Plastics are essential in modern medicine, shaping the design and function of medical devices. This guide looks at how medical-grade plastics have evolved and improved healthcare by boosting safety, efficiency, and innovation.
It traces their use from early materials like nylon and Bakelite to the rise of PVC, known for its flexibility and chemical resistance. Today, plastics support the creation of safer and more affordable tools.
The guide also covers common plastic types, key properties, selection tips, sterilization methods, and their role in improving patient care.
Medical Device Plastics Overview
Nylon and Bakelite, two innovative plastics that first appeared in medical devices in the early 20th century, serve as the story’s starting point. Due to their cost and durability, these materials served as the cornerstone of the plastic revolution in the healthcare industry.
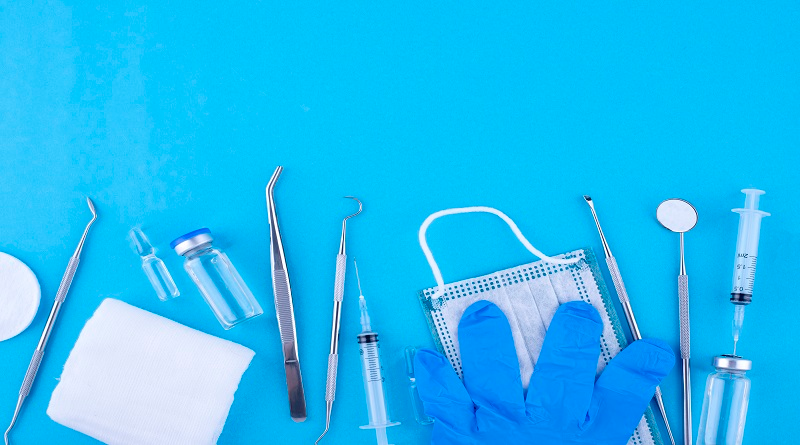
PVC (polyvinyl chloride), has revolutionized the production of medical devices. It was the perfect material for a variety of medical applications due to its flexibility, transparency, and chemical resistance.
Innovation has been at the forefront of enhancing patient care and results in the quickly developing field of medical technology. The usage of plastics for medical devices is a major component of this breakthrough.
These adaptable materials have revolutionized the healthcare sector by making it possible to develop medical devices that are safer, more effective, and more affordable.
We will delve into the realm of medical device plastics in this complete guide, looking at their characteristics, uses, advantages, and potential future developments.
Realizing Its Importance
The importance of medical device plastics rests in their capacity to handle the particular problems that the healthcare industry presents. In contrast to conventional materials like metals, medical device plastics have many benefits.
They are lightweight, which is essential for portable, user-friendly gadgets. Furthermore, their adaptability enables the development of complex and patient-specific designs.
Types of Plastic Frequently Used in Medical Devices
The materials used in the manufacture of medical devices have advanced dramatically throughout time. Due to their adaptability, affordability, and compatibility with sterilization procedures, plastics have become more popular. Let’s examine the most typical plastics found in medical equipment:
- PE (Polyethylene): A common plastic noted for its flexibility and chemical resistance is polyethylene. Due to its biocompatibility and simplicity in molding, it is frequently used in medical device components such as tubing, containers, and packaging.
- PP (Polypropylene): Another common material for medical uses is polypropylene. It has a high level of chemical resistance and is frequently utilized in syringes, lab apparatus, and medical implants.
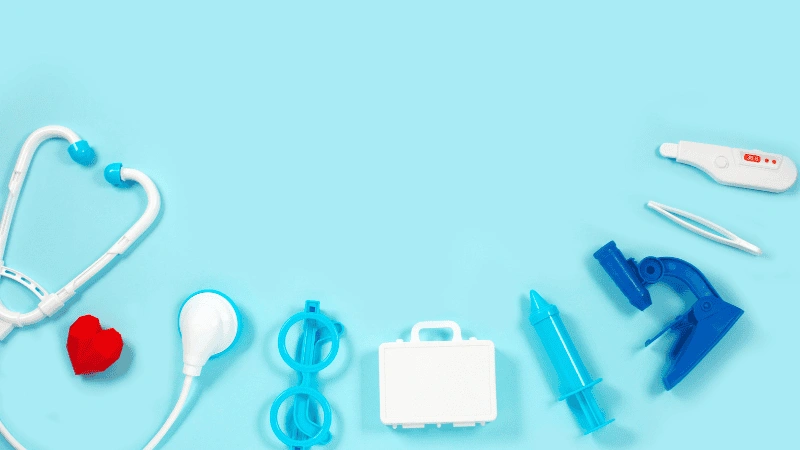
- PVC (Polyvinyl chloride): PVC is coveted for its flexibility and transparency. It is utilized in medical gloves, blood bags, and intravenous (IV) tubing. However, worries about plasticizers have prompted the creation of substitutes in several applications.
- PC (Polycarbonate): The strength and clarity of polycarbonate are legendary. It is utilized in medical devices like incubators and surgical instruments that need clarity and great impact resistance.
- PET (Polyethylene terephthalate): PET is frequently used in medical device packaging because of its durability, transparency, and contamination-resistance qualities.
- ABS (Acrylonitrile Butadiene Styrene): ABS is prized for its sturdiness and longevity. It has uses in housings for medical devices, where durability is crucial.
- PMMA (Polymethyl methacrylate): Clear, shatter-resistant plastic known as polymethyl methacrylate (PMMA) is employed in optical applications within medical devices, such as eyeglass lenses and shields. Breast implants, catheters, and breathing masks are among the many medical devices that use silicone, a biocompatible material.
Take the First Step:
Requst for an Inquire
Quality Meets Affordability. Inquire Now for High-Quality Products at Low Volumes.
Medical Device Selection Criteria for Plastic
The selection of materials is crucial in the realm of medical devices. Choosing the proper type of plastic is one of the most important choices made during the design and production of medical equipment.
Rapid innovation in the medical device sector is aimed at bettering patient outcomes and care. Due to its adaptability, plastic is a common material. However, not all polymers can be used in medical settings.
Biocompatibility
Choosing plastics for medical equipment requires careful consideration of their biocompatibility. The substance must not cause the human body to react negatively when it comes into contact with it.
The ISO 10993 standards offer recommendations for evaluating biocompatibility. Toxic-free plastic that doesn’t cause tissue or inflammation must be produced by manufacturers.
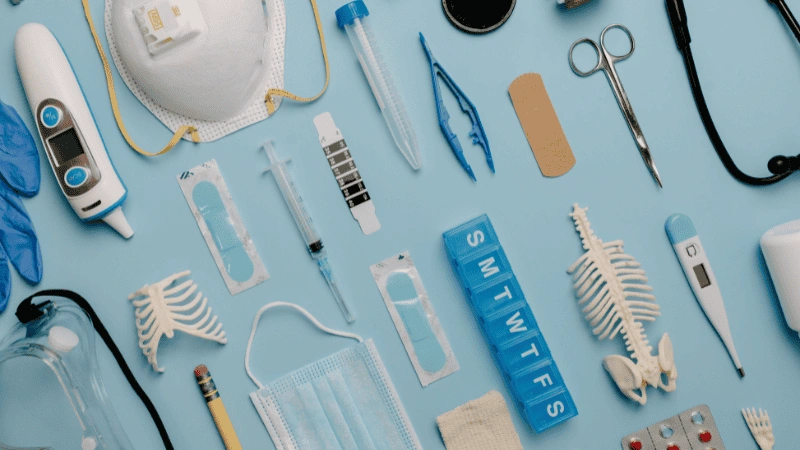
Chemical Defense
Drugs and other substances, such as disinfectants, are frequently exposed to medical devices. To maintain its structural integrity and performance when exposed to these contaminants, the chosen plastic must have chemical resistance. The ability to be cleaned and sterilized using various techniques is essential.
Technical Features
For medical devices to survive a long time, the mechanical strength and durability of the plastic are essential. Plastics must be capable of withstanding mechanical forces like bending and twisting without losing their performance.
The device’s intended usage must be compatible with the mechanical characteristics, such as elasticity and tensile strength.
Regulatory Conformity
In the medical device industry, compliance with regulations is a must. Manufacturers are required to confirm that the chosen plastic complies with laws like FDA, CE, or ISO requirements. Regulatory compliance ensures the device’s security and efficiency.
Medical Device Applications for Plastic Materials
Plastic materials have become essential parts of many medical devices in the quickly developing field of medical technology. These adaptable materials are perfect for a variety of medical applications because of their durability, flexibility, and affordability, among other advantages.
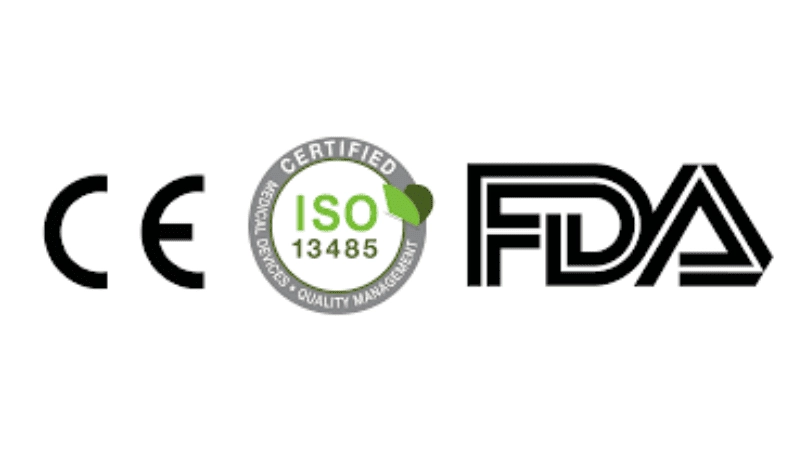
Plastic In Surgical Instruments
Plastic materials are frequently used in surgical tool handles and casings. These substances were picked for their sturdiness, cleaning simplicity, and corrosion resistance.
Sterilization and packaging
Medical equipment and supplies are packaged using plastic on a regular basis. Throughout storage and transportation, they preserve sterility and avoid contamination.
Sterilization Techniques That Work With Various Plastics
A crucial step in making sure medical gadgets are safe is sterilization. In order to preserve their integrity, various polymers need to be sterilized using particular techniques.
Steam Sterilization
Plastics with high-temperature steam sterilization resistance include polypropylene and polyethylene.
The important and frequently used method of steam sterilization, also known as autoclaving, ensures the total removal of hazardous microorganisms, such as bacteria, viruses, and spores, from a variety of objects and surfaces.
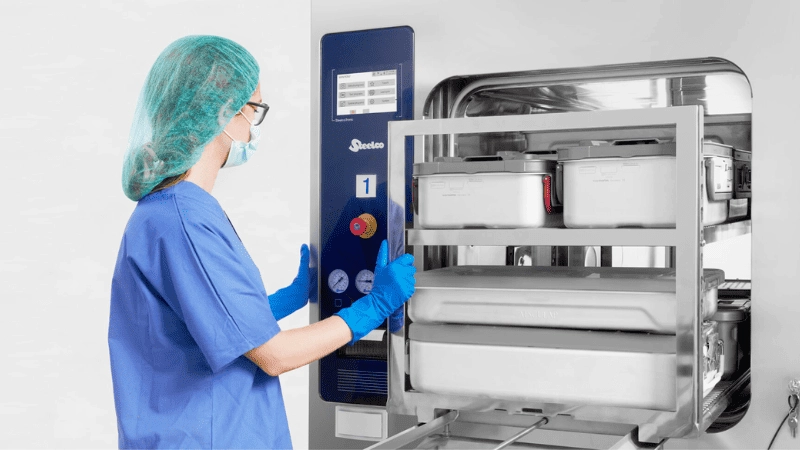
In order to attain temperatures much beyond the boiling point of water, often approximately 121°C (250°F) or more, depending on the individual application, this approach uses high-pressure steam.
Sterilization with Ethylene Oxide (EO)
Numerous plastics, including polycarbonate and polyurethane, can be sterilized with EO.
In order to achieve microbial inactivation in materials and goods that cannot withstand high-temperature sterilizing methods, ethylene oxide sterilization is an essential technique.
It is a useful instrument for assuring the safety and sterility of a variety of products and materials due to its capacity to operate at lower temperatures and penetrate complicated objects.
However, because of how dangerous it is, using it calls for cautious handling, constant supervision, and adherence to legal requirements.
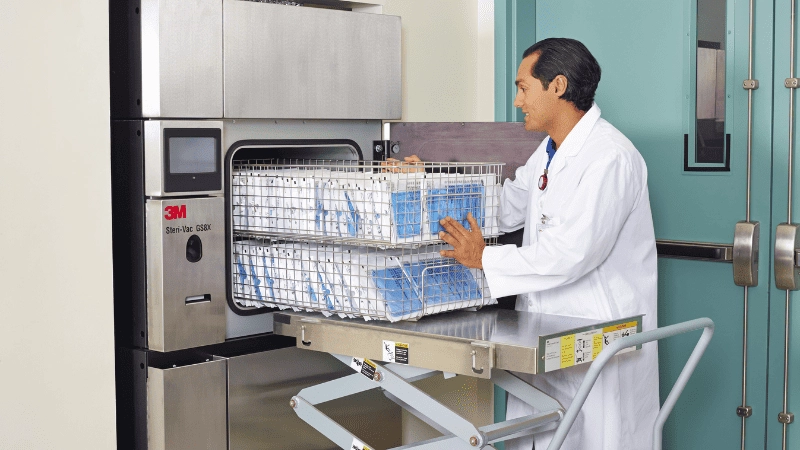
Gamma Radiation
Gamma radiation sterilization is suitable for some plastics, such as polyethylene and polypropylene. Plastics and other materials that cannot tolerate high temperatures can be sterilized using the beneficial technology of gamma radiation sterilization.
It is an essential tool in businesses where maintaining sterility is a strict necessity due to its compatibility with a broad variety of polymers and its capacity to deliver consistent sterilization and cold sterilization procedures. Its successful deployment depends on appropriate safety precautions and quality monitoring.
Hongju Silicone: Leading in Medical Innovation
Hongju Silicone, established in 1999, has become a leader in the medical device sector through its commitment to innovation, quality, and research. The company has greatly impacted global healthcare with products ranging from diagnostic tools to life-saving gadgets.
To maintain a competitive edge, Hongju Silicone heavily invests in R&D and has assembled a top-tier research team. Expanding both domestically and internationally, the company meets strict regulatory standards and emphasizes quality assurance.
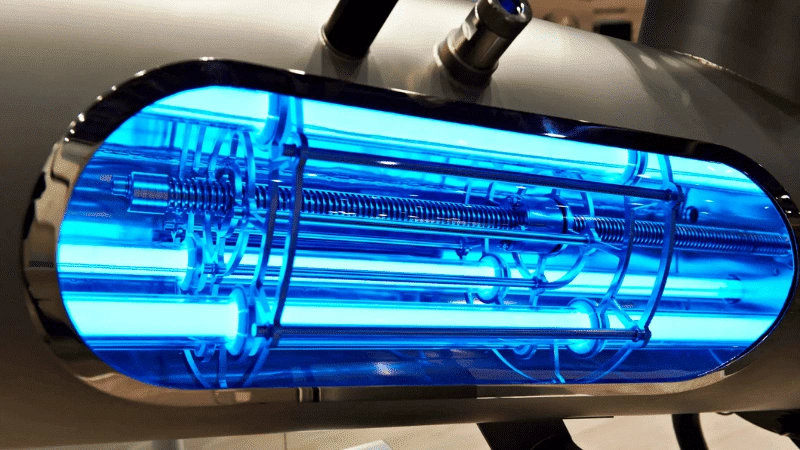
Additionally, Hongju Silicone is environmentally responsible and engages in community outreach. Looking forward, the firm remains steadfast in its mission to advance healthcare technology while adhering to its core values.
Conclusion
The evolution of plastics in medical devices has been a remarkable journey, transforming the healthcare landscape. From basic materials to sophisticated biocompatible polymers, plastics have played a pivotal role in improving patient care.
As the industry continues to innovate, the careful selection of medical-grade plastics remains vital to the creation of safe and effective medical devices.
Hongju Silicone’s Commitment to Excellence and Versatility
Hongju Silicone stands as a leading beacon in the world of silicone products, offering innovation, quality, and versatility that set us apart.
With a commitment to excellence and a dedication to meeting the unique needs of our customers, we have established ourselves as a trusted partner in various industries, from automotive to healthcare. Contact us now and get a free consultation for your business.