In this post, we’ll explore five key benefits of using silicone rubber molds for product design. We’ll dive into how these molds enhance design capabilities and why they’re becoming increasingly popular across automotive and consumer goods industries.
5 Advantages of Silicone Rubber Molds
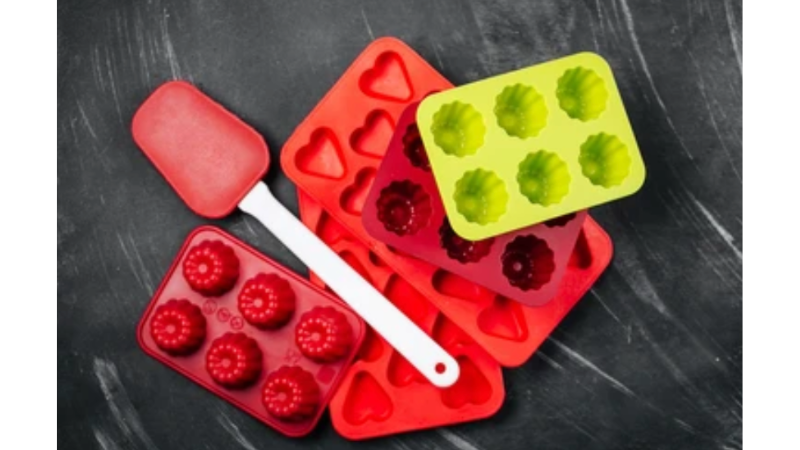
Silicone rubber molds have remarkable attributes that can notably enhance your business’s production process and amplify the quality of the end product. Let’s explore the five key advantages with specific business examples.
1. Versatility
The foremost advantage is the versatility of rubber injection molding. They are adept at replicating intricate patterns and delicate components, catering to various industries. For instance, an automotive manufacturer might use them to create precise engine parts, while a culinary business may use them to shape unique silicone utensils.
2. Durability
The robustness of silicone molds is another notable benefit. Their resistance to wear and tear allows repeated usage without losing shape or quality. For example, in the toy manufacturing industry, a single silicone mold can be used to produce thousands of identical, high-quality action figures, leading to substantial cost savings over time.
3. Flexibility
Silicone molds’ flexibility facilitates the easy release of complex or delicate designs without causing damage. For instance, a jewelry manufacturer can create detailed, fragile designs in their products, knowing that each piece will come out of the mold intact.
4. Heat Resistance
Many production processes involve heat, and silicone molds can withstand it. In the electronics industry, for instance, these molds can handle high temperatures during procedures such as over-molding for cable assemblies, ensuring the safety and efficiency of the operation.
5. Compatibility
Lastly, silicone mold works well with various materials, including liquid silicone rubber and urethane. This compatibility allows businesses to select the material that best meets their specific needs.
For example, a prosthetics company might use urethane for its mechanical properties, while a kitchenware company may use liquid silicone rubber for its food-grade quality.
These advantages underscore why silicone rubber molds are a valuable asset for businesses in diverse industries.
Disadvantages of Silicone Rubber
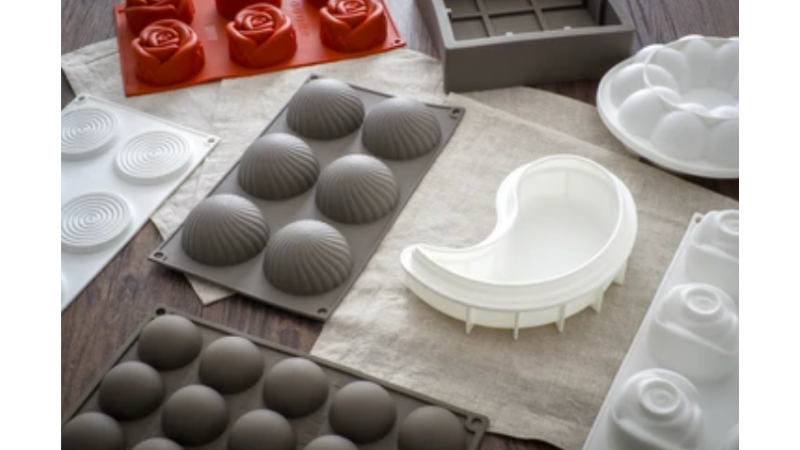
While silicone rubbers have several benefits, it’s also important to be aware of some potential challenges. Here’s what you should consider:
Initial Cost of Silicone Materials
Silicone rubber materials might seem pricey initially compared to other molding materials. However, considering the long-term benefits, such as durability and reduced replacement costs, is crucial, which can offset the upfront investment.
Proper Curing and Mold Release Techniques
Silicone mold needs proper curing to achieve optimal results. Inadequate curing can affect the final product’s quality. Additionally, using the right silicone mold release techniques is crucial to prevent sticking and ensure easy demolding.
Sensitivity to Contaminants
Silicone rubber can be sensitive to certain contaminants. Exposure to substances like sulfur, latex, or amines can inhibit the curing process. This means careful handling and storage are required to maintain silicone rubber’s performance.
Dimensional Limitations
Though silicone molds are versatile, they might not be suitable for very large or heavy parts due to their flexibility. In such cases, other silicone mold-making methods might be more appropriate.
Understanding these potential drawbacks can help you decide whether silicone rubber molds fit your business. It’s all about finding the balance that best suits your production needs and budget.
Applications of Silicone Rubber Molds
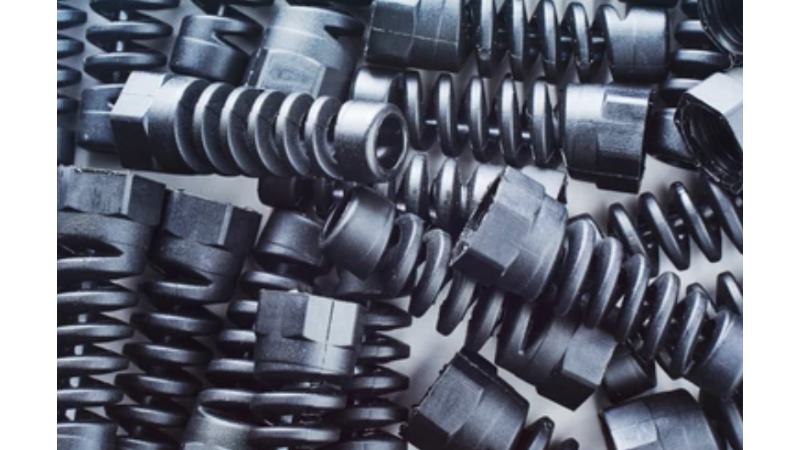
Silicone rubber molds find a range of applications across industries due to their distinctive advantages. Here’s how they’re making a difference:
Injection Molding
Silicone rubber is a go-to choice for liquid injection molding. Its heat resistance allows it to withstand the high temperatures involved in this process. It results in precise, high-quality parts efficiently and consistently.
Urethane Casting
In urethane casting, silicone mold shines by producing high-quality, detailed prototypes and end-use parts. Their flexibility ensures the easy release of the cast parts, even those with intricate designs, contributing to a smoother production process.
Other Applications
Silicone rubber molding is not limited to industrial processes. They are used in a variety of creative applications. For example, they’re used for creating molds for concrete or resin art, where their flexibility and durability enable the creation of detailed, long-lasting pieces.
In the food industry, food-grade silicone molds are used for their non-toxic, non-stick, and heat-resistant properties, making them perfect for creating a variety of food products.
Regardless of the application, silicone rubber molds offer key advantages that can enhance the efficiency and quality of your production process, making them a valuable asset for businesses across sectors.
Silicone Mold Making Process
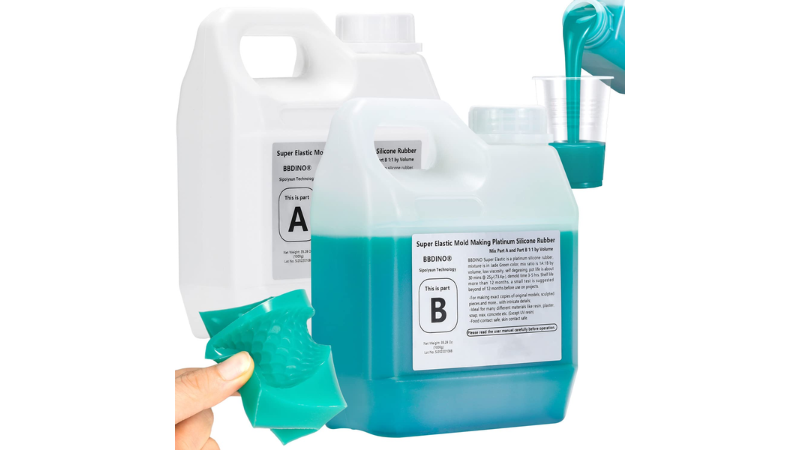
Creating silicone molds is a key task in many industries. It’s a step-by-step process that transforms designs into real-life products. This process is valued for its accuracy, time efficiency, and cost-effectiveness. Let’s delve into the specifics.
Mold Preparation
Proper mold preparation is a must. It forms the basis for a high-quality mold that accurately replicates the design. Here’s how it’s done:
- Craft the Master Model: First, create a master model. This model, made of materials like wood, metal, or plastic, is the basis for the mold. The model needs to be precise in design, size, and texture.
- Get the Mold Box Ready: Next, set up a mold box. This box will house the silicone rubber and the master model. Make sure the box is sturdy and has enough room for the model and rubber.
- Use a Mold Release Agent: Finally, apply a mold release agent. This agent stops the silicone rubber from sticking to the model and the box. This makes it easier to remove the mold later and also allows for reuse.
Mixing and Pouring Silicone
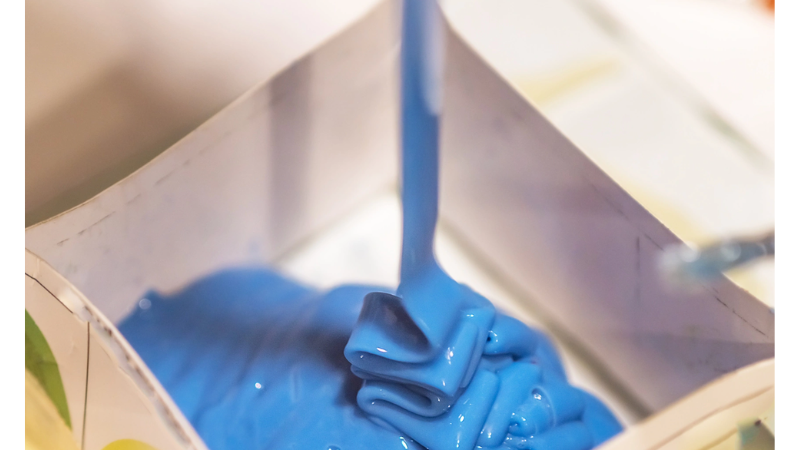
The next phase involves mixing and pouring silicone. It’s a delicate task that demands precision and patience. Here’s how to proceed:
- Measure the Silicone: Start by measuring the required silicone rubber and catalyst. Follow the manufacturer’s instructions to get the correct ratio.
- Mix Thoroughly: Blend the silicone rubber and catalyst together. Make sure the mix is thorough, but try to prevent too much air from getting in.
- Pour Slowly: Pour the silicone mix over the master model in the mold box. Begin at the lowest point and move up to minimize air bubbles.
You can create a smooth, bubble-free mold by carefully measuring, mixing, and pouring.
Curing Process and Challenges
Curing is the process of letting the silicone harden. It’s simple but has its own challenges. Here’s what you need to know:
- Let It Cure: Allow the silicone to cure as per the manufacturer’s guidelines. The recommended time and conditions vary, so it’s important to check.
- Beware of Bubbles: Air bubbles can spoil the finish of the mold. You can avoid them by degassing the silicone mix in a vacuum chamber before pouring. Another tip is gently tapping the mold box to let any trapped air escape.
By paying attention to these points, you can ensure your mold cures smoothly.
Demolding and Finishing
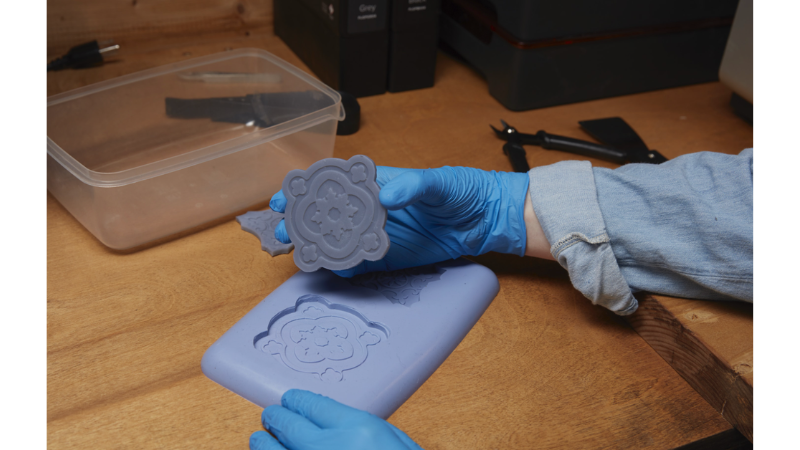
The last stage is demolding and finishing. It’s all about carefully extracting the mold and tidying it up. Here’s the process:
- Remove the Mold: Carefully take out the cured silicone mold from the mold box.
- Release the Model: Gently separate the master model from the silicone mold.
- Inspect and Trim: Look over the mold for any faults. Trim off any excess silicone if needed.
By following these steps and addressing common challenges, you can create high-quality silicone molds that meet your specific needs. The proper mold-making process ensures a smoother production experience and better end results for your business.
Conclusion
In wrapping up, silicone rubber molding is a game-changer in product design across industries. Rubber materials have diverse temperature ranges, which aids in high-quality production.
Although there are a few challenges, proper techniques can help overcome these for optimal results. For more in-depth resources, feel free to explore our other blog posts and resources on our website. Let’s harness the power of silicone rubber molds to drive our industries forward.
Ready to Enhance Your Product Design?
Reach out to us today! At Hongju Silicone, we’re experts in silicone rubber molds and can help guide you through the process. Whether you’re new to silicone molds or looking to improve your existing processes, our team is here to assist. Visit our contact page to get in touch. Let’s work together to elevate your product design to new heights.