Are you tired of dealing with complicated and expensive materials in your electrical and electronic applications? Look no further than plastic! This versatile material is a must-have in the electrical and electronic industry, offering numerous advantages such as cost-effectiveness and durability. Not to mention the sustainable solutions it provides for power transmission.
In this article, we’ll talk about the widespread use of plastic in electrical and electronic components. Further in the article, we’ll discuss the benefits of choosing this material:
Importance of Using Plastic Materials in Electrical Applications
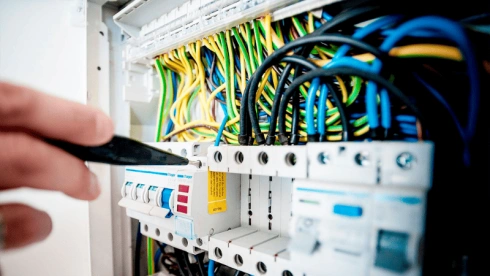
You’ll find electrical and electronic plastic in many surprising places, including your home!
Here are the five most common uses of plastic components in the electrical industry:
Cable and Wiring Insulation
Every household cable and wire comprises an electrical enclosure to improve strength, provide electrical insulation, and ensure safety.
Additionally, a plastic enclosure provides excellent insulation properties, minimizing the risk of current leakage and electric shock. Plus, plastic is resistant to corrosion, giving you peace of mind that it won’t degrade quickly.
Circuit Breaker Housings
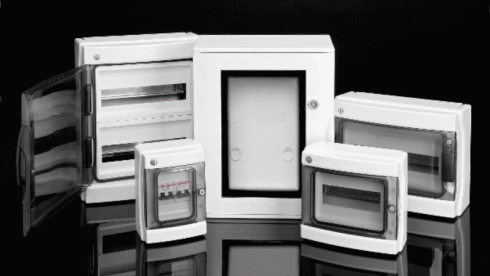
Circuit breakers are more powerful than a standard casing to safely handle the influx of electrical charges.
For this reason, high-voltage circuit breakers contain plastic components, ensuring no risk of fires or other hazards.
Conduits
Electrical conduits route the wiring in a robust structure while insulating wires to prevent electrical leakage. As such, plastic is an excellent choice for pipes!
You can select a rigid or flexible exterior based on the unique project demands.
Casings
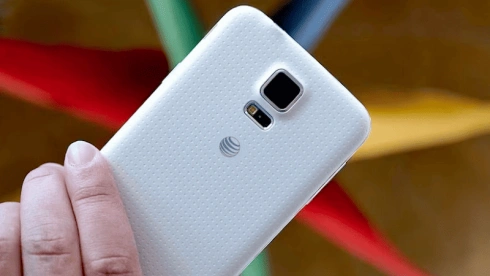
Plastics like polycarbonate are ideal for use in modern electronic components. Cell phone and laptop casings generally consist of a chemically-treated polycarbonate, offering scratch resistance.
Therefore, these electrical appliances can withstand extreme temperature fluctuations, ensuring durability.
Circuit Boards
Circuit boards are prevalent across almost every industry. Using an electrical and non-conductive plastic allows power transmission across the copper tracks while ensuring safety.
You’ll find circuit boards with plastic products in electronics, including cell phones, laptops, automobiles, and televisions. Many producers now create 3D-printed circuit boards to enhance manufacturing processes and save costs!
Inquire About Our Silicone and Plastic Products!
Types of Plastic Used in Electrical and Electronic Applications
When designing plastic components for electronic devices, one of the essential things is to consider the properties you require. Based on your needs, you can select one of a million types of plastic to fulfill the project’s demands.
Although plastics are of various types, they fall into two broad categories:
Thermoplastics
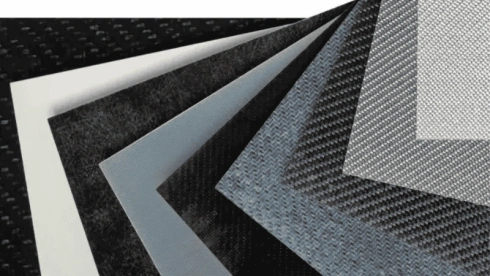
Thermoplastics are solid at room temperature but convert into fluid when heated above the glass transition temperature (Tg). Since the resin lacks strong chemical bonds, you can pour them into any mold to achieve your desired shape.
In addition, you can reheat, recycle, and remold thermoplastic elastomers without affecting their conductive and insulation properties. As a result, the plastic material is perfect for use in extrusion, injection molding, and thermoforming processes.
Thermoplastics generally offer excellent elasticity, strength, and shrinkage resistance. As such, its applications include industrial machine components and plastic bags.
Thermosetting plastics
Thermosetting plastics, or thermosetting resin, are polymers that liquidity at room temperature and harden upon heating and chemical addition.
The production processes for thermosetting plastic include Reaction Injection Molding (RIM) and Resin Transfer Molding (RTM). The polymer forms strong chemical bonds during curing, holding the molecules in place and transforming the material’s nature.
After heating, thermoset plastics acquire a unique form, and the monomer chains, called crosslinks, prevent the material from melting. In addition, the material boasts high dimensional stability and heat and chemical resistance. Therefore, this polymer is ideal for application with heat, including electronic appliances or chemical processing equipment.
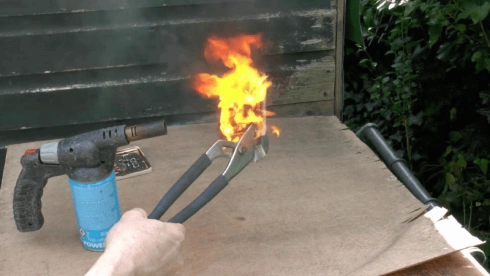
Comparison of Thermoplastics and Thermosetting plastics
Although thermoplastic and thermosetting plastics are polymers, they differ with regard to properties, manufacturing processes, applications, and benefits.
Thermoplastics and thermosets are two distinct classes of plastics. The former can be remelted and remolded after curing, while the latter retain their shape under heat. Most people tend to use thermoplastics where recycling is required, as they have low melting points. But for applications where materials must withstand high temperatures and show phenomenal dimensional stability, thermosets are the best choice.
When considering aesthetics, there’s no question about it – thermoplastics take the cake! However, both thermoplastic and thermoset plastics allow for in-mold painting and spraying coatings into the mold before injection molding. This means that either can be personalized to match your desired style and look. Furthermore, both kinds of plastics can be made in a wide variety of colors and textures, making them excellent choices for both functional and decorative applications.
Inquire About Our Silicone and Plastic Products!
Advantages of Using Plastic in Electrical and Electronic Applications
Plastics are invaluable in electrical and electronic devices due to their versatile and robust properties, including:
1. Excellent Electrical Properties

Electricity is an essential element of modern life, but it also comes with the potential for danger. According to the Centers for Disease Control and Prevention(CDC), electrical injuries led to 360 fatalities and 426 permanent disabilities in 2020. As such, it’s vital to prioritize safety measures when installing or handling electrical devices. One such measure is to use plastic components with excellent insulation properties in our electronic devices. This way, we can reduce the risks of electrical injuries and other accidents.
Many people use Polyvinyl Chloride (PVC) to insulate electric wirings, whereas light fittings, handles, and switches involve thermoset plastics. PVC and silicone rubber have similar features, but they are not the same. In addition, you’ll find high-quality plastic on daily electrical components, such as razors, food mixers, and hairdryers, to protect the wiring and consumer’s life.
2. Wide Range of Chemical Resistance
Plastics come in a variety of compositions and chemistries, each with unique properties that make them suitable for different applications. Many plastics, such as those made from polyethylene and polypropylene, have excellent resistance to hydrocarbons and acids and are suitable for use in electronics and semiconductor processing.
Meanwhile, other plastics, such as acetals, have a low resistance to acids but can withstand strong bases and organic solutions, making them ideal for specialty applications where resistance to these chemicals is necessary.
It’s worth noting that some plastics, such as ultra-high-molecular-weight polyethylene (UHMW), have superior resistance to both acids and alkalis, as well as organic solvents, and are excellent choices for applications involving harsh environments.
3. Ability to Withstand High Temperatures
Most plastics are poor conductors of heat; however, manufacturers provide fire-resistant options by adding flame-retardant additives. These heat-resistant plastics help mitigate the risk of burns and injuries and are therefore prevalent in electrical equipment.
Therefore, different plastic materials have varying heat resistance. For instance, Teflon can withstand temperatures as high as 500°F (280°C), whereas polyphenylene sulfide (PPS) displays heat resistance up to 428°F (220°C).
4. Cost-Effectiveness
Another fantastic benefit of plastic is it incurs low cost despite offering high performance.
The versatile material provides durability, sustainability, and longevity and is cost-efficient! Therefore, manufacturers can prevent the high-cost production of electrical components and appliances by leveraging plastic.
Inquire About Our Silicone and Plastic Products!
Other Electrical Insulators
Apart from plastic, electrical components may utilize different insulation materials. These include wood, glass, and rubber.
Below we’ll discuss in-depth the electrical and thermal performance of these materials in electrical and electronic devices:
Wood
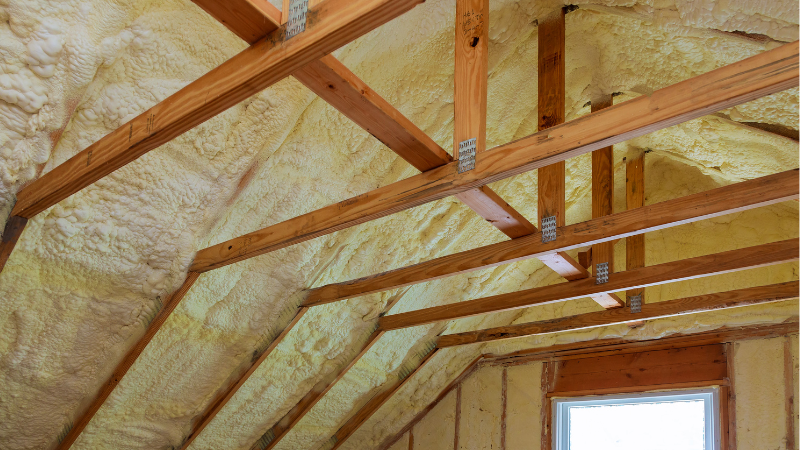
Wood is a sustainable and long-lasting material used in homes and industrial applications. Dry wood is an excellent electrical and thermal insulator because there are no free ions.
However, moist wood comprising impurities like salts can conduct electricity. Although poor conductors, any moisture can allow the flow of small amounts of electrical charge. Plastic is a safer option, particularly since it is water-resistant.
Glass
Glass, as an electrical insulation material, is inferior to rubber and plastic! That’s because the thermal conductivity of plastic is up to 5 to 10 times lower than that of glass.
In addition, glass tends to have a more regular atomic arrangement than plastic, such that it allows the flow of electrons. Contrarily, plastic has no free electrons, making them the ideal thermal and electrical insulator.
Rubber
Similar to plastic, rubber is a polymer comprising multiple monomers that link together to form a solid material. The primary difference between plastic and rubber is that the latter are elastomers, whereas the former has plasticity.
That means you can stretch rubbers, and upon release, they will retain 90% of their original shape and dimensions. In contrast, heat and pressure lead to a long-lasting dimensional impact on plastics.
Although both materials have exceptional electrical and insulation properties, plastic stands out. The material lacks free electrons, eliminating conductivity and enhancing thermal and electrical insulation.
Why is Plastic a Good Electrical Insulator?
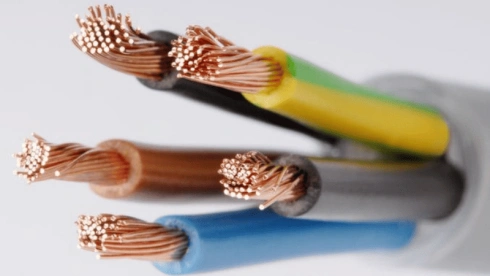
If you’re scratching your head about plastic’s electrical insulation properties, allow us to explain.
Plastic’s tightly bound nuclei are devoid of free-moving electrons, which eliminates electrical current and ensures safe, steady transmission of power. With no random electron movement, the polymer’s outermost valance shell becomes an effective sound insulator too!
Thanks to the exceptional electrical insulation of plastic, it plays a crucial role in the manufacturing of electrical and electronic components, including handles, switches, and plugs.
Inquire About Our Silicone and Plastic Products!
How Does Plastic Make Wires Safe to Handle?
As we discussed, plastic limits the flow of electrons, ensuring no current passes and protecting the consumer against electric shocks. Therefore, using the non-conductive material on wires ensures the current doesn’t flow outside the system.
In addition, by creating a barrier between electrical wires and the user, plastic prevents current and sparks that could lead to injuries. Beyond arcing and sparking, the plastic film mitigates the risk of fire by dissipating heat build-up.
Sustainability of Using Plastic in Electrical and Electronic Applications

Another factor in plastic’s ever-growing popularity is its sustainability. The polymer is not only durable, but it’s also energy-efficient and recyclable!
Let’s discuss in depth why plastic is a sustainable alternative in electrical and electronic applications:
Environmental Impact of Using Plastic Materials
Plastic takes less energy to produce, making them cheaper to manufacture and buy while benefitting the environment. The material can help protect our environment by conserving water and energy resources, reducing waste, and minimizing greenhouse gas emissions from vehicles.
As such, plastics are greener than other materials, making them ideal for electronic applications. Additionally, the polymers are resistant to UV rays and chemical attacks, meaning they can last for years before needing replacements.
Overall, plastic outperforms traditional materials in terms of sustainability because:
- The material has a lower environmental impact
- You can recycle waste plastics into various forms
- You can convert the polymer into fuel
- The material is lightweight, requiring less fuel to transport
- You can easily compress the material, which allows for efficient storage
Recycling and Reusing Plastic Materials
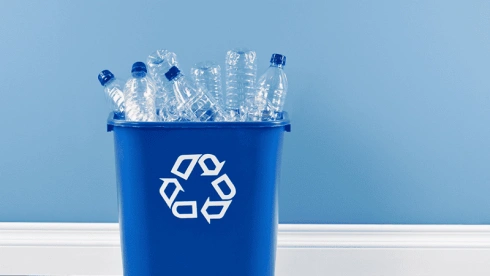
When you no longer require plastic components, you can recycle and repurpose them instead of discarding them to prolong their lifespan and minimize energy consumption. The process typically starts with sorting and then involves mechanical and/or chemical recycling methods to make them suitable for reuse.
Here’s why recycling and reusing plastic materials is a must:
1. It helps Reserve Natural Resources
Recycling plastic waste products lessens the demand for the natural resources present on the earth, including water, wood, gas, and oil. We can significantly reduce the amount of plastic waste in landfills by recycling instead of repeatedly producing the same quality material. Recycling existing trash makes it feasible to conserve resources. Furthermore, as an alternative to discarding used plastic bags and bottles, creating wood-plastic composites is recommended for better and longer-lasting use.
Plastic-making processes use natural resources, thus wasting water, energy, and petroleum. Reducing the use of plastic would probably ensure conserving these natural resources to make non-biodegradable plastic in the future. Reduced dependency on natural resources will lower atmospheric carbon dioxide concentrations and prevent an oversupply of petroleum products.
2. Aids in minimizing landfills
Plastics take several years to decompose. No matter where it is stored or maintained, it will take some time to break down. Customers may successfully decrease the amount of plastic waste taking up landfill space that could be utilized for biodegradable goods by recycling plastic raw materials and transforming them into other products. Recycling is a good idea for even items like induction stove pans.
According to theory, one ton of recovered plastic can prevent the consumption of seven cubic yards of waste disposal space. Overfilling landfills could be disastrous because there isn’t enough space for all the rubbish. Recycling plastic benefits the environment and keeps it from entering landfills.
Inquire About Our Silicone and Plastic Products!
Conclusion
The advantages of synthetic materials in the form of plastic for use in electronic components have been revealed to you. The implementation of proper protective measures ensures that you effectively minimize electrical hazards, thereby avoiding electrical shocks and potentially hazardous fires. Furthermore, you’ll be doing your part in ensuring environmental protection.
Contact Hongju for Plastic Materials
Enhance the life of your electrical components and electronic devices and ensure maximum safety by installing top-notch covering, whether plastic or rubber. At Hongju Silicone, we recognize the importance of high-quality rubber for electrical components and show it through our superior quality.