Looking for a cutting process that is accurate, fast, and clean? Well, kiss cutting is a popular process that cuts only through the top layer, keeping the baking layer intact. This cutting technique is popularly used in the automotive, medical, and electronic industries. This guide covers what is a kiss cut, how it works, and its industrial applications. So read on:
What Is A Kiss Cutting?
Kiss cutting is a process in which only the top layer of a material is cut, while the bottom layer, or backing layer, remains intact. This cutting method is popularly used for cutting silicone gaskets and seals.
For example, if you are manufacturing silicone gaskets or any other product, kiss cutting allows the product to be cut but keeps it attached to the liner or adhesive backing. You can then easily peel off the product when needed, without ruining its shape.
Kiss cutting offers clean and precise cuts, making it perfect for sticker sheets, adhesives, and gaskets. As the parts after cutting stay attached to the backing material, it is easy to peel them off during packaging. Additionally, kiss cutting reduces waste and enables easy transportation and storage of parts.
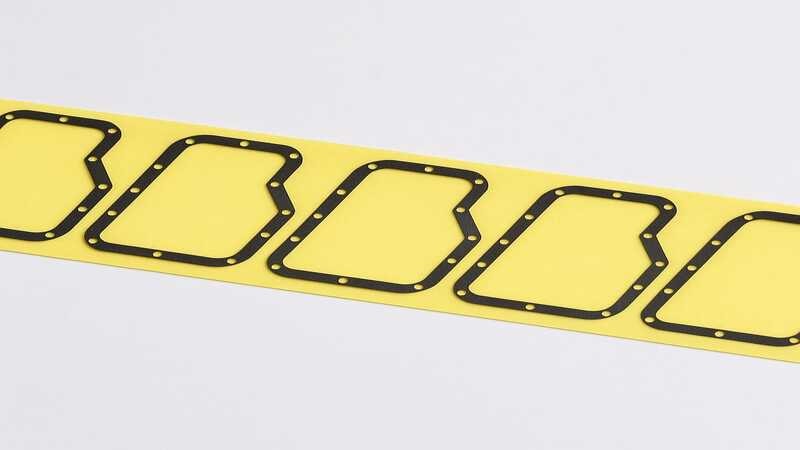
Example of kiss cutting: A simple way to explain kiss cutting is by looking at a sticker sheet. You can easily peel off a sticker while the back layer of the sheet stays in its place.
How Does Kiss Cutting Work?
As discussed earlier, kiss cutting cuts only the top part of the material, keeping the bottom layer intact. The kiss-cutting works on multiple materials, including silicone, paper, vinyl, adhesive, and foams.
Finely calibrated kiss cutting machines carry out the kiss cutting. These machines apply the right amount of pressure on the material to cut only the top layer.
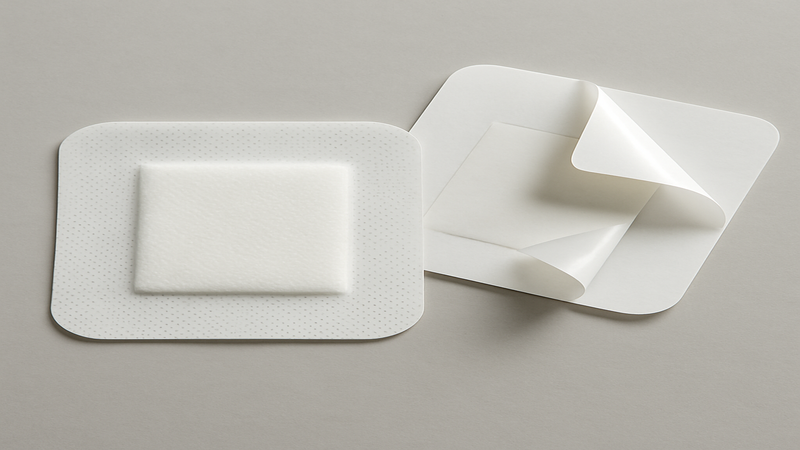
These kiss cutting machines use a blade, laser, or die to apply pressure to cut the top layer of material. The material in the machines may be fed in the form of a roll or laid flat. For higher production volumes, it’s better to feed the machine using rollers for continuous processing.
The final result of kiss cutting is clean as the product is attached to the backing material, and can be peeled easily. With kiss cutting, the product remains undamaged, and waste material is reduced too.
Step-by-Step Kiss Cutting Process
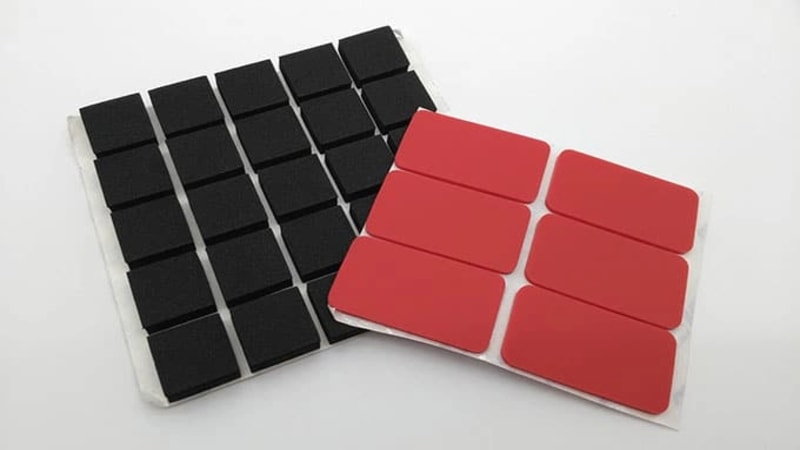
A step-by-step kiss cutting process is given below to assist product designers in conducting kiss cutting accurately and to reap its benefits:
1. Material preparation
The first step is to prepare the material you want to cut. Clean the material and mount it on the liner or backing sheet accurately to prepare it for cutting.
2. Setting the blade/laser depth
Calibrate the machine and set the blade depth to cut only the top layer of material.
3. Feeding the material
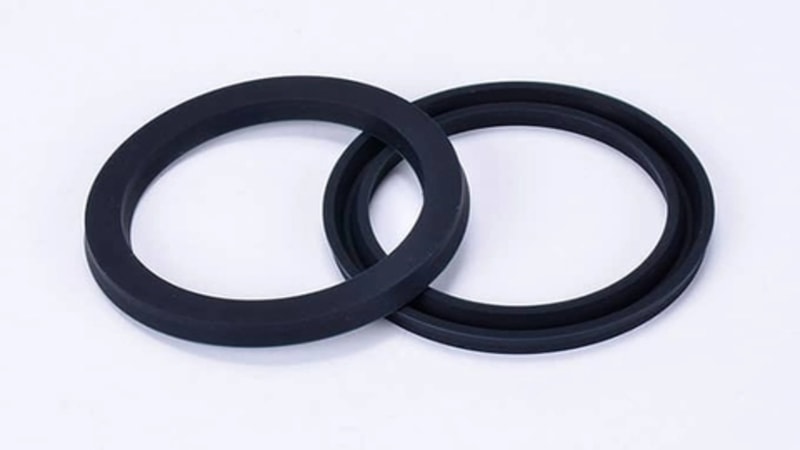
The third step in the kiss cutting process is feeding the material. You can either feed the material in the form of rolls or place it flatly under the cutting tool.
4. Surface layer cutting
In this step, kiss cutting is actually performed, as the machine forms an outline of each piece on the material.
5. Peeling off the finished product
In the last step, the finished part attached to the backing material is peeled off easily, which is then packed and stored or transported. The kiss cutting process is ideal for silicone pads, vinyl, labels, and gaskets.
Kiss Cutting vs. Die Cutting Process
Another common cutting process is die cutting. Unlike kiss cutting, die cutting cuts through all the layers of materials. In die cutting, a sharp steel blade or die applies high pressure on the material to cut evenly through all layers, including the top layer and backing sheet.
A simple example to explain die cutting would be a cookie cutter, which cuts the shape entirely out of material. The common materials used in die cutting are cardboards, foams, plastic films, rubber, silicone, and adhesive sheets.
While comparing die cutting vs kiss cutting, we can say that die cutting solves manufacturing problems by cutting through all layers, whereas kiss cutting only cuts through the top layer.
The table below further compares these cutting methods side-by-side to help engineers choose the one that is best suited to their requirements:
Feature | Kiss Cutting | Die Cutting |
---|---|---|
Cutting Depth | Cuts the top layer only | Cuts through all layers |
Liner Intact | Yes | No |
Typical Materials | Stickers, adhesive pads | Foam, cardboard, gaskets |
Equipment Pressure | Low to medium | High |
Precision | High | Moderate |
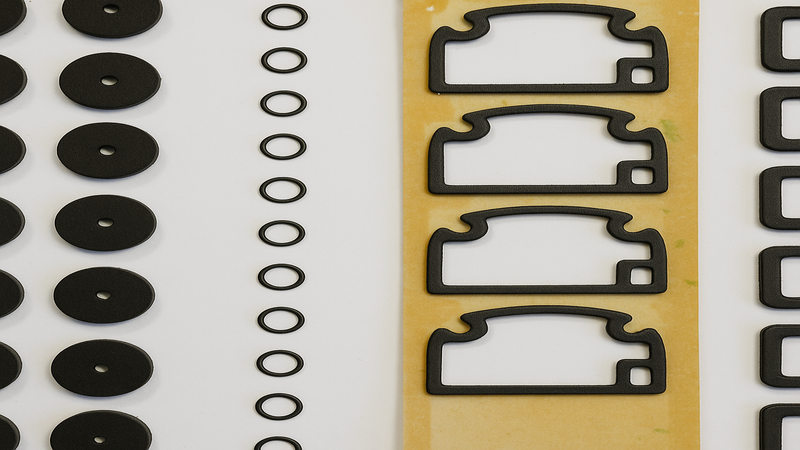
Industrial Applications of Kiss Cutting
Industries that require precision, adhesive control, and easy separation from liners benefit a lot from kiss cutting. Given below are some of the industries that benefit hugely from kiss cutting:
Automotive Industry
Industrial kiss cutting is widely used in the automotive industry. In this industry, rubber, foams, and adhesive-based films are cut using this process. Commonly, the seals, gaskets, and vibration pads are manufactured using the kiss-cutting process.
The reason behind the widespread use of kiss cutting in the automotive industry is that the kiss-cut products are in accurate shape and can be peeled off easily without damaging the product and backing sheet.
Medical Industry
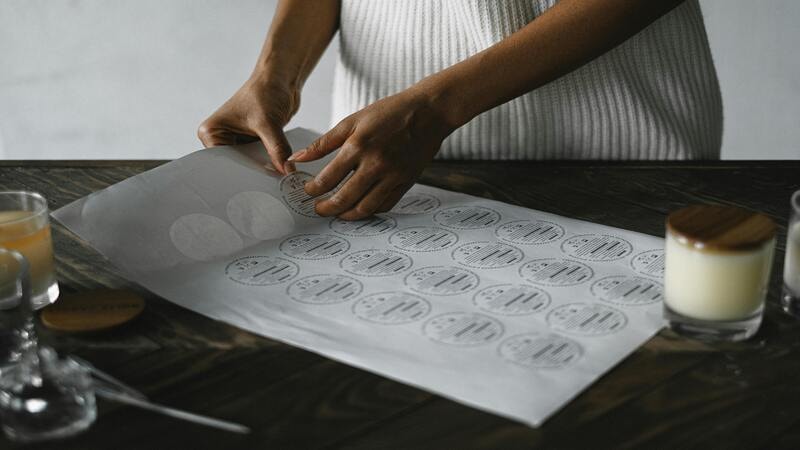
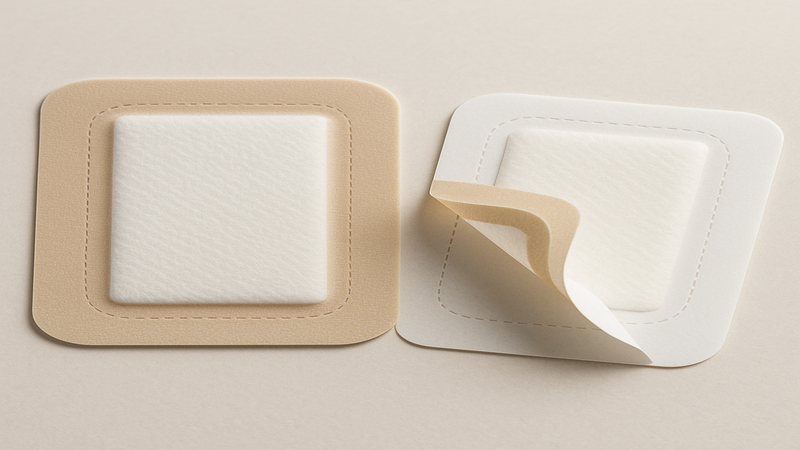
In the medical industry, kiss cutting uses include manufacturing wound care dressings and electrode pads. These products are often made from medical-grade silicone and pressure-sensitive adhesives.
In this industry, sterile and easy-to-handle components are needed. Kiss cutting offers clean cuts and hygiene liner retention – thus it is widely used in the health care sector.
Electronics
EMI/RFI shielding films and adhesive pads are often cut into specific shapes using kiss cutting for internal component mounting. This is done because kiss cutting ensures that the products are precise and fit well in components without damaging the sensitive parts.
The main reason for using this method for electrical industrial applications is that it offers precision and is fast.
Types of Kiss Cutting Machines
There are different types of kiss cutting machines, each having its own pros. Given below are the three main types of kiss cutting machines. Read them to invest in one that is as per your requirements:
1. Rotary Die Cutting
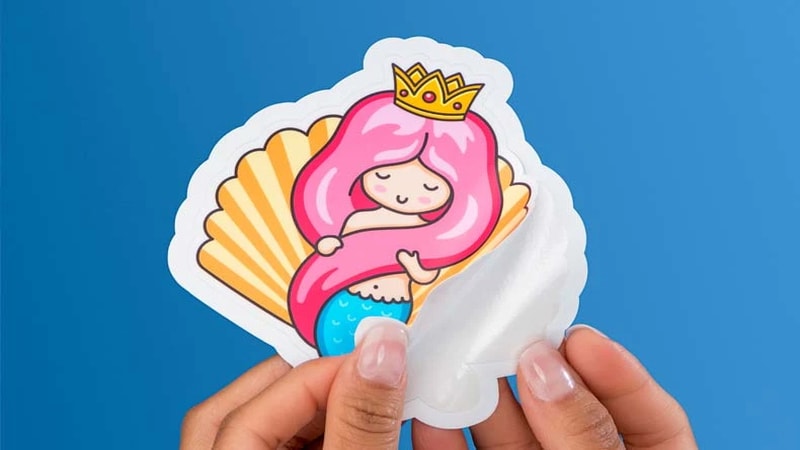
The first type of kiss cutting machine is a rotary die cutting machine. The machine uses a cylindrical die to cut materials. The die spins in a circular motion to cut desired shapes out of materials.
This machine is particularly beneficial in high-volume productions. The roll-to-roll labels and sticker sheets mostly use rotary die cutting.
The pros of this machine are that it is extremely fast and consistent, making it ideal for repetitive shapes. The cons associated with rotary die cutting are that it may not be able to cut through hard materials and has a higher cost.
2. Flatbed Die Cutting
A flatbed die cutting process uses a flat and fixed base with a movable steel rule die to cut shapes from materials. This machine cuts thick materials easily and is ideal for low to medium production volume. This machine is a bit slower than other machines; however, it offers highly precise cuts.
3. Laser Kiss Cutting
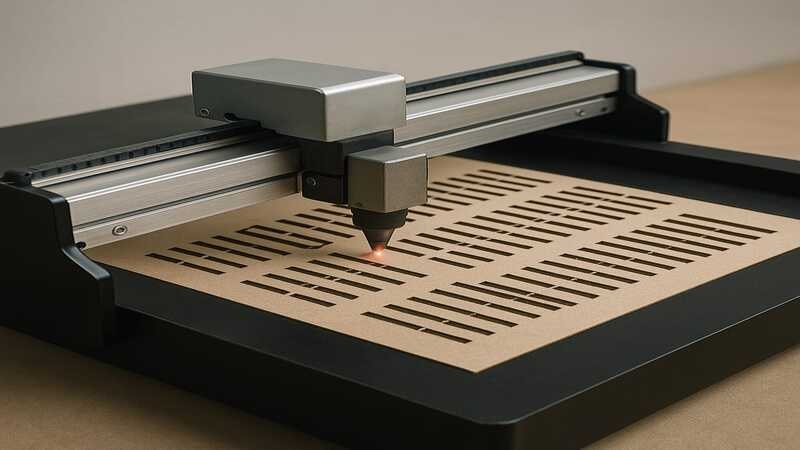
Laser kiss cutting process, as the name indicates, uses a non-contact high-beam laser to cut through the material. Using laser technology, this machine works well in cases of intricate designs, custom shapes, and for smaller batches.
The pros of this machine are that it offers high precision and does not require any physical tools. The cons include that it is slower than rotary die cutting and is expensive.
What Is a Cut Sheet?
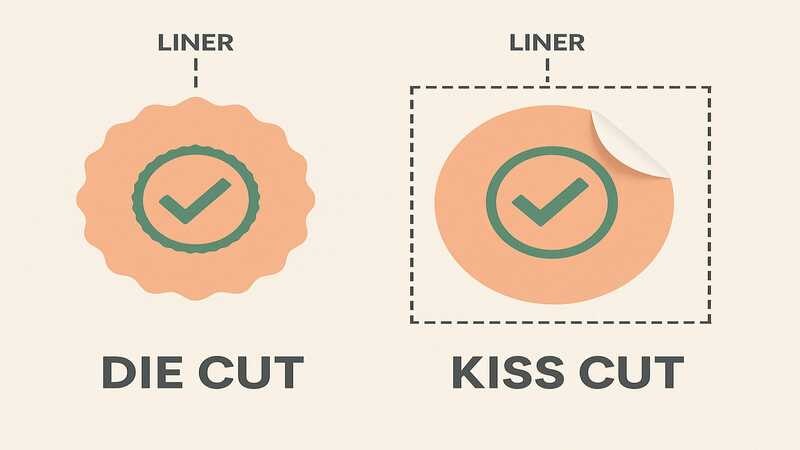
In terms of kiss cutting, a cut sheet is a flat material sheet that is cut partially. In a cut sheet, the shapes are kiss cut on the top layer of material; however, they are attached to the backing material, i.e. the back sheet is still intact.
The shapes that have been cut remain a part of the sheet until they are peeled off. To define a cut sheet easily, think of it as an example of a sticker sheet. The stickers can be peeled off easily; however, until peeled, the stickers are fixed on one flat sheet.
Another example of a cut sheet is a medical silicone pad sheet. The medical pad sheet consists of multiple pre-wound dressing pads ready to be used. A technical gasket sheet, where gaskets are cut but are attached with a back layer, is also an example of a cut sheet.
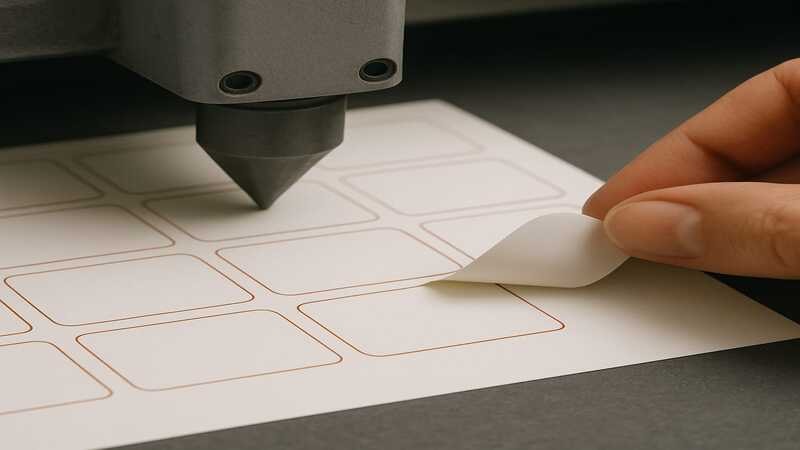
Cut sheets are beneficial as they make it easier to:
- Store or transport parts without damaging them
- Apply kiss-cut pieces quickly
- Keep products organised for use
Owing to all these benefits, cut sheets are an ideal choice for almost all applications.
How to Pick a Kiss Cut Silicone Partner
To reap all the benefits of kiss cutting, you need to find out the most reliable supplier. If you are an industrial buyer, choosing the right supplier is important as it not only improves operational efficiency but also is cost-effective in the long run.
To choose the right supplier, you need to follow the steps given below:
- Expertise
Always choose a supplier who has proven experience working in your industry. The supplier having expertise in the relevant sector better understands your needs and can meet them easily.
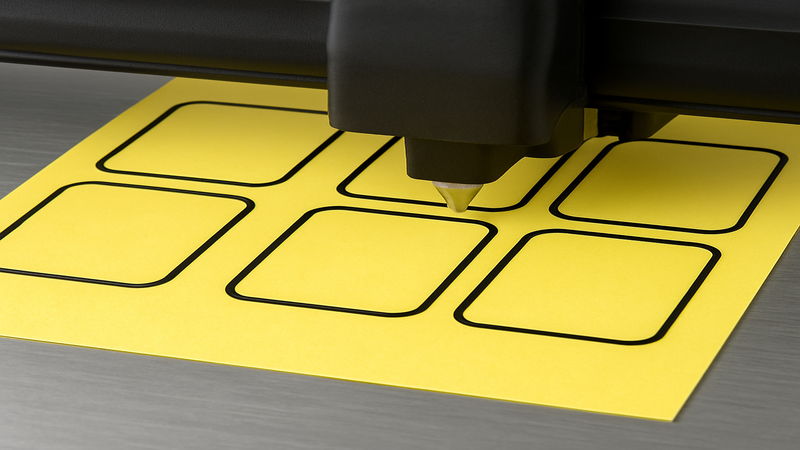
- Machine Capabilities
Choose a supplier that is capable of operating various types of kiss-cutting machines. The supplier should be capable of performing rotary die cutting for high-volume production runs.
Also, the supplier should be able to kiss-cut rigid material using flatbed die cutting. Lastly, suppliers should know how to conduct laser kiss cutting for custom shapes or intricate designs.
- Material Compatibility
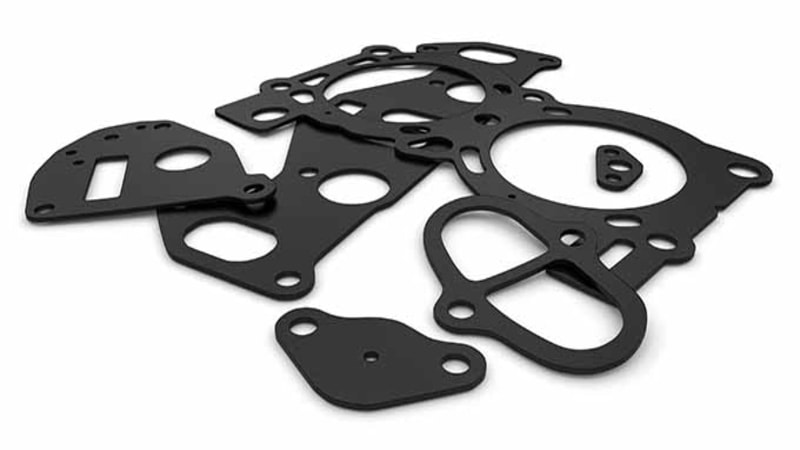
The chosen supplier should have knowledge and experience of working with your material type. Common material types include silicone, foam, vinyl, adhesives, and EMI shielding films. To select the right supplier, you need to determine your material type first.
- Custom cutting services/prototyping available
Check if the supplier can provide custom products and rapid prototyping. Suppliers who offer custom cutting service and prototyping should be given preference over those who are not able to offer custom services and prototyping.
- Quality assurance & certifications
Look for suppliers who meet specific quality standards and hold relevant certifications like ISO 9001 and ISO 13485.
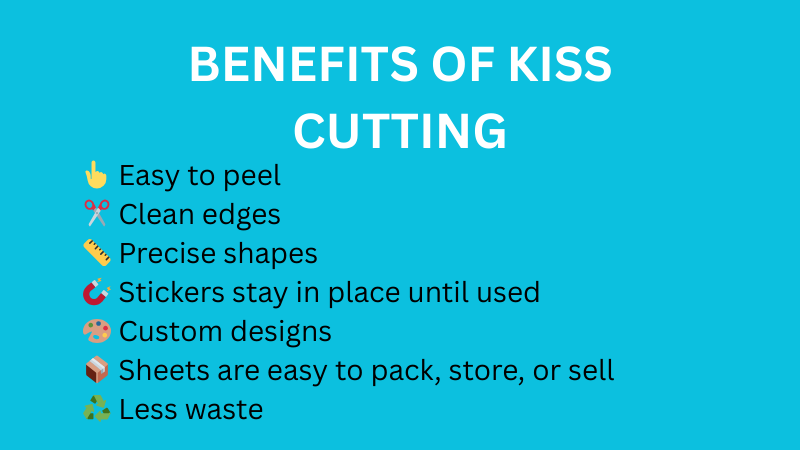
Conclusion
Industrial buyers or product engineers who need precision in cutting should definitely switch to kiss cutting. No matter whether you want to make custom products from silicone or foam, or have to cut intricate designs from vinyl, kiss cutting offers multiple advantages.
To reap all the benefits of kiss cutting, choose a supplier that can offer 24/7 customer support, provides timely delivery, and is ISO 9001 certified.
Explore Custom Kiss Cut Products With Hongju Silicone Today
We at Hongju Silicone are ready to assist you with your kiss-cut projects. Our dedicated team is experienced in meeting all your needs. With our best prices and timely deliveries, there is no way we can disappoint you.
Contact us today to find the perfect cutting method for your unique industrial application and achieve success in your business.
FAQs
Q1. What is a kiss cut?
A kiss cut is when only the top layer of material is cut, but the back sheet remains intact. A sticker sheet best explains the kiss cut meaning.
Q2. Which is better, kiss cut or die-cut?
The answer to this question is not fixed. If you need individual and loose parts, then a die cut is better. However, if you need stickers, labels, or adhesives that stay on the liner until peeled off, then you should go for a kiss cut.
Q3. What is the difference between kiss cut and square cut?
Kiss cut, cut only the top layer, leaving the back layer intact. In contrast, a square cut cuts a straight edge through all layers. It is commonly used for cutting rectangles and squares.