Read this article to learn about the process of liquid silicone rubber injection molding, its main features, advantages, and applications.
What is Liquid Silicone Rubber (LSR) Injection Molding?
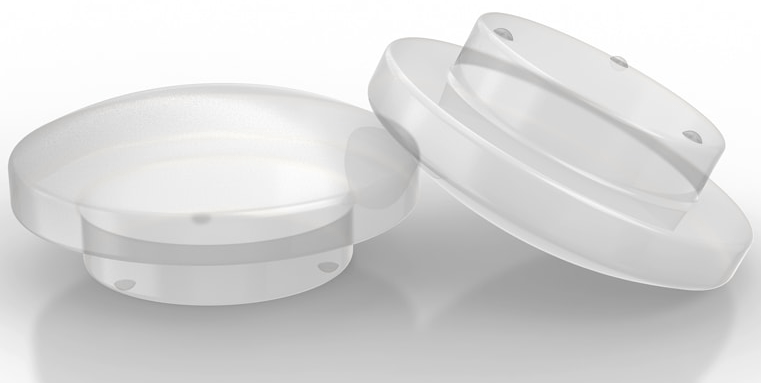
First of all, silicone and silicon are two different things. So, let’s not confuse these two. The existence of liquid silicone rubber was found in the late 1970s. Injection molding of liquid silicone rubber offered a much better quality of parts than thermoplastic injection molding. Therefore the process became popular quickly for manufacturing liquid silicone rubber parts.
The liquid silicone rubber is a thermoset elastomer. Silicon molding allows the heating of the mold while the delivery system of the material cools down. The liquid silicone rubber molding design process is automatic. Its cycle time is concise. For this reason, the price of the liquid silicone rubber parts is low.
Liquid silicone rubber components have excellent mechanical properties. The material has high tensile strength, low viscosity, and elasticity. Moreover, they resist electricity, heat, and chemical reactions. Their biodegradable nature allows them to be sterilized as well. Therefore, these components suit medical, automotive, consumer goods, and electrical applications.
Liquid Silicone Rubber Injection Molding Process
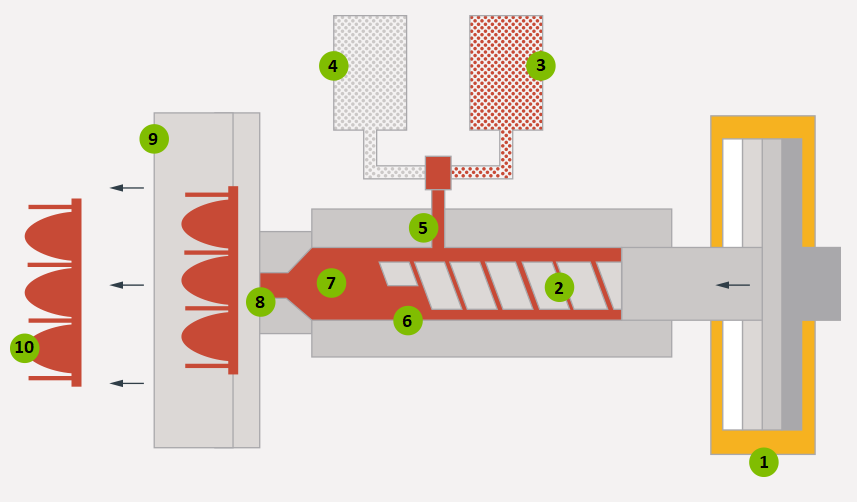
The below section shows a step-by-step guide for the complete silicone rubber injection molding process:
- Two containers or supply drums hold uncured liquid silicone. One of these containers contains the base-forming material. The other one includes a catalyst.
- There is a metering unit. It helps to automatically release the two materials in an equal and constant ratio. If there are any pigmentation additives, the metering units also release these.
- The operator can customize and program the silicone rubber molding machine to make it automatic. The injection is customized to maintain a consistent shot size for each part.
- Pistons and platens are aligned before closing the mold. The alignment has different settings for the pressure applied, temperature, cycle time, and injection rate, adjustable depending on specifications.
- After the operator sets all the values, the molding machine gets hot, and the mold temperature rises. A proper level of clamping force is applied to the mold clamp.
- When the mold is closed and the pump and the injector are ready, the silicone rubber is pushed into the mold cavity with the help of an injection mechanism.
- The liquid silicone rubbers are cured at an appropriate pressure and temperature until solidification occurs.
- Once solid, the operator can manually remove the silicone rubber product. An automatic ejection mechanism with gippers can be used as well. But, the removal doesn’t require ejector pins as silicone rubber is very flexible.
After finishing the steps above, the manufacturer prepares the mold for the following liquid silicone injection molding cycle.
Note that there are also post-molding processes such as post-curing, cleaning, inspection, and packaging. These steps are equally necessary for the quality assurance of your silicone rubber products.
Unique Capabilities of Liquid Silicone Rubber Injection Molding
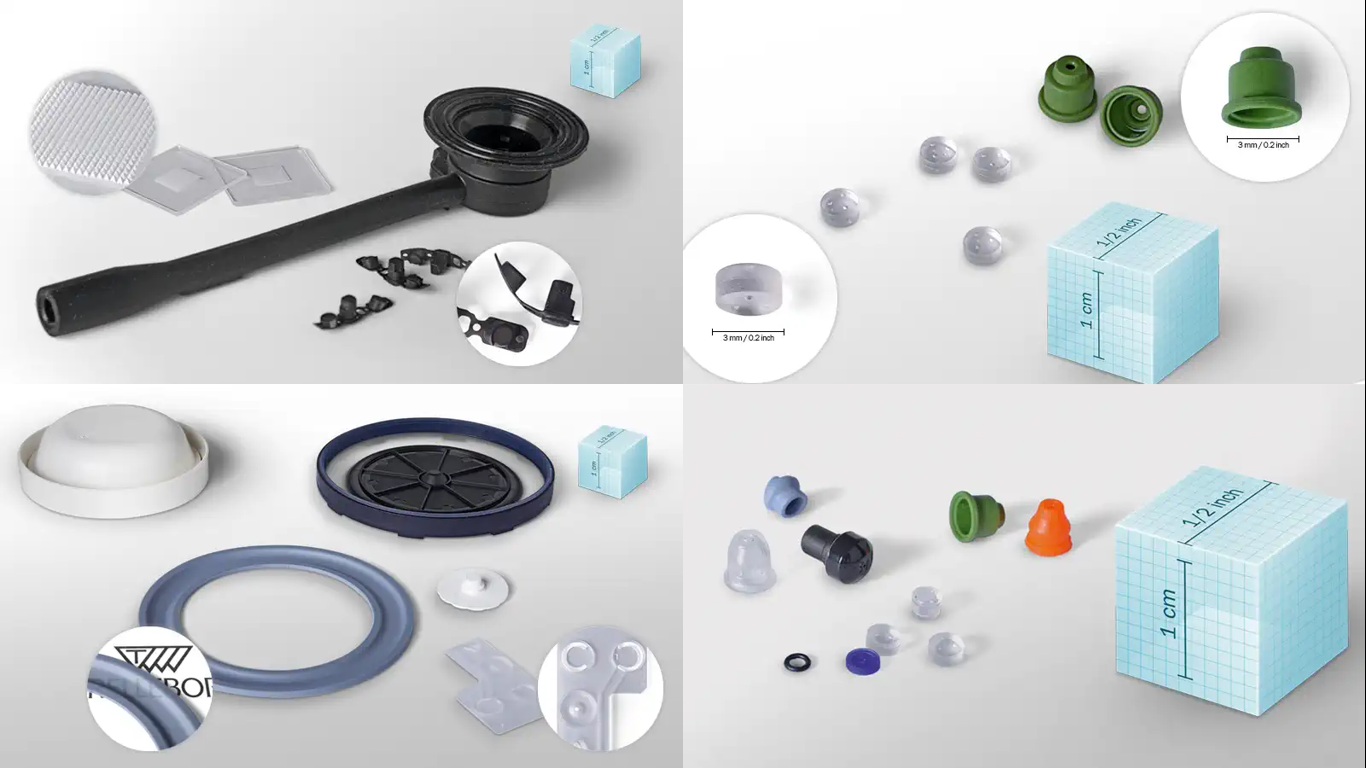
Liquid silicone injection molding is a process capable of many unique manufacturing aspects. Here are a few special properties of the liquid injection molding process:
Thin Sections
Silicon molding can create parts with sections as thin as 0.1 mm or 0.004 inches. The parts will have perfect thickness. The quality will be consistent throughout the whole part as well. LSR parts have no pinholes due to the latest technology of molds. The materials used in this production process are ideal for thin sheets or membranes.
No Flash
The manufacturer doesn’t need any secondary deflashing in the production process of LSR parts. The primary materials used in this process give extreme dimensional stability to the products. This production process is a wasteless and flashless process with high efficiency.
Nano/Micro Technology
Liquid injection molding can make minimal parts that may weigh below 10 mg. The parts for the production process are fully automatic, and the injection system is a needlepoint injection. For this reason, such low-weight parts can be obtained.
Delicate Parts
Very delicate parts can be produced using this manufacturing technology. And every time the operator starts the direct injection process, the parts are formed each time reliably. The unique construction tools and automation allows the production of silicone parts with fine texture and intricate details.
High Precision
The textured surface of the parts is highly polished due to the LSR materials. The manufacturing process is consistent, even if the manufacturer intends to produce millions of parts with the same machine.
Blind Sections
You can produce plastic parts using the LSR molding process. Every time the machine operates to create a part, through-holes are shaped each time perfectly. The manufacturer can also produce long tube sections accurately without any worries. It is easy to make special tools using this process.
Undercuts
Undercuts in product design are a critical aspect of any manufacturing. However, that’s not the case for Liquid silicone injection molding. Due to the flexible nature of silicone rubber, the parts can be easily removed from the tooling. So, special design considerations are not necessary for undercuts.
Advantages of Liquid Silicone Injection Molding
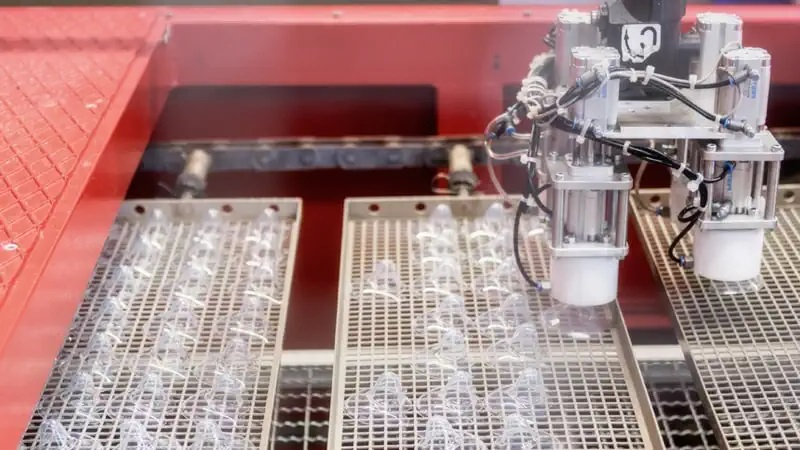
LSR or liquid silicone rubber parts offer many benefits for users. Here are some of the advantages of this molding process:
Consistency
The silicone molding process is very consistent in producing the same part. The main reason behind this is using the same mold for making the same part. Being consistent provides a lot of convenience to the manufacturer and the customers.
Precision
Liquid silicone molding ensures excellent precision for your parts. You can design parts with intricate details and undercuts without worry. Also, you are less likely to need costly post-processing to improve the accuracy of parts.
Quality
If the parts don’t have high quality, the customers won’t be satisfied with the product. In addition, manufacturers use the injection molding process to ensure the high quality of the parts.
Purity
The mixing process of the LSR injection compression molding is exact, and the final product contains minimum impurity. The final product has almost no impurity due to the highly sophisticated manufacturing process.
Limitless Design
If the liquid silicone rubber LSR parts are made of injection compression molding, then there is a chance of designing a part with any design that pops up in the operators’ minds. This is because the raw material is easy to handle, and it is very easy to make the mold.
Reliability
The manufacturers can easily rely on the injection molding process of LSR for product manufacturing. Because this process is straightforward and fast to perform, it is convenient to keep track of the quality of the finished goods.
Cost-effectiveness
The LSR injection molding process has a fast cycle that allows manufacturers to make products in high volumes faster. For this reason, sales volume increases. This is why this manufacturing process is relatively cost-effective.
Applications of Liquid Silicone Rubber Molded Parts
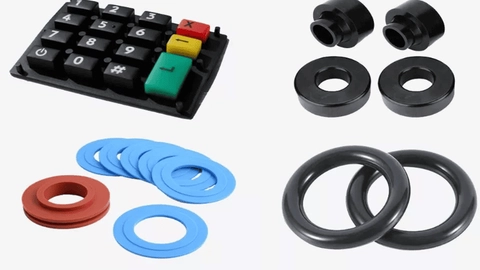
Many industries use liquid silicone injection molded parts for many applications. The below list shows a few of those industries:
- Medical
- Infant and Geriatric Care
- Automotive
- Electronic Products
- Food and Beverage
Various parts such as silicone rubber keypads, O-rings, seals, wire harness seals, bellows, vibration dampeners, faucets, bacteria-resistant shower heads, electric toothbrushes, hearing aid ear tips, headphone ear tips, baby bottle tips, rubber grommets, etc. are made of this process for the above-given industries.
Conclusion
To ensure optimal results with the Liquid Silicone Rubber Injection Molding Process, it’s crucial to evaluate the capabilities, track record, and customer service of potential manufacturers before making a decision.
The article provides a comprehensive overview of the process, highlighting its key steps and benefits. Conduct careful research, adequate analysis, and evaluation of each manufacturer’s capabilities and values to ensure successful results in the process. Proper supplier selection is crucial to achieving optimal outcomes.
Why Should You Choose Hongju for Silicone Rubber Products?
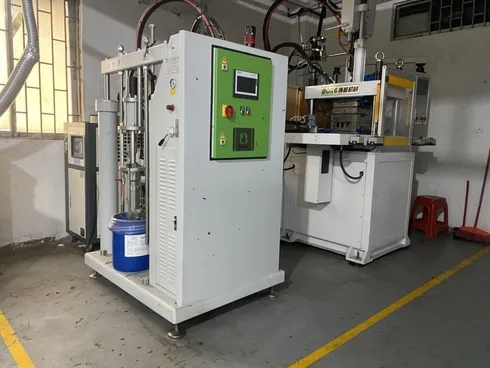
- We make customized parts based on your demands and requirements.
- Our manufactured goods are FDA and CE-approved. These are safe to use.
- We focus on the environment and manufacture eco-friendly products.
- You can always get support from us regarding any query you have.
Buy Liquid Silicone Injection Molded Components from Hongju
If you are looking for customized silicon rubber products, you can contact us at Hongju. For over 20 years, we have been manufacturing components using LSR for various industries. Our manufactured parts include silicone rubber keypads, rubber grommets, O-rings, seals, gaskets, etc.
We are dedicated to assisting our customers in making their vision a reality. We will do our best to achieve the best possible outcomes, whether manufacturing unique silicone items or working directly with our customers.