Do you want to know more about this versatile synthetic material? If yes, then continue reading. Today, you will get a complete picture of polypropylene fiber’s role in the modern construction industry
This guide explains PP fibers, their complete history and evolution of PPF, their manufacturing process, applications, and advantages. After reading this post, you can choose the suitable polypropylene fiber for your next construction project.
It’s time to explore the multifaceted role of polypropylene fiber in contemporary concrete construction. Learn how these synthetic fibers contribute to structural integrity and longevity. Let’s get started.
What is Polypropylene Fiber?
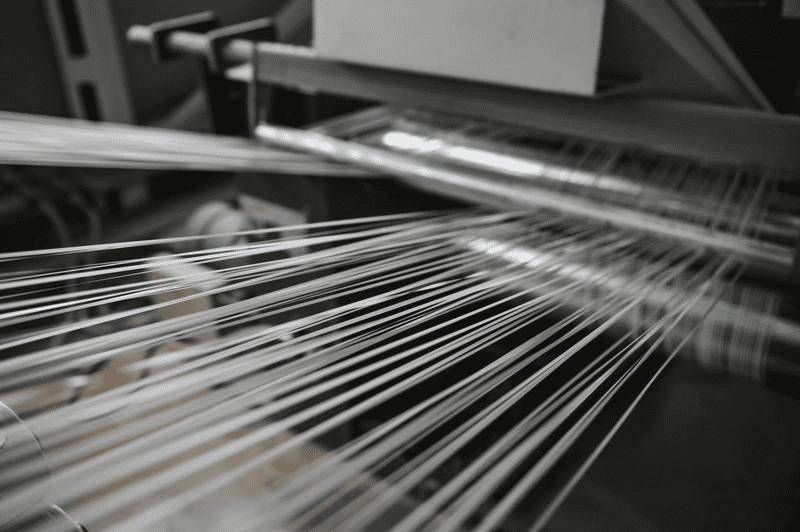
It is a synthetic fiber whose specific mechanical properties make it the most suitable material in the construction industry, especially concerning the concrete surface. This versatile synthetic fiber is made from the thermoplastic polymer polypropylene.
Here are some mechanical characteristics of polypropylene fibers that make them ideal materials to blend with concrete.
- Crack Resistance: The biggest issue with concrete is crack formation, especially in the early stages of construction. This issue can be resolved quickly with PPF. This material enhances the crack resistance of a structure. Preventing small cracks ensures that the structure won’t lead to significant issues over time.
- Durability: Another property that makes polypropylene Fiber an ideal material to use in construction is chemical resistance. Regardless of the harsh environmental factors, these fibers resist freeze-thaw cycles and chemical exposure. As a result, the concrete structure life cycle enjoys a significant boost.
- Impact Resistance: Conventional concrete can’t withstand impacts and mechanical loads in high-traffic areas. So, adding polypropylene fibers in plain concrete is always a good idea when an area has heavy loads. As a result, this mixture can withstand mechanical loads.
- Reduce Shrinkage Cracks: When concrete dries and cures, it usually causes shrinkage cracks. So, mixing Polypropylene with concrete is always a good idea because it maintains structural integrity and aesthetics.
- Corrosion Resistance: The non-corrosive nature of Polypropylene fiber makes it a suitable material for concrete reinforcement. If you don’t want to compromise structural integrity, there is a need to add this material with concrete. It’s how you can get a structure that won’t corrode over time.
- Reduced Permeability: Hydraulic engineers advise a mixture of concrete plus Polypropylene fiber, which reduces the porous structure of concrete. This reduction in permeability ensures that the structure won’t experience damage due to water infiltration. This combination is necessary in the marine environment or when construction involves Dams.
- Fire Resistance: Another plus point of Polypropylene fibers is that they are inherently fire-resistant. When you have to construct a building while complying with fire safety standards, it becomes vital to add PPF into concrete.
Send your inquiry for prompt quotations!
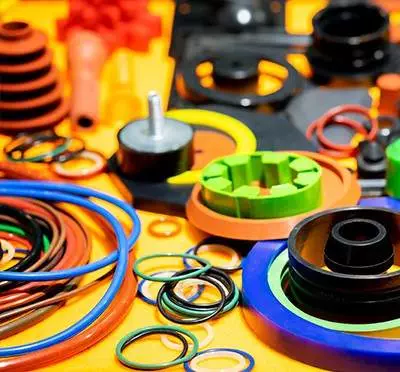
Historical Context of Polypropylene Fibre
It’s time to dig into the history of fiber to understand the modern and historical context of PPF. So, let’s get into that.
Traditional fiber reinforcement in the concrete mixture
According to Wikipedia, If you check the history, you will find out that fibers have been used to reinforce concretes from ancient times. A quick look at history records depicts that contractors used to incorporate different materials for construction such as animal hair, and straws.
Even asbestos fibers were used to boost the durability and strength of a structure in the 1900s. However, health risks associated with asbestos pushed experts to look for alternative fibers that can boost the compressive strength of concrete without putting anyone at health risk.
Emergence of Synthetic Fibers
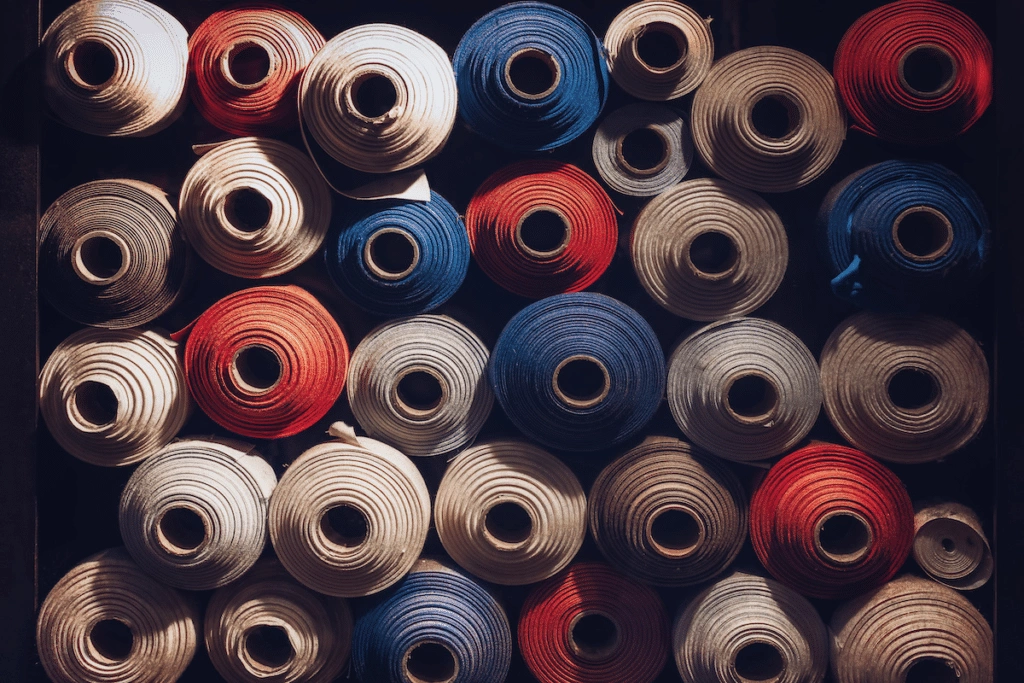
Scientific studies on different fibers brought polypropylene fiber into the game of construction in the 1960s. It was when steel fibers were commonly used for their high tensile strength and other fantastic engineering properties.
In the mid-20th Century, synthetic fiber revolutionized the construction industry to a great extent. Polypropylene wasn’t the only type of fiber used in construction. Other standard fibers put into great use were nylon and polyethylene.
Although multiple synthetic fibers emerged in history, polypropylene fiber became more popular than others due to its favorable mechanical properties such as corrosion resistance, impact resistance, high tensile strength, and durability.
Evolution of Polypropylene Fiber Usage
- From the 1960s to 1970, commercial polypropylene fibers were designed to reinforce concrete. The primary purpose of these fibers was to decrease plastic shrinkage in concrete.
- By the 1990s, Polypropylene had gained popularity in different structural applications. They were mainly used to improve impact resistance and performance of concrete slabs in industrial pavements and floors.
- From the 2000s to the Present, many scientific studies have been conducted on this versatile fiber. These days, you can get different types of polypropylene fibre reinforced concrete, which you can customize as per your construction project requirements. Steel reinforcement is also commonly used for high-strength concrete.
Send your inquiry for prompt quotations!
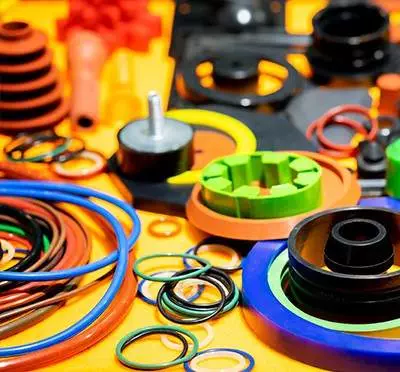
Manufacturing Process of Polypropylene Fibre
It’s time to explore the step-by-step manufacturing process of Polypropylene Fibre.
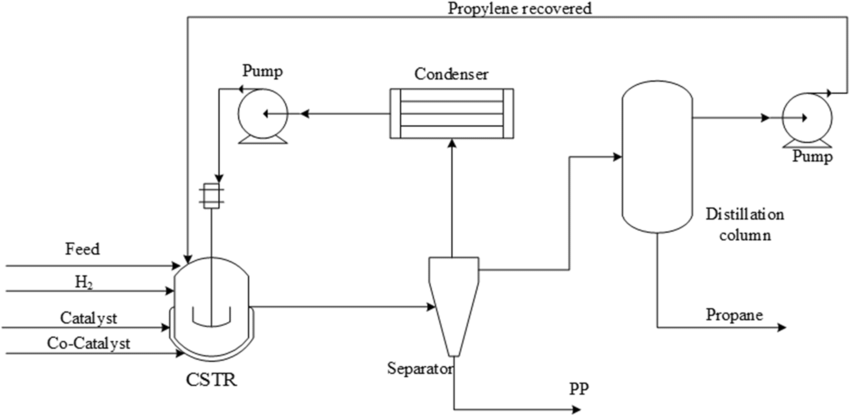
- Polymerization: It all begins with the polymerization of propylene monomers. This process is done by utilizing Ziegler-Natta catalysts or metallocene catalysts. The purpose of this catalyst is to speed up the boding of polypropylene monomers to produce long chains of polypropylene molecules.
- Extrusion: Polypropylene polymers are melted and extruded using a spinneret in this step. The melted polymer is forced through the spinneret. As a result, continuous filaments are formed. Initially, these filaments are in a molten state.
- Cooling and Solidification: The cooling process begins when molten filaments pass through air cooling and get a quenching bath. The purpose of cooling is to solidify the fibers. This solidification gives the fiber a solid and stable form.
- Drawing: The solid filaments are now drawn through a series of heated godets. This drawing aims to improve the alignment of polymer chains and boost their orientations and tensile strength.
- Cutting: After drawing the filaments, the cutting process begins. Filaments are cut into either short fiber lengths or continuous filaments. Cutting of fibers ultimately depends on their applications.
- Packaging: The finished polypropylene fibers are packed into different forms and then distributed to manufacturers of various products.
Applications of Polypropylene Fibre in Modern Construction
Here are the most common uses of Polypropylene fibre reinforced concrete in the modern construction industry.
1. Concrete Reinforcement
These fibers are commonly mixed with create to reduce the formation and propagation of cracks. They effectively control plastic shrinkage cracking and reduce all the effects of temperature-related stresses.
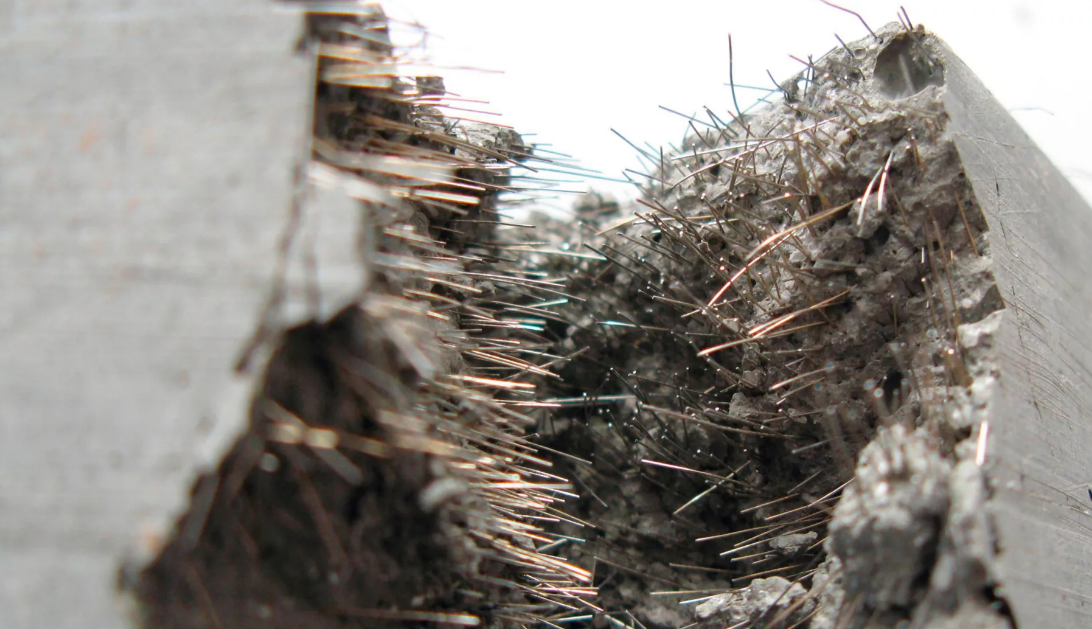
Due to their impact resistance properties, they are commonly used to produce bridge decks, pavements, and industrial floors. They reduce the risk of surface damage due to heavy traffic, load, or impact.
Polypropylene fibre-reinforced concrete is often added to Mortar and Render Systems because it boosts up tensile and flexural strength—the durability properties of wall coating increase due to polypropylene fibers.
2. Geotechnical Engineering
Polypropylene fibers are mixed with soils to improve their load-bearing capacity. They also increase soil cohesion. Besides these, steel and polypropylene fibers are used to create geotextiles and erosion control blankets, which effectively prevent soil erosion in riverbanks and slopes.
3. Tunnel and Mine Construction
These fibers are often added to concrete and shotcrete mixes during underground construction. They are robust building materials for mine support concrete structures and tunnel lining due to their exceptionally high tensile strength.
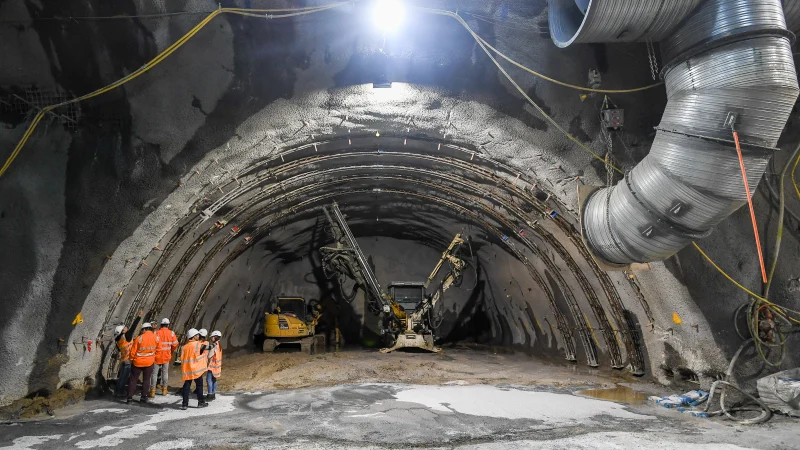
4. Concrete Pipes and Precast Products
These fibers increase the toughness of concrete pipes and precast concrete products. When fibers are added to production, it increases the resistance against the cracking of fresh concrete.
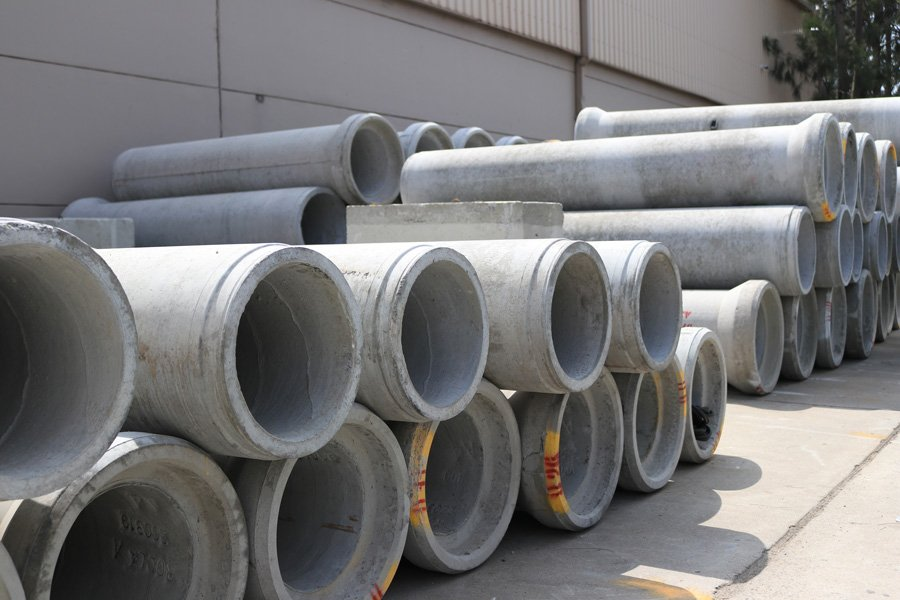
5. Bridge Decks
When contractors need to create a bridge in areas prone to the freeze-thaw cycle, it becomes essential to add polypropylene fibers as they add strength to the structure and enhance the crack and impact resistance of concrete.
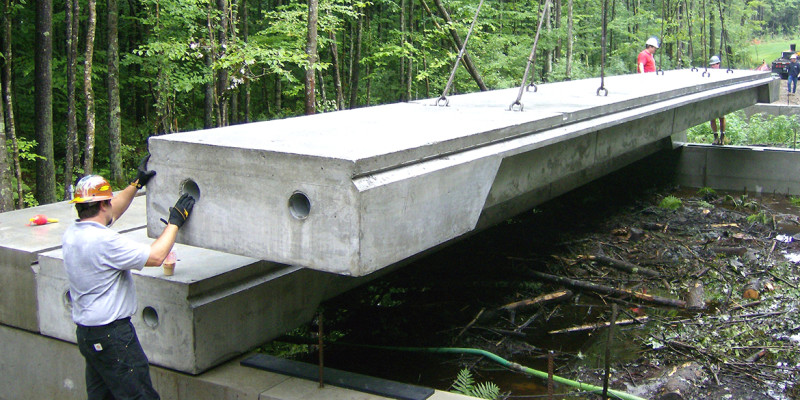
6. Residential and Commercial Construction
When constructing solid and stable floors, expert engineers always add Polypropylene fibre reinforced concrete to the building material plan. They improve the durability of a floor surface and increase its resistance against heavy traffic.
Send your inquiry for prompt quotations!
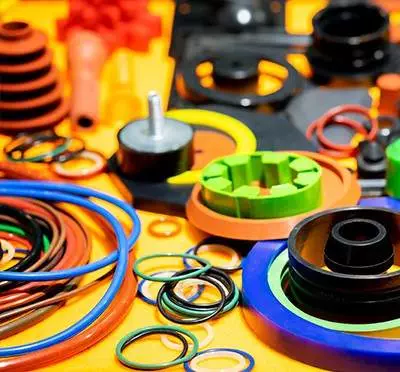
Advantages of Polypropylene Fibre Reinforced Concrete
Here are some benefits you can get by reinforcing concrete with Polypropylene
1. Reducing Spalling Risk in Concrete with Polypropylene Fibers
Whenever concrete is exposed to extreme temperatures, the water inside it turns into steam. As a result, spalling and loss of structural integrity happen. When polypropylene Fibres are mixed with concrete, these fibers melt and design a route for steam to escape. Water absorption reduces.
The fire-resistance properties of Polypropylene fibre reinforced concrete makes them an ideal reinforcement building material for constructing tunnels, bridges, and other fire-resistant concrete structures.
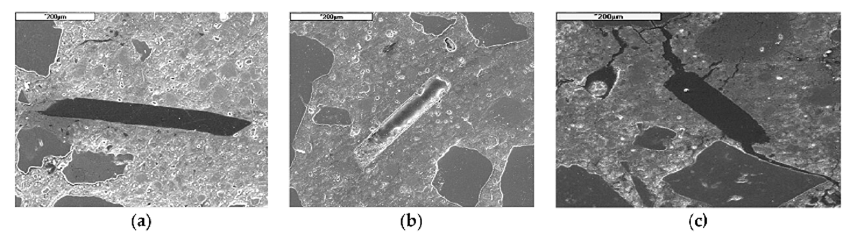
2. Utilizing Polypropylene Fiber for Sustainable Structural Reinforcement
Every contractor wants to create a sustainable structure. Thanks to polypropylene fibers, the durability of concrete is boosted. This structure requires less maintenance and repairs. Minimizing resource consumption and the long lifespan of structure contribute to overall sustainability while reducing environmental impact.
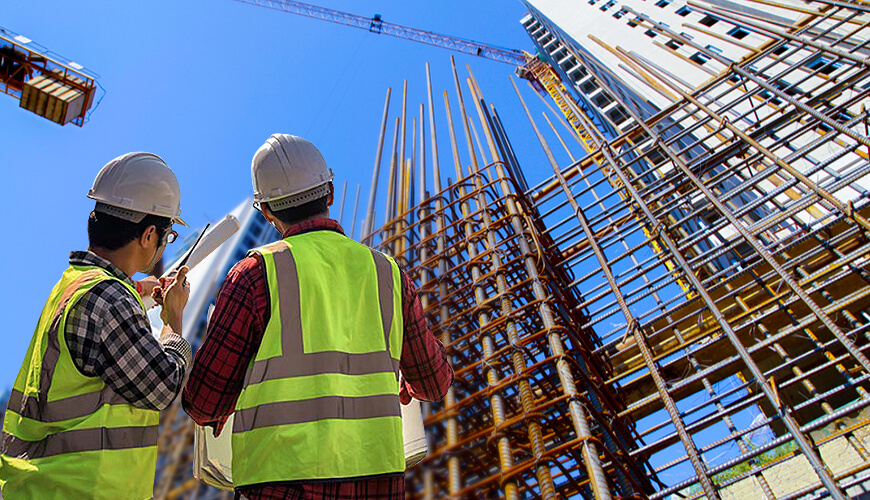
3. Enhancing Concrete Strength and Durability with Polypropylene Fibers
These fibers improve the mechanical properties of concrete, such as flexural strength, tensile strength, and impact resistance. This reinforcement leads to durable and long-lasting concrete structures. Therefore, it is an ideal mixture to create pavements and industrial floors.
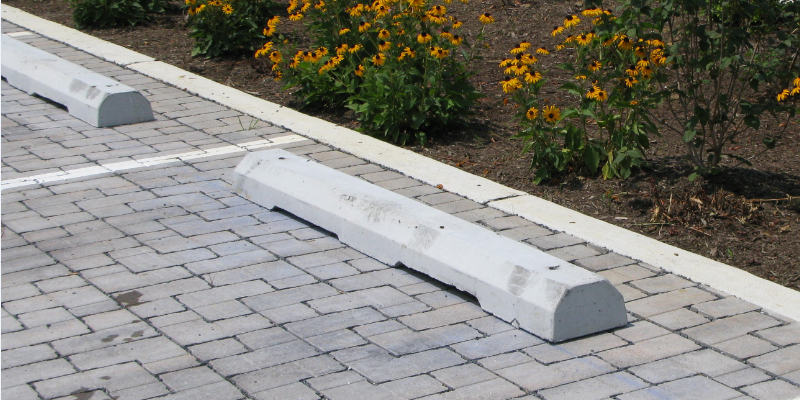
4. Controlling Shrinkage and Crack Formation in Concrete using Polypropylene Fibers
PP Fibre reinforced concrete addresses the biggest constructional challenge of concrete, aka cracks, formed during cure and over time. When contractors support concrete with Polypropylene fibers, they reduce cracking- both plastic and drying shrinkage. You can improve structural aesthetics through these fibers.
5. Improving Impact Resistance and Fire Resistance of Concrete with Polypropylene Fibers
PP Fibres can improve fire resistance and impact resistance properties of concrete. These fibers are commonly used in heavy traffic or heavy load areas due to their load-carrying capacity. Many commercial floors, military bunkers, and bridge decks are created with polypropylene fibers enforced concrete. The purpose is to reduce impact and prevent fire hazards.
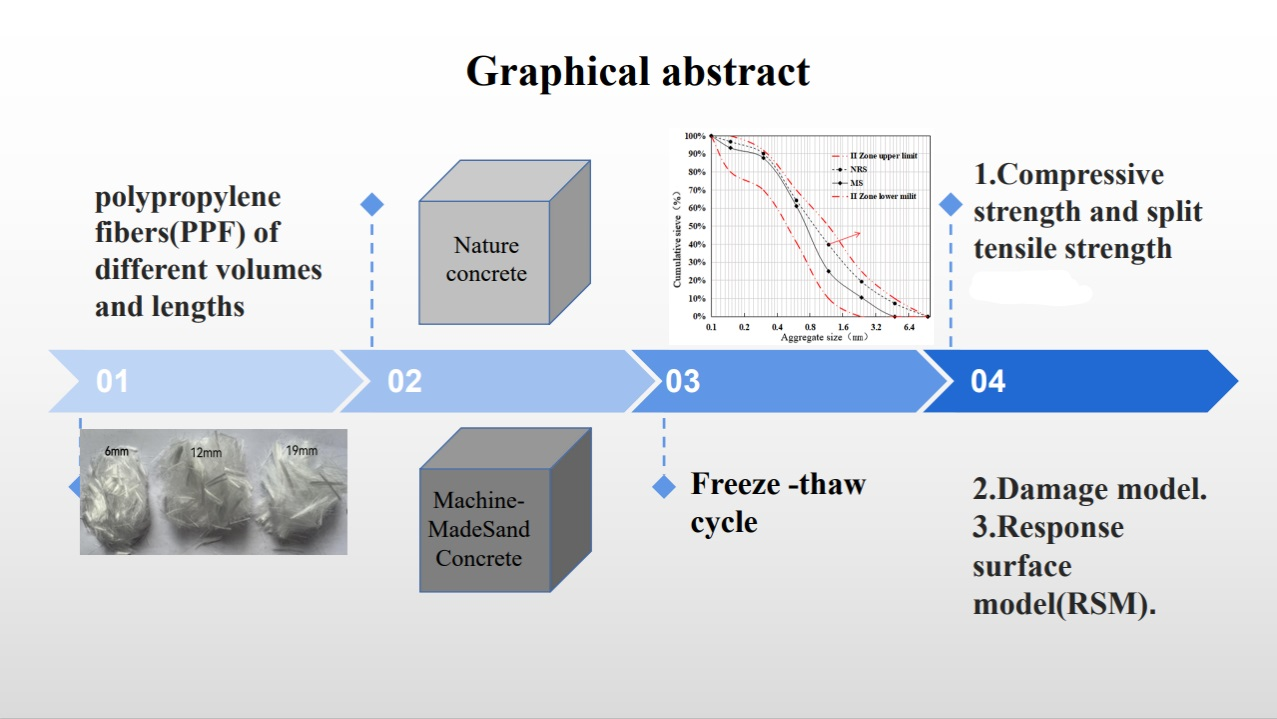
Choosing the Right PP Fibre for Your Needs
It would be best if you chose the right Polypropylene (PP) fiber by looking into various factors such as:
1. Application Requirements
What’s the primary purpose you want to achieve from PP fiber in your project? These fibers let you control cracks, improve fire resistance, and boost durability. Choose a fiber as per your specific goal.
2. Fiber Type
You can find different types of Polypropylene fibers. Monofilament/Single strand is ideal for a construction project where you want to control shrinkage cracking. This filament offers better dispersion in the mix. Conversely, using multifilament to improve structural reinforcement and impact resistance would be best.
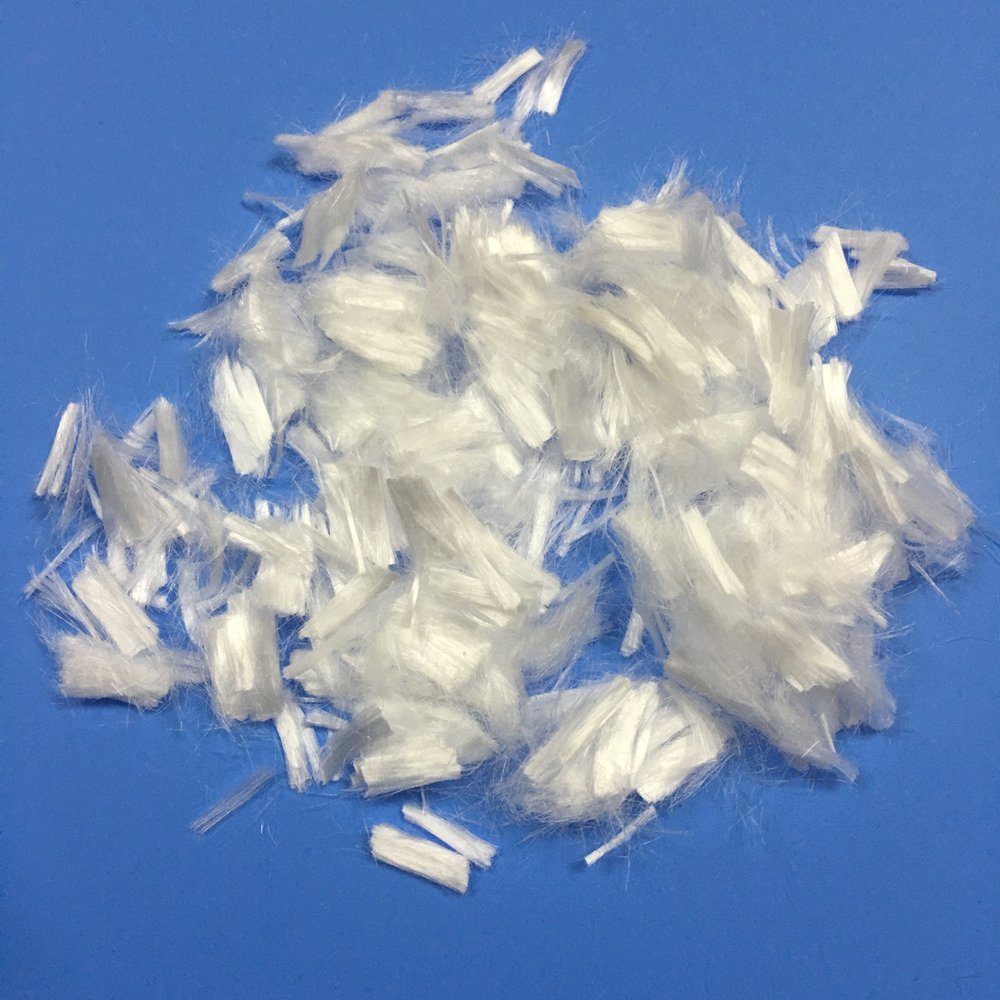
3. Fiber Geometry and Length
Another thing to consider when choosing the suitable fiber for the construction is the Fibre length. Short fibers are effective in controlling plastic shrinkage cracking. But when a project requires you to boost structural reinforcements, then long fibers are suitable.
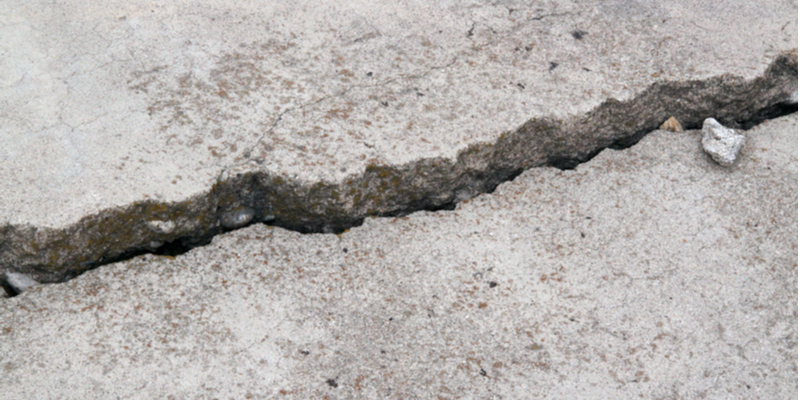
4. Dosage Rate
You can find polypropylene fibers in different dosage ranges, ranging from 0.1% to 2% by concrete mix volume. You will pick a specific dosage rate as per your project requirements.
5. Compliance with Standards
ASTM International has set specific standards for fibers used for the strength of plain concrete. So, when you are going to use these fibers in a particular project, make sure they meet relevant industry standards and guidelines.
6. Compatibility
You need to mix many additives, aggregates, lightweight aggregate concrete, and other materials during construction. Before picking a specific fiber, double-check its compatibility with other materials. It’s because any compatibility issue will affect the overall performance of concrete.
7. Consultation
When unsure about the type of PP Fibres, it’s good to seek advice from experts such as structural engineers or concrete contractors.
Send your inquiry for prompt quotations!
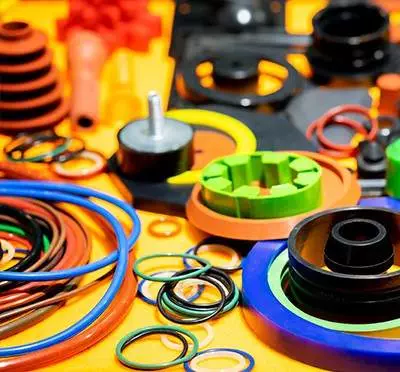
Conclusion
Finally, you know the remarkable role of Polypropylene fiber in modern concrete construction. From enhancing concrete’s durability to boosting its strength and sustainability, these fibers play a pivotal role. These meticulously engineered fibers can provide a solution to the challenges of conventional plain concrete structures.
From decreasing spalling risk in high-temperature scenarios to boosting structural enforcement, these fibers find application in residential and infrastructural projects. Best of all, Polypropylene fibre reinforced concrete helps you achieve sustainability goals quickly.
Unlock the Full Potential of Polypropylene Fibres with Hongju!
Do you want to elevate your construction project? Or are you seeking stronger, safer, and more resilient plain concrete structures?
No matter what you want, Hongju‘s experts are here to help. We will guide you on how you can control cracks by making the right choice of PPF. Our expert advice and guidance will let you enjoy long-term sustainability for your next construction project. Contact Now!