In this guide, we’ll explore different types of synthetic rubber, their uses, and the benefits of synthetic rubber to give you a comprehensive understanding of why it’s a preferred choice in many industries.
Definition and Characteristics of Synthetic Rubber
Synthetic rubber is an artificial elastomer that is different from natural rubber in its production process and properties. Unlike tree rubber, harvested from rubber trees, synthetic rubber comes from the polymerization of various petroleum byproducts. Since it’s a manufactured product, we can control its properties much better than natural rubber.
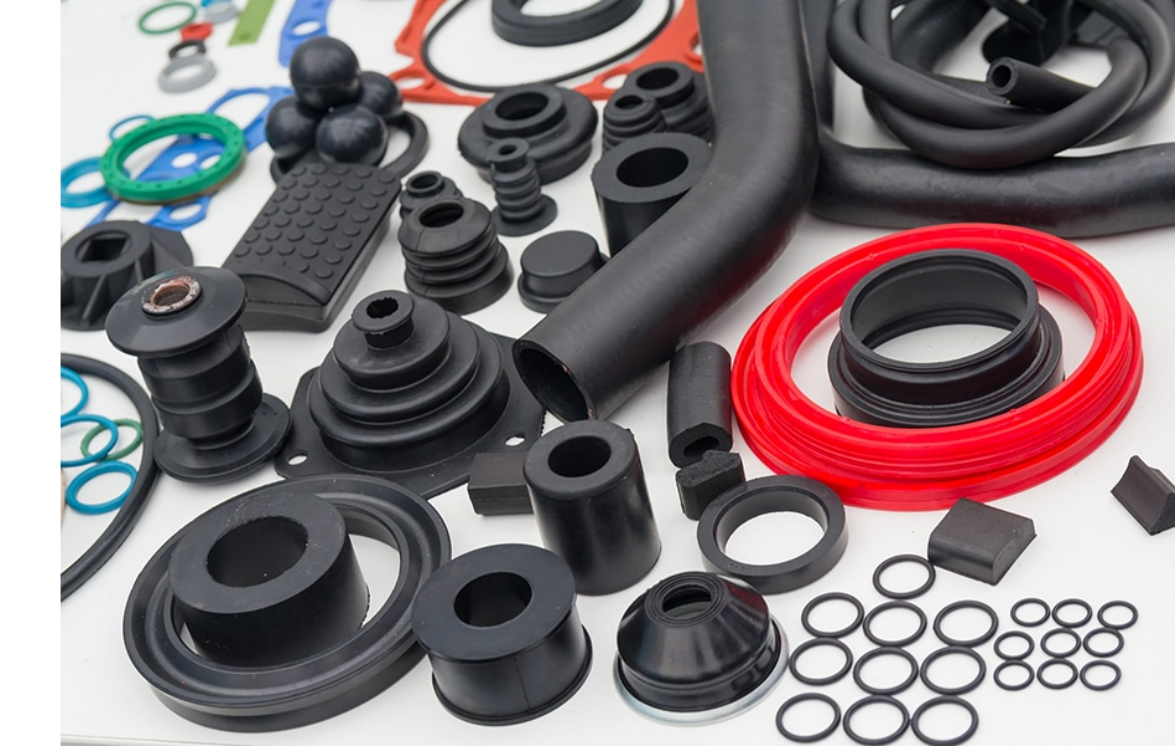
Synthetic rubber manufacturers use polymers synthesized from petroleum byproducts as base compounds. Using leftover materials makes the production process of synthetic rubber more sustainable. These polymers include certain types of butyls, styrene rubber (SBR), and nitrile butadiene rubber (NBR), also known as nitrile rubber.
By utilizing these compounds, the rubber industry can produce elastomers with enhanced characteristics such as high abrasion resistance, flame resistance, chemical and oil resistance, and superior performance at extreme temperatures.
Synthetic rubber can be used instead of regular rubber because of its improved specialized elastomeric properties. For instance, ethylene propylene diene monomer (EPDM) rubber offers outstanding resistance to weathering and ozone, while butadiene rubber is known for its high tensile strength and durability. These properties make synthetic rubber ideal for various applications, including tire inner tubes, industrial hoses, seals, gaskets, and automotive parts.
Additionally, synthetic rubbers are widely used in the construction, automotive, and medical industries to produce consumer products like shoe soles and sporting goods.
History and Development
The search for synthetic rubber dates back to the late 1880s but gained urgency during World War II. The conflict caused significant shortages of traditional rubber, which triggered the U.S. government to enlist the help of rubber companies, the petrochemicals industry, and university research laboratories to increase synthetic rubber production and industrial applications.
This collaboration led to the development of various types of synthetic rubber, such as styrene-butadiene rubber (SBR) and butyl rubber. By the war’s end, synthetic rubber had largely replaced organic rubber in many industrial applications.
Today, about 70% of rubber used in manufacturing is synthetic. This shift has been driven by synthetic rubber’s superior properties, such as high abrasion resistance, excellent chemical resistance, and performance in extreme temperatures. The widespread adoption of synthetic rubber continues to grow, meeting the demands of the automotive, aerospace, and construction industries.
Physical and Chemical Properties of Synthetic Rubber
The main reason behind their popularity is their boosted physical and chemical properties. Artificial rubbers, such as butyl rubber, neoprene, and EPDM, show various properties, such as abrasion, heat, and excellent chemical resistance.
These materials can withstand extreme conditions, including hot and cold temperatures, and are highly resistant to solvents, oxygen, oils, natural gas, and other chemicals. Synthetics like nitrile butadiene rubber (NBR) and styrene butadiene rubber are designed to endure harsh environments. Their unique properties make them ideal for applications in the automotive industry, construction industry, and aerospace industry.
Types of Synthetic Rubbers
Butyl Rubber and Its Applications
Butyl rubber, a copolymer of isobutylene and isoprene, is an essential material due to its low gas and vapor permeability. It’s an ideal material for manufacturing tire inner tubes, speakers, roofing, and gas masks. It is also highly resistant to gas and moisture permeation, oxygenated solvents, alkalis, flexing, and abrasion.
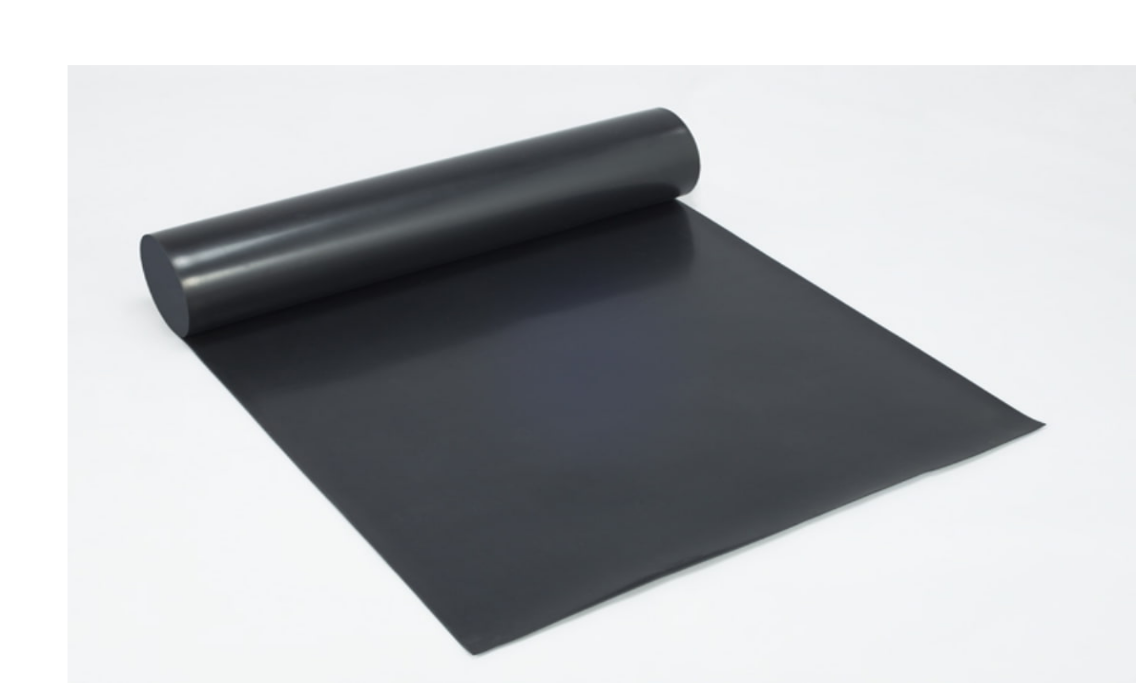
These rubbers are used as waterproofing materials, liners in tanks and ponds, patchwork for membrane roofs, and insulating materials. When combined with other chemicals, polyisobutylene creates oil and fuel additives and demisting agents for machining lubricants.
As a vibration dampener, this rubber is utilized in shock mounts, suspension bushings, and car and truck body mounts. Speaker cone edges, once commonly made of foam, are now often made from butyl rubber. The material is also used to manufacture stoppers for labware and medical equipment, and its low permeability makes it ideal for gas masks. Although not as soft and compliant as silicone rubber, butyl rubber is flexible enough to achieve a good face seal.
Butyl rubber is available in tubes, slabs, sheets, tapes, and as an adhesive/sealant. It can be molded using transfer, injection, and compression molding processes and extruded to make gaskets, hoses, O-rings, and more.
Butyl rubber is costlier than tree rubber due to more complex processing requirements. There is some debate regarding natural vs. butyl rubber motorcycle tire tubes, as tree rubber is said to have better puncture resistance and tear strength. In contrast, butyl rubber tubes can go longer between airings.
Other synthetic rubbers, such as styrene-butadiene rubber (SBR), nitrile butadiene rubber (NBR), and ethylene propylene diene monomer (EPDM) rubber, offer specialized properties for various industrial uses. For instance, SBR is known for its abrasion resistance, NBR for its oil resistance, and EPDM for its weathering and ozone resistance. These synthetic rubbers provide tailored solutions for specific needs across numerous automotive, aerospace, and construction industries.
Natural and Synthetic Rubber: Key Differences
Properties, Uses, and Benefits
Natural rubber is obtained from latex, a milky fluid found in about 2,500 species of plants. It is used in various applications, including protective gloves, balloons, roofing membranes, etc.
Key Metric | Natural Rubber | Synthetic Rubber |
---|
Industrial and Commercial Applications of Synthetic Rubber
Synthetic rubber is a versatile material used in numerous applications, including adhesives, latex gloves, aircraft tires, hose pipes, and waterproof gaskets. Its durability and resistance to extreme conditions make it ideal for various industries, such as HVAC, automotive, transportation, and appliances.
Synthetic rubber is essential for manufacturing tires, seals, and gaskets that withstand high temperatures and abrasion in the automotive industry. In the HVAC industry, it ensures airtight seals in ducts and pipes. Its wide range of properties allows synthetic rubber to meet the diverse needs of many sectors.
In the aerospace industry, nitrile butadiene rubber (NBR) and ethylene propylene diene monomer (EPDM) are highly valued for their resistance to extreme temperatures, fuels, and other chemicals. These rubbers produce fuel system seals, hydraulic hoses, and O-rings, which must endure high pressure and fluctuating temperatures without degrading.
Additionally, the flexibility and durability of synthetic rubber make it ideal for vibration-dampening components that smoothen aircraft operation.
Advantages of Synthetic Rubber Over Natural Rubber
High-Temperature Resistance
These rubbers can withstand extreme conditions, including hot and cold temperatures, and resist solvents, oxygen, oils, and other chemicals. Here are some examples:
- EPDM (Ethylene-Propylene-Diene Monomer):
- Low Temperature Usage: -20°F to -60°F (-29°C to -51°C)
- High Temperature Usage: Up to 350°F (Up to 177°C)
- Silicone:
- Low Temperature Usage: -60°F to -150°F (-50°C to -100°C)
- High Temperature Usage: Up to 480°F (Up to 250°C)
- Neoprene:
- Low Temperature Usage: 10°F to -50°F (-12°C to -46°C)
- High Temperature Usage: Up to 250°F (Up to 121°C)
- Nitrile (NBR and HNBR) Rubber:
- Low Temperature Usage: -30°F to -40°F (-34°C to -40°C)
- High Temperature Usage: Up to 250°F (121°C)
- Viton:
- Low Temperature Usage: 10°F to -10°F (-12°C to -23°C)
- High Temperature Usage: 400°F to 600°F (204°C to 315°C)
- Natural Rubber:
- Low Temperature Usage: -20°F to -60°F (-29°F to -51°C)
- High Temperature Usage: Up to 175°F (Up to 80°C)
- Butyl Rubber:
- Low Temperature Usage: -75°F (-50°C)
- High Temperature Usage: Up to 250°F (120°C)
Manufacturing Process and Sustainability
Environmental Impact and Future Developments
Rubber manufacturers are committed to reducing the use of non-renewable resources in their production process. They focus more on using toxic byproducts that may pollute the environment. The synthetic industry is focused on increasing sustainability and reducing environmental impact.
The production of synthetic rubber from petroleum byproducts still has environmental implications, but advancements aim to reduce its footprint. Future developments focus on sustainable production methods, recycling, and bio-based alternatives.
Conclusion and Future Outlook
Synthetic rubber continues to revolutionize industries with its remarkable versatility and resilience. By 2029, this substance will have a market value of 41.15 billion, and it’s currently growing at a CAGR of 4.21% (Source) At the same time, the global automotive industry will reach 619.6 billion U.S. dollars by 2033, and the aerospace industry will reach 583.3 billion U.S. dollars.
So, synthetic rubber has the potential to meet increasingly complex demands across the ever-growing automotive, aerospace, construction, and medical sectors. Innovations in sustainable production methods and quality recycling initiatives promise a greener future for this material.