The rubber sector is a key sector for businesses. The industry provides essential products for the automotive, healthcare, and industrial sectors. Natural rubber and synthetic rubber offer inherent benefits of durability, elasticity, and usage. Knowing the detailed manufacturing process will elevate your business game in the market. So let’s read.
What is Rubber Processing?
Rubber processing converts raw rubber into a finished good. Rubber processing involves both physical and chemical processes.
The procedure includes simple processes, some of which include mixing, Compression molding, vulcanisation, and finishing. Yet all of these processes must be highly accurate with strict quality control.
Strict quality control leads to functional, safe, and consistent rubber products.
The Rubber Making Process
Rubber production employs natural and synthetic rubber as input. This results in long-lasting, quality output. Such products have many applications. We need to understand the process for smart buying, production, and quality control.
Natural Rubber Production
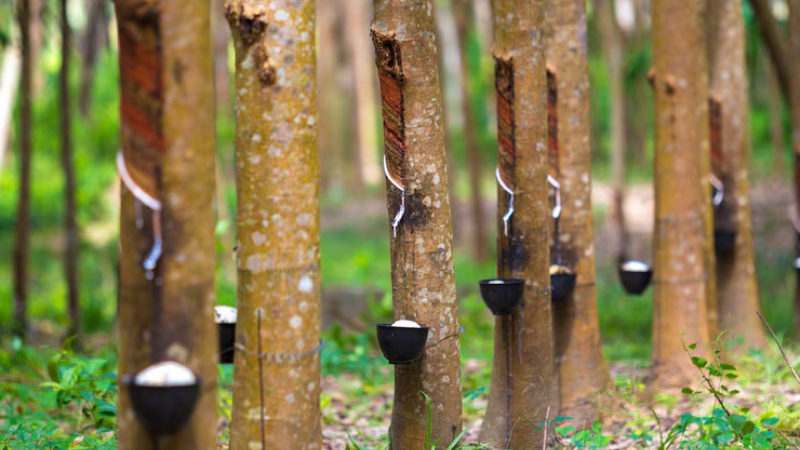
Natural rubber latex is a product of Hevea brasiliensis latex, the primary source of the rubber. It starts by tapping trees’ latex sap to collect latex rubber for filtration, packaging, and export.
Treated with acid for pre-vulcanisation, coagulation, and vulcanisation, it becomes elastic and hard-wearing. Then this vulcanised rubber is moulded into Sheets, moulded articles, and slabs are the end-products that have diversified end-use.
Synthetic Rubber Production
Synthetic rubber comes from petrochemical materials like natural gas and naphtha. Styrene monomer and butadiene polymerisation is the method applied.
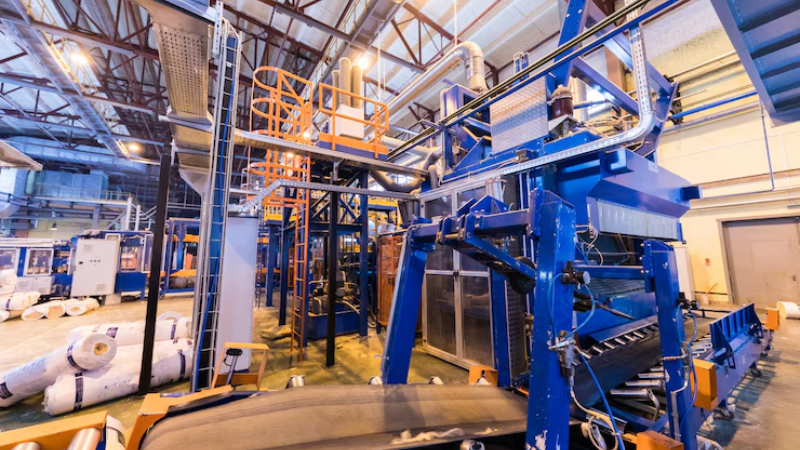
Synthetic rubber is also vulcanised like natural rubber for enhanced properties. Synthetic types, unlike natural rubber, are produced with a certain performance. They are homogenous and chemically resistant. They are suitable for industrial applications.
Difference Between Natural and Synthetic Rubber Making Processes
Below is a comparison table of natural rubber and synthetic rubber. So, you are better equipped beforehand when choosing the best one for you:
Feature | Natural Rubber | Synthetic Rubber |
---|---|---|
Source | Rubber tree natural latex | Petrochemicals |
Main Input | Latex, acid | Monomers, catalysts |
Start Process | Tapping, filtering | Polymerization |
Coagulation | Yes | No |
Vulcanization | Yes | Yes |
Eco Impact | Renewable | Non-renewable |
Consistency | Varies | High |
Machinery Used in Rubber Production
Rubber production relies on sophisticated machinery to facilitate precision, efficiency, and scale. The most rudimentary machines are rubber mixers and hydraulic presses. They need to process raw materials and create end products.
Rubber Mixers
Mixers utilised in raw material blending range between 5L and 110L. They include fillers, polymers, and additives. Batch mixers are most sought in high-volume industrial processes for effective mixing.
High-performance mixers improve efficiency and ensure uniformity. They are essential in providing uniform rubber parts.
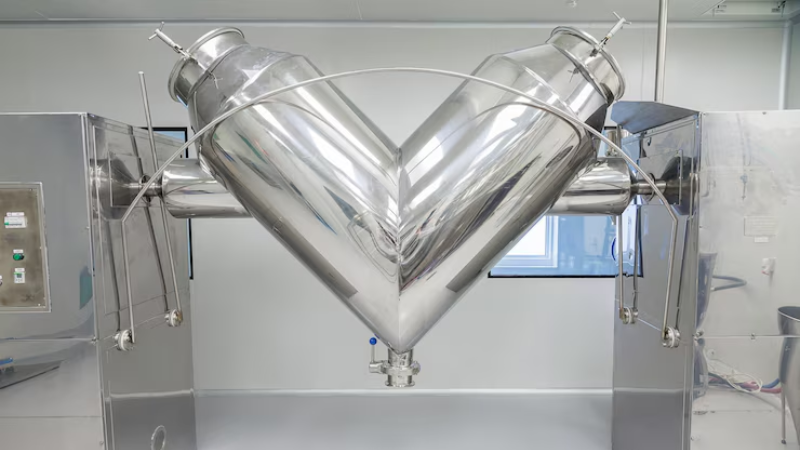
Hydraulic Presses
Hydraulic presses make use of the employment of rubber pieces to regulate pressure. Hydraulic presses shape rubber pieces into sheets. They offer precision and accuracy, especially during mass production.
Businesses prefer hydraulic presses to manufacture high-quality rubber pieces. Hydraulic presses are applied in the automotive, medical, and industrial industries.
5 Key Factors Affecting Rubber Production
Some key factors greatly influence quality and performance in rubber production. Organisations find these drivers so that products perform well and the process works effectively:
1. Raw Material Quality
Raw material quality ensures ruggedness, strength, and resistance of the final rubber product.
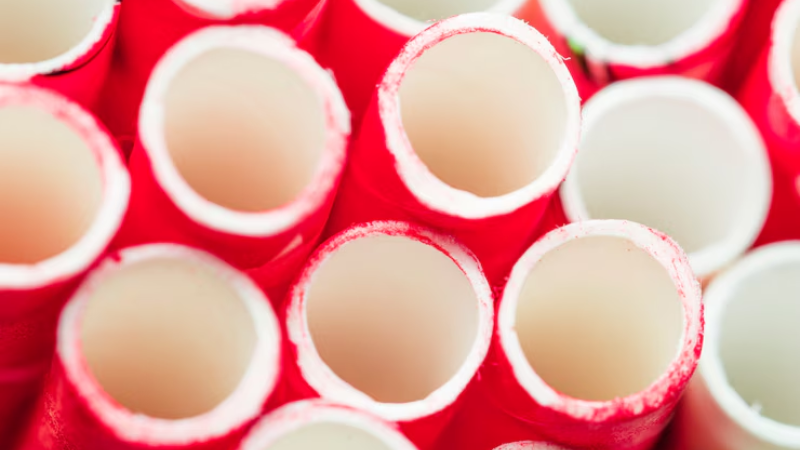
2. Technological Advances
Advanced process technology enhances accuracy, faster processing, and energy efficiency. It also contributes to consistency and minimises production cost.
3. Environmental Sustainability
Governments and institutions nowadays try to save energy, recycle, and reduce waste.
4. Skilled Workforce
Trained personnel can handle equipment, control processes, and remove defects during production.
5. Quality Control Systems
A proper test and inspection routine is required. They offer product uniformity, standardize the industry, and eliminate defects.
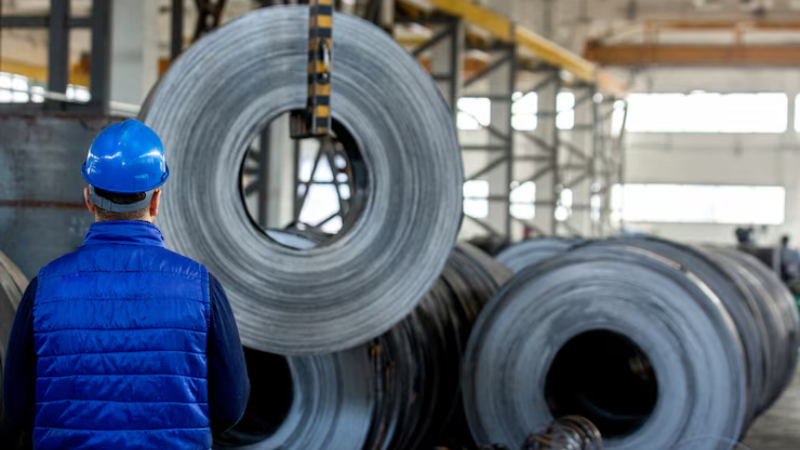
General Applications of Rubber Products
Internal duality of rubber material makes it a great benefit to numerous industries. Its unique attributes are elasticity, tensile strength, and wear resistance. These attributes find numerous useful applications:
Industrial Application: Rubber has a wide range of industrial silicone applications like is as tires, seals, gaskets, hoses, and parts that reduce vibration. This helps cars run smoothly.
Rubber is used in many places, like:
- belts
- machine pads
- pipe seals
- rubber rings
- guards
Everyday Use: Rubber is found in shoes, sports gear like balls and grips, floor mats, and home devices.
Medical Use: Moulded Rubber parts are used in gloves, tubes, syringes, seals, and soft machine parts that need to stay clean.
Electronics and Electricals: Liquid silicone rubber is utilised in insulating, cable coverings, and static shielding mats.
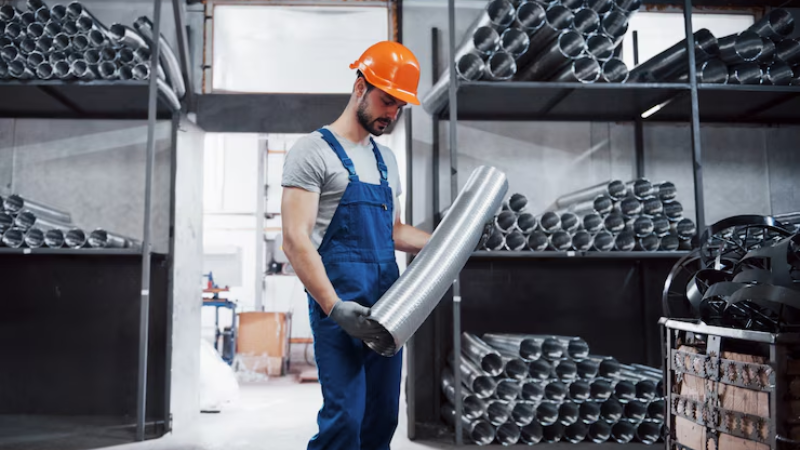
Learning how rubber is made allows companies to find the best materials and specs for their needs. It enhances product quality as well as ease in complying with the law.
Choosing the Best Rubber Processing Equipment
When choosing rubber equipment like presses and mixers, keep a few factors in mind.
- First, is it going to be a large volume of production?
- Second, what type of materials will be worked with?
- Third, how much power will the equipment need?
The choice of equipment has to be able to meet the technology and manufacturing needs of the company. The right machinery enhances product quality, minimises waste, and optimises overall manufacturing efficiency.
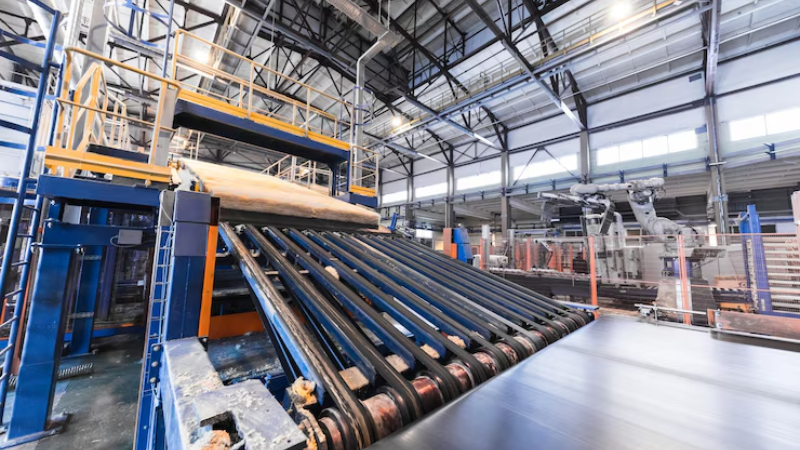
Conclusion
It is very important to know the rubber manufacturing process for your business. It results in quality, efficiency, and competitiveness.
The firms must invest in technological upgrades and the intensity of quality tests. It will drive rubber production to its limits as well as aid in adapting to changing market demands.
Partner With a Dependable Rubber Manufacturing Specialist
Hongju Silicone is experienced for more than 15 years. We provide high-quality rubber and silicone products tailored for your business. Our new machines and well-trained staff guarantee quality and precision in every step.
From the selection of machines to the manufacturing of silicone rubber products, we strictly control every step and wholeheartedly meet the product and business needs of our customers. Check out our solutions or call us now to order a quote or free consultation today. We’ll custom-fit your idea for your product!