubber grommets for round holes, then sealing grommets are perfect. This type of rubber grommet can withstand vibrations easily. As it is mostly made of EPDM, it is waterproof. A sealing rubber grommet performs quite well in greasy and oily environments.
Quick-Fit Grommets
A quick-fit rubber grommet is usually a tapered shape. This allows quick installation. Such rubber grommets are suitable for sharp plate cuttings, edges of electrical enclosures, and panels. These are made of TPE or silicone. These materials are very good sealants and have excellent heat resistance.
Edging Rubber Grommets
Edging rubber grommets are applicable for places with longer runs of wiring and cables. It is easy to cut the desired length for the grommet to protect cables and wiring. It is usually made of TPE and is also used in enclosure panels of automobiles.
Final words
In conclusion, rubber grommets are designed to protect wiring and cabling from the elements. They are crucial for ensuring proper sealing and insulation in electrical connectors, equipment, and appliances.
Rubber grommets are made through a variety of techniques, including injection molding, pressure molding, compression molding, and others. These methods ensure the production of high-quality, long-lasting grommets for a wide range of applications.
Ultimately, rubber grommets are an essential component for many industries, from transportation to telecommunications, and their effectiveness and efficiency have led to their widespread adoption worldwide.
Looking for Custom Rubber Grommets? Hongju Can Help You
Hongju Silicone is an innovative custom-molded rubber products manufacturer in China. We provide high-quality custom silicone rubber products for our customers in different industries.
Our main products include conductive silicone keypads, rubber grommets, furniture rubber feet, gaskets, O-rings, etc. To glimpse our diverse and high-grade product range, visit our products page.