This article aims to delve into the question: Can PEEK withstand high temperatures? We will explore its mechanical properties, heat deflection temperature, and melting point to understand how it performs in high-temperature environments.
What is PEEK?
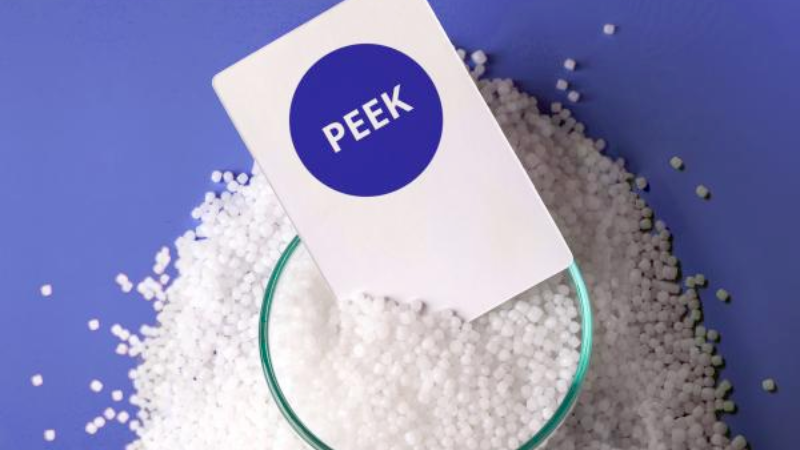
PEEK is a high-performance engineering thermoplastic known for its exceptional mechanical properties and heat resistance. Let’s delve into the composition, molecular structure, and thermal stability of PEEK.
Definition and Composition of PEEK Polymer
PEEK (polyether ether ketone) is a high-performance thermoplastic polymer that offers exceptional properties and versatility. PEEK belongs to the family of polyaryletherketones(PAEK), specifically classified as a semi-crystalline thermoplastic. It is composed of repeating units derived from aromatic monomers known as bisphenols and aromatic dihalides. The unique combination of these building blocks results in the formation of a robust polymer with outstanding characteristics.
Unique Molecular Structure of PEEK
The molecular structure of PEEK contributes significantly to its exceptional properties. Its backbone consists of alternating ether (O) and ketone (C=O) groups bonded to aromatic rings. This arrangement imparts rigidity to the polymer chain while maintaining flexibility due to the presence of oxygen atoms. The strong carbon-oxygen bonds enhance its overall durability.
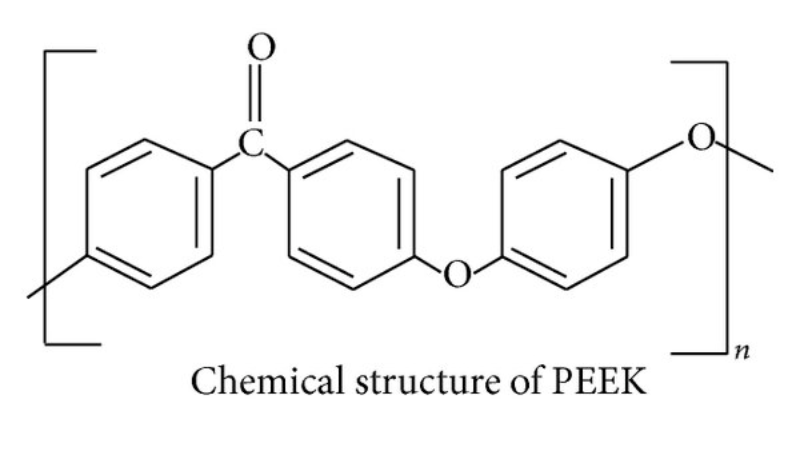
PEEK is a high-performance engineering thermoplastic that consists of a unique chemical structure, providing it with an exceptional balance of mechanical properties. Its chemical composition offers outstanding chemical resistance, making it resilient against a wide range of chemicals. The polymer chain in PEEK is both rigid and flexible, allowing for excellent heat resistance and stability.
The molecular architecture of PEEK contributes to its high melting point and heat deflection temperature, which means that it maintains its shape and mechanical strength even at high temperatures. Its specific chemical compound enables it to provide stable performance in both high-temperature environments and corrosive conditions. This makes PEEK an invaluable material in industries requiring materials that can withstand temperatures and offer long-lasting durability.
Understanding the Chemical Compound PEEK: Toxicity and Properties
PEEK is a really good plastic that is used in lots of different industries. It’s strong and can handle chemicals well. But we need to know more about its chemicals to make sure it’s safe to use.
Toxicity
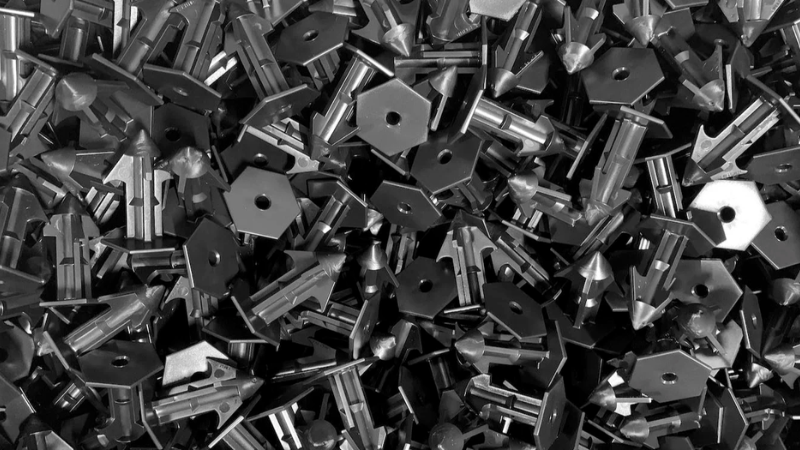
PEEK is generally considered to be a biocompatible material, meaning it has low toxicity. It is often used in medical implants and other medical industry applications where low toxicity is a critical requirement. This implies that PEEK can safely be used in environments that require strict adherence to health and safety guidelines.
Properties
- High Melting Point: One of PEEK’s most notable attributes is its high melting point, allowing it to be used in extremely high temperatures.
- Chemical Resistance: PEEK offers outstanding chemical resistance, making it highly durable against a wide variety of chemicals.
- Mechanical Strength: The thermoplastic possesses excellent mechanical properties that make it suitable for rigorous applications, including the aerospace industry and oil and gas applications.
- Wide Temperature Range: PEEK can operate in a wide temperature range, making it versatile for high-temperature applications.
- Heat Resistance: Its heat-resistant plastic nature enables it to maintain its integrity even when subjected to high temperatures.
Understanding the low toxicity and exceptional properties of PEEK allows for its broader and more effective utilization in various industrial applications, making it a preferred choice among heat-resistant plastic materials.
Comparing PEEK with PEK and PTFE
PEEK, PEK, and PTFE are three high-performance polymers that offer distinct differences in terms of thermal stability, mechanical properties, chemical resistance, and more. Each polymer has its own unique advantages that set it apart from the others.
Properties/Features | PEEK | PEK | PTFE |
---|---|---|---|
Glass Transition Temperature | High | Slightly Lower than PEEK | Lower than both PEEK and PEK |
Melting Point | Up to 343°C (649°F) | Slightly Lower than PEEK | Around 327°C (620°F) |
Chemical Resistance | Outstanding | Comparable to PEEK | Excellent |
Heat Resistance | Excellent | Very Good | Excellent |
Mechanical Properties | Strong and robust | Slightly Less Robust than PEEK | Less Mechanically Robust |
Industry Applications | Aerospace, Medical, Oil and Gas | Similar to PEEK | Broad, but less in high-temperature applications |
Heat Deflection Temperature | High | Slightly Lower than PEEK | Lower than both PEEK and PEK |
How is PEEK Used in High Temperatures Applications?
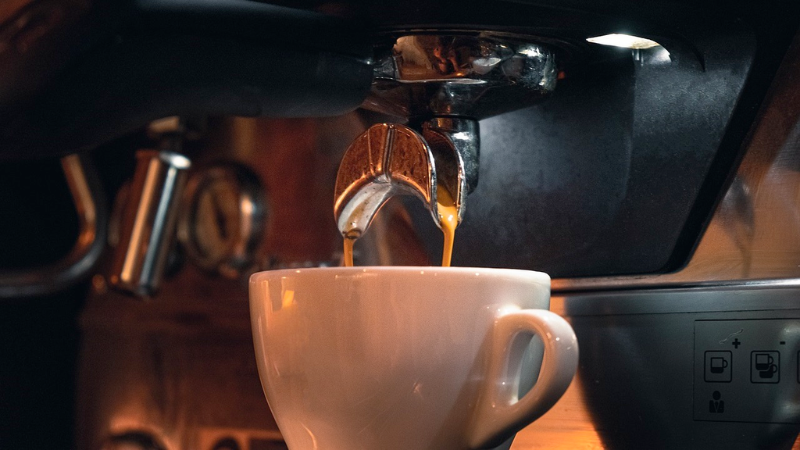
PEEK (Polyether Ether Ketone) is extensively utilized in high-temperature applications due to its exceptional thermal stability, superior mechanical properties, and outstanding chemical resistance. This makes it an ideal choice for challenging environments that would cause other materials to degrade or fail. Below are some ways PEEK is utilized in high-temperature applications:
- Aerospace Industry: PEEK is often used in aerospace components like compressor linings, wire coatings, and seals. The material’s ability to withstand temperatures up to 343°C (649°F) makes it suitable for parts that are exposed to extremely high temperatures during flight.
- Oil and Gas Applications: In the oil and gas sector, PEEK is used for making components like seals, bearings, and compressor rings that can endure aggressive chemicals and high-temperature environments. This is crucial for applications deep within the Earth’s crust where both pressure and temperature are exceedingly high.
- Medical Industry: PEEK’s biocompatibility and high-temperature resistance make it ideal for sterilizable surgical instruments and implants. Instruments made from PEEK can be sterilized at high temperatures without losing their mechanical integrity.
- Automotive Applications: PEEK is used in various automotive components, including transmission parts and bearing cages. It is preferred for its ability to endure high friction and heat resistance under intense operating conditions.
- Industrial Equipment: In industrial settings, PEEK is used in making parts for pumps, valves, and conveyor belts, which often have to function at elevated temperatures. Its mechanical properties and ability to withstand temperatures make it an excellent material for these applications.
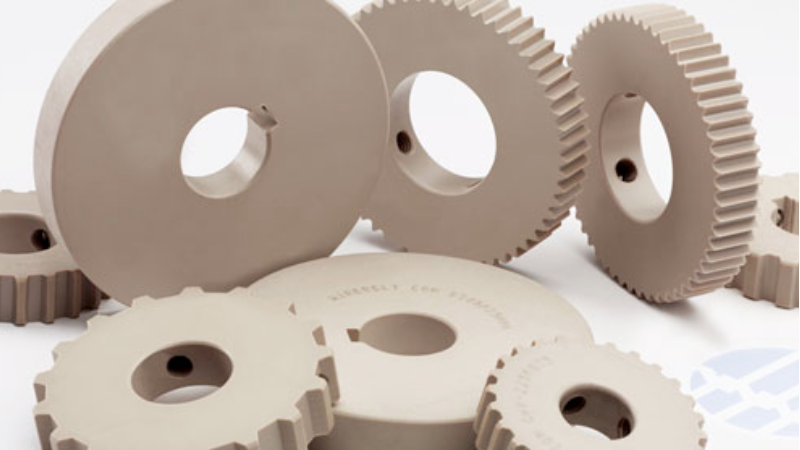
By excelling in a wide temperature range and offering heat-resistant characteristics, PEEK has secured its place as a high-performance engineering thermoplastic for various industries. Its versatility and robustness continue to make it a preferred material for applications that involve extreme conditions.
Why is PEEK the Most Widely Used High-Temperature Sealing Material
PEEK has earned its reputation as a leading high-temperature sealing material due to a combination of its unique properties that make it ideal for harsh and demanding environments. Here are the three key reasons why PEEK is the most widely used high-temperature sealing material:
Exceptional Thermal Stability
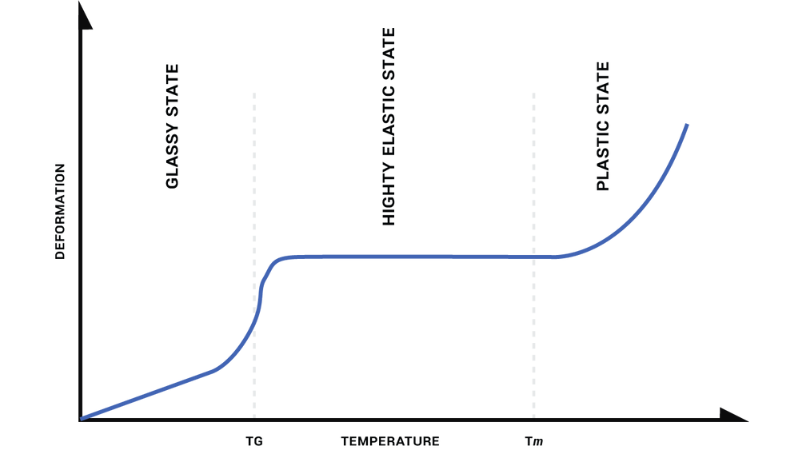
One of the standout characteristics of PEEK is its remarkable thermal stability. It has a high melting point of around 343°C (649°F) and can operate continuously at temperatures up to 250°C (482°F). This makes it perfect for high-temperature applications in various industries such as aerospace, automotive, and oil and gas. The ability to maintain its structural and mechanical properties at high temperatures is crucial for seals, which must prevent leaks and maintain pressure boundaries in thermal extremes.
Outstanding Chemical Resistance
PEEK offers outstanding chemical resistance, meaning it can withstand exposure to a wide range of corrosive substances without degradation. This makes it highly desirable in industries like chemical processing, medical, and oil and gas applications where seals come into contact with aggressive chemicals. The material’s chemical inertness further ensures that it does not react with substances it seals, thus maintaining the integrity of the system.
Excellent Mechanical Properties
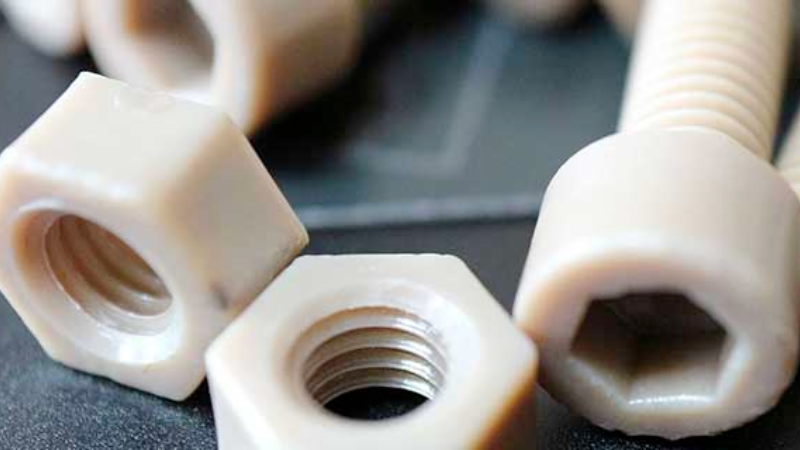
PEEK possesses impressive mechanical properties, including high tensile strength and wear resistance, making it ideal for sealing applications in high-pressure environments. Its toughness and resilience also contribute to its long lifespan, reducing the frequency of maintenance and replacements. In industries where the performance of seals is critical for safety and operational reliability, PEEK’s mechanical strength makes it the material of choice
How Does PEEK Compare to Other High-Temperature Sealing Materials?
When it comes to high-temperature sealing materials, PEEK is often compared to other contenders such as PEK (Polyether Ketone) and PTFE (Polytetrafluoroethylene). Each material has its own set of advantages and limitations, but PEEK consistently stands out for high-temperature applications. Below is a comparative table illustrating some of the critical properties of these materials:
Property | PEEK | PEK | PTFE |
---|---|---|---|
Melting Point (°C) | 343 | 372 | 327 |
Continuous Service Temp (°C) | Up to 250 | Up to 260 | Up to 260 |
Chemical Resistance | Outstanding | Excellent | Exceptional |
Mechanical Strength | High | Moderate | Low |
Wear Resistance | Excellent | Good | Moderate to Poor |
Price Point | High | Higher | Moderate |
Key Points:
- Temperature Tolerance: While PEEK and PEK both offer good heat resistance, PEEK operates well at temperatures up to 250°C, making it versatile for a range of high-temperature applications. PTFE, although it also withstands high temperatures, loses some of its mechanical properties at elevated temperatures.
- Chemical Resistance: PEEK and PTFE both have outstanding chemical resistance, making them ideal for use in chemically aggressive environments. PEK also offers good chemical resistance but is generally considered less resistant than PEEK.
- Mechanical Properties: PEEK has better mechanical properties, including tensile strength and wear resistance, than PEK and far superior mechanical properties compared to PTFE. This makes PEEK ideal for applications requiring both thermal stability and mechanical strength.
How to Select the Correct Type of PEEK for Your Needs
There are several factors that need to be considered. The temperature requirements, chemical exposure, and mechanical properties needed all play a crucial role in determining the most suitable PEEK grade. Here’s what you should keep in mind when making this important decision.
Factors to Consider When Choosing PEEK Grade
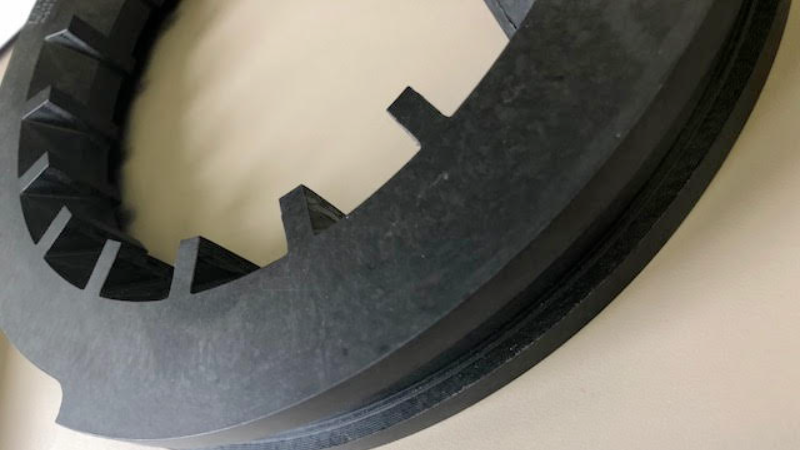
Temperature Requirements:
- Determine the maximum and minimum temperatures the PEEK will be exposed to.
- Consider whether high-temperature stability or cryogenic performance is necessary.
- Evaluate if thermal conductivity is a significant factor.
Chemical Exposure:
- Identify the types of chemicals or solvents that the PEEK will come into contact with.
- Check compatibility charts provided by manufacturers for chemical resistance information.
- Assess if any specialized grades are required for aggressive environments.
Mechanical Properties Needed:
- Define the load-bearing requirements and stress levels expected in your application.
- Consider factors such as wear resistance, impact strength, and stiffness.
- Determine if electrical conductivity or insulation properties are essential.
Conclusion
In conclusion, PEEK stands out as an exceptional choice for high-temperature sealing applications due to its unparalleled thermal stability, chemical resistance, and mechanical properties. It effectively outperforms other sealing materials like PEK and PTFE in extreme conditions, making it the go-to material for industries ranging from aerospace to oil and gas.
Partner with Hongju for Unmatched High-Temperature PEEK Solutions
Elevate the performance and longevity of your high-temperature applications by partnering with Hongju. We offer tailor-made PEEK solutions that not only meet but exceed industry standards. With Hongju, you get quality, reliability, and state-of-the-art technology, all designed to help your projects withstand extreme conditions.
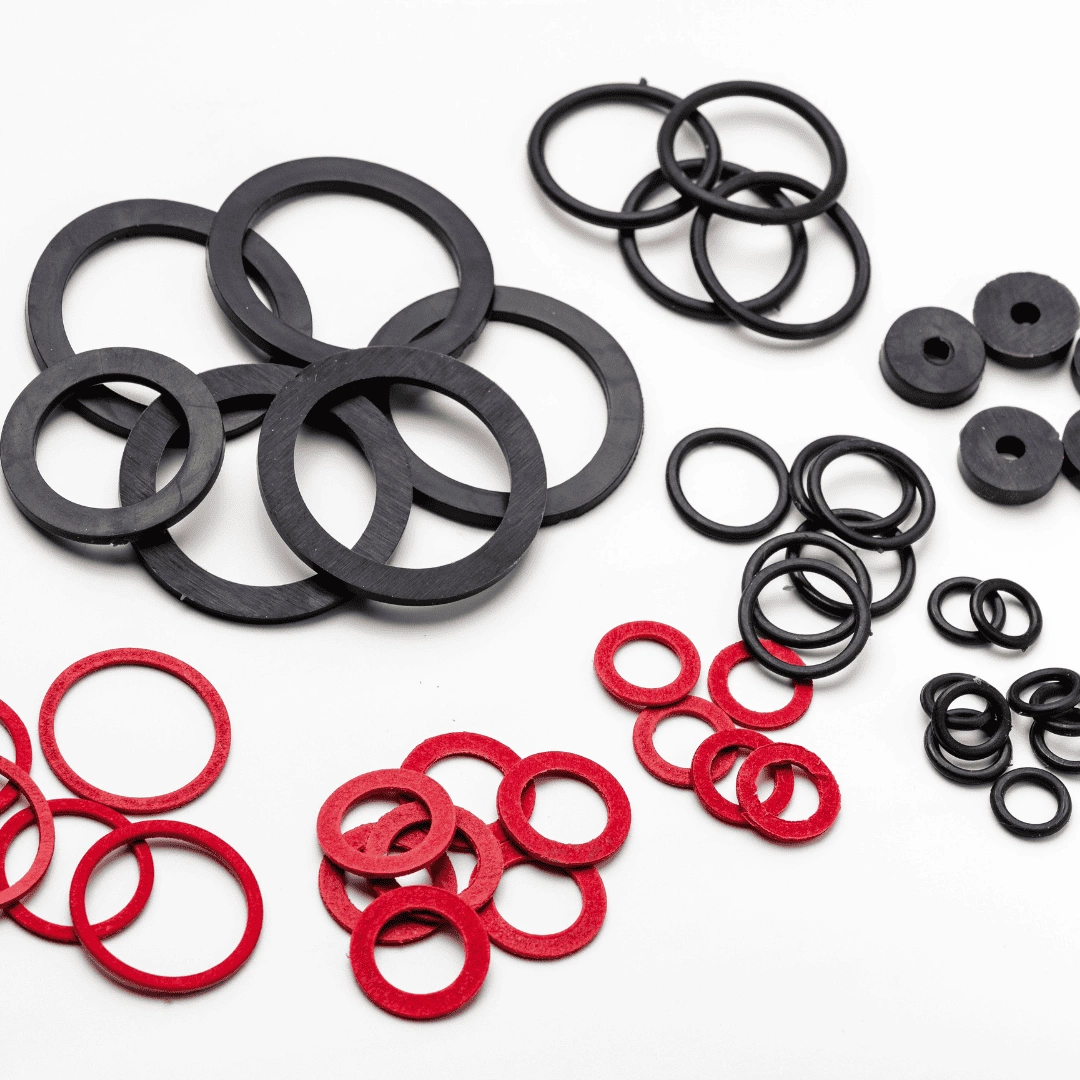
Send Your Inquiry Now!
Quality Meets Affordability. Inquire Now for High-Quality Products at Low Volumes.