In this article, we’ll delve into the fascinating world of PP granules and discover how they contribute to making strong and long-lasting plastic products, from plastic bottles and plastic bags to various household and industrial items.
What are PP Granules?
PP granules(Polypropylene granules) including copolymer polypropylene, are small particles of polypropylene plastic that serve as the raw material for various thermoplastic applications.
These granules are generated through a polymerization process that combines propylene monomers to form polypropylene resin.
The granular form allows for easier handling, transport, and processing, ultimately being melted and molded into a variety of household and industrial applications, such as plastic bottles, plastic bags, and even shampoo bottles.
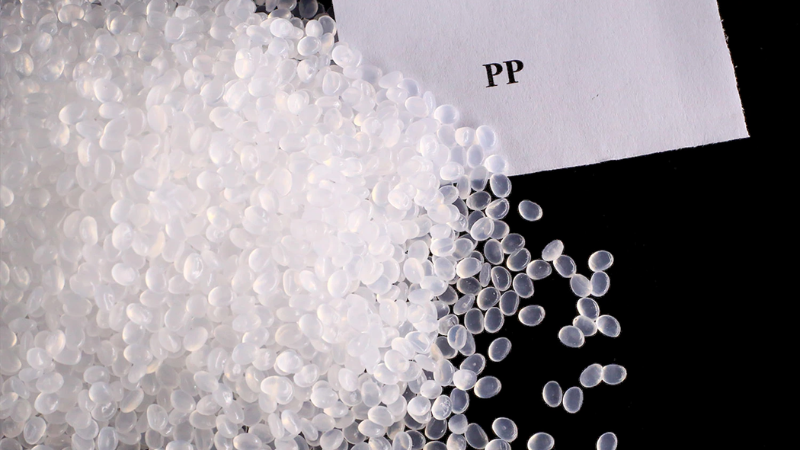
Understanding the nature and applications of PP granules provides insights into the chemical resistance, low melt viscosity, and relatively low melting point that make them an ideal choice for a multitude of uses.
The Chemistry Behind PP Granules
Polypropylene granules are the result of polymerizing propylene gas with a catalyst, typically Ziegler-Natta or metallocene catalysts. The polymerization occurs in a controlled environment, usually in a high-pressure reactor, to form long chains of polypropylene.
From a molecular perspective, polypropylene is a linear hydrocarbon polymer, meaning it is composed of a long chain of carbon atoms, each bonded to two hydrogen atoms. The chemical resistance of PP granules is attributable to the absence of any real functional groups along the polymer chain.
This makes the material highly resistant to a wide variety of chemicals, including many acids, alkalis, and organic solvents.
Various types of polypropylene can be created by modifying the chain architecture, which can be achieved through the use of specific catalysts and polymerization techniques.
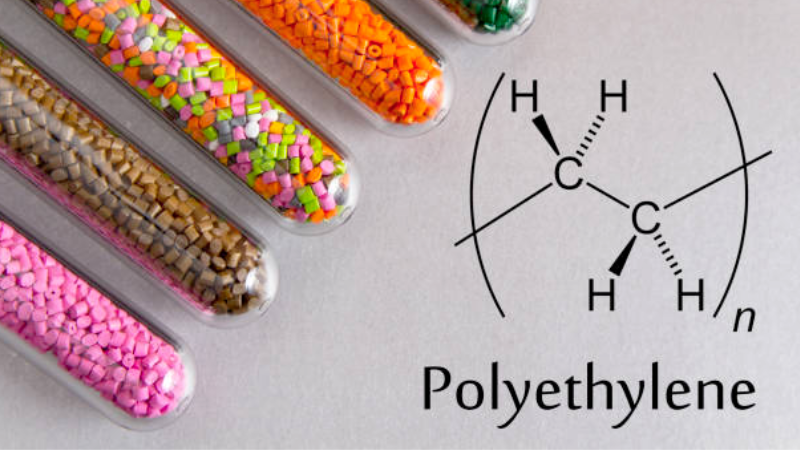
These include block copolymers and random copolymers, each with unique properties that make them suitable for different applications.
The melting point and low melt viscosity of PP granules also make them easy to process. They can be easily molded into various shapes, and their low viscosity allows for smoother flow during the molding process, resulting in high-precision industrial components.
Customizing PP Granules Through Chain Architecture
In the world of plastics, not all polypropylene (PP) granules are created equal. Various types of polypropylene can be tailored to suit specific applications by modifying the chain architecture. Let’s break down the details:
Chain Architecture
The basic structure of polypropylene consists of long chains of propylene monomers. However, the arrangement of these chains can be modified in various ways to create different types of polypropylene, each with its own set of properties. The major types are:
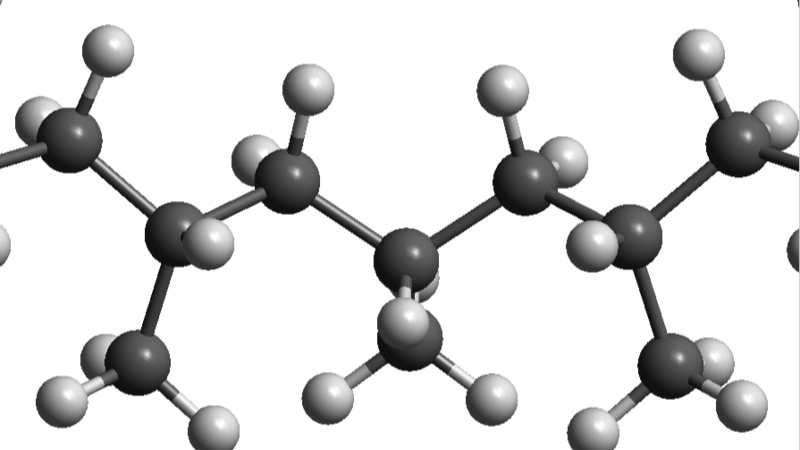
- Homopolymer PP: Made of a single type of monomer (propylene), it’s the most basic form and is widely used.
- Copolymer PP: Incorporates different types of monomers alongside propylene, usually ethylene. This creates a material with a combination of the properties of both monomers.
- Block Copolymer and Random Copolymer: In block copolymers, long chains of a single type of monomer (usually propylene) are interspersed with blocks of different monomers (usually ethylene). In random copolymers, the different monomers are randomly dispersed along the chain.
Catalysts
Catalysts are substances that speed up chemical reactions without being consumed in the process. In the case of polypropylene, special catalysts such as Ziegler-Natta or metallocene catalysts can be used to control the polymerization process.
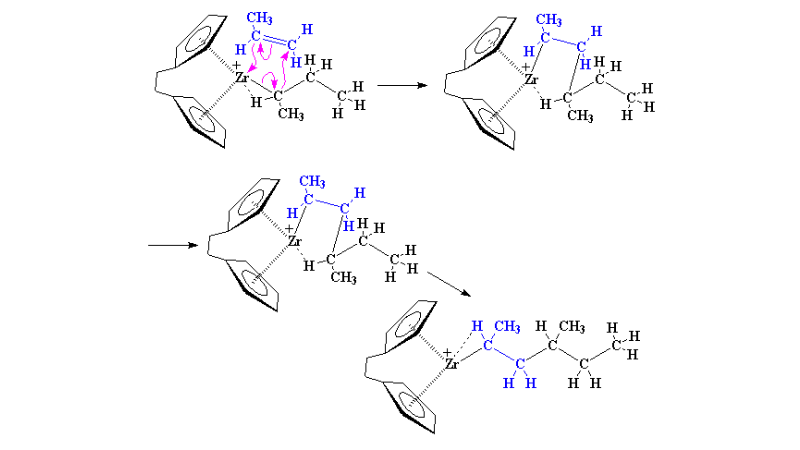
The choice of catalyst can influence the chain architecture, molecular weight, and other properties of the final product.
Polymerization Techniques
Various polymerization techniques can be employed to make polypropylene, each affecting the chain architecture differently:
- Bulk Polymerization: Often used for making homopolymers and random copolymers.
- Slurry Polymerization: Suitable for making high-molecular-weight PP.
- Gas-Phase Polymerization: Used for making PP with specific morphologies and characteristics.
By combining the right choice of monomers, catalysts, and polymerization techniques, manufacturers can produce PP granules with desired properties like high tensile strength, improved chemical resistance, or better thermal stability, tailored for specific applications.
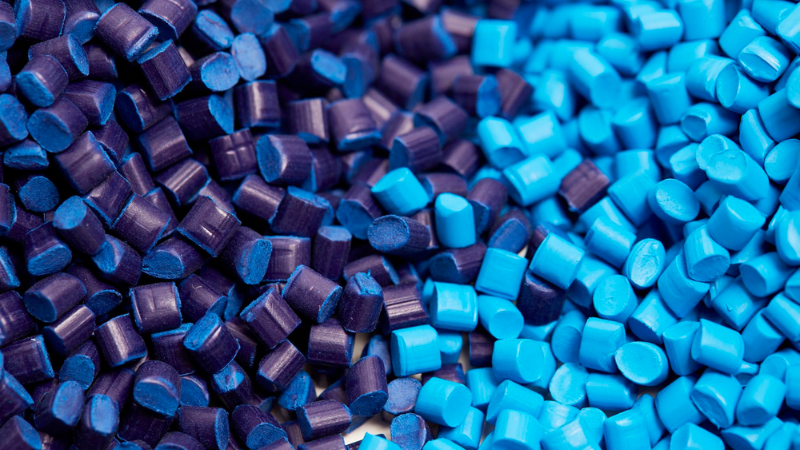
Where are PP Granules Used?
Plastic granules are the usual form of delivering thermoplastic materials used in the plastic processing industry. Polypropylene (PP) granules are incredibly versatile and find applications across a multitude of industries.
Their unique properties, such as good chemical resistance, high tensile strength, and low melt viscosity, make them suitable for a wide variety of uses. Here are some common applications:
- Packaging Industry: One of the primary consumers of PP granules is the packaging sector. From food storage containers to bottle caps and shrink wraps, polypropylene’s moisture-resistant and lightweight properties make it an ideal choice.
- Automotive Sector: PP granules are used in the production of various car parts, including bumpers, dashboards, and door panels, owing to their durability and resistance to chemicals.
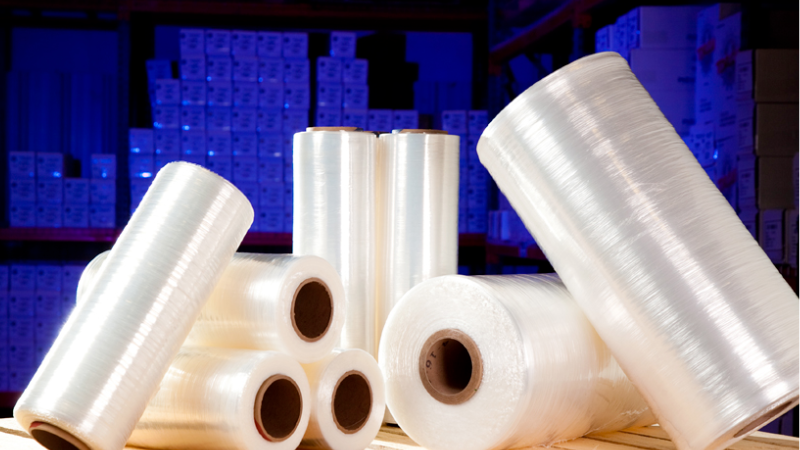
- Textile Industry: Polypropylene is also used in the production of textiles like ropes, carpets, and synthetic cloths due to its resistance to moisture and chemicals.
- Consumer Goods: Many household items like kitchenware, garden furniture, and even toys are made from PP granules.
- Medical Equipment: Due to its chemical resistance and sterilizability, polypropylene is commonly used in syringes, laboratory containers, and other medical devices.
- Construction Sector: PP is used in various construction materials like piping, insulation, and concrete molds because of its strength and resistance to wear.
- Electronics: PP granules find applications in the insulation of wires and the production of electrical components due to their natural electrical insulating properties.
Given the variety of applications, PP granules serve as a cornerstone in the manufacturing world, touching almost every aspect of modern life.
Benefits of Adding PP Granules in Plastic Production
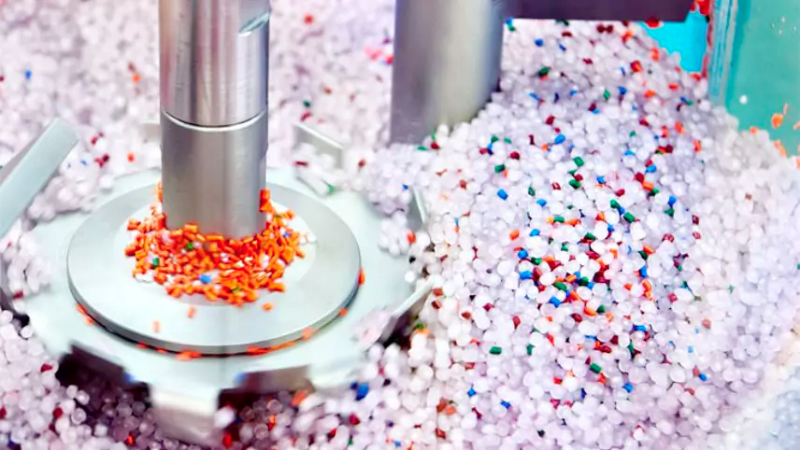
Polypropylene granules (PP granules) play a crucial role in elevating the overall quality and durability of plastic products. Here’s why incorporating them into the plastic production process can result in better, more resilient products:
- Improved Tensile Strength: PP granules have excellent tensile strength, which means that the final products are less likely to crack or break under stress.
- Thermal Stability: PP granules have a relatively high melting point, providing the final product with enhanced thermal stability. This is especially useful for plastic items that need to withstand high temperatures, like kitchenware.
- Lightweight Yet Durable: PP granules contribute to making products that are not only lightweight but also durable, striking a perfect balance that is often difficult to achieve with other materials.
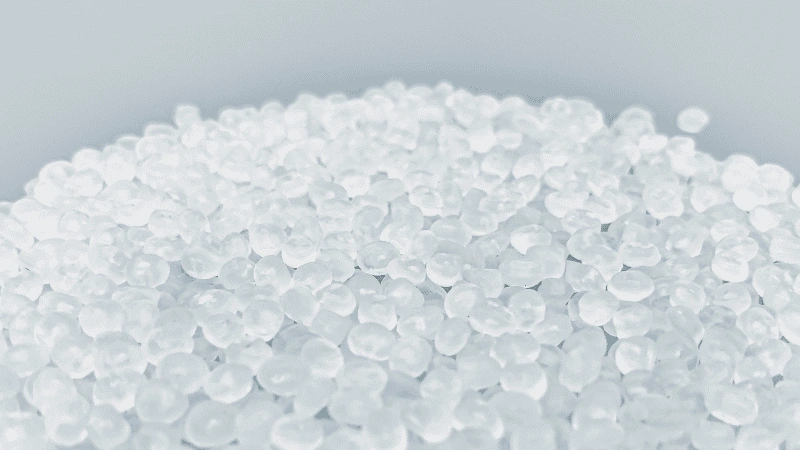
- Customization: As discussed earlier, the chain architecture of polypropylene can be modified to suit specific needs, enabling manufacturers to tailor the properties of the final product.
- Consistency in Quality: The granular form of PP allows for more uniform mixing during the production process, which leads to more consistent quality in the final product.
- Lower Production Errors: The uniform characteristics of PP granules allow for a smoother production process with fewer defects, reducing waste and increasing the yield of quality products.
By incorporating PP granules into the production process, manufacturers can not only improve the mechanical and thermal properties of the final product but also benefit from the material’s cost-effectiveness and versatility, making it a staple in the production of strong and durable plastic products.
Comparison with Other Types of Plastic Granules
To truly understand the advantages and limitations of PP granules, it’s helpful to compare them with other types of plastic granules commonly used in the industry. Below is a comparison table outlining the key features:
Property | PP Granules | HDPE (High-Density Polyethylene) | LDPE (Low-Density Polyethylene) | PET (Polyethylene Terephthalate) | PVC (Polyvinyl Chloride) |
---|---|---|---|---|---|
Melting Point | Moderate | High | Low | Moderate | Moderate |
Durability | High | High | Moderate | Moderate | High |
Chemical Resistance | Good | Good | Moderate | Good | Poor |
Cost | Moderate | Moderate | Low | Moderate | Moderate |
Energy for Production | Moderate | High | Moderate | High | High |
Recyclability | Good | Good | Moderate | Good | Poor |
Environmental Impact | Moderate | Moderate | High | Moderate | High |
Common Applications | Packaging, textiles | Containers, pipes | Plastic bags, wraps | Bottles, textiles | Pipes, cable coatings |
Key Takeaways
- Melting Point: PP granules have a moderate melting point, making them suitable for a wide range of applications. Unlike high-density polyethylene, they don’t require extremely high temperatures, which can reduce energy consumption during the manufacturing process.
- Durability: PP granules excel in terms of durability, rivaling even HDPE in many applications. This makes them ideal for products that require long-term durability.
- Chemical Resistance: PP is known for its good chemical resistance, similar to HDPE, but better than LDPE, PET, and especially PVC.
- Environmental Impact: Although not entirely eco-friendly, PP has a lower environmental impact compared to LDPE and PVC, mostly due to its recyclability and lower energy requirements for production.
- Cost: The cost of producing PP granules is moderate, making them a cost-effective choice for many applications compared to more expensive plastics like PET and PVC.
By comparing PP granules with other types of plastic granules, it becomes evident why PP is often the material of choice for various household and industrial applications. Its balance of properties offers a combination of versatility, durability, and relative environmental friendliness.
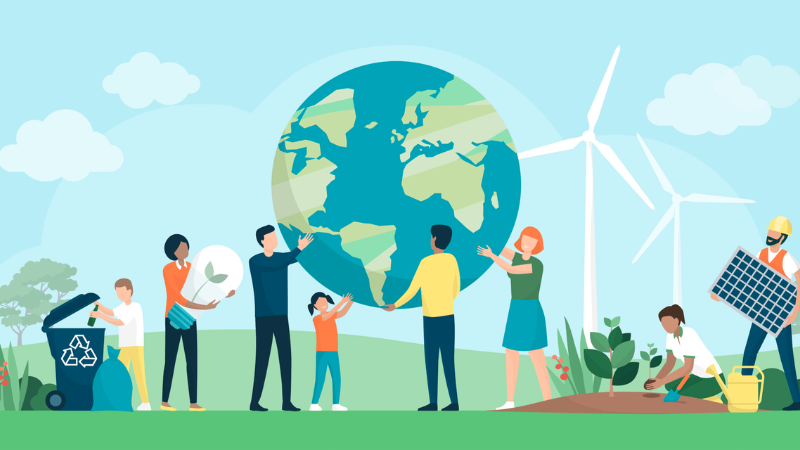
Global Market Trends and Future of PP Granules
The global demand for plastic products is on a steady rise, which in turn is driving the market for PP granules. As consumers continue to rely on plastic goods for various purposes, manufacturers are under pressure to produce strong and durable plastic products.
This has led to an increased demand for polypropylene (PP) granules, which are known for their excellent properties and versatility.
One of the key factors contributing to the growing popularity of PP granules is the increasing awareness of sustainable practices. Rising global concerns about plastic waste highlight the urgent need for recyclable materials in plastic production to mitigate environmental and health risks.
One of the advantages of using PP Granules is their potential for recycling. Initiatives for recycling polypropylene are increasingly gaining attention, as they contribute to sustainability and waste reduction. PP granules offer a sustainable solution as they can be easily recycled and reused without compromising their quality or performance.
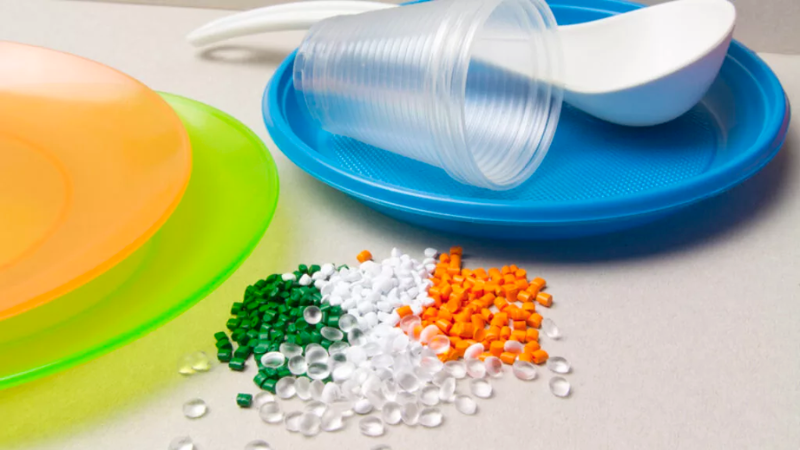
This eco-friendly aspect has made them a preferred choice among manufacturers looking to reduce their carbon footprint.
Technological advancements have also played a significant role in enhancing the properties and performance of PP granules. Through innovative processes such as compounding, additives can be incorporated into the granules to improve their strength, flexibility, heat resistance, and chemical stability.
These advancements have expanded the applications of PP granules across various industries, including automotive, packaging, construction, and consumer goods.
The Future
- Bio-based PP Granules: Research is underway to produce PP granules from renewable sources, which will significantly reduce their carbon footprint.
- Smart Materials: Advancements in nanotechnology and material science may pave the way for “smart” PP materials with enhanced properties, such as self-healing capabilities or responsiveness to environmental changes.
- Circular Economy: Efforts are being made to close the loop on PP recycling, thereby contributing to a circular economy. Improved recycling technologies can make this a reality.
- Global Supply Chains: As developing nations industrialize, the demand for PP granules is expected to rise, resulting in more complex and interconnected global supply chains.
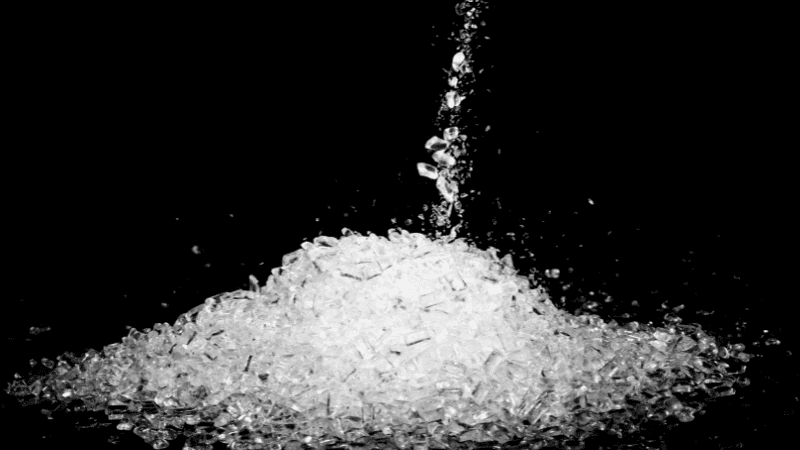
Given these trends and the innate advantages of PP granules, their future in the global market looks promising. They are poised to continue being a versatile and highly sought-after material for a myriad of applications, driving innovations in multiple sectors.
Conclusion
In summary, PP granules are crucial for creating high-quality, durable plastic products. Their unique chemistry allows for customization, making them versatile in various applications.
As environmental concerns grow, PP granules offer a sustainable option, promising a brighter future for both manufacturers and consumers. Choose PP granules for quality, durability, and environmental responsibility.
Choose Hongju Silicone for Quality PP Granules
Ready to elevate the quality of your plastic products while being environmentally responsible? Trust Hongju for all your PP granule needs. Our industry-leading PP granules are the secret to making your products strong, durable, and sustainable. Don’t compromise—choose the best to be the best. Contact us now and get a free solution for your project to improve your business.
Take the First Step:
Requst for an Inquire
Quality Meets Affordability. Inquire Now for High-Quality Products at Low Volumes.